首末件管理规定
冲压首末件管理规定
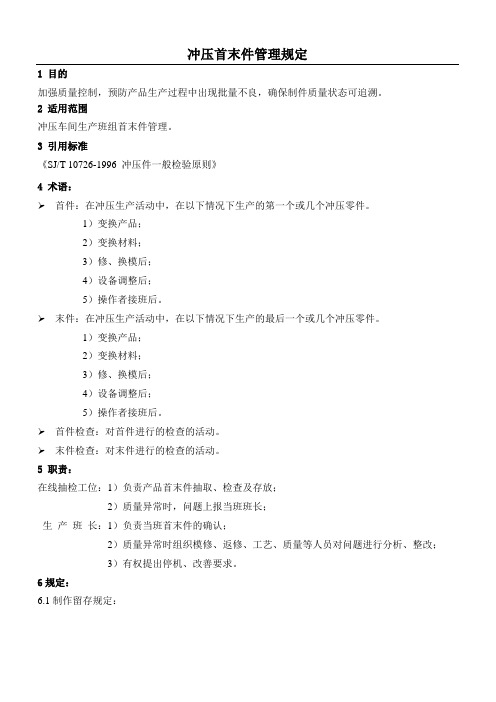
1 目的加强质量控制,预防产品生产过程中出现批量不良,确保制件质量状态可追溯。
2 适用范围冲压车间生产班组首末件管理。
3 引用标准《SJ/T 10726-1996 冲压件一般检验原则》4 术语:➢首件:在冲压生产活动中,在以下情况下生产的第一个或几个冲压零件。
1)变换产品;2)变换材料;3)修、换模后;4)设备调整后;5)操作者接班后。
➢末件:在冲压生产活动中,在以下情况下生产的最后一个或几个冲压零件。
1)变换产品;2)变换材料;3)修、换模后;4)设备调整后;5)操作者接班后。
➢首件检查:对首件进行的检查的活动。
➢末件检查:对末件进行的检查的活动。
5 职责:在线抽检工位:1)负责产品首末件抽取、检查及存放;2)质量异常时,问题上报当班班长;生产班长:1)负责当班首末件的确认;2)质量异常时组织模修、返修、工艺、质量等人员对问题进行分析、整改;3)有权提出停机、改善要求。
6规定:6.1制作留存规定:➢当批生产的首件及末件进行检查后留存;➢顶盖生产涉及到品种转换时,分别制作并留存有天窗及无天窗产品首末件;➢当批生产未完成,出现临时换模生产或设备维修等情况时,继续生产后产生的首末件替换当批之前件;➢操作者接班后,设备重新启动生产的首件替换当批之前件;➢当批生产过程中若包含实验料,分别制作各材料首末件;➢当批生产需要多垛板料,每垛料分别制作首末件。
6.2存放规定:➢当批首末件:装入首末件工位器具,替换上批次的首末件。
➢上批次首末件:装入当批生产成品件工位器具中。
➢试验料首末件:装入试验料成品件工位器具中。
➢料剁更换产生的首末件:如无其他情况,第一垛板料的首件及最后一垛板料的末件作为当批生产首末件。
生产过程中产生的其它首末件按抽检件存放到相应工位器具中。
6.3签字要求:➢签字位置:在制件的里侧面醒目位置。
➢签字内容:包括生产日期、操作者、班长签名等内容,并且标注○首或○末。
6.4检查标准:➢按《抽检作业指导书》进行首末件检查及标注。
产品首末件管理制度(2篇)
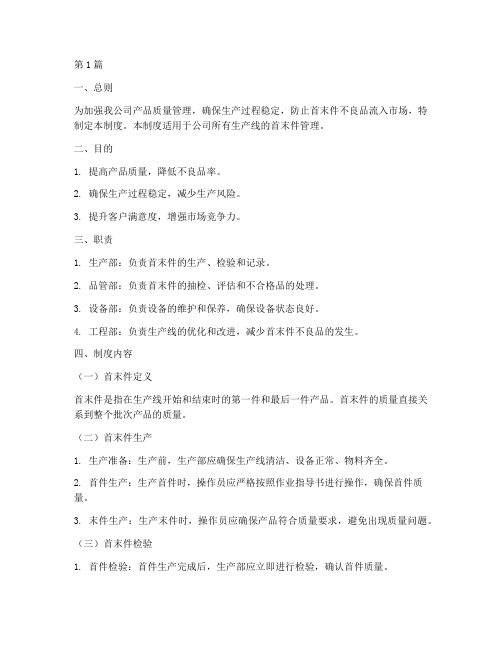
第1篇一、总则为加强我公司产品质量管理,确保生产过程稳定,防止首末件不良品流入市场,特制定本制度。
本制度适用于公司所有生产线的首末件管理。
二、目的1. 提高产品质量,降低不良品率。
2. 确保生产过程稳定,减少生产风险。
3. 提升客户满意度,增强市场竞争力。
三、职责1. 生产部:负责首末件的生产、检验和记录。
2. 品管部:负责首末件的抽检、评估和不合格品的处理。
3. 设备部:负责设备的维护和保养,确保设备状态良好。
4. 工程部:负责生产线的优化和改进,减少首末件不良品的发生。
四、制度内容(一)首末件定义首末件是指在生产线开始和结束时的第一件和最后一件产品。
首末件的质量直接关系到整个批次产品的质量。
(二)首末件生产1. 生产准备:生产前,生产部应确保生产线清洁、设备正常、物料齐全。
2. 首件生产:生产首件时,操作员应严格按照作业指导书进行操作,确保首件质量。
3. 末件生产:生产末件时,操作员应确保产品符合质量要求,避免出现质量问题。
(三)首末件检验1. 首件检验:首件生产完成后,生产部应立即进行检验,确认首件质量。
2. 末件检验:生产结束时,生产部应进行末件检验,确保末件质量。
