板带生产工艺5
冷轧板带生产工艺流程

冷轧板带生产工艺流程
冷轧板带的生产工艺流程通常包含以下几个步骤:
1. 原料准备:选择适当的冷轧板材料,并进行切割、打底、扫描等预处理工作。
2. 加热处理:将冷轧板加热到适当的温度,以改善材料的塑性和可锻性。
3. 轧制:通过轧制设备将加热后的冷轧板材料进行多道次的轧制,以减小板带的厚度和调整其形状。
4. 高温退火:对轧制后的板带进行高温退火处理,以消除残余应力和改善材料的物理性能。
5. 镀锌处理:对退火后的板带进行镀锌处理,以提高其耐腐蚀性和外观质量。
6. 表面处理:对板带进行清洗、抛光等表面处理工序,以提高外观质量和润滑性能。
7. 检验和修整:对制成的冷轧板带进行尺寸测量、外观检查和质量评估,如果有需要,进行修整或再加工。
8. 包装和出厂:对合格的冷轧板带进行包装,并按照客户要求进行出厂发货。
需要注意的是,具体的生产工艺流程可能会根据不同的生产要求和产品类型有所差异。
上述流程仅为一般的参考。
板带生产工艺冷轧板带钢生产
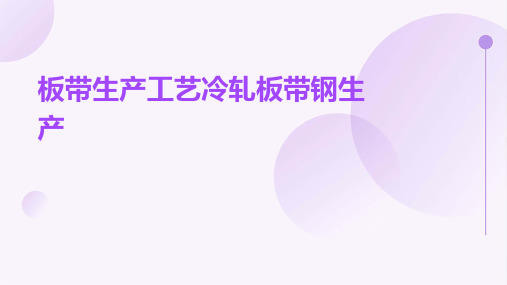
详细描述
冷轧板带钢的生产流程包括原料选择、加热、轧制、 冷却、精整等环节。原料选择是根据产品要求选择合 适的钢板;加热是为了使钢板软化,便于轧制;轧制 是利用轧机对钢板进行多次轧制,使其变薄、变长; 冷却是在轧制过程中对钢板进行快速冷却,使其内部 组织更加稳定;精整是对轧制后的钢板进行矫直、剪 切、表面处理等加工,以满足产品要求。
建立废水处理设施,对生产过程中产生的废水进行分类处理,
确保废水达标排放。
废气处理
03
对生产过程中产生的废气进行收集和处理,减少废气对环境的
影响。
资源利用与可持续发展
节能降耗
采用节能技术和设备,降低能源消耗,提高资源利用效率。
循环经济
实现废物的减量化、资源化和无害化处理,促进循环经济的发展 。
绿色产品开发
轧机设备主要包括工作辊、支撑辊和轧制力矩测量装置等部分。工作辊和支撑辊是轧机的核 心部件,负责将轧制力传递给钢板并进行塑性变形。轧制力矩测量装置则用于监测和控制轧 制过程中的力矩,以确保生产出的冷轧钢板厚度和性能符合要求。
为了确保轧制质量和生产效率,轧机设备需要定期进行维护和更换易损件,同时对设备参数 进行优化调整。
题发生。
生产过程质量控制
工艺参数控制
严格控制生产过程中的温度、压力、速度等工艺 参数,确保产品性能的稳定。
设备维护与检查
定期对生产设备进行检查和维护,确保设备处于 良好的工作状态。
过程监控与记录
对生产过程进行实时监控,并做好相关记录,以 便对产品质量的追溯和控制。
产品检验与质量评估
外观检验
对冷轧板带钢的表面质量进行 检验,确保产品表面无明显缺
轧制道次
根据带钢的材质和厚度要 求,确定合理的轧制道次 和每道次的压缩率。
轧钢生产中板带热轧工艺流程分析

223管理及其他M anagement and other轧钢生产中板带热轧工艺流程分析许 锌(山钢集团莱芜分公司特钢事业部,山东 济南 271104)摘 要:生产工艺流程就是某个产品的生产工序,工序流程依次排序的过程,正确制定工艺就是轧钢车间工艺设计当中的重要内容,制定轧钢生产工艺的主要目的,就是确保施工质量符合产品要求,确保质量的同时,在此基础上追求轧钢的高产量,从而降低原料成本与做好材料消耗,从整体上来确降低产生的生产成本。
