1长城哈弗越野车驱动桥后桥设计知识讲解
1长城哈弗越野车驱动桥后桥设计

第1章绪论1.1 概述1.1.1驱动桥总成概述随着汽车工业的发展及汽车技术的提高,驱动桥的设计,制造工艺都在日益完善。
驱动桥也和其他汽车总成一样,除了广泛采用新技术外,在机构设计中日益朝着“零件标准化、部件通用化、产品系列化”的方向发展及生产组织的专业化目标前进。
汽车驱动桥位于传动系的末端, 一般由主减速器,差速器,车轮传动装置和桥壳组成。
其基本功用是增扭、降速和改变转矩的传递方向,即增大由传动轴或直接从变速器传来的转矩,并将转矩合理的分配给左右驱动车轮;其次,驱动桥还要承受作用于路面或车身之间的垂直力,纵向力和横向力,以及制动力矩和反作用力矩等。
根据车桥上车轮的作用,车桥又可分为转向桥、驱动桥、转向驱动桥和支持桥四种类型。
其中,转向桥和支持桥都属于从动桥,一般越野车多以前桥为转向桥,而后桥为驱动桥。
驱动桥的结构型式与驱动车轮的悬挂型式密切相关。
当驱动车轮采用非独立悬挂时,例如在绝大多数的载货汽车和部分小轿车上,都是采用非断开式驱动桥;当驱动车轮采用独立悬挂时,则配以断开式驱动桥。
1.1.2 驱动桥设计的要求设计驱动桥时应当满足如下基本要求:1)选择适当的主减速比,以保证汽车在给定的条件下具有最佳的动力性和燃油经济性。
外廓尺寸小,保证汽车具有足够的离地间隙,以满足通过性的要求。
2)齿轮及其它传动件工作平稳,噪声小。
在各种载荷和转速工况下有较高的传动效率。
3)具有足够的强度和刚度,以承受和传递作用于路面和车架或车身间的各种力和力矩;在此条件下,尽可能降低质量,尤其是簧下质量,减少不平路面的冲击载荷,提高汽车的平顺性。
与悬架导向机构运动协调。
4)结构简单,加工工艺性好,制造容易,维修,调整方便。
1.2 驱动桥设计方案的确定1.2.1 主减速器结构方案的确定1)主减速器齿轮的类型螺旋锥齿轮能承受大的载荷,而且工作平稳,即使在高速运转时其噪声和振动也是很小的。
本次设计采用螺旋锥齿轮。
2)主减速器主动锥齿轮的支承形式及安装方式的选择本次设计选用:主动锥齿轮:骑马式支撑(圆锥滚子轴承)从动锥齿轮:骑马式支撑(圆锥滚子轴承)3)从动锥齿轮的支承方式和安装方式的选择从动锥齿轮的两端支承多采用圆锥滚子轴承,安装时应使它们的圆锥滚子大端相向朝,而小端相向朝外。
越野车驱动桥后桥主要部件的设计

摘要汽车驱动桥一般由主减速器、差速器、半轴以及桥壳四部分组成,其基本功用是增大由传动轴或直接由变速器传来的转矩,将转矩分配给左、右驱动轮,并使左、右驱动车轮具有汽车行驶运动学所要求的差速功能;此外,还要承受作用于路面和车架或车厢之间的铅垂力、纵向力和横向力。
本文介绍了越野车驱动桥后桥主要部件的设计方法以及设计过程。
论述了驱动桥后桥的总体结构,分析了驱动桥后桥各部分结构型式及布置方式,确定了总体设计方案以及驱动桥后桥的基本尺寸数据。
本文越野车驱动桥后桥采用整体式驱动桥,螺旋锥齿轮的单级减速器,普通对称式圆锥行星齿轮差速器,全浮式半轴及整体式桥壳。
同时进行了越野车驱动桥后桥相应的参数计算、几何尺寸计算、强度校核及材料的选取等工作。
最后使用AutoCAD 进行平面制图。
关键词驱动桥;设计;越野车;材料;减速器-I-AbstractGeneral from the main drive axle reducer, differential, axle and axle housing composed of four parts, and its basic use is increased by the transmission shaft, or directly from the transmission from the torque, the torque distribution to the left and right-hand