(10)光刻技术
光刻技术

光刻机总体结构
照明系统 掩模台系统 环境控制系统 掩模传输系统 投影物镜系 统
自动对准系 统
调平调焦测 量系统 框架减振系 统
硅片传输系 统
工件台系统
整机控制系统
整机软件系统
图为CPU内部SEM图像
图为硅芯片集成电路放大图像
图为在硅片上进行的光刻图样
图为Intel 45nm高K金属栅晶体 管结构
SU-8交联示意图
正胶与负胶性能对比
正胶 缺点 (DQN) 特征 优点 优点 分辨率高、对比度好 粘附性差、抗刻蚀能力差、高成本 近紫外,365、405、435nm的波长曝 光可采用 良好的粘附能力、抗蚀能力、感光能 力以及较好的热稳定性。可得到垂直 侧壁外形和高深宽比的厚膜图形 显影时发生溶胀现象,分辨率差 对电子束、近紫外线及350-400nm紫 外线敏感
投影式印刷:在投影式印刷中,
用镜头和反光镜使得像聚焦到硅平 面上,其硅片和掩模版分得很开。
三种方法的比较
接触曝光:光的衍射效应较小,因而分辨率高;但易损
坏掩模图形,同时由于尘埃和基片表面不平等,常常存 在不同程度的曝光缝隙而影响成品率。
接近式曝光:延长了掩模版的使用寿命,但光的衍射效
应更为严重,因而分辨率只能达到2—4um 左右。
坚膜也是一个热处
理步骤。 除去显影时胶膜 吸收的显影液和水分, 改善粘附性,增强胶 膜抗腐蚀能力。 时间和温度要适 当。 时间短,抗蚀性 差,容易掉胶;时间 过长,容易开裂。
刻蚀就是将涂胶前所
沉积的薄膜中没有被 光刻胶覆盖和保护的 那部分去除掉,达到 将光刻胶上的图形转 移到其下层材料上的 目的。
等离子体去胶,氧气在强电场作用下电离产生的活性氧, 使光刻胶氧化而成为可挥发的CO2、H2O 及其他气体而被 带走。
光刻技术的现状和发展
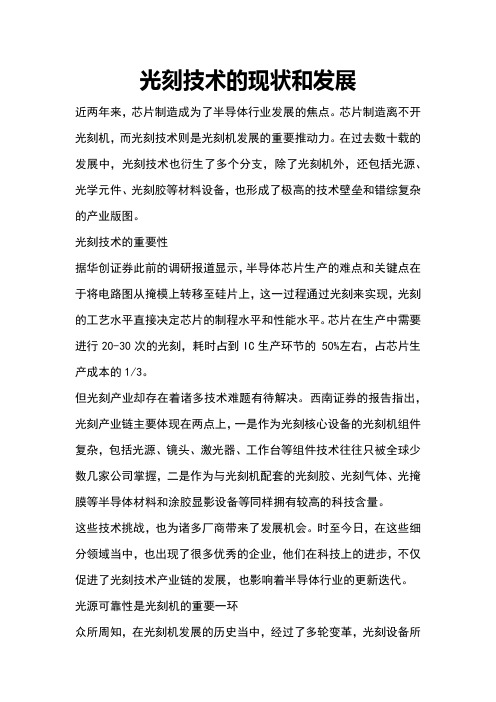
光刻技术的现状和发展近两年来,芯片制造成为了半导体行业发展的焦点。
芯片制造离不开光刻机,而光刻技术则是光刻机发展的重要推动力。
在过去数十载的发展中,光刻技术也衍生了多个分支,除了光刻机外,还包括光源、光学元件、光刻胶等材料设备,也形成了极高的技术壁垒和错综复杂的产业版图。
光刻技术的重要性据华创证券此前的调研报道显示,半导体芯片生产的难点和关键点在于将电路图从掩模上转移至硅片上,这一过程通过光刻来实现,光刻的工艺水平直接决定芯片的制程水平和性能水平。
芯片在生产中需要进行20-30次的光刻,耗时占到IC生产环节的 50%左右,占芯片生产成本的1/3。
但光刻产业却存在着诸多技术难题有待解决。
西南证券的报告指出,光刻产业链主要体现在两点上,一是作为光刻核心设备的光刻机组件复杂,包括光源、镜头、激光器、工作台等组件技术往往只被全球少数几家公司掌握,二是作为与光刻机配套的光刻胶、光刻气体、光掩膜等半导体材料和涂胶显影设备等同样拥有较高的科技含量。
这些技术挑战,也为诸多厂商带来了发展机会。
时至今日,在这些细分领域当中,也出现了很多优秀的企业,他们在科技上的进步,不仅促进了光刻技术产业链的发展,也影响着半导体行业的更新迭代。
光源可靠性是光刻机的重要一环众所周知,在光刻机发展的历史当中,经过了多轮变革,光刻设备所用的光源,也从最初的g-line,i-line发展到了KrF、ArF,如今光源又在向EUV方向发展。
Gigaphoton是在全球范围内能够为光刻机提供激光光源的两家厂商之一(另外一家是Cymer,该公司于2012年被ASML收购)。
