精益生产--LPS--精益生产的由来
精益生产系统管理概述

精益生产系统管理概述引言精益生产系统是由日本丰田汽车公司所引进并发扬光大的一种生产管理体系。
它的核心思想是通过消除浪费,提高生产效率和质量,从而实现企业的可持续发展。
本文将围绕精益生产系统的概念、原则和应用进行详细介绍,以帮助读者深入了解并灵活运用精益生产系统管理技术。
一、精益生产系统定义精益生产系统(Lean Production System,简称LPS)是一种以供应链为驱动,以价值流为导向,通过消除浪费、流程优化和员工参与等策略,实现生产效率和质量的全面提升的管理方法。
它的核心是通过持续改进来降低生产成本、减少库存、提高交付能力和顾客满意度。
二、精益生产系统原则1.价值流观念精益生产系统强调以顾客为导向,将价值流定义为一系列能够满足顾客需求并使顾客满意的活动。
通过细致的价值流分析,找出生产中的浪费环节,并采取相应措施进行改进。
2. 流程优化流程优化是精益生产系统的核心内容之一。
通过优化流程,减少浪费,提高生产效率和质量水平。
其中包括以下几个方面的内容:•连续流:追求生产过程的顺畅流动,减少停工等待时间,降低库存。
•小批量生产:以小批量生产为目标,减少库存压力,提高灵活性。
•快速交付:追求快速交付产品,减少等待时间,提高顾客满意度。
3. 人员参与精益生产系统强调员工的积极参与和创新意识的发挥。
通过培训和激励机制,激发员工的创造力和工作积极性,实现全员参与,不断改善。
4. 持续改进持续改进是精益生产系统的核心理念之一。
通过PDCA循环(Plan-Do-Check-Act),不断地进行问题分析、解决和改进,使生产过程更加优化和高效。
三、精益生产系统的应用精益生产系统可以应用到各种规模和行业的企业中,包括制造业、服务业和非营利组织等。
下面以制造业为例,介绍精益生产系统在实际应用中的一些常见方法:1. 5S工作法5S工作法是精益生产系统中的一个重要工具,它通过整理、整顿、清扫、清洁和素养的步骤,实现工作环境的改善和生产效率的提高。
LP-精益生产
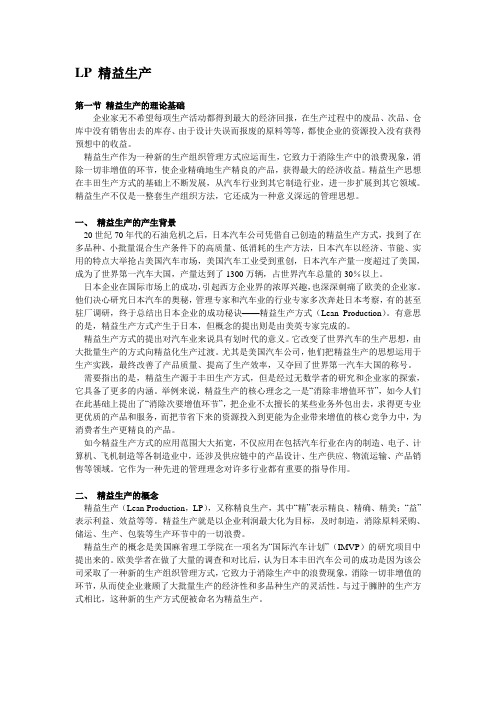
LP 精益生产第一节精益生产的理论基础企业家无不希望每项生产活动都得到最大的经济回报,在生产过程中的废品、次品、仓库中没有销售出去的库存、由于设计失误而报废的原料等等,都使企业的资源投入没有获得预想中的收益。
精益生产作为一种新的生产组织管理方式应运而生,它致力于消除生产中的浪费现象,消除一切非增值的环节,使企业精确地生产精良的产品,获得最大的经济收益。
精益生产思想在丰田生产方式的基础上不断发展,从汽车行业到其它制造行业,进一步扩展到其它领域。
精益生产不仅是一整套生产组织方法,它还成为一种意义深远的管理思想。
一、精益生产的产生背景20世纪70年代的石油危机之后,日本汽车公司凭借自己创造的精益生产方式,找到了在多品种、小批量混合生产条件下的高质量、低消耗的生产方法,日本汽车以经济、节能、实用的特点大举抢占美国汽车市场,美国汽车工业受到重创,日本汽车产量一度超过了美国,成为了世界第一汽车大国,产量达到了1300万辆,占世界汽车总量的30%以上。
