花键套零件地机械加工实用工艺规程及工序地设计计算
套筒零件的机械加工工艺规程及夹具设计
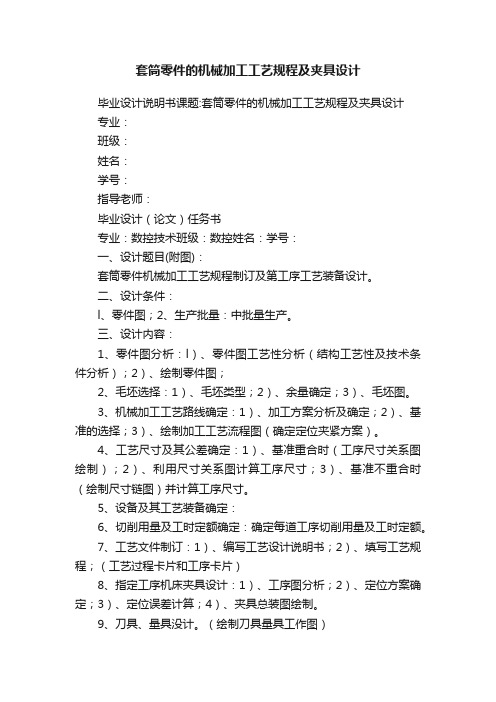
套筒零件的机械加工工艺规程及夹具设计毕业设计说明书课题:套筒零件的机械加工工艺规程及夹具设计专业:班级:姓名:学号:指导老师:毕业设计(论文)任务书专业:数控技术班级:数控姓名:学号:一、设计题目(附图):套筒零件机械加工工艺规程制订及第工序工艺装备设计。
二、设计条件:l、零件图;2、生产批量:中批量生产。
三、设计内容:1、零件图分析:l)、零件图工艺性分析(结构工艺性及技术条件分析);2)、绘制零件图;2、毛坯选择:1)、毛坯类型;2)、余量确定;3)、毛坯图。
3、机械加工工艺路线确定:1)、加工方案分析及确定;2)、基准的选择;3)、绘制加工工艺流程图(确定定位夹紧方案)。
4、工艺尺寸及其公差确定:1)、基准重合时(工序尺寸关系图绘制);2)、利用尺寸关系图计算工序尺寸;3)、基准不重合时(绘制尺寸链图)并计算工序尺寸。
5、设备及其工艺装备确定:6、切削用量及工时定额确定:确定每道工序切削用量及工时定额。
7、工艺文件制订:1)、编写工艺设计说明书;2)、填写工艺规程;(工艺过程卡片和工序卡片)8、指定工序机床夹具设计:1)、工序图分析;2)、定位方案确定;3)、定位误差计算;4)、夹具总装图绘制。
9、刀具、量具没计。
(绘制刀具量具工作图)10、某工序数控编程程序设计。
四、上交资料(除资料2使用标准A3手写外,其余电子文稿指导教师审核后,打印上交)1、零件机械加工工艺规程制订设计说明书一份;(按统一格式撰写)2、工艺文件一套(含工艺过程卡片、每一道工序的工序卡片,工序附图);3、机床夹具设计说明书一份;(按统一格式撰写)4、夹具总装图一张(打印图纸);零件图两张以上(A4图纸);5、刀量具设计说明书一份;(按统一格式撰写)6、刀具工作图一张(A4图纸);量具工作图一张(A4图纸)。
7、数控编程程序说明书五、起止日期:2010年月日一2010年月日(共8周)六、指导教师:七、审核批准:教研室主任:系主任:年月日八、设计评语:九、设计成绩:年月日目录第一章工艺设计说明书 (6)1.零件图的工艺性分析 (6)1.1零件结构功用性分析 (6)1.2零件技术条件分析 (6)1.3零件的结构工艺性分析 (7)2毛坯的选择 (7)2.1毛坯的类型 (7)2.2毛坯余量的确定 (7)2.3毛坯-零件合图 (7)3.机械加工工艺路线确定 (8)3.1加工方法分析确定 (9)3.2加工顺序的安排 (9)3.3定位基准选择 (9)3.4加工阶段划分 (9)3.5主要机加工工序简图 (10)4.设备及其工艺装备确定 (12)4.1选择机床和夹具 (12)4.2刀具的选择 (12)4.3量具的选择 (13)5.切削用量的选择 (14)5.1主轴转速的确定 (15)5.2进给速度的确定 (16)5.3背吃刀量的选择 (16)第二章第50号工序夹具设计说明书 (17)1.工序尺寸精度分析 (17)2.定位方案确定 (17)3.定位误差分析 (17)4.加紧方案及元件确定 (17)5.夹具总装草图 (17)第三章第20、25号工序刀具设计说明书 (19)1.工序尺寸精度分析 (19)2.刀具类型的确定 (19)3.刀具设计参数确定(数据来源参考书[3]) (19)4.刀具工作草图 (20)第四章第45号工序量具设计说明书 (21)1.工序尺寸精度分析 (21)2.量具类型确定 (21)3.极限量具尺寸公差确定 (21)4.极限量具公差带图 (21)5.极限量具结构设计 (22)第五章第30、35、65、70号工序数控编程设计说明书 (23)1.数控加工工艺性分析 (23)2.走刀路线的确定 (23)3.刀具及切削用量确定 (23)4.编程原点的确定及数值计算 (24)5.程序编写及说明 (25)第六章毕业设计体会 (29)第七章参考资料 (30)致谢 (31)套筒零件的工艺规程、夹具及程序设计摘要本文主要讲述套筒零件的加工工艺,通过开篇对其零件图纸进行工艺分析,然后设计出毛坯,制定出机械加工工艺路线,分析工序尺寸与确定公差,选择加工设备,再到夹具、刀具、量具的设计,最终编制出零件的数控加工程序,运用程序在数控机床上进行数控加工,最后完成该零件的所有工序,得到合格的零件。
套筒零件的机械加工工艺规程及夹具设计-加工工艺设计-毕业论文

摘要这次毕业设计内容包括:深入学习了解了机械制造工艺规程设计、机床夹具设计、金属切削机床和可互换的测量和技术等相关的课程。
