粉体粒度分布的测定激光法
激光粒度仪湿法测定粒径时粉体的分散方法
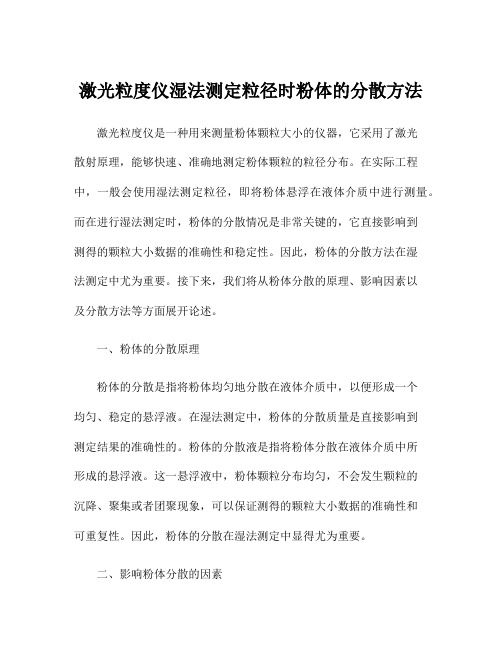
激光粒度仪湿法测定粒径时粉体的分散方法激光粒度仪是一种用来测量粉体颗粒大小的仪器,它采用了激光散射原理,能够快速、准确地测定粉体颗粒的粒径分布。
在实际工程中,一般会使用湿法测定粒径,即将粉体悬浮在液体介质中进行测量。
而在进行湿法测定时,粉体的分散情况是非常关键的,它直接影响到测得的颗粒大小数据的准确性和稳定性。
因此,粉体的分散方法在湿法测定中尤为重要。
接下来,我们将从粉体分散的原理、影响因素以及分散方法等方面展开论述。
一、粉体的分散原理粉体的分散是指将粉体均匀地分散在液体介质中,以便形成一个均匀、稳定的悬浮液。
在湿法测定中,粉体的分散质量是直接影响到测定结果的准确性的。
粉体的分散液是指将粉体分散在液体介质中所形成的悬浮液。
这一悬浮液中,粉体颗粒分布均匀,不会发生颗粒的沉降、聚集或者团聚现象,可以保证测得的颗粒大小数据的准确性和可重复性。
因此,粉体的分散在湿法测定中显得尤为重要。
二、影响粉体分散的因素1.粉体的本身性质粉体的本身性质对于分散性有着重要的影响。
不同的粉体其本身的粒径大小、形状、表面性质等都会对分散性产生影响。
比如,颗粒大小较小、表面粗糙的粉体往往更难分散,而颗粒大小较大、表面光滑的粉体更容易分散。
2.分散剂的选择在粉体分散中,有时需要添加一些分散剂来帮助粉体均匀地分散在液体介质中。
不同的粉体所需的分散剂也会有所不同。
常用的分散剂有表面活性剂、分子量较大的聚合物等。
3.搅拌速度和时间在进行粉体分散时,搅拌速度和搅拌时间对于分散的效果有着显著影响。
适当的搅拌速度和时间可以帮助粉体均匀地分散在液体介质中。
4. PH值的调节部分粉体需要在特定的PH值条件下进行分散。
在进行分散前,可以通过调节液体介质的PH值来使得粉体更容易分散。
5.温度的控制温度对于某些粉体的分散也会产生影响。
一些粉体在较高的温度下分散效果更好,而另一些粉体则在低温下更容易分散。
三、湿法粉体分散的方法1. Mechanochemical effect机械化学作用通常通过使用高速剪切机、分散机或搅拌机等设备来实现。
钨粉粒度分布

钨粉粒度分布
钨粉是一种重要的工业材料,广泛应用于金属切削、矿山、冶金、化工、航空航天等领域。
钨粉的粒度分布对其性能和应用有很大影响。
本文将介绍钨粉粒度分布的测试方法、影响因素及应用领域。
钨粉粒度分布的测试方法
钨粉粒度分布的测试方法主要有:筛分法、沉降法、激光粒度仪法等。
筛分法:通过筛网将钨粉分级,测量各级别的质量百分比,从而得到粒度分布。
筛分法操作简便,但精度较低。
沉降法:通过测量钨粉在液体中的沉降速度,计算颗粒的粒度分布。
沉降法操作较复杂,但精度较高。
激光粒度仪法:利用激光散射原理,测量钨粉颗粒的粒度分布。
激光粒度仪法测试速度快、精度高,是目前常用的测试方法。
钨粉粒度分布的影响因素
钨粉粒度分布受以下因素影响:
钨矿石的品质:钨矿石中的钨含量、杂质含量、矿物结构等都会影响钨粉的粒度分布。
冶炼工艺:冶炼过程中温度、压力、还原剂等条件的控制会影响钨粉的粒度分布。
粉碎工艺:粉碎过程中转速、时间、料球比等参数的选择会影响钨粉的粒度分布。
