首件检验规定
首件检验管理规定
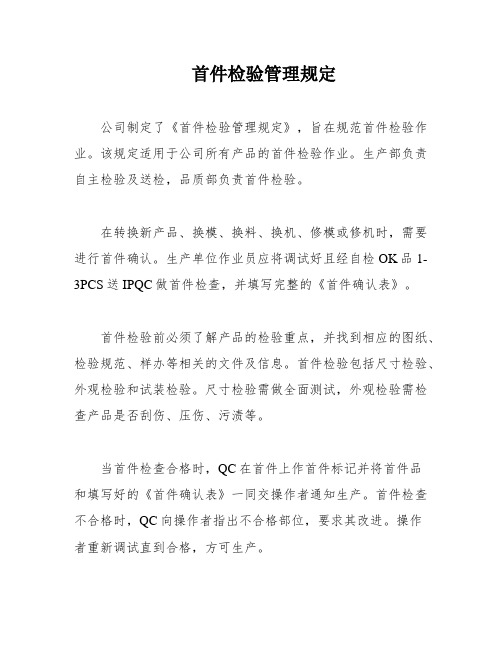
首件检验管理规定
公司制定了《首件检验管理规定》,旨在规范首件检验作业。
该规定适用于公司所有产品的首件检验作业。
生产部负责自主检验及送检,品质部负责首件检验。
在转换新产品、换模、换料、换机、修模或修机时,需要进行首件确认。
生产单位作业员应将调试好且经自检OK品1-
3PCS送IPQC做首件检查,并填写完整的《首件确认表》。
首件检验前必须了解产品的检验重点,并找到相应的图纸、检验规范、样办等相关的文件及信息。
首件检验包括尺寸检验、外观检验和试装检验。
尺寸检验需做全面测试,外观检验需检查产品是否刮伤、压伤、污渍等。
当首件检查合格时,QC在首件上作首件标记并将首件品
和填写好的《首件确认表》一同交操作者通知生产。
首件检查不合格时,QC向操作者指出不合格部位,要求其改进。
操作
者重新调试直到合格,方可生产。
经XXX填写好的《首件确认表》及首件样品应挂于机台旁。
当IPQC接到首件品时应立即确认,原则上首件确认不可超过半个小时,以免影响生产进度。
XXX根据检验结果填写《品质检测报告》交主管审核后存档。
最后,公司没有参考文件,但制定了《首件确认表》作为表单记录。
首件检验管理规定

1 职责项目部负责组织实施首件鉴定。
2 首件鉴定首件鉴定是按照设计图样和工艺规程的要求,对试制和批量试生产的第一件零部(组)件进行全面的工序和成品的检查,以确定生产工艺和设备(生产条件)能否保证生产出符合设计要求的产品。
以验证和鉴定过程的生产能力,为产品的生产(工艺)定型作准备。
3 首件鉴定范围3.1生产(工艺)定型前试制的零部件(组)的首件;3.2在批量生产过程中:a)设计图样的重大更改(如涉及性能、可靠性、维修性、安全性或其他重要特性的更改)后制造的首件;b)工艺规程的重大更改(如设计工艺方法、检测方法、工艺装置、设备等更改)后,对产品的符合性产生影响的首件;c)产品转厂生产的首件;d)非连续批次生产制造的收件。
3.3合同要求制定的项目4 首件鉴定的要求4.1项目部应选定对质量进度或成本有重要影响的零部(组)件,至少应包括关键件、重要件和含有关键工序的零部件。
4.2图样、工艺规程等技术文件应正确、完整、协调和现行有效。
4.3首件鉴定件应有“首件”标识(签)。
4.4首件选用的原材料、器材应符合技术标准或文件规定的要求。
4.5选用的加工、试验设备、检测设备、工艺装备和监视测量应符合规定的要求,处于正常工作状态,并处于合格有效期内。
4.6首件原始记录应完整、准确、清晰。
4.7首件操作者和检验人员必须有相应的资格。
4.8首件生产过程应按《生产过程控制程序》进行控制。
4.9首件鉴定应依据现行有效的合同、设计图样、工艺规程和检验规程等。
4.10首件鉴定合格后,方可进行后续批试制或生产。
4.11首件鉴定不合格时,在鉴定记录完整的前提下,允许用后续产品递补,重新进行首件鉴定。
5 首件鉴定的程序5.1组织首件鉴定组项目部组织进行首件鉴定,首件鉴定成员由设计、工艺、生产、检验等有关人员参加,必要时,请顾客代表参加。
5.2首件鉴定成员应确定首件鉴定检验项目。
5.3生产部按要求生产(加工)首件产品,并对首件进行标示。
首检检验
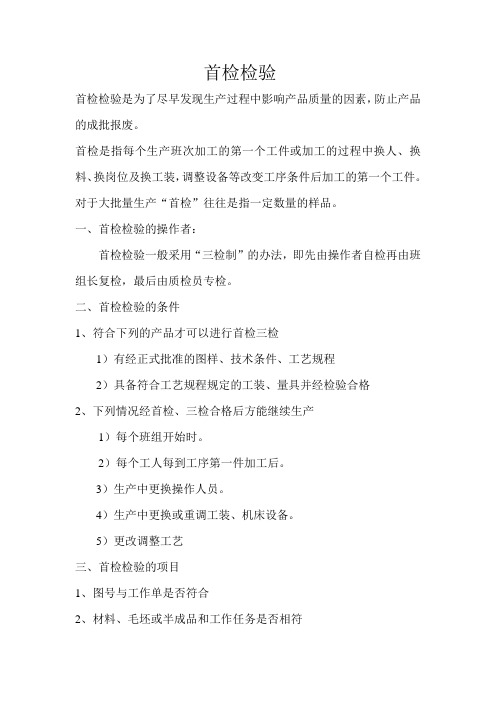
首检检验首检检验是为了尽早发现生产过程中影响产品质量的因素,防止产品的成批报废。
