平均无故障时间(MTBF)
UPS电源单机的平均无故障工作时间

UPS电源单机的平均无故障工作时间(MTBF)在UPS电源供电系统中,我们常用平均无故障工作时间(MTBF)来评价UPS电源的可靠性。
它代表的物理含义是:从UPS电源投入运行起,直到因UPS电源供电系统中的某个关键器件"出故障",并最终导致在其输出端出现"停电"故障时为止的平均工作时间。
显而易见,UPS电源的MTBF值越大越好。
其大小不仅受控于UPS电源中的各种元件和部件的失效率(λ),还受控于UPS电源设计方案和制备工艺。
这就意味着:即使UPS电源厂家釆用的是相同的元器件。
然而,由于设计方案和制造工艺的不同、也会导致不同的UPS电源具有不同的失效率(λ)的情况发生。
平均无故障工作时间(MTBF)与失效率(λ)之间的关系为:MTBF=1/λ如图1所示,在最常用和最可靠的带"输出隔离变压器"的双变換、在线式UPS 电源中、有如下3条供电通道:逆变器供电通道:由输入交流电源、整流器(电池)、逆变器、输出隔离变压器、输出静态开关/断路器开关等所组成的UPS电源逆变器供电通道;交流旁路供电通道:由输入交流电源和旁路"静态开关"等所组成的UPS电源交流旁路供电通道维修旁路供电通道:由输入交流电源和手动维修旁路开关所组成的UPS电源维修旁路供电通道。
因此,对于1台UPS电源单机电源来说,它有两个平均无故障工作时间(MTBF)值:(a)UPS电源逆变器的MTBFI:它代表当UPS电源被置于"不帶交流旁路"工作状态下运行时,从UPS电源投入正常工作时起、到因故致使UPS电源的逆变器进入"自动关机",并造成UPS电源输出"停电"时的平均无故障工作时间。
从某种意义上讲、对于不允许出现"网络瘫痪"故障的关键性网络来说(例如:政府的电子政务和军事网控系统、电信企业的收费系统、石化和IC生产线、银行的交易和营业系统、交通管理和售票系统等),是不允许它们所用的UPS电源进入"交流旁路(包括交流静态旁路和维修旁路)"工作状态的。
平均无故障工作时间计算公式

平均无故障工作时间计算公式
一、平均无故障工作时间(MTBF)的定义。
平均无故障工作时间是指可修复产品两次相邻故障之间的平均时间,是衡量一个产品(尤其是电器等可修复产品)的可靠性指标。
二、计算公式。
1. 基本公式。
- 对于已知总工作时间T和故障次数n的情况,平均无故障工作时间MTBF=(T)/(n)。
- 例如,某设备运行总时长为1000小时,期间发生了5次故障。
那么根据公式MTBF=(1000)/(5) = 200小时。
2. 当有多个样本设备时。
- 如果有m个相同设备,每个设备的工作时间分别为T_1,T_2,·s,T_m,对应的故障次数分别为n_1,n_2,·s,n_m。
- 首先计算总的工作时间T = T_1+T_2+·s+T_m,总的故障次数n=n_1 +
n_2+·s+n_m。
- 然后再根据基本公式MTBF=(T)/(n)计算。
例如有3台设备,设备1工作了500小时,发生2次故障;设备2工作了800小时,发生3次故障;设备3工作了600小时,发生2次故障。
- 总工作时间T=500 + 800+600=1900小时,总故障次数n = 2+3+2 = 7次。