3. 检验方法:首末件检验应采用目视、手感、测量等方法,确保检验的准确性。
(四)首末件记录1. 记录内容:首末件检验记录应包括产品名称、生产日期、检验结果、检验员等信息。
2. 记录方式:首末件检验记录可采用纸质记录或电子记录,确保记录的完整性和可追溯性。
(五)不合格品处理1. 不合格品判定:首末件检验发现不合格品时,应立即判定不合格品,并采取措施防止不合格品流入下一道工序。
2. 不合格品处理:不合格品处理应遵循“四不放过”原则,即:不查明原因不放过、不采取纠正措施不放过、不落实责任不放过、不进行总结教训不放过。
(六)首末件评估1. 评估周期:每月对首末件进行一次评估,分析首末件不良品的原因,制定改进措施。
2. 评估内容:评估内容包括首末件不良品率、不良品原因分析、改进措施实施情况等。
首末件管理规定

首末件管理规定1、编写目的为加强产品质量控制,预防产品在生产过程中出现批次质量事故,保证产品实物质量,促进产品顺利交付,特制定本管理办法。
2、使用范围本办法适用于公司所有生产工序首末件的确定及管理。
3、术语定义3.1首件:每个班次刚开始时或过程中条件发生改变,而后加工正常的第一或前几件产品,由生产人员确认后提交检验室做首件检验。
“首件”一般指正常批量生产前,经一定检验标准确认合格且适合用于评判生产产品品质的样品。
3.2末件:是指当批或当班生产的最后一个(组)产品。
3.3控制要求:3.3.1有下列情况之一的,需进行首件检验(首件首检触发条件):--重新开机时--换模、换料后--加工工艺重新调整后--工装、模具维修后--质量标准修订后--生产场地变更后3.3.2有下列情况之一的,需进行末件检验(末件检验触发条件):--该批次生产结束前--停机停产前4、职责划分4.1制造部的产品负责人需及时提交首末件到检验室进行首检、末检。
4.2质量异常时,制造部需组织人员对问题点进行分析、调整、改善。
4.3质量部检验室负责首末件的确认及过程检验。
4.4质量部检验室对不合格的首末件,要配合制造部进行分析,并有权提出停机要求改善。
5、作业程序5.1根据本办法第3.3.1条款,由制造部产品负责人提交首件产品到质量部检验室进行首件检验。
5.2检验结果不符合标准要求的,质量部检验室通报制造部重新调试;检验结果符合标准要求的,检验负责人应将检验后的产品按规定标识后,存档质量部,以供追溯模具状况所需。
5.2.1首件标识内容包含:产品图号、名称、送检日期、检验人员签名或签章。
5.2.2首件确认合格后,制造部方可开始生产。
5.3根据本办法第3.3.2条款,需要制作末件时,由制造部产品负责人提交首件产品到质量部检验室进行首件检验。
5.4末件检验合格,标识后转制造部进行保管并记录,以供追溯模具状况所需。
5.5末件标识内容包含:产品图号、名称、送检日期、检验人员签名或签章。
产品首末件管理制度

产品首末件管理制度一、背景介绍在产品生产的过程中,首末件管理是一个非常重要的环节。
首末件是指每一批产品的第一件和最后一件,对于产品质量的控制和生产效率的提高起着关键作用。
因此,建立科学的首末件管理制度对于企业来说至关重要。
二、首末件管理的意义首末件管理是产品生产过程中的一个重要环节,其意义主要有以下几个方面:1.保证产品质量首件是产品生产过程中的第一件产品,其质量直接影响到后续产品的质量。
通过对首件进行严格的检测和控制,可以及时发现问题并及时进行调整,从而确保产品质量的稳定。