日本企业在国际市场上的成功,引起西方企业界的浓厚兴趣,也深深刺痛了欧美的企业家。
他们决心研究日本汽车的奥秘,管理专家和汽车业的行业专家多次奔赴日本考察,有的甚至驻厂调研,终于总结出日本企业的成功秘诀——精益生产方式(Lean Production)。
有意思的是,精益生产方式产生于日本,但概念的提出则是由美英专家完成的。
精益生产方式的提出对汽车业来说具有划时代的意义。
它改变了世界汽车的生产思想,由大批量生产的方式向精益化生产过渡。
尤其是美国汽车公司,他们把精益生产的思想运用于生产实践,最终改善了产品质量、提高了生产效率,又夺回了世界第一汽车大国的称号。
需要指出的是,精益生产源于丰田生产方式,但是经过无数学者的研究和企业家的探索,它具备了更多的内涵。
举例来说,精益生产的核心理念之一是“消除非增值环节”,如今人们在此基础上提出了“消除次要增值环节”,把企业不太擅长的某些业务外包出去,求得更专业更优质的产品和服务,而把节省下来的资源投入到更能为企业带来增值的核心竞争力中,为消费者生产更精良的产品。
【实用资料】精益生产起源简介.doc

精益生产简介精益生产(Lean Production,简称LP)是美国麻省理工学院根据其在“国际汽车项目”研究中,基于对日本丰田生产方式的研究和总结,于1990年提出的制造模式。
目前,在众多的生产管理的新思想、新理论中,精益生产与MRPII(制造资源计划)的影响最为广泛,并进行过大量的实践。
在我国,精益生产与MRPII的应用也正广泛地展开。
此时,深入开展对精益生产与MRPII管理思想内核的研究,正是在实践中进一步有效推进工业工程的基础。
本文全面介绍精益生产。
1.精益生产的历史背景精益生产是起源于日本丰田汽车公司的一种生产管理方法。
其核心是追求消灭包括库存在内的一切“浪费”,并围绕此目标发展了一系列具体方法,逐渐形成了一套独具特色的生产经营管理体系。
1.1管理技术背景二战以后,日本汽车工业开始起步,但此时统治世界的生产模式是以美国福特制为代表的大量生产方式。
这种生产方式以流水线形式生产大批量、少品种的产品,以规模效应带动成本降低,并由此带来价格上的竞争力。
具体而言:在当时,大量生产方式即代表了先进的管理思想与方法。
大量的专用设备、专业化的大批量生产是降低成本、提高竞争力的主要方式。
与此同时,全面质量管理在美国等先进的工业化国家开始尝试推广,并开始在实践中体现了一定的效益。
生产中库存控制的思想(以MRPII思想为主)也开始提出,但因技术原因未能走向实用化。
1.2丰田式生产方式发展的环境当美国汽车工业处于发展的顶点时,日本的汽车制造商们是无法与其在同一生产模式下进行竞争的。
丰田汽车公司从成立到1950年的十几年间,总产量甚至不及福特公司一天的产量。
与此同时,日本企业还面临需求不足与技术落后等严重困难,加上战后日本国内的资金严重不足,也难有大规模的资金投入以保证日本国内的汽车生产达到有竞争力的规模。
此外,丰田汽车公司在参观美国的几大汽车厂之后还发现,在美国企业管理中,特别是人事管理中,存在着难以被日本企业接受之处。
