大型锻造用电渣重熔锭的冶炼工艺
电渣重熔工艺流程
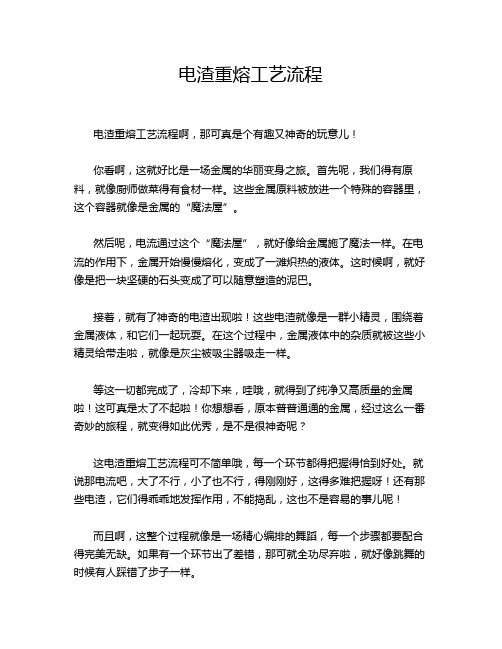
电渣重熔工艺流程
电渣重熔工艺流程啊,那可真是个有趣又神奇的玩意儿!
你看啊,这就好比是一场金属的华丽变身之旅。
首先呢,我们得有原料,就像厨师做菜得有食材一样。
这些金属原料被放进一个特殊的容器里,这个容器就像是金属的“魔法屋”。
然后呢,电流通过这个“魔法屋”,就好像给金属施了魔法一样。
在电流的作用下,金属开始慢慢熔化,变成了一滩炽热的液体。
这时候啊,就好像是把一块坚硬的石头变成了可以随意塑造的泥巴。
接着,就有了神奇的电渣出现啦!这些电渣就像是一群小精灵,围绕着金属液体,和它们一起玩耍。
在这个过程中,金属液体中的杂质就被这些小精灵给带走啦,就像是灰尘被吸尘器吸走一样。
等这一切都完成了,冷却下来,哇哦,就得到了纯净又高质量的金属啦!这可真是太了不起啦!你想想看,原本普普通通的金属,经过这么一番奇妙的旅程,就变得如此优秀,是不是很神奇呢?
这电渣重熔工艺流程可不简单哦,每一个环节都得把握得恰到好处。
就说那电流吧,大了不行,小了也不行,得刚刚好,这得多难把握呀!还有那些电渣,它们得乖乖地发挥作用,不能捣乱,这也不是容易的事儿呢!
而且啊,这整个过程就像是一场精心编排的舞蹈,每一个步骤都要配合得完美无缺。
如果有一个环节出了差错,那可就全功尽弃啦,就好像跳舞的时候有人踩错了步子一样。
但是呢,一旦成功了,那收获可就大啦!高质量的金属可以用来制造各种各样厉害的东西,比如超级坚固的工具啦,精密的仪器啦等等。
这可都是电渣重熔工艺流程的功劳呀!