钨粉粒度分布的应用领域
不同粒度分布的钨粉适用于不同的应用领域:
细粒度钨粉:适用于金属切削、矿山、冶金等领域,具有高硬度、良好的耐磨性。
中粒度钨粉:适用于化工、催化剂等领域,具有较高的表面积,有利于提高催化性能。
粗粒度钨粉:适用于航空航天、喷涂等领域,具有较好的强度和抗冲击性。
总之,钨粉粒度分布对其性能和应用具有重要影响。
通过选择合适的测试方法和工艺条件,可以制备出具有特定粒度分布的钨粉,以满足不同领域的需求。
粉体粒度及其分布测定
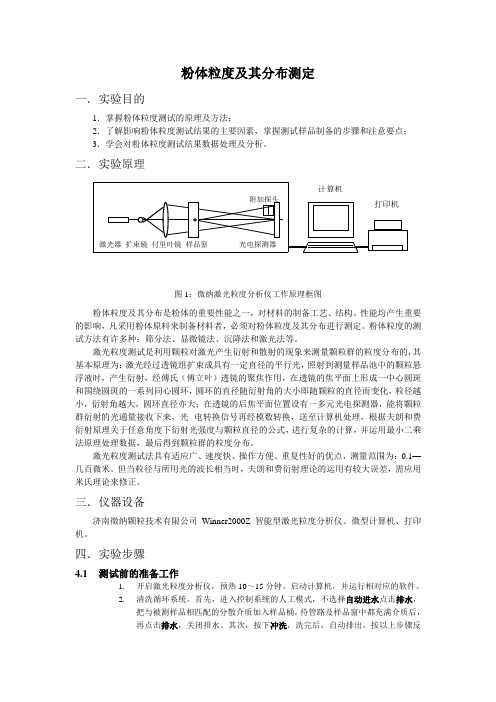
粉体粒度及其分布测定一.实验目的1.掌握粉体粒度测试的原理及方法;2.了解影响粉体粒度测试结果的主要因素,掌握测试样品制备的步骤和注意要点;3.学会对粉体粒度测试结果数据处理及分析。
二.实验原理图1:微纳激光粒度分析仪工作原理框图粉体粒度及其分布是粉体的重要性能之一,对材料的制备工艺、结构、性能均产生重要的影响,凡采用粉体原料来制备材料者,必须对粉体粒度及其分布进行测定。
粉体粒度的测试方法有许多种:筛分法、显微镜法、沉降法和激光法等。
激光粒度测试是利用颗粒对激光产生衍射和散射的现象来测量颗粒群的粒度分布的,其基本原理为:激光经过透镜组扩束成具有一定直径的平行光,照射到测量样品池中的颗粒悬浮液时,产生衍射,经傅氏(傅立叶)透镜的聚焦作用,在透镜的焦平面上形成一中心圆斑和围绕圆斑的一系列同心圆环,圆环的直径随衍射角的大小即随颗粒的直径而变化,粒径越小,衍射角越大,圆环直径亦大;在透镜的后焦平面位置设有一多元光电探测器,能将颗粒群衍射的光通量接收下来,光--电转换信号再经模数转换,送至计算机处理,根据夫朗和费衍射原理关于任意角度下衍射光强度与颗粒直径的公式,进行复杂的计算,并运用最小二乘法原理处理数据,最后得到颗粒群的粒度分布。
激光粒度测试法具有适应广、速度快、操作方便、重复性好的优点,测量范围为:0.1—几百微米。
但当粒径与所用光的波长相当时,夫朗和费衍射理论的运用有较大误差,需应用米氏理论来修正。
三.仪器设备济南微纳颗粒技术有限公司Winner2000Z智能型激光粒度分析仪、微型计算机、打印机。
四.实验步骤4.1测试前的准备工作1.开启激光粒度分析仪,预热10~15分钟。
启动计算机,并运行相对应的软件。
2.清洗循环系统。
首先,进入控制系统的人工模式,不选择自动进水点击排水,把与被测样品相匹配的分散介质加入样品桶,待管路及样品窗中都充满介质后,再点击排水,关闭排水。
其次,按下冲洗,洗完后,自动排出。
粉体粒度测试实验报告
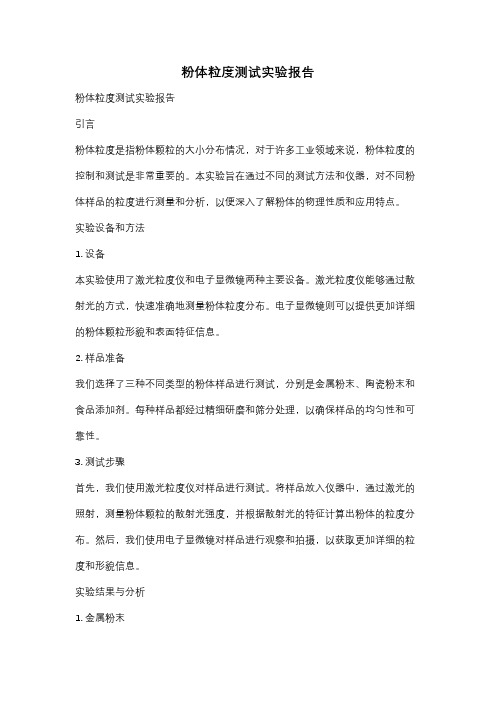
粉体粒度测试实验报告粉体粒度测试实验报告引言粉体粒度是指粉体颗粒的大小分布情况,对于许多工业领域来说,粉体粒度的控制和测试是非常重要的。
本实验旨在通过不同的测试方法和仪器,对不同粉体样品的粒度进行测量和分析,以便深入了解粉体的物理性质和应用特点。
实验设备和方法1. 设备本实验使用了激光粒度仪和电子显微镜两种主要设备。
激光粒度仪能够通过散射光的方式,快速准确地测量粉体粒度分布。
电子显微镜则可以提供更加详细的粉体颗粒形貌和表面特征信息。