Gigaphoton的Toshihiro Oga认为,光源是一项专业性较强的领域,并需要大规模的投资去支撑该技术的发展,而光源又是一个相对小众的领域,尤其是用于光刻机的光源有别于用于其他领域的光源——其他领域所用光源多为低频低功率,而光刻机所用光源则为高频高功率,这也让许多企业对该领域望而却步。
光刻机的技术原理

光刻机的技术原理光刻技术是一种常用于微电子制造的重要工艺。
它主要用于将电子器件的图形或芯片上的图案转移到光刻胶或光刻膜上,然后通过化学蚀刻等工艺步骤将所需的微小结构转移到芯片表面,从而完成电子器件的制造。
下面,我将详细介绍光刻技术的工作原理和主要步骤。
光刻技术的主要原理是利用光的透射和反射来形成期望的图案。
它主要包括以下几个基本步骤:光源辐射、掩膜制作、曝光、开发和蚀刻。
首先,光刻机中的光源会产生紫外光或可见光的光辐射。
这些光线经过光学投影系统的透镜等光学元件的聚焦,形成一束高能量的并具有特定波长的光线。
在整个光刻过程中,这束光线是非常重要的。
接下来,准备好的掩膜会被放置在光刻机上。
掩膜是一种透光性好的玻璃或石英板,上面的透光区域和不透光区域按照所需的图案进行了刻蚀处理。
光刻机的光学系统使得掩膜上的图案被放大并投射到光刻胶或光刻膜上。
在曝光阶段,将掩膜和芯片的表面(涂有光刻胶或光刻膜)与光学系统的接触式接头对准,并启动光刻机进行曝光。
透过掩膜上的透明区域,通过特定波长的光线照射芯片表面,将图案的影像投射到光刻胶或光刻膜上。
在曝光的过程中,光刻胶或光刻膜上的化学和物理特性发生了变化,从而使图案在曝光区域产生显影作用。
然后,光刻胶或光刻膜需要进行显影。
显影是利用显影液将未曝光区域的光刻胶或光刻膜溶解掉的过程。
因为曝光区域的光刻胶或光刻膜已被特定波长的光线照射,使其化学结构发生了变化,从而形成了想要的图案。
而未曝光区域的光刻胶或光刻膜保持原来的状态,因此通过浸泡在显影液中,未曝光区域的物质会被显影液迅速溶解。
最后一步是蚀刻,也称为刻蚀。
刻蚀是将光刻胶或光刻膜已经形成的图案转移到芯片表面的过程。
光刻胶或光刻膜的蚀刻一般通过化学蚀刻或物理蚀刻来完成。
化学蚀刻使用蚀刻溶液对芯片进行蚀刻,而物理蚀刻则通过向芯片表面投射离子束或激光束来完成。
综上所述,光刻机的技术原理主要是通过光的透射和反射将电子器件的图案转移到光刻胶或光刻膜上,然后通过显影和蚀刻等工艺步骤将所需的微小结构转移到芯片表面上。
(10)光刻技术剖析
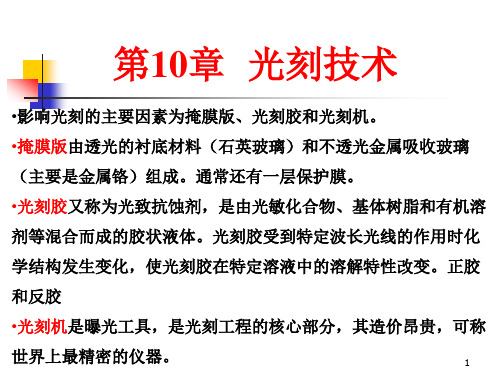
•影响光刻的主要因素为掩膜版、光刻胶和光刻机。
•掩膜版由透光的衬底材料(石英玻璃)和不透光金属吸收玻璃
(主要是金属铬)组成。通常还有一层保护膜。
•光刻胶又称为光致抗蚀剂,是由光敏化合物、基体树脂和有机溶
剂等混合而成的胶状液体。光刻胶受到特定波长光线的作用时化
学结构发生变化,使光刻胶在特定溶液中的溶解特性改变。正胶
X射线光刻胶:
43
10.3 光学分辨率增强技术
光学分辨率增强技术包括: 移相掩模技术(phase shift mask )、 离轴照明技术(off-axis illumination)、 光学邻近效应校正技术(optical proximity correction)、
光瞳滤波技术(pupil filtering technology)等。
26
27
28
10.2 光刻胶(PR-光阻)