drive cars round, and left and right wheel drive car with a kinematic differential required functions. In addition, the role also have to face or on the road and inside the frame between the vertical force, vertical force and horizontal force.This paper introduces the sport utility vehicle rear drive axle of the main components of design methods and design process. After the drive axle on the bridge's overall structure, an analysis of the rear axle drive axle parts and layout structure, identifying a design program and rear drive axle of the basic size of the data. In this paper, cross-country drive axle vehicles using integrated rear axle drive axle, spiral bevel gear reducer of single-stage, general symmetric cone planetary gear differential, full floating axle and axle housing the overall style. At the same time, calculate a sport utility vehicle rear drive axle of the corresponding parameters, geometric dimensions, the intensity calibration and the selection of materials and so on. Finally, using the AutoCAD soft ware for mapping plane.Keywords Drive Axle; Design; SUV; Material; Reducer-II-目录摘要 (I)Abstract (II)目录 (III)第1章绪论 (1)1.1 课题的背景 (1)1.2 课题的意义 (2)1.3 国内外研究现状 (2)第2章驱动桥简介与设计方案确定 (4)2.1 概述 (4)2.1.1 驱动桥总成概述 (4)2.1.2 驱动桥设计的要求 (4)2.2 驱动桥设计方案的确定 (4)2.2.1 主减速器结构方案的确定 (4)2.2.2 差速器结构方案的确定 (5)2.2.3 半轴形式的确定 (6)2.2.4 桥壳型式的确定 (6)2.3 本章小结 (7)第3章主减速器设计 (8)3.1 主减速比的计算 (8)3.2 主减速齿轮计算载荷的确定 (9)3.3 主减速器齿轮参数的选择 (10)3.3.1 齿数的选择 (10)3.3.2 节圆直径地选择 (10)3.3.3 齿轮端面模数的选择 (12)3.3.4 齿面宽的选择 (12)3.3.5 螺旋锥齿轮螺旋方向 (12)3.3.6 螺旋角的选择 (12)3.4 主减速器螺旋锥齿轮的几何尺寸计算与强度计算 (12)3.4.1 主减速器螺旋锥齿轮的几何尺寸计算 (12)3.4.2 主减速器螺旋锥齿轮的强度计算 (12)3.5 主减速器齿轮的材料及热处理 (17)3.6 