套筒部件的机械加工工艺规程设计和铣削表面沟槽工艺的夹具设计包括有零件加工的工艺设计、工序设计和专用夹具设计这些环节。
在进行工艺设计时,第一步要对零件进行分析,先通过对零件加工工艺的了解设计出零件毛坯的结构,在这之后选择零件的加工工艺基准,设计出零件的加工路线;第二步是对零件各个步骤中的步骤进行尺寸设计计算,其中最重要的是确定每个工艺的切削加工用量和加工设备数量。
在进行专用夹具设计时,第一步设计出组成该夹具的各个部件,例如夹紧元件、引导元件、定位元件、夹具体与机床的连接部件以及其它部件;第二步计算过程目的是夹具的精确定位误差;最后分析出该夹具结构的合理之处和不足之处,并在今后的学习和工作的设计中加强注意。
关键词:工艺;工序;夹紧;定位目录摘要 (III)Abstract................................................................................................... 错误!未定义书签。
前言............................................................................................................................. - 1 - 第一章国内外工艺夹具设计的现状及前景.................................................... - 2 -1.1 国外工艺夹具设计的现状及前景.................................................................... - 2 -1.2 国内工艺夹具设计现状及前景........................................................................ - 3 - 第二章本课题研究的内容及目的....................................................................... - 4 -2.1 本课题研究的内容............................................................................................ - 4 -2.2本课题研究的目的............................................................................................. - 4 - 第三章零件的分析................................................................................................... - 6 -3.1 零件的作用及特点............................................................................................ - 6 -3.2 零件的工艺分析................................................................................................ - 6 - 第四章工艺规程设计 .............................................................................................. - 8 -4.1 确定毛坯的制造形式........................................................................................ - 8 -4.2 基准的选择........................................................................................................ - 8 -4.3 制定工艺路线.................................................................................................... - 9 -4.4 机械加工余量、工序尺寸及毛坯尺寸的确定...............................................