总之呢,电渣重熔工艺流程虽然复杂,但是它真的很重要,很神奇!它让我们的生活变得更加美好,更加精彩!不是吗?。
YC7合金电渣重熔工艺技术-大冶金
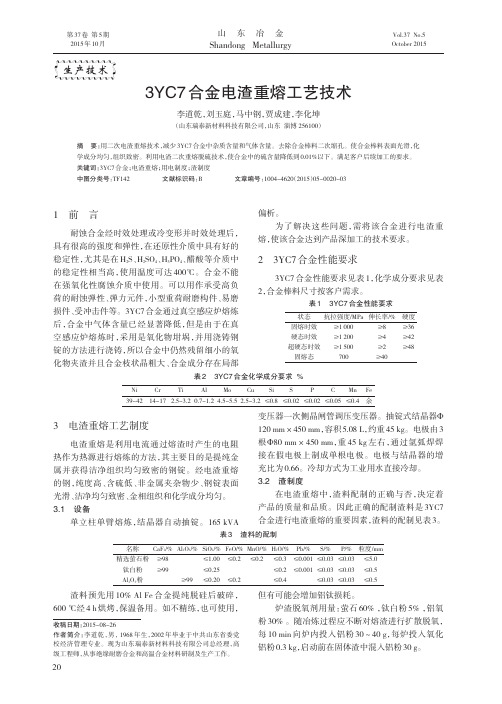
ɤ0.2 ɤ0.3 ɤ0.2 ɤ0.4 ɤ0.001 ɤ0.03 ɤ0.03 ɤ0.001 ɤ0.03 ɤ0.03 ɤ0.03 ɤ0.03 Pb/% S/% P/% 粒度/mm ɤ5.0 ɤ0.5 ɤ0.5
CaF2/% Al2O3/% SiO2/% FeO/% MnO/% H2O/% ɤ0.2 ɤ0.2
第 37 卷 第 5 期 2015 年 10 月
������������ ������������������������������������������������������������
山
东
冶
金
Shandong Metallurgy
Vol.37 No.5 October 2015
1 前 言
耐蚀合金经时效处理或冷变形并时效处理后, 具有很高的强度和弹性, 在还原性介质中具有好的 稳定性, 尤其是在 H2S、 H2SO4、 H3PO4、 醋酸等介质中 的稳定性相当高, 使用温度可达 400℃。合金不能 在强氧化性腐蚀介质中使用。可以用作承受高负 荷的耐蚀弹性、 弹力元件, 小型重荷耐磨构件、 易磨 损件、 受冲击件等。3YC7 合金通过真空感应炉熔炼 后, 合金中气体含量已经显著降低, 但是由于在真 空感应炉熔炼时, 采用是氧化物坩埚, 并用浇铸钢 锭的方法进行浇铸, 所以合金中仍然残留细小的氧 化物夹渣并且合金枝状晶粗大、 合金成分存在局部
李道乾等
3YC7 合金电渣重熔工艺技术 350
2015 年第 5 期 130 90 50 10 5
3.3
电制度
H 金/mm
的关系及电渣炉电流密度与电极直径的关系 (见图 1 和图 2) 可知, 当电极直径<100 mm 时, 电流密度 >0.6 A/mm2。该产品由于属于试制阶段, 为了实验 安全, 电流密度取下限 0.6 A/mm2。
大锻件 第4部分 锻造用钢锭及铸锭技术

第四部分锻造用钢锭及铸锭技术一、 大型钢锭的组织结构及类型1.大型钢锭的组织结构z 激冷层:锭身表面的细小等轴晶区。
厚度仅6~8mm ;因过冷度较大,凝固速 度快,无偏析;有夹渣、气孔等缺陷。
z 柱状晶区:位于激冷层内侧;由径向呈细长的柱状晶粒组成;由于树枝状 晶沿温度梯度最大的方向生长,该方向恰为径向,因此形成了柱状晶区;其凝固速度较快,偏析较轻,夹杂物较少;厚度约50~120mm 。
z 分枝树枝晶区:从柱状晶区向内生长;主轴方向偏离柱状晶,倾斜,并出现 二次以上分枝;温差较小,固液两相区大,合金元素及杂质浓度较大。
z A 偏析区:枝状晶间存在残液,比锭内未凝固的钢液密度小,向上流动,形成A 偏析;在偏析区合金元素和杂质富集,存在较多的硫化物,易产生偏析裂纹。
z 等轴晶区:位于中心部位;温差很小,同时结晶,成等轴晶区。
钢液粘稠, 固相彼此搭桥,残液下流形成V 偏析,疏松增多。
z 沉积锥区:位于等轴晶区的底端;由顶面下落的结晶雨、熔断的枝状晶形成的自由晶组成,显示负偏析;等轴的自由晶上附着大量夹杂物,其组织疏松,且夹杂浓度很大;应切除。
z 冒口区:最后凝固的顶部;因钢液的选择性结晶,使后凝固的部分含有大量的低熔点物质,最后富集于上部中心区,其磷、硫类夹杂物多;若冒口保温不良,顶部先凝固,因无法补缩形成缩孔;质量最差,应予切除。
