水泥发展历程
水泥发展历程
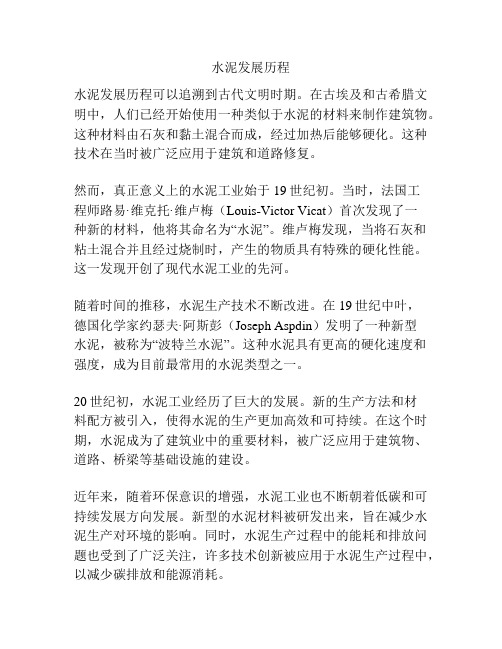
水泥发展历程水泥发展历程可以追溯到古代文明时期。
在古埃及和古希腊文明中,人们已经开始使用一种类似于水泥的材料来制作建筑物。
这种材料由石灰和黏土混合而成,经过加热后能够硬化。
这种技术在当时被广泛应用于建筑和道路修复。
然而,真正意义上的水泥工业始于19世纪初。
当时,法国工程师路易·维克托·维卢梅(Louis-Victor Vicat)首次发现了一种新的材料,他将其命名为“水泥”。
维卢梅发现,当将石灰和粘土混合并且经过烧制时,产生的物质具有特殊的硬化性能。
这一发现开创了现代水泥工业的先河。
随着时间的推移,水泥生产技术不断改进。
在19世纪中叶,德国化学家约瑟夫·阿斯彭(Joseph Aspdin)发明了一种新型水泥,被称为“波特兰水泥”。
这种水泥具有更高的硬化速度和强度,成为目前最常用的水泥类型之一。
20世纪初,水泥工业经历了巨大的发展。
新的生产方法和材料配方被引入,使得水泥的生产更加高效和可持续。
在这个时期,水泥成为了建筑业中的重要材料,被广泛应用于建筑物、道路、桥梁等基础设施的建设。
近年来,随着环保意识的增强,水泥工业也不断朝着低碳和可持续发展方向发展。
新型的水泥材料被研发出来,旨在减少水泥生产对环境的影响。
同时,水泥生产过程中的能耗和排放问题也受到了广泛关注,许多技术创新被应用于水泥生产过程中,以减少碳排放和能源消耗。
总的来说,水泥作为一种重要的建筑材料,经历了漫长的发展历程。
从古代文明的试验性应用到现代工业化生产,水泥在建筑和基础设施建设中发挥着关键作用。
随着科技的进步和环境意识的增强,水泥工业将继续迎来新的发展和创新。
水泥的历史与发展
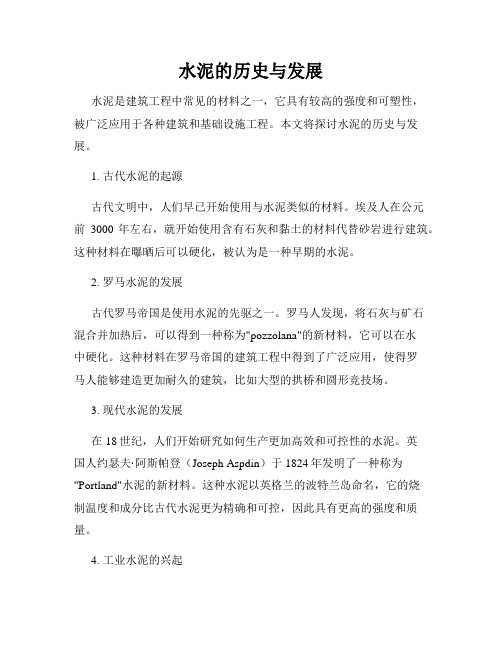
水泥的历史与发展水泥是建筑工程中常见的材料之一,它具有较高的强度和可塑性,被广泛应用于各种建筑和基础设施工程。
本文将探讨水泥的历史与发展。
1. 古代水泥的起源古代文明中,人们早已开始使用与水泥类似的材料。
埃及人在公元前3000年左右,就开始使用含有石灰和黏土的材料代替砂岩进行建筑。
这种材料在曝晒后可以硬化,被认为是一种早期的水泥。
2. 罗马水泥的发展古代罗马帝国是使用水泥的先驱之一。
罗马人发现,将石灰与矿石混合并加热后,可以得到一种称为"pozzolana"的新材料,它可以在水中硬化。
这种材料在罗马帝国的建筑工程中得到了广泛应用,使得罗马人能够建造更加耐久的建筑,比如大型的拱桥和圆形竞技场。
3. 现代水泥的发展在18世纪,人们开始研究如何生产更加高效和可控性的水泥。
英国人约瑟夫·阿斯帕登(Joseph Aspdin)于1824年发明了一种称为"Portland"水泥的新材料。
这种水泥以英格兰的波特兰岛命名,它的烧制温度和成分比古代水泥更为精确和可控,因此具有更高的强度和质量。
4. 工业水泥的兴起随着工业革命的到来,水泥的生产方式得到了革新。
法国人路易·韦兰(Louis Vicat)于1817年发展出了一种称为"hydraulic"水泥的新材料,它在水中可以硬化。
到了19世纪末,人们开始使用旋转窑的方式生产水泥,大大提高了生产效率。