2.提高生产效率通过对末件进行检测和评估,可以及时发现生产过程中存在的问题和瓶颈,从而及时采取措施解决,提高生产效率。
3.降低生产成本通过对首末件进行管理,可以及时发现生产过程中存在的问题,避免不合格品的生产,降低二次加工成本,提高生产效率。
4.改善生产环境通过对首末件进行管理,可以及时发现生产环境中存在的问题,及时进行整改,改善生产环境,提高工作效率。
三、建立首末件管理制度的必要性建立首末件管理制度对于企业来说是非常必要的,其主要原因有以下几点:1.规范生产流程通过建立首末件管理制度,可以规范生产流程,建立起严谨的产品生产管理体系,提高生产效率。
2.提高产品质量通过对首末件进行严格管理,可以及时发现存在的问题并及时解决,从而提高产品质量。
3.降低生产成本通过对首末件进行管理,可以降低不合格品的生产,减少二次加工成本,提高生产效率。
4.改善生产环境通过对首末件进行管理,可以及时发现生产环境中存在的问题,及时进行整改,改善生产环境,提高工作效率。
四、建立首末件管理制度的具体措施为了建立一个科学、规范的首末件管理制度,需要采取以下具体措施:1.明确首末件的定义和标准首末件管理的第一步是明确首末件的定义和标准,确定首末件的检测方法和要求,从而为后续的管理和控制奠定基础。
2.建立责任制建立明确的首末件管理责任制,明确各个环节的责任人和责任范围,确保每个环节都能够按照规定的要求进行操作。
首末件管理规定

1 目的为加强质量控制,预防产品生过程中,出现批量超差、返修、报废等情况,保证产品实物质量,促进产品顺利交付,特制定本管理办法.2 范围本文件适用公司所有生产工序首末件确认;3 定义3.1.首件:每个班次刚开始时或过程发生改变后加工的第一或前几件产品,对于大批量生产,“首件”往往是指一定数量的样品。
3.2.末件:是指当批或当班生产零件的最后一个零件;3.3.控制要求:下列情况之一的,需进行首检:(首检时机)----重新开机; ----换模、换料、换班或设备更换时;----工艺参数重新调整时; ----工装、模具变更换维修后; ----生产场地发生变更;4 责任与权限制造部:4.1.负责产品首末件的自检,互检;4.2.质量异常时,负责组织人员对问题点进行分析、调整;品质部:4.3.负责首末件的确认,过程检验;4.4.配合制造部门对不合格的首末件进行分析及调整并有向制造部提出停机的权限;5 首末件操作流程沧州永达五金制造有限公司编 号: Q/YBZY-PJ-12 版 次: A/0 制定部门: 品技部首末件管理规定制定日期: 2014.08.15第 1 页 共 3 页编 号: Q/YBZY-PJ-12责任部门相关记录《8D报告单》责任部门对问题点进行根源分析和改善措施,对于造成恶劣影响或成本报废的异常,提供责任人名单品技部沧州永达五金制造有限公司版 次: A/0确认责任部门回复的原因分析和改善措施是否有效,并跟进改善效果/合格后对控制计划进行修定按照首件批量生产,并负责保管好《自检记录表》生产部品技部品技部生产部制定部门: 品技部首件流程图制定日期: 2014.08.15第 2 页 共 3 页说明流程图经培训合格的员工允许上岗,并按照技术资料和SOP,每个独立的作业单位首先生产第一件产品操作工对首件生产的产品进行检验,确认符合技术要求和SOP要求,填写《自检记录表》并签名(尺寸需填写具体测量数值)班长对操作工进行必须的岗前培训,准备好生产所需的技术文件和工装治具,并确认文件和治具正确性和适用后,派发给操作工,作业前对人、机、料、法、环进行确认生产部《作业准备验证记录表》生产部《自检记录表》品技部《不合格品评审处置单》 