2. 样品准备我们选择了三种不同类型的粉体样品进行测试,分别是金属粉末、陶瓷粉末和食品添加剂。
每种样品都经过精细研磨和筛分处理,以确保样品的均匀性和可靠性。
3. 测试步骤首先,我们使用激光粒度仪对样品进行测试。
将样品放入仪器中,通过激光的照射,测量粉体颗粒的散射光强度,并根据散射光的特征计算出粉体的粒度分布。
然后,我们使用电子显微镜对样品进行观察和拍摄,以获取更加详细的粒度和形貌信息。
实验结果与分析1. 金属粉末经过测试,金属粉末的粒度分布主要集中在10-50微米之间,呈现出较为均匀的分布特征。
电子显微镜观察发现,金属粉末颗粒表面较为光滑,形状规则,没有明显的凹凸和气孔。
这种粉末粒度适中,适合用于金属材料的加工和制备。
2. 陶瓷粉末陶瓷粉末的粒度分布相对较宽,主要分布在1-100微米之间。
电子显微镜观察发现,陶瓷粉末颗粒形状不规则,表面粗糙,存在一定数量的微小颗粒和孔隙。
这种粉末粒度分布广泛,适合用于陶瓷材料的制备和涂料的添加。
3. 食品添加剂食品添加剂的粉体粒度要求相对较高,需要粒度分布较为均匀,颗粒形状规则。
经过测试,食品添加剂的粒度主要分布在1-100微米之间,整体呈现出较为均匀的分布特征。
电子显微镜观察发现,食品添加剂颗粒表面光滑,形状规则,没有明显的杂质和气孔。
这种粉末粒度适中,适合用于食品加工和调味品的制备。
结论通过本次实验,我们成功地使用了激光粒度仪和电子显微镜对不同类型的粉体样品进行了粒度测试和分析。
《粉体工程》复习题

《粉体工程》复习题——海公公1平均粒径的表示方法有哪几种?个数平均径,长度平均径,面积平均径,体积平均径,平均表面积径,平均体积径,调和平均径,NND,MMD2粉体的粒度分布的测定方法有哪些?其测量基准和测量范围是什么?①显微镜法:颗粒的平面投影图像,普通光学:0.5-200微米;透射电子:几十纳米到几个微米;扫描电子:0.005-50微米②筛分法:以重量为基准20-100㎜③沉降法:在适当介质中颗粒沉降,导致光强度变化④激光衍射法:夫朗和弗衍射原理⑤比表面法:假定颗粒为均匀光滑球形⑥库尔特粒度仪:颗粒体积,电压脉冲,精度取决于被计数颗粒的数目0.5-200微米3试用斯托克斯定律说明用沉降法测定颗粒粒径的原理。
将均匀分散的颗粒悬浊液装入静置的透明容器里,颗粒在重力作用下产生沉降现象,会出现下部浓度大上部浓度小的浓度分布,面对这种浓度变化,从侧向投射光线,由于颗粒对光的吸收散射等效应,使光强减弱,其减弱的程度与颗粒的大小和浓度有关,所以通过光强度变化能反映悬浊液内粉末的粒径组成。
4形状系数和形状指数的意义是什么?形状系数:是用来衡量实际颗粒形状与球形或长方形颗粒形状的差异程度;形状指数:是对单一颗粒本身几何形状的指数化,它是根据不同的使用目的,给出颗粒理想的形状图像,然后将理想的形状与实际形状进行比较,找出二者之间差异并指数化。
5用等大球体的规则充填和不规则充填,及不等大球的充填试验研究结果,说明如何才能获得最紧密充填?以等径球最紧密堆积为例,在形成最密堆积后,空间存在四个球构成的四面体空隙和有六个球构成的八面体空隙。
若基本等径球为E,填入八面体最大径球为2次球J,填入四面体空隙最大等径球为3次球K,再填入4次最大径球与1、2间隙,填5次球最大径球于1、3次球间隙,最后以更微小等径球填入残留空隙,从而构成最紧密填充,即Horsfield填充。