基于这种认识正确制定产品工艺,保证施工工艺合理化来发挥轧机的作用。
关键词:轧钢;生产;热轧;工艺;流程中图分类号:TG335 文献标识码:A 文章编号:11-5004(2020)24-0223-2 收稿日期:2020-12作者简介:许锌,男,生于1990年,汉族,山东人,本科,中级,研究方向:轧钢工艺。
钢铁产业是我国经济发展的重要组成部分,尤其随着科技信息的快速发展,该产业和以往相比也发生较大变化。
由于热轧板轧钢其自身具有足够的厚度和宽度,因而根据轧钢成分和密度可以分为焊瓶钢、低碳钢、结构钢等。
在生产过程中一定要保证劳动条件,确保最好的经济效益。
在具体工艺流程当中,一定要保证原则,这里简要阐述几个原则:产品技术条件、生产规模、生产消耗成本、劳动力成本等。
文章基于轧钢生产过程中使用的热轧工艺流程进行分析阐述,阐述生产工艺流程。
目前热轧带钢生产企业面临的主要问题之一如何优化热轧带钢生产工艺,从而更好地提高热轧带钢产品质量,进一步推动钢铁产业快速稳定发展。
1 生产工艺过程1.1 板坯、轧前准备板坯选择主要是确定几何尺寸、重量。
板坯厚度在综合考虑的基础上,考虑板坯连铸机、热轧带钢轧机的生产能力。
板坯厚度一般为150~250mm ,最厚为300~350mm。
板坯宽度由成品宽度来决定,正常情况下,在生产之后,板坯的宽度比成品大约50mm,如图1所示。
当前板坯宽度的实际加工可以达到2300mm,热连轧带钢板板卷重量为20~30T,重量最高为45T。
板带钢生产工艺课件.pptx

的生产工艺;掌握轧制力矩的计算和
压下规程的制定方法,为今后从事专
业技术工作、解决生产实际问题及学
习新的科学技术奠定必要的基础。
轧制产品根据断面形状分为四大类:
板带钢 型钢 钢管 特殊类型钢材
板带钢生产特点
• 一、热轧板带材短流程、高效率化。
体现在三方面:
1.常规生产工艺的革新 2.薄板坯连铸连轧技术 3.薄带连续铸轧技术
置。
§1.3 板带材轧制技术的发展
• 1)技术发展的关键: • 降低轧制压力,使板带钢易于变形。 • 2)途径:
• 1.降低板带钢本身的变形抗力; • 2.改变应力状态,减少应力状态影响系数,减
少外摩擦等对金属变形的影响(减少外阻)。 • 3.控制轧机的变形:增强和控制机架的刚性和
辊系的刚性,采用厚度自动控制等技术控制轧辊 的变形。
•
T H E E N D 17、一个人如果不到最高峰,他就没有片刻的安宁,他也就不会感到生命的恬静和光荣。下午8时53分1秒下午8时53分20:53:0120.10.18
谢谢观看
2.铸坯温度保证与输送技术
• 铸坯输送与温度保证技术如图1-3所示。 • 利用液芯潜热,使铸坯保持更高更均匀的温
度; • 在保证充分冷却不致拉漏的前提下,合理控
制钢流速度和冷却制度来保加热温度,将铸 坯完全凝固的时刻控制在连铸机冶金长度的 末端,否则还要降温。 • 具体方法:采用上部强冷,下部缓冷的变化 冷却制度,提高整体温度; • 不对板坯的边部喷水,使液芯尾端两侧呈凸 起形(通常中心呈凸形),提高边角温度; • 边部减少冷却水量,中部适当加大水量,消
• 2、开发的目的 • 大幅度降低轧制压力;增大压下量,减少道
次与轧程(冷轧有轧程);生产薄带;提高板 带的厚度精度。
