宝钢工艺流程图
宝钢厚板生产工艺 ppt课件
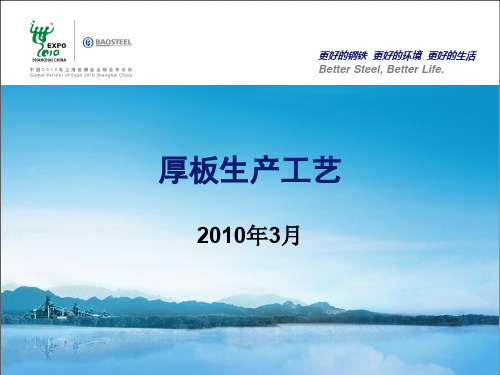
产品交货状态:热轧、控轧、TMCP、热处理
第三部分 产品生产工艺
宽厚板工程为一套4200mm双机架宽厚板轧机机组、剪切线和配套的 热处理炉。主作业线机械设备从德国SMS-Demag公司引进,电器设备 由德国Siemens公司提供。宽厚板生产线集成当今世界上最先进的宽厚 板生产技术,如HAGC、CVC、直接淬火及加速冷却装置(DQ+ACC)、 在线测宽仪和测厚仪等,轧机的最大轧制力达10000吨
装炉、加热及出炉
共设1座推钢式加热炉和两座步进式加热炉,其中一期第一阶段建设1座 推钢式加热炉和1座步进式加热炉。 由30t半门型吊车,将板坯按轧制计划要求一块块吊放到上料辊道上。板 坯向入炉辊道方向上运输,在称量辊道上称重,以核对板坯重量。之后, 板坯送到1号或2号加热炉炉后的入炉辊道上,由装炉辊道送至加热炉前, 再由推钢机将板坯送入加热炉内加热。
板坯库工艺流程简述
热装的板坯,从二次切割线下线后装入保温坑或由平车直接从炼钢连 铸运送来的板坯。需要时从保温坑吊出经过跨车过跨,大吊车再运至上 料点上料。 余坯(09坯)从炼钢送入,吊车卸料放入1#板坯库,需要时可经二次切 割线切割或用平车运入2#板坯库,手工切割(采用半自动切割机)为定尺 坯。 外供板坯,吊车卸料放入1#板坯库,待外运。 外购不锈钢定尺坯,吊车卸料放入1#板坯库,需要时经二次切割线切 割或用平车运入2#板坯库,手工切割(采用半自动切割机)为定尺坯。再 用过跨车运入4#板坯库和1#加热炉跨备料点,等待吊车装入上料辊道。
钢铁生产流程详解图
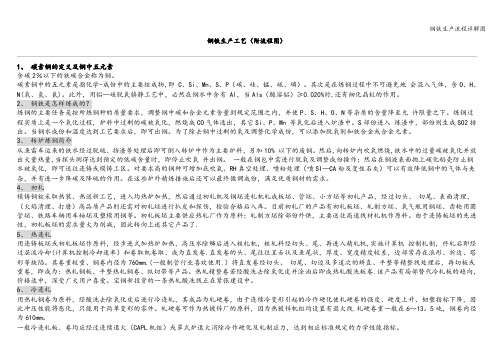
钢铁生产工艺(附流程图)1、碳素钢的定义及钢中五元素含碳2%以下的铁碳合金称为钢。
碳素钢中的五元素是指化学-成份中的主要组成物,即 C、Si、Mn、S、P(碳、硅、锰、硫、磷)。
其次是在炼钢过程中不可避免地会混入气体,含O、H、N(氧、氢、氮)。
此外,用铝—硅脱氧镇静工艺中,必然在钢水中含有 Al,当Als(酸溶铝)≥0.020%时,还有细化晶粒的作用。
2、钢铁是怎样炼成的?炼钢的主要任务是按所炼钢种的质量要求,调整钢中碳和合金元素含量到规定范围之内,并使P、S、H、O、N等杂质的含量降至允许限量之下。
炼钢过程实质上是一个氧化过程,炉料中过剩的碳被氧化,燃烧成CO气体逸出,其它Si、P、Mn 等氧化后进入炉渣中。
S部份进入炼渣中,部份则生成SO2排出。
当钢水成份和温度达到工艺要求后,即可出钢。
为了除去钢中过剩的氧及调整化学成份,可以添加脱氧剂和铁合金或合金元素。