2. 大型钢锭的类型z 普通钢锭高径比:=+dD H 2 1.8~2.5;通常,10吨以下的钢锭:2.1~2.3,10吨以上的钢锭:1.5~2;锥度:=%100-D Hd 3~4% ; 横断面为8棱角形。
大钢锭为16,24,32棱角。
z 短粗型钢锭高径比: 0.5~2;锥度: 8~12%。
高宽比减小,锥度加大有利于钢锭实现自下而上顺序凝固,易于钢水补缩,中心较密实;有利于夹杂上浮,气体外溢,减少偏析;锭身较短,钢水压力小,侧表面不易产生裂纹;锥度大,易脱模;可增加拔长锻比。
辽宁科技大学科技成果——抽锭电渣重熔工艺及铸锭凝固质量控制技术
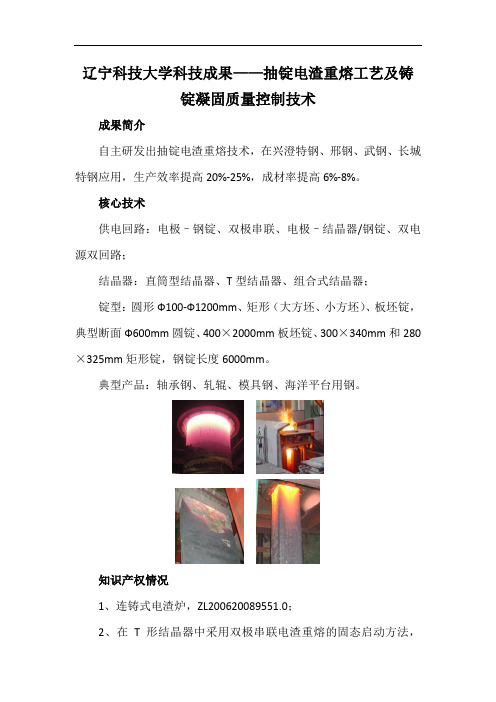
辽宁科技大学科技成果——抽锭电渣重熔工艺及铸
锭凝固质量控制技术
成果简介
自主研发出抽锭电渣重熔技术,在兴澄特钢、邢钢、武钢、长城特钢应用,生产效率提高20%-25%,成材率提高6%-8%。
核心技术
供电回路:电极–钢锭、双极串联、电极–结晶器/钢锭、双电源双回路;
结晶器:直筒型结晶器、T型结晶器、组合式结晶器;
锭型:圆形Ф100-Ф1200mm、矩形(大方坯、小方坯)、板坯锭,典型断面Ф600mm圆锭、400×2000mm板坯锭、300×340mm和280×325mm矩形锭,钢锭长度6000mm。
典型产品:轴承钢、轧辊、模具钢、海洋平台用钢。
知识产权情况
1、连铸式电渣炉,ZL200620089551.0;
2、在T形结晶器中采用双极串联电渣重熔的固态启动方法,
ZL200610046626.1;
3、一种导电结晶器,ZL200720010214.2;
4、一种板坯电渣炉,ZL20071010096.X。
电渣重熔冶炼技术
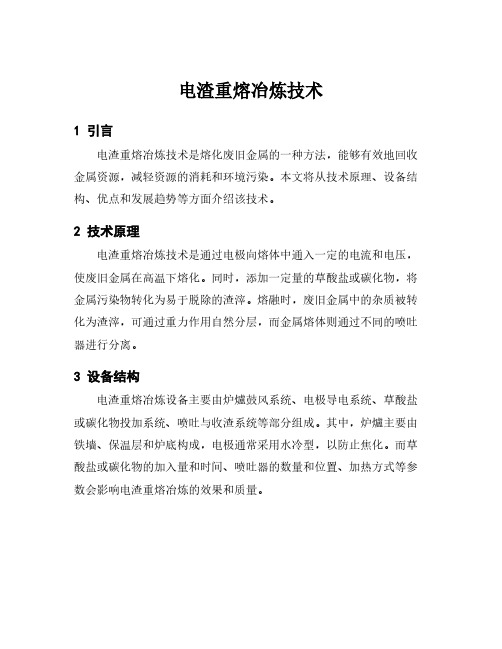
电渣重熔冶炼技术
1 引言
电渣重熔冶炼技术是熔化废旧金属的一种方法,能够有效地回收金属资源,减轻资源的消耗和环境污染。
本文将从技术原理、设备结构、优点和发展趋势等方面介绍该技术。
2 技术原理
电渣重熔冶炼技术是通过电极向熔体中通入一定的电流和电压,使废旧金属在高温下熔化。
同时,添加一定量的草酸盐或碳化物,将金属污染物转化为易于脱除的渣滓。
熔融时,废旧金属中的杂质被转化为渣滓,可通过重力作用自然分层,而金属熔体则通过不同的喷吐器进行分离。
3 设备结构
电渣重熔冶炼设备主要由炉爐鼓风系统、电极导电系统、草酸盐或碳化物投加系统、喷吐与收渣系统等部分组成。
其中,炉爐主要由铁墙、保温层和炉底构成,电极通常采用水冷型,以防止焦化。
而草酸盐或碳化物的加入量和时间、喷吐器的数量和位置、加热方式等参数会影响电渣重熔冶炼的效果和质量。
4 优点
电渣重熔冶炼技术的主要优点是可以高效、环保地回收废旧金属,减少对地球资源的消耗和环境的污染。
此外,该技术还可以生产高纯
度的金属材料,广泛应用于工业生产。
5 发展趋势
电渣重熔冶炼技术已经成为国际铸造行业中广泛使用的一种高效、环保的回收技术。
未来,随着金属回收利用的重要性不断提升,电渣
重熔冶炼技术将在材料回收领域中扮演更为重要的角色。
同时,技术
革新和设备升级还将进一步提高电渣重熔冶炼技术的效率和质量。
6 结论
无论是从环保角度,还是从资源利用率的角度来看,电渣重熔冶
炼技术都是一种十分重要的回收技术。
未来,我们应该进一步加强对
该技术的研究和探索,为推动环境保护和可持续发展做出贡献。
关于巨型钢锭电渣技术之我见

量性能要求越来越高 , 以致大锻件特别是高端大
锻件 已成 为制约 我国重 大型装备 制造业 发展 的重