板带生产工艺5(热连轧带钢生产)课件

推动产业升级和转型
02
新技术应用将推动传统钢铁产业的升级和转型,实现绿色、智
能、高效的生产方式转变。
满足市场需求和推动经济发展
03
新技术应用将满足市场对高品质、高性能热连轧带钢的需求,
推动相关产业的发展和经济增长。
07
实践环节与案例分析
实践环节安排
实践环节目标
通过实践操作,加深对热连轧带钢生产工艺的理解,掌握 关键技术和设备操作。
原料切割
将原料按照轧制长度进行 切割,准备进入加热工序 。
原料加热
加热温度
控制加热温度在适当的范 围内,以保证轧制过程的 稳定性和产品质量。
加热时间
根据原料的厚度和加热温 度确定加热时间,确保原 料充分软化。
加热方式
采用连续式加热炉或步进 式加热炉进行加热,提高 加热效率。
加热质量与控制
温度均匀性
确保加热过程中温度分布均匀精度
对加热温度进行精确控制,以获 得稳定的轧制过程和产品质量。
氧化与脱碳
控制加热过程中的氧化和脱碳程 度,避免对产品质量造成影响。
04
轧制过程与控制
粗轧过程与控制
粗轧阶段
轧制速度
在粗轧阶段,带钢经过几道轧制后逐 渐成形,主要目标是控制带钢的宽度 和厚度,确保其满足后续精轧和成品 的要求。
热连轧带钢生产工艺流程
加热
将原料加热至轧制所需温度。
冷却
控制冷却速度,以获得所需的 金属组织和性能。
原料准备
选用合适的原料,进行表面清 理和切割。
轧制
通过多道次轧制,使原料逐渐 减薄和延伸,直至达到所需规 格。
精整
对轧制后的带钢进行表面处理 、矫直和切割等操作,以满足 产品要求。
热轧板带工艺流程-初学者

热轧板带工艺流程----初学必看1.主轧线工艺流程简述板坯由炼钢连铸车间的连铸机出坯辊道直接送到热轧车间板坯库,直接热装的钢坯送至加热炉的装炉辊道装炉加热,不能直接热装的钢坯由吊车吊入保温坑,保温后由吊车吊运至上料台架,然后经加热炉装炉辊道装炉加热,并留有直接轧制的可能。
连铸板坯由连铸车间通过板坯上料辊道或板坯卸料辊道运入板坯库,当板坯到达入口点前,有关该板坯的技术数据已由连铸车间的计算机系统送到了热轧厂的计算机系统,并在监视器上显示板坯有关数据,以便工作人员进行无缺陷合格板坯的核对和接收。
另外,通过过跨台车运来的人工检查清理后的板坯也需核对和验收,并输入计算机。
进入板坯库的板坯,由板坯库计算机管理系统根据轧制计划确定其流向。
常规板坯装炉轧制:板坯进入板坯库后,按照板坯库控制系统的统一指令,由板坯夹钳吊车将板坯堆放到板坯库中指定的垛位。
轧制时,根据轧制计划,由板坯夹钳吊车逐块将板坯从垛位上吊出,吊到板坯上料台架上上料,板坯经称量辊道称重、核对,然后送往加热炉装炉辊道,板坯经测长、定位后,由装钢机装入加热炉进行加热。
碳钢保温坑热装轧制:板坯进入板坯库后,按照板坯库控制系统的统一指令,由板坯夹钳吊车将板坯堆放到保温坑中指定的垛位。
轧制时,根据轧制计划,由板坯夹钳吊车逐块将板坯从保温坑取出,吊到板坯上料台架上上料,板坯经称量辊道称重、核对,然后送往加热炉装炉辊道,板坯经测长、定位后,由装钢机装入加热炉进行加热。
直接热装轧制:当连铸和热轧的生产计划相匹配时,合格的高温连铸板坯通过加热炉上料辊道运到称量辊道,经称重、核对,进入加热炉的装炉辊道,板坯在指定的加热炉前测长、定位后,由装钢机装入加热炉进行加热。
