谈水下超大直径超长钻孔桩施工技术
超长超大直径钻孔灌注桩施工工法最终
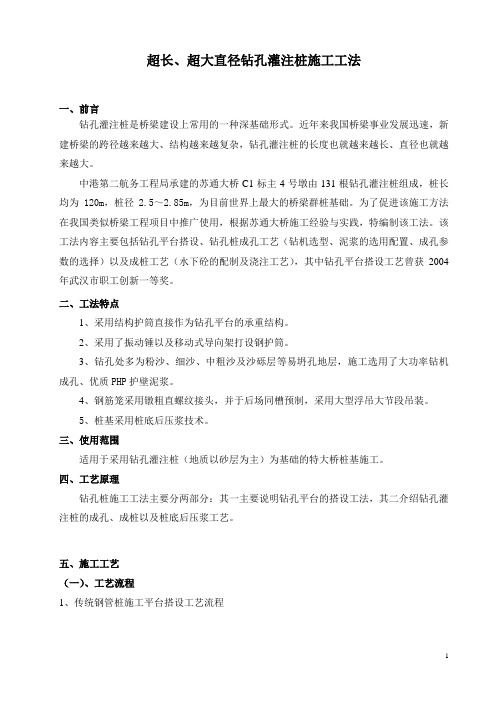
超长、超大直径钻孔灌注桩施工工法一、前言钻孔灌注桩是桥梁建设上常用的一种深基础形式。
近年来我国桥梁事业发展迅速,新建桥梁的跨径越来越大、结构越来越复杂,钻孔灌注桩的长度也就越来越长、直径也就越来越大。
中港第二航务工程局承建的苏通大桥C1标主4号墩由131根钻孔灌注桩组成,桩长均为120m,桩径2.5~2.85m,为目前世界上最大的桥梁群桩基础。
为了促进该施工方法在我国类似桥梁工程项目中推广使用,根据苏通大桥施工经验与实践,特编制该工法。
该工法内容主要包括钻孔平台搭设、钻孔桩成孔工艺(钻机选型、泥浆的选用配置、成孔参数的选择)以及成桩工艺(水下砼的配制及浇注工艺),其中钻孔平台搭设工艺曾获2004年武汉市职工创新一等奖。
二、工法特点1、采用结构护筒直接作为钻孔平台的承重结构。
2、采用了振动锤以及移动式导向架打设钢护筒。
3、钻孔处多为粉沙、细沙、中粗沙及沙砾层等易坍孔地层,施工选用了大功率钻机成孔、优质PHP护壁泥浆。
4、钢筋笼采用镦粗直螺纹接头,并于后场同槽预制,采用大型浮吊大节段吊装。
5、桩基采用桩底后压浆技术。
三、使用范围适用于采用钻孔灌注桩(地质以砂层为主)为基础的特大桥桩基施工。
四、工艺原理钻孔桩施工工法主要分两部分:其一主要说明钻孔平台的搭设工法,其二介绍钻孔灌注桩的成孔、成桩以及桩底后压浆工艺。
五、施工工艺(一)、工艺流程1、传统钢管桩施工平台搭设工艺流程图5.1 传统钢管桩施工平台搭设工艺流程2、采用钢护筒作为承重结构的钻孔平台搭设工艺流程图5.2 采用钢护筒作为承重结构的钻孔平台搭设工艺流程3、钻孔灌注桩施工工艺流程图5.3 钻孔桩施工流程图4、桩底后压浆流程图5.4 桩底后压浆施工流程图(二)、施工要点1、传统钢管桩施工平台搭设施工要点①钢管桩施工a、钢管桩制作、运输钢管桩均按设计规格拼装成整桩,按沉放顺序分批加工制作,出厂检验合格后,用驳船运输至施工现场。
b、钢管桩沉设钢管桩沉设定位采用测量定位。
深水超长大直径钻孔灌注桩施工关键技术研究
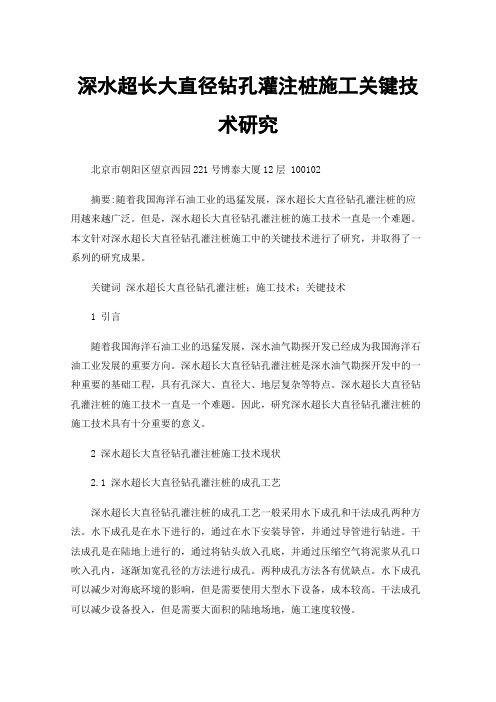
深水超长大直径钻孔灌注桩施工关键技术研究北京市朝阳区望京西园221号博泰大厦12层 100102摘要:随着我国海洋石油工业的迅猛发展,深水超长大直径钻孔灌注桩的应用越来越广泛。
但是,深水超长大直径钻孔灌注桩的施工技术一直是一个难题。
本文针对深水超长大直径钻孔灌注桩施工中的关键技术进行了研究,并取得了一系列的研究成果。
关键词深水超长大直径钻孔灌注桩;施工技术;关键技术1 引言随着我国海洋石油工业的迅猛发展,深水油气勘探开发已经成为我国海洋石油工业发展的重要方向。
深水超长大直径钻孔灌注桩是深水油气勘探开发中的一种重要的基础工程,具有孔深大、直径大、地层复杂等特点。
深水超长大直径钻孔灌注桩的施工技术一直是一个难题。
因此,研究深水超长大直径钻孔灌注桩的施工技术具有十分重要的意义。