3、转炉炼钢简介从鱼雷车运来的铁水经过脱硫、挡渣等处理后即可倒入转炉中作为主要炉料,另加10% 以下的废钢。
然后,向转炉内吹氧燃烧,铁水中的过量碳被氧化并放出大量热量,当探头测得达到预定的低碳含量时,即停止吹氧并出钢。
一般在钢包中需进行脱氧及调整成份操作;然后在钢液表面抛上碳化稻壳防止钢水被氧化,即可送往连铸或模铸工区。
对要求高的钢种可增加底吹氩、RH真空处理、喷粉处理(喷SI—CA粉及变性石灰)可以有效降低钢中的气体与夹杂,并有进一步降碳及降硫的作用。
在这些炉外精炼措施后还可以最终微调成份,满足优质钢材的需求。
4、初轧模铸钢锭采取热装、热送新工艺,进入均热炉加热,然后通过初轧机及钢坯连轧机轧成板坯、管坯、小方坯等初轧产品,经过切头、切尾、表面清理,(火焰清理、打磨)高品质产品则还需对初轧坯进行扒皮和探伤,检验合格后入库。
目前初轧厂的产品有初轧板坯、轧制方坯、氧气瓶用钢坯、齿轮用圆管坯、铁路车辆用车轴坯及塑模用钢等。
初轧板坯主要供应热轧厂作为原料;轧制方坯除部份外供,主要送往高速线材轧机作原料。
钢铁生产工艺流程图

钢铁生产工艺流程炼焦生产流程:炼焦作业是将焦煤经混合,破碎后加入炼焦炉内经干馏后产生热焦碳及粗焦炉气之制程。
资源来源:台湾中钢公司网站。
烧结生产流程:烧结作业系将粉铁矿,各类助熔剂及细焦炭经由混拌、造粒后,经由布料系统加入烧结机,由点火炉点燃细焦炭,经由抽气风车抽风完成烧结反应,高热之烧结矿经破碎冷却、筛选后,送往高炉作为冶炼铁水之主要原料。
资源来源:台湾中钢公司网站。
高炉生产流程:高炉作业是将铁矿石、焦炭及助熔剂由高炉顶部加入炉内,再由炉下部鼓风嘴鼓入高温热风,产生还原气体,还原铁矿石,产生熔融铁水与熔渣之炼铁制程。
资源来源:台湾中钢公司网站。
转炉生产流程:炼钢厂先将熔铣送前处理站作脱硫脱磷处理,经转炉吹炼后,再依订单钢种特性及品质需求,送二次精炼处理站(RH真空脱气处理站、Ladle Injection盛桶吹射处理站、VOD真空吹氧脱碳处理站、STN搅拌站等)进行各种处理,调整钢液成份,最后送大钢胚及扁钢胚连续铸造机,浇铸成红热钢胚半成品,经检验、研磨或烧除表面缺陷,或直接送下游轧制成条钢、线材、钢板、钢卷及钢片等成品。
资源来源:台湾中钢公司网站。
连铸生产流程:连续铸造作业乃是将钢液转变成钢胚之过程。
上游处理完成之钢液,以盛钢桶运送到转台,经由钢液分配器分成数股,分别注入特定形状之铸模内,开始冷却凝固成形,生成外为凝固壳、内为钢液之铸胚,接着铸胚被引拔到弧状铸道中,经二次冷却继续凝固到完全凝固。
经矫直后再依订单长度切割成块,方块形即为大钢胚,板状形即为扁钢胚。
此半成品视需要经钢胚表面处理后,再送轧钢厂轧延。
资源来源:台湾中钢公司网站。
热轧生产流程。
热轧生产流程。
资源来源:台湾中钢公司网站。
