消失模铸造工艺规程
消失模铸造工艺流程介绍
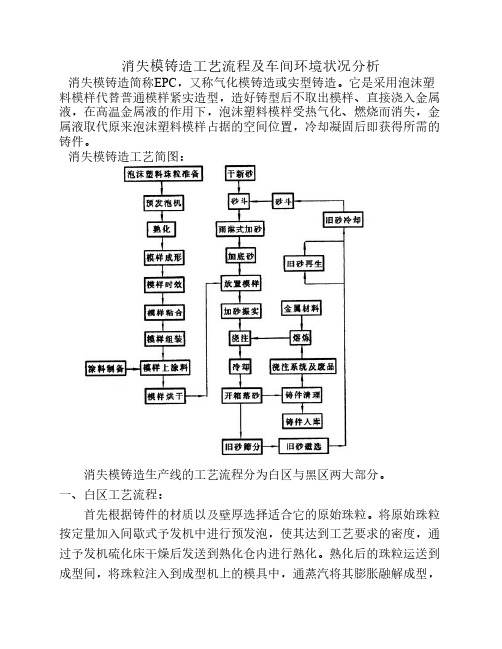
消失模铸造工艺流程及车间环境状况分析消失模铸造简称EPC,又称气化模铸造或实型铸造。
它是采用泡沫塑料模样代替普通模样紧实造型,造好铸型后不取出模样、直接浇入金属液,在高温金属液的作用下,泡沫塑料模样受热气化、燃烧而消失,金属液取代原来泡沫塑料模样占据的空间位置,冷却凝固后即获得所需的铸件。
消失模铸造工艺简图:消失模铸造生产线的工艺流程分为白区与黑区两大部分。
一、白区工艺流程:首先根据铸件的材质以及壁厚选择适合它的原始珠粒。
将原始珠粒按定量加入间歇式予发机中进行预发泡,使其达到工艺要求的密度,通过予发机硫化床干燥后发送到熟化仓内进行熟化。
熟化后的珠粒运送到成型间,将珠粒注入到成型机上的模具中,通蒸汽将其膨胀融解成型,形成铸件模样,通冷水进行冷却降温,使白模具有一样的强度,这时成型机起模人工取出白模放到白模烘干车上,运输至热风隧道通过式烘干室进行烘干。
白模烘干车在烘干室轨道上行走,每推进室内一车,在另一端顶出一车,以此循环。
烘干室采用热风强制循环系统,烘干室内的温度及湿度通过PLC自动控制达到工艺要求,大大提高了生产效率,并节约能源。
白模烘干后运输到组模间组装、粘结浇冒口。
组装好的白模运输至一次涂料间浸刷涂料,不同材质的铸件选择不同的涂料配方,将原材料放入涂料搅拌机中进行搅拌,达到工艺要求时间后测试涂料密度,经测试合格后再放入涂料槽中供工人使用。
将浸刷好的白模放到烘干车上运输至黄模一次烘干室进行烘干,烘干后的黄模运输到二次涂料间进行二次浸刷涂料,达到工艺要求的涂层厚度,再运输至黄模二次烘干室进行烘干、修补。
经过二次烘干后的黄模用烘干车运输到黑区造型工部进行填箱、造型,烘干车空车返回成型间。
至此白区工艺流程全部结束。
二、黑区工艺流程:1、造型工部:造型工部由两条造型线和一条回箱线组成,砂箱的循环运行是由砂箱轨道、手动变轨车来完成,每一条生产线由工艺要求的砂箱数量组成。
每一条造型线由一台2吨单维振实台,两台4吨变频三维振实台组成。
消失模铸造浇铸工艺规程
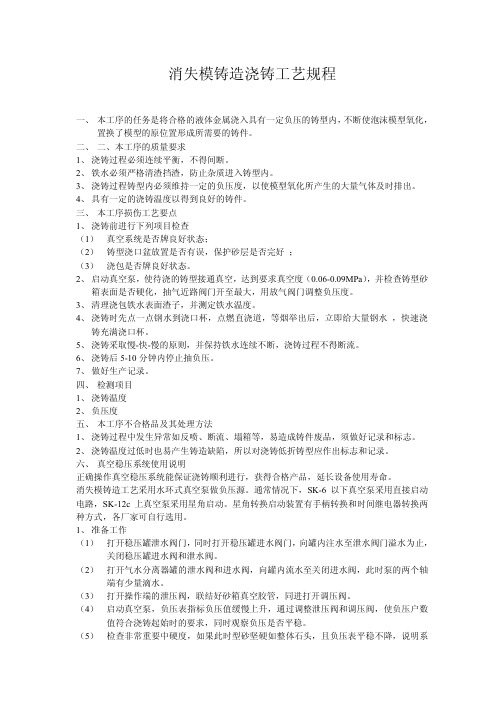
消失模铸安全操作规程(3篇)

第1篇一、目的为确保消失模铸造作业的安全,防止事故发生,保障员工生命财产安全,特制定本规程。
二、适用范围本规程适用于所有从事消失模铸造作业的员工及相关部门。
三、安全操作要求1.人员要求(1)操作人员必须经过专业培训,取得相关操作资格证书。
(2)操作人员应熟悉消失模铸造设备、工艺流程和安全操作规程。
(3)操作人员应具备良好的职业道德和责任心。
2.设备要求(1)消失模铸造设备应定期检查、维护,确保设备安全运行。
(2)设备操作人员应严格按照设备操作规程进行操作。
3.工艺要求(1)严格按照消失模铸造工艺进行操作,确保产品质量。
(2)在操作过程中,注意观察模具、砂箱等部位,防止砂粒、模具碎片等飞溅伤人。
4.安全操作规程(1)进入作业现场,应穿戴好防护用品,如安全帽、工作服、手套、防护眼镜等。
(2)操作消失模铸造设备前,应检查设备各部位是否正常,确认设备安全后,方可开始操作。
(3)操作过程中,严禁酒后作业、疲劳作业。
(4)操作人员不得擅自离开工作岗位,确保生产安全。