主减速器轴承的计算 (17)3.6.1 作用在主减速器主动齿轮上的力 (18)3.6.2 主减速器轴承载荷的计算 (19)-III-3.7 主减速器的润滑 (20)3.8 本章小结 (20)第4章差速器设计 (21)4.1 概述 (21)4.2 对称式圆锥行星齿轮差速器 (21)4.2.1 差速器齿轮的基本参数选择 (22)4.2.2 差速器齿轮的几何尺寸计算与强度计算 (26)4.3 本章小结 (27)第5章半轴设计 (28)5.1 概述 (28)5.2 半轴的设计与计算 (28)5.2.1 全浮式半轴的设计计算 (28)5.2.2 半轴的结构设计及材料与热处理 (30)5.3 本章小结 (31)第6章驱动桥桥壳的强度计算 (32)6.1 概述 (32)6.2 桥壳的受力分析及强度计算 (32)6.2.1 桥壳的静弯曲应力计算 (32)6.2.2 在不平路面冲击载荷作用下桥壳的强度计算 (33)6.2.3 汽车以最大牵引力行驶时的桥壳的强度计算 (33)6.2.4 汽车紧急制动时的桥壳强度计算 (35)6.2.5 汽车受最大侧向力时桥壳的强度计算 (36)6.3 本章小结 (39)结论 (40)致谢 (41)参考文献 (42)附录1 (43)附录2 (46)-IV--V-第1章绪论1.1课题的背景随着汽车工业的逐渐发展以及汽车技术的提高,驱动桥的设计、制造工艺都在日益完善。
越野车后桥设计
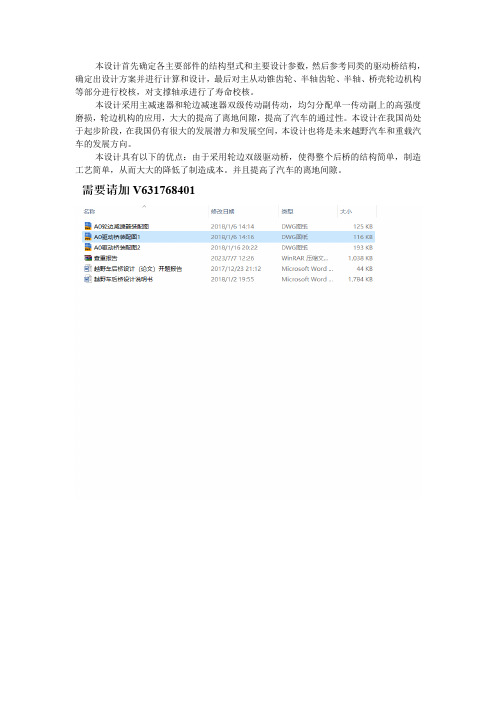
本设计首先确定各主要部件的结构型式和主要设计参数,然后参考同类的驱动桥结构,确定出设计方案并进行计算和设计,最后对主从动锥齿轮、半轴齿轮、半轴、桥壳轮边机构等部分进行校核,对支撑轴承进行了寿命校核。
本设计采用主减速器和轮边减速器双级传动副传动,均匀分配单一传动副上的高强度磨损,轮边机构的应用,大大的提高了离地间隙,提高了汽车的通过性。
本设计在我国尚处于起步阶段,在我国仍有很大的发展潜力和发展空间,本设计也将是未来越野汽车和重载汽车的发展方向。
本设计具有以下的优点:由于采用轮边双级驱动桥,使得整个后桥的结构简单,制造工艺简单,从而大大的降低了制造成本。
并且提高了汽车的离地间隙。
驱动桥设计知识点

驱动桥设计知识点一、引言驱动桥作为汽车动力系统中的重要组成部分,承担着将发动机的动力传递到汽车的驱动轮上的重要任务。
在驱动桥的设计中,需要考虑到各种因素,如驱动方式、扭矩分配、差速器的作用等。
本文将介绍驱动桥设计的几个关键知识点。
二、驱动方式1. 前驱动桥前驱动桥是指驱动力传递到车辆前轮的设计方式。
它具有结构简单、空间利用率高等优点,常用于小型、紧凑型汽车。
前驱动桥的设计需要考虑到动力输出的效率、车辆转向的稳定性等因素。
2. 后驱动桥后驱动桥是指驱动力传递到车辆后轮的设计方式。
相比于前驱动桥,后驱动桥具有更好的操控性能和牵引力,适用于大型、高性能汽车。
后驱动桥的设计需要注意驱动力和刹车力的分配,以保证车辆的平稳行驶。
3. 四驱动桥四驱动桥是指同时将动力传递到四个车轮的设计方式。
四驱动桥通常应用于越野车和SUV等需要在复杂路况下保持优良牵引力的车辆。
在四驱动桥的设计中,需要考虑到前后桥之间的扭矩分配以及前后轴之间的差速器的作用。
三、扭矩分配在驱动桥的设计中,扭矩分配是一个关键的问题。
合理的扭矩分配可以使车辆在加速、转向和刹车时保持稳定。
一般情况下,驱动桥会根据车辆的重心、车轮的抓地力以及车辆的操控需求来进行扭矩的分配。
四、差速器差速器是驱动桥中的重要组成部分,它起到了将扭矩分配到两个驱动轮上的作用。
差速器可以通过不同的齿轮传动来实现扭矩的分配,同时还可以允许车轮在行驶过程中的差速旋转,提高车辆的操控性能和通过性能。
五、总结驱动桥作为汽车动力系统中的重要组成部分,在车辆的性能和稳定性方面起着至关重要的作用。