2 深水超长大直径钻孔灌注桩施工技术现状2.1 深水超长大直径钻孔灌注桩的成孔工艺深水超长大直径钻孔灌注桩的成孔工艺一般采用水下成孔和干法成孔两种方法。
水下成孔是在水下进行的,通过在水下安装导管,并通过导管进行钻进。
干法成孔是在陆地上进行的,通过将钻头放入孔底,并通过压缩空气将泥浆从孔口吹入孔内,逐渐加宽孔径的方法进行成孔。
两种成孔方法各有优缺点。
水下成孔可以减少对海底环境的影响,但是需要使用大型水下设备,成本较高。
干法成孔可以减少设备投入,但是需要大面积的陆地场地,施工速度较慢。
2.2 深水超长大直径钻孔灌注桩的混凝土灌注工艺深水超长大直径钻孔灌注桩的混凝土灌注工艺一般采用导管法和压力灌注法两种方法。
导管法是在钻孔内插入导管,通过导管进行混凝土的灌注。
压力灌注法是在钻孔内装满混凝土后,通过向孔内注入高压水,使混凝土产生压力,从而实现混凝土的灌注。
两种方法各有优缺点。
导管法可以减少混凝土的离析和堵管现象,但是需要较长的混凝土灌注时间。
压力灌注法可以提高混凝土的灌注效率,但是需要注意控制混凝土的压力和流量。
2.3 深水超长大直径钻孔灌注桩的质量控制深水超长大直径钻孔灌注桩的质量控制是一个重要的问题。
大直径超长钻孔桩基础深水施工技术
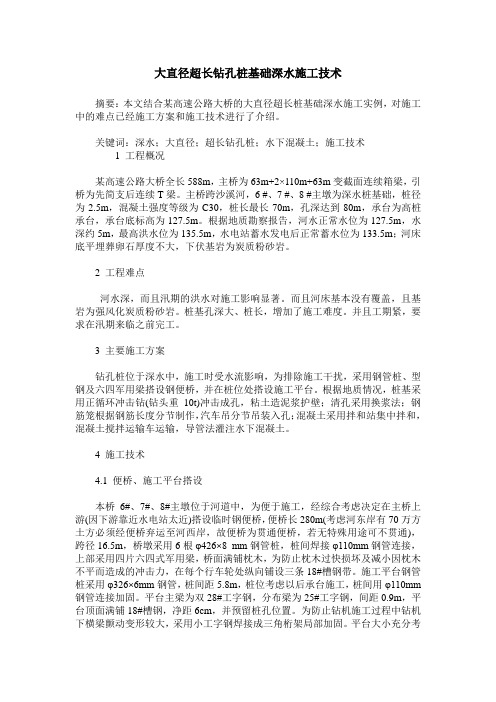
大直径超长钻孔桩基础深水施工技术摘要:本文结合某高速公路大桥的大直径超长桩基础深水施工实例,对施工中的难点已经施工方案和施工技术进行了介绍。
关键词:深水;大直径;超长钻孔桩;水下混凝土;施工技术1 工程概况某高速公路大桥全长588m,主桥为63m+2×110m+63m变截面连续箱梁,引桥为先简支后连续T梁。
主桥跨沙溪河,6 #、7 #、8 #主墩为深水桩基础,桩径为2.5m,混凝土强度等级为C30,桩长最长70m,孔深达到80m,承台为高桩承台,承台底标高为127.5m。
根据地质勘察报告,河水正常水位为127.5m,水深约5m,最高洪水位为135.5m,水电站蓄水发电后正常蓄水位为133.5m;河床底平埋葬卵石厚度不大,下伏基岩为炭质粉砂岩。
2 工程难点河水深,而且汛期的洪水对施工影响显著。
而且河床基本没有覆盖,且基岩为强风化炭质粉砂岩。
桩基孔深大、桩长,增加了施工难度。
并且工期紧,要求在汛期来临之前完工。
3 主要施工方案钻孔桩位于深水中,施工时受水流影响,为排除施工干扰,采用钢管桩、型钢及六四军用梁搭设钢便桥,并在桩位处搭设施工平台。
根据地质情况,桩基采用正循环冲击钻(钻头重10t)冲击成孔,粘土造泥浆护壁;清孔采用换浆法;钢筋笼根据钢筋长度分节制作,汽车吊分节吊装入孔;混凝土采用拌和站集中拌和,混凝土搅拌运输车运输,导管法灌注水下混凝土。
4 施工技术4.1 便桥、施工平台搭设本桥6#、7#、8#主墩位于河道中,为便于施工,经综合考虑决定在主桥上游(因下游靠近水电站太近)搭设临时钢便桥,便桥长280m(考虑河东岸有70万方土方必须经便桥弃运至河西岸,故便桥为贯通便桥,若无特殊用途可不贯通),跨径16.5m,桥墩采用6根φ426×8 mm钢管桩,桩间焊接φ110mm钢管连接,上部采用四片六四式军用梁,桥面满铺枕木,为防止枕木过快损坏及减小因枕木不平而造成的冲击力,在每个行车轮处纵向铺设三条18#槽钢带。