首检是指每个生产班次加工的第一个工件或加工的过程中换人、换料、换岗位及换工装,调整设备等改变工序条件后加工的第一个工件。
对于大批量生产“首检”往往是指一定数量的样品。
一、首检检验的操作者:首检检验一般采用“三检制”的办法,即先由操作者自检再由班组长复检,最后由质检员专检。
二、首检检验的条件1、符合下列的产品才可以进行首检三检1)有经正式批准的图样、技术条件、工艺规程2)具备符合工艺规程规定的工装、量具并经检验合格2、下列情况经首检、三检合格后方能继续生产1)每个班组开始时。
2)每个工人每到工序第一件加工后。
3)生产中更换操作人员。
4)生产中更换或重调工装、机床设备。
5)更改调整工艺三、首检检验的项目1、图号与工作单是否符合2、材料、毛坯或半成品和工作任务是否相符3、材料、毛坯的表面处理和安装定位是否相符。
4、配发配料是否符合规定要求、5、首件产品加工进来后的实际质量是否符合图纸或技术文件的规定要求、四、首件检查的要求进行首件产品的检验时,必须注意以下事项1)首件三检要由操作人员办理交验手续,经首件三检检验合格的零件产品要在检验单上签字,并做好首件检验的记录。
2)首件三检错误时,由参加三检者负责。
3)不执行首件三检盲目生产,不听劝告者检验员有权拒绝验收其产品,由此造成的废品由直接责任人负责。
视情节轻重程度赔偿废品损失。
4)首件三检不合格需查明原因,采取措施排除故障重新进行首件三检。
5)首件三检合格后,生产人员在生产过程中还要勤看、勤量、勤检验,检验员要加强巡回检验,预防不合格品产生。
6)对于重要零部件的关键工序和尺寸,应建立质量控制点,加强首件三检,增加巡回抽检的次数。
7)检验员应按规定在检验合格后的首件上作出标识,并保留到该产品完工。
8)首件检验必须及时,以免造成不必要的浪费,首件检验后要保留必要的记录,填写“首件检验记录表”五、首件检验规定第一条目的为确保生产质量,避免出现批量性的质量问题,特制定本规定第二条适用范围公司均应在生产加工过程中进行首件检验后,并依本规定执行。
首件检验管理规定

首件检验管理规定1.目的:为加强质量控制,规范检验管理,减少批量性返工、用错料,规范作业产品统一性。
2.适用范围:适用制造过程当中所有首件检验。
3.职责:3.1 生产部负责提供首件,并对生产物料、工艺、生产过程的确认并完成首件自检,作好状态标识,照实填写完整《首件确认表》并将首件样、制造工单一起交由品质部。
3.2 品管单位负责制程中的首件检验工作。
3.3 工程技术部:负责提供产品检验所需的产品图样及设计文件、技术标准等技术资料。
3.4 未经新品首件、批首件检验或首件检验不合格,而擅自生产产品,由此引起的质量事故,由直接责任者负责。
3.5 检验员、生产线负责人对首件检验的正确性负责。
3.6 对首件确认工作未完成,检验人员开始出具质量凭证,造成的质量事故,责任由检验人员承担。
4.内容:4.1 首件检验时,操作人员、检验人员必须首先做到“三对照”,即工艺路线卡、工艺规程、原材料(或半成品)要三者相符。
4.2 首件提供:制造单位依据生产进度按生管开立的《生产单》至仓库领料,并作好首件并自检,要根据工艺规程要求进行检验,须经检验合格后再提交品质人员专检。
提交时应包含《制造工单》、《首件确认表》,单个产品需包装完全(包含贴好标识标签;附件如合格证、说明书;所有配件及包装套料)。
4.3 首件检验时,应按工艺规程要求,检验人员在《首件确认表》上签字确认,且在首件产品上做出标识。