精益生产的起源
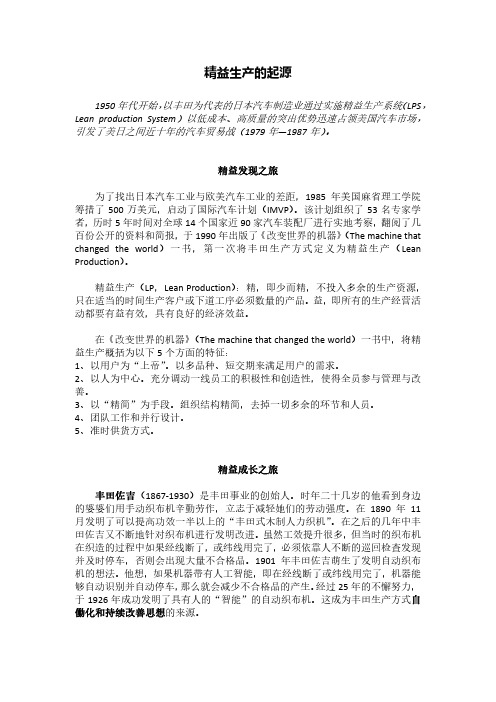
精益生产的起源1950年代开始,以丰田为代表的日本汽车制造业通过实施精益生产系统(LPS,Lean production System)以低成本、高质量的突出优势迅速占领美国汽车市场,引发了美日之间近十年的汽车贸易战(1979年—1987年)。
精益发现之旅为了找出日本汽车工业与欧美汽车工业的差距,1985年美国麻省理工学院筹措了500万美元,启动了国际汽车计划(IMVP)。
该计划组织了53名专家学者,历时5年时间对全球14个国家近90家汽车装配厂进行实地考察,翻阅了几百份公开的资料和简报,于1990年出版了《改变世界的机器》(The machine that changed the world)一书,第一次将丰田生产方式定义为精益生产(Lean Production)。
精益生产(LP,Lean Production):精,即少而精,不投入多余的生产资源,只在适当的时间生产客户或下道工序必须数量的产品。
益,即所有的生产经营活动都要有益有效,具有良好的经济效益。
在《改变世界的机器》(The machine that changed the world)一书中,将精益生产概括为以下5个方面的特征:1、以用户为“上帝”。
以多品种、短交期来满足用户的需求。
2、以人为中心。
充分调动一线员工的积极性和创造性,使得全员参与管理与改善。
3、以“精简”为手段。
组织结构精简,去掉一切多余的环节和人员。
4、团队工作和并行设计。
5、准时供货方式。
精益成长之旅丰田佐吉(1867‐1930)是丰田事业的创始人。
时年二十几岁的他看到身边的婆婆们用手动织布机辛勤劳作,立志于减轻她们的劳动强度。
在1890年11月发明了可以提高功效一半以上的“丰田式木制人力织机”。
在之后的几年中丰田佐吉又不断地针对织布机进行发明改进。
虽然工效提升很多,但当时的织布机在织造的过程中如果经线断了,或纬线用完了,必须依靠人不断的巡回检查发现并及时停车,否则会出现大量不合格品。
精益生产方式的历史发展过程

精益生产方式的历史发展过程精益生产是一种以减少浪费为核心的生产管理方法,它的发展经历了多个阶段。
本文将从精益生产的起源开始,逐步介绍其历史发展过程。
1. 起源精益生产起源于日本的丰田汽车公司。
20世纪50年代,日本汽车工业正处于起步阶段,丰田公司面临着生产效率低下、质量问题频发等困境。
为了改变这种局面,丰田公司邀请美国专家德鲁克来进行生产管理方面的指导。
德鲁克提出了“减少浪费”的理念,这成为了精益生产的核心。
2. 第一阶段:丰田生产方式丰田公司根据德鲁克的理念,开始进行生产流程的优化。
他们提出了“丰田生产方式”,强调通过精确的生产计划、合理的库存控制以及员工的积极参与来提高生产效率。
这一阶段的精益生产注重提高生产效率,减少不必要的浪费。
3. 第二阶段:丰田生产系统随着丰田公司逐渐摆脱了生产效率低下的困境,他们开始深入研究生产流程中的各个环节,并发展出了“丰田生产系统”。