5. 水泥的广泛应用水泥的发展使得建筑工程的规模和质量得到了质的飞跃。
现代的建筑中,水泥被广泛应用于混凝土、水泥砂浆、砌块等材料的生产。
水泥还可以用于修复和加固老旧建筑,提高其结构强度和稳定性。
6. 水泥产业的挑战与未来发展然而,水泥产业也面临着一些挑战。
首先,水泥的生产对环境造成了一定的影响,如二氧化碳排放等。
其次,水泥的生产与能源消耗较高,对资源的压力也日益增加。
因此,未来的水泥产业需要朝着更加环保和可持续发展的方向前进,探索新的材料制备和能源利用方式,从而减少对环境的负面影响。
世界水泥史话
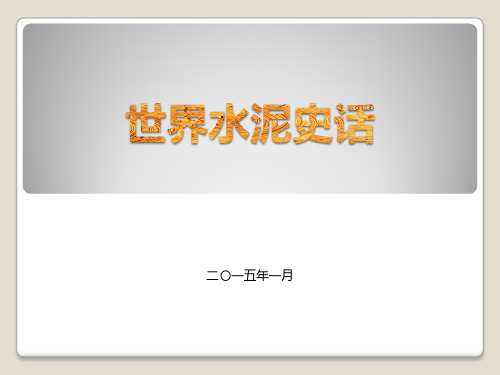
两份重量白垩和一份重量黏土混合后加水湿磨成泥浆,送入料槽进行 沉淀,置沉淀物于大气中干燥,然后放入石灰窑中煅烧,温度以料子 中碳酸气完全挥发为准,烧成产品呈浅黄色,冷却后经细磨制成水泥。
“英国水泥”由于煅烧温度较低,其质量明显不及“罗马水泥”,尽 管售价较低,但销售量不大。这种水泥虽然未能被大量推广,但其制 造方法已是近代水泥制造的雏型,这是水泥制造工艺中的又一次重大 飞跃。
20世纪
1975年,多伦多CN电视塔建成。 这座混凝土建筑是目前世界最高 的单体建筑物。
1980's,混凝土减水剂开始应用。
1985年,中国水泥总产量达1.46 亿吨,产量首次位居世界第一。
20世纪
1990's,法国FCB公司开发出HOROMILL(又叫卧式辊磨)。 这种HOROMlLL磨是继辊压机、立式磨之后发展起来的新一代 水泥粉磨技术。
19世纪
1824年英国利兹城的泥水匠阿 斯谱丁发明了世界最早的硅酸
盐水泥——波特兰水泥,获得
英国第5022号的“波特兰水 泥”专利证书,从而成为了被
后世永远牢记的水泥发明人。
19世纪
“波特兰水泥”的制造方法 把石灰石捣成细粉,配合一定量的黏土,掺水后以人工或机械 搅和均匀成泥浆。置泥浆于盘上,加热干燥。将干料打击成块,
有石灰会使水泥硬化后开裂。
根据这些发现,强生确定了水泥制造的两个基本条件:第一是烧窑的温度必 须高到足以使烧块含一定量玻璃体并呈黑绿色;第二是原料比例必须正确而 固定,烧成物内部不能含过量石灰,水泥硬化后不能开裂。
这些条件确保了“波特兰水泥”质量,解决了阿斯谱丁无法解决的质量不稳 定问题。从此,现代水泥生产的基本参数已被确定。
中国水泥百年回顾
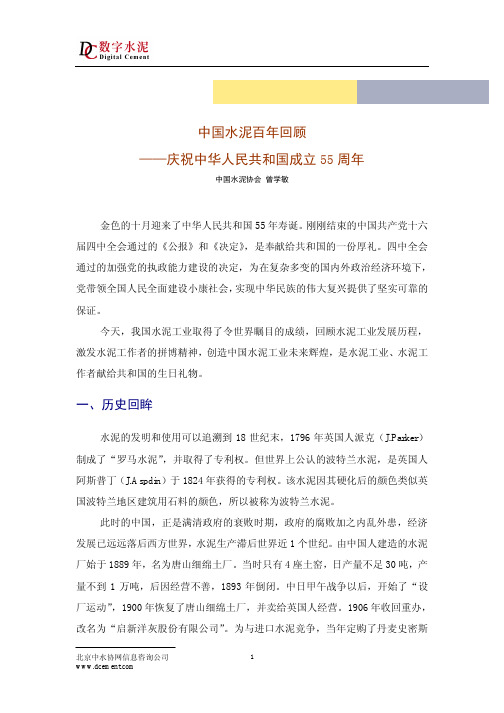
由于旧中国基本上无水泥工厂设计力量,机械制造工业基础也十分薄弱,为 解决水泥短缺的燃眉之急,不得不从国外大量引进成套设备。为了发展我国自己 的水泥设计及机械制造技术,在 1956 年和 1958 年调查研究的基础上,确定了以 “小屯型窑”和“华新型窑”作为我国干、湿法发展的主导窑型,在设计部门和 机械制造部门通力合作下,在湘乡水泥厂的建设上,采用了我国自行设计制造的 第一台华新窑,该厂筹建于 1958 年,由于适逢经济调整时期,推迟到 1967 年才 建成投产;使用小屯窑型建设的最早两个工厂是永安水泥厂和西卓子山水泥厂, 也筹建于 1958 年,同湘乡厂一样,分别推迟到 1971 年和 1972 年先后建成投产。 湘乡、永安、西卓子山几个水泥厂的建成,改变了我国依靠国外装备的被动局面, 水泥工业设计及装备制造走上自力更生的道路。