- 则MTBF=(1900)/(7)≈271.43小时。
平均无故障时间MTBF测试及计算过程
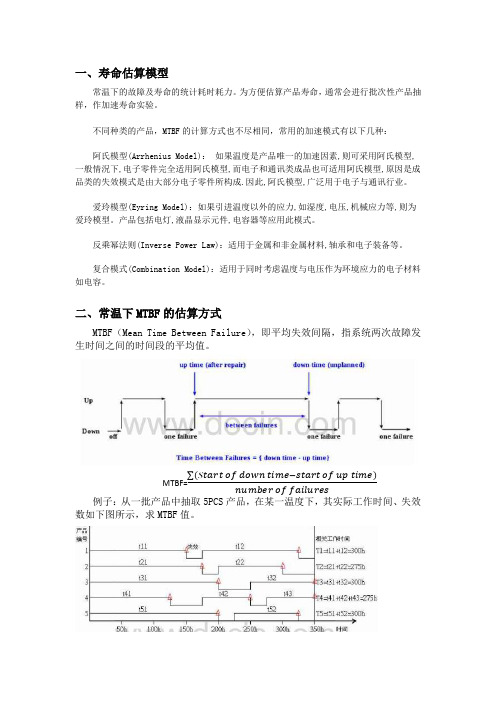
一、寿命估算模型常温下的故障及寿命的统计耗时耗力。
为方便估算产品寿命,通常会进行批次性产品抽样,作加速寿命实验。
不同种类的产品,MTBF 的计算方式也不尽相同,常用的加速模式有以下几种: 阿氏模型(Arrhenius Model): 如果温度是产品唯一的加速因素,则可采用阿氏模型, 一般情況下,电子零件完全适用阿氏模型,而电子和通讯类成品也可适用阿氏模型,原因是成品类的失效模式是由大部分电子零件所构成.因此,阿氏模型,广泛用于电子与通讯行业。
爱玲模型(Eyring Model):如果引进温度以外的应力,如湿度,电压,机械应力等,则为爱玲模型。
产品包括电灯,液晶显示元件,电容器等应用此模式。
反乘幂法则(Inverse Power Law):适用于金属和非金属材料,轴承和电子装备等。
复合模式(Combination Model):适用于同时考虑温度与电压作为环境应力的电子材料如电容。
二、常温下MTBF 的估算方式MTBF (Mean Time Between Failure ),即平均失效间隔,指系统两次故障发生时间之间的时间段的平均值。
MTBF=∑(Start of down time−start of up time)number of failures例子:从一批产品中抽取5PCS 产品,在某一温度下,其实际工作时间、失效数如下图所示,求MTBF 值。
解:带入公式计算MTBF=∑(Start of down time−start of up time )number of failures =T1+T2+T3+T4+T511=145011=131.8 二、MTBF 阿氏模型只有一项加速因子,如温度,且服从指数分布的加速寿命实验,可采用MTBF 阿氏模型计算公式进行估算。
阿氏模型起源于瑞典物理化学家Svandte Arrhenius 1887年提出的阿氏反应方程式.R:反应速度 speed of reactionA:溫度常数 a unknown non-thermal constant EA:活化能 activation energy (eV) K:Boltzmann 常数,等地8.623*10-5 eV/0K. T:为绝对溫度(Kelvin)Ea=(ln L2-ln L1)*k/(1/T2-1/T1) K =EXP[Ea k (1T3−1T1)]MTBF=L1* KEa 为活化能(eV );T1、T2为加速寿命测试的实验温度(需换算为绝对温度参与计算); T3为常温温度25℃,换算为绝对温度为298K ;L1、L2分别为加速寿命测试温度T1、T2下测得的寿命;寿命L=抽样测试总测试时间允许故障数量K 为Boltzmann 常数,值为8.62X 10−5 (eV/K);以同类型产品做参照,其计算过程如下:在85℃条件下测试72小时出现第一次出现故障时间,计T1。
MTBF
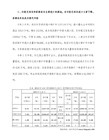