光刻时接受图像的介质称为光刻胶。 以光刻胶构成的图形作为掩膜对薄膜进行腐蚀,图形就
转移到晶片表面的薄膜上了,所以也将光刻胶称为光致 抗蚀剂。 光刻胶在特定波长的光线下曝光,其结构发生变化。 如果胶的曝光区在显影中除去,称为正胶;反之为负胶。
29
45
通过移相层后光波与正常光波产生的相位差可用 下式表达:
Q 2d (n 1)
式中 d——移相器厚度; n——移相器介质的折射率; λ——光波波长。
46
附加材料造成 光学路迳差异, 达到反相
47
10.3.1 移相掩模技术
粗磨、精磨、厚度分类、粗抛、精抛、超声清洗、检验、平 坦度分类等工序后,制成待用的衬底玻璃。
2、铬膜的蒸发 铬版通常采用纯度99%以上的铬粉作为蒸发
源,把其装在加热用的钼舟内进行蒸发。蒸发前 应把真空度抽至10-3mmHg以上,被蒸发的玻璃 需加热。其它如预热等步骤与蒸铝工艺相似。
简述光刻技术
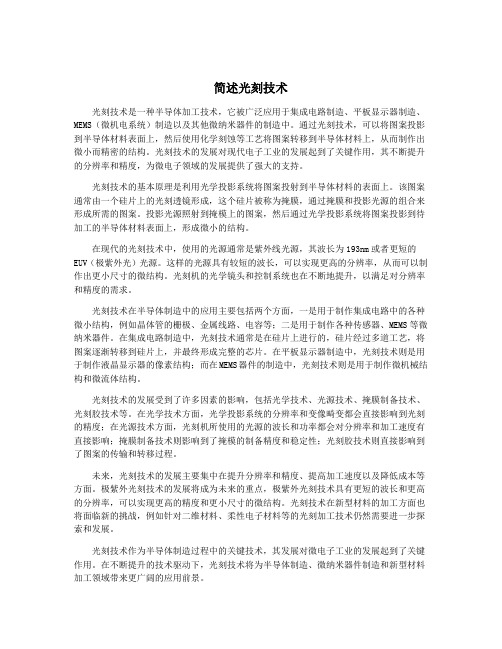
简述光刻技术光刻技术是一种半导体加工技术,它被广泛应用于集成电路制造、平板显示器制造、MEMS(微机电系统)制造以及其他微纳米器件的制造中。
通过光刻技术,可以将图案投影到半导体材料表面上,然后使用化学刻蚀等工艺将图案转移到半导体材料上,从而制作出微小而精密的结构。
光刻技术的发展对现代电子工业的发展起到了关键作用,其不断提升的分辨率和精度,为微电子领域的发展提供了强大的支持。
光刻技术的基本原理是利用光学投影系统将图案投射到半导体材料的表面上。
该图案通常由一个硅片上的光刻透镜形成,这个硅片被称为掩膜,通过掩膜和投影光源的组合来形成所需的图案。
投影光源照射到掩模上的图案,然后通过光学投影系统将图案投影到待加工的半导体材料表面上,形成微小的结构。
在现代的光刻技术中,使用的光源通常是紫外线光源,其波长为193nm或者更短的EUV(极紫外光)光源。
这样的光源具有较短的波长,可以实现更高的分辨率,从而可以制作出更小尺寸的微结构。
光刻机的光学镜头和控制系统也在不断地提升,以满足对分辨率和精度的需求。
光刻技术在半导体制造中的应用主要包括两个方面,一是用于制作集成电路中的各种微小结构,例如晶体管的栅极、金属线路、电容等;二是用于制作各种传感器、MEMS等微纳米器件。
在集成电路制造中,光刻技术通常是在硅片上进行的,硅片经过多道工艺,将图案逐渐转移到硅片上,并最终形成完整的芯片。
在平板显示器制造中,光刻技术则是用于制作液晶显示器的像素结构;而在MEMS器件的制造中,光刻技术则是用于制作微机械结构和微流体结构。
光刻技术的发展受到了许多因素的影响,包括光学技术、光源技术、掩膜制备技术、光刻胶技术等。
在光学技术方面,光学投影系统的分辨率和变像畸变都会直接影响到光刻的精度;在光源技术方面,光刻机所使用的光源的波长和功率都会对分辨率和加工速度有直接影响;掩膜制备技术则影响到了掩模的制备精度和稳定性;光刻胶技术则直接影响到了图案的传输和转移过程。
光刻技术的发展现状及趋势

光刻技术的发展现状及趋势光刻技术作为微电子制造中至关重要的一个环节,其发展也一直在不断推进,从而推动了整个微电子产业的快速发展。
本文将从几个方面阐述光刻技术的发展现状及趋势。
第一、发展历程。
20世纪60年代初,光刻技术逐渐进入人们的视野。
随着半导体工艺的不断提升,人们对于光刻机的要求也越来越高。
80年代中期,光刻技术实现了从g-line到i-line的跨越。
