液压冷拔管工艺流程
冷拔无缝钢管技术操作规程

冷拔无缝钢管技术操作规程文件名称:工艺文件文件编号: **-JW-03-03 编制: 审核:会签:标准化:批准:2014年5月1.适应范围:本规程规定了************有限公司冷拔工艺技术内容及要求。
2.工艺流程:退火连拔管料——打头——酸洗——清洗——磷化——清洗——皂化—拔制中间热处理———热处理——矫直——切割——检验——成品——打包入库3.产品规格范围及主要钢种3.1规格范围目前产品主要范围为:外径10—102,壁厚1—143.2钢种范围10、20、35、45、Q345B、20Cr、40Cr、30CrMo、42CrMo、37Mn5等4.打(改)头4.1设备:150公斤空气锤3台、轧尖机3台、65公斤空气锤1台、160吨磨擦压力机1台。
4.2操作技术要求:4.2.1来料必须按钢号、炉号、规格、支数和质量情况进行核对是否与工艺流转卡相符,若不相符及时查对处理。
4.2.2开车前必须对所有使用运转设备的润滑情况进行检查。
4.2.3按工艺流转卡进行打(改)头,不得任意更改,如发现工艺不合理应及时与工艺(质量)员联系。
4.2.4打(改)头技术要求:4.2.4.1打(改)头头部中心线与管料中心线一致,不得弯曲;4.2.4.2打(改)头应圆正结实,过渡部分无棱角;4.2.4.3打(改)头加热长度不得超过180mm,冷拔断头管打头时,加热长度尽量缩短,温度不宜太高,应符合温度控制表规定。
4.2.5钢管打(改)头加热温度控制如下:4.2.6打头时,应选毛管头部进行(冷拔在制品中间切断后,分别打头部和尾部,切老头管子应打头部)。
4.2.7打(改)头后,钢管尾部应放齐,不同规格钢号、炉号、批号的钢管应分别堆放,壁厚小于2mm的钢管应轻拿轻放,防止压扁、摔弯等。
5.酸洗5.1设备:花岗岩石槽规格(内腔尺寸:长×宽×深m)12×1.0×1.05.2硫酸酸洗的使用制度新溶液中硫酸的浓度(%) 15—24酸洗液的温度(℃)50—70硫酸的最低浓度(%)4—7硫酸亚铁的含量(克/升)<200—250酸洗时间(分):毛管30—60中间管15—255.3盐酸溶液的使用制度盐酸浓度( %) 8—12亚铁含量(克/升)<100酸洗温度(℃)室温酸洗时间(分)30—605.4操作技术要求5.4.1严格核对酸洗的管料与工艺流转卡是否相符,若不符则应及时处理,不同钢号、炉号、规格的钢管必须分开酸洗。
冷拔钢管生产工艺

冷拔钢管生产工艺
冷拔钢管,冷轧钢管机组是用冷轧、冷拔或冷轧和冷拔相结合的冷加工方法生产管材的整套装备组合,是对热轧管材或焊接管进行深度加工的机组。
冷拔机组是依据管材(圆钢穿孔毛坯管、热轧无缝钢管、焊接钢管)的加工性能、管材尺寸、质量要求以及投资和效益来选择的对管料进行外径、内孔、壁厚、直线度、外表状态的一种粗加工方式,从而使管材达到尺寸更精确,外表更光滑、内孔更圆润、机械加工余料更小,促进后续机械加工等深加工精加工用户达到节约钢材的目的的一种相对性的辅助加工流程。
冷拔管加工的基本工序有:
1.管料供给---冷拔管价格所用管料为热轧成品管或半成品管、挤压管以及焊接管;
2.管料准备---对原材料管料进行尺寸、壁厚、内孔、材质进行检查、打捆、酸洗、清洗、冲洗、中和、烘干、涂润滑剂等一系列前期工作;
(3)冷加工(冷轧或冷拔)---对已经前期处理过的原材料上冷轧或冷拔机组进行相应的生产流程;
(4)成品检验---对冷轧或冷拔生产线上已完成的产品进行外径、内孔、壁厚测量的基本操作后,对已生产完成的产品进行热处理、矫直、取样、切头尾、检查(人工检查和各种探伤)、水压试验、涂油、包装、入库等。
注:不同的产品精整内容有所差异。
本资料由聊城鹏煜钢管有限公司整理提供,转载请注明出处。
冷拔工艺流程
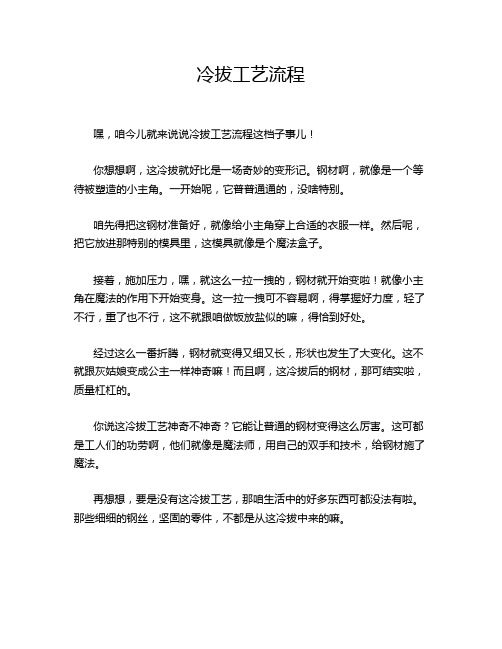
冷拔工艺流程
嘿,咱今儿就来说说冷拔工艺流程这档子事儿!