大瓶 颈 问题 。 比如 , 国核 电建设 已步入 规模化 、 我
1 1 精炼 作用 充分 .
批量 化快 速发 展 的新 阶段 , 未来 2 0年 , 年都 将 每 有 6台 一 1 O台百万千 瓦级 的核 电机 组开工 建设 。 核 电大 锻件需 要 60t 电炉锭 , 0 的 在世 界范 围内采 购都很 紧张 , 国外 厂 家有 时 都不 一 定 会卖 。汽 轮 机低 压转子 、 大型 支撑辊 等也有类 似情 况 。
NO 4 .
《 大型铸锻件》
HEAV C r NG AN 0RG NG Y AS ’ D F I l I
J l O O uv2 1
关于 巨型钢 锭 电渣 技 术之 我 见
向 大林
( 海 重 型机 器 厂 有 限 公 司 , 海 20 4 ) 上 上 02 5
钢水直接电渣重熔生产工艺流程
钢水直接电渣重熔生产工艺流程
改造前
配料→电弧炉冶炼+LF钢包精炼→VOD真空吹氧精炼→中间包→VC真空浇铸(二期预留)→自耗电极(铸锭)→电极退火→电渣重熔→结晶电渣锭→结晶电渣锭加热→油压机锻造→锻后热处理→钻中心孔→剥皮(或粗车)→探伤、检测→入库→交货
改造后
配料→电弧炉冶炼+LF钢包精炼→VOD真空吹氧精炼→中间包→电渣重熔→结晶电渣锭→结晶电渣锭加热→油压机锻造→锻后热处理→钻中心孔→剥皮(或粗车)→探伤、检测→入库→交货。
工艺流程简述:选用优质废钢、生铁和高Cr合金材料,通过EAF电弧炉熔炼、转换到专用中间钢包,钢包自带电极连接端,直接电渣重熔,结晶形成电渣锭,经过此工艺改进后每吨可节约600度电左右。
电渣锭由钢锭保温车运入并热装炉,经加热达到锻造温度后的电渣锭由运输起重机吊至锻造油压机工作区,并在锻造操作车、锻造起重机以及套筒等辅助设备或工具的协助下进行锻造,锻坯成型后立即热装炉进行热处理,热处理后的锻坯经精整、剥皮、探伤、检测后入库交货。
其中10000吨冷轧辊毛坯经高温热处理炉、喷淬机和中温炉调质处理后,进行半精车加工,再经预热加热,双频淬火机床深淬处理。
到加工车间进行粗磨、镗铣等工序后,成品经检验合格,包装入库。
图示对比:。
电渣重熔工艺和理论知识
电渣重熔工艺和理论知识ESR techniques and theoretical knowledge* 一、电渣重熔基础理论知识1、概述电渣冶金起源于美国,一九四〇年霍普金斯取得了发明专利。
一九五八年,苏联德聂泊尔特钢厂工业电渣炉建成,现代电渣冶金开始进入工业化进程。
六十年代中期,由于航空、航天、电子、原子能等工业的发展,电渣重熔在苏联、西欧、美国获得较快的发展,生产的品种包括:优质合金钢、高温合金、精密合金、耐蚀合金以及铝、铜、钛、银等有色金属合金。
我国是世界上电渣冶金起步较早的国家之一,一九六〇年,重庆特殊钢厂、大冶特殊钢厂,大连钢厂及上钢五厂的电渣炉先后建成投产。
紧随其后齐齐哈尔钢厂、抚顺钢厂等工业电渣炉相继建成投产。
五十多年来,我国电渣冶金始终保持着旺盛的发展趋势。
随着我国科学技术突飞猛进的发展,航天航海、汽车制造、石油化工、电站建设、核设施、机械制造等诸多行业,以及军工事业的发展、列车提速等许多领域越来越发挥着电渣钢的作用。
目前最大的一座是原上海重型机器厂电渣炉,重熔钢锭重达200t,现在又筹建450t大型电渣炉。
2009年,我国电渣重熔钢生产能力已超过170万t。
50多年来国内外电渣冶金取得了突飞猛进的发展,新工艺、新技术层出不穷,形成了一个跨专业、跨行业的新学科。
2、现代炼钢方法转炉,电弧炉,电渣重熔炉,真空感应炉,真空自耗炉(电弧重熔炉),电子束重熔炉(EBR)等。