其中一部分通过卸料辊道运输的直接热装板坯需通过吊车吊运一次放到上料辊道后直接送至加热炉区。
如果炼钢厂可以实现直接热装板坯由上料辊道运送,则可减少部分吊车吊运作业。
板坯经加热炉的上料辊道送到加热炉后由托入机装到加热炉内,加热到设定温度后,按轧制节奏要求由出钢机托出,放在加热炉出炉辊道上。
板带生产工艺热连轧带钢生产

热连轧带钢生产是钢铁工业中的 重要环节,广泛应用于汽车、建 筑、家电、造船、轻工等领域。
热连轧带钢生产工艺流程
粗轧
通过多道次轧制,将钢坯 轧制成厚度较薄的中间坯
。
冷却与卷取
将轧制出的带钢进行冷却 ,并卷取成卷。
01
02
03
04
05
钢坯准备
将原料钢坯进行加热、除 鳞等预处理,使其达到轧 制所需的温度和表面质量
。
精轧
对中间坯进行精细化轧制 ,得到所需规格和性能的
带钢。
精整与处理
对卷取后的带钢进行平整 、矫直、剪切等处理,以 满足不同用户的需求。
热连轧带钢生产的重要性
提高钢材利用率
通过连续的轧制,可以减少钢材的切头、切 尾等浪费,提高钢材利用率。
优化产品性能
通过精确的轧制工艺控制,可以获得具有优 异性能的带钢产品,满足不同领域的需求。
详细描述
智能化、自动化生产技术能够提高生产效率、降低能耗和减少人工干预,从而降低生产 成本和提高产品质量。通过采用传感器、物联网、大数据和人工智能等技术手段,实现 生产过程的实时监控、智能调度和自动控制,优化轧制工艺参数,提高热连轧带钢生产
的稳定性和可靠性。
感谢您的观看
THANKS
精整设备操作与维护
操作人员需要严格遵守操作规程,确保精整设备在最佳状态下运行, 同时定期进行维护和保养,提高设备使用寿命和稳定性。
冷却设备
冷却设备种类
冷却设备是热连轧带钢生产中用于控制带钢冷却速度的设 备,包括水冷装置、风吹装置和辊道输送装置等。
冷却设备性能参数
冷却设备的主要性能参数包括冷却速度、均匀性和可控性 等,这些参数直接影响带钢的性能和组织结构。
板带钢生产工艺学

板带钢生产工艺学
板带钢是一种重要的金属材料,其生产工艺是指将原料经过多道工序加工和处理,最终形成具有一定厚度和宽度的板带状材料的过程。
板带钢生产工艺主要包括原料准备、精炼冶炼、连铸连轧、热轧、冷拉平、冷轧、退火、分切整平等工序。
下面,我们将详细介绍这些工艺。
1. 原料准备:在板带钢的生产过程中,主要原料是钢坯,其它辅助材料包括添加剂、脱氧剂、合金元素等。
这些原料需要经过筛分、破碎、配料等工序,以保证原料的质量和配比的准确性。
2. 精炼冶炼:将原料放入高炉中进行冶炼,通过高炉的高温、高压等条件,将炉料中的杂质和不良元素去除,使得冶炼后的钢液质量更加纯净。
3. 连铸连轧:冶炼好的钢液通过连铸机连续浇铸成板坯,然后经过连轧机的轧制,使板坯逐渐变细,形成带钢。
4. 热轧:将连铸机得到的板坯经过加热,然后在热轧机上进行轧制,使板坯变细、变宽,形成所需的板带钢。
5. 冷拉平:将热轧的板带钢经过拉拔机进行拉拔,使其进一步细长,同时提高其机械性能。
6. 冷轧:将冷拉平的板带钢通过冷轧机进行轧制,使其更加细小和光滑,提高其表面质量和尺寸精度。
7. 退火:将冷轧后的板带钢进行退火处理,通过加热和保温,使其晶体结构发生变化,降低其硬度和脆性,提高其延展性和塑性。