2. 计划经济时期
1953 年我国国民经济发展步入了第一个五年计划。水泥工业为了适应经济
北京中水协网信息咨询公司
3
建设发展的需要,国家出资从 1953 年开始大规模从东欧、东德、罗马尼亚、捷 克引进成套设备建设新厂。先后建设了大同、永登、昆明、江油、耀县、巢湖、 江山、贵州、庐山、柳州等十个厂。除柳州厂是 1964 年建成投产的以外,其余 九个厂都在 1957 年到 1960 年先后建成投产。水泥工业因此得到迅速发展。1960 年水泥生产能力达到 1100 万吨,水泥工业的布局也得到很大的改善,运输半径 由 1956 年的 854 公里缩短到 1980 年的 383 公里。
中联水泥的成长历程

中联水泥成长历程1999年6月,中国联合水泥有限责任公司成立,重组鲁南水泥厂(鲁南中联)、河南南阳航天水泥厂(南阳中联)、河南安阳海工水泥厂(安阳中联)。
2001年3月,重组江苏巨龙水泥集团有限公司(淮海中联)。
2003年6月,重组邢台鑫磊建材(集团)股份有限公司(邢台中联);同年,该企业日产2500吨新型干法水泥熟料生产线竣工投产。
2004年2月,设立青州中联水泥有限公司(青州中联)。
2004年4月,南阳中联日产3000吨新型干法水泥孰料生产线竣工投产。
重组山东安厦水泥集团枣庄鑫厦水泥有限公司(枣庄中联);同年,该企业日产2500吨新型干法水泥熟料生产线竣工投产。
2004年11月,鲁南中联日产5000吨新型干法水泥熟料生产线技改项目竣工投产。
2004年12月,淮海中联日产5000吨新型干法水泥熟料生产线竣工投产。
2006年3月,中国建材股份有限公司(HK3323)在香港联交所挂牌上市,中国联合水泥有限责任公司是其上市四大业务平台中重要的水泥制造业平台。
2006年7月,重组拥有日产10000吨新型干法水泥熟料生产线的徐州海螺水泥有限责任公司(徐州中联)。
2006年9月,中国联合水泥有限责任公司更名为“中国联合水泥集团有限公司”(简称中国联合水泥)。
2006年12月,中国联合水泥统一规范各所属企业名称。
2006年12月,青州中联水泥有限公司(青州中联)日产6000吨新型干法水泥熟料生产线竣工。
设立西峡中联水泥有限公司(西峡中联)。
2007年4月,为加强一体化管理,推出全新的“CUCC”品牌,并成为各所属企业水泥、熟料、商品混凝土等产品的统一品牌。
2007年7月,重组泰山水泥集团有限公司(泰山中联)。
2007年8月,南阳中联日产6000吨新型干法水泥熟料生产线竣工投产。
2007年9月,设立德州中联大坝水泥有限公司(德州中联)。
2007年10月,重组日照市港源水泥有限公司(日照中联),日照港集团有限公司港口粉磨站(日照港口中联)。
(完整版)混凝土发展简史

混凝土发展简史当代建筑用量最大、范围最广、最经济的建筑材料——混凝土的发展虽然只有100多年的历史,却走过了不平凡的历程。
1824年英国工程师阿斯普丁(Aspdih)获得第一份水泥专利,标志着水泥的发明。
这以后,水泥以及混凝土才开始广泛应用到建筑上。