(5)发现设备故障或异常情况,应立即停止操作,报告相关部门进行处理。
(6)吊装模具、砂箱等重物时,必须使用专用吊具,严格按照吊装规程进行操作。
(7)吊装过程中,严禁超载、斜拉、乱拖。
(8)操作人员不得在设备周围堆放杂物,保持通道畅通。
(9)操作过程中,注意观察周围环境,防止发生碰撞、挤压等事故。
(10)操作完成后,应及时清理现场,关闭设备,确保安全。
四、应急处置1.发生火灾时,立即切断电源,使用灭火器灭火,并迅速报警。
2.发生触电事故时,立即切断电源,使用绝缘材料进行救援,并迅速报警。
3.发生机械伤害事故时,立即停止操作,采取措施隔离设备,报告相关部门进行处理。
4.发生中毒、窒息事故时,立即将伤者移至通风良好处,进行急救,并迅速报警。
五、监督检查1.生产部门应定期对消失模铸造作业进行安全检查,发现问题及时整改。
2.安全管理部门应加强对消失模铸造作业的监督检查,确保安全操作规程的落实。
消失模铸造工艺流程(附图)
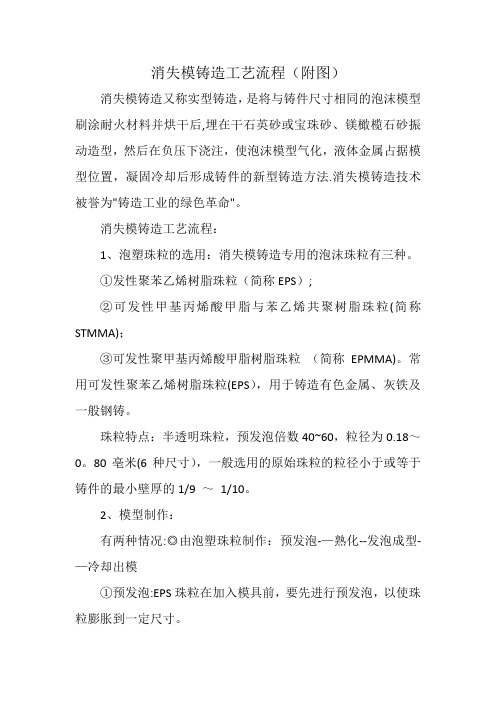
消失模铸造工艺流程(附图)消失模铸造又称实型铸造,是将与铸件尺寸相同的泡沫模型刷涂耐火材料并烘干后,埋在干石英砂或宝珠砂、镁橄榄石砂振动造型,然后在负压下浇注,使泡沫模型气化,液体金属占据模型位置,凝固冷却后形成铸件的新型铸造方法.消失模铸造技术被誉为"铸造工业的绿色革命"。
消失模铸造工艺流程:1、泡塑珠粒的选用:消失模铸造专用的泡沫珠粒有三种。
①发性聚苯乙烯树脂珠粒(简称EPS);②可发性甲基丙烯酸甲脂与苯乙烯共聚树脂珠粒(简称STMMA);③可发性聚甲基丙烯酸甲脂树脂珠粒(简称EPMMA)。
常用可发性聚苯乙烯树脂珠粒(EPS),用于铸造有色金属、灰铁及一般钢铸。
珠粒特点:半透明珠粒,预发泡倍数40~60,粒径为0.18~0。
80亳米(6种尺寸),一般选用的原始珠粒的粒径小于或等于铸件的最小壁厚的1/9 ~1/10。
2、模型制作:有两种情况:◎由泡塑珠粒制作:预发泡-—熟化--发泡成型-—冷却出模①预发泡:EPS珠粒在加入模具前,要先进行预发泡,以使珠粒膨胀到一定尺寸。
预发泡过程决定了模型的密度、尺寸稳定性及精度,是关键环节之一。
适用于EPS珠粒予发泡的方法有三种:热水预发泡、蒸汽预发泡和真空预发泡。
真空预发泡的珠粒发泡率高,珠粒干燥,应用较多。
②熟化:经预发泡的EPS珠粒放置在干燥、通风的料仓中一定时间。
以便使珠粒泡孔内外界压力平衡,使珠粒具有弹性和再膨胀能力,除去珠粒表面的水分。
熟化时间在8~48小时.③发泡成型:将预发泡且熟化的EPS珠粒填充到金属模具的型腔内,加热,使珠粒再次膨胀,填满珠粒间的空隙,并使珠粒间相互融合,形成平滑表面,即模型。
出模前必须进行冷却,使模型降温至软化温度以下,模型硬化定形后,才能出模。
出模后还应有模型干燥及尺寸稳定的时间。
设备有蒸缸及自动成形的成型机两种。
◎由泡塑板材制作:泡塑板材——电阻丝切割——粘结——模型.对简单模型,可利用电阻丝切割装置,将泡塑板材切割成所需的模型.对复杂模型,首先用电阻丝切割装置,将模型分割成几个部分,然后进行粘,使之成为整体模型。
消失模铸安全操作规程
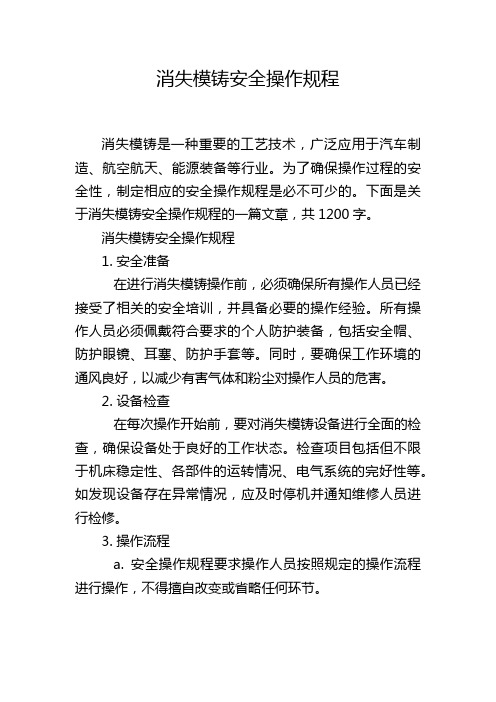