平均故障修复时间 平均故障修复时间(Mean Time To Repair,简称MTTR),源自于IEC 61508中的平均维护时间(Mean Time To Repair),目的是为了清楚界定术语中的时间概念,MTTR是随机变量恢复时间的期望值。它包括确认失效发生所需的时间,以及维护所需要的时间。MTTR也包含获得配件的时间,维修团队的响应时间,记录所有任务的时间,还有将设备重新投入使用使用的时间,即指系统修复一次故障所需要的时间。它是衡量一个产品可靠性的指标,它的值越小说明该系统的可靠性越高。
价值流图分析法 对一个产品来说,以下两条主要流动路径是至关重要的:一是从原材料到达顾客手中的生产流程;二是从概念到正式发布的产品设计流程。价值流就是使一个产品通过这些主要流程所需要的全部活动,包括增值活动、必要但非增值活动和非增值活动(即浪费)三类。研究表明,企业用于增值活动的时间仅占整个流程的极小部分,大部分时间都花在非增值的活动中。价值流图是一种使用铅笔和纸的工具,它有助于观察和理解产品通过价值流过程时的物料流动和信息流动,以及其中的增值和非增值活动,从而发现浪费和确定需要改善的地方,为改善活动定下一个蓝图和方向。同时也便于员工了解企业的状态,提供参与改善的机会。 应用价值流图分析企业生产流程,意味着要从全盘看待问题,而不是集中于某个单独的过程;意味着将改变整体,而不仅仅是优化某个部分。价值流图分析可以是针对企业又称为“四堵墙以内”)的活动进行分析和改善,也可以针对“四堵墙以外”,即从供应商出货起到顾客收货为止的整个价值流的分析和改善。 图二价值流图示意图在价值流分析中,有一套约定俗成的符号供绘制价值流图之用,使用者只要经常运用,就能轻易掌握。价值流图分析法的一般先对运作过程的现状进行分析,即所谓“当前状态图”。从顾客一端开始,首先要了解顾客的需求情况及节拍Takt,因为Takt决定了生产各个工序的节拍。生产节拍不能满足Takt的要求,就有可能导致过量生产或停顿、生产不足或延迟,这些都是浪费。延迟发货还会导致顾客的不满意,造成进一步的信誉损失。然后研究运作流程中的每一道工序,从下游追溯到上游,直至供应商。分析每个工序的增值和非增值活动,包括准备、加工、换型、库存、物料转移方法、质量状况、停机次数、班次、人数等等,记录对应的时间。接着要了解和分析物流信息的传递方法和路径,包括顾客到工厂、工厂到供应商、生产物料计划到各工序的信息传递情况,生产计划是如何下达的。最后,有了上面的资料,就可以计算出整个运作过程的生产周期(TotalProductCycleTime)以及相应的增值时间。通常,人们会发现改善之前增值时间只占Tpct的很小比例,远不足5%。 有了“当前状态图”,管理人员一般都能比较容易地判别和确定出浪费所在及其原因,为消灭浪费和持续改善提供目标。“未来状态图”是以精益思想为指导,按照企业的实际情况,为未来的运作模式指明方向,设计新的精益流程。所谓“未来状态”,也仅仅是基于当前的技术和认知水平,在一定时间内可以达到的较为理想的目标。随着人们技术和认知水平的提高,原来的目标又变得不理想了,人们又进入了一个更高层次的改善循环。