这一阶段的精益生产注重优化生产流程,强调通过标准化、自动化和流程改进来提高生产效率。
丰田生产系统的核心原则是“Just-in-Time”(即时制),即在所需的时间和数量上实现生产和交付。
4. 第三阶段:精益生产精益生产是在丰田生产系统的基础上进一步发展起来的。
这一阶段的精益生产注重提高价值创造能力,将焦点放在满足客户需求和提供高质量产品上。
精益生产强调通过精确的需求预测、灵活的生产计划和快速的交付来实现客户价值的最大化。
5. 当前发展精益生产的理念和方法已经不仅局限于汽车行业,而是被广泛应用于各个领域。
在全球范围内,越来越多的企业开始采用精益生产方式来提高效率、降低成本、提高质量和客户满意度。
同时,随着数字化技术的发展,精益生产也与人工智能、大数据等技术相结合,为企业提供更加智能化和高效化的生产管理解决方案。
总结起来,精益生产方式的历史发展经历了起源阶段、丰田生产方式阶段、丰田生产系统阶段以及当前的精益生产阶段。
这一发展过程不仅改变了丰田公司的生产管理方式,也对全球范围内的企业生产管理产生了深远的影响。
精益生产起源简介
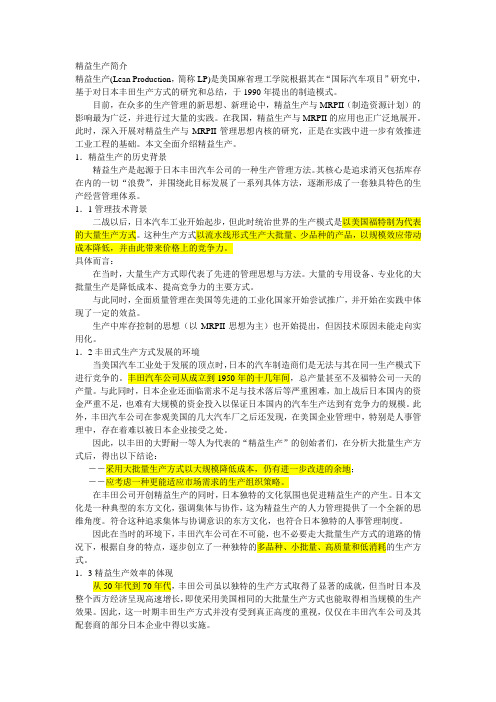
精益生产简介精益生产(Lean Production,简称LP)是美国麻省理工学院根据其在“国际汽车项目”研究中,基于对日本丰田生产方式的研究和总结,于1990年提出的制造模式。
目前,在众多的生产管理的新思想、新理论中,精益生产与MRPII(制造资源计划)的影响最为广泛,并进行过大量的实践。
在我国,精益生产与MRPII的应用也正广泛地展开。
此时,深入开展对精益生产与MRPII管理思想内核的研究,正是在实践中进一步有效推进工业工程的基础。
本文全面介绍精益生产。
1.精益生产的历史背景精益生产是起源于日本丰田汽车公司的一种生产管理方法。
其核心是追求消灭包括库存在内的一切“浪费”,并围绕此目标发展了一系列具体方法,逐渐形成了一套独具特色的生产经营管理体系。
1.1管理技术背景二战以后,日本汽车工业开始起步,但此时统治世界的生产模式是以美国福特制为代表的大量生产方式。
这种生产方式以流水线形式生产大批量、少品种的产品,以规模效应带动成本降低,并由此带来价格上的竞争力。
具体而言:在当时,大量生产方式即代表了先进的管理思想与方法。
大量的专用设备、专业化的大批量生产是降低成本、提高竞争力的主要方式。
与此同时,全面质量管理在美国等先进的工业化国家开始尝试推广,并开始在实践中体现了一定的效益。
生产中库存控制的思想(以MRPII思想为主)也开始提出,但因技术原因未能走向实用化。
1.2丰田式生产方式发展的环境当美国汽车工业处于发展的顶点时,日本的汽车制造商们是无法与其在同一生产模式下进行竞争的。
丰田汽车公司从成立到1950年的十几年间,总产量甚至不及福特公司一天的产量。
与此同时,日本企业还面临需求不足与技术落后等严重困难,加上战后日本国内的资金严重不足,也难有大规模的资金投入以保证日本国内的汽车生产达到有竞争力的规模。