电渣重熔是一种炼钢方法,而不是炉外精炼。
炉外精炼方法有LF,VD,VOD,VAD,RH 等。
3、电渣重熔炉类型3.1按工艺特点分:普通电渣重熔炉,电渣熔铸炉,加压电渣炉,保护气氛(可控气氛)电渣炉,连铸式电渣炉,电渣离心浇注炉,电渣热封顶等。
可控气氛电渣重熔技术。
电渣重熔通常在大气下进行,重熔合金中的氧含量,取决于主要脱氧元素的浓度和该脱氧元素的氧化物在渣中的活度。
此外,渣池上的氧分压或多或少也会产生一定的影响。
过去通常采用往渣池中加入脱氧剂的方法对熔渣连续脱氧,但是这会导致熔渣成分的改变。
电渣重熔炼钢术
电渣重熔炼钢术
电渣重熔炼钢术是一种钢铁生产技术,是利用电弧产生高温并在电渣作用下熔化再冷却制成钢材的过程。
这种技术被广泛应用于制造高品质的合金钢和特殊材料,如高速钢、不锈钢等。
电渣重熔炼钢术的工艺过程如下:首先,在熔炉中加入废钢、铁合金和谷子,然后通电在炉内产生电弧,使炉内温度升高至4000°C以上,使原料熔化。
此时,炉内的电渣被加入,电渣中含有特殊的成分,能够吸收和清除钢液中的杂质,同时还能够调节钢液中的成分比例。
在制造特殊的钢材时,还需添加合适的合金元素。
最后,将炉内熔化的钢液倒入模具中进行冷却,得到成型的钢材。
这种工艺可以有效去除钢材中的气泡、杂质和不均匀的成分,从而提高钢材的品质、性能和使用寿命。
电渣重熔冶炼技术
电渣重熔冶炼技术电渣重熔冶炼技术是一种先进的冶金技术,其主要应用于金属材料的回收和再利用。
该技术利用电弧加热,将废旧金属材料熔化,通过电渣的作用,将杂质分离出来,得到高纯度的金属材料,从而实现资源的有效利用和环境的保护。
一、电渣重熔冶炼技术的原理电渣重熔冶炼技术是利用电弧加热将废旧金属材料熔化,通过电渣的作用,将杂质分离出来,得到高纯度的金属材料。
在电渣重熔冶炼过程中,电极和金属材料之间形成的电弧产生高温,将金属材料熔化。
同时,电极和金属材料之间的电流产生电渣,电渣起到了隔离空气和杂质的作用,使金属材料被分离出来,从而得到高纯度的金属材料。
二、电渣重熔冶炼技术的应用1. 废旧金属材料的回收和再利用废旧金属材料中含有很多有价值的金属元素,如铁、铜、铝等。
这些金属元素可以通过电渣重熔冶炼技术进行回收和再利用,从而实现资源的有效利用和环境的保护。
2. 金属材料的精炼和纯化电渣重熔冶炼技术可以将金属材料中的杂质分离出来,得到高纯度的金属材料。
这一过程可以对金属材料进行精炼和纯化,提高其质量和性能。
3. 金属材料的合金化电渣重熔冶炼技术可以将不同种类的金属材料进行熔合,形成合金材料。
这些合金材料具有更好的性能和应用价值,可以广泛应用于冶金、机械制造、航空航天等领域。
三、电渣重熔冶炼技术的优点1. 能够回收和再利用废旧金属材料,实现资源的有效利用。
2. 能够精炼和纯化金属材料,提高其质量和性能。
3. 能够将不同种类的金属材料进行熔合,形成合金材料,具有更好的性能和应用价值。
4. 能够实现无污染生产,保护环境。
四、电渣重熔冶炼技术的发展趋势随着社会经济的快速发展,金属材料的需求量越来越大。
电渣重熔冶炼技术的应用将会越来越广泛,发展前景十分广阔。
未来,电渣重熔冶炼技术将会更加智能化、自动化,实现无人化生产。
同时,电渣重熔冶炼技术将会与其他领域的技术相结合,形成更加高效、环保、节能的新型冶金技术,为人类的发展和进步做出更大的贡献。
- 1、下载文档前请自行甄别文档内容的完整性,平台不提供额外的编辑、内容补充、找答案等附加服务。