如此往复,正是精益思想中“与完美竞争,永无止境”的精髓所在。 价值流图析应用的常见错误 1. 选错跟踪对象 大家很清楚在做价值流图析的时候,选择跟踪的对象是产品或者服务。假设自己是流程中流动的一件产品,观察在形状、功能、包装会发生什么改变。在一般的制造业流程中,作为实物形态的原料,半成品和成品都还比较清楚,不容易出现错误。但在服务业或者行政办公室的环境下,有时候就会犯错误。因为在服务业环境中,在某些环节的人会离开或转移工作,“产品”实际上已经发生了改变或转移,但我们会仍然坚持跟踪原来的对象。 2. 纸上谈兵 指的是在没有实际生产产品或提供服务的情况下去做价值流图析。有时候某些产品并非经常生产,或者碰巧最近一段时间没有生产,或者生产周期太长,但又需要分析其价值流(有时是来自客户的压力,有时是来自管理层的压力)。于是有人在没有“看”到的情况下,依靠现有的作业数据和工程标准(例如生产部或IE部门提供的数据)完成了价值流图析。更有甚者,还以此计算出了项目所取得的所谓“收益”! 他们忘记了精益生产的一些基本原则。首先如果没有实际考察流程中的各种库存,他们实际上得到的是流程图(Process Map),而非价值流图。其次,没有观察到价值流图中的各项时间测量值是怎样来的,所有他们也无法确定这其中存在的浪费以及改善的机会。再者,闭门造车的价值流常会忽略实际操作中一些细节,跟实际的操作差别会导致一线操作人员非常迷惑,失去了应有的指导价值。 对于价值流图析,笔者建议一个月起码做一次,以观察不同情况下的实际状况,并作比较 3. 道听途说 这一点跟第二点有点类似,指的是呆在办公室里而没有深入到现场观察就完成了价值流图析。笔者辅导过许多企业干部,他们一般处于企业中层管理位置,发现他们在很多时候都不太愿意深入实践。在普遍使用计算机的今天,很多数据都会存储在电脑里。在描绘价值流图时,有些人不愿意深入到车间第一线去观察,而宁愿呆在办公室里调用电脑里的数据(如库存量)。还有一种情况是喜欢听别人提供的现场数据(例如叫下属去查找数据,然后回来汇报),但这些数据本身未经确认,具有很大的差异性。从技术的角度而言,有些数据的确是可以从文件或电脑储存的数据中获得,可以把大体的流程图拼凑出来。例如某流程有多少工序,有多少个操作工人,仓库库存有多少,车间的布局如何,走动的距离有多少。 但技术上的正确并不意味着实际上的情况也是如此,实际上的情况可能差别很大。做价值流图析的人如果不深入车间现场,则意味着失去了很多观察到浪费的地方。 4. 重复计算时间 在准备把观察所得填进数据框(information box) 时候,请务必要考虑清楚什么是流程步骤,什么应该放进数据框,什么不应该。例如发生的换型时间 (Changeover time),大家都知道要放进数据框,因为书上都是这样讲的。但仍然有人不明白为什么不单独列出来,在前置时间 (Lead time) 上有个单独的记录。又例如走动时间,假设在两个流程之间花了15分钟的走动时间,那是不是在价值流图上应该单独画个数据框?前面提到的这两个时间算不算流程处理时间?要不要放进数据框? 在这里关键是要把那些造成库存堆积的原因和实际产品或服务的流程分离开来,不能混淆。