热轧生产流程>第一热轧钢带生产流程:热轧钢带工场主要制程是将扁钢胚加热后,经粗轧机及精轧机轧延成钢带,并以层流冷却系统喷水冷却至适当温度,再由盘卷机卷成粗钢卷。
资源来源:台湾中钢公司网站。
热轧生产流程>一号调质重卷线布置图:主要功能为将原料钢卷上线解卷、调质轧延、分切、重卷及包装为成品H.R COIL 或H.R BAND〔HR BAND 未调质轧延〕。
宝钢三高炉II系设备工艺
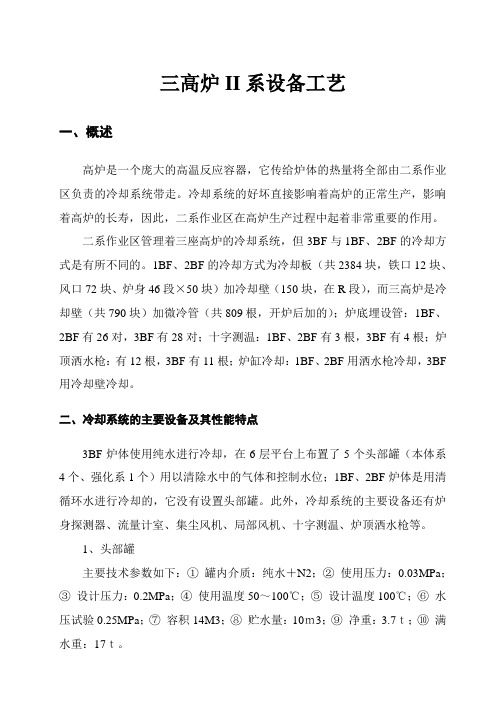
三高炉II系设备工艺一、概述高炉是一个庞大的高温反应容器,它传给炉体的热量将全部由二系作业区负责的冷却系统带走。
冷却系统的好坏直接影响着高炉的正常生产,影响着高炉的长寿,因此,二系作业区在高炉生产过程中起着非常重要的作用。
二系作业区管理着三座高炉的冷却系统,但3BF与1BF、2BF的冷却方式是有所不同的。
1BF、2BF的冷却方式为冷却板(共2384块,铁口12块、风口72块、炉身46段×50块)加冷却壁(150块,在R段),而三高炉是冷却壁(共790块)加微冷管(共809根,开炉后加的);炉底埋设管:1BF、2BF有26对,3BF有28对;十字测温:1BF、2BF有3根,3BF有4根;炉顶洒水枪:有12根,3BF有11根;炉缸冷却:1BF、2BF用洒水枪冷却,3BF 用冷却壁冷却。
二、冷却系统的主要设备及其性能特点3BF炉体使用纯水进行冷却,在6层平台上布置了5个头部罐(本体系4个、强化系1个)用以清除水中的气体和控制水位;1BF、2BF炉体是用清循环水进行冷却的,它没有设置头部罐。
此外,冷却系统的主要设备还有炉身探测器、流量计室、集尘风机、局部风机、十字测温、炉顶洒水枪等。
1、头部罐主要技术参数如下:①罐内介质:纯水+N2;②使用压力:0.03MPa;③设计压力:0.2MPa;④使用温度50~100℃;⑤设计温度100℃;⑥水压试验0.25MPa;⑦容积14M3;⑧贮水量:10m3;⑨净重:3.7t;⑩满水重:17t。
冷却系统补水标准:当头部罐水位低于-300mm时开始补水,当头部罐水位高于300mm时停止补水。
强化系一天补水3~4次,每隔7、8个小时补一次水。
2、炉身探测器①工艺技术条件②主要技术规格3、流量计室每个高炉各有4个流量计室,分别位于4根柱子旁。
3BF各流量计室内控制的风口为:1#流量计室:35#~38#,1#~6#;2#流量计室:7#~15#;3#流量计室:16#~25#;4#流量计室:26#~34#。
钢铁厂生产工艺流程介绍PPT钢铁生产流程

(2)浇铸周期
准备时间
连铸机的浇铸时间及必要的
T= t1+n×t2 其中:T-浇铸周期
t1-准备时间 t2-单炉浇铸时间
n-平均连浇炉数