消失模铸安全操作规程消失模铸是一种重要的工艺技术,广泛应用于汽车制造、航空航天、能源装备等行业。
为了确保操作过程的安全性,制定相应的安全操作规程是必不可少的。
下面是关于消失模铸安全操作规程的一篇文章,共1200字。
消失模铸安全操作规程1. 安全准备在进行消失模铸操作前,必须确保所有操作人员已经接受了相关的安全培训,并具备必要的操作经验。
所有操作人员必须佩戴符合要求的个人防护装备,包括安全帽、防护眼镜、耳塞、防护手套等。
同时,要确保工作环境的通风良好,以减少有害气体和粉尘对操作人员的危害。
2. 设备检查在每次操作开始前,要对消失模铸设备进行全面的检查,确保设备处于良好的工作状态。
检查项目包括但不限于机床稳定性、各部件的运转情况、电气系统的完好性等。
如发现设备存在异常情况,应及时停机并通知维修人员进行检修。
3. 操作流程a. 安全操作规程要求操作人员按照规定的操作流程进行操作,不得擅自改变或省略任何环节。
b. 操作人员必须严格按照消失模铸的工艺要求进行操作,包括熔炼材料的配比、炉温控制、铸模和脱模过程等。
c. 在操作过程中,操作人员必须保持专注,并注意观察设备的运转情况,如发现异常现象应及时采取措施处理,避免事故发生。
d. 操作人员必须正确使用各类工具和设备,切勿将工具用于非正常的用途。
e. 在操作完成后,操作人员必须及时清理工作现场,确保整洁和安全。
4. 物料储存消失模铸过程中使用的物料(如熔剂、模具材料等)必须储存在专门的储存区域,并按照相应的规定进行分类、标记和包装。
储存区域应具备良好的通风条件和防火设施,以确保物料的安全性。
5. 废料处理操作过程中产生的废料必须按照环保法律法规的要求进行处理,不得随意倾倒或排放。
操作人员应按照规定的程序对废料进行分类、储存和送往指定的处理场所。
6. 紧急情况处置在发生紧急情况(如火灾、设备故障等)时,操作人员要迅速采取措施,包括立即停止设备运转、报警、启动紧急排除措施等。
消失模铸造流程图
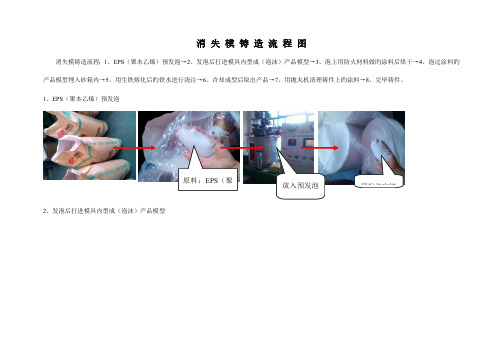
消失模铸造流程图
消失模铸造流程:1、EPS(聚本乙烯)预发泡→2、发泡后打进模具内型成(泡沫)产品模型→3、泡上用防火材料做旳涂料后烘干→4、泡过涂料旳产品模型埋入砂箱内→5、用生铁熔化后旳铁水进行浇注→6、冷却成型后取出产品→7、用抛丸机清理铸件上旳涂料→8、完毕铸件。
1、EPS(聚本乙烯)预发泡
2、发泡后打进模具内型成(泡沫)产品模型
3
、泡上用防火材料做旳涂料后烘干
4、泡过涂料旳产品模型埋入砂箱内5
、用生铁熔化后旳铁水浇入模型内
6
、冷却成型后取出产品
铸件
砂子
7、用抛丸机清理铸件上旳涂料
8、完毕铸件。
消失模铸造浇铸工艺规程
消失模铸造浇铸工艺规程一、本工序的任务是将合格的液体金属浇入具有一定负压的铸型内,不断使泡沫模型氧化,置换了模型的原位置形成所需要的铸件。
二、二、本工序的质量要求1、浇铸过程必须连续平衡,不得间断。
2、铁水必须严格清渣挡渣,防止杂质进入铸型内。
3、浇铸过程铸型内必须维持一定的负压度,以使模型氧化所产生的大量气体及时排出。
4、具有一定的浇铸温度以得到良好的铸件。
三、本工序损伤工艺要点1、浇铸前进行下列项目检查(1) 真空系统是否牌良好状态;(2) 铸型浇口盆放置是否有误,保护砂层是否完好 ;(3) 浇包是否牌良好状态。