6颗粒密度是如何定义的?何谓真密度,表观颗粒密度?它们之间的区别在哪里?颗粒质量除以表观体积;真密度:是指颗粒的质量除以不包括开孔,闭孔在内的颗粒真体积;表观颗粒密度:颗粒的质量除以包含闭孔在内的颗粒体积。
粉体粒度的检测方法

粉体粒度的检测方法
粉体粒度是指粉末颗粒的大小分布情况,是粉末物料的重要物理性质之一。
粉体粒度的检测方法主要有激光粒度分析法、显微镜法、筛分法、沉降法等。
激光粒度分析法是一种常用的粉体粒度检测方法。
该方法利用激光散射原理,通过测量散射光的强度和角度,计算出粉末颗粒的大小分布情况。
该方法具有精度高、速度快、操作简便等优点,适用于大多数粉末物料的粒度分析。
显微镜法是一种直接观察粉末颗粒的大小和形状的方法。
该方法需要使用显微镜对粉末样品进行观察和测量,可以得到较为准确的粒度分布情况。
但该方法需要专业的技术人员进行操作,且速度较慢,适用于对粉末颗粒形状和大小的详细分析。
筛分法是一种常用的粉体粒度检测方法。
该方法利用筛网的不同孔径对粉末进行筛分,得到不同粒径的颗粒分布情况。
该方法操作简便,适用于颗粒较大的粉末物料的粒度分析。
沉降法是一种通过测量粉末颗粒在液体中的沉降速度来确定粒度分布的方法。
该方法需要将粉末样品与液体混合后进行沉降,通过测量沉降速度和时间,计算出粉末颗粒的大小分布情况。
该方法适用于颗粒较小的粉末物料的粒度分析。
不同的粉体粒度检测方法各有优缺点,应根据具体情况选择合适的方法进行粒度分析。
在实际应用中,可以结合多种方法进行综合分析,以得到更为准确的粉体粒度分布情况。
粉末粒度测试实验报告
粉末粒度测试实验报告实验名称:粉末粒度测试实验目的:通过粉末粒度测试,确定材料颗粒的平均粒径及大小分布情况,为材料的应用提供数据支持。
实验原理:粉末的粒度是指颗粒的大小。
常用的粒度分析方法有筛分法、激光粒度分析法等。
本实验使用的是激光粒度分析仪进行测试。
该仪器通过激光照射粉末样品,测量散射光的强度和角度分布,从而获得粉末的粒径分布情况。
实验步骤:1. 准备实验材料:将待测试的粉末样品取出,并加以充分搅拌,使样品均匀。
2. 调节仪器参数:打开激光粒度分析仪,根据样品特性调节适当的激光功率、散射角度以及测量时间等参数。
3. 校正仪器:按照仪器说明书的要求,进行零点校正、灵敏度校正等操作,确保仪器的准确性和可靠性。
4. 测试样品:将经过搅拌的粉末样品加入样品盖板,放入仪器中,开始测试。
5. 数据分析:通过仪器自动计算和生成粒度分布曲线,并得出平均粒径等相关数据。
实验结果及数据分析:根据激光粒度分析仪的测试结果,得到了粉末样品的粒径分布曲线和平均粒径。
根据实验数据,可以分析得出以下结论:1. 粉末样品的平均粒径为Xμm,说明样品的颗粒大小较为均匀。
2. 样品的粒径分布曲线呈现正态分布或偏态分布等特点,说明样品中存在不同粒径的颗粒。
3. 可以通过对粒径分布曲线的分析,进一步得到样品中粒径较大颗粒和微粒的分布情况,为材料的应用提供指导。
实验讨论及误差分析:在进行粉末粒度测试时,可能会存在一定的误差源。
主要包括以下几个方面:1. 样品制备的不均匀性:如果样品制备不均匀,会导致在测量过程中产生偏差。