此外,丰田汽车公司在参观美国的几大汽车厂之后还发现,在美国企业管理中,特别是人事管理中,存在着难以被日本企业接受之处。
精益导师考试指南

精益导师考试指南(Lean Production System, 简称LPS)是美国麻省理工学院数位国际计划组织的专家对日本“丰田JIT(Just In Time)生产方式的赞誉之称.起源于50年代的日本丰田汽车公司。
由美国国际汽车计划组织研究人员将之命名为精益生产。
●英文“LEAN”,是“瘦身”的意思。
中文取“精益”,其中“精”表示精良、精确、精美,即少而精;“益”表示利益、效益,即所有经营活动要有益有效,具有经济性。
●精益生产是一种系统的识别和剔除浪费的理念和方法。
●狭义的精益生产是生产系统的精益化。
广义的精益生产已超越了生产系统,就是企业的精益管理思想,精益管理思想的核心就是消灭一切浪费,为客户创造价值。
●精益生产的特点是剔除一切浪费、追求精益求精和尽善尽美,精简是它的核心.●精益生产的五个原则是指价值、价值流、流动、需求拉动、尽善尽美。
●精益生产系统的基础是5S、目视化管理、均衡化生产、料.设备.人力. 场地。
●通过及时生产,实现多品种、小批量的生产,消除生产现场中的无效劳动与浪费,最大限度地获取利润和效益●JIT基本要素:使用小巧、便宜的机器,设备. 逆时钟传送需求拉动定义“标准操作”并实施.(Beat)、“节奏”(Rhythm)或“速度” (Tempo).按节拍生产是精益生产的重要原则之一●节拍是指相继完成两件在制品或产品之间的时间间隔,通常以“秒”为单位,分为客户节拍及生产线节拍●节拍的计算是以客户的需求为基准●节拍计算公式:客户节拍=<净操作时间>/<客户需求量>●对生产线来讲,节拍就是完成一个产品的时间●节拍生产的规则:精益生产线必须按照设定的节拍生产每一个工位的员工都按照设定的相应的节拍生产.每个员工必须熟知自己所在生产线的生产线节拍和操作员节拍并达成节拍设定的生产进度,零件始终处于不停滞、不堆积、不超越,按节拍一个一个的流动的生产方法, 该方式可以消除库存的浪费并且及时发现异常.●所谓拉动生产,就是以客户需求为动力,以“看板”为链条,由后向前层层拉动每道工序的生产,从而达到按时按量提供所需产品。
精益生产简介
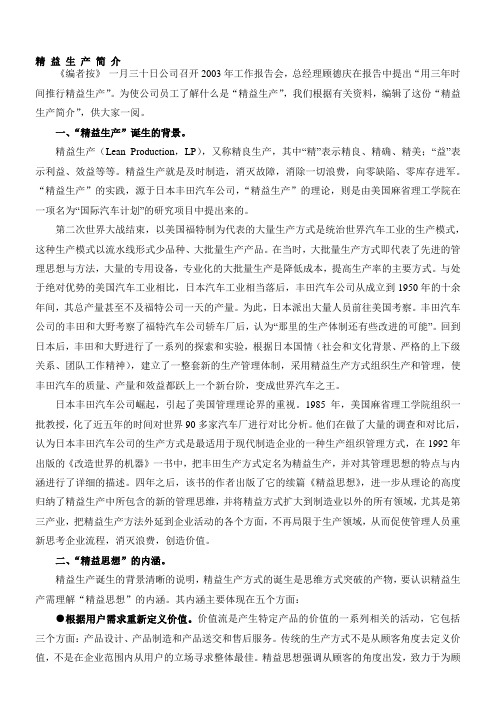
精益生产简介《编者按》一月三十日公司召开2003年工作报告会,总经理顾德庆在报告中提出“用三年时间推行精益生产”。
为使公司员工了解什么是“精益生产”,我们根据有关资料,编辑了这份“精益生产简介”,供大家一阅。
一、“精益生产”诞生的背景。
精益生产(Lean Production,LP),又称精良生产,其中“精”表示精良、精确、精美;“益”表示利益、效益等等。
精益生产就是及时制造,消灭故障,消除一切浪费,向零缺陷、零库存进军。
“精益生产”的实践,源于日本丰田汽车公司,“精益生产”的理论,则是由美国麻省理工学院在一项名为“国际汽车计划”的研究项目中提出来的。
第二次世界大战结束,以美国福特制为代表的大量生产方式是统治世界汽车工业的生产模式,这种生产模式以流水线形式少品种、大批量生产产品。