超长、超大直径钻孔灌注桩施工工法(最终)

超长、超大直径钻孔灌注桩施工工法一、前言钻孔灌注桩是桥梁建设上常用的一种深基础形式。
近年来我国桥梁事业发展迅速,新建桥梁的跨径越来越大、结构越来越复杂,钻孔灌注桩的长度也就越来越长、直径也就越来越大。
中港第二航务工程局承建的苏通大桥C1标主4号墩由131根钻孔灌注桩组成,桩长均为120m,桩径~2.85m,为目前世界上最大的桥梁群桩基础。
为了促进该施工方法在我国类似桥梁工程项目中推广使用,根据苏通大桥施工经验与实践,特编制该工法。
该工法内容主要包括钻孔平台搭设、钻孔桩成孔工艺(钻机选型、泥浆的选用配置、成孔参数的选择)以及成桩工艺(水下砼的配制及浇注工艺),其中钻孔平台搭设工艺曾获2004年武汉市职工创新一等奖。
二、工法特点1、采用结构护筒直接作为钻孔平台的承重结构。
2、采用了振动锤以及移动式导向架打设钢护筒。
3、钻孔处多为粉沙、细沙、中粗沙及沙砾层等易坍孔地层,施工选用了大功率钻机成孔、优质PHP护壁泥浆。
4、钢筋笼采用镦粗直螺纹接头,并于后场同槽预制,采用大型浮吊大节段吊装。
5、桩基采用桩底后压浆技术。
三、使用范围适用于采用钻孔灌注桩(地质以砂层为主)为基础的特大桥桩基施工。
四、工艺原理钻孔桩施工工法主要分两部分:其一主要说明钻孔平台的搭设工法,其二介绍钻孔灌注桩的成孔、成桩以及桩底后压浆工艺。
五、施工工艺(一)、工艺流程1、传统钢管桩施工平台搭设工艺流程图传统钢管桩施工平台搭设工艺流程2、采用钢护筒作为承重结构的钻孔平台搭设工艺流程图采用钢护筒作为承重结构的钻孔平台搭设工艺流程3、钻孔灌注桩施工工艺流程图钻孔桩施工流程图4、桩底后压浆流程施工准备注浆管安装钻孔桩砼浇筑注浆管开塞洗孔、初注控制注浆压力和注浆量,记录最大压效果检查图桩底后压浆施工流程图(二)、施工要点1、传统钢管桩施工平台搭设施工要点①钢管桩施工a、钢管桩制作、运输钢管桩均按设计规格拼装成整桩,按沉放顺序分批加工制作,出厂检验合格后,用驳船运输至施工现场。
大直径、超长钻孔灌注桩施工工法

大直径、超长钻孔灌注桩施工工法大直径、超长钻孔灌注桩施工工法一、前言大直径、超长钻孔灌注桩施工工法是一种常用于基础设施建设和土木工程中的桩基处理方法。
本文将介绍该工法的特点、适应范围、工艺原理、施工工艺、劳动组织、机具设备、质量控制、安全措施、经济技术分析以及一些实际工程实例。
二、工法特点大直径、超长钻孔灌注桩施工工法具有以下特点:1. 桩径大:桩径通常在1米以上,可以承受较大的荷载。
2. 桩长长:桩长可以超过30米,适用于地质条件复杂的场地。
3. 纵向连续:桩体在整个长度上都是连续且密实的。
4. 抗震性能好:桩体的纵向连续性和密实性可以提高桩体的抗震性能。
5. 施工周期短:与传统钢筋混凝土桩相比,施工速度更快。
三、适应范围大直径、超长钻孔灌注桩施工工法适用于以下情况:1. 荷载要求高:适用于承受大荷载的建筑物和桥梁。
2. 地质条件复杂:适用于地质条件复杂的地区,如松软土层、强风化岩层等。