8. 分切整平:将退火后的板带钢进行剪切和整平,使其尺寸和平整度符合要求。
以上是板带钢的主要生产工艺。
通过这些工艺的处理,原料可以被加工成具有一定厚度和宽度的板带形式,方便后续加工和应用。
同时,这些工艺还能够提高板带钢的质量和性能,满足不同领域的需求。
- 1、下载文档前请自行甄别文档内容的完整性,平台不提供额外的编辑、内容补充、找答案等附加服务。
- 2、"仅部分预览"的文档,不可在线预览部分如存在完整性等问题,可反馈申请退款(可完整预览的文档不适用该条件!)。
- 3、如文档侵犯您的权益,请联系客服反馈,我们会尽快为您处理(人工客服工作时间:9:00-18:30)。
的板坯边缘部加热器及2400kW,500~1000Hz
可变频板料边部感应加热器,精轧前使板坯边 部温度由1070℃提高到1250℃~1270℃,以保 持板坯断面温度均匀。
为使连铸与轧机生产能力相匹配,连铸
速度必须保持在2.0~2.5m/min的范围内 。热轧成品尺寸为厚1.0~12.7mm,宽 600~1630mm,卷重30t。设有在线缺陷 检测器,把一部分有缺陷的板坯检出,
调宽技术,但即使连铸机具有快速调宽
装置,为了稳定浇铸作业,稳定炼钢与 连铸的节奏均衡及减少锥形板坯的长度
,也应尽量减少结晶器宽度的调节变化
,亦即结晶器宽度的改变应该是越少越 好,而将调宽改变板坯规格的任务主要
交给轧钢去承担。在轧钢车间调控板坯
的宽度采用的技术主要有:
轧钢车间调控板坯的宽度采用的技术
移辊轧制技术(HCW或WRS)
WRS轧机开发的新轧制法如图所示: (a)为往复移动法,即是使带凸度的工作
辊轴向移动,防止因轧辊局部磨损而导 致带钢表面出现局部高点或凸峰,使轧 辊保持均匀磨损的外形和热凸度,以便
能进行随意计划轧制,这也就是HCW轧 制技术;
WRS轧机开发的新轧制法
(b)为锥体调节法,即一侧车成锥度的工作辊
作轴向移动,以减少凸度和边部减薄;
(c)为锥体振荡法,即一侧车成锥度的工作
轧辊作短行程的振荡串动,以减少带钢凸度, 并防止轧制带钢边缘产生异常磨损。一侧带有 锥度的工作辊之所以能减少带钢边部变薄,其 原理如图所示。HCW轧机和WRS轧机都是除工 作辊作轴向移动以外,还配有工作辊弯辊装置 。
HCW轧机的基本特性如图所示。HCW轧
况比较如图
自由程序轧制与常规轧制的比较
为了实现自由程序或随意计划轧制,必须
增长轧辊的使用寿命,减少及均化轧辊的磨损 ,保证板带的板形平坦度和厚度精度质量,并 加强自动控制及快速换辊技术:
(1)改进轧辊材质,减少轧辊磨损,开发新钢
种轧辊(如高碳高速钢轧辊等)及采用热轧润滑 以减少轧辊磨损,降低轧制压力。
为了维持连续而稳定的生产,必须
尽量减少轧机设备的事故和停工时间, 必须采用最快的速度换辊和变换产品规 格和钢种,当然快速操作要求自动化, 自动化才能保证快速度。
连铸坯直接轧制工艺流程与车间布置
日本新日铁界厂于1981年7月首次实现
了宽带钢的连铸坯直接轧制(CC-DR), 其车间设备布置如图
该厂为改建而成的CC-DR工艺,新建连
板带生产工艺5
调宽轧制(AWC)及自由程序轧制(SFR )
高度现代化的钢铁工业生产要求提
高产量、质量、节省能源、降低消耗及 成本,因而向着高度连续化、自动化的 方向发展。尤其是为了实现炼钢-连铸-轧 钢等多工序周期性连续生产,就必然要 求轧制技术的高度灵活和可靠,也就是 要求高度柔性生产。