在当时,大批量生产方式即代表了先进的管理思想与方法,大量的专用设备,专业化的大批量生产是降低成本,提高生产率的主要方式。
与处于绝对优势的美国汽车工业相比,日本汽车工业相当落后,丰田汽车公司从成立到1950年的十余年间,其总产量甚至不及福特公司一天的产量。
为此,日本派出大量人员前往美国考察。
丰田汽车公司的丰田和大野考察了福特汽车公司轿车厂后,认为“那里的生产体制还有些改进的可能”。
回到日本后,丰田和大野进行了一系列的探索和实验,根据日本国情(社会和文化背景、严格的上下级关系、团队工作精神),建立了一整套新的生产管理体制,采用精益生产方式组织生产和管理,使丰田汽车的质量、产量和效益都跃上一个新台阶,变成世界汽车之王。
日本丰田汽车公司崛起,引起了美国管理理论界的重视。
1985年,美国麻省理工学院组织一批教授,化了近五年的时间对世界90多家汽车厂进行对比分析。
他们在做了大量的调查和对比后,认为日本丰田汽车公司的生产方式是最适用于现代制造企业的一种生产组织管理方式,在1992年出版的《改造世界的机器》一书中,把丰田生产方式定名为精益生产,并对其管理思想的特点与内涵进行了详细的描述。
- 1、下载文档前请自行甄别文档内容的完整性,平台不提供额外的编辑、内容补充、找答案等附加服务。
- 2、"仅部分预览"的文档,不可在线预览部分如存在完整性等问题,可反馈申请退款(可完整预览的文档不适用该条件!)。
- 3、如文档侵犯您的权益,请联系客服反馈,我们会尽快为您处理(人工客服工作时间:9:00-18:30)。
二次世界大战时美国人在太平洋战场上击败了日本,而日本全心的模仿了美国,以至于美国人出专 用资金和派遣大批的学者研究日本
5/14/2015
7
精益生产方式的5个特征
工厂组织、产品设计、供货环节、顾客和企业管理;理解成对外以用户为上帝,对内以“人”为中
心,在组装机构上以“精简”为手段,在工作方法上采用“Team Work”(综合工作组)和并行设计
制造成本组成
利润Profit 行政管理费用 G&A
Direct Material 直接材料费用 Direct labor 直接人工費用 Indirect 间接費用
价格
总成本 Total Cost
Cost of Goods Sold
PRICE
制造成本
企业的经营理念
可分为三种 成本中心型 、售价中心型和利润中心型 1.成本中心型 以计算或实际的成本为中心,加上预先设定好的利润而得出的售价,这种经营理念称之为成本中 心型。 售价=成本+利润 例如:生产成本100元,利润设定20元那么售价就为120元。这是供不应 求时,垄断产品,例如:油、电、气、通信等甚至火车票都是,这个也是用文化大革命时期计划经 济 2.售价中心型 在供大于求是,以售价为中心,当市场降低的时候利润也随之降低。 利润=售价-成本 例如:目前小挖供不应求时,我们说多少就是多少,可是到今天济宁遍地都 是小挖,那么有些缺乏改善和竞争力的企业,采用降价,那么成本不变的情况下,利润就降下来了 。慢慢降降,当售价接近或是低于成本的时候,企业就走不动了,下一步面临的将是停产 3.利润中心型 以利润为中心,当市场售价降低时,成本也必须降低,使获得的利润不会减少 即,成本=售价-利润 这是现代企业追寻的目标。 其实数学角度来看这些都是一样的,但是理念的不同,最终的结果却大相径庭。