3. 抗震要求高:适用于地震烈度较高的区域。
4. 空间限制:适用于空间受限的施工场地。
四、工艺原理大直径、超长钻孔灌注桩施工工法的工艺原理基于以下几点:1. 钻孔:先通过钻机进行钻孔,直径和深度根据设计要求确定。
2. 灌注:将钢筋和混凝土注入钻孔中,形成桩体。
混凝土可以通过自流或振捣灌注。
3. 后期处理:桩体灌注完成后,可以进行护壁和加固处理。
五、施工工艺大直径、超长钻孔灌注桩施工工法的施工工艺包括以下几个阶段:1. 建立施工现场:确定施工范围、布置钻机和其他机具设备。
2. 钻孔:使用钻机进行钻孔工作,根据设计要求确定钻孔的直径和深度。
3. 清洁孔底:清除孔底的杂物和泥浆,保证孔底的纯净。
4. 安装钢筋笼:将预制的钢筋笼放置在钻孔中,并进行调整和固定。
5. 灌注混凝土:使用泵车将混凝土注入钻孔中,可以采用自流或振捣灌注。
6. 护壁和加固:灌注完成后,对桩体进行护壁和加固处理,以提高桩体的强度和稳定性。
六、劳动组织大直径、超长钻孔灌注桩施工工法的劳动组织包括以下几个方面:1. 现场安全人员:负责保证施工现场的安全。
倾斜岩大直径超长深水钻孔桩施工工法(2)
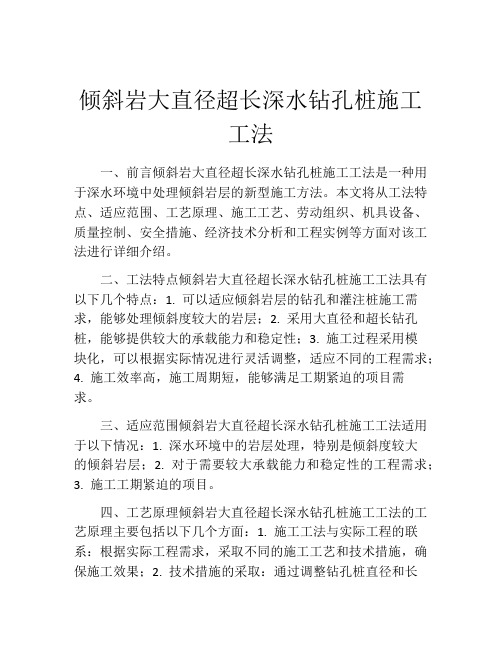
倾斜岩大直径超长深水钻孔桩施工工法一、前言倾斜岩大直径超长深水钻孔桩施工工法是一种用于深水环境中处理倾斜岩层的新型施工方法。
本文将从工法特点、适应范围、工艺原理、施工工艺、劳动组织、机具设备、质量控制、安全措施、经济技术分析和工程实例等方面对该工法进行详细介绍。
二、工法特点倾斜岩大直径超长深水钻孔桩施工工法具有以下几个特点:1. 可以适应倾斜岩层的钻孔和灌注桩施工需求,能够处理倾斜度较大的岩层;2. 采用大直径和超长钻孔桩,能够提供较大的承载能力和稳定性;3. 施工过程采用模块化,可以根据实际情况进行灵活调整,适应不同的工程需求;4. 施工效率高,施工周期短,能够满足工期紧迫的项目需求。
三、适应范围倾斜岩大直径超长深水钻孔桩施工工法适用于以下情况:1. 深水环境中的岩层处理,特别是倾斜度较大的倾斜岩层;2. 对于需要较大承载能力和稳定性的工程需求;3. 施工工期紧迫的项目。
四、工艺原理倾斜岩大直径超长深水钻孔桩施工工法的工艺原理主要包括以下几个方面:1. 施工工法与实际工程的联系:根据实际工程需求,采取不同的施工工艺和技术措施,确保施工效果;2. 技术措施的采取:通过调整钻孔桩直径和长度,选择合适的地质钻机和灌注设备,以及采取合适的钻孔桩组合形式,实现对倾斜岩层的稳定处理。
五、施工工艺倾斜岩大直径超长深水钻孔桩施工工艺主要包括以下几个步骤:1. 前期准备工作:包括现场勘测、工程设计、工艺研究、机具设备调配等工作;2. 钻孔施工:采用合适的地质钻机进行钻孔,根据实际需求确定钻孔直径和长度;3. 灌注桩施工:采用合适的灌注设备进行桩灌注,确保桩体稳定性和承载能力;4. 后期处理工作:包括桩顶修整、钻孔桩验收等工作。
六、劳动组织倾斜岩大直径超长深水钻孔桩施工工法的劳动组织主要包括现场施工人员、技术指导人员和管理人员等。
根据施工进度和工程需求,合理安排施工人员的工作任务和工作时间,确保施工进度和质量。