《报废申请单》生产部《自检记录表》QC对生产的《自检记录表》做确认,确认车间有正常进行首件自检工作,并核对检验结果后在《自检记录表》签字生产部《自检记录表》班组长确认操作工每个首件都有做检验,并对操作工的首件检验结果做确认签字品技部当QC发现生产未做自检,按《质量奖惩制度》的相关规定进行处罚,当发现生产首件自检错误并造成报废时,按《不良品控制程序》反馈责任部门负责人,必要时可要求停止生产沧州永达五金制造有限公司编 号: Q/YBZY-PJ-12 版 次: A/0OKOKOKOK NGNGNGNG产前准备自检 首件生产组长确QC 确认 质量异常单 原因分析和改善措施品质确批量生产责任部门相关记录生产部生产部《自检记录表》生产部品技部品技部《自检记录表》品技部生产部编制:审核:批准:识在流转卡上签字确认,并通知生产部门可流入到下道工序《不合格品评审处置单》检验员对当班生产合格的零件贴上合格标进行封样生产班长或员工,对问题进行分析与调整3、对当班生产的不合格品需进行隔离,并开具《不合格品评审处置单》进行处理检验员确认末件合格后,检验结果需填入《自检记录表》,并在样件上贴上末件标签1、检验员在接到生产部门通知后,10分钟之内需完成末检2、当确认末件不合格时,检验员需立即通知作业员需对当班或当批次生产的末件进行自检1、当班班长需对作业员自检的末件进行互检2、确认后如末件合格,需通知当班检验员对末件进行确认;流程图说明沧州永达五金制造有限公司末件流程图第 3 页 共 3 页 制定部门: 品技部 制定日期: 2014.08.15产结束前作业员班长检验员产品标识 流入下道工序通知当班班长立即调查原因并整改立即对当班生产的产品进行确认不良品进行标不良品进行标OKOKNGOK OKNGOK。
首末件管理规定

首末件管理规定
1.目的
为防止正常生产时产生批量不合格,确保生产过程得到有效控制以及对产品标准中不能用文字表达或虽用文字表达,还不确切而又必须用实样来说明规定要求。
2.适用范围
适用于公司所有经客户认可、已批量供货的产品(包括半成品)。
3.职责
质量部归口管理。
4.名词解释
4.1首件:是换摸后调试后符合检验规范的第一个产品,此调试过程中产生的报废件不超过10个;
4.2末件:产品批次注塑结束前,正常生产状态时的产品。
5.程序
5.1在下列情况下需进行首件确认
5.1.1每批连续生产前;
5.1.2工艺更改后;
5.1.3原材料(油漆)更改后;
5.1.4生产流程更改后;
5.1.5设备或工装维修后;
5.1.6采用新的工装;
5.1.7其它能较大影响产品质量的情况。
5.2每班生产开始/批量生产开始由操作工检验,过程检验员参照生产样件和过程检验规范
对首件检验确认,并签字,做好首件产品检验记录。
5.3首件检验如出现不合格,生产部门应查明原因,采取纠正措施,然后重新进行首件确认,直到首件合格后才可批量生产。
5.4每班生产结束/批量生产结束前或批量生产意外中断,应做末件产品检验记录,具体操
作同首件检验;若末件产品合格,合格首件不加特别标识流入批量中。
5.5每班生产开始/批量生产开始或批量生产意外中断的再生产,若首件产品合格,合格末
件不加特别标识流入批量中。