90年代中期,光刻技术又实现了从i-line到KrF的跨越。
现在,已经有了更加高端的ArF光刻技术,而且正在向EUV(极紫外线)技术转型。
可以说,光刻技术发展越来越成熟,也越来越复杂。
第二、新技术的应用。
当前,人们在开发新型半导体工艺中特别注重极紫外光刻技术和自组织光刻技术。
极紫外光刻技术的出现,不仅意味着芯片结构的再次升级,而且也使半导体工艺面板的生产成本有所降低。
自组织光刻技术是指采用场致异质原子效应所实现的一种制程技术,已经被应用于国内外的生产中,成为了一种重要的MEMS制造技术。
第三、制程逐渐精细。
随着半导体工艺的不断提升,人们对于微电子产品的精细度及稳定性要求也越来越高。
光刻技术在制程的过程中被应用最为广泛,因此在制程方面也逐步加强了对光刻技术的要求。
如此,会对光刻技术的工艺设置、技术规范等进行深入改进和提高,有利于提高生产效率及缩小生产成本,使得微电子产品的质量和稳定性得以更好地保证。
总之,光刻技术的发展现状及趋势,不仅关系到微电子产业的发展方向,在国际市场的竞争中也具有非常重要的含义。
随着物联网、人工智能等新型技术的出现,将会进一步带动光刻技术的发展。
光刻机技术进展及未来发展方向
随着信息技术的迅猛发展和半导体产业的不断壮大,光刻机技术作为半导体制造工艺中极为重要的一环,也在不断进行创新与突破,实现了长足的发展。本文将对光刻机技术的进展进行探究,并展望其未来的发展方向。
一、光刻机技术的进展
1.微影技术的应用
光刻机技术作为微影技术的核心,能够在光敏胶片或光刻胶层上进行光照、显影、蚀刻等工序,使图案投射到硅片上,实现了微小化的电子元件和线路的制造。随着相干光刻技术、准直光刻技术等的应用,半导体芯片的制作精度和复杂度得以提升。
二、光刻机技术的未来发展方向
1.极紫外光刻技术(EUV技术)
极紫外光刻技术采用13.5nm波长的极紫外光进行曝光,制程尺寸进一步缩小,是当前光刻技术的研究热点。然而,由于光源、光刻胶和掩膜等相关技术仍处于发展阶段,EUV技术在商业化应用方面仍面临一定的挑战。未来,随着技术突破和商业化成本的降低,EUV技术有望成为下一代光刻技术的主流。
2.光刻机设备的集成与智能化
随着芯片制程的不断革新,光刻机设备将继续向着集成化和智能化方向发展。光刻机设备将逐渐实现多工艺模块集成,提高生产效率和设备利用率。同时,光刻机设备还将加强机器学习和人工智能技术的应用,通过数据分析和优化算法,提高设备的自动化程度和制程控制精度。
3.新材料与新工艺的应用
随着新材料的不断涌现,比如二维材料、有机半导体材料等,光刻机技术也需要与之相适应,探索新的制备工艺和工艺参数。未来,光刻机技术将与新材料和新工艺相结合,为电子器件带来更多的创新和突破。
2.紫外光刻技术的突破
紫外光刻技术采用了更短波长的光线,使得线宽更加精细,解决了传统光刻机技术面临的线宽限制难题。采用193nm波长的氟化氖激光器,使得制程尺寸进一步缩小,为微电子产业的发展提供了重要的支撑。
光刻技术的发展趋势
光刻技术的发展趋势
光刻技术是半导体工艺中至关重要的一项关键技术,对半导体器件的制造和性能有重要影响。
随着半导体工艺的不断发展,光刻技术也在不断演进和进步。
以下是光刻技术发展的一些趋势:
1. 紫外光刻机的发展:紫外光刻机是目前主流的光刻技术,随着半导体器件的尺寸不断缩小,紫外光刻机需要不断提高分辨率和稳定性来满足制程要求。