4.4 首件经检验人员确认合格后方可继续加工。
未进行首件检验的产品,检验人员有权拒绝验收。
4.5 检验人员依工程样品/检验规范/BOM/等检验依据,将判定的结果记录于《首件确认表》。
A.当确认 OK 时,由主管核准;B.当确认 NG 时,则经理核准;4.6 在首件检验中发现的不合格产品,应立即退回,重做首件,并做好记录,按“不合格品控制程序”的规定处理。
4.7 外观要求按照以下标准检验(见下页)。
类别分类归纳检验项目检验标准检验工具缺陷判定内容备注: 1.在外观类中,A 面为光源直面照射方向所在的面;B 面为A 面的2个侧面;C 面为A 面的反面.2.在包装类中,A 面为包装完成正常放置时朝上的面,B 面为A 面的2个侧面;C 面为A 面的反面.3.抽样水准按GB/T2828.1-2003一般Ⅱ次检验进行.其中CRI=0;MAJ=0.65;MIN=1.5. CRI MAJ MIN外观点污点/杂质 A 面(正面)≦0.4m ㎡或≧0.4m ㎡但不超出2点B 面(侧面)≦1.0m ㎡或≧1.0m ㎡但不超出3点C 面(底部)≦2.0m ㎡或≧2.0m ㎡但不超出4点 直尺/目视 ▲ 砂眼 A 面不可有B 和C 面≤0.5m ㎡卡尺/目视 ▲ 线 划痕 A 面 10mm*0.5mm ≦1条 B 面 15mm*0.75mm ≦2条且间隔≦5cmC 面 20mm*1.0mm ≦3条且间隔≦5cm 目视 ▲毛边 尺寸≤0.3mm卡尺/目视 ▲间隙 间隙≤0.8mm (含除包材外的任意材料间因组装产生的间隙) 卡尺/目视 ▲面 色差/色斑 颜色需与客户要求相同,色差,色斑不允许距灯表面 30cm 仰角30度观察可见卡尺/目视 ▲包装点 气泡/油污 A 面 点条状≤2m ㎡ 且≤3pcs B 面 点条状≤2m ㎡ 且≤3pcsC 面 点条状≤3m ㎡ 且≤5pcs或距油污表面45cm 处观察不可见目视 ▲线 皱折 A 面 10m ㎡ ≤1条 B 面 10m ㎡ ≤1条 C 面 30m ㎡ ≤2条或距皱折表面45cm 处观察不可见 目视 ▲切割偏斜 切割或因破损组合后皆应≤2mm目视 ▲ 面印刷不良印刷位置偏移≤2mm或距印刷表面45cm 处观察无异样 目视 ▲。
首件检验管理规定

首件检验管理规定文件管理序列号:[K8UY-K9IO69-O6M243-OL889-F88688]首件检验管理制度一、目地:为规范首件作业流程,避免因未做首件出现盲目生产造成批量性质量问题,特制订本管理规定二、范围:本公司各车间制造过程,均应进行首件检验。
三、定义:首件检验:是指产品在批量生产之前,或因生产过程中设备、人员等影响产品生产的因素有较大变化时,应对产品所用原材料和所生产出的产品重新进行全方位的检查确认;首件品指的是量产前面第一或前几件产品。
四、检验时机:1. 产品连续批量生产前;2. 设备模具更换或设备模具损坏维修好以及优化改进后;3. 工程变更产品首次生产时;4. 批量生产后中途转做其它产品,重新开始生产时;五、检验流程:1. 操作工按照生产计划单依据工艺技术标准要求进行自检;2. 操作工判定生产制作的产品首件符合要求时,填写自检数据并签名,并将首件交互检人员进行确认,互检人员确认合格后签名。
3. 由班组长对首件进行确认;3. 操作工将该首件提交QC(过程检验员)进行确认.4. QC(过程检验员)依据依据工艺卡片、图纸等技术标准进行全面检查确认,并对检验的结果作出判定。
如判定不合格,应向相应的操作工提出,并要求改善,重新制作首件,直至判定为合格为止,方可以进行量产。