因此,在实验中需充分搅拌样品,以保证样品的均匀性。
2. 仪器误差:激光粒度分析仪本身存在一定的误差。
使用过程中,需要按照仪器说明书的要求,进行校正和操作,以减小仪器误差的影响。
3. 测量环境的影响:实验室的温度、湿度等因素也会对测试结果产生一定影响。
因此,在实验中需要控制好实验环境,尽量减小外界因素的干扰。
实验总结:通过粉末粒度测试,我们可以得到样品的平均粒径和粒径分布情况。
dls粉体粒度测试方法的原理
dls粉体粒度测试方法的原理DLS(dynamic light scattering)是粉体粒度测试中常用的一种方法。
它是基于光散射现象,通过分析光束散射的光学信息,来获取粉体粒子的尺寸分布信息的。
DLS最初应用于分子生物学、胶体化学的研究中,后被应用于粉体粒度测试中。
DLS的粒度测试原理是,当一束激光照射在粉体粒子上时,由于粒子的存在,激光会被散射。
粒子的尺寸越小,散射光的角度越大,因此通过测量散射光的角度以及散射光的强度,可以计算出粒子的平均尺寸和尺寸分布情况。
具体来说,DLS通过测量散射光的相干光强度,获得被测样品的自相关函数。
这里所谓的自相关函数是指,测量一段时间内样品中粒子的几何特性的变化。
比如,当一个较大的粒子移动时,会影响到它周围的其他粒子,从而影响到散射光的强度。
通过对自相关函数进行分析,可以计算出样品中的粒子尺寸分布情况。
需要注意的是,DLS虽然非常便捷,但其仅仅适用于测量粒径在几纳米至几微米的粒子。
同时,DLS只能测量粒子的尺寸分布情况,并无法获得关于粒子形状和表面质量等更详细的信息。
因此,在进行粉体粒度测试时需要综合使用多种测试手段,以获取更全面和准确的粒子信息。
综上所述,DLS的粉体粒度测试原理基于光散射现象,通过测量散射光的角度和强度,来计算出样品的粒子尺寸分布情况。
DLS虽然简单易用,但需要注意其仅适用于粒径较小的粒子,同时并不能提供关于粒子形状和表面质量等更多的信息。
在进行粉体粒度测试时,需要根据实际情况选择合适的测试方法,并结合多种测试手段以获取更全面和准确的粒子信息。
粉体粒度测试方法、关键指标知识总结-精品
5、粒度分布的表示方法:①表格法:用表格的方法将粒径区间分布、累计分布一一列出的方法。
②图形法:在直角标系中用直方图和曲线等形式表示粒度分布的方法。
③函数法:用数学函数表示粒度分布的方法。
这种方法一般在理论研究时用。
如著名的Rosin-Rammler分布就是函数分布。
6、粒径和等效粒径:粒径就是颗粒直径。
这概念是很简单明确的,那么什么是等效粒径呢,粒径和等效粒径有什么关系呢?我们知道,只有圆球体才有直径,其它形状的几何体是没有直径的,而组成粉体的颗粒又绝大多数不是圆球形的,而是各种各样不规则形状的,有片状的、针状的、多棱状的等等。
这些复杂形状的颗粒从理论上讲是不能直接用直径这个概念来表示它的大小的。
而在实际工作中直径是描述一个颗粒大小的最直观、最简单的一个量,我们又希望能用这样的一个量来描述颗粒大小,所以在粒度测试的实践中的我们引入了等效粒径这个概念。
等效粒径等效粒径是指当一个颗粒的某一物理特性与同质的球形颗粒相同或相近时,我们就用该球形颗粒的直径来代表这个实际颗粒的直径。