- 2、"仅部分预览"的文档,不可在线预览部分如存在完整性等问题,可反馈申请退款(可完整预览的文档不适用该条件!)。
- 3、如文档侵犯您的权益,请联系客服反馈,我们会尽快为您处理(人工客服工作时间:9:00-18:30)。
大型锻造用电渣重熔锭的冶炼工艺天津赛瑞机器设备有限公司闫崇榜林军福王刚刘元飞158********yanchongbang@摘要:结合大型筒形锻件产品的使用环境和技术条件,对大型电渣锭的电渣重熔工艺的编制进行了讨论。
重点阐述了三相电渣炉生产大型电渣锭时,工艺参数的设定原则和经验,并结合生产产品的生产技术指标对工艺的合理性进行了评价。
为今后此类产品的生产积累了经验。
关键词:筒形锻件大型电渣锭三相电渣炉工艺参数The Process of ESR Large Ingot with ForgingTianjin SERI Machinery Equipment Corporation LimitedYAN Chong-bang,LIN Jun-fu,WANG Gang and LIU Yuan-feiAbstract:The use of environmental and technical conditions of this combination of large tubular forgings products,preparation of large ESR ingot electroslag remelting process was discussed.Focuses on the production of large three-phase electroslag ingot,setting principle and experience of process parameters,Combined with the production index of the production technology products of technology rationality was evaluated.Accumulate experience for future production of such products.Key words:Cylinder forging;Large electroslag remelting ingot;Three-phase electroslag furnace;process parameters1引言电渣重熔在中型及大型锻件生产中,处于优势地位[1]。
随着国内大锻件生产能力的逐步增强,市场对电渣重熔锻件的需求量也逐渐增大。
在各种大型设备上,凡是较为关键的部件或主要受力部件都会采用大型锻件,复杂恶劣的工作环境,要求其必须拥有可靠性及安全性等特点,这也决定了大型锻件必须有着过硬的机械性能和超声波探伤等质量指标。
为了满足这些指标,又畏于大型铸锭的缩孔、疏松、偏析、夹杂物聚集等冶金缺陷,大多数厂家会选用电渣重熔锭作为原材料进行生产。
本文所述的大型电渣锭用于一种筒类锻件的生产,该锻件将用于一种大型挤压机,并且是该挤压机的关键部件。
该产品生产难度较大,国内关于大型电渣锭的生产经验较少,本文结合了我公司生产设备情况、工件技术要求和生产技术指标等数据,对电渣重熔工艺的编制过程及工艺合理性进行了讨论。
2生产设备简介在设计电渣重熔车间时,会根据产品大纲选择适当的炉型,实践证明了三相电渣炉生产较大型及大型电渣锭的可行性和可靠性[2]。
我公司的40t三相双支臂交替式电渣炉(下文简称40t炉)。