七、机具设备倾斜岩大直径超长深水钻孔桩施工工法所需的机具设备主要包括地质钻机、灌注设备、深水作业平台等。
水中大直径钻孔桩施工工法-secret
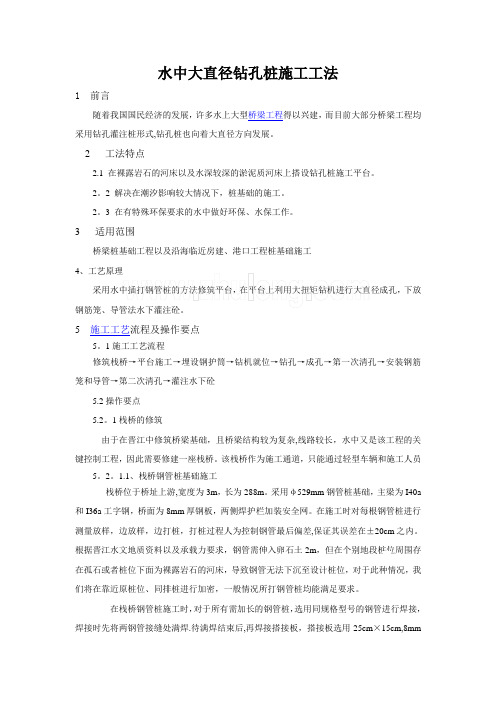
水中大直径钻孔桩施工工法1 前言随着我国国民经济的发展,许多水上大型桥梁工程得以兴建,而目前大部分桥梁工程均采用钻孔灌注桩形式,钻孔桩也向着大直径方向发展。
2 工法特点2.1 在裸露岩石的河床以及水深较深的淤泥质河床上搭设钻孔桩施工平台。
2。
2 解决在潮汐影响较大情况下,桩基础的施工。
2。
3 在有特殊环保要求的水中做好环保、水保工作。
3 适用范围桥梁桩基础工程以及沿海临近房建、港口工程桩基础施工4、工艺原理采用水中插打钢管桩的方法修筑平台,在平台上利用大扭矩钻机进行大直径成孔,下放钢筋笼、导管法水下灌注砼。
5 施工工艺流程及操作要点5。
1施工工艺流程修筑栈桥→平台施工→埋设钢护筒→钻机就位→钻孔→成孔→第一次清孔→安装钢筋笼和导管→第二次清孔→灌注水下砼5.2操作要点5.2。
1栈桥的修筑由于在晋江中修筑桥梁基础,且桥梁结构较为复杂,线路较长,水中又是该工程的关键控制工程,因此需要修建一座栈桥。
该栈桥作为施工通道,只能通过轻型车辆和施工人员5。
2。
1.1、栈桥钢管桩基础施工栈桥位于桥址上游,宽度为3m,长为288m。
采用φ529mm钢管桩基础,主梁为I40a 和I36a工字钢,桥面为8mm厚钢板,两侧焊护栏加装安全网。
在施工时对每根钢管桩进行测量放样,边放样,边打桩,打桩过程人为控制钢管最后偏差,保证其误差在±20cm之内。
根据晋江水文地质资料以及承载力要求,钢管需伸入卵石土2m,但在个别地段桩位周围存在孤石或者桩位下面为裸露岩石的河床,导致钢管无法下沉至设计桩位,对于此种情况,我们将在靠近原桩位、同排桩进行加密,一般情况所打钢管桩均能满足要求。
在栈桥钢管桩施工时,对于所有需加长的钢管桩,选用同规格型号的钢管进行焊接,焊接时先将两钢管接缝处满焊.待满焊结束后,再焊接搭接板,搭接板选用25cm×15cm,8mm厚4块钢板。
焊接完成后必须将焊渣清除,保证焊缝无明显残留焊渣,无蜂窝。
大直径深孔水下灌注桩施工技术

大直径深孔水下灌注桩施工技术摘要:随着现代化科学技术水平的提高,建筑行业在施工技术上也逐渐有了新的突破。
在桩基础的施工过程中,由于大直径深孔水下灌注桩技术简明方便,承受强度高,设备相对简单,不受各种地质条件的约束,因此这项施工技术逐渐被广泛采用。
本文将根据实际的桥路施工建设过程中使用大直径深孔水下灌注桩技术做深入的分析探讨。
关键词:大直径;深孔;水下灌注桩一、大直径深孔水下灌注桩概述水下灌注桩技术在桥路施工过程中的每一个环节都至关重要,每项施工技术都具有紧密联系,特别是填筑混凝土时的水泥、泥浆的调配比例,浇灌的深度、承载力、负荷量以及浇灌的数量等都需要经过精确的测量,保证每个环节都按照严格的规范和要求进行。
以下我们将结合具体施工中的大桥桩基础建设来探讨大直径深孔水下灌注桩施工技术的应用。