5. 检验人员对首件判定不合格但属于设计问题或生产加工单位暂时无法改善的问题时.由生产车间通知部门主管、品质主管、技术中心进行裁决,必要时通知其他有关部门人员一起进行判定评审,判定合格或临时放行才能进行大批量生产。
六、 首件合格品处理方式:首件合格样品均由过程检验员放置在过程检验遏制区,并由过程检验员进行钢印标识,待本工序完工后与剩余相同规格的半成品一起流入下道。
七、 责任划分:1. 对于所有检验项目以检验指导书、工艺卡片及图纸等技术标准为准,检验必须认真对照技术标准确认,不能漏检项目或在不确认是否合格的情况下盲目签字确认。
34.首件(样品)检验规定

1. 目的:为确保生产品质,避免出现批量性品质问题,特制订本规定。
2. 适用范围:本公司首件(样品)检验,均依本规章执行。
3. 职责:(1)总经理室负责本规定的制定、修改和废止的起草工作。
(2) 总经理室负责本规定的制定、修改和废止的核准。
(3) 品质部负责本规定的贯彻执行。
4. 作业规定4.1. 首件检验的定义本规定所称的首件是指采购、委外加工或内部生产的首件产品,经自我调试确认,判定合乎要求后,拟进行批量生产前的第一只产品(半成品、成品)。
4.2. 首件检验的时机(1)新产品第一次量产前的收件产品。
(2)老产品新模或新工艺投入生产时的首件产品。
(3)非常规或特殊订单开始生产的首件产品。
4.3. 新产品首件检验(1).制造单位依工艺流程加工或调试,并自行自检。
(2).制造单位认定生产的产品合乎要求时,将该首件交检验员进一步检验。
(3).检验人员依据检验文件、规范,对首件进行全面的检查,如判定不合格,应向制造单位提出,并要求改善,直到判定合格为止。
(4).检验人员判定合格,或判定不合格但属设计问题或制造单位无法改善的问题时,由检验人员填写“首件(样品)检验报告”,呈品质经理审核。
(5).经品质经理审核的“首件(样品)检验报告”及首件产品由检验员直接送往技术部门,交具体开发该产品的技术人员检验。
(6).技术部技术人员经检验后,做出合格与不合格的判定,并填入“首件(样品)报告”中。
(7). 技术部、品质部均判定合格后,“首件(样品)检验报告”一联由品质部保留,一联由技术部保留,一联转生产单位(供应单位),首件检验合格后生产单位(供应单位)方可正式量产。
(8).技术部、品质部判定不合格时,如属制造单位原因时,应由制造单位改善,调试指导合格为止。
如属设计原因时,应停止生产,由技术部负责拟出对策加以改善后,方可恢复生产,并需重新首件确认。
(9).品质部应新产品量产开始后,依规定随机抽样,就未进行检验的项目实施检验,发现问题应及时反馈对策。
9首件检验管理办法
首件检验管理办法
1主题内容与适用范围
1.1本办法规定了首件检查管理办法。
1.2本办法适合于加工首件检验。
2首件检查
在加工生产过程中,具有下列情况之一,必须进首件检查。
2.1每台每班机床工作者,加工完第一个产品零件一道工序时,必须停车送检。
2.2变更工序或变换加工零件时。
2.3变换机床设备或操作工人时。
2.4改变工艺方法或更换工装时,都必须进行首件检查。
3首件检查要求
3.1首件检查必须按图纸工艺和有关技术文件,要认真进行质量检查。
在确认首件合格后,检查人员注(或打上)标记,方可进行成批生产。
3.2在加工过程中一旦发现首件检查出现问题“不合格”,出现质量问题时,检查人员必须填写首件检查质量问题报告单,可借用《工料废品通知单》但必须注明“首件”字样说明原因。