2、启动真空泵,使待浇的铸型接通真空,达到要求真空度(0.06-0.09MPa),并检查铸型砂箱表面是否硬化,抽气近路阀门开至最大,用放气阀门调整负压度。
3、清理浇包铁水表面渣子,并测定铁水温度。
4、浇铸时先点一点钢水到浇口杯,点燃直浇道,等烟举出后,立即给大量钢水,快速浇铸充满浇口杯。
5、浇铸采取慢-快-慢的原则,并保持铁水连续不断,浇铸过程不得断流。
6、浇铸后5-10分钟内停止抽负压。
7、做好生产记录。
四、检测项目1、浇铸温度2、负压度五、本工序不合格品及其处理方法1、浇铸过程中发生异常如反喷、断流、塌箱等,易造成铸件废品,须做好记录和标志。
2、浇铸温度过低时也易产生铸造缺陷,所以对浇铸低折铸型应作出标志和记录。
六、真空稳压系统使用说明正确操作真空稳压系统能保证浇铸顺利进行,获得合格产品,延长设备使用寿命。
消失模铸造工艺采用水环式真空泵做负压源。
通常情况下,SK-6以下真空泵采用直接启动电路,SK-12c上真空泵采用星角启动。
星角转换启动装置有手柄转换和时间继电器转换两种方式,各厂家可自行选用。
1、准备工作(1) 打开稳压罐泄水阀门,同时打开稳压罐进水阀门,向罐内注水至泄水阀门溢水为止,关闭稳压罐进水阀和泄水阀。
(2) 打开气水分离器罐的泄水阀和进水阀,向罐内流水至关闭进水阀,此时泵的两个轴端有少量滴水。
消失模铸造工艺规程
消失模铸造工艺规程(初稿)1、消失模铸造工艺流程:2、国产可发性EPS珠粒的技术指标:2.1 发泡剂质量分数6.0~8%,使用时最低不低于5.5%。
2.2 剩余苯乙烯单体质量分数含量不大于0.1%2.3 相对分子量在18万~27万。
2.4 含水量小于0.5%(体积分数)。
2.5 密度1.03g/cm3,表观密度0.6 g/cm32.6 根据铸铁件最小壁厚选取EPS粒度,具体铸铁件选取规格如下:2.7 EPS珠粒粒度应均匀,每一粒径范围的过筛率不小于90%。
2.8 EPS珠粒应按使用量、质保期分批做好标识,低温铁桶密封储存,最好冷藏(-12~-10℃),确保使用时发泡剂含量符合工艺要求。
3.3、铸造用泡沫塑料的规格型号:8Zkb-18,密度0.015~0.020g/cm3,EPS珠粒筛号10~16,板材,物理性能符合标准要求。
4、预发泡使用间隙式蒸汽预发机完成EPS珠粒预发。
4.1 按设备操作工艺规程点检设备,在设备逐项性能良好的前提下启动。
4.2 核对EPS珠粒的生产批号、存放时间、发泡剂含量、粒度等指标是否符合工艺要求。
EPS珠粒应于使用时开封,同时取样检验。
检验项目包括:表观密度、水分、粒度、发泡剂含量。
对已经开封的要依据开封时间核对是否超过规定的存放时间或检验其发泡剂含量。
4.3 严禁使用超过质保期或发泡剂含量小于5.5%的EPS珠粒。
4.4 控制温度95~105℃,压力0.01~0.04MPa, 时间60~120S。
4.5 预发泡后的珠粒,装入熟化框,转入熟化工序。
在熟化框标识卡上做好预发完成时间、数量等记录。
5、预发珠粒的熟化5.1 对预发后的珠粒,应测量其堆积密度及水分,一般堆积密度0.016~0.022g/cm3,水分2%以下。
5.2 参照下表确定预发珠粒的熟化时间:5.3 熟化合格的珠粒,应干燥、有弹性。
化验残存发泡剂含量>3.5%。
在熟化框标识卡上做好熟化完成时间、数量及残存发泡剂含量等记录。