- 11 -4.5确定切削用量及基本工时............................................................................... - 17 - 第五章夹具设计 ..................................................................................................... - 35 -5.1工序XIII夹具设计......................................................................................... - 35 -5.2 工序XIV夹具设计.......................................................................................... - 37 - 第六章结论.. (40)参考文献.............................................................................................. 错误!未定义书签。
(新)花键轴课程设计
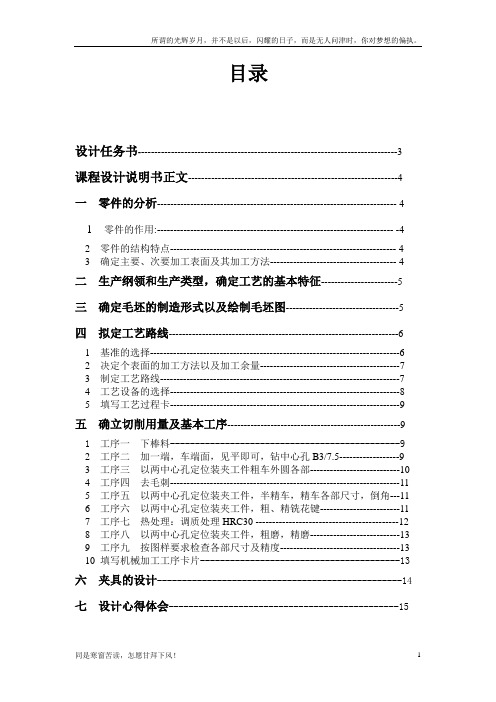
目录设计任务书------------------------------------------------------------------------------3 课程设计说明书正文---------------------------------------------------------------4 一零件的分析------------------------------------------------------------------------ 41 零件的作用:----------------------------------------------------------------------- -42 零件的结构特点-------------------------------------------------------------------- 43 确定主要、次要加工表面及其加工方法--------------------------------------4 二生产纲领和生产类型,确定工艺的基本特征-----------------------5 三确定毛坯的制造形式以及绘制毛坯图----------------------------------5 四拟定工艺路线---------------------------------------------------------------------61 基准的选择---------------------------------------------------------------------------62 决定个表面的加工方法以及加工余量------------------------------------------73 制定工艺路线------------------------------------------------------------------------74 工艺设备的选择---------------------------------------------------------------------85 填写工艺过程卡---------------------------------------------------------------------9 五确立切削用量及基本工序----------------------------------------------------91 工序一下棒料----------------------------------------------92 工序二加一端,车端面,见平即可,钻中心孔B3/7.5------------------93 