如上面所举的太长的换型时间和走动距离,往往造成流程的某个地方 / 岗位上库存堆积,是造成企业各种形式库存的原因,其实都是是我们实施精益生产要消除的地方。这不算是产品或服务的真正流程。当我们清点库存的时候,实际上也就把这些因素包括在生产前置时间(Lead time)之内了。 进行价值流图析时,要分析清楚哪些是造成库存积压的原因,哪些才是加工产品或服务的实际流程步骤。 5. 忽略共享资源 在很多情况下,流程中存在着共享资源。共享资源指的是支持 / 服务超过一个产品族的资源,有可能是人,有可能是整条组装生产线,也有可能某台机器。例如,某注塑企业主要生产手机和MP3,喷涂车间某台机器专门给一切较小的零部件提供喷涂,这些小件的产品包括了手机、MP3各种小配件。又例如仓库的收发区域,各种各样的货物、原料都经过这里做收货或发送的处理。在以上的两个例子中,喷涂机器和收货区域都属于共享资源,还包括这里员工。如果忘记掉这一点,则很容易得出错误的结论。 以上面的收发区域作个简单的比较,假设该区域给两个重型车间提供服务,每个车间平均每天会生产80件产品,一天总共收到160个产品,平均每小时收到20件产品,每个车间10件。如果一个收发员一小时能完成10件的工作,这里显然需要两个收发员在此岗位工作。如果在价值流图析中错误地只计算一个产品族的工作量,则会使人认为这个岗位上只需要一个人。也许这个例子太简单,但当你面对数百种产品许多的产品族时,则有可能会发生错误,漏掉或忽略掉一些产品族了。所以一定要留意是不是共享资源。 请记住正确识别共享资源,否则会导致一些重要的计算错误,如节拍时间和周期时间都会算错。 6. 产品族 (系列) 混淆不清。 在批阅企业递交的价值流图时,笔者有时候会发现主价值流图上有很多小的价值流进进出出,看起来非常的复杂,增加了分析的难度。这种问题的发生主要在于开始图析之前的产品族分析没有做好。有些产品族是非常明显的,例如家电企业生产不同型号的电视机、微波炉、冰箱等,一看就知道;有些则不是很明显,例如电子零件生产企业,产品上百种,甚至过千种,产品类型相似,产品加工工序复杂,少则十几道,多则几十道,其中还有许多分支和合流的地方。一般认为研究对象的流程处理工序达到80%以上相同的就可以判为同一个产品族。在分析过程中,如果没有很好的识别流程中的共享资源,也没有很好的跟踪适当的产品或人的流向通常都会导致价值流图非常复杂,不能反映产品族的真正情况,甚至会在错误的路径上越走越远。
数控机床的平均无故障时间
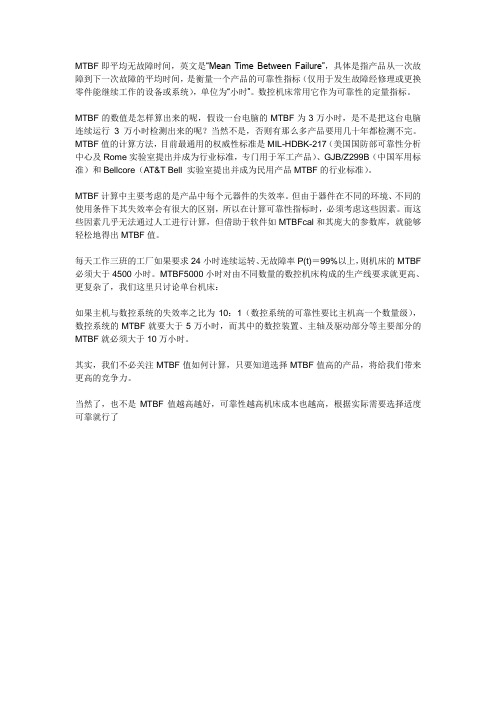
MTBF即平均无故障时间,英文是“Mean Time Between Failure”,具体是指产品从一次故障到下一次故障的平均时间,是衡量一个产品的可靠性指标(仅用于发生故障经修理或更换零件能继续工作的设备或系统),单位为“小时”。
数控机床常用它作为可靠性的定量指标。
MTBF的数值是怎样算出来的呢,假设一台电脑的MTBF为3万小时,是不是把这台电脑连续运行3万小时检测出来的呢?当然不是,否则有那么多产品要用几十年都检测不完。