3.3不打“首件”检查,不能进行生产加工、所加工件不予检查、不予记录计件工资。
4检查与考核
4.1本办法由技术质量计量检验办归口管理与考核检查。
26。
首件检验作业规定
1.目的﹕確保投入生產之產品符合品質要求﹐生產運作暢通。
2.範圍﹕各生產工站均屬之。
3.定義﹕3.1生產制作首件,首件檢驗作業可由員工代表干部執行,在班長確認之前所生產的產品需區隔。
員工資格能力經品保認OK并具備QC資格証后,方可代替干部確認首件。
生產班長如確認不了時需找品保IPQC巡檢確認﹐首件數量最少5PCS。
鐵芯穿線﹕確認材料﹑圈數等打長結﹕確認材料﹑機器參數等組立繞線﹕確認材料﹑第一腳位﹑極性反等灌膠/切腳﹕確認材料﹑調膠比例﹑使用年限﹑端子規格﹑面板規格﹑烘烤條件等鍍錫﹕確認材料﹑溫度﹑時間﹑吃錫狀況等自動化/整腳﹕確認外觀尺寸﹑外觀不良﹑平整度﹑外殼受損等排板﹕確認材料﹑第一腳位﹑端子松緊度等沖料片﹕確認沖切模具﹑料片規格﹑彎角度等印字/烘烤﹕確認材料﹑調膠比例﹑產品型號﹑周期﹑第一腳位﹑烘烤條件等SMT:確認材料﹑元件位置﹑短路﹑AIR溫度等本體組裝﹕確認本體型號﹑膠殼規格﹑組裝位置等扣鐵殼/自檢﹕確認材料﹑型號等貼標簽﹕確認材料﹑產品型號﹑標簽排板方式等包裝﹕確認包材規格﹑包裝方式﹑標示等裝燈﹕確認材料﹑LED燈位置﹑方向等切燈﹕確認材料﹑燈規格等GXP切腳﹕確認儀器設備﹑面板規格﹑端子規格等激光打標﹕確認型號﹑位置等(線上需有不良樣品與良品樣品做比對)MD沖切﹕確認尺寸﹑模具﹑產品規格等4.權責﹕生產負責首件制作。
品保負責生產不能確認之首件確認。
工程協助首件制作(新產品)。
5.作業內容﹕℃5.1 首件制作條件﹕正常量產﹑換人作業﹑換線作業﹑換模具﹑換參數﹑換冶具﹑開機作業﹑新產品上線﹑工程變更﹑切換機種﹑Air reflow溫度設定﹑模具維修時生產必須做首件,首件OK時不需保留樣品﹐NG時樣品生產線至少保留一天后才能報廢處理(換人作業不適用與外觀站)。
5.2 檢驗方式﹕首件由生產單位全檢﹐品保做抽檢。
5.3 制程核對及首件確認5.3.1 SMT站別﹕5.3.1.1 產線依貼片圖位置進行制作首件同時依SMT半成品外觀檢驗標准檢驗項目確認首件無誤后﹐交品保進行確認《IPQC制程巡回檢查表》。
首检三检管理规定
1.0目的和范围:为了使首件三检作业规范化,预防生产过程中不良品的发生,从而更好地控制生产过程中的产品品质。
特制定本规定。
2.0定义:①自检:指操作员对首件半成品(或成品)按照工艺标准规定进行尺寸、重量、外观等方面的检验。
②互检:指车间生产的组长、科长对操作员已经检验过的首件半成品(或成品)按照工艺标准规定对尺寸、重量、外观等方面进行的再次检验。
③专检:指现场IPQC对经过操作员、组长、主管检验的首件半成品(或成品)按照工艺标准规定及其质量检验标准对尺寸、重量、外观等进行全面的检验。
④正常动作条件:机器设备参数符合工艺规定,机器动动作无异常。
3.0相关文件和资料:《生产工艺标准》《品质控制计划》《生产作业指导书》实物样品和其他辅助三阶文件4.0职责:操作员:机器在正常动作条件下,对首件进行自检。
生产组长:机器在正常动作条件下,对首件进行互检。
IPQC:机器在正常动作条件下,对首件进行专检。
生产主管、IPQC组长:定时抽检首检情况,并须有书面记载。
品质经理/主管、生产总监/经理、研发总工:随机性地对首检状况进行抽查。
