JIT与精益生产方式概述(PPT 45页).ppt
JIT的精益生产管理PPT课件

• Improve product quality • Identify inefficient processes
Thus, save millions of dollars!!
2
Origin of JIT
Year
13
Globalization contd.
Shippers and receivers expect faster, smaller and reliable transportation
Present scenario Inventory costs are low Transportation distances are far
personnel, or technology Massive software installations for supply chain and inventory
management, with dubious returns
17
Recommendations
At times increased inventory protects producers against unpredictable demand fluctuations and breakdown in the supply chain
16
JIT programs that have exceeded optimum level of inventory reduction may exhibit some
of the following symptoms
Have not resulted in anticipated financial gains, or initial gains have diminished or reversed
工厂生产车间精益生产方式介绍员工JIT准时制生产培训PPT模板课件

目录
CONTENTS
主要原则
CARDINAL PRINCIPLE
主要原则
主要原则
基本内容
BASIC CONTENT
基本内容
基本内容
基本内容
项目实施
PROJECT IMPLEMENTATION
项目实施
管理实施
MANAGEMENT IMPLEMENTATION
管理实施
管理实施
工厂生产车间培训专用
基本概念
准时制生产方式(Just In Time简称JIT), 又 称 作 无 库 存 生 产 方 式 ( stockless production),零库存(zero inventories), 一个流(one-piece flow)或者超级市场生 产方式(supermarket production)。
物料需求计划是通过把生产环节与对物料的需求计划紧密地联在 一起,由此来降低需求的不确定性,从而降低库存水平。而准时 制运作强调对全部运作环节进行组织,使得各个运作环节在最恰 当的时间实施运作。看起来,定义是非常简单的,但是运作起来 的确不是一件轻松的事情。要想取得成功,企业需要对其内部的 态度和运作模式完全加以改变,同时还需要经过周密的计划和严 密控制、实施工作才行,这往往需要花费数年的时间。
JIT准时制 生产培训
汇报人:
基本特点
JIT的核心是追求一种无库存的生产系统,或使库 存达到最小的生产系统。为此而开发了包括“看 板””在内的一系列具体方法,并逐渐形成了一 套独具特色的生产经营体系。JIT以准时生产为出 发点,首先暴露出生产过量和其他方面的浪费, 然后对设备、人员等进行淘汰、调整,达到降低 成本、简化计划和提高控制的目的。