(一)工程结构特点第一座大桥为昆明至安宁高速公路高峣立交桥,桥梁为三层半立交结构,下部结构为桩柱式,上部结构为预制小箱梁、现浇箱梁结构。
桥位位于滇池断层与西山结合处,坡体上残留的泥土层粘性比较大,平均厚度一般为3m左右,局部达到了8m。
下层土质主要为淤泥及草煤层,地质报告显示部分桩基位置地表下50~60米左右为玄武岩。
桩孔直径为1.5~2.5m,设计桩基共有438根,桩基单根的长度为65~90m。
第二座桥为高峣至海口一级公路高峣大桥,地质情况与上例相近,但更靠近昆明草海,局部桩位存在流砂层,施工难度较大。
桥梁上部结构为预制20米预制I型梁加现浇桥面板结构,下部结构为桩基承台加圆柱结构,每个桥墩(单幅)设置2~6根桩基,桩径为1.2~1.8米,桩基单根的长度为40~60m。
(二)施工技术方案的选择与应用对两条桥路的施工在前期设计阶段,要预先设计好使用的设备,开工的流程等,设备主要采用CZ-50型号规格的冲击钻打桩成孔,在浇灌混凝土时采用分开作业的方法,将成孔和灌注交叉施工。
主要流程为场地位置的选择、桩基础设计、钻孔、灌注、验收、检查设备等步骤。
- 1、下载文档前请自行甄别文档内容的完整性,平台不提供额外的编辑、内容补充、找答案等附加服务。
- 2、"仅部分预览"的文档,不可在线预览部分如存在完整性等问题,可反馈申请退款(可完整预览的文档不适用该条件!)。
- 3、如文档侵犯您的权益,请联系客服反馈,我们会尽快为您处理(人工客服工作时间:9:00-18:30)。
谈水下超大直径超长钻孔桩施工技术
摘要:本文以鱼山大桥为例,介绍了水下超大直径超长钻孔桩施工技术,并介
绍了一些在施工中的问题,希望对其他同行有所帮助。
关键词:水下;超大直径;超长钻孔桩
前言:
施工实践表明,在水下超大直径超长钻孔桩施工中该技术和措施可行、方便,保证了施工质量,取得了良好的经济效益,为同类钻孔桩的施工提供了一些经验。
一、工程概况(鱼山大桥)
鱼山大桥位于岱山县,鱼山大桥项目是宁波舟山港主航道(玉山石化分公司
高速公路项目),连接岱山岛和鱼山国际绿色石化基地。
路线起点位于岱山县双
河村后沙洋山嘴,岱山岛高沿西北向海洋延伸的路线,在花山南侧向西南,跨越2000吨级航道向西北大鱼后,在山东侧约2km计划穿越海堤玉山填海区,舟山
路规划终点绿色石化基地的禹山路。
鱼山大桥项目路线全长8.815km,沿线共设
置特大桥7781.75米/1座(主跨跨径260m),其中通航孔桥采用连续-刚构混合梁
结构体系,主跨中间90m采用钢箱梁,下部结构采用群桩基础,桩径φ4.0-3.0m。
非通航孔桥采用70m和50m节段预制拼装箱梁,下部结构采用单桩单柱,桩基
根据受力不同分别采用φ5.0-3.8m~φ3.4-2.5m的钢管复合桩。
禹山桥梁设计标准
技术标准:本项目采用《公路工程技术标准》(JTG b01-2014);公路等级:四
车道高速公路(最近实施的一半);设计速度:80公里/小时;宽度:12.75m;
桥梁宽度:考虑DN600mm管道和220kV电缆桥,桥宽15.6m桥;车辆设计荷载
等级:等级公路桥梁设计;最高潮位:1/300;其他技术指标符合国家相关标准和实施。