你想想啊,这冷拔就好比是一场奇妙的变形记。
钢材啊,就像是一个等待被塑造的小主角。
一开始呢,它普普通通的,没啥特别。
咱先得把这钢材准备好,就像给小主角穿上合适的衣服一样。
然后呢,把它放进那特别的模具里,这模具就像是个魔法盒子。
接着,施加压力,嘿,就这么一拉一拽的,钢材就开始变啦!就像小主角在魔法的作用下开始变身。
这一拉一拽可不容易啊,得掌握好力度,轻了不行,重了也不行,这不就跟咱做饭放盐似的嘛,得恰到好处。
经过这么一番折腾,钢材就变得又细又长,形状也发生了大变化。
这不就跟灰姑娘变成公主一样神奇嘛!而且啊,这冷拔后的钢材,那可结实啦,质量杠杠的。
你说这冷拔工艺神奇不神奇?它能让普通的钢材变得这么厉害。
这可都是工人们的功劳啊,他们就像是魔法师,用自己的双手和技术,给钢材施了魔法。
再想想,要是没有这冷拔工艺,那咱生活中的好多东西可都没法有啦。
那些细细的钢丝,坚固的零件,不都是从这冷拔中来的嘛。
所以啊,咱可不能小瞧了这冷拔工艺流程,它可在背后默默为我们的生活做了大贡献呢!它就像是一个低调的英雄,虽然不常被提起,但却不可或缺。
咱得给它点个赞,是不是?这就是冷拔工艺,看似简单,实则暗藏玄机,充满了奇妙和惊喜!。
冷拔无缝钢管制作过程
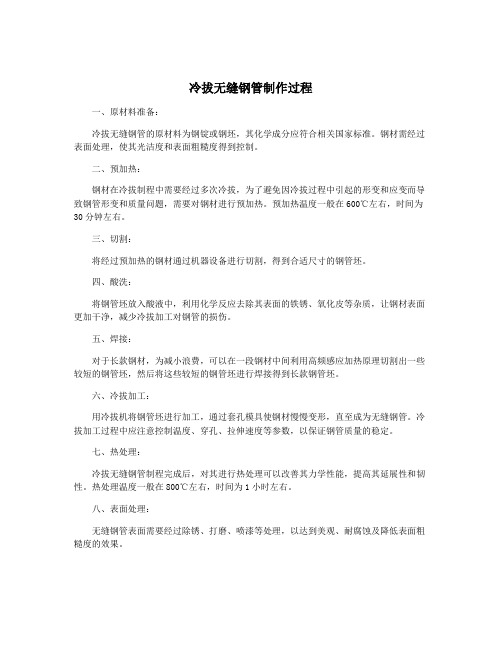
冷拔无缝钢管制作过程
一、原材料准备:
冷拔无缝钢管的原材料为钢锭或钢坯,其化学成分应符合相关国家标准。
钢材需经过表面处理,使其光洁度和表面粗糙度得到控制。
二、预加热:
钢材在冷拔制程中需要经过多次冷拔,为了避免因冷拔过程中引起的形变和应变而导致钢管形变和质量问题,需要对钢材进行预加热。
预加热温度一般在600℃左右,时间为30分钟左右。
三、切割:
将经过预加热的钢材通过机器设备进行切割,得到合适尺寸的钢管坯。
四、酸洗:
将钢管坯放入酸液中,利用化学反应去除其表面的铁锈、氧化皮等杂质,让钢材表面更加干净,减少冷拔加工对钢管的损伤。
五、焊接:
对于长款钢材,为减小浪费,可以在一段钢材中间利用高频感应加热原理切割出一些较短的钢管坯,然后将这些较短的钢管坯进行焊接得到长款钢管坯。
六、冷拔加工:
用冷拔机将钢管坯进行加工,通过套孔模具使钢材慢慢变形,直至成为无缝钢管。
冷拔加工过程中应注意控制温度、穿孔、拉伸速度等参数,以保证钢管质量的稳定。
七、热处理:
冷拔无缝钢管制程完成后,对其进行热处理可以改善其力学性能,提高其延展性和韧性。
热处理温度一般在800℃左右,时间为1小时左右。
八、表面处理:
无缝钢管表面需要经过除锈、打磨、喷漆等处理,以达到美观、耐腐蚀及降低表面粗糙度的效果。
以上为冷拔无缝钢管制作过程的主要步骤。
其中每个步骤都需要严格控制工艺流程、涉及到机器设备的精度要求等方面的问题。
只有严格执行生产操作规程和质量控制标准,才能生产出高质量的无缝钢管。
冷拔工艺

四、冷拔钢管缺陷及分析
缺陷名称:折叠、裂缝(裂纹、发纹) 缺陷名称:折叠、裂缝(裂纹、发纹)、凹坑、尺寸超差、壁厚不均、 椭圆、划道(擦伤) 椭圆、划道(擦伤)、抖纹、纵向开裂、纵向凹折、翘皮、 夹杂、麻面(针孔) 夹杂、麻面(针孔)、矫痕、内外折等。
序 缺陷 号 名称
特征 产生原因 预防和消除方法
1 横裂 钢管表面 有连续或 断续的横 向破裂
酸洗时间过长引起氢脆 热处理不当, 热处理不当,加工应力未充分消除 拔制变形量过大 拔制速度过快, 拔制速度过快,产生热应力 空拔厚壁管内外变形不一致, 空拔厚壁管内外变形不一致,产生 附加应力
正确执行工艺制度, 正确执行工艺制度,按 操作规程作业 合理安排变形量 对厚壁管特别注意内外 性能均匀、要控制壁厚 不均
缺陷缺陷名称名称特征特征产生原因产生原因预防和消除方法预防和消除方法22钢管表面钢管表面呈直线形呈直线形划痕划痕拔模表面不光滑有裂纹或粘钢拔模表面不光滑有裂纹或粘钢锤头过渡区有棱角磨损工具锤头过渡区有棱角磨损工具欠酸洗或钢管表面残留有氧化皮欠酸洗或钢管表面残留有氧化皮润滑质量不高拔速过快润滑质量不高拔速过快热轧管料有青线拔后未能消除热轧管料有青线拔后未能消除模具硬度不够或已磨损模具硬度不够或已磨损变形量过大变形量过大热处理欠温或不均匀热处理欠温或不均匀提高模具的质量提高模具的质量氧化铁皮要洗干净氧化铁皮要洗干净涂层均匀牢固涂层均匀牢固锤头过渡区的质量锤头过渡区的质量勤检查模具和钢管表勤检查模具和钢管表面发现问题及时处面发现问题及时处理理33沿长度方沿长