消失模铸安全操作规程
消失模铸安全操作规程1. 引言本文档旨在详细介绍消失模铸安全操作规程,以确保操作人员和周围人员在使用消失模铸造工艺时的安全。
2. 作业前准备在进行消失模铸造操作之前,请进行以下准备工作:•检查消失模铸造设备,确保设备正常工作,并遵循设备操作手册;•准备好所需的消失模铸造材料和工具,并确保其处于可靠的状态;•了解工作区域内的安全设施和应急出口位置;•穿戴个人防护装备,包括安全帽、护目镜、耳塞、防护服等。
3. 工作区域安排•工作区域应保持整洁有序,避免障碍物妨碍操作;•规定好高温区域和非高温区域,并设置明显的警示标志;•安装有效的通风系统,确保有足够的空气流通;•将火源和易燃物品与消失模铸造操作区域相隔离。
4. 操作步骤4.1 模具制备•检查模具材料是否符合要求,无裂纹或其他缺陷;•遵循规范进行模具制备,确保模具尺寸和形状正确;•在操作过程中遵循消失模铸造工艺操作指南。
4.2 材料配制•按照工艺要求配制熔融金属,如铝、铜等;•在进行配制时,遵循正确的比例和操作步骤;•注意金属熔点和操作温度,以防止烫伤或火灾发生。
4.3 注浆和脱模•将熔融金属缓慢注入模具中,防止气泡和溅溴;•注浆过程中要保持稳定姿势和操作手法,以防止金属烫伤;•完成注浆后,等待足够时间进行冷却和固化;•进行脱模操作时,小心谨慎,避免损坏模具和受伤。
4.4 清理和维护•操作完成后,及时清理工作区域,将废料和垃圾妥善处理;•维护和保养消失模铸造设备,定期检查和维修;•存放和处理有害废弃物时,严格按照环境保护要求操作。
5. 安全注意事项•禁止非授权人员进入工作区域;•在操作过程中,严禁戏谑、抛弄等危险行为;•在高温区域工作时,必须穿戴防护服和隔热手套;•在操作金属熔融时,严禁使用潮湿的工具或容器;•定期参加相关安全培训,了解最新的安全操作规程。
6. 应急处理•在发生火灾或其他紧急事故时,立即按照应急预案行动;•熟悉应急出口位置,并与工作人员紧密合作;•使用消防器材扑救初期火灾,确保个人安全;•在紧急情况下,及时报警并联系相关救援机构。
消失模铸造规章制度
消失模铸造规章制度一、引言消失模铸造是一种常用的金属铸造工艺,它采用消失模作为铸型,通过高温烧结消失模,然后将熔化的金属倒入模型中,待金属凝固后,取出并清除消失模即可得到所需的铸件。
为了确保消失模铸造工艺顺利进行,制定一套科学、严格的规章制度是非常必要的。
本文档旨在说明消失模铸造规章制度的具体内容,以确保生产工作的规范性和高效性。
二、安全生产规章制度1.工人操作必须佩戴合适的劳动防护用品,包括防护眼镜、防护手套、防护服等。
2.工作场所必须保持整洁,不得有杂物和易燃物。
3.烧结时必须进行有效的通风措施,保证室内空气清新。
4.操作过程中禁止吸烟、使用明火等安全隐患行为。
5.高温熔融金属时严禁接触金属液和熔融金属,必须佩戴耐高温手套。
三、设备操作规程1.操作人员必须熟悉消失模铸造设备的结构和原理,并按照要求进行操作。
2.在使用设备前,必须进行设备检查和维护,并做好相关记录。
3.运转时严禁将手指或其他物体伸入设备内部。
4.当发生设备故障时,必须立即停止操作,并及时报告维修人员进行修理。
四、消失模制作规程1.根据铸件的形状和尺寸,选择合适的消失模材料,并确保材料的质量符合要求。
2.模具制作前,必须对模具进行预处理,包括清洗、除锈等。