工序三以两中心孔定位装夹工件粗车外圆各部---------------------------104 工序四去毛刺---------------------------------------------------------------------115 工序五以两中心孔定位装夹工件,半精车,精车各部尺寸,倒角---116 工序六以两中心孔定位装夹工件,粗、精铣花键------------------------117 工序七热处理:调质处理HRC30 -------------------------------------------128 工序八以两中心孔定位装夹工件,粗磨,精磨---------------------------139 工序九按图样要求检查各部尺寸及精度------------------------------------1310 填写机械加工工序卡片----------------------------------------13六夹具的设计-------------------------------------------------14七设计心得体会----------------------------------------------15机械制造工艺与机床夹具课程设计任务书设计题目:“花键轴”零件的机械加工工艺规程一任务及要求:1.绘制零件图和毛坯图综合图各1张2.机械加工工艺卡1份3.机械加工工序卡1套4.说明书1份二时间分配:课程设计时间为一周,具体非配如下:1.熟悉零件画零件毛坯综合图1天2.选择加工方案填写工艺文件 2.5天3.编写说明书 1.5天三原始资料:1.生产类型小批生产2.生产条件车间现有设备四方法与步骤:参考教材课程设计指导书部分五要求交电子版和纸质课程设计(一人有二道工序数控加工程序)设计任务书河南工业职业技术学院机械加工技术课程设计任务书设计题目:“花键轴”零件的机械加工工艺规程设计内容:1.产品零件图2.产品毛坯图3.机械加工工艺过程卡4.机械加工工序卡片5.课程设计说明书班级:定向 0901 班设计者:李宁指导老师:教研室主任:2011年5月18日课程设计说明书正文一零件的分析,并进行结构工艺性审查零件的分析包括零件结构及其工艺性分析和零件的技术要求的分析该零件是轴类零件,外圆柱面需要在普通车床上进行车削。
花键轴的机械加工工艺规程

花键轴的机械加工工艺规程1花键轴的技术要求及零件作用(1)右端面外圆26为安装齿轮的配合表面.表面粗糙度R为0.8.公差等级为IT6(2)二外圆20为安装滚动轴承定位基准.表面粗糙度为R为0.8.公差等级为IT6.(3)轴肩外圆M24的左端面圆.外圆33的左端面圆.外圆26的右端面圆为安装定位表面.以基准A-B的端面圆跳动公差为0.04.表面粗糙度为1.6(4)直径30的键槽.以基准C的对称度为0.05.表面粗糙度为1.6(5)花键外圆33.为安装表面.以基准A-B平行度为0.03-0.038.表面粗糙度为1.6(6)调质处理40-42HRC.使花键轴获得强度.韧度适中的综合机械性能2选择材料和毛坯(1)花键轴负荷一般.选择材料为40CR钢(2)毛坯直径相差不大.大批量生产.毛坯选择为模D件的热扎圆棒3工艺分析选择主要加工表面的加工方法和确定精基准(1)选择主要加工表面的加工方法.轴颈外圆20.20.与装配基准面外圆25为主要加工面.公差等级为IT8.表面粗糙度为0.8.选用粗车,半精车,磨削方法。
轴向装配基准端面圆26.M24.33为主要加工表面.表面粗糙度为1.6,通过车端面,磨端面加工(2)(2)基准选择为保证花键轴各圆柱面的同轴度和其他位置精度,半精车、精车和磨削时应该选择基准轴线为定位基准,轴两端钻中心孔,用两顶尖装夹。
两端中心孔相关尺寸和位置精度以及粗糙度是影响加工精度的重要因素,因此工件在调质等热处理后要安排修磨中心孔的工序。
粗车时为了保证工件装夹刚性,常采用一夹一顶的装夹方法,左端采用三爪自定心卡盘夹紧、右端采用活动顶尖支顶。
4机械加工顺序安排预备加工下料------车端面,钻中心孔-------粗车各外圆---------调质------修研中心孔-------半精车各外圆,倒角,切槽,-------车螺纹-------滚键槽-------修研中心孔--------磨外圆,台阶面。
矩形齿花键套机械加工工艺规程设计演示
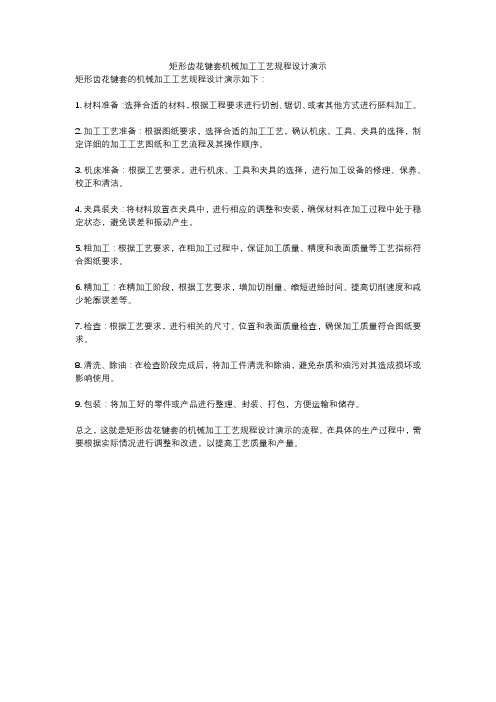