5.6不合格末件由制造部保存,直到合格首件产生后进行其它处理。
6.相关文件
产品标识和可追溯规定
7.使用表单。
首末件管理规定
首末件管理规定
1.目的:
为加强产品质量控制,预防产品在生产过程中出现批量不良,在下次前处理好本次生产
过程中的问题点,确保下次生产时顺利进行,以达到降低成本、提高效率。
特制定本管
理规定。
2.
3.1
“首3.2
4
4.1
4.2
5.
5.1生产开始时根据本规定的第3.1条款,需要制作首件时,由生产部领班提供产品通报当班质检员进行首件检验。
5.1.1当班质检员接到生产部领班通知后,根据《生产指令单》和《检验指导书》对该机台的
产品进行检验判定。
5.1.2质检员需在10分内做出外观判定,20分钟内做出最终判定。
——仅供参考
5.1.3若检验结果符合要求的要及时做好首件样品(样品包括:日期、时间、质检员签名)和
加工样品并挂于相应的机台上,检验结果不符合标准要求的,质检员需立即通报生产
领班重新调试,重新报检。
5.2首件再确认:当首件确认合格后生产了1.5-2小时时,质检员要对生产中的产品进行一次再
确认,并做好样件。
5.3
5.5
——仅供参考。
班组零部件加工首、末件检验管理规定
1目的为了强化班组的质量管理,规范首件、末件检验,降低质量风险。
2适用范围本管理规定适用于生产线的首件检验和末件检验。
3职责3.1 技术质量室负责本规定的归口管理,对执行情况进行检查并按《班组产品质量评审考核办法》实施考核。
3.2 各相关部门应严格执行本规定。
4机加工工序首件检验要求4.1 首件检验指令的分类首件检验指令包括:首件自检、首件边做边检和首件停机送检等。
首件自检:即首件生产后仅要求操作工进行自检,合格后开始生产。
首件边做边检:即首件生产后送精测间或平台边生产边等待检测结果。
首件停机送检:即首件生产后送精测间或平台停机检测,检测合格后生产。
4.2 自检检测要求4.2.1普通加工工序:要求所有加工项目都要检测。
4.2.1.1同一把刀具钻、攻、粗镗具有相同检测内容的孔允许使用规定的检测手段检测该刀具加工的最后一个孔,其它孔目测。
4.2.1.2其它同一把刀具加工的具有相同检测内容的加工部位,首、尾加工部位必须检测,中间加工部位目测。
4.2.1.3具有不相同检测内容的加工部位,必须按4.3.1.1和4.3.1.2规定进行检测。
4.2.2精加工工序:同一把刀具钻、攻具有相同检测内容的孔允许按4.3.1.1和4.3.1.3要求检测,其它同一把刀具加工的所有内容都必须检测。
4.2.3有专用量具检测的项目必须使用相应的专用量具检测。
无专用量具检测的项目,通用量具可以检测的项目必须使用通用量具检测(高精度通用量具可以代用低精度通用量具,量程在测量范围内的游标卡尺、深度卡尺允许代用)。
无专用量具检测的项目,通用量具不可以检测的项目必须目测。
4.2.4首检工件在填写自检记录表时在“追溯号”旁标注“首”记号(自检记录表中有特殊规定的按自检记录表中的要求填写)。
末检件工件在填写自检记录表时在“追溯号”旁标注“末”记号。
4.2.5首件自检必须完成所有频次检内容。
4.3 送精测间检测要求4.3.1送检前工件必须进行自检并清理,送检时按照精测间要求进行登记,并注明“首件”、“专检”等能清楚表明检测目的的字样(允许简写)。
首末件管理办法
1 目的为了更好的控制产品的质量,预防产品在生产过程中的批量不良,在下次生产前处理好本次过程中的问题,确保使后续生产顺利进行,以达到降低成本、提高效率。