2. 多重曝光技术:多重曝光技术是解决光刻机分辨率限制的一种重要方式。
通过多次曝光和光栅设计,可以实现更高分辨率的芯片制造。
3. 电子束光刻技术:电子束光刻技术是一种高分辨率的曝光技术,能够实现更小尺寸的芯片制造,但成本较高。
随着半导体工艺进一步发展,电子束光刻技术有望在某些特殊领域得到更广泛应用。
4. 次波长光刻技术:次波长光刻技术是克服紫外光刻分辨率限制的一种关键技术。
通过使用更短波长的光源或者其他技术手段,可以实现更高分辨率的制程。
5. 3D立体印刷技术:3D立体印刷技术是一种新兴的光刻技术,可以实现对器件表面的高精度加工。
随着3D芯片和器件的需求增长,3D立体印刷技术有望成为未来的发展方向。
总体来说,光刻技术的发展趋势是朝着更高分辨率、更快速度和更低成本的方向发展。
随着新一代半导体工艺的引入和应用需求的变化,光刻技术会继续不断演进和创新。
光刻技术简介
PPT学习交流
1
讲解内 容
光刻技术简 光刻的介原理概
光刻胶述-光致抗蚀 光刻的一剂般流
程
光刻技术应用举例
PPT学习交流
2
光刻的原理简 介
光刻: 利用照相复制与化学腐蚀相结 合的技术,在工件表面制取精 密、微细和复杂薄层图形的化 学加工方法。多用于半导体器 件与集成电路的制作。
传统方法制作电极的缺陷:
1:PVDF压电薄膜两侧的电极层的尺寸大小和 形状与薄膜不匹配。 2:未经过处理的压电薄膜在电极两侧加上电 压时,会产生放电现象。
PPT学习交流
18
光刻技术在PVDF压电薄膜电极制作中的应 用
第一步: 设计要制作的电极的形状与尺寸
PPT学习交流
19
光刻技术在PVDF压电薄膜电极制作中的应 用
原理:利用光致抗蚀剂(或称光刻胶)感 光后因光化学反应而形成耐蚀性 的特点,将掩模板上的图形刻制 到被加工表面上。
PPT学习交流
3
光刻 胶
光刻胶:也称为光致 抗蚀剂,它是由感光 树脂、增感剂和溶剂 三部分组成的对光敏 感的混合液体。
光刻胶主要用来将 光刻掩模板上的图形 转移到元件上。
PPT学习交流
第二步: 对PVDF压电薄膜进行清洗处理。采用 有机溶剂丙酮。
第三步: 涂胶。选用正性光刻胶,采用手工操作 涂到需要保护的电极层上。
第三步: 前烘与曝光。
第四步: 腐蚀。采用湿法刻蚀方法。选取碘和碘化 钾的水溶液(质量比为1:4:40)作为金的 腐蚀溶剂,体积分数为40%的氢氟酸作为 铬层的腐蚀溶剂。
22
谢谢大家
PPT学习交流
23
5 显影 6 坚模 7 刻蚀 8 去胶
光刻技术原理全解
光刻技术原理全解光刻技术是一种微电子制造中非常重要的技术方法,常用于半导体器件制造过程中。
它通过使用光刻胶光刻胶(photoresist)和光源光源(light source)制作芯片上各种测量、定义和纳米加工细节的光刻工艺步骤,实现高精度的微纳米尺寸特征的制作。
下面将为您介绍光刻技术的原理。
光刻技术的原理基于光的光的干涉和衍射原理。
首先,需要一个光源,通常使用的是紫外线(UV)光源,因为紫外线具有高能量和短波长,对于制作微小特征具有优势。
光源产生的UV光通过光学系统会聚到准直镜上,进一步聚焦到光刻胶表面。
光刻胶是光刻技术中非常关键的材料。
它是一种光敏树脂,通过特殊的化学处理使其对紫外线光有响应。
在曝光过程中,光刻胶对紫外线光会产生化学反应,发生聚合或降解的变化,被曝光的区域与未曝光区域的物性发生差异,从而形成图案。
在光刻胶的表面上,需要使用掩膜(mask)制作出期望的图案。