矩形齿花键套机械加工工艺规程设计演示
矩形齿花键套的机械加工工艺规程设计演示如下:
1. 材料准备:选择合适的材料,根据工程要求进行切割、锯切、或者其他方式进行胚料加工。
2. 加工工艺准备:根据图纸要求,选择合适的加工工艺,确认机床、工具、夹具的选择,制定详细的加工工艺图纸和工艺流程及其操作顺序。
3. 机床准备:根据工艺要求,进行机床、工具和夹具的选择,进行加工设备的修理、保养、校正和清洁。
4. 夹具装夹:将材料放置在夹具中,进行相应的调整和安装,确保材料在加工过程中处于稳定状态,避免误差和振动产生。
5. 粗加工:根据工艺要求,在粗加工过程中,保证加工质量、精度和表面质量等工艺指标符合图纸要求。
6. 精加工:在精加工阶段,根据工艺要求,增加切削量、缩短进给时间、提高切削速度和减少轮廓误差等。
7. 检查:根据工艺要求,进行相关的尺寸、位置和表面质量检查,确保加工质量符合图纸要求。
8. 清洗、除油:在检查阶段完成后,将加工件清洗和除油,避免杂质和油污对其造成损坏或影响使用。
9. 包装:将加工好的零件或产品进行整理、封装、打包,方便运输和储存。
总之,这就是矩形齿花键套的机械加工工艺规程设计演示的流程。
在具体的生产过程中,需要根据实际情况进行调整和改进,以提高工艺质量和产量。
毕业设计(论文)-花键轴零件机械加工工艺工装设计()
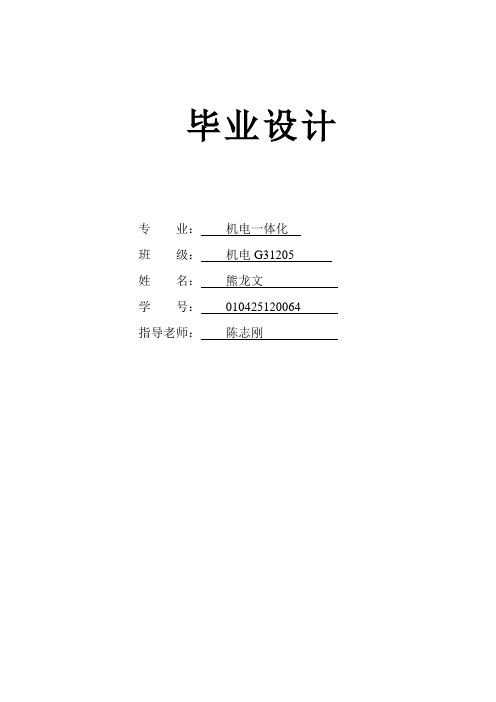
五、起止日期:
2 014年月日一2014年月日(共周)
六、指导教师:
七、审核批准:
教研室主任:系主任:
年月日
八、设计评语:
九、设计成绩:
年月日
第一部分 工艺设计说明书
1.零件图工艺性分析
1.1零件结构功用分析
根据零件简图分析:该主轴零件的结构具有如下特点:从形状上看该工件为阶梯结构的花键轴,由于长度与直径之比L/D≈5,所以该工件属于钢行主轴。从表面加工类型看,主要加工表面有圆柱面,花键,单键槽,螺纹,属于典型的加工表面,易加工。
3.表面粗糙度:两端轴段Φ20+ -0.008外圆和Φ250 -0.03、Φ260 -0.01外圆为Ra=0.8μm,花键齿面及其左端面、:螺纹M24×1.5的左端面和Φ260 -0.01的右端面为Ra=1.6μm,M24×1.5的螺纹及花键右端面为Ra=3.2μm,花键齿根圆为Ra=6.3μm,其余为Ra=6.3μm。
从主轴箱表牌上查实际主轴转速取为900r/min
⑷算切削工时:/nf=76/900*0.3=16.8min
粗铣花键
⑴定铣削深度:由于加工余量不大,故可一次走刀完成,则ae=zb=0.7mm
⑵确定每齿进给量:af=0.1mm
⑶计算切削速度:根据表3-27选刀具耐用度t=7.8*1000
由表3-29确定cv=68.5,zv=0.25, xv=0.3.yv=0.2,uv=0.1,pv=0.1,m=0.2
第三部分 第XX号工序刀具设计说明书……………………………………………………………
…………
第四部分 第XX号工序量具设计说明书……………………………………………………………
花键传动轴零件加工工艺及夹具设计

花键传动轴零件加工工艺及夹具设计花键传动轴是一种机械传动零件,主要功能是在传动时,可以解决两轴间的同步问题,与普通传动方式相比,其具有传动精度高、传动效率高、安装方便等优点。
本篇文章将介绍花键传动轴零件的加工工艺及夹具设计。
一、加工工艺1. 材料选择花键传动轴通常采用45#钢材料加工而成,其硬度约在HRC28~32之间,具有较好的可加工性、焊接性和热处理性能。
2. 工艺流程首先,将原料切割成所需长度,然后进行粗车加工,形成整体形状。
接下来,边丝锥加工花键槽,并加工防止滑动的卸荷槽。
最后,进行细车、磨削和表面处理等工序。
3. 注意事项在加工过程中,需要注意以下几点:(1)精度要求高花键传动轴的加工过程中要求精度高,尤其是花键槽的加工要求较为困难,因此在加工过程中需要采用高精度的设备进行加工。
(2)刀具选择在车削车辆时需要选择合适的刀具,确保零件尺寸和形状的精度达到设计要求。
(3)热处理在花键传动轴加工完成后,需要进行热处理,以提高材料硬度和强度,从而保证零件的耐久性和使用寿命。
二、夹具设计1. 夹具种类花键传动轴的加工需要使用多种夹具,包括粗车夹具、丝锥加工夹具、细车加工夹具和磨削夹具等。
2. 夹具设计原则(1)夹紧力均匀夹具需要保证夹紧力均匀,以防止零件变形或损坏。
(2)跳动控制夹具需要设计成具有调节功能,可以控制零件的跳动,在加工中保证加工精度和质量。