二、深水中大直径钻孔桩施工技术
6号- 8号深水钻孔桩、水上钻孔平台施工,大吨位起重机的使用(120t)水
钻井平台建设,并根据大桩径及地质条件下钻孔灌注桩的特点,采用kpg-3000型
旋挖钻机、泥浆反循环排渣的建设方法。
并用垂直管灌注混凝土桩施工技术。
2. 1施工平台架设
水上施工平台采用浮动式振动锤0.8米直径钢管插入河道作为平台墩,并采
用万向杆拼装施工平台,对施工平台进行精确放样,如图1所示。
根据桩位设计
坐标打直径3.0m和14毫米壁厚的钢管施工保护管,然后用直径0.4米的钢管在
泥壳焊接相通,使其各可以回收利用,避免泥浆排放到河中,有效地保护环境,
施工平台安装后安装kpg-3000a旋转钻机。
大直径钻孔灌注桩是保持泥浆压力的关键部位。
为了使钻井顺利进行,泥浆
柱在孔内的压力应满足以下关系。
地层压力<泥浆柱压力<地层破裂压力
当局部压力>泥浆柱压力时,孔壁部分坍塌。
当泥柱压力大于地层破裂压力时,泥柱压力会引起压裂地层的泥浆损失。
(1)护筒顶端高程的确定
潮差是4.5-5.0米,地层压力范围约48千帕。
当进行泥浆和套管设置时,泥浆柱压力是固定值,不受潮汐影响。
潮涨时,
满足泥浆柱压力大于地层压力之间的关系,泥浆柱压力增大,当低潮泥浆柱压力
会产生反窜压裂地层漏失,以及套管费用会增加,所以应建立合理的h值。
考虑
到波浪在这一地区的影响,项目需要控制在2.5-3.0米。
(2)护筒埋人深度的确定
考虑到管角,h2河埋深越深,套管越长,孔壁防护效果越好,但随着h2的
增加,安装施工难度加大,护管成本也随之增加。
h2越小,套管深度越小,压裂
压力越小,低潮泥柱压力很可能使地层破裂,泥浆从套管底部漏失,因此h2也
应有最佳值。
根据工程经验和云河床地质条件、埋管深度的人h2 h1从河床砂体
厚度为2m,埋入深度为6m。
(3)护筒长度H
H=h+ h1+h2
2.3泥浆配制
钻井泥浆采用集中搅拌、集中供应、集中净化的方法。
泥浆是由土壤:膨胀剂:水是1:16:0.3。
2.4钻进施工方法
kpg-3000a钻机大型钻探设备、振动和齿轮的功能比传统的钻钻是完全不同的,尤其是在硬岩钻井地质钻井速度是5-8倍的传统冲击钻头,在钻头旋转冲击钻墙壁,效果优于传统的。
(1)当进行开钻时,首先用低档,要保持慢速,以正循环的方式钻进,主要采
用泥浆护壁,钻5m后进行反循环钻进。
(2)钻孔时,钻压不得超过该钻具重量的80%(浮力),和重锤的指导作用应
保证垂直度和孔型。
(3)对于每层淤泥层,采用中速、优质、大量钻井泥浆泵进行钻进;粉质土钻
进速度中等,泵体积大,钻井泥浆变薄;对于砂体,采用轻压、慢低、高泵速、
厚泥浆钻进。
为避免孔壁不稳定,局部扩孔或部分塌孔,充分渣、排渣、防埋现象;砂砾层、低质、缓粗泥浆钻进,保证壁厚,并钻进全渣、排渣,为花岗斑岩
层采用低齿轮慢压钻进。
总之,应根据地质条件选择钻井压力和钻井速度。
具体
索引见表1。
(4)当钻取接近1-2米的井底位置时,应采用低压低钻钻进次数,并控制进尺,保证管口底部稳定地层。
当钻杆底部2-3米时,正常钻井状态恢复。
三、施工中出现的一些质量问题
3. 1声测管堵塞