(3)连铸机的小时产量 P=B×D×Vg×r×60×N 其中: P:连铸机的小时产量 B×D:铸坯断面面积 Vg:拉速 r: 铸坯比重 N:连铸机的流数
(4)连铸机的日产量 A=(1440/ T)×n×G×η 其中: A:连铸机的日产量 T:连铸机的浇铸周期 n:连浇炉数 G:转炉平均出钢量 η:金属收得率
铁水预处理与 钢水炉外精炼处理工艺
连铸工艺与设备
1 现代炼钢技术的发展(连铸技术的作用) (1) 1947年-1974年: 技术特点:转炉、高炉的大型化;以模铸-初 轧为核心,生产外延扩大。 (2) 1974年-1989年: 技术特点:全连铸工艺,以连铸机为核心。 (3) 1989年-现在:
技术特点:连铸-连轧工艺,以薄板 坯,连铸-连轧为代表,钢厂向紧凑化发展。
(5)椭圆型连铸机 (超低头连铸机)
- 机身高度低,厂房高度降低; - 多次变形,每次变形量不大,铸坯质量好; - 钢液静压小,坯壳鼓肚量小,质量好。 ·结晶器内夹杂物不能上浮分离,且内弧集聚; ·多半径,连铸机的对弧、安装、调整困难,设备较复杂。
2.1.3 连铸机机型选择的原则
- 满足钢种和断面规格的要求; - 满足铸坯的质量要求; - 节约建设投资。
紧凑式连续化的专业生产线
连续铸钢的技术特点
· 高效凝固 · 优化成型 · 化学冶金 · 物理冶金 · 节能
凝固理论
连续铸钢的工艺特点
(1)提高综合成材率:模铸从钢水到成坯的收 得 率大约84~88%,连铸为95~96%;
宝钢工艺
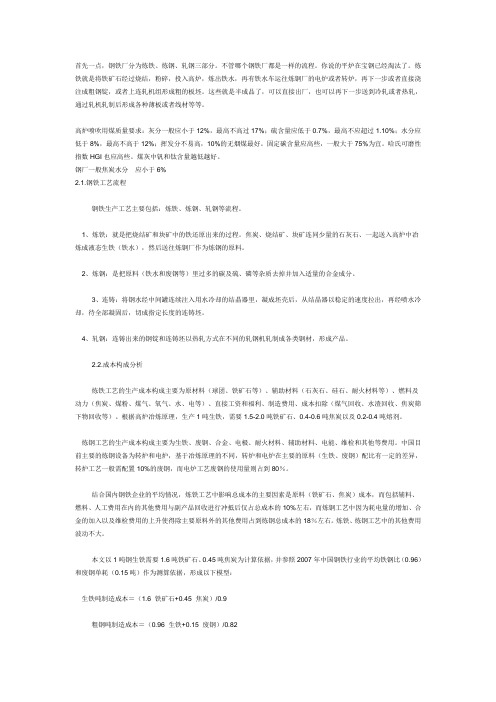
首先一点,钢铁厂分为炼铁、炼钢、轧钢三部分。
不管哪个钢铁厂都是一样的流程。
你说的平炉在宝钢已经淘汰了。
炼铁就是将铁矿石经过烧结,粉碎,投入高炉,炼出铁水,再有铁水车运往炼钢厂的电炉或者转炉,再下一步或者直接浇注成粗钢锭,或者上连轧机组形成粗的板坯。
这些就是半成品了,可以直接出厂,也可以再下一步送到冷轧或者热轧,通过轧机轧制后形成各种薄板或者线材等等。
高炉喷吹用煤质量要求:灰分一般应小于12%,最高不高过17%;硫含量应低于0.7%,最高不应超过1.10%;水分应低于8%,最高不高于12%;挥发分不易高,10%的无烟煤最好。
固定碳含量应高些,一般大于75%为宜。
哈氏可磨性指数HGI也应高些。
煤灰中钒和钛含量越低越好。
钢厂一般焦炭水分应小于6%2.1.钢铁工艺流程钢铁生产工艺主要包括:炼铁、炼钢、轧钢等流程。
1、炼铁:就是把烧结矿和块矿中的铁还原出来的过程。
焦炭、烧结矿、块矿连同少量的石灰石、一起送入高炉中冶炼成液态生铁(铁水),然后送往炼钢厂作为炼钢的原料。
2、炼钢:是把原料(铁水和废钢等)里过多的碳及硫、磷等杂质去掉并加入适量的合金成分。