度方向出现高向出现高低不平的低不平的环形波浪环形波浪热处理后性能不均匀热处理后性能不均匀酸洗后冲洗不干净润滑不良酸洗后冲洗不干净润滑不良拔制时抖动拔制时抖动芯杆过细拔制时弹性变形引起芯杆过细拔制时弹性变形引起抖动抖动启动速度过快或链条振动启动速度过快或链条振动外模形状不合理入口锥角太大外模形状不合理入口锥角太大按规程进行热处理按规程进行热处理酸洗干净磷化润滑酸洗干净磷化润滑良好良好适当的拔制速度适当的拔制速度合理的道次变形量合理的道次变形量缺陷缺陷名称名称特征特征产生原因产生原因预防和消除方法预防和消除方法44在钢管纵在钢管纵向上管向上管壁厚向内壁厚向内呈条状凹呈条状凹空拔薄壁管时减径量过大空拔薄壁管时减径量过大钢管锤头部过渡太急钢管锤头部过渡太急合理分配减径量合理分配减径量锤头部应平缓无皱折锤头部应平缓无皱折管料修磨位置长宽比要管料修磨位置长宽比要合适合适55开裂开裂呈穿透管呈穿透管壁的纵向壁的纵向裂开裂开全长全长和局部和局部空拔管变形量过大空拔管变形量过大热处理不当加工硬化未全部热处理不当加工硬化未全部消除消除拔制后未及时热处理拔制后未及时热处理连拔道次多加工硬化严重连拔道次多加工硬化严重钢管本身塑性低钢管本身塑性低合理编排拔制表合理编排拔制表合金管和连拔管拔后及合金管和连拔管拔后及时热处理时热处理按工艺要求进行热处理按工艺要求进行热处理缺陷缺陷名称名称特征特征产生原因产生原因预防和消除方法预防和消除方法66表面成片表面成片的细点状的细点状凹坑凹坑过酸洗过酸洗氧化皮厚矫直量压入基体氧化皮厚矫直量压入基体钢管表面有油污加热时烧钢管表面有油污加热时烧酸洗后停放时间过
液压抽管的工艺流程

液压抽管的工艺流程英文回答:The process of hydraulic tubing involves several stepsto ensure the proper installation and functionality of the system. Here is a breakdown of the process:1. Planning and Design: Before starting theinstallation, it is essential to plan and design the hydraulic tubing system. This includes determining the layout, size, and type of tubing required for the specific application. It is crucial to consider factors such as pressure, flow rate, temperature, and the type of fluid being used.2. Material Selection: Once the design is finalized,the next step is to select the appropriate tubing material. Common materials used for hydraulic tubing include steel, stainless steel, and copper. The choice of material depends on factors such as corrosion resistance, strength, and cost.3. Tube Cutting: After selecting the tubing material,it needs to be cut to the required length. This can be done using various methods, including sawing, shearing, or using a tube cutter. It is important to ensure clean and precise cuts to prevent any leaks or damage to the tubing.4. Tube Bending: In many hydraulic systems, tubing needs to be bent to fit around obstacles or to follow specific