驱动桥的设计需要考虑到驱动方式、扭矩分配以及差速器的作用等多个因素。
通过合理的设计和创新,可以为汽车提供更好的操控性能和驾驶体验。
本文介绍了驱动桥设计的几个关键知识点,希望能为读者对驱动桥设计提供一定的了解和参考。
汽车技术的不断发展和创新将进一步推动驱动桥设计的进步,提升汽车的性能和安全性。
越野车驱动桥设计课程设计

越野车驱动桥设计课程设计一、课程目标知识目标:1. 让学生理解驱动桥的基本结构、工作原理及其在越野车中的作用;2. 掌握驱动桥设计中涉及的关键参数和计算方法;3. 了解不同驱动桥形式的优缺点,并能结合实际需求进行选择。
技能目标:1. 培养学生运用CAD软件进行驱动桥三维建模的能力;2. 培养学生运用仿真软件对驱动桥进行性能分析的能力;3. 提高学生团队协作、沟通交流以及解决实际工程问题的能力。
情感态度价值观目标:1. 培养学生对汽车工程技术的兴趣和热爱,激发创新意识;2. 培养学生严谨、务实的科学态度,注重实践与理论相结合;3. 增强学生的环保意识,了解绿色、可持续发展的重要性。
课程性质:本课程为实践性较强的课程,旨在让学生通过实际操作,掌握驱动桥设计的基本方法和技能。
学生特点:学生为高年级本科生,具有一定的机械原理、汽车构造和CAD软件应用基础。
教学要求:结合学生特点和课程性质,将课程目标分解为具体的学习成果,注重理论与实践相结合,提高学生的综合运用能力。
在教学过程中,注重启发式教学,引导学生主动探究,培养学生的创新能力和实际操作能力。
1. 驱动桥的基本结构和工作原理:讲解驱动桥的组成部分、各部件功能及相互关系,分析驱动桥在越野车中的作用及工作原理。
相关教材章节:第二章“汽车驱动系统及驱动桥概述”2. 驱动桥关键参数计算:介绍驱动桥设计中涉及的关键参数,如扭矩、齿数、模数等,讲解计算方法及注意事项。
相关教材章节:第三章“驱动桥的设计计算”3. 驱动桥形式及选择:分析不同驱动桥形式的优缺点,探讨如何根据越野车性能需求选择合适的驱动桥形式。
相关教材章节:第四章“驱动桥的结构形式及选择”4. CAD软件在驱动桥设计中的应用:教授学生运用CAD软件进行驱动桥三维建模,提高设计效率。
相关教材章节:第五章“CAD软件在汽车零部件设计中的应用”5. 仿真软件在驱动桥性能分析中的应用:介绍仿真软件的使用方法,指导学生进行驱动桥性能分析。
驱动桥基础知识讲解

双速主减速器结构示意图
×
高速主传动比: i0= i01
低速主传动比: i0= i01 × i02
五、贯通式主减速器
▪ 主要应用于多轴驱动的汽车,具有方便布置,结 构简化,零部件通用性好特点
贯通式主减速器
第三节 差速器
▪ 功用:
➢ 汽车转弯或在不平路面上行驶时,左右车轮 以不同速度滚动,以保证车轮作纯滚动。
第十六章 驱动桥
▪ 主要内容:
➢ 概述 ➢ 主减速器:单级、双级、轮边、双速、贯通式的特点 ➢ 差速器:齿轮式差速器、防滑差速器 ➢ 半轴与桥壳:半轴支承和结构,桥壳分类、特点
第一节 概述
驱动桥组成:
主减速器、差速器、半轴和驱动桥桥壳等。
桥壳 主减速 器
差速 器
轮毂
半轴
驱动桥的功用
▪ 将动力传递给驱动轮; ▪ 通过主减速器实现降速增扭的作用; ▪ 发动机纵置时,通过主减速器圆锥齿轮改
第二节 主减速器
▪ 作用:
➢ 减速增扭;改变扭矩的方向。
▪ 分类:
➢ 按传动齿轮副的数目: 单级主减速器 双级主减速器 轮边减速器
➢ 按主减速器档位: 单速式 双速式
➢ 按齿轮副结构形式: 圆柱齿轮式、圆锥齿轮式、准双曲面齿轮式
几种类型的主减速器
▪ 单级主减速器 ▪ 双级主减速器 ▪ 轮边减速器 ▪ 双速主减速器 ▪ 贯通式主减速器
差速原理
主减从动齿轮--差速器壳--行星齿轮轴--行星齿轮--半轴齿轮
差速原理
结论
▪ 左右两侧半轴的速度之和等于差速器壳速 度的2倍,与行星齿轮的速度无关
▪ 分析:
➢ 当任意一侧车轮转速为零时 ➢ 当差速器壳的速度为零时
差速器的转矩分配
汽车驱动桥的设计

汽车驱动桥的设计汽车驱动桥是将发动机的动力传递到车轮上的重要部件,它承载着扭矩的传递、转向力和悬挂的载荷,直接影响到汽车的动力性能、行驶稳定性和操控性能。
本文将从结构设计、功能和类型分类、工作原理和配套系统等方面进行阐述。
一、结构设计汽车驱动桥主要由差速器、后桥壳、半轴、主减速齿轮和齿轮箱等部件组成。
差速器通常位于驱动轴两半轴之间,起到分配扭矩和使驱动轮各自具有不同转速的作用。
后桥壳是驱动桥的承载结构,负责支撑和固定驱动桥的各个部件。
二、功能和类型分类汽车驱动桥的主要功能是将发动机的动力转化为车轮的动力,并且通过差速器的作用,使两个驱动轮以不同的转速旋转。
根据驱动轮的数量不同,可以将汽车驱动桥分为前驱动桥、后驱动桥和四驱动桥。
其中,前驱动桥一般布置在驾驶员座位后面,主要用于小型轿车和城市SUV;后驱动桥布置在车辆的后部,主要用于大型SUV和商用车;四驱动桥则将动力传递到四个车轮上,提供更强的通过性和驾驶稳定性。
三、工作原理汽车驱动桥的工作原理主要包括力的传递、扭矩的分配和转速的差异化。
当发动机输出扭矩传递到差速器时,差速器将扭矩通过齿轮传递到后桥壳,由主减速齿轮将扭矩分配到左右两个半轴上。
同时,差速器还可以使驱动轮各自具有不同的转速,以适应车辆转弯和路面状态的变化。
四、配套系统汽车驱动桥还有一些配套系统,用于提升驾驶性能。
其中,差速器锁定功能可以让两个驱动轮以相同的转速旋转,提供更强的通过性能;牵引力控制系统可以通过降低驱动轮的滑动,提供更好的牵引力,提高车辆的爬坡能力;加速差速器可以通过改变齿轮的传动比,提供更快的加速性能。
总之,汽车驱动桥作为汽车动力传递的核心部件,其设计要满足高强度、高刚度和轻量化的要求。
同时,根据不同的车型和用途,还要考虑到其功能需求和工作环境,以提供更好的驾驶性能和操控性能。
SUV驱动桥设计方案传动系统与动力输出匹配策略分析
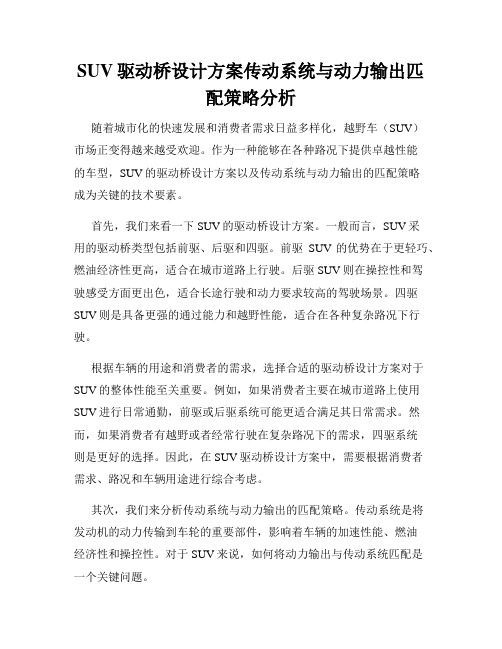
SUV驱动桥设计方案传动系统与动力输出匹配策略分析随着城市化的快速发展和消费者需求日益多样化,越野车(SUV)市场正变得越来越受欢迎。
作为一种能够在各种路况下提供卓越性能的车型,SUV的驱动桥设计方案以及传动系统与动力输出的匹配策略成为关键的技术要素。
首先,我们来看一下SUV的驱动桥设计方案。
一般而言,SUV采用的驱动桥类型包括前驱、后驱和四驱。
前驱SUV的优势在于更轻巧、燃油经济性更高,适合在城市道路上行驶。
后驱SUV则在操控性和驾驶感受方面更出色,适合长途行驶和动力要求较高的驾驶场景。
四驱SUV则是具备更强的通过能力和越野性能,适合在各种复杂路况下行驶。
根据车辆的用途和消费者的需求,选择合适的驱动桥设计方案对于SUV的整体性能至关重要。
例如,如果消费者主要在城市道路上使用SUV进行日常通勤,前驱或后驱系统可能更适合满足其日常需求。
然而,如果消费者有越野或者经常行驶在复杂路况下的需求,四驱系统则是更好的选择。
因此,在SUV驱动桥设计方案中,需要根据消费者需求、路况和车辆用途进行综合考虑。
其次,我们来分析传动系统与动力输出的匹配策略。
传动系统是将发动机的动力传输到车轮的重要部件,影响着车辆的加速性能、燃油经济性和操控性。
对于SUV来说,如何将动力输出与传动系统匹配是一个关键问题。
传动系统的选择包括手动变速器、自动变速器以及近年来兴起的CVT变速器等。
手动变速器具有操作灵活、性能稳定的优点,适合对驾驶操控有要求的消费者。
自动变速器则能提供更舒适的驾乘体验,适合日常通勤和长途驾驶。
CVT变速器则兼具自动变速器和手动变速器的优点,能够实现更加平顺的动力输出。
在动力输出方面,SUV通常需要具备较高的扭矩和马力输出,以适应各种路况和行驶需求。