3、连铸:将钢水经中间罐连续注入用水冷却的结晶器里,凝成坯壳后,从结晶器以稳定的速度拉出,再经喷水冷却,待全部凝固后,切成指定长度的连铸坯。
4、轧钢:连铸出来的钢锭和连铸坯以热轧方式在不同的轧钢机轧制成各类钢材,形成产品。
2.2.成本构成分析炼铁工艺的生产成本构成主要为原材料(球团、铁矿石等)、辅助材料(石灰石、硅石、耐火材料等)、燃料及动力(焦炭、煤粉、煤气、氧气、水、电等)、直接工资和福利、制造费用、成本扣除(煤气回收、水渣回收、焦炭筛下物回收等)。
根据高炉冶炼原理,生产1吨生铁,需要1.5-2.0吨铁矿石、0.4-0.6吨焦炭以及0.2-0.4吨熔剂。
炼钢工艺的生产成本构成主要为生铁、废钢、合金、电极、耐火材料、辅助材料、电能、维检和其他等费用。
中国目前主要的炼钢设备为转炉和电炉,基于冶炼原理的不同,转炉和电炉在主要的原料(生铁、废钢)配比有一定的差异,转炉工艺一般需配置10%的废钢,而电炉工艺废钢的使用量则占到80%。
宝钢烧结工艺简介与环境保护.ppt
1 烧结知识简介
1.2铁矿粉造块方法 铁矿粉造块方法,目前主要有烧结和球团两种。经过造块
3 烧结生产工艺
3.4 烧结成矿机理
铁矿粉烧结过程中,矿石中的酸性氧化物与碱性氧化 物在800℃左右开始通过固相反应生成低熔点化合物。随 着温度进一步升高,这些低熔点化合物逐渐熔化形成液相 ,且扩散至整个烧结体,形成立体“网状交织结构”,将未 熔矿粉粘结起来,冷却后形成烧结矿。概括来说,烧结矿 的成矿过程主要包括固相反应、液相生成、结晶和冷却几 个步骤。
2 宝钢烧结概况
一期烧结最初的三电控制系统为中央集中控制模式,分别 由日本横河电机的I系列单元组合仪表、YODIC-1000过程控制 计算机、日本三菱电机的MLPIAC-50可编程控制器构成,代表 了70年代末世界先进水平。
二烧结三电控制系统则是第一代的集散型控制系统,部分 功能已经下放到L1,由日本三菱的MACTUS-620 综合仪表控制 系统、 MELCOM 350-50/1000计算机构成,为80年代末世界领 先水平。
宝钢烧结工艺简介与环境保护
宝钢股份炼铁厂
主要内容
1 烧结知识简介 2 宝钢烧结概况 3 宝钢烧结生产工艺 4 宝钢烧结工序的环境保护
1 烧结知识简介
一 烧结知识简介 1.1高炉工艺的需求 1.2铁矿粉造块方法 1.3烧结的定义 1.4现代烧结生产的特点
1 烧结知识简介
1.1高炉工艺的需求 随着钢铁工业的发展,对铁矿石的要求量日益增多。然而
宝钢炼钢工艺和设备_详细
二、铁水预处理
▪ 电石粉的特点:
▪ (1)分解出的钙离子与[S]有极强的亲和力,因此 CaC2有很强的脱硫能力,耗量少,渣量也较少。
▪ (2)生成物CaS熔点高,形成固体渣,防止回硫, 扒渣容易,对耐材侵蚀较轻。