那么这个球形颗粒的粒径就是该实际颗粒的等效粒径。
等效粒径具体有如下几种:①等效体积径:与实际颗粒体积相同的球的直径。
一般为激光法所测直径为等效体积径。
②等效沉速径:在相同条件下与实际颗粒沉降速度相同的球的直径。
沉降法所测的粒径为等效沉速径,又叫Stokes径。
③等效电阻径:在相同条件下与实际颗粒产生相同电阻效果的球形颗粒的直径。
库尔特法所测的粒径为等效电阻径。
④等效投进面积径:与实际颗粒投进面积相同的球形颗粒的直径。
显向镜法和图像法所测的粒径大多是等效投影面积直径。
激光粒度仪湿法测定粒径时粉体的分散方法
激光粒度仪湿法测定粒径时粉体的分散方法1.搅拌粉体样品并加入适量的溶剂,使其充分分散。
Mix the powder sample and add an appropriate amount of solvent to ensure full dispersion.2.使用超声波或搅拌器对粉体样品进行处理,以增加其分散性。
Use ultrasonication or a stirrer to treat the powder sample to enhance its dispersibility.3.确保搅拌过程中不产生气泡或振动,以防止分散效果的降低。
Ensure that no bubbles or vibrations are created during the stirring process to prevent the reduction of dispersion effects.4.使用适当的分散剂来增强粉体样品的分散性能。
Use appropriate dispersants to enhance the dispersibility of the powder sample.5.将分散后的样品放置一段时间,使其达到稳定状态。
Allow the dispersed sample to stand for a period of time to reach a stable state.6.避免在分散过程中引入过多的能量,以免影响后续的粒径检测结果。
Avoid introducing too much energy during the dispersion process to avoid affecting the subsequent particle size measurement results.7.在分散后及时进行粒度检测,以确保分散状态的准确性。
Conduct particle size measurements promptly after dispersion to ensure the accuracy of the dispersion state.8.对于难分散的样品,可以考虑采用特殊的分散技术来提高其分散效果。
- 1、下载文档前请自行甄别文档内容的完整性,平台不提供额外的编辑、内容补充、找答案等附加服务。
- 2、"仅部分预览"的文档,不可在线预览部分如存在完整性等问题,可反馈申请退款(可完整预览的文档不适用该条件!)。
- 3、如文档侵犯您的权益,请联系客服反馈,我们会尽快为您处理(人工客服工作时间:9:00-18:30)。