针对不同的动力输出需求,可采取调整发动机的调校策略以及匹配不同的传动比例来实现。
特别是在SUV中,可以通过分时四驱系统或者主动四驱系统来实现对于动力输出的不同配比,以满足消费者在城市和越野行驶中的需求。
- 1、下载文档前请自行甄别文档内容的完整性,平台不提供额外的编辑、内容补充、找答案等附加服务。
- 2、"仅部分预览"的文档,不可在线预览部分如存在完整性等问题,可反馈申请退款(可完整预览的文档不适用该条件!)。
- 3、如文档侵犯您的权益,请联系客服反馈,我们会尽快为您处理(人工客服工作时间:9:00-18:30)。
第1章绪论1.1 概述1.1.1驱动桥总成概述随着汽车工业的发展及汽车技术的提高,驱动桥的设计,制造工艺都在日益完善。
驱动桥也和其他汽车总成一样,除了广泛采用新技术外,在机构设计中日益朝着“零件标准化、部件通用化、产品系列化”的方向发展及生产组织的专业化目标前进。
汽车驱动桥位于传动系的末端, 一般由主减速器,差速器,车轮传动装置和桥壳组成。
其基本功用是增扭、降速和改变转矩的传递方向,即增大由传动轴或直接从变速器传来的转矩,并将转矩合理的分配给左右驱动车轮;其次,驱动桥还要承受作用于路面或车身之间的垂直力,纵向力和横向力,以及制动力矩和反作用力矩等。
根据车桥上车轮的作用,车桥又可分为转向桥、驱动桥、转向驱动桥和支持桥四种类型。
其中,转向桥和支持桥都属于从动桥,一般越野车多以前桥为转向桥,而后桥为驱动桥。
驱动桥的结构型式与驱动车轮的悬挂型式密切相关。
当驱动车轮采用非独立悬挂时,例如在绝大多数的载货汽车和部分小轿车上,都是采用非断开式驱动桥;当驱动车轮采用独立悬挂时,则配以断开式驱动桥。
1.1.2 驱动桥设计的要求设计驱动桥时应当满足如下基本要求:1)选择适当的主减速比,以保证汽车在给定的条件下具有最佳的动力性和燃油经济性。
外廓尺寸小,保证汽车具有足够的离地间隙,以满足通过性的要求。
2)齿轮及其它传动件工作平稳,噪声小。
在各种载荷和转速工况下有较高的传动效率。
3)具有足够的强度和刚度,以承受和传递作用于路面和车架或车身间的各种力和力矩;在此条件下,尽可能降低质量,尤其是簧下质量,减少不平路面的冲击载荷,提高汽车的平顺性。
与悬架导向机构运动协调。
4)结构简单,加工工艺性好,制造容易,维修,调整方便。
1.2 驱动桥设计方案的确定1.2.1 主减速器结构方案的确定1)主减速器齿轮的类型螺旋锥齿轮能承受大的载荷,而且工作平稳,即使在高速运转时其噪声和振动也是很小的。
本次设计采用螺旋锥齿轮。
2)主减速器主动锥齿轮的支承形式及安装方式的选择本次设计选用:主动锥齿轮:骑马式支撑(圆锥滚子轴承)从动锥齿轮:骑马式支撑(圆锥滚子轴承)3)从动锥齿轮的支承方式和安装方式的选择从动锥齿轮的两端支承多采用圆锥滚子轴承,安装时应使它们的圆锥滚子大端相向朝内,而小端相向朝外。
为了防止从动锥齿轮在轴向载荷作用下的偏移,圆锥滚子轴承应用两端的调整螺母调整。
主减速器从动锥齿轮采用无辐式结构并用细牙螺钉以精度较高的紧配固定在差速器壳的凸缘上。
4)主减速器的轴承预紧及齿轮啮合调整支承主减速器的圆锥滚子轴承需要预紧以消除安装的原始间隙、磨合期间该间隙的增大及增强支承刚度。
分析可知,当轴向力于弹簧变形呈线性关系时,预紧使轴向位移减小至原来的1/2。
预紧力虽然可以增大支承刚度,改善齿轮的啮合和轴承工作条件,但当预紧力超过某一理想值时,轴承寿命会急剧下降。
主减速器轴承的预紧值可取为以发动机最大转矩时换算所得轴向力的30%。
主动锥齿轮轴承预紧度的调整采用调整螺母(利用轴承座实现),从动锥齿轮轴承预紧度的调整采用调整螺母。
5)主减速器的减速形式主减速器的减速形式分为单级减速、双级减速、单级贯通、双级贯通、主减速及轮边减速等。