丰田公司的准时制采取的是多品种少批量、 短周期的生产方式,实现了消除库存,优化 生产物流,减少浪费目的。JIT生产方式的基 本思想是“只在需要的时候,按需要的量, 生产所需的产品”,也就是追求一种无库存, 或库存达到最小的生产系统。JIT的基本思想 是生产的计划和控制及库存的管理。所以, JIT生产模式又被称为“精益生产”。
JIT精益生产(价值30万的PPT)

造成等待的常见原因: ☆ 线能力不平衡
☆ 计划不合理 ☆ 设备维护不到位 ☆ 物料供应不及时
搬运浪 费
移动费时费力
空间、时间、人力和工具浪费 搬运过程中的放置、堆积、移
动、整理等都造成浪费。
浪费
多数手工作业 面向生产线
2H工位轮换 自主质量改进 (多技能)
案例 组装线员工技能评价表
姓名 张惠妹
插件1 插件2 插件3
△
●
○
自动 插件
●
焊接 组装1 组装2 检测
○
◎
◎
●包Biblioteka ●徐小凤 ●○◎
○
◎
○
△
多技能员工 金 庸 ○
△
●
△
◎
◎
韦小宝 ◎
○
○
●
F4
○
◎
●
○
◎
拉登 ◎
●
△
●
○
萨达姆 △
●
◎
●
不良造成额外成本
常见的等待现象: ☆ 材料损失
☆ 设备折旧 ☆ 人工损失 ☆ 能源损失 ☆ 价格损失
☆ 订单损失 ☆ 信誉损失
动作
浪费
多余动作 增加强度降低效率
常见的12种浪费动作:
① 两手空闲
⑦ 转身角度大
② 单手空闲
⑧ 移动中变换动作
③ 作业动作停止 ⑨ 未掌握作业技巧
④ 动作幅度过大 ⑩ 伸背动作
多品种 量大固然好, 品种也重要
高质量
构建不产生不良 的体系,全检或 零缺陷免检
低价格 将“干毛巾拧出 水”,消除浪费
准时制和精益生产培训课件(PPT 43页)
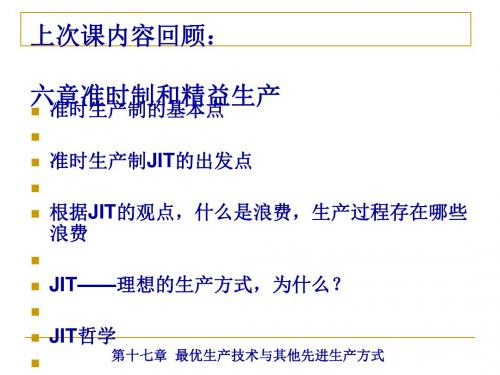
第2节 OPT的目标
Opt:企业真正的目标只有一个:赚钱 财务指标:
净利润 投资收益率 现金流量 作业指标: 产销率T——产销率指单位时间内企业获取的利润额,
是OPT对企业目标实现程度的关键度量标准 库存I 运行费OE OPT的主要贡献之一:财务指标→→作业指标
(1)MRP II要真正发挥企业的最大效能,仍存在一 些局限。
——MRP II系统虽然是根据生产线上的能力制定计划 的,但能力平衡时必然有一定的误差,为了应付企业 能力中的不确定因素,必须在提前期等指标上留有一 定的宽裕度,必然存在着一定的浪费,这就使MRP II 招致了一些!期!的批评。
—— 人员附属于生产线,积极性难以充分发挥。 ——重视事前计划,现场得不到充分的重视,易使管
资源A成为约束,原来的约束B已经被打破了。 于是又返回到第一步。如果没有这一步,人们 还以B为约束控制系统运行,影响了进一步改进。
第十七章 最优生产技术与其他先进生产方式
DBR系统
Drum----鼓点,Buffer----缓冲器,Rope----绳子DBR 系统是应用OPT另一个重要思想和工具。如图:
第十七章 最优生产技术与其他先进生产方式
第12章 OPT,MRP,JIT的比较
第四篇 生产运作系统的维护与更新
一、TOC与MRP II、JIT产生背景比较
第十七章 最优生产技术与其他先进生产方式
第十七章 最优生产技术与其他先进生产 Nhomakorabea式第十七章 最优生产技术与其他先进生产方式
第十七章 最优生产技术与其他先进生产方式
理人员产生惰性,不利于持续不断地改善管理。
第十七章 最优生产技术与其他先进生产方式
(2)JIT在生产管理中追求消灭一切浪费,但在我国目前的市场 环境中难以全面实现。
JIT精益生产PPT
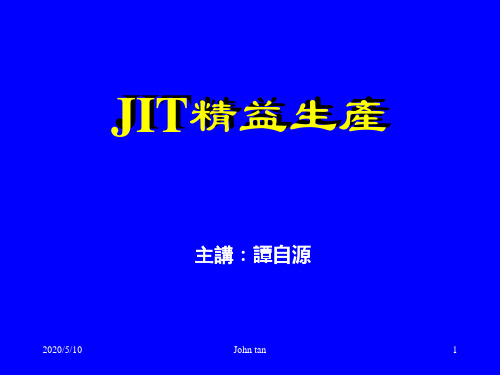