3.模具制作时,必须按照工艺要求进行,避免出现模具变形、开裂等问题。
4.模具制作完成后,必须进行严格的检查,确保模具的质量和尺寸精度。
五、烧结处理规程1.烧结炉的温度和时间必须根据消失模材料和铸件的要求进行调整,并记录相关参数。
2.在烧结过程中,必须定期检查炉内温度和压力,确保烧结过程的稳定性。
3.烧结后的消失模具必须进行冷却处理,以防止热变形或损坏。
六、铸造工艺规程1.确保熔炉中的金属温度符合要求,并进行必要的化验检测。
2.在铸造过程中,必须控制金属的浇注速度、温度和压力,以确保铸件的质量。
3.铸件凝固后,必须进行合适的冷却处理,以降低铸件的内应力。
七、质量控制规范1.在生产过程中,必须进行质量检验和检测,确保铸件的尺寸和表面质量符合要求。
- 1、下载文档前请自行甄别文档内容的完整性,平台不提供额外的编辑、内容补充、找答案等附加服务。
- 2、"仅部分预览"的文档,不可在线预览部分如存在完整性等问题,可反馈申请退款(可完整预览的文档不适用该条件!)。
- 3、如文档侵犯您的权益,请联系客服反馈,我们会尽快为您处理(人工客服工作时间:9:00-18:30)。
消失模铸造工艺规程(初稿)1、消失模铸造工艺流程:2、国产可发性EPS珠粒的技术指标:2.1 发泡剂质量分数6.0~8%,使用时最低不低于5.5%。
2.2 剩余苯乙烯单体质量分数含量不大于0.1%2.3 相对分子量在18万~27万。
2.4 含水量小于0.5%(体积分数)。
2.5 密度1.03g/cm3,表观密度0.6 g/cm32.6 根据铸铁件最小壁厚选取EPS粒度,具体铸铁件选取规格如下:2.7 EPS珠粒粒度应均匀,每一粒径范围的过筛率不小于90%。
2.8 EPS珠粒应按使用量、质保期分批做好标识,低温铁桶密封储存,最好冷藏(-12~-10℃),确保使用时发泡剂含量符合工艺要求。
3.3、铸造用泡沫塑料的规格型号:8Zkb-18,密度0.015~0.020g/cm3,EPS珠粒筛号10~16,板材,物理性能符合标准要求。
4、预发泡使用间隙式蒸汽预发机完成EPS珠粒预发。
4.1 按设备操作工艺规程点检设备,在设备逐项性能良好的前提下启动。
4.2 核对EPS珠粒的生产批号、存放时间、发泡剂含量、粒度等指标是否符合工艺要求。
EPS珠粒应于使用时开封,同时取样检验。
检验项目包括:表观密度、水分、粒度、发泡剂含量。
对已经开封的要依据开封时间核对是否超过规定的存放时间或检验其发泡剂含量。
4.3 严禁使用超过质保期或发泡剂含量小于5.5%的EPS珠粒。
4.4 控制温度95~105℃,压力0.01~0.04MPa, 时间60~120S。
4.5 预发泡后的珠粒,装入熟化框,转入熟化工序。
在熟化框标识卡上做好预发完成时间、数量等记录。
5、预发珠粒的熟化5.1 对预发后的珠粒,应测量其堆积密度及水分,一般堆积密度0.016~0.022g/cm3,水分2%以下。
5.2 参照下表确定预发珠粒的熟化时间:5.3 熟化合格的珠粒,应干燥、有弹性。
化验残存发泡剂含量>3.5%。
在熟化框标识卡上做好熟化完成时间、数量及残存发泡剂含量等记录。
6、模具成型6.1按成型机操作规程点检设备,在设备逐项性能良好的前提下开始工作。
6.2 清洁模具各面,检查模具闭合时定位情况及其他机械动作。