19世纪中后期,清朝洋务派进步人士掀起学习西方先进工业技术的高潮,并在上海建成了我国第一家水泥厂,当时,称水泥为“洋灰”。
19世纪中叶,法国人约瑟夫·莫尼哀(1823-1906)制造出钢筋混凝土花盆,并在1867年获得了专利权。
在1867年巴黎世博会上,莫尼哀展出了钢筋混凝土制作的花盆、枕木,另一名法国人兰特姆展出了钢筋混凝土制造的小瓶、小船。
1928年,美国人Freyssinet发明了一种新型钢筋混凝土结构形式:预应力钢筋混凝土,并于二次世界大战后亦被广泛地应用于工程实践。
钢筋混凝土和预应力钢筋混凝土解决了混凝土抗压强度高、抗折、抗拉强度较低的问题,以及19世纪中叶钢材在建筑业中的应用,使高层建筑与大跨度桥梁的建造成为可能。
早期混凝土组分简单(水泥+砂+石子+水),强度等级低,施工劳动强度巨大,靠人工搅拌或小型自落实搅拌机搅拌,施工速度慢,质量控制粗糙。
高性能混凝土外加剂的广泛应用,是混凝土发展史上有一座里程碑。
外加剂不但可以减少水用量、实现大流动性,使混凝土施工变得省力、省时、经济。
1962年日本服部健一首先将萘磺酸甲醛缩合物(n≈10)用于混凝土分散剂,1964年日本花王石碱公司作为产品销售。
1971-1973年,德国首选将超塑化剂研制成功,流态混凝土出现,混凝土垂直泵送高度达到310m。
混凝土外加剂大大改善了混凝土的性能,使混凝土泵送成为可能。
泵送混凝土的出现,20世纪二战后,机械工业的飞速发展,混凝土生产运输、浇注施工带来了又一场革命。
20世纪末期,出现了集中搅拌的专业混凝土企业,使泵送混凝土施工中混凝土的搅拌供料有保证。
1978年,在江苏省常州市,中国建成第一家混凝土搅拌站,当时每盘混凝土只能搅拌1立方。
中国水泥工业现代化发展之路
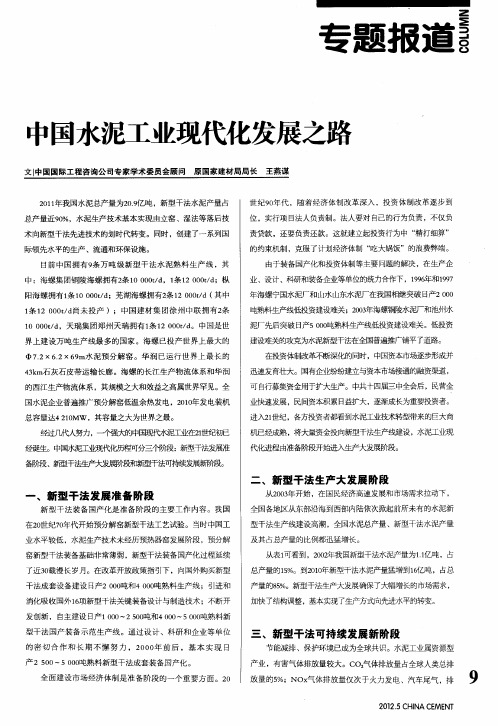
界上建设万吨 生产线最多的国家。海螺 已投产世界上最大 的
72×62 9 . . 6 m水 泥 预 分 解 窑 。 华 润 已 运 行 世 界 上 最 长 的 X
建设难关的攻克为水泥新型干法在全国普遍推广铺平了道路。 在投资体制改革不断深化的同时,中国资本市场逐步形成并 迅速发育壮大。国有企业纷纷建立与资本市场接通的融资渠道,
节能减排、保护环境 已成为全球共识。水泥工业属资源型 产业,有害气体排放量较大。C 气体排放量占全球人类总排 O: 放量的5 %;NOx 气体排放量仅次于火力发 电、汽车尾气 ,排
的密 切合 作 和长 期不 懈 努力 ,2 0 年 前后 ,基 本 实现 日 00 产2 5 0 0吨熟料新型干法成套装备国产化。 0 ~50 0 全面建设 市场经济体制是准备阶段 的一个重要方面。2 O
目前 中国拥有9 条万吨 级新 型干法水泥熟料 生产 线 ,其 中 :海螺集团铜 陵海螺拥有2 1 0td 条1 0 td 条 0O 0/ ,1 2O 0/ ;枞 阳海 螺拥有1 0O 0/ ;芜湖海螺拥有2 1 0 td( 中 条1 0 td 条 20 0/ 其 1 2 0 0/ 尚未 投产 );中国建材集 团徐州 中联拥有2 条1 0 td 条