持續全員實踐
2018/7/21
John tan
11
3、精益生產追求的目標
7個“
零
”目標
☆ 零切換浪費 ☆ 零庫存 ☆ 零浪費 ☆ 零不良 ☆ 零故障 ☆ 零停滯 ☆ 零事故
12
2018/7/21
John tan
零目標
目的
現
狀
思考原則與方法
零 切換 浪費
多品種 切換時間長, 對應 切換後不穩定
7個“
JIT精益生產
主講:譚自源
2018/7/21
John tan
1
提要
1960年代開始,以豐田為代表的日本汽車製造 業通過實施JIT生產模式,以低成本、高質量的突出 優勢迅速佔領美國汽車市場,引發了美日之間長達 十年的汽車貿易戰。JIT——因其經營效率極限化被 美國學者讚譽為“精益生產”,並對人類的生產革 命產生了長遠影響。
利潤 實現
企業的使命實踐
市場 需求 企業 管理 產品 實現 顧客 滿意
2018/7/21
John tan
32
$
2018/7/21
增
值
工作的根本目的是給產品和服務 增加價值。 一切不增加對顧客和企業價值的 活動都是浪費。
John tan
33
3、企業常見的八種浪費
國內企業之大現狀: ☆ 現場混亂,插不進腳 ☆ 員工儀容不整,兩眼無光 ☆ 物料混放,標識不清 ☆ 設備故障不段,苟延殘喘 ☆ 人海戰術,加班加點但還是要待工待料
2018/7/21
John tan
6
不同力量主導的生產方式比較
項 目 生產企業主導 消費者主導
P(品種)
Q(品質)
少品種
jit准时制和精益生产.pptx

一)、JIT的形成与发展
4、精益生产的初期实践 大野耐一开发了冲压中的快速换模技术,
采用了滚子来移动模具配以简单的调整机 构,并由生产工人来承担更换模具的工作。 在西方是用几百台压床来制造汽车的所有 零部件,而大野的这项技术能够用少数几 条冲压线生产整部汽车。
17
一)、JIT的形成与发展
4、精益生产的初期实践 在试验的过程中,大野意外地发现,这样小批量
• JIT概念 • JIT基本思想 • JIT的主要方法 • JIT推进的主要步骤 教学难点 • JIT的主要方法
3
13.1 JIT的基本思想与主 要方法
4
一、生产方式的演变
1、手工生产阶段 福特汽车公司于1902年成立,推出了福特
设计的第一批产品——既实用又便宜的车型, 售价仅为850美元,获得了巨大的成功。 1905年福特公司每季度的销售量达到了 5000辆,成为同行中的佼佼者,至此,福 特汽车的巨大成功仅仅是初露端倪,究竟是 什么样的汽车最符合市场的需要,仍是悬而 未决的问题。
5
一、生产方式的演变
1906年,福特公司推出了8种车型,其中 售价最低为1000美元,最高为2000美元, 这一决策带来了灾难性的结果,销售量猛 然下降,迫使福特公司重新转向薄利多销。 次年,公司降低了售价,销售量魔术一般 地回升,尽管当时全美经济萧条已经开始, 但1906年到1907年间,福特车的顾客之多 是前所未有。
6
一、生产方式的演变
1908年,福特制定了一个划时代的决策,宣 布从此致力于生产标准化,只制造较低廉的 单一品种。
福特开发了新产品——T型车。T型车全身上 下找不到一丝装饰或华而不实之处,百分之 百地实用。它去掉了所有附件,规格一致, 以850美元一辆出售。与当时其他类型的汽 车相比,T型车具有经久耐用、构造精巧和 轻盈便利的优点。
JIT生产方式PPT课件
2020年10月2日
2
2.JIT 生产方式
生产情报和物品的流动
情报的流动 物品的流动
推的生产
计划需要量
生产计划
购入(外注 计划)
在制品的制造过程中 与目标不一致的加工方法, 发生顺序的浪费.