(3)夹口尺寸合适夹具的夹口尺寸需要与零件的尺寸和形状相匹配,以确保零件的稳定性。
(4)易于操作夹具需要设计成易于操作和安装,方便操作人员的使用和维护。
夹具需要选择耐磨损、硬度高、稳定性好的材料制作,以提高夹具的使用寿命和加工质量。
三、总结因为花键传动轴的加工要求较高,需要采取相应的加工工艺和夹具设计,以保证零件的精度和质量。
在实际生产中,需要根据具体的需求和加工工艺,灵活运用各种加工设备和技术,提高加工效率和质量。
花键轴加工工艺设计
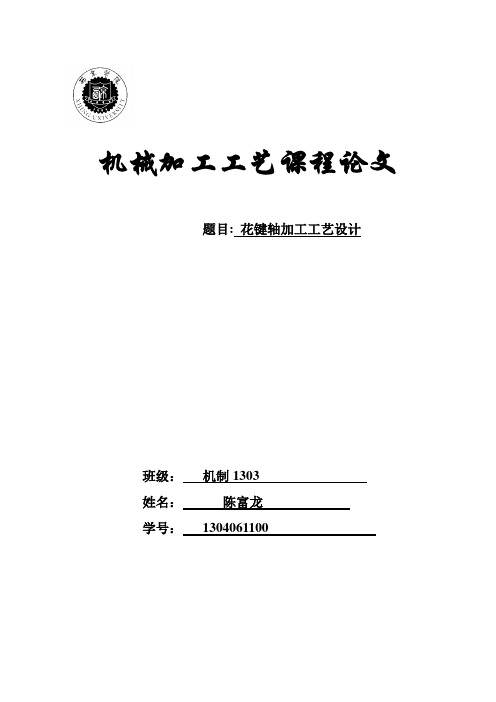
机械加工工艺课程论文题目: 花键轴加工工艺设计班级:机制1303姓名:陈富龙学号:1304061100第1节零件的工艺分析1.1花键轴介绍花键轴用于各个轴用于轴与轴承配合、螺纹主要用于紧固和传动连接、键与花键用于轴和轴上传动件之间的可拆卸连接,用于传递扭矩,有时也作用轴上传动件的导向。
矩形花键轴能够多齿工作,对中性好,导向性好,齿根较浅,应力集中,轴与毂强度削弱小加工方便,在机械制造中应用非常广泛。
其中,该矩形花键轴按国家标准,为花键的中系列,经过查表(教材《互换性与测量技术》表10—7)可得其规格为N*d*D*B=6*34。
2*40*10,标注外花键规格和尺寸代号为6*34.2f7*40f7*10d9 GB/T1144-2001.花键轴1。
2零件结构分析根据零件简图分析:该主轴零件的结构有以下特点:从形状上看该工件为阶梯结构的花键,由于长度与直径之比L/D < 5,所以该工件属于钢性主轴。
从表面加工类型看,主要加工表面有外圆柱面,花键,双键槽,内螺纹孔,属于典型的加工表面,易加工.1。
3零件的工艺分析零件的视图正确、完整,尺寸、公差及技术要求齐全。
但花键外圆柱面Φ40f7mm与右端外圆柱面Φ35k6mm要求Ra0。
8μm有些偏高。
该零件属轴类零件,它的所有表面均需切削加工,各表面的加工精度和表面粗糙度都不难获得。
花键轴径向设计基准是轴中心线,轴向设计基准是花键外圆柱面Φ40f7mm的左端平面。
花键径向设计基准为Φ40f7mm外圆柱面。
M12螺纹孔的径向设计基准是轴中心线,轴向设计基准是花键外圆柱面Φ40f7mm的左端平面。
M5径向设计基准为花键外圆柱面Φ40f7mm的左端平面,轴向设计基准与花键呈30°角。
总体来说,这个零件的工艺性较好。
1.3。
1技术要求该零件属于轴类零件,主要构成表面主要为外圆、倒角、退刀槽、键槽、内螺纹和外花键等;各轴段装配表面粗糙度要求极高,Ra达0。
8μm,为IT6、IT7级;而尺寸精度和位置精度要求也高(重点保证外圆表面的加工),轴右端Φ35mm(基面B)以及花键大径Φ40mm(基面A)的加工尤为重要,它们分别与退刀槽侧面、键槽宽有圆度和对称度要求,外花键键齿与基面A有平行度要求。
- 1、下载文档前请自行甄别文档内容的完整性,平台不提供额外的编辑、内容补充、找答案等附加服务。
- 2、"仅部分预览"的文档,不可在线预览部分如存在完整性等问题,可反馈申请退款(可完整预览的文档不适用该条件!)。
- 3、如文档侵犯您的权益,请联系客服反馈,我们会尽快为您处理(人工客服工作时间:9:00-18:30)。
课程设计学院:机械工程学院班级:数控1311班学号:设计地点(单位): 2教学楼设计题目:花键套的工艺设计完成日期:2015 年 5 月29日机械学院课程设计任务书设计题目:花键套零件的机械加工工艺规程及工序的设计计算教研室主任:贾伟杰指导教师:健2013年 6月 8日目录1 零件的分析 (2)1.1零件的工艺分析 (2)1.2花键套的技术要求 (3)2 毛坯的选择 (3)2.1 毛坯种类的选择 (3)2.2毛坯制造方法的选择 (4)2.3毛坯形状及尺寸的确定 (4)3 工艺路线的拟定 (5)3.1 定位基准的选择 (5)3.2 零件表面加工方案的选择 (5)3.3 加工阶段的划分 (6)3.4 工序顺序的安排 (6)3.4.1.机械加工顺序 (6)3.4.2热处理工序的安排 (6)3.4.3辅助工序的安排 (6)3.5 机床设备及工艺设备的选用 (8)3.6 确定工艺路线 (9)3.6.1工艺分析 (10)4 确定加工余量和工序尺寸 (10)4.1各表面加工工序 (10)5 确定切削用量及基本工时 (11)5.1工序20计算 (11)5.2 工序30 (13)5.3工序50计算 (14)5.4工序60计算 (15)5.5工序70 拉花键孔 (17)5.6工序80计算 (17)5.7工序90计算 (20)6 总结 (21)参考文献 (22)附表机械加工工艺规程设计1.1设计任务如图所示的是花键套简图,该零件材料为45号钢,其外锥表面对花键孔的轴线保证同轴,这样花键套在与花键轴联接时可以满足对中的要求,使花键孔较好的起到传递转矩和运动的功能。