调宽轧制(AWC)及自由程序轧制(SFR )
轧钢车间调控板坯的宽度采用的技术
(3)采用定宽压力机以大压下量有效地调
整板坯宽度。如我国宝钢1580mm、鞍 钢1780m轧机即是如此。除此之外,原
来常规热带轧制中采用的一些板宽控制 技术在连铸连轧生产中仍然可以使用, 对调控板、带宽度精度也可起较大的作 用。
自由程序(或随意计划)轧制技术(SFR )
了提高轧机的宽度压下能力,将立辊破鳞机改 造成一架可逆式轧机,经5道次压下,可使侧 边总压下量达150mm。
轧钢车间调控板坯的宽度采用的技术
(2)一些工厂(如界厂等)由于使用M机架的立辊
轧边,提供了一种宽度自动控制(AWC)功能。
这种功能在大压下量轧制或轧制因结晶宽度改 变而形成的锥形板坯时,能使宽度得到较精确 的控制。板坯的宽度用宽度计进行测量。利用 测出的板坯宽度,计算出立辊的开口度(辊缝) ,再根据测量辊测得的数据,定时进行立辊开 口度的调整。当不使用AWC时,带钢宽度变化 达5.5mm,而当使用AWC时,则宽度差得到消 除,使板宽精度大大提高。在界厂,锥度达 140mm的板坯可直接送往热带轧机进行轧制。
连铸直接轧制(CC-DR)工艺对轧钢操作的
要求与该厂原来的(CC-DR)工艺是差不多的,
即是都必须能宽度大压下,灵活改变板坯的宽
度及实行自由程序轧制。为此该厂具有一大立 辊轧机(VSB)和几台轧边机(粗轧机前)可完 成宽度压下量达300mm以上;采用了移辊轧制 技术以均化轧辊磨损,延长其使用寿命;采用 6辊式精轧机有很强的凸度控制能力,还采用 了热轧润滑技术和精轧前的板边感应加热器, 以保证产品精度和板形质量。
(1)提高铸坯边部温度的技术:要使铸坯的液芯
尾端尽可能靠近铸机出口,以便利用凝固潜热 获得高温铸坯;二冷制度不对铸坯边部喷水以 保持边部的较高温度;连铸机内采用绝热技术 并在切割机附近采用感应加热或煤气烧嘴加热 ,使板坯边部温度提高约200℃,以有效地控 制AlN的沉淀析出。
(2)采用高速保温输送车运输铸坯。
(1)设立定宽(径)轧机或大立辊破鳞机,实现
宽度大压下,如日本大分厂设立了立平立
(VHV)三联可逆式定径轧机,道次压下量可达 150mm,总减宽量可达1050mm。由于前端和 尾端宽度缩小而增加剪切损失,使金属收得率
降低,为此大分厂采用了宽度自动控制和挤压 轧制技术,使收得率达99%以上。
机架的凸度变化对于后机架凸度变化的影响。
这种凸度变化可用凸度的遗传性和轧辊形状的
复制现象进行整理和定量分析,实行在线控制
。2)高精度轧制技术。
(4)自动控制及快速换辊技术,随着连
铸-直接轧制和SFR轧制技术的实现,产 品品种多样化,产品精度质量严格化, 从而使热带轧制作业更趋复杂,这就更 加要求有精确的设定和监视,要求全面 计算机自动控制,并实现超过人类感觉 器官的、对诸设备运动状况的监视,实 现对产品各种指标的迅速而准确的判断 ,才能维持连续而稳定的生产。
(2)均化轧辊磨损的技术:
1)采用在线磨辊(ORG)技术,以及时修复不均
匀磨损的辊型
2)采用移辊轧制技术(HCW或WRS)。在生产