2020年10月2日
20
3.新生产方式的 7 大浪费 e.在库的浪费
※ 在库减少数10 成的话经费就会减少4 成
2020年10月2日
-利息负担的增大
(运转资金感到困难)
-产生维持在库费用 (保险, 仓库费, 资产税) -折旧的损失 (收益的恶化) -占据场所 (需要搁板, 仓库) -浪费作业的发生 (产生停体, 运搬, 不良等浪费) -多余的管理 (出入库记录, 在库调查等) -材料, 部品的事前使用 当其它的发注到来的时候不能使用 - 能源的浪费使用等
3.新生产方式的 7 大浪费
c.运搬的浪费
次工程
1. 运搬的实体 不必要的运搬距离, 重复运搬, 一时的停体, 运搬堆积
前工程
过度的分工 发生了运搬 的浪费
2. 发生的原因 ① 工程的过度分散 ② 过度的分工 ③ 继续增设工厂建筑 ④ LOT生产 ⑤ 没有停放位置, 停放标志
没有停放位置 停放标志,一时 性的堆放
平准化生产 生产 Lead-Time 减少
TPM 五行 不范围的改善活动
2020年10月2日
JIT生产在 新生产方式 体系中的位置
人力节 减
人力活用的最高 标准作业
准时化生产方式(jit)与精益生产方式(lp)共14页
准时化生产方式(JIT)与精益生产方式(LP)内容提要准时化生产方式(Just In Time, JIT)是日本在20世纪五六十年代研究和开始实施的生产管理方式,是一种有效地利用各种资源、降低成本的准则,其含义是:在需要的时间和地点生产必要数量和完美质量的产品和零部件,以杜绝超量生产,消除无效劳动和浪费,达到用最少的投入实现量大产出的目的。
JIT系统以准时生产为出发点,首先揭示出生产过量的浪费,进而暴露出其他方面的浪费(如设备布局不当、人员过多)然后对设备、人员等资源进行调整。
如此不断循环,使成本不断降低,计划和控制水平也随之不断提高。
80年代,随着日本企业在国际市场竞争中的胜利,准时化生产方式被作为日本企业成功的秘诀受到广泛的关注,现在JIT已在许多国家推广、运用,它是精益生产方式的核心。
第一节准时化生产方式的组成和目标一、准时化生产方式的组成JIT 生产方式由以下三方面组成:(一)JIT生产方式的新思维JIT之所以成功,首先是由于它大胆地向传统管理观念提出了挑战,使得生产管理的观念发生了巨大的变化。
JIT生产方式的新思维是JIT最基本的方面。
(二)JIT生产系统设计与计划技术为达到准时生产、杜绝浪费、合理利用资源,在JIT系统中要进行广义的生产系统设计。
JIT生产系统设计与计划技术体现JIT的新思维,同时为JIT的生产现场管理与控制打下基础。
(三)JIT生产现场管理JIT的零部件权当后续工序提出要求时才生产,是一种“拉动”的生产方式,后工序需要多少,前工序就生产或供应多少。
它将传统生产过程中前道工序向后工序送货,改为后道工序根据“看板”向前道工序取货。
看板系统是JIT生产现场控制技术的核心。
二、准时生产的目标JIT方式的目标是彻底消除无效劳动造成的浪费。
用专业化的术语来说明,JIT寻求达到以下目标:(1)废品量最低(零废品);(2)准备时间最短(零准备时间);(3)库存量最低(零库存);(4)搬运量最低;(5)机器损坏率低;(6)生产提前期短;(7)批量小。
JIT精益生产实务讲义(ppt 19页)
JIT精益生产实务
1
精益生产概论
1、何谓精益生产方式 2、现代生产组织系统 3、精益生产追求的目标 4、精益生产实施过程全貌 5、精益生产案例
2
1、何谓精益生产方式
L P ean roduction 精益生产,以低成本、高质量的突出优 势迅速占领美国汽车市场,引发了美日之间长达十年 的汽车贸易战。