MTBF值的计算方法,目前最通用的权威性标准是MIL-HDBK-217(美国国防部可靠性分析中心及Rome实验室提出并成为行业标准,专门用于军工产品)、GJB/Z299B(中国军用标准)和Bellcore(AT&T Bell 实验室提出并成为民用产品MTBF的行业标准)。
MTBF计算中主要考虑的是产品中每个元器件的失效率。
但由于器件在不同的环境、不同的使用条件下其失效率会有很大的区别,所以在计算可靠性指标时,必须考虑这些因素。
而这些因素几乎无法通过人工进行计算,但借助于软件如MTBFcal和其庞大的参数库,就能够轻松地得出MTBF值。
每天工作三班的工厂如果要求24小时连续运转、无故障率P(t)=99%以上,则机床的MTBF 必须大于4500小时。
MTBF5000小时对由不同数量的数控机床构成的生产线要求就更高、更复杂了,我们这里只讨论单台机床:如果主机与数控系统的失效率之比为10:1(数控系统的可靠性要比主机高一个数量级),数控系统的MTBF就要大于5万小时,而其中的数控装置、主轴及驱动部分等主要部分的MTBF就必须大于10万小时。
其实,我们不必关注MTBF值如何计算,只要知道选择MTBF值高的产品,将给我们带来更高的竞争力。
当然了,也不是MTBF值越高越好,可靠性越高机床成本也越高,根据实际需要选择适度可靠就行了。
MTBF
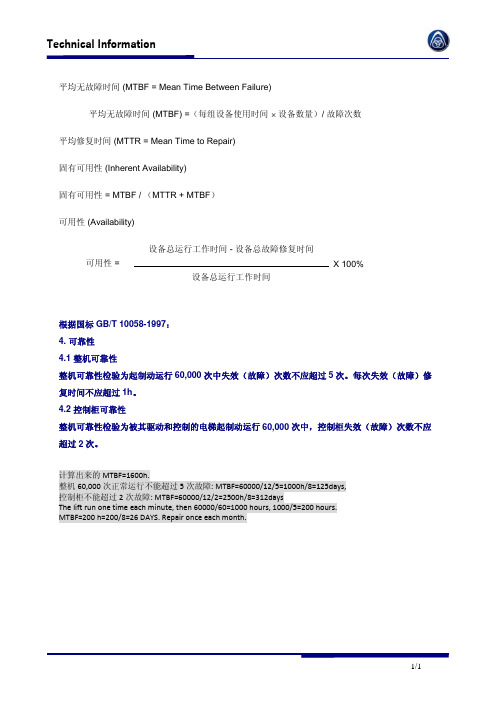
Technical Information
1/1 平均无故障时间 (MTBF = Mean Time Between Failure)
平均无故障时间 (MTBF) =(每组设备使用时间 × 设备数量)/ 故障次数
平均修复时间 (MTTR = Mean Time to Repair)
固有可用性 (Inherent Availability)
固有可用性 = MTBF / (MTTR + MTBF )
可用性 (Availability)
可用性 =
设备总运行工作时间 - 设备总故障修复时间 X 100%
设备总运行工作时间
根据国标GB/T 10058-1997:
4. 可靠性
4.1 整机可靠性
整机可靠性检验为起制动运行60,000次中失效(故障)次数不应超过5次。
每次失效(故障)修复时间不应超过1h 。
4.2 控制柜可靠性
整机可靠性检验为被其驱动和控制的电梯起制动运行60,000次中,控制柜失效(故障)次数不应超过2次。
计算出来的MTBF=1600h.
整机60,000次正常运行不能超过5次故障: MTBF=60000/12/5=1000h/8=125days,
控制柜不能超过2次故障: MTBF=60000/12/2=2500h/8=312days
The lift run one time each minute, then 60000/60=1000 hours, 1000/5=200 hours.
MTBF=200 h=200/8=26 DAYS. Repair once each month.。
平均无故障工作时间MTBF
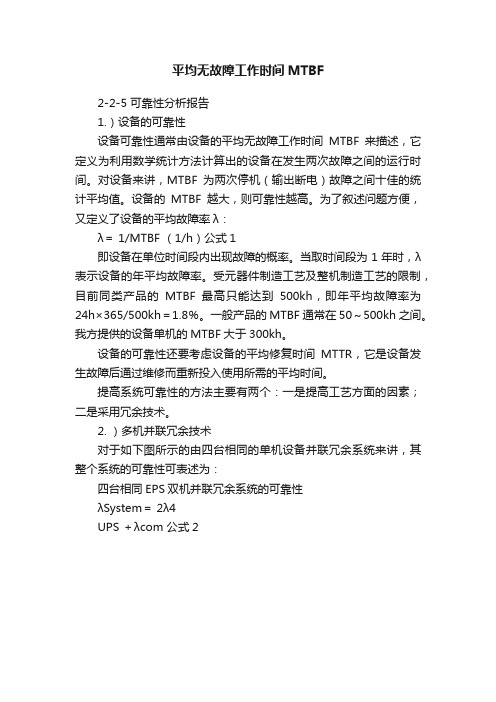