特制定本管理规定。
2 范围适用于本公司注塑车间首末件管理3 术语和定义首件:每次换模开始时或过程中条件发生变化时(包括:换机、换料、换色、修模、停机后、工艺发生变化较大时),由生产领班确认合格的产品后第15模报质检员做首件检验。
“首件”一般指正常批量生产前,依照检验标准确认合格的样品。
末件:是指当批次生产的最后一只产品制作的合格样品。
报废:为避免不合格品原有预期用途误用而对其所采取的措施。
废弃模:开机生产初期尺寸、外观不稳定的产品确认为不良品报废处理。
4 职责4.1 生产部负责首件自检,通报质检员做首末件,在质量异常时,负责组织人员对问题点进行分析和调整、改善。
4.2产生部门/车间负责组织对产品的评审工作及对生产现场产品的标识、隔离,并按评审结果进行处理及让步接受的申请。
4.3品质部负责对首末件的确认及过程检验,确保首末件产品的外观、尺寸、结构、性能等各方面满足客户的要求。
配合生产部门对改善品的检查,必要时组织相关部门参加评审。
4.4当出现批量不合格时,检验员有权要求停止生产;当外协辅料影响生产时检验员有权要求异常辅料隔离退换,有权要求对生产的产品进行追溯隔离,产品检查合格后方可放行。
4.5品质部负责首件产品品质记录的制作及保存,首件样品最长保存期限为三个月,末件产品最长保存期限为六个月4.6技术部负责返工返修指导书的编制;负责异常产品对顾客影响程度的评审。
5首末件检查时机5.1 每日每班到岗上班,某机台开始生产时,某机台转换产品颜色或材料时,某工序变更生产工艺后,生产异常改善后再生产时,模具生产机台及周边设备异常修复后,其它特殊情况导致生产机台不能正常生产停止生产后再继续生产时,应执行首件检查5.2 每批次生产的最后1个零件执行末件检查,末件随模具流转或者放置在固定的机台位置6首件检验6.1 IPQC接到生产部的首件样品后,依据《检验作业指导书》、“OK样品”、“限度样件”及外观标准、规格尺寸、性能需求及其它特殊要求对产品外观、尺寸、结构、性能等方面进行综合判定并做好相关记录。
首末件管理办法
1、编写目的为加强产品质量控制,预防产品在生产过程中出现批次质量事故,保证产品实物质量,促进产品顺利交付,特制定本管理办法。
2、使用范围本办法适用于公司所有生产工序首末件的确定及管理。
3、术语定义3.1首件:每个班次刚开始时或过程中条件发生改变,而后加工正常的第一或前几件产品,由生产人员确认后报IPQC做首件检验。
“首件”一般指正常批量生产前,经一定检验标准确认合格且适合用于评判生产产品品质的样品。
3.2末件:是指当批或当班生产的最后一个(组)产品。
3.3控制要求:3.3.1有下列情况之一的,需进行首件检验(首件首检触发条件):--重新开机时--换模、换料后--加工工艺重新调整后--工装、模具维修后--当班接班时--质量标准修订后--生产场地变更后3.3.2有下列情况之一的,需进行末件检验(末件检验触发条件):--当班交班前--该批次生产结束前--停机停产前4、职责划分生产部:4.1负责首末件的制作及自检,通报IPQC首检。
4.2质量异常时,负责组织人员对问题点进行分析、调整、改善。
品质部:4.3负责首末件的确认及过程检验。
4.4配合生产部门对不合格的首末件进行分析,并有权提出停机要求改善。
5、作业程序5.1根据本办法第3.3.1条款,需要制作首件时,由生产部人员提供产品通报当班IPQC进行首件检验。