2H工位轮换 自主质量改进 (多技能)
16
案例 组装线员工技能评价表
多技能员工
备注:△—计划学习,○—基本掌握,◎—完全掌握,●精通
17
案例 QC小组活动
Q C C uality ontrol ycle
针对主要的质量问题,由10名左右相关人员组 成改善小组,运用PDCA循环和质量改善工具,自主 进行不良分析并实施具体改善的质量活动。
推行QC小组活动的意义有: ● 通过小组式的学习型组织, 提高一线员工独立思考和相互启发的能力
● 通过QC手法的学习与运用, 加强企业的基础管理 ● 通过循序渐进渐进的课题活动, 创造有活力的工作场所 ● 发挥群众智慧,全员参与经营
18
案例
习惯
素养
6SK 5S
整理
整顿 清洁
清扫 健康
19
易
缺
足
难
14
J I T ust n ime
适品 · 适量 · 适时
适时化 生产
平稳化 生产
安定化 生产
流线化 生产
15
5、精益生产实施案例
中间在库0,一位停整线停
案例 松下电器大坂收音机工厂组装线
自动插件
插件1 插件2 插件3
焊接
自动
设备
JIT精益生产实务课件(PPT75张)
JIT精益生产实务
主讲:陈祖林
【讲师简介】
陈祖林
美国AITA国际职业顾问,注册培训师 ZERO Program 零牌专家组 首席顾问 中山大学管理学院MBA《组织文化》客座讲师 擅长业务:◎企业运营系统改善 · 现场管理 · 质量管理 · 生产管理 · 价值工程 ◎企业中层干部培养 工作外语:日语
16:00~16:40 16:40~17:10 17:10~17:30
中餐 练习:mini兴衰录 课程六 适时化生产 课程七 自主管理活动
练习:钎焊的烦恼 自由交流 培训总结、课程调查
·陈祖林 · 《JIT》系列课程之三
流线化生产
(一)流线化生产线 (二)流线化设备设计与调整
目
(一)流线化生产线 1、流线化生产的意义 2、流线生产与批量生产的区别 3、流线化生产的八个条件 4、流线化生产的建立 5、设备布置的三不政策 6、有弹性的生产线布置 7、流线生产的布置要点 8、一笔画的工厂布置
1、流线化生产的意义
冲压区 包装区 冲压
攻丝
装配
包装
攻丝区
装配区
水平布置
垂直布置
水平布置和垂直布置的比较
项目 水平布置 项目 垂直布置
方式
适用
相同功能的加工设备 集中摆放在同一区域
大批量生产
方式
适用
根据产品类别 按照加工顺序依此排列
柔性生产
特点 集中生产、集中搬运、 减少搬运次数
缺点 在制品搬运浪费大 等待时间长 生产周期长 空间占用大 造成“乱流”
离群 不 索居
对于涂装、电镀等大型加工设备, 由于生产环境的关系,通常安装在另外 一个隔离的地点,从而影响生产的流畅 性。
- 1、下载文档前请自行甄别文档内容的完整性,平台不提供额外的编辑、内容补充、找答案等附加服务。
- 2、"仅部分预览"的文档,不可在线预览部分如存在完整性等问题,可反馈申请退款(可完整预览的文档不适用该条件!)。
- 3、如文档侵犯您的权益,请联系客服反馈,我们会尽快为您处理(人工客服工作时间:9:00-18:30)。
1
10
2
9
3
8
4
7
5
6
(3)适时适量-Just In Time (JIT)
“只在必要的时候,按必要 的量,生产必要的产品” (Just In Time)。
如何实现适时适量生产?
推动生产系统 拉动生产系统
看板控制方式
生产计划
推动生产系统
工序A
工序B
工序C
库存
库存
完成
生产计划
拉动生产系统
工序A
工序B
丰田生产方式:日本汽车工业是怎 样崛起的?
JIT生产方式-市场多样化环境下 如何制造产品?
精益生产方式-如何赢得全球竞争?