由于 装备 国产 化和投 资 体制 等主要 问题 的解 决 ,在 生产 企 业 、设计 、科研和装 备企业等 单位的 统力合作下 ,19年和 19 96 97 年 海螺 宁国水 泥厂 和 山水 山东水 泥 厂在我 国相继突 破 日产200 0 吨 熟料生产 线低投资建 设难关 ; 03 : 20: 螺铜陵水泥厂和 池州水  ̄ 泥 厂先 后突破 日产 500 0吨熟 料生 产线低 投资建 设难关 。低投 资
水 泥 概 述

水泥的优点: 1、可塑性好,可调成各种形状和尺寸的
泥凝土构件; 2、适应性强,可用于海上、地下或干热、
严寒地区以及耐侵蚀、防辐射等特殊要求的工 程;
3、耐久性好,水泥混凝土既没有钢材的生 锈问题,也没有木材的腐朽等缺点,更没有塑 料制品的老化、污染等问题;
4、可获得很高的强度,通过改变熟料的矿 物组成,既可调节其性能,获得高的强度,还 能与纤维等材料匹配,制成水泥基复合材料;
水泥历史及发展
■ 1905年湿法回转窑出现。 ■ 1910年土立窑得到了改进,实现了立窑机械化连续生产。 ■ 1928年德国的立列波博士和波利休斯公司在对立窑、回转窑综
合分析研究后,创造了带回转炉箅子的回转窑,取名为“立波 尔窑”。
■ 1950年,悬浮预热器由德国发明成功并开始应用,大幅度降低 了熟料生产的热耗,极大地提高了生产规模。
■ 1824年,英国J.阿斯普丁发明了一种把石灰石和粘土混和 后加以煅烧来制造水泥的方法,并获得了专利权。这种水泥 同英国附近波特兰小城盛产的石材颜色相近,故称为波特兰 水泥。人类最早是利用间歇式土窑(后发展成土立窑)煅烧 水泥熟料。
■ 1877年回转窑烧制水泥熟料获得了专利权,继而出现了单筒 冷却机、立式磨及单仓钢球磨等,从而有效地提高了水泥的 产量和质量。
5、可利用工业废渣
建筑材料与检测
我国水泥技术
小
湿 法
立
回
窑
转 窑
分日 解产 窑二 新千 型吨 干熟 法料
预
分日 解产 窑五 新千 型吨 干熟 法料
预
我国水泥产量
年产量(亿吨)25来自24 25 25 22.1
20
20
22.5 17 18
15
16.5
- 1、下载文档前请自行甄别文档内容的完整性,平台不提供额外的编辑、内容补充、找答案等附加服务。
- 2、"仅部分预览"的文档,不可在线预览部分如存在完整性等问题,可反馈申请退款(可完整预览的文档不适用该条件!)。
- 3、如文档侵犯您的权益,请联系客服反馈,我们会尽快为您处理(人工客服工作时间:9:00-18:30)。
水泥生产自1824年诞生以来,生产技术历经了多次变革。
从间歇作业的土立窑到1885年出现回转窑;从1930年德国伯力鸠斯的立波尔窑到1950年联邦德国洪堡公司的悬浮预热器窑;1971年日本石川岛公司和秩父水泥公司在悬浮预热技术的基础上研究成功了预分解法,即预分解窑。
新型干法水泥生产技术,是以悬浮预热和预分解技术为核心,利用现代流体力学、燃烧动力学、热工学、粉体工程学等现代科学理论和技术,并采用计算机及其网络化信息技术进行水泥工业生产的综合技术。
新型干法水泥生产技术具有高效、优质、节能、节约资源、环保和可持续发展的特点,充分体现了现代水泥工业生产大型化、自动化的特征。
新型干法水泥生产技术的出现,彻底改变了水泥生产技术的格局和发展进程,它采用现代最新的水泥生产工艺和装备,逐步取代了立窑生产技术、湿法窑生产技术、干法中空窑生产技术以及半干法生产技术,从而把水泥工业生产推向一个新的阶段。