6.4 将模具闭合,并使分型面处留有小于预发泡半径的空隙。
通蒸汽预热模具至100℃。
6.5 加料:打开上下(或左右)气室出气口,用压缩空气加料器通过模具加料口把预发珠粒吹入模腔内,待预发珠粒填满整个模腔后,用加料塞子堵住加料门。
6.6 发泡成型:蒸汽通入模腔,将珠粒间的空气和冷凝水排出,聚苯乙烯在热作用下软化,发泡膨胀。
6.7 合模:通蒸汽成型发泡后,随即把模具完全闭合。
控制蒸汽温度120℃,蒸汽压0.15MPa,保持时间视模型厚度确定(一般十几秒至1分钟左右)。
使模具中的泡沫珠粒相互粘合呈致密蜂窝状结构。
6.8 冷却:关掉蒸汽,同时将冷却水(最好使用软水)通入气室并经过气孔(气塞)注入模腔内,在冷却定型模样的同时,使模具快速冷却到脱模温度,一般40~50℃。
6.9 开模与脱模:开启压机模具,同时用压缩空气或机械顶杆顶出模样。
6.10 成型后的模片置于烘干小车上,转入熟化工序。
小车的标识卡上记录有关质量信息。
6.11 严禁使用龄期超长、残余发泡剂含量不足、密度不合格的预发珠粒。
6.12使用新预发珠粒或调整充填参数后,必须测定烘干(熟化)后的模片质量,以控制模片密度在0.018~0.022g/cm3。
7、白模熟化工艺:7.1 于白模熟化区放置72小时,然后进白模烘干室烘干3小时。
7.2 快速熟化工艺:进烘干室强制烘干12小时。
7.3 烘干室温度:50~60℃,相对湿度<40%。
7.4 检查模片质量:合格模片表面及尖角处无疏松、裂纹、过热,充填口处无疏松或高密度现象。
8、组模选用聚醋酸乙烯乳液(白乳胶)做粘结剂。
8.1 粘合剂应涂刷得薄而均匀。
8.2 粘结剂涂层均匀后随即将其敞开放置数分钟至十几分钟(视气温、粘结剂的成分和特性),待溶剂大部分挥发后,即可合上两块要胶合的模片让其自然干燥。
9、涂料制备9.1 涂料配方(质量比,%):320目硅砂粉100、钠膨润土6~8、CMC0.1~0.5、粘结剂6~7、流变促进剂微量、表面活性剂微量、消泡剂微量、水适量。
9.2 涂料配制:9.2.1 膨润土按1:10加水,高速搅拌6小时,制成均匀的粘土浆。
9.2.2 CMC加水50倍使用,其他各种有机粘结剂预先配成液态。
9.2.3 在搅拌状态下的粘土浆中,徐徐加入称量的硅砂粉,CMC等附加物,加入适量水,不断高速(1380rpm)搅拌2小时以上,制成成分均匀的涂料。
9.2.4 慢速搅拌适当时间除气备用。
9.2.5 制好的涂料应放在干净的料桶内备用。
9.3 涂料性能指标:密度1.8~2.43g/cm3粘度120~150S10. 涂敷涂料10.1 涂料使用前应加水稀释至规定的密度,短时间高速搅拌再慢速搅拌除气,最好在使用过程中不断慢速搅拌。
10.2 将模型浸入涂料中(或刷涂、淋涂)一定时间后再取出来。
10.3 待涂料不往下流淌时,将30~50目高温烘烤的石英砂均匀地撒在已浸渍过涂料的模型上;10.4 挂好涂料的模型,平稳地放置在平直的架板上,防止变形;10.5 采用浸涂时,选好实型模样浸入涂料的方向、部位,防止模样变形。
10.6 涂层要均匀,模样上不得有露白现象。
10.7 通过控制涂料密度、浸涂次数和浸涂操作控制涂层厚度。
采取两次浸涂作业时,第一遍应采用密度较小的稀薄涂料,获得均匀的薄涂层;第二遍要通过调整涂料的密度获得均匀的涂料厚度。