精益生产方式的基本理念
获取利润
精
降低成本—彻底排除浪费
益
适时适量
弹性作业人数
质量保证
生
产
Just In Time (JIT)
少人化
“自动化”
方
式
生产批量极 小化
生产同步 化
六、现场管理与连续改进
连续改进的基本思想 从“5S”开始做起 分析与改进的工具
连续改进的基本思想
任何一个组织,在任何环境下,都有 改进的余地
改进的对象:产品与服务质量,工作 效率,业务流程,作业现场…….
贵在“连续” 全员参与
从“5S”开始作起
什么是“5S”? 1、整理: 区分生产现场必要和不必要的物品,将不必
·2至6个月一次
·存放在工作区附近
·至少1个月一次
·至少1周一次
·至少1天一次
·存放在个人工作点
·至少1小时一次
如何进行整理? -实施步骤(续)
步骤3:给不需要的物品贴上标签,并暂时存放在 指定的地点
步骤4:给贴上标签的物品分类,除去那些确实已 经无用的物品
步骤5:如果这些工作很费时,制定一个行动计划
现状
为什么
能否改进
新方案
原因 why 干的必要性 理由是否充分 有无新理由 新理由
对象 what 干什么 为何要干它 能否干别的 应该干什么
地点 where 何处干 为何在此干 能否在别处干 应在哪儿干
时间 when 何时干 为何在此时干 能否在其它 应在何时干
时间干
人员 who 由谁干 为何由他干 能否由别人干 应该由谁干
3
)
搬
运
的
浪
费
4
)
库
存
的
浪
费
5
)
动
作
的
浪
费
6)工序安排中的浪费
7)不合格品的浪费
操作
搬运
检查
等待
存储
生产过程中的各种活动
原材料
完成品
传统的生产过程
精益生产过程
精益生产方式的主要方法
获取利润
精
降低成本—彻底排除浪费
益
适时适量
弹性作业人数
质量保证
生
产
Just In Time (JIT)
少人化
“自动化”
4
15
89
12
5
14
6
13 12 11 10 9 8
7
7
1
6
2
5
3
4
第N月作业分配情况(作业者人数=8人)
1
10
2
9
3
8
4
7
5
6
12 34
5
18 17
6
3
4
2
7
1
8
5
123
4 6 98
5
76
16 7
3
4
15
89
12
5
14
6
13 12 10 11 9 8
7
7
1
6
2
5
3
4
第N+1月作业分配情况(作业者人数=6人)
场 步骤2:制定并张贴维护指南 步骤3:建立审查程序 步骤4:定期公布并张贴审查结果
分析与改进的工具
5W1H分析法 ECRS(四巧)技术 流程图 因果分析图 BPR
5W1H分析法
为什么这项工作是 必不可少的?
WHY 为什么
为什么这项工作要 以这种方式这种顺 序进行?
为什么为这项工作 制定这些标准?
如何进行清扫?
定义:打扫和擦拭,使生产场地和设备干净 实施步骤: 步骤1:彻底进行整理和整顿 步骤2:发现污染源(灰尘,油渍,冷却液,泄漏
等) 步骤3:分析原因 步骤4:制定计划并安排任务
如何进行维护?