我国水泥工业几乎同步把握了世界新型干法水泥生产技术的发展脉搏。
1 “四平型”预分解窑的形成1970年建筑材料科学研究院(以下简称建材研究院)根据石灰石配料和悬浮预热器的实践,提出了“两级煅烧,即窑尾加把火”的设想,这是我国关于水泥预分解技术的最早设想,与当时的日本等国在设想的提出时间上相差无几。
1970年6月经原国家建委建材工业组批准立项,首先在建材研究院实验室的0.7m×7m窑系统中进行中间试验,效果良好。
1972年在杭州水泥厂的立筒预热器的底部采用喷入少量煤粉补燃的办法,实施了“窑尾加把火”的生产性探索试验。
后因历史原因而搁置,直到1973年建材研究院正式开始对预分解技术进行系统研究,在试验室配备有四级旋风预热器的0.7m×7m窑系统上,完成了烧油和烧煤的试验室试验。
1976年在吉林四平石岭水泥厂2.4m×40m窑上完成了烧油预分解的工业试验,即“四平型”预分解窑设计,产量比同规模的中空窑提高一倍以上。
这是我国第一台预分解窑的工业规模生产线。
该项目1977年通过部级鉴定,1978年获全国科学大会奖。
1976年我国第一台“四平型”烧油预分解窑在吉林石岭水泥厂投产后,各设计院即着手以煤为燃料,先后开发700t/D、1000t/D级预分解窑。
1978年3月,建材研究院设计的本溪水泥厂1200t/D(燃煤)熟料生产线(3.7m×57m窑、KSV炉)建成投产。
该项目1979年6月通过部级鉴定,并获部级二等奖。
仅就分解炉烧煤的研究而言,我国起步早于日本,应用生产也早于日本,为我国2000t/D预分解窑生产线的设计提供了生产实例和实践数据,使我国正式把水泥预分解生产技术列入国家水泥工业技术发展的主攻方向。
2 江西万年国产化2000t/D生产线的开发设计1975年,天津水泥工业设计研究院(以下简称天津水泥院)围绕我国国产化的2000t/D 新型干法生产线的关键技术和设备大型化问题,开展了系统性的科研攻关和开发设计工作,并于1978年基本完成了装备设计工作。
在我国相继成套引进冀东、宁国4000t/D生产线后,国家建材局加大了水泥大型装备国产化的步伐,决定在江西万年的江西水泥厂建设我国第一条国产化2000t/D新型干法水泥生产线。
天津水泥院承担了全部的装备成套和工程设计工作。
该生产线于1982年开始工程设计,1986年建成进入试生产,1989年通过国家验收,各项主要技术经济指标均达到了设计指标。
我国自行设计、自行制造、自行安装的第一条2000t/D生产线的建成投产,标志着我国新型干法水泥生产技术的发展树立了一个新的里程碑。
之后,天津水泥院在国家建材局领导下,立即组织了2000t/D大型预分解窑的国产化“一条龙”攻关和16项单机技术引进及4000t/D级生产线的攻关工作,为我国国产化2000t/D生产线的全面提高打下了坚实的基础。
3 国产化700 t/D生产线的推广1982年经国家计委、经委和科委批准,把“水泥预分解技术及装备”列为第六个国家科技攻关五年计划的三十八个重点项目之一(第二十二项),此举有力地推动了我国新型干法水泥生产技术的发展。
为此,国家建材局选择江苏邳县水泥厂和新疆水泥厂700t/D熟料烧煤预分解生产线作为国家科技攻关重点项目。