其变压器额定功率4500kVA,一次电压10kV,二次电压50-80V,二次电流3×18750A,单支臂承重3×5t=15t,电极行程4500mm,夹持电极最大长度6500mm。
该电渣炉采用三相供电制、双支臂结构,滚珠丝杠传动。
每个支臂每次可装卡三支电极,双支臂交替炼钢,三支电极的极心圆大小可调。
控制系统采用计算机自动化控制系统,可实现自动控制和手动控制。
交换电极采用人工手动操纵,变压器为三相有载有级调压。
可采用直径范围Φ1000~Φ1400的结晶器,生产8~42.5t电渣锭。
图1为40t 炉生产过程照片。
图140t电渣炉生产过程照片3产品技术要求该产品将用于大型挤压机的挤压筒,挤压筒是挤压机设备中的一个重要组成部分,其在作业时需要承受高温、高压、高摩擦的作用,工作条件十分恶劣[3]。
为了延长该挤压筒的使用寿命,减少工具损耗、降低生产成本,对此锻件提出了化学成分、非金属夹杂物、探伤、机械性能等方面的要求,在编制电渣重熔工艺时应充分考虑。
3.1产品的锻件草图产品锻件草图如图2,在编制锻造工艺过程中,通过锻件草图,并考虑锻比、钢锭的成材率等,给出所需电渣锭的尺寸及重量。
图2产品锻件草图3.2钢牌号化学成分要求本筒体锻件所选用的材质为5CrNiMo其化学成分范围为C:0.5-0.60;Si≦0.40;Mn:0.50-0.80;P≦0.015;S≦0.012;Cr0.50-0.80;Ni1.40-1.80;Mo:0.15-0.303.3非金属夹杂物要求该产品的技术要求中要求,锻件非金属夹杂物按GB10561-ASTM评级图评定,A、B、C、D类夹杂物均不大于2级。
3.4超声波探伤要求超声波探伤指标是电渣重熔过程控制的重点和难点,本文所述锻件产品的探伤要求如下:超声波的起始灵敏度按GB11880-89中的4.7条规定执行,并且满足:(1)锻件允许存在个别的、分散的、不大于当量直径Φ2mm的冶金缺陷。
(2)在100cm2的面积内,当量直径Φ2~4的冶金缺陷不得超过3个,其中当量直径Φ3~Φ4的冶金缺陷只允许有1个。
(3)允许有2~4个小于当量直径Φ2mm的冶金缺陷密集区,但每区不得超过10cm3,每区之间距不得小于150mm。
要满足上述的探伤要求,编制电渣重熔工艺时,必须着重考虑冶炼过程的稳定。
3.5力学性能要求需要经过电渣重熔的产品,力学性能要求一般都较为严格,此筒体也不例外,其技术条件中要求的力学性能要求为σb≧1000MPa;σ0.2≧900MPa;δ≧12%;Ψ≧40%;AKV≧20J;硬度294HB~332HB。
虽然电渣产品具有金属纯净、组织致密、成分均匀等特点,但是随着电渣锭型的不断增大,上述指标也会随之恶化,尤其是钢锭本身的“偏析”会对产品的塑性造成很大影响。
所以为了满足产品的技术要求,采用合理电渣重熔工艺起着关键性的作用。
3.6其他技术要求除上述指标外,该产品对锻件的锻比、晶粒度、磁粉检验、及尺寸外观检验等,也有着明确的要求,由于上述指标受电渣重熔工艺影响不大,此处暂不做讨论。
4电渣重熔工艺的制定目前,国内三相电渣炉较少,相关的生产经验数据很少,只有东北特钢等少数企业拥有三相电渣炉,且暂未总结出适用性较强的经验公式。
编制工艺时,只能通过与相关技术人员进行交流与平时生产经验的总结相结合,来确定工艺参数。
4.1结晶器与自耗电极的选用4.1.1结晶器的选用根据用户提出的产品尺寸来确定结晶器尺寸,这是选择基本控制参数的前提[1]。
根据我公司现有设备情况,决定选用Φ1350mm/1400mm×4150mm结晶器进行冶炼。