在建设初期,由于插入式薄壁声测管的使用,没有在安装过程中采取有效措施,致使一些声管堵塞的现象,通过桩的部分造成的不可使用超声波和钻芯法只
能用于测试,不仅增加了成本和时间延迟。
3. 2桩基桩底少量胶结
在钻孔灌注桩检测中桩底发现个别胶结性差的现象,项目部召开专题会议,
研究项目的质量,发现问题的主要原因:一是清孔不彻底,灌注前孔底沉渣量超
过标准在输液导管;底部的孔距离过大,导致浇注第一罐混凝土孔底沉渣混合;
三是超钻清孔现象的置换;中存在的问题,项目部专门制定了措施,取得了良好
的效果。
四、对成桩质量采取的一些保证措施
(1)进一步加强和完善质量保证体系,提高施工管理人员,特别是现场施工人
员的责任心和责任感。
(2)要加强施工现场的过程控制和内部控制,严格按照施工工艺和程序文件进
行施工,实行过程控制,对每个过程负责,使施工过程得到有效、有效的控制。
(3)加强施工人员,特别是施工人员的培训,使施工人员能够根据实际施工过
程的要求,熟记工艺规范,进行操作和内部监控。
(4)现场施工的改进方案及措施
①认真计算泥浆池和沉淀池的容量,合理布置,延长泥浆循环周期,控制各
墩钻机数量,便于泥浆配制和处理。
②严格控制泥浆原料、配制和处理,严格控制泥浆指标。
③泥浆分离器足够的配置,这在清孔、钢筋笼安装第一时间在要求的范围内
的各种目标控制下的泥,尤其是泥砂率提高在2%以下的标准和控制,以减少时
间完成混凝土浇注孔沉积物的过程。
④清理完毕后,应提前做好钢筋笼的安装和速度,尽量减少孔的完工时间,
并尽量减少初浇混凝土的第一孔清洗时间。
⑤应加强导管的定期检测和严密性检查。
应加强导管安装后的整体矫直检查,为了保证管柱位于孔底的中心位置,减少混凝土,提高初期灌溉的影响,减少泥
沙的影响。
⑥两孔清洗采用逆循环孔清洗,并利用吊车移到更直的导管孔,当孔深检测
时通过多点测量,孔底主要是孔底周围沉积物可以完全去除,从而保证水下混凝
土的质量。
⑦严格控制水下混凝土的原材料和生产质量,加强混凝土的运输保障。
⑧为了保证混凝土封底的质量,必须根据实际的孔形,仔细计算初始灌溉时
混凝土的方量。
⑨定期组织施工组织和质量分析,分析施工过程中存在的问题,及时、针对
性地改进施工工艺和现场施工组织。
⑩声波管的安装应便于桩基检测。
桩基础施工完成后应尽快组织自检,以确
定桩的质量,提前发现并解决问题。
结束语:
泥浆护壁是一种比较成功的护壁方法。
桥梁钻孔灌注桩施工过程中无坍塌现象。
各项指标均符合标准要求。
在超长大直径桩基础施工过程中,超声波检测超长大直径桩必须加强施工过程控制。
无缝钢管不应作为试验管道堵塞,必须避免声管堵塞。
在建设过程中,要及
时解决问题。
由于桩基早期检测中桩底胶结不良,使施工工期推迟了近20天。
解决了这一难题,取得了良好的效果,成桩率高达95%以上。
参考文献:
[1]顾元威.海上大直径钻孔灌注桩施工技术[J].煤田地质与勘探,2003,31(4):41-44.
[2]TB10203-2002/J162-2002,铁路桥涵施工规范[S].
[3]铁建设【2005】160号,铁路桥涵工程施工质量验收标准[S].。