定义:持续保持整理、整顿和清扫的效果 实施步骤: 步骤1:制定生产现场维护的责任表,并张贴在现
看板
工序C 看板
完成
存放位置
零件加工
生产看板
领取看板 装配线
看板运行示意图
精益生产方式下的供应商关 系
“命运共同体” JIT式的供应
供应商改进能力和技术 能力的提高
精益生产方式下的产品开发
并行工程 团队工作 供应商的早期参加
精益生产方式与大量生产方式的比较
所需人力资源 在制品库存 工厂占用面积 成品库存 产品质量
要的物品除去 2、整顿: 使必要物品的放置标准化,易于识别、易于
使用 3、清扫: 打扫和擦拭,使生产场地和设备干净 4、维护: 持续保持整理、整顿和清扫的效果 5、教养: 养成自觉遵守生产场地纪律和秩序的习惯
“5S”的目的
“物有其位,物在其位” 目视管理 提高安全性 现场工作效率的提高 职工良好行为习惯的养成
方
式
生产批量极 小化
生产同步 化
的
设备布 置
多面手
构
缩短作业更
后工序领
造
换时间
取
体
生产均衡化
系
看板方式
标准作业
目视控制
现场改善
(1)质量保证-“自动化”的含 义
融入生产组织中的两种机制
(1)设备运行机制: 使设备或生产线能够自
动检测不良产品,一旦发 现异常或不良产品即自动 停止。
(2)管理机制: 生产第一线的设备操作
的
设备布 置
多面手
构
缩短作业更
后工序领
造
换时间
取
体
生产均衡化
系
看板方式
标准作业
目视控制
现场改善
如何获取利润?
成本+%(利润)=价格 ቤተ መጻሕፍቲ ባይዱr
利润=价格-成本
如何降低成本?
彻底排除浪费
浪费的含义
“只使成本增加的生产 诸因素”
“不会带来任何附加 价值的诸因素”
七种浪费
1)过量生产的浪费
2)等待的浪费(工件等待、人员等待、设备等待)
浇铸 出炉频率 浇铸顺序
浇涛量 过热与否
金属成份 炉膛温度
冷却温度 铸模温度
表面有裂纹
时间拖延
缺乏部 门协调
无日程计划
收费不合理
无人关注 整个流程
无明确的标准 各部门自行其事
顾客不满意
管理体制
“顾客第一” 的观念
技能 业务流程设计
质量意识 工作责任感
无专人面对顾客
修理质量差
如何进行整理?
定义: 区分生产现场必要和不必要的物品,
将不必要的物品除去。
必要物品:支持日常作业,并经常使 用的物品。
如何进行整理? -实施步骤
步骤1:确定物品是否必须 步骤2:确定每件物品的使用频率-“优先权清单”
优先权 低
平均 高
优先权清单
使用频率
存放
·小于一年一次
·扔掉
·可能一年一次
·存放在较远的地方
生产现场整理行动计划
需要整理 的物品
存放 负责人 开始 目标 已完成
地点
时间
(%)
·无用的物品 和包装箱 ·废弃的工具 和设备 ·剩余维修物品 ·过量存货
如何进行整顿?
定义:使必要物品的放置标准化,易于识别、易 于使用
实施步骤: 步骤1:彻底进行整理 步骤2:确定每件物品的最大和最小量 步骤3:根据使用频率确定最适当的放置位置 步骤4:放置位置贴上明确的标签(用彩色标签) 步骤5:制定一个行动计划
工人发现产品或设备问题 时有权自行停止生产。
(2)弹性作业人数-“少人化”
根据生产量的变动,弹性增减各生产线 的人数;
尽量用较少的人力完成较多的工作。
如何实现弹性配置作业人数?
独特的设备布置-U型布置 “多面手” “标准作业”的制定和组合
入口
1
2
4
5
3
7
6
出口
8 9
10
12 34 5
大量生产方式 1 1 1 1
1
精益生产方式 1/2
1/10 1/2 1/4
3
精益生产方式的本质及其普遍意义
不仅仅是一种基于日本社会、文化及政 治背景的产物
包括生产经营全过程、全方位的生产和 经营模式(Lean production →Lean enterprise)
对企业如何高质量、低成本地创造价值, 赢得竞争的深刻思考(Lean thinking)
为什么完成这项工 作需要这些投入?
为什么这项工作需 要这种人员素质?
WHAT HOW
WHO WHERE
WHEN
这项工作的目的 何在?
这项工作如何能 更好完成?
何人为这项工作 的恰当人选?
何处开展这项工 作更为恰当?
何时开展这项工 作更为恰当?
5W1H分析法(续)