4.1.2自耗电极的选用自耗电极对整个电渣重熔过程和电渣产品的质量起着至关重要的作用,我公司所用自耗电极需外购,为了满足产品的技术要求,控制自耗电极的质量,对电渣重熔过程也是极为重要的。
自耗电极的采购技术协议中,规定了自耗电极的冶炼方法、化学成分、表面质量、低倍、气体含量、交货状态和硬度等要求。
除内在质量外,自耗电极的尺寸要经过计算。
其计算方式如下:(1)自耗电极直径的确定:单相电渣炉的自耗电极的直径,一般是根据填充比或填充系数确定,而三相电渣炉除考虑填充系数外还应考虑炉台的极心圆大小等因素。
在选用三相电渣炉使用电极坯料直径的时候主要考虑因素有,第一,填充系数不应过小,否则重熔过程不能正常进行。
我厂三相电渣炉在选择填充系数时一般在0.25±0.05。
第二,电极尺寸不能过大,否则电极无法进入。
图3自耗电极摆布示意图如图3,图中所示ΦW表示电极极心圆,ΦD1、D2分别表示结晶器的上、下口直径,Φd1、Φd2是电极坯可以选择的尺寸范围,δ标示安全间隙,三相电渣炉的安全间隙可与单相电渣炉相同。
我厂一般选择在大于等于100mm。
(2)自耗电极长度的选择双臂交替式电渣炉对自耗电极的长度要求并不严格。
确定自耗电极的长度是该考虑到设备的承载能力,原则上为了提高金属收得率,自耗电极的长度越长越好。
而且受三相电渣炉填充系数较小的影响,如果自耗电极过短可能造成一次熔化不完全的现象,从而增加交换电极次数,影响电渣重熔过程稳定性,并且造成热量浪费。
我公司受自耗电极来料所限,此工艺选择的电极坯料为模铸坯,故自耗电极的长度为模铸坯的锭身长度。
4.2工艺渣系的选用与渣量的确定电渣重熔渣系、配比和渣量的选择对电渣钢的冶金质量、熔炼技术经济指标以及环境保护具有重大的影响[1]。
综合考虑钢中合金元素的烧损、气体的去除、有害元素的去除、夹杂物的去除等方面,从而确定电渣工艺的渣制度。
4.2.1渣系的选择我公司常用渣系有二元渣系、三元渣系、五元渣系等。
本产品采用的钢种为5CrNiMo,其熔点大约在1475℃~1490℃范围内,除Si元素烧损较为严重以外,其余元素重熔前后均不会有明显变化,渣料方面无需考虑特殊控制。
故采用上述三种渣系均可,但因考虑到冶炼过程的稳定性和经济性,决定选用65F/0/5/30三元渣系。
4.2.2渣量的确定渣量的大小实际上是作为炉渣电阻大小的标志,它对于产品质量和冶金效率都有影响[1]综合考虑电渣冶炼过程的稳定性、经济型及可操作性,选择合适的渣高通过下式进行计算。
2G D H 4πρ 结渣渣渣式中G 渣——渣总量,kgD 结——结晶器截面尺寸,mmH 渣——渣池的高度,mm 经验参数ρ渣——渣料的密度,约2.5/g·cm -3应注意电渣锭尺寸的不同、高度不同,渣皮造成的渣池损耗有所差异,故设计渣量时应予以考。
4.2.3渣料的烘烤为了防止钢在电渣冶炼过程中增气,主要是防止增氢,电渣重熔所用的渣料,必须入电阻炉烘烤,在800℃保温至少8小时后随用随取。
4.3熔化速率电渣重熔的熔化速率是电渣制度综合表征函数,根据我公司的生产经验,合理的熔速对产品的内在质量控制起着决定性作用,大量的生产实践证明,熔速对产品的机械性能指标、探伤指标、偏析程度有很大影响。
综合产品技术要求及我公司的生产经验,熔化速率要求计算如下:V 熔=(0.75)D 结±30kg 。
4.4冶炼电制度结合结晶器尺寸、电极坯料填充系数等参数,考虑满足相应的熔速要求,冶炼电压电压范围应在40V~65V ,设定电压50~70V 。
冶炼电流1.3KA~1.5KA ,冶炼过程中需要实时监控熔化速度,根据熔速要求适时对电力制度进行调整。