经过参加攻关的有关单位和全体同志的共同努力,达到了预期的效果,并于1984年4月和8月分别在江苏邳县和新疆乌鲁木齐市成功地召开了国家科技攻关验收会议。
这项科技成果极大地鼓舞了我国水泥科技工作者发展新型干法水泥生产技术的信心。
为便于各地方和各部门在工程建设时有所遵循、有所借鉴,国家建材局水泥司于1984年11月举办了700t/D熟料预分解工艺线示范设计讲座。
天津水泥院设计的上海川沙水泥厂(650t/D),建材研究院设计的新疆水泥厂(700t/D),合肥水泥院设计的山东枣庄矿务局水泥厂(650t/D),都起到了很好的示范作用。
4 中国水泥发展中心在天津水泥院建立1980年7月,国家建筑材料工业部眼80演建材基字551号文决定在天津水泥院建立联合国开发计划署(UNDP)援助我国的“中国水泥发展中心”。
1983年1月10日,“中国水泥发展中心”(英文缩写CCDC)在天津水泥院正式成立,它是亚太地区唯一的国际性水泥机构,主要任务是“原燃料工艺性能试验、资源和工业废渣综合利用、新技术、新工艺开发、人材交流及人材培训,协助中国水泥工业提高产量和质量”。
“中国水泥发展中心”作为中国水泥的对外窗口,在联合国的帮助下,不断引进国外先进技术,使中国水泥工业逐步达到了世界先进水平,同时向发展中国家推广我国的技术与装备,在我国水泥工业走向世界的进程中起到了积极的作用。
5 学习国外先进技术我国水泥工程技术人员在自力更生、开拓进取的同时,也十分重视学习和借鉴国外先进的科学技术成就。
从1978年开始,相继从日本石川岛、川崎、丹麦史密斯、罗马尼亚等国家引进了4000t/D和3200t/D大型预分解窑的成套设备,冀东、宁国、柳州、株江、淮海等厂一系列大型预分解生产线相继建成投产。
1990后,一些国外独资及中外合资水泥项目也相继进入中国,如烟台三菱、泗水大宇、秦皇岛浅野等大型企业相继建成投产,极大地丰富了我国新型干法水泥生产技术的设计经验。
在通过引进先进技术装备的同时,还采取走出去的学习方式。
1984年,在刚刚完成江西水泥厂2000t/D生产线工程设计后,天津水泥院就派出主要开发设计人员加入到中国建材对外公司承揽的伊拉克卡尔巴拉水泥厂生产劳务承包队伍中;1990年和1993年,天津水泥院又先后两次派出工程技术人员共40余人到丹麦FLS公司参加联合设计。
由此,不但学习了国际先进技术,而且也学习了国际先进管理经验,为全面掌握新型干法水泥生产技术创造了条件。
6 水泥工业的“中国第一线”早在1990年双阳水泥厂2000t/D生产线被国家计委列入“八五”期间重点建设项目时,为了推动我国水泥工业技术水平的提高,国家计委、国家建材局决定把在“六五”和“七五”期间从国外引进的14项先进技术及国内开发的5项新技术集中应用在双阳水泥厂的设计中。
为此,天津水泥院集中力量,开展引进转化、科研开发、技术创新,从原料破碎、原料预均化、生料制备、生料均化、熟料烧成、水泥粉磨到水泥包装的各个环节的技术装备,全部采用国产化的最新技术成果。