5.1 程序:5.2 首检时机:①开机时;②换材料(换型号)时;③修机(换模)后;④调整设备参数后;⑤突发性停电,恢复用电开机时;⑥人员调换时。
5.3 作业细则:5. 2.1操作员、生产组长、生产主管及现场IPQC确认设备是否正常运作(若否,应通知工程部及其它相关人员进行调整)确认机器正常运作后,方可开始首件三检作业。
6. 2.2操作员据《生产作业指导书》《生产工艺》进行首件生产,取5~10pcs不等(根据实际需要)按照工艺标准对首件半成品(或成品)尺寸、重量、外观等进行测量,确认合格后,转交生产组长进行互检。
并在《首件三检记录表》相关栏目中填写相关记录。
7. 2.3生产组长或主管接到操作员转交的首件,必须重新确认机器设备运作是否正常,且按照工艺标准做进一步的尺寸、重量、外观等确认,并在《首件三检记录表》指定的位置签名,同时把首件送检现场IPQC做专检。
首件检验规定
1、目的为使本公司产品质量得到有效控制,防止批量质量事故的发生和报废品的产生,提高产品合格率,特制定本规定。
2适用范围本规定适用于所有产品的首件检验。
3 定义3.1 首件检验:指对生产开始时和工序要素变化后的首件产品质量进行的检验。
3.2 自检:指由操作者对自己所生产的产品,按照图纸工艺或相应的技术标准进行的检验。
4职责4.1 生产车间操作者负责首件产品的自检工作。
4.2 班组长负责首件产品的确认。
5、首件检验的条件凡是符合下列条件之一的,在第一件产品加工完成后,均必须经过操作者自检,班组长确定合格后方可继续加工后续产品。
5.1 产品开始加工,且加工产品有3件以上的;5.2 生产中更换操作者的;5.3 更换或调整工艺装备、生产设备的;5.4 加工工艺参数或材料批次作了更换的。
6 首件检验流程图(见附件)7 首件检验不合格的处理首件检验如出现不合格,操作者应及时查明原因,必要时班组长、技术质量人员应积极协助操作者分析原因,采取纠正措施,重新进行首件加工,检验合格后方可进行批量生产。
8 首件标识对检验合格的首件产品,由操作者连同首件检验记录放在产品首件区,待该批产品生产完工,检验合格转工序时,一同随该批转入下道工序。
9 首件检验的记录首先由操作者将首件自检合格的产品,交班组长检验,检验合格后班组长如实将检查结果记录在《首件检查记录表》上并签名确认,留下一联存档,剩余联返回操作者作为进行批生产的依据。
当检查结果为不合格,应及时与操作者进行沟通,必要时双方共同对首件进行再确认,达成意见统一。
若意见不能统一时,应提交检验组长判定。
10流程图编制:批准:。
- 1、下载文档前请自行甄别文档内容的完整性,平台不提供额外的编辑、内容补充、找答案等附加服务。
- 2、"仅部分预览"的文档,不可在线预览部分如存在完整性等问题,可反馈申请退款(可完整预览的文档不适用该条件!)。
- 3、如文档侵犯您的权益,请联系客服反馈,我们会尽快为您处理(人工客服工作时间:9:00-18:30)。
首件检验规定
Document number:WTWYT-WYWY-BTGTT-YTTYU-2018GT
首件检验规定
1目的
规范和管理品质检验工作,防止不合格品在生产过程中使用,确保总装产品质量。
2适用范围
适用于本公司生产质量管理工作首件检测活动。
3术语
检验:通过观察和判断,适当时结合测量、试验所进行的符合性评价;
质量检验:就是对产品的一个或多个质量特性进行观察、测量、试验,并将结果和规定的质量要求进行比较,以确定每项质量特性合格情况的技术性检查活动;
不合格:未满足要求.