平均无故障工作时间MTBF2-2-5 可靠性分析报告1.)设备的可靠性设备可靠性通常由设备的平均无故障工作时间MTBF来描述,它定义为利用数学统计方法计算出的设备在发生两次故障之间的运行时间。
对设备来讲,MTBF为两次停机(输出断电)故障之间十佳的统计平均值。
设备的MTBF越大,则可靠性越高。
为了叙述问题方便,又定义了设备的平均故障率λ:λ= 1/MTBF (1/h)公式1即设备在单位时间段内出现故障的概率。
当取时间段为1年时,λ表示设备的年平均故障率。
受元器件制造工艺及整机制造工艺的限制,目前同类产品的MTBF最高只能达到500kh,即年平均故障率为24h×365/500kh=1.8%。
一般产品的MTBF通常在50~500kh之间。
我方提供的设备单机的MTBF大于300kh。
设备的可靠性还要考虑设备的平均修复时间MTTR,它是设备发生故障后通过维修而重新投入使用所需的平均时间。
提高系统可靠性的方法主要有两个:一是提高工艺方面的因素;二是采用冗余技术。
2. )多机并联冗余技术对于如下图所示的由四台相同的单机设备并联冗余系统来讲,其整个系统的可靠性可表述为:四台相同EPS双机并联冗余系统的可靠性λSystem=2λ4UPS +λcom 公式23λUPS +μUPS式中,λSystem为整个系统的平均故障率λUPS为单机的平均故障率λcom为公共环节的平均故障率μUPS为的平均维修率由公式2中可以看出,提高μUPS ,减小λUPS和λcom可以减少λSystem,一般情况下,MTBF>>MTTR,即μUPS >>λUPS,则公式2又可近似为:λSystem=2λ4UPS+λcomμUPS=2λUPS ·λUPS+λcomμUPS通常情况下,公共环节的设计原则是少而精,所及平均故障率极低。
若忽略λcom,则有λSystem≈ 2λUPS ·λUPSμUPS又因2λUPS << μUPS,即2λUPS<<1,μUPS故有λSystem<<λUPS即整个并机冗余系统的平均故障率比单机大大地降低了。
MTBF计算方法概论
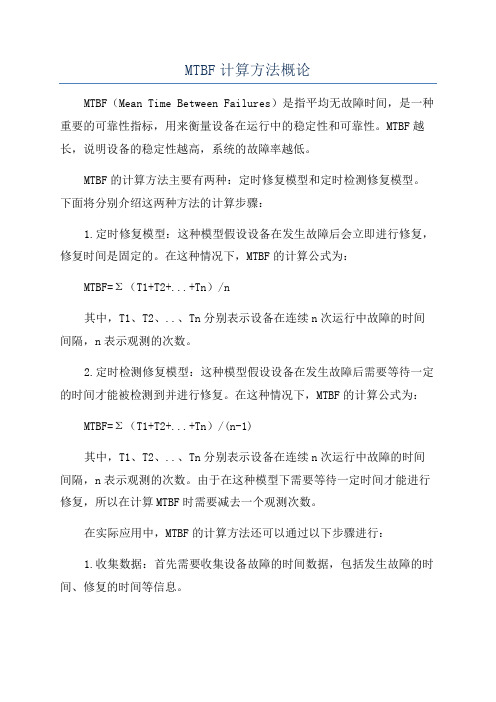
MTBF计算方法概论MTBF(Mean Time Between Failures)是指平均无故障时间,是一种重要的可靠性指标,用来衡量设备在运行中的稳定性和可靠性。
MTBF越长,说明设备的稳定性越高,系统的故障率越低。
MTBF的计算方法主要有两种:定时修复模型和定时检测修复模型。
下面将分别介绍这两种方法的计算步骤:1.定时修复模型:这种模型假设设备在发生故障后会立即进行修复,修复时间是固定的。
在这种情况下,MTBF的计算公式为:MTBF=Σ(T1+T2+...+Tn)/n其中,T1、T2、..、Tn分别表示设备在连续n次运行中故障的时间间隔,n表示观测的次数。
2.定时检测修复模型:这种模型假设设备在发生故障后需要等待一定的时间才能被检测到并进行修复。
在这种情况下,MTBF的计算公式为:MTBF=Σ(T1+T2+...+Tn)/(n-1)其中,T1、T2、..、Tn分别表示设备在连续n次运行中故障的时间间隔,n表示观测的次数。
由于在这种模型下需要等待一定时间才能进行修复,所以在计算MTBF时需要减去一个观测次数。