减速形式的选择与汽车的类型及使用条件有关,有时也与制造厂的产品系列及制造条件有关,但它主要取决于动力性、经济性等整车性能所要求的主减速比的大小及驱动桥下的离地间隙、驱动桥的数目及布置形式等。
本次设计主要从越野车传动比及载重量超过2t,保证离地间隙等方面考虑,主减速器采用单级减速即可。
1.2.2 差速器结构方案的确定差速器的结构型式选择,应从所设计汽车的类型及其使用条件出发,以满足该型汽车在给定的使用条件下的使用性能要求。
差速器的结构型式有多种,大多数汽车都属于公路运输车辆,对于在公路上和市区行驶的汽车来说,由于路面较好,各驱动车轮与路面的附着系数变化很小,因此几乎都采用了结构简单、工作平稳、制造方便、用于公路汽车也很可靠的普通对称式圆锥行星齿轮差速器。
1.2.3 半轴型式的确定(a)半浮式;(b)3/4浮式;(c)全浮式图1.1 半轴型式及受力简图3/4浮式半轴,因其侧向力引起弯矩使轴承有歪斜的趋势,这将急剧降低轴承的寿命,故未得到推广。
全浮式半轴广泛应用于轻型以上的各类汽车上。
本次设计选择全浮式半轴。
1.2.4 桥壳型式的确定桥壳有可分式、整体式和组合式。
整体式桥壳的特点是将整个桥壳制成一个整体,桥壳犹如一个整体的空心梁,其强度及刚度都比较好。
且桥壳与主减速器壳分作两体,主减速器齿轮及差速器均装在独立的主减速壳里,构成单独的总成,调整好后再由桥壳中部前面装入桥壳内,并与桥壳用螺栓固定在一起。
使主减速器和差速器的拆装、调整、维修、保养等都十分方便。
本次设计选择整体式桥壳。
1.3本章小结本章首先进行了驱动桥总成的概述。
通过分析确定了驱动桥各主要部件的型式。
主减速器的减速形式,主减速器齿轮的类型,主、从动锥齿轮的支承形式及安装方式,主减速器的轴承预紧及齿轮啮合调整,差速器、半轴及桥壳型式的初步选定。
第2章 主减速器设计2.1主减速比的计算主减速比对主减速器的结构形式、轮廓尺寸、质量大小以及当变速器处于最高档位时汽车的动力性和燃料经济性都有直接影响。
0i 的选择应在汽车总体设计时和传动系统的总传动比一起由整车动力计算来确定。
可利用在不同的下的功率平衡图来计算对汽车动力性的影响。
通过优化设计,对发动机与传动系参数作最佳匹配的方法来选择0i 值,可是汽车获得最佳的动力性和燃料经济性。
表2.1 基本参数表为了得到足够的功率而使最高车速稍有下降,一般选得比最小值大10%~25%,即按下式选择:LBFh gh a Pr i i i v n r i max 0)472.0~377.0(= (2.1)式中 r r ——车轮的滚动半径,r r =0.388; gh i ——变速器最高档传动比,gh i =0.856; gh i ——分动器或加力器的高档传动比,gh i =1;LB i ——轮边减速器的传动比,LB i =1。
经计算,本文选取0i =6.408。
2.2 主减速齿轮计算载荷的确定通常是将发动机最大转矩配以传动系最低档传动比时和驱动车轮打滑时这两种情况下作用于主减速器从动齿轮上的转矩(ϕj je T T ,)的较小者,作为载货汽车计算中用以验算主减速器从动齿轮最大应力的计算载荷。
即T TL e je K i T T η⋅⋅⋅=0max /n=2173.496 (m N ⋅) (2.2)LBLB rj i r G T ⋅⋅⋅=ηϕϕ2=6110.574(m N ⋅) (2.3)式中:max e T ——发动机最大扭矩190m N ⋅;TL i ——由发动机到所计算的为加速器从动齟轮之间的传动系最低档传动比;TL i =0i 1i =3.967×6.408=25.421T η——上述传动部分的效率,取T η=0.9; 0K ——超载系数,取0K =1.0;r r ——滚动半径,取r r =(265毫米 X 65%)+(17 X 25.4毫米/2)=0.388mm ; n ——驱动桥数目2;2G ——汽车满载时驱动桥给水平地面的最大负荷,N ;但后桥来说还应考虑到汽车加速时负载增大量,可初取:2G =N G 95.15118%558.9=⨯⨯满LB LB i ,η——分别为由所计算的主减速器从动齿轮到驱动轮之间的传动效率和减速比,分别取0.96和1。