复合材料科学与工程实验指导书
实验:复合材料结构微观观察
一、实验目的
1. 了解几种典型复合材料的显微组织形貌特征;
2. 学会用定量金相的方法来测定增强相或基体的体积分数;
3. 掌握颗粒增强复合材料的密度及弹性模量的评估方法。
二、实验原理
混合定理:根据混合定理可以计算复合材料的性能。
对于标量性能,像密度、热熔,复合材料的性能是各向同性的并可以用最简单的混合定理来计算。
如复合材料的密度ρc 可用公式(1)来计算。
ρc =V m ρm +V f ρf (1)
式中ρm 和ρf 分别为基体与增强相的密度,V m 和V f 分别为基体与增强相的体积分数。
对于矢量性能如弹性模量、导电率,复合材料的性能与增强相的形状与取向有关。
如纤维增强复合材料弹性模量是各向异性的,在纤维方向的弹性模量E c 可用混合定理公式(2)来计算
E c =V m E m +V f E f (2)
式中E m 和E f 分别为基体与增强相的弹性模量。
如果增强体为颗粒状的复合材料,其弹性模量为各向同性,可用混合定理(3)来计算。
E c =V m E m +KV f E f (3)
式中K 为修正系数,与V f 和 E r /E m 的比值有关,其值通常在0.1 ~ 0.6。
体积分数:在计算复合材料性能时,要知道增强相和基体的体积分数。
由于复合材料不透明,不能直接观察三维空间图像,只能在二维截面上得到有关几何参数,然后运用数理统计的方法推断三维空间的几何参数。
如V f =L f (L f 为增强相的线长度分数 L f ),只要测出增强相的线长度分数 L f ,即可求得增强相的体积分数V f 。
用截线法测量增强相的线长度分数L f 如图1所示。
测量时,在显微组织照片上作任意直线,把落在增强相上的线段相加(L α=L 1+L 2+L 3+….),得总长度L α,然后除以测试线总长度L T ,即可求得增强相体积分数:
V f =L f =
T L L α (4)
图1截线法测量L f
用截线法测量L f 与放大倍数无关。
不过为提高测量精度,应考虑测量的截线数量,使用的截线总数越多,测量误差越小。
增强相尺寸:对于颗粒增强复合材料,一般用增强相直径大小表示增强相尺寸。
对于形状不规则的增强相可用平均截线长度L ′来表示其尺寸。
平均截线长度指在截面上任意测试直线穿过每个增强相颗粒的平均值。
L ′=P L α (5) 式中P 为测试线上增强相颗粒数。
三、仪器及材料
金相显微镜与数码图像处理系统;SiC 增强铝合金、Cu-W 合金、Al-Cu 复合材料、玻璃纤维增强聚酯树脂。
四、实验步骤
1. 观察并拍照复合材料试样
a) 利用显微镜观察一个复合材料试样,并用数码摄像仪进行拍照;
b) 记录该试样中增强材料与基体材料;
c) 按基体和增强材料对所观察试样进行复合材料分类。
2. 颗粒SiC 增强2024铝合金体积分数、密度和弹性模量计算
a) 用金相分析软件打开颗粒SiC 增强2024铝合金复合材料金相照片;用截线法测量照片中SiC 颗粒尺寸并 计算平均值L′;用截线法测量照片中SiC 颗粒的线长度分数 L f ;
b) 计算该复合材料中SiC 的体分数V f ;
c) 计算该复合材料的密度ρc 和弹性模量E c 。
d)。