paths. Tube bending can be done using manual or hydraulic tube benders. Care should be taken to ensure proper bending angles and radii to maintain the integrity of the tubing.5. Flaring and Swaging: Flaring and swaging are techniques used to create a leak-proof connection between the tubing and fittings. Flaring involves expanding the end of the tube to create a flared shape, while swaging involves compressing the tube end to fit inside a fitting. These techniques provide a secure connection that can withstand high pressures.6. Assembly and Installation: Once the tubing is cut, bent, and prepared with flares or swages, it is ready for assembly. This involves connecting the tubing to various components such as valves, pumps, and cylinders usingfittings and connectors. Proper tightening and sealing techniques should be followed to prevent any leaks.7. Testing and Inspection: After the installation is complete, it is crucial to test the hydraulic system forany leaks or faults. This can be done by pressurizing the system and checking for any pressure drops or visible leaks. Additionally, a visual inspection should be performed to ensure all connections are secure and properly installed.8. Maintenance and Troubleshooting: Regular maintenance and troubleshooting are essential to keep the hydraulic tubing system in optimal condition. This includes checking for any signs of wear, corrosion, or damage, and addressing any issues promptly to prevent system failure.中文回答:液压抽管的工艺流程包括以下几个步骤,以确保系统的正确安装和功能正常。
冷拔工艺

二、冷拔工艺流程
毛管 分选 毛管修磨
坯料
称重
加热
喷印
穿孔
复检
打头
酸洗
润滑
人工检验
冷拔
切管
热处理
矫直序作用及要求
3.1管料 外径和壁厚尺寸越接近成品尺寸越好,可减小拔制道次,节省成本。 来料规格要考虑钢种、品种、设备能力、供料条件 尺寸精度:D±1~1.5%,S ±10%,弯曲度≤2mm/m 内外表质量:不得有影响成品的折皱、结疤、划道、裂纹存在(轻微 的要修磨干净) 管料的检查与修磨:对提高成品合格率相当重要
5.1热轧毛管 坯料:φ60~φ75,采用斜底炉加热,最大入炉长度1450mm 毛管:φ64~78×3~6,最大长度4100mm。
3.2锤头 要求:严实,能够拔2~3道次;
长度不超180mm,
过渡园滑,无尖锐棱角 中心线与管体一致,不得有扭转 ,防止局部凹陷 管端加热温度、长度要求 对小径薄壁管可采用轧头。