4职责
品管部是检验和试验的归口管理部门,负责对程序的监督和管理;
工艺技术部负责提供产品检验和试验所需的产品图样及设计文件、技术标准等技术资料;品管部负责组织编制首件检验和试验规范或检验作业指导书;负责对检验数据的记录和保存,定期进行数据分析并形成报表,并对产品质量问题进行反馈,责成供货方进行整改;生产单位负责生产物料的接收、确认和报检,作好状态标识,以及将首件样品交品质部确认并填写(首件质量确认报告)表。
检验人员负责对生单位送检之产品的检测、判定、隔离和标识;
品管部主管负责部分重要零部件的检验和试验;
5补充说明
生产用物料接收和检验通知
物料从仓库料出后,由生产组长依生产计划单对所到物料的名称、规格、数量和生产产品型号规格等进行确认;
如果所生产的物料为客户要求试做样品,生产组长需在样品及《生产计划单》上注明“样品”标识。
新样品由工艺技术部进行测试,品管部协助。
如物料为客户加急订单,生产组长应在《首件质量报告》表上注明为“加急订单”,并及时向相关部门报检;
物料报检应在领料后的半个小时内完成。
物料检验
检验责任部门在收到首件检验通知后,区分是否为急需用料,如是急料,应在接到通知的第一时间内安排检验,并将检验结果及时告知生产部和品管部。
如不能及时完成,应立刻与工艺技术部和生产部协商解决。
检验员收到送检通知后,依据对应的图纸及检验指导书规定的检验内容逐项检验。
对有经确认检验样品的零部件,需参照样品的质量水平进行对比检验。
无检测手段的可采用上机测试的方法进行验证;
每种物料检验的抽样比例按《物料检验抽样规范》中的规定执行,无抽样比例的与品管部门协商决定;
一般物料检验部门应按报检先后顺序进行检验,原则上在接到《首件检验通知单》的半个小时内完成。
检验完毕后,检验人员应及时填写检验记录并存档;
各部门检验后的记录应及时交由品管部存档和统计分析;将填写好的《首件检验通知单》过程质量管理看板上。
不合格品处置
对检验过程中发现的不合格品,检验人员和及时做出隔离、标识,避免混用;检验人员判定不合格的零件,在检验完成后应及时向品管部报告并提供相关检验报告或数据;
经测试检验,判定为不合格的物料,原则上退货回仓库;品质部通知相关责任部门进行整改。
适当时,品管部经理会同工艺技术部、生产车间及研发中心等部门的相关人员对不合格品进行评审,决定其处置方式:
a.返工、返修(须再次检验确认);
b.让步接收;
c.选用(从批量不良品中挑选出合格品);
d.退货给相关部门整改。
E.如属加急订单,在品质人员确认对产品性能没有影响情况下可以特殊生产,生产过程中增加之成本从相关物料供应商货款中扣除。
6.作业流程
(见附表)
此规定自总经办签字批准之日起实施,请相关部门积极配合。
编制:杨文栋审核:批准:
首件检验流程。