由式(2.2),(2.3)求得的计算载荷,是最大转矩而不是正常持续转矩,不能用它作为疲劳损坏依据。
对于公路车辆来说,使用条件较非公路车俩稳定,其正常持转矩是根据所谓平均牵引力的值来确定的,即主加速器的平均计算转矩为 jm T =)()(P H R LB LB rT a f f f ni r G G ++⋅⋅⋅+η=989.812(m N ⋅) (2.4)式中:a G ——汽车满载总重1960×9.8=19208N ;T G ——所牵引的挂车满载总重,N ,仅用于牵引车取T G =0;R f ——道路滚动阻力系数,越野车通常取0.020~0.035,可初选R f =0.034; H f ——汽车正常使用时的平均爬坡能力系数。
货车通常取0.09~0.30,可初选取H f =0.15;P f ——汽车性能系数])(195.016[1001maxe T a P T G Gf +-=(2.5) 当max)(195.0e T a T G G +=46.86>16时,取P f =0.134。
.2.3 主减速器齿轮参数的选择1)齿数的选择 对于普通单级主减速器,当0i 较大时,则应尽量使主动齿轮的齿数1z 取得小些,以得到满意的驱动桥离地间隙,当0i≥6时,1z 的最小值为5,但是为了啮合平稳及提高疲劳强度,1z 最好大于5.,这里1z 取7。
为了磨合均匀,主、从动齿轮的齿数1z 、2z 之间应避免有公约数,这里2z 取45。
2)节圆直径地选择 根据从动锥齿轮的计算转矩(见式2.2,式2.3并取两者中较小的一个为计算依据)按经验公式选出:322j d T K d ⋅==168.395~207.256 mm (2.6)式中:2d K ——直径系数,取2d K =13~16;j T ——计算转矩,m N ⋅,取jm T ,je T 较小的。
初取2d =200mm 。
3)齿轮端面模数的选择2d 选定后,可按式22/z d m ==4.5算出从动齿轮大端模数,并用下式校核t m m K =~5.181m K ——模数系数,取m K =0.3~04。
4)齿面宽的选择 汽车主减速器螺旋锥鼿轮鼿面宽度推荐为:F=0.1552d =31mm ,可初取F 2=35mm 。
5)螺旋锥齿轮螺旋方向 一般情况下主动齿轮为左旋,从动齿轮为右旋,以使二齿轮的轴向力有互相斥离的趋势。
6)螺旋角的选择 螺旋角应足够大以使≥F m 1.25。
因F m 越大传动就越平稳噪声越低。
螺旋角过大时会引起轴向劚亦过大,因此应有一个适当的范围。
在一般机械制造用的标准制中,螺旋角推荐用35°。
2.4 主减速器螺旋锥齿轮的几何尺寸计算与强度计算2.4.1 主减速器螺旋锥齿轮的几何尺寸计算2.4.2 主减速器螺旋锥齿轮的强度计算在完成主减速器齿轮的几何计算之后,应对其强度进行计算,以保证其有足够的强度和寿命以及安全可靠性地工作。
在进行强度计算之前应首先了解齿轮的破坏形式及其影响因素。
螺旋锥齿轮的强度计算:(1)主减速器螺旋锥齿轮的强度计算 ①单位齿长上的圆周力FPp =(2.7) 式中:p ——单位齿长上的圆周力,N/mm;P ——作用在齿轮上的圆周力,N ,按发动机最大转矩max e T 和最大附着力矩两种载荷工况进行计算;按发动机最大转矩计算时:F d i T p g e ⋅⋅⋅=21013max =339.286<893N/mm (2.8)g i ——为一档传动比,取g i =3.967按最大附着力矩计算时:F d rG p r ⋅⋅⋅⋅=210232ϕ=1424.6/N mm (2.9) 虽然附着力矩产生的p 很大,但由于发动机最大转矩的限制p 最大只有893N/mm,可知,校核成功。