3.3酸洗润滑 洗掉钢管表面的氧化铁皮,减少磨擦,降低拔制力。防止在拔 制时产生划道等缺陷。 ⑴氧化铁皮的分布 三层:最外层为Fe2O3,极薄,占1~2%
工作表面光洁,不得有任何缺陷存在
⑷配模与安装 模具分类 外模:锥形和弧形
主要参数:入口锥、出口锥、定径带
内模:柱形和锥形 配模:锥形外模+柱形内模;弧形外模+锥形内模
安装:拔管模中心线与拔制中心线一致,避免产生弯曲或壁厚不
均。 芯棒在变形区的位置不能过前或过后。过前则增加了拔制
力,易拔断和造成划道;过后则起不到减壁的作用。
缺点:需加热
对铁基侵蚀大,易氢脆 表面暗,生产物溶解度小而不易去除,特别是含Cr、Ni钢
酸洗速度慢
冷拔作业指导书

冷拔作业指导书标题:冷拔作业指导书引言概述:冷拔是一种金属加工工艺,通过拉伸金属材料来改变其形状和尺寸。
冷拔作业需要一定的技术和操作要求,以确保产品质量和生产效率。
本指导书将详细介绍冷拔作业的流程和注意事项,匡助操作人员正确进行冷拔作业。
一、准备工作1.1 确定冷拔材料和规格:在进行冷拔作业前,需要准确确定所需的材料种类和规格,以确保产品质量和生产效率。
1.2 准备冷拔设备:检查冷拔设备的工作状态和保养情况,确保设备正常运转。
1.3 安全防护措施:操作人员需要佩戴符合要求的防护装备,如手套、护目镜等,确保人身安全。
二、冷拔作业流程2.1 加热材料:将金属材料加热至适当温度,以提高材料的塑性,便于冷拔操作。
2.2 冷拔拉伸:将加热后的材料通过冷拔机进行拉伸,改变其形状和尺寸。
2.3 冷却处理:冷拔完成后,材料需要进行冷却处理,以增强其硬度和强度。
三、注意事项3.1 控制冷拔速度:冷拔速度过快容易造成材料变形或者裂纹,需要根据材料种类和规格合理控制冷拔速度。
3.2 定期检查设备:定期检查冷拔设备的工作状态和润滑情况,确保设备正常运转。
3.3 注意材料选择:不同的金属材料适合于不同的冷拔工艺,需要根据实际情况选择合适的材料。
四、质量检验4.1 外观检查:检查冷拔产品的外观质量,包括表面光洁度、尺寸精度等。
4.2 物理性能测试:对冷拔产品进行物理性能测试,包括硬度测试、拉伸强度测试等。
4.3 化学成份分析:对冷拔产品进行化学成份分析,确保产品符合相关标准要求。
五、后续处理5.1 清洗处理:清洗冷拔产品,去除表面污物和润滑剂残留。
5.2 包装存储:对冷拔产品进行包装,储存在干燥通风的环境中,避免产品受潮或者氧化。
5.3 报告记录:记录冷拔作业过程中的关键参数和质量检验结果,以备后续参考。
结语:冷拔作业是一项重要的金属加工工艺,正确的操作流程和注意事项对产品质量和生产效率至关重要。
通过本指导书的详细介绍,希翼能够匡助操作人员正确进行冷拔作业,确保产品质量和生产效率。
- 1、下载文档前请自行甄别文档内容的完整性,平台不提供额外的编辑、内容补充、找答案等附加服务。
- 2、"仅部分预览"的文档,不可在线预览部分如存在完整性等问题,可反馈申请退款(可完整预览的文档不适用该条件!)。
- 3、如文档侵犯您的权益,请联系客服反馈,我们会尽快为您处理(人工客服工作时间:9:00-18:30)。
1、外径偏差范围、内径所留余量需由客户提供合理要求。 2、内径圆度控制:内径≦100mm,圆度≦0.1mm;内径≧100-300,圆度≦0.2mm。 3、壁厚偏差控制:≦±5%。 4、直线度控制:0.3mm/1000mm。
液压冷拔管工艺流程:
管坯
退火
酸洗/润滑
第一道直 ⑥
⑦
定尺锯切
去应力退火
外表面抛光 ⑧
锯管头
精密拔制
⑤
酸洗/润滑 ③
⑩
冷拔成品检验
成品打包入库
⑨
珩磨
检验
打包入库
成品打包入库
检验
刮削滚光
①原材料检验入库,筛选标准:壁厚控制在±8%内,外径控制±0.75%内。 ②为达到客户要求的机械性能,退火前做性能分析,制定退火工艺。之后检验退火效果。 ③检验酸洗、磷化、皂化效果。 ④按要求检验外径、内径、壁厚等偏差精度。 ⑤精密拔制(第二次拔制),经过两道拔制,管材偏差更加精确、性能更加稳定。按客户要求检
验,有缺陷放入次品区。 ⑥做抗拉、屈服、延伸、硬度、冲击功等试验,检验是否达到客户要求的机械性能。 ⑦校直过程中检验每单米的直线度,保证0.3mm/1000mm。 ⑧根据客户需要做外表面抛光,外表更美观、更利于上漆 ⑨再次检验每根管材的精度偏差,符合要求的进入下道工序货打包入库环节。 ⑩根据管材质、规格、客户要求等制订虚线框内工艺。