人员组建的做功能设计组,对产品的开发和生产具有很强的指导和集成能力。综合负责的一个产品
型号的开发和生产,包括设计、工艺设计、编制预算、材料购置、生产部准备及投产等方面,并根 据实际情况调整原有对计划和设计。
5.准时供货 最小的库存,最少的在制品
6.“零”缺陷 对质量问题的“零”容忍,最低的成本、最好的质量、无废品、零库存与产品多样
单件手工生产
1776
1920
1950
1990
(年份)
第一次工业革命 18世纪60年代-19世纪70年代;第二次工业革命—20世纪初 这个阶段都隶属于到批量生产方式,这个历史上我们都学过
5/14/2015
5
丰田生产模式(TPS,Toyota Production System)
丰田生产方式是由丰田公司的第一任总经理丰田喜一郎根据日本市场的需求创造出来的,经丰田公 司原总经理大野耐一在近20年得以完善的生产方式。主要是二战以后 ,日本经济萧条,生产效率 低下,日本的汽车行业生产效率只有美国的1/9—1/8要想发展不可能全面引进美国的设备,丰田喜 一郎引进了福特的传送带技术,加以改造,而后来大野耐一根据美国的自由超市的启迪,发明了拉 动式生产同时开发了看板等一系列的管理工具。因此早期的大野管理模式。直到1962年才被正式 命名为TPS,到1974年才公布于世。
3.以“精简”为手段 去掉一切多余环节,将层次细分工,横向打破部门障碍,管理模式平行网络,减
少非直接员工作业,采用管理工具最大限度的减少库存,减少场所、设备等,减少工艺复杂性,提 供多样产品。
5/14/2015
8
4. Team Work和并行设计 精益生产强调的是以Team Work工作方式的并行设计。是由各部门专业
精——少而精 ,不投入多余的生产要素,只要在适当的时间生产必要
数量的市场急需产品(或是下一道工序急需的产品)
益——所有经营活动都要有效有益,具有经济效益
5/14/2015
*接下来就是精益生产的发展史
4
精益生产的发展其实社会生产方式的演变
1990 1955 1913
精益生产
丰田生产方式
大批量生产方式
5/14/2015
利润 售 价 成 本
利润
成 本
售 价
1. 成本型:售价= 成本 + 利润
利润
售 价
3.利润型.:成本= 售价—利润
成 本
5/14/2015
2.售价型:利润= 售价—成本
14
丰田的管理模式 很多都源于日本的生活我们这一代是看着《蜡笔小新》长大的,里面的很多故事情节还有日本大地 震以后日本人的有序安置等
5/14/2015
6
丰田生产模式 向精益生产模式的演变
到20世纪80年代末—美国的市场份额被日本慢慢吞噬,这样很多的美国人就去研究日本的经济,并
尝试借鉴。1985年美国麻省理工学院—制定了-{国际汽车计划}-用了近5年53位专家和学者对14个国