5.1.1当班IPQC接到生产部首件检验要求后,根据《生产计划单》核对该产品《检验指导书》并提取该产品样件。
如在连续生产中为交接班首检时,可参考上班次首件,有疑问时再提取样件。
5.1.2必须的检验工具,需符合质量控制标准中《计量器具管理规定》要求,以确保检验结果准确可靠。
5.1.3按该产品《检验指导书》规定,结合实物样件对生产部提供的产品进行检验。
5.1.4检验结果不符合标准要求的,IPQC通报生产部重新调试;检验结果符合标准要求的,IPQC将检验后的产品按规定标识后,放置在机台对应位置(该位置由生产部门提供)。
- 1、下载文档前请自行甄别文档内容的完整性,平台不提供额外的编辑、内容补充、找答案等附加服务。
- 2、"仅部分预览"的文档,不可在线预览部分如存在完整性等问题,可反馈申请退款(可完整预览的文档不适用该条件!)。
- 3、如文档侵犯您的权益,请联系客服反馈,我们会尽快为您处理(人工客服工作时间:9:00-18:30)。
首末件管理规定
1.目的:
为加强产品质量控制,预防产品在生产过程中出现批量不良,在下次前处理好本次
生产过程中的问题点,确保下次生产时顺利进行,以达到降低成本、提高效率。
特
制定本管理规定。
2.范围:
适用于公司注塑车间首末件管理。
3.定义:
3.1首件:每次换模开始时或过程中条件(包括:换机、换料、换色、修模、停机后或工艺
变化较大时)发生变化时,由生产领班确认合格的产品后第15模报质检员做首
件检验。
“首件”一般指正常批量生产前,依照检验标准确认合格的样品。
3.2末件:是指当批生产的最后一只产品制作的合格样品。
4.职责:
4.1生产部:负责首末件的自检,通报质检员做首末件。
在质量异常时,负责组织人员对问题点进行分析、调整、改善。
4.2品质部:负责首末件的确认及过程检验。
配合生产部门对不合格的首末件进行分析,并有权提出停机要求及改善要求。
5.作业流程:
5.1生产开始时根据本规定的第3.1条款,需要制作首件时,由生产部领班提供产品通报当班质检员进行首件检验。
5.1.1当班质检员接到生产部领班通知后,根据《生产指令单》和《检验指导书》对该
机台的产品进行检验判定。
5.1.2质检员需在10分内做出外观判定,20分钟内做出最终判定。
5.1.3若检验结果符合要求的要及时做好首件样品(样品包括:日期、时间、质检员签
名)和加工样品并挂于相应的机台上,检验结果不符合标准要求的,质检员需立
即通报生产领班重新调试,重新报检。
5.2首件再确认:当首件确认合格后生产了1.5-2小时时,质检员要对生产中的产品进行一
次再确认,并做好样件。
5.3根据本规定第3.2条,需要制作末件时,由生产领班提供最后一只产品通报当班质检员
进行末件检验。
5.3.1当班质检员接到生产领班末件后,根据该产品《检验指导书》并对比首件对末件
进行检查。
5.3.2末件检验合格,标识(同首件标识)后转生产领班随同模具一起入到模具仓库。
5.3.3末件检验不合格,应通报当班领班并对本批产品进行标识隔离,清理出所有有问
题产品,并追查出现问题的原因予以解决。
5.4当生产完成时虽然产品的首末件都是合格的,但是因后续加工较麻烦、成本高或劳动
强度大时,生产部和品质部要提出改善措施或报告技术部(以修改模为主)以便下次生产时达到降低成本、提高效率。
5.5领模时模具仓管员要把末件随同模具一起发给注塑车间。