花键孔的外径尺寸和槽两侧尺寸精度都有较高的要求,在完成花键孔的拉削加工后,一般都是以它作为定位基准,来加工下道工序容。
1.2花键套的工艺分析与计算1.2.1花键套的主要基准是Φ25±0.0065mm 外圆轴线。
1.2.2外圆锥0030.034-φmm 表面对Φ25±0.0065mm 孔轴线的径向跳动公差为0.02mm ,粗糙度Ra0.8μm。
1.2.3花键孔018.0016+φmm 表面对Φ25±0.0065mm 外圆轴线的同轴度公差为0.01mm ,粗糙度Ra1.6μm。
1.2.4普通外螺纹的中径、顶径的公差带的偏差代号为g ,公差等级为6级。
1.2.5Φ25±0.0065mm 外圆表面粗糙度为Ra0.8μm。
(1)将各个需要加工表面的尺寸精度、粗糙度、形位精度绘制为下表1。
表1 零件技术要求分析(2) 技术条件为:调制处理、倒角1*45°。
2.1 毛坯的选择该机械零件的毛坯为调质高合金钢。
常用作受力情况复杂,重载、力学性能要求较高零件的毛坯。
毛坯选择时应考虑零件材料、零件的力学性能要求,所以选用Φ50×200的45号圆钢作为毛坯因零件的材料为合金钢45号钢。
花键套的尺寸为Φ34×86,且有较多不需要切削加工表面,所以毛坯的制造选用自由锻造。
2.2.1锻件不应有裂缝,锻件表面应清除毛刺、披缝结瘤和粘砂等。
2.2.2调质处理:硬度235HBS,以消除应力,改善切削加工性能。
2.2.3未注倒角的为1×45º。
2.3毛坯形状及尺寸的确定根据表面最终尺寸及机械加工余量计算毛皮尺寸如表2-1。
表2-1 毛坯尺寸及加工余量最终表面尺寸(mm )加工余量(mm) 毛坯尺寸(mm )外圆0030.034-φ 3.2+0.3+0.3 Φ37.8 外圆Φ25±0.006510+1+0.5+0.3 Φ36.8 长度 865+0.15+0.2+0.291.55选毛坯尺寸为Φ38×92的轴。
形状如下图。
毛坯3 工艺路线的拟定3.1 选择定位基准粗基准选择毛坯表面,精基准选择遵循基准重合,基准统一,互为基准,自为基准原则,具体选择方法如下:该零件图中较多尺寸都以Φ25±0.0065mm外圆为设计基准。
在拉削之后,以花键孔及端面作为定位基准,根据粗、精基准面选择确定加工表面基准如下表2。
表2加工部位基准的选择3.2 零件表面加工方案的选择方案选择如下表。
表3各表面加工方案3.4 工序顺序的安排3.4.1.机械加工顺序(1)遵循“先基准后其他”的原则。
首先加工基准—Φ25±0.0065mm外圆轴线。
(2)遵循“先粗后精”的原则。
先安排粗加工工序,然后再安排加工工序。
(3)遵循“先主后次”的原则。
先加工主要表面—030.034-φmm外圆、Φ25±0.0065mm外圆(4)遵循“先面后孔”的原则。
首先加工各个端面和表面,后加工各个孔。
3.4.2热处理工序的安排粗加工后半精加工前进行调质处理。
3.4.3辅助工序的安排按图纸对零件的精度和要求进行检验工艺路线方案一:工序1 . 车粗车外圆030.034-φmm工序2. 钻Φ12孔工序3. 车粗车外圆Φ25±0.0065工序4. 热处理调质工序5. 车半精车Φ25±0.0065mm外圆工序6 . 镗镗Φ21mm孔,Φ13花键孔工序7. 车半精车030.034-φmm外圆毛坯,工序8. 车精车M27×1.5外圆工序9. 车半精车1:8锥面工序10. 拉拉花键孔工序11. 切槽工序12. 车车螺纹M27×1.5-6g.工序13. 磨磨外圆030.034-φmm,Φ25±0.0065mm外圆,1:8圆锥面工序14. 检验3.5 机床设备及工艺设备的选用根据以上所诉可列机床设备及工艺装备如下表4所示:3.6 确定工艺路线3.6.1工艺分析3.6.1.1该花键套由于是小批量生产,在工序过程的安排上遵循了集中与分散相结合的原则,大部分路线都采用了通用和工艺装置。
3.6.1.2在拉削过程中以018.0016+φmm 孔和35mm 长度左端面作为定位基准,所以在半精车工序中要保证018.0016+φmm 孔和端面位置度的要求,加工时要注意工艺要求。
3.6.1.3工序60花键拉削后,在后续的工序均以它作为加工的定位基准,修整Φ25±0.0065mm 外圆和1:8外锥面,对花键孔的同轴度的位置精度。