过程中,板宽边部的温度比中部要低,而宽度 方向的金属流动在边部又较大,因此与板材边 部接触的轧辊表面局部磨损也大。为了解决边 部磨损问题,在轧制中采用移动工作辊技术, 以使磨损得以分散,使其影响得以缩小。
移辊轧制技术(HCW或WRS)
HCW移动工作辊的轧制技术首先是日本
日立制作所开发,并于1982年在新日铁八幡厂
热带轧机精轧机上得到应用(如图a)以后,仅三
年内就很快得到推广应用。以后日本川崎钢铁 公司又进一步开发了K-WRS工作辊移动轧制技
术,其不同点是将工作辊身一端做成锥形(如 图(b)、(c))再进行轴向移动,在热带轧机上 得到应用。这些轧制技术不仅特别适用于连铸 连轧生产,而且适用于常规热轧板、带生产。 它们不仅可以减少和均化轧辊磨损,延长轧辊 使用寿命,灵活轧制任意宽度的板带,而且可 明显提高带钢的板形平坦度和厚度精度质量。
中小型企业薄板带钢生产
高速连续轧制的方法无疑是当前生
产薄板带钢的主要方向,但它不是唯一
的方向。宽带连轧机的投资大、建厂慢 、生产规模太大,受到资源和需要等条 件的限制,也有不利的一面。随着发展 中国家的兴起,随着工业先进国家废钢 的日益增多,随着较薄板坯的铸造技术 的提高,中小型企业板带钢生产的方法
轧机为1420mm全连续式,粗轧为2台2
辊加4台4辊式(R1~R6),其R3经改造后 已移至精轧机组前作为M机架,紧接着是 6架4辊精轧机(F1~F6),产品尺寸为 (1.2~1.6)×(600~1300)mm板卷,重约
20t。该厂现已转卖给中国梅山钢厂。
日本钢管福山厂继新日铁界厂、室兰厂等之后
在常规连铸与轧钢生产工艺中,板坯出连
铸机后进行冷却,送板坯存放场进行检查清理 及堆垛存放,再运往轧钢车间按照轧钢生产管 理计划编组,按每套轧辊先轧宽板后逐渐轧制
窄板的一定程序进行轧制生产,连铸与轧制是 两个独自编制生产计划的互不相干的工厂。但
在连铸一连轧生产时,铸坯不经冷却,直接热 送到加热或补热装置,然后立即直接进行热轧 ,炼钢、连铸与轧钢三者联成一个整体,服从 于统一的全厂总生产计划。
远距离CC-DR工艺
日本新日铁八幡厂研制出板坯保温高速输
送车,结论是远距离(1000mm以上)输送车优 于辊道输送。由于保温车可使铸坯在高温保温
箱内得到均热,且保温箱的保温效果远远大于 长程保温辊道的效果,故对于远距离连铸连轧
工艺必须采用保温车输送。如图为八幡厂远距
离CC-DR工艺中连铸与热带轧机衔接部分的平 面布置图。图14-22为八幡厂的远距CC-DR工 艺流程示意图。该厂连铸机距离热连轧机 620m,以前用辊道连接只能实行热装炉轧制 (CC-HCR)工艺。
1987年该厂采用高速保温车输送铸坯和火
焰式边部加热器等措施,开发了远距离直接轧 制技术(CC-DR)。从连铸出口到轧机前板坯边 部加热器的距离为430m,保温车输送速度 15km/h,运送时间约为2min。采用喷流火焰 式边部加热器经6~7min边都加热后送轧机轧 制。与过去辊道输送进行热装炉轧制工艺相比 ,节约燃料约合每t钢5.7kg标煤,以年产 300×lO4t计,可节煤17100t。
又将日益得到重视和发展。
叠轧薄板生产
叠轧薄板是最古老的热轧薄板生产方式 叠轧薄板:把数张钢板叠放在一起送进轧辊进
行轧制
优点:设备简单,投资少,生产灵活性大,能
铸车间在连轧机近旁140m,与轧制线成 垂直布置,与炼钢车间相距600m,用铁 路运送钢水包