在实际应用中,MTBF的计算方法还可以通过以下步骤进行:1.收集数据:首先需要收集设备故障的时间数据,包括发生故障的时间、修复的时间等信息。
2.计算每次故障的时间间隔:根据收集到的数据,计算每次故障发生的时间间隔。
3.计算MTBF:根据收集到的每次故障的时间间隔,使用上述的计算公式计算MTBF。
4.分析结果:根据计算得到的MTBF结果,对设备的稳定性和可靠性进行评估,并根据需要进行优化和改进。
总的来说,MTBF是衡量设备稳定性和可靠性的重要指标,通过合理的数据收集和计算方法,可以准确地评估设备的运行状态,并为设备的维护和管理提供参考依据。
在实际应用中,需要根据具体情况选择合适的计算方法,并通过分析结果进行有效的决策和措施。
- 1、下载文档前请自行甄别文档内容的完整性,平台不提供额外的编辑、内容补充、找答案等附加服务。
- 2、"仅部分预览"的文档,不可在线预览部分如存在完整性等问题,可反馈申请退款(可完整预览的文档不适用该条件!)。
- 3、如文档侵犯您的权益,请联系客服反馈,我们会尽快为您处理(人工客服工作时间:9:00-18:30)。
MTBF,即平均无故障时间,英文全称是“Mean Time Between Failure”。
是衡量一个产品(尤其是电器产品)的可靠性指标。
单位为“小时”。
它反映了产品的时间质量,是体现产品在规定时间内保持功能的一种能力。
具体来说,是指相邻两次故障之间的平均工作时间,也称为平均故障间隔。
它仅适用于可维修产品。
同时也规定产品在总的使用阶段累计工作时间与故障次数的比值为MTBF。
磁带机产品的MTBF值不应低于200000小时。
通常,我们在产品的手册或包装上能够看到这个MTBF值,如8000小时,2万小时,那么,MTBF的数值是怎样算出来的呢,假设一台电脑的MTBF为3万小时,是不是把这台电脑连续运行3万小时检测出来的呢?答案是否定的,如果是那样的话,我们有那么多产品要用几十年都检测不完的。
其实,关于MTBF值的计算方法,目前最通用的权威性标准是MIL-HDBK-217、GJB/Z299B和Bellcore,分别用于军工产品和民用产品。
其中,MIL-HDBK-217是由美国国防部可靠性分析中心及Rome实验室提出并成为行业标准,专门用于军工产品MTBF值计算,GJB/Z 299B是我国军用标准;而Bellcore是由AT&T Bell 实验室提出并成为商用电子产品MTBF值计算的行业标准。
MTBF计算中主要考虑的是产品中每个器件的失效率。
但由于器件在不同的环境、不同的使用条件下其失效率会有很大的区别,例如,同一产品在不同的环境下,如在实验室和海洋平台上,其可靠性值肯定是不同的;又如一个额定电压为16V的电容在实际电压为25V 和5V下的失效率肯定是不同的。
所以,在计算可靠性指标时,必须考虑上述多种因素。
所有上述这些因素,几乎无法通过人工进行计算,但借助于软件如MTBFcal软件和其庞大的参数库,我们就能够轻松的得出MTBF值。
其实,MTBF值如何算出并不是我们所关心的问题,我们应该把重点放在一个产品的MTBF 的值到底有多少上,对于用户来讲,应该选用MTBF值高的产品。