家90家汽车装配厂实地考察,对比分析后,1990年出版了《改变世界的机器》将丰田模式定名为: 精益生产方式,这里将丰田生产模式从生产制造领域扩展到产品研发、协作配套、销售服务、财务 管理等各个领域,贯穿企业生产经营活动的全部过程。(熟悉汽车的都知道目前的销售冠军是通用,
最盈利的是丰田,财务管理成本最低的汽车制造业)
5/14/2015
3
什么是精益生产 精益生产(Lean Production System) :是通过系统结构、人员组织、 运行方式和市场等方面的变革,是生产系统能够很快的使用用户的需 求的不断变化,并能使一切生产过程中取用、多余的东西被简化,最
终达到包括市场供销在内的生产各方面最好的结果。
(我们在做想要一个详细的定义,这个定义是我们国人北京航空航天大学的一个教授给 定义的,我们理解下面的就行)
,在供货方式上采用“JIT”方式,在最终目标方面“零缺陷”
1.以用户为上帝 生产的东西就是销售给客户的 , 多产品面向不同客户优良的品质、快速的交货、优质 的服务 2.以“人”为中心 人是企业的主体,所有的活动都有人为展开,积极发挥员工的积极性和创造性。管 理层下放部分权利,使人人有权,人人有责(现在中央都进行权利下放了),满足员工的学习新知 识和实现价值的愿望,一定形成具有竞争意识的的企业文化团队。催进度忙的一团糟 不合格品就像水中的葫芦此起彼伏 新员工老是出问题 人手从来不够用 物料随处可见却找不到自己想要的 生产效率一直上不去
不要着急!我们一 起分析。来吧!
5/14/2015
2
不管当前如何,部门里的人都会说一句 “忙”,可是等你要结果的时候,他还是 一句很效率的话“忙,还没有出来
5/14/2015
10
第二章 精益生产基本思想
1、生产成本的真谛
成本!成本!还是成本!!!! 效率!效率!还是效率!!!! 市场竞争的激烈与产品同质化压力,制造型企 业要获取生存空间,降低成本成为主要渠道。
无论是什么样的企业,都是以盈利为目的。那什么是盈利呢?在商业上,盈利是只对 购进的商品以购进价格加上一定比率进行的销售,这个比率即是商人的盈利;我们 制造业的赢利是指购进生产加工的原材料,用自己的继续设备,雇佣工人进行生产加工 ,使原材料的附加值在生产中增值,让后卖给消费者,以获取生产过程中的增加部分 要想赢利有两种方法 1.提高产品的销售价格 2.降低产品的生产成本
性。这是每一家企业最求的目标。
(到这里是不是打消掉一些人心中的疑问,精益生产不就是生产中的事情吗,跟我们非生产部门有 什么管理呢?如果到这里你的疑问还不能消除,那看下面的)
5/14/2015
9
生产方式的特点比较
生产方式特点比较 项目 手工生产方式 大批量生产方式 精益生产方式 产品特点 完全按照顾客要求 标注化、产品单一 品种多样化、系列化 设备和工装 零活、便宜 专用、高效、昂贵 柔性高、效率高 作业分工与 粗略、丰富 细致、简单、重复 ∩粗略、多技能、丰富 作业内容 对操作工人 懂设计制造、有较 不需要专业技能 多技能 的要求 高操作技能 库存水平 高 高 低 制造成本 高 低 更低 产品质量 低 高 更高 所适应的市 极少量需求 物质缺乏、供不应求 买方市场 场时代