掩膜是一个类似于胶片的透明基片,其上涂有几层不同材料构成的图案。
掩膜上的不透明部分会阻挡光的透过,形成尺寸精确的光刻图案。
掩膜的图案是根据芯片设计师所需的结构进行设计和制作的。
当光刻胶在光源的照射下进行曝光时,通过光学系统重新聚焦到光刻胶表面,被曝光的区域会发生化学反应,使光刻胶发生改变。
在光刻胶材料中有两类最常用的光刻胶,一种是正相光刻胶(positive photoresist),另一种是负相光刻胶(negative photoresist)。
正相光刻胶在紫外线照射下,被照射的区域聚合形成硬化的物质,而负相光刻胶则是被照射区域发生降解,形成溶解物。
曝光之后,还需要进行显影(develop)的工艺步骤。
显影是使光刻胶发生物理或化学变化,从而去除未曝光或曝光后不需要的材料的过程。
对于正相光刻胶,未曝光区域显影后会被去除,而曝光区域则会保留下来。
对于负相光刻胶,则是未曝光区域保留,而曝光区域被去除。
经过显影之后,我们得到了期望的图案,其中未被照射的区域通过显影工艺去除的,形成了芯片上的光刻图案。
- 1、下载文档前请自行甄别文档内容的完整性,平台不提供额外的编辑、内容补充、找答案等附加服务。
- 2、"仅部分预览"的文档,不可在线预览部分如存在完整性等问题,可反馈申请退款(可完整预览的文档不适用该条件!)。
- 3、如文档侵犯您的权益,请联系客服反馈,我们会尽快为您处理(人工客服工作时间:9:00-18:30)。
光的胶膜被显影液除去,图形发生反转。
负胶多由长链高分子有机物组成。如由顺聚异戊二烯
和对辐照敏感的交联剂,以及溶剂组成得负胶,响应
波长330-430nm,胶膜厚度0.3-1μm,显影液二甲苯 等。
38
2、负胶
负胶
39
顺聚异戊二烯负胶显影原理
hv
顺聚异戊二烯+交联剂作用下交联,成为体型 高分子,并固化,不再溶于有机溶剂构成的显影液, 而未曝光的长链高分子溶于显影液,显影时被去掉。
20
(2)玻璃基板的制备 挑选好的制版玻璃,通过切割、铣边、例棱、倒角、
粗磨、精磨、厚度分类、粗抛、精抛、超声清洗、检验、平
坦度分类等工序后,制成待用的衬底玻璃。
2、铬膜的蒸发
铬版通常采用纯度99%以上的铬粉作为蒸发
源,把其装在加热用的钼舟内进行蒸发。蒸发前
应把真空度抽至10-3mmHg以上,被蒸发的玻璃
需加热。其它如预热等步骤与蒸铝工艺相似。
21
3、蒸发后对铬膜的质量检查
•从真空室中取出蒸好的铬版,用丙酮棉球擦洗表面,然后放在 白炽灯前观察。检查铬层有否针孔,厚度是否均匀,厚薄是否适 当。 •如果铬膜太厚,腐蚀时容易钻蚀,影响光刻质量。太薄则反差 不够高。铬膜的厚度可用透过铬版观察白炽灯丝亮度的方法,根
31
2、分类
按曝光区在显影中被去除或保留来划分:
正(性)胶 负(性)胶
按其用途划分:
光学光刻胶 电子抗蚀剂 X-射线抗蚀剂
32
10.2.1
光刻胶的特征量
响应波长
灵敏度,又称光敏度,指最小曝光剂量E0 抗蚀性,指耐酸、碱能力 黏滞性,指流动特性的定量指标 黏附性 ,指与硅、二氧化硅表面结合力的大小 光刻胶的膨胀 微粒数量和金属含量 储存寿命
化学稳定性及高光穿透性等特质;
掩膜版之所以可以作为图形转移的模板,关键就在于
有无铬膜的存在,有铬膜的地方,光线不能穿越,反
之,则光可透过石英玻璃而照射在涂有光刻胶的晶片
上,晶片再经过显影,产生不同的图形。
15
掩模版上的缺陷一般来自两个方面:
一是掩模版图形本身的缺陷,大致包括针孔、黑点、黑区 突出、白区突出、边缘不均及刮伤等,此部分皆为制作过程中
第10章 光刻技术
•影响光刻的主要因素为掩膜版、光刻胶和光刻机。
•掩膜版由透光的衬底材料(石英玻璃)和不透光金属吸收玻璃
(主要是金属铬)组成。通常还有一层保护膜。 •光刻胶又称为光致抗蚀剂,是由光敏化合物、基体树脂和有机溶 剂等混合而成的胶状液体。光刻胶受到特定波长光线的作用时化 学结构发生变化,使光刻胶在特定溶液中的溶解特性改变。正胶
③整套掩模中的各块掩模能很好地套准。
④图形与衬底要有足够的反差,透明区无灰雾。
⑤掩模应尽可能做到无缺陷。
⑥版面平整、光洁、结实耐用。
17
10.1.3
铬版的制备技术
•铬版工艺的特点如下:
①由于金属铬膜与相应的玻璃衬底有很强的粘附
性能;质地坚硬。所以耐磨、寿命长。
②图形失真小,分辨率极高。
③铬膜的光学密度大,搭配透明衬底,反差极好。
据经验判断;精确的厚度必须用测厚仪测量。铬膜质量不好的常
见毛病是针孔,产生原因主要是玻璃基片的清洁度不够好,有水 汽吸附,铬粉不纯,表面存在尘埃等。
22
10.1.3
铬版的制备技术
4、铬膜质量
(1)膜厚 (2)均匀性 (3)针孔 (4)牢固度
23
10.1.4 彩色版制备技术
•彩色版是一种采用新型的透明或半透明掩模,因有颜色,即俗称 彩色版,它可克服超微粒干版缺陷多,耐磨性差及铬版针孔多、易 反光、不易对准等缺点。
以一定的间距和布局做在基版上,供光刻工艺中重复
使用。
制造商将设计工程师交付的标准制版数据传送给一个
称作图形发生器的设备,图形发生器会根据该数据完
成图形的产生和重复,并将版图数据分层转移到各层
光刻掩模版(为涂有感光材料的优质玻璃板)上,这
就是制版。
3
掩模版使用低膨胀系数的熔融石英上淀积金属铬 (1000埃)制成。
•彩色版的最主要特点是对曝光光源波长不透明,而对于观察光源
波长透明。 •彩色版种类很多,有氧化铁版、硅版、氧化铬版、氧化亚铜版等, 目前应用较广的是氧化铁彩色版。 •氧化铁具备作为选择透明掩模材料的所有要求的最佳的化学和物
理特性。据报道,在紫外区(300~400nm)的透射率小于1%,在
可见光区(400~800nm)透射率大于30%。
42
其他光刻胶: 电子束光刻胶:也是涂在衬底表面用来实现图形传递 的物质,通过电子束曝光使得光刻胶层形成所需要的 图形。通常用于非光学光刻中的光刻胶由长链碳聚合 物组成。 在相邻链上碳聚合物接受电子束照射的原子会产生移 位,导致碳原子直接键合,这一过程称为交联。高度 交联的分子在显影液中溶解缓慢。
通过电子束直写,将设计图转化为掩模版图形。 特征尺寸减小,要求保护掩模版避免掉铬、擦伤、 颗粒污染和静电放电损伤。
4
光刻版
5
6
(A)电路图;(B)版图
(A)
(B)
7
10.1.1 制版工艺简介
掩模版的制作流程
8
10.1.1 制版工艺简介
硅平面晶体管或基层电路掩膜版的直走,一般来讲要
经过原图绘制(版图绘制和刻分层图)、初缩、精缩
复印:在集成电路生产的光刻过程中,掩膜版会受磨
损产生伤痕。使用一定次数后需要换用新掩膜版。因
此得到目版后要采用复印技术复制多块工作掩膜版工
光刻用。
13
10.1.2 掩模板的基本构造及质量要求
掩模版的基本构造
14
10.1.2 掩模板的基本构造及质量要求
玻璃基片,一般具有低热膨胀系数、低含钠含量、高
29
使用光刻胶的目的:
将掩膜版图案转移到硅片表面顶层的光刻胶中; 在后续工艺中,保护下面的材料;
随着尺寸的越来越小,需要注意和改进的几个点:
更好的图形清晰度、黏附性、均匀性、增加工艺容度。
30
10.2
光刻胶
1、组成
聚合物材料:聚合物在广德照射下不发生化学反应,其 主要作用是保证光刻胶薄膜的附着性和抗腐蚀性;使胶 具有一定的粘度,能均匀涂覆; 感光材料:感光材料一般为复合物(简称PAC或感光 剂)。感光剂在受光辐照之后会发生化学反应。正胶的 感光剂在未曝光区域起抑制作用,可以减慢光刻胶在显 影液中的溶解速度。在正性光刻胶暴露于光线时有化学 反应,是抑制剂变成感光剂,从而增强了胶的溶解速度。 溶剂 :它的作用是可以控制光刻胶机械性能,使其在 被涂到硅片表面之前保持液态。
45
通过移相层后光波与正常光波产生的相位差可用 下式表达:
Q 2d
(n 1)
式中 d——移相器厚度; n——移相器介质的折射率;
λ——光波波长。
46
附加材料造成 光学路迳差异, 达到反相
47
10.3.1 移相掩模技术
移相掩模的主要类型有:
交替式PSM
衰减型PSM
边缘增强型PSM
24
氧化铁版在使用上还有以下优点:
①在观察光源波长下是透明的,而在曝光光源波长 下是不透明的。 ②反射率较低的。 ③克服光晕效应。 ④结构致密且无定形,针孔少。 ⑤与玻璃粘附性好、比较耐磨。 ⑥复印腐蚀特性比较好。
25
10.1.5 光刻制版面临的挑战
1、传统光学光刻及制版技术面临的挑战 2、掩模制造设备面临的挑战 3、越来越重要的DFM(Design for Manufacturing)
④金属铬在空气中十分稳定。
• 铬膜版制备有两个部分的内容:蒸发蒸镀与光刻技术
18
10.1.3
铬版的制备技术
空白铬版制作工艺流程
19
1、玻璃基板的选择与制备
(1)基板玻璃的选择 为保证版的质量,玻璃衬底必须满足如下要求: ①热膨胀系数:要求越小越好,对于白玻璃,要求 ≤9.3×10-6K-1;对于硼硅玻璃,要求≤4.5×10-6K-1;对于石 英玻璃,要求≤0.5×10-6K-1。 ②透射率:在360nm以上的波长范围内,透射率在 90%以上。 ③化学稳定性:掩模版在使用和储存过程中,很难绝 对避免与酸、碱、水和其它气氛接触。它们对玻璃都有不同 程度的溶解力。 ④选择方法:表面光泽,无突起点、凹陷、划痕和气 泡,版面平整。厚度适中、均匀。对于接触式曝光,为能承 受接触复印压力,厚度应在3mm以上。
响应波长330-430nm 胶膜厚1-3μm,显影液是氢氧化 钠等碱性物质。
35
1、正胶
正胶
IC主导
36
DQN显影原理
曝光的重氮醌 退化,易溶于 显影液,未曝 光的重氮醌和 树脂构成的胶 膜难溶于碱性
显影液。
光刻胶曝光、水解和显影过程中 的化学反应方程
37
2、负胶
最早用的光刻胶。曝光后,窗口处的胶膜保留,未曝
和反胶
•光刻机是曝光工具,是光刻工程的核心部分,其造价昂贵,可称 世界上最精密的仪器。
1
10.1 光刻掩模版的制造 10.2 光刻胶 10.3 光学分辨率增强技术 10.4 紫外光曝光技术 10.5 其它曝光技术 10.6 光刻设备
2
10.1 光刻掩模版的制造
掩模版就是将设计好的特定几何图形通过一定的方法
兼分布重复、复印阴版和复印阳版等几部。
在实际制作中,掩膜版制作人员根据图形产生的数据,
再加上不同的应用需求及规格,会选用不同的制作流
程。
9
10.1.1 制版工艺简介