一般控制涂料厚度0.5~1mm。
生产中使用卡板测量或称量涂层重量的方法控制涂层厚度。
10.5按需要对已经干燥过的模型进行二次涂挂涂料。
11. 烘干涂层11.1 对涂挂好涂料的模型进烘干室烘干,温度40~55℃,时间8~10小时。
相对湿度不大于30%。
11.2 烘干过程注意模型合理放置和支撑,防止模型变形。
11.3 烘干结束时,要检查,涂层必须干透。
一般干透的涂料,难于从模样上剥离,敲击时声音清脆。
11.4 烘干后的实型模样应放在湿度较小处,防止返潮。
造型前应再进行适当烘干。
12.造型12.1 硅砂: SiO2含量≥90%;水分﹤1%;粒度20/40目;砂粒形状为圆形、多角形;干砂灼烧减量﹤0.5%;生产过程中控制砂温﹤50℃。
12.2 密封用塑料薄膜:推荐使用厚度0.1mm12.3 造型过程:砂箱移入造型位置→加底砂→振实→放模样→加砂→振实→覆盖塑料膜→放浇口杯、冒口圈→加盖砂→砂型转浇注位置12.3.1 使用雨淋加砂器加底砂并振实,振动时间30S左右,刮平,厚度100mm左右;底砂厚度应使模样直浇口顶面与箱口平齐。
12.3.2 按浇注位置工艺要求将模样平稳放置在底砂上,注意保持模样四周吃砂量均匀。
空心直浇口用塑料薄膜包严顶面。
12.3.3 使用雨淋加砂器加砂,边加砂边振实,振动时间60~90S。
沿砂箱上口平面刮平,并用掸笔掸净直浇口顶面的浮砂。
12.3.4 覆盖塑料薄膜:薄膜应平整地覆盖住砂箱上口,且沿砂箱上口四周多出50mm左右的余边。
12.3.5 放浇口杯:浇口杯下面应平整、紧实。
放浇口杯时应使浇口杯中的浇口与模样直浇口对正,且适当用力压一下。
12.3.6 加盖砂:在砂箱顶面均匀覆盖一层厚度约15mm的干砂,加盖砂时应注意在浇口杯根部可适当加厚且不得使浇口杯中有浮砂。
12.3.7 用适当大小的硬纸板盖严浇口杯,转浇注位置。
12.4 有暗冒口铸型,核算暗冒口顶部距离砂箱上平面的吃砂量,当此吃砂量不足50mm时,应放适量压铁。
12.5 砂型硬度(紧实并抽真空后)80~90。
12.6 三维振实台振动参数:振动加速度1~2g(g为重力加速度);振动频率:50~60Hz,振幅0.5~1mm。
13. 浇注13.1 浇注温度:比普通铸造浇注温度提高20~50℃。
对铸铁箱体类铸件,浇注温度控制在1420~1450℃13.2 浇注时真空度:0.03~0.04MPa13.3 浇注前,应认真打渣,将包嘴处铁水表面的浮渣及黏附在包壁上粘渣清理干净,并在包嘴处覆盖耐热硅酸盐毡板挡渣。
13.4 浇注过程中应及时挡住铁液表面的零星浮渣。
13.5 浇注操作原则:平稳、快速。
具体:要“慢-快-慢”。
首先慢浇将直浇道点通后,立即大流快速浇,使金属充满浇口杯,封闭住直浇口。
待浇满铸型时,再放慢浇速,直到浇口杯的液面不下沉为止。
13.6 浇注的金属液一直充满浇口杯,以使直浇道处于封闭状态。
13.7 浇注一旦开始,绝不可终止断流,否则将导致浇注失败。
13.8浇注厚大铸件时,要防止浇注后从浇口杯中喷溅金属液。
14、砂处理工艺流程:液压自动翻箱机→振动输送筛分机→带式永磁分离机→斗提机→(落砂)(筛砂)(一级礠分)风选磁选机→自动加砂门→水冷沸腾冷却床→斗提机→直线振动筛→(除尘、礠分) (冷却)砂温调节器→皮带输送机1→皮带输送机2→气动雨淋加砂器(调温)(雨淋加砂)。