3.6.1.4工序80磨锥面中即要保证1:8外锥面的锥度精度,有要控制0030.034-φmm 外圆长度10mm,因锥度较大,每磨小径0.12mm 左右时就要涉及到长度1mm 的误差。
3.6.1.5花键套的热处理工序,调质处理主要目的是使零件可获得良好的综合机械性能4 确定加工余量和工序尺寸4.1各表面加工工序4.1.1 Φ34外圆的加工工序见表6。
表6Φ34表面加工工序4.1.2 Φ25外圆的加工工序见表7。
4.1.3 1:8 锥面的加工工序见表8。
表8 锥面加工工序4.1.4 M27螺纹的加工工序见表9。
表9 M27螺纹的加工工序4.1.5 Φ21孔的加工工序见表10。
4.1.6端面的加工工序见表11。
表11 端面的加工工艺5 确定切削用量及基本工时5.1工序2计算粗车Φ0030.034-φmm 外圆及端面,钻Φ12mm 孔,孔口倒角。
5.1.1粗车Φ0030.034-φmm 外圆及端面5.1.1.1确定背吃刀量ap 。
端面总加工余量为0.6mm ,一次走刀加工完成,ap=0.3mm 。
5.1.1.2确定进给量f 。
查表得f=0.4~0.5mm/r ,根据CA6140卧式车床的横向进给量查表取f=0.46mm/r.5.1.1.3确定切削速度Vc 。
查[5]表5-110得Cv=242,m=0.2,xv=0.15,yv=0.35,kMv=0.77,kHv=1.18,khv=0.8,ktV=0.81,ktv=1.0, 刀具寿命选T=60min 。
kv fap T Cv Vc yvxv M ==35.015.02.046.03.060242⨯⨯×0.77×1.18×0.8 ×0.81×1.0 =104m/min5.1.1.4确定机床主轴转速n 。
n=1000Vc/πdw=1000×104/π×38r/min =557r/min查[2]表4-25得相近较小的机床转速为n=500r/min.所以实际的切削速度Vc=89m/min.5.1.1.5计算基本时间T0。
切削加工长度L=50mm ,端面车刀选用主偏角kr=90°,背吃刀量ap=0.3mm,查表得切出及切人量y+△=2mm。
i nfy L T △++=0 =146.0500250⨯⨯+=0.22min5.1.1.6确定辅助时间Tf 。
查表得装夹工件时间为0.8min ,启动机床为0.02min ,启动调节切削液为0.05min ,取量具并测量尺寸为0.5min,共计Tf=1.37min.5.1.2钻Φ12mm 孔至Φ12 018.00+mm5.1.2.1确定进给量f 。
查表5-22得f=0.4~0.5mm/r ,根据CA6140卧式车床的横向进给量查表取f=0.46mm/r 。
5.1.2.2确定切削速度Vc 。
查表得Cv=242,m=0.2,xv=0.15,yv=0.35,kMv=0.77,kHv=1.18,khv=0.8,ktV=0.81,ktv=1.0, 刀具寿命选T=60min 。
故 kv fap T Cv Vc yvxv M ==35.015.02.046.035.060242⨯⨯×0.77×1.18×0.8×0.81×1.0=20m/min5.1.2.3确定机床主轴转速n 。
n =1000Vc/πdw=1000×20/π×50r/min =455r/min查表得相近较小的机床转速为n=350r/min.所以实际的切削速度Vc=25.6m/min.5.2 工序3计算 粗车Φ25±0.0065mm 外圆及端面5.2.1确定背吃刀量ap 。
端面总加工余量为5mm,两次走刀加工。
ap=2.5mm5.2.2 确定进给量f 。
查表5-2得f=0.4~0.5mm/r ,根据CA6140卧式车床的横向进给量查表取f=0.46mm/r 。
5.2.3确定切削速度Vc 。
查表得Cv=242,m=0.2,xv=0.15,yv=0.35,kMv=0.77,kHv=1.18,khv=0.8,ktV=0.81,ktv=1.0, 刀具寿命选T=60min 。
kvfap T Cv Vc yvxv M ==35.015.02.046.05.260242⨯⨯×0.77×1.18×0.8 ×0.81×1.0=71.85mm/r5.2.4确定机床主轴转速n.n=1000Vc/πdw=1000×71.85/π×34r/min =457r/min查表得相近较小的机床转速n=350 r/min ,所以实际的切削速度Vc=45.8m/min 。