▪ (3)脱硫生成的碳除饱和于铁水外,其余以石墨态 析出。同时还有少量CO、C2H2气体,以及少量电石 粉和石灰粉会污染环境,因此必须设置除尘设备。
升降装置由升降小车、横移台车、升降卷扬装 置及升降轨道组成。
三、转炉
(3)副枪装置 为了提高吹炼终点控制的命中率,在吹炼过程
中获得钢水温度、成分、炉内造渣情况等信息。 可装上不同的探头达到不同的检测目的,枪体采 用水冷,使用寿命较长,运行安全可靠,测定速 度快、精度高。副枪装置由旋转框架及其驱动装 置、副枪及升降小车、升降小车驱动装置、探头 供给及装着装置、探头提取及试样切断装置、刮 渣装置及副枪孔密封装置、副枪枪体矫直装置、 探头回收溜槽等。
▪ (4)电石粉极易吸潮劣化,在大气下与水分接触迅 速发生反应,生成C2H2(乙炔)气体易爆,应采取 安全措施。
▪ (5)电石粉价格昂贵。
二、铁水预处理
▪ 石灰粉的特点: ▪ (1)当铁水中的[Si]氧化后,生成Ca2SiO4和SiO2,
相应消耗有效CaO,降低了脱硫效率。 ▪ (2)脱硫渣为固体渣,对耐材侵蚀较轻微,扒渣方
▪ 宝钢现有的炉外精炼装置有:RH-OB(1#RH)、 RH-KTB(3#RH)、RH-MFB(2#RH)、VD、 CAS-OB、KIP、IR、UT、LF炉和喂丝等。
四、炉外精炼
(1)RH真空脱气的基本原理和工艺 为了减少钢中的有害气体和夹杂,净化钢水,提高钢
材的内在质量,改善机械性能,国内外各大钢厂均采用了 各种脱气方法,其中RH真空循环脱气法生产能力大,脱 气效果好,能使用于高生产率的氧气顶吹转炉。
宝钢特钢高合金钢生产线工艺流程简介
宝钢特殊钢分公司高合金钢生产线改造工程宝钢公司特殊钢分公司高合金钢生产线改造工程项目是宝钢建设现代化特殊钢制造中心和特钢精品基地的重大步骤。
高合金钢生产线改造工程是宝钢公司结合特钢产品结构调整,淘汰落后工艺设备,建成一条世界先进,国内一流的专业化特殊合金和高合金钢热轧生产线。
其主要产品定位为生产高附加值、高技术难度的新材料。
这些产品是未来世界经济、军事竞争的焦点,也是一个国家特殊钢工业生产和综合实力的体现和保证。
该工程由中冶京城工程技术有限公司设计,上海宝钢建设监理公司进行工程监理。
工程建设在原上钢五厂特钢分公司西区一块无建筑物的平坦土地上,北靠五钢大道,南靠大电炉,西靠西区五大道,东靠西区四大道。
整条生产线设计年生产能力为10万吨。
其中高合金钢4万吨、合金钢6万吨。
工程项目的核心是轧钢车间。
新建的轧钢主厂房由原料跨、主轧跨、加热炉跨、热处理精整跨〔共二跨〕以及轧棍间和主电室组成,建筑面积约4万平方米。
主厂房内主要设备有:步进梁式加热炉、隧道式中间加热炉各一座,室式炉一座。
轧线主要设备有:一架粗轧机、16架连轧机(中轧8架、预精轧和精轧各4架)以及相应的飞剪、冷床收集等在线和离线装置。