在总结前几条2000t/D生产线的基础上,确定了“生产可靠、技术先进、节省投资、提高效益”的指导思想,把引进吸收与自行研发相结合、借鉴与创新相结合,开展创新设计,首次采用一磨(第一台国产4.6m×7.5+3.5m原料磨)一窑(4m×60m)一磨(4.2m×11m水泥磨+辊压机)的工艺流程,并在其它方面也都有新的突破。
1993年6月29日双阳水泥厂顺利投产,不但各项技术经济指标达到上世纪80年代的国际先进水平,而且一年内超过了设计指标,真正实现了“建成之日即为达标、达产之日”的目标。
这条以引进国外先进技术转化的水泥装备国产化2000t/D生产线的“一条龙”项目被誉为“中国第一线”。
为表彰天津水泥院在推动我国新型干法水泥生产技术方面做出的突出贡献,1995国务院发展中心认定天津水泥院为“全国首家设计新型干法水泥生产线的设计研究院”,并收入《中华之最荣誉大典》(1949~1995)。
7 持续技术创新、优化设计在1996年前按“双阳型”建设的10余条2000t/D级生产线基本上都达到了产品高质量和运行可靠性的目标,但由于基建投资过高(按年产能力计,一般为800~1000元/吨),加上项目投资体制不完善和贷款利息过高等原因,使企业几乎无经济效益可言,进而使投资者对新型干法生产线的建设缺乏信心。
1996年原国家建材局根据国家产业政策和建材工业“由大变强、靠新出强”的跨世纪战略的要求,要大力发展以新型预分解技术为主,具有规模经济的大中型水泥项目。
为此而制定的“低投资、国产化、大型化”原则,一直是我国新型干法水泥生产技术发展的主旋律。
鉴于此,在国家建材局的主持下,天津等设计院投入大量人力开展“优化设计、国产化、低投资”的研究和技术创新活动,相继提出了1000t/D、2000t/D、4000t/D水泥熟料生产示范线设计方案。
方案的特点主要是:(1)具有先进的技术指标;(2)具有长期安全运转的可靠性;(3)具有低投入、高产出的良好经济效益。
1998~2000年,又进一步开展技术创新、优化设计活动,在一系列关键技术和装备上,如高效组合式选粉机、高效低压损预热器及分解炉系统、第三代篦式冷却机、高效生料均化库等实现了大的突破,完成了提高型示范设计方案。
在此基础上,天津水泥院先后在宁国二线、白马山4号窑、山东水泥厂3号窑、双阳二线2000t/D等,以及葛洲坝3号窑2500t/D等项目的建设上,技术不断创新、设计不断优化,在确保“优质、高产、低消耗”的前提下,实践“国产化、低投资”技术方案取得了新的突破,达到了项目建设工期短、工程质量好、投资省、达标达产快的目标。
基建投资得以大幅度降低(300~400元/吨),这为新型干法生产线的普及推广奠定了坚实的基础。
与此同时,成都建筑材料工业设计研究院(以下简称成都建材院)和建材研究院致力于高海拔、高风速地区建设新型干法生产线的设计研究。
1995年,成都建材院设计的云南红塔滇西水泥有限公司1号线1000t/D建成投产,一年后被当时的国家建材局列为达标达产示范线。
该生产线的建设成功,为后来在青海、西藏、贵州的高原地区建设新型干法水泥厂提供了经验。
天津水泥院在西藏拉萨设计的西藏高天水泥厂2000t/D生产线是国内外海拔最高、规模最大的新型干法水泥生产线。
8 资源综合利用,走可持续发展之路水泥工业是用煤大户,为了适应水泥工业发展,采用无烟煤代替烟煤既可以解决无烟煤地区建厂,又可降低成本,提高企业经济效益和社会效益。