后道精整热处理部分包括:轧后预退火的车底式退火炉二座、连续式退火炉一座、移盖式退火炉二座、固溶炉及时效炉各一座。
新建和利旧有抛丸机、校直机、倒棱机、探伤仪、磨床、抛光机等精整设备以及其相配套的公辅设施等主要公辅设施有:水处理站、总图运输及厂区各专业介质管线、电气室和生活服务设施等。
以及相应进行配套改造和联网:如调压站、七中央以及生产能源或介质管线等改造工程也列入本工程中。
辊底式退火炉设备在安装中车底式退火炉设备在安装中冷床设备在安装中冷床输入辊道设备安装主厂房外景冷床设备在安装中注:〔该工程主轧跨为27m、加热炉跨为18m、热处理精整跨为24和27m、轧辊间为30m和主电室为15m,均成平行布置,原料跨与上述各跨呈丁字形布置。
钢铁生产工艺流程(连铸之前部分)
钢铁生产工艺流程简介铁矿石从开采到最终轧制成各类钢材,需要经过采矿—选矿—烧结—炼铁—炼钢—精炼—各类轧制等若干道工序,另外还需要煤、焦、水、电、气等多种辅助材料,是一种综合的物理和化学变化过程。
下面简要介绍各工序要点。
从铁矿石到各类成品材常规生产工艺流程见图1所示。
图1 钢铁生产常规工艺流程一、铁矿石资源概况、开采与选矿1.1铁矿石资源概况铁矿石以各种复杂的伴(共)生形式广泛存在于地壳表、浅层中。
据2005年的探明数据,世界铁矿石保有储量(可立即开发的工业品位的总量)为1600亿吨,基础储量(可开发的工业品位和一级边界品位储量)为3700亿吨。
澳大利亚、巴西、中国、俄罗斯、乌克兰、加拿大、美国和印度等国家都是铁矿石资源大国。
中国、巴西、澳大利亚、印度是世界上铁矿石产量最多的国家,其中巴西的淡水河谷公司(CVRD)、澳大利亚的力拓(Rio Tinto)和必和必拓(BHP)是世界上铁矿石生产量和贸易量最大的三家公司,三家的贸易量占世界铁矿石贸易总量的70%左右。
我国是铁矿石储量大国,目前已探明的资源储量为600多亿吨,可利用资源250多亿吨,但铁矿石品位(含铁量)较低,平均品位只有30%-35%左右,贫矿(低品位矿)比例为97%。
我国铁矿石分布广泛而又相对集中,储量较多的地区有辽宁、河北、四川、内蒙古、山东和安徽等。
按照铁存在的化合物形式,可将铁矿石分为赤铁矿(Fe2O3)、磁铁矿(Fe3O4)、菱铁矿(FeCO3)和褐铁矿(Fe2O3·H2O)等。
1.2铁矿石的开采主要开采形式有露天开采和地下开采。
1.3 铁矿石的选矿我国铁矿由于贫矿多(占总储量的97.5%)和伴(共)生有其它组分的综合矿多(占总储量的1/3),所以在冶炼前绝大部分需要进行选矿处理。
选矿的目的就是通过各种方法,将铁矿石中的铁氧化物以外的脉石等其它杂质尽可能地去除,提高最终产品中铁的含量。
主要流程:铁矿石破碎—磨粉—选矿—烘干—成品精矿粉。