铸造工技师论文(初稿)
铸造加工论文电火花加工技术论文

铸造加工论文电火花加工技术论文论铸造齿轮替代机械加工齿轮摘要:对齿轮的加工,传统的加工都是机械切削加工而制造出来的,就是通过毛坯粗车到精车。
再滚齿成形,最后到热处理成产品。
如果改用一种新型的熔模精密铸造,这种小无切削的加工工艺。
大大地降低了生产成本节约了合金资源,提高了生产效率,特别是对于低速大模数的齿轮,效果更为明显。
本文是以扎钢机直齿轮为例,探讨研究。
关键词:齿轮;模具;精密铸造工艺一般中小型的扎钢机械,在使用运行过程中,由于设备的环境、条件、工况较差,加上是传动力距大,又是连续运行,导致齿轮磨损大,视这零件为易损配件,需经常更换的一种备件。
一、加工齿轮与铸造齿轮的比较(一)机加工轧钢机齿轮的要求与各项指标(1)齿轮模数 m=7齿数 z=25(2)压力角a=20°(3)齿节(分度园)d=m·z=7×25=175(4)齿顶高ha=m=7(5)齿根高hf=1.25×m=1.25×7= 8.75(6)全齿高h=2.25×m=2.25×7=15.75(7)顶隙c=0.25×m=0.25×7=1.75(8)齿顶圆直径da=d+2ha=175+2×7=189(9)齿根圆直径df=d-2hf=175-2×8.75=157.5(10)基圆直径db=d·cosa(11)齿距 p=πm=3.14×7=21.98(12)齿厚s=πm/2=21.98/2=10.99(13)齿间宽e=πm/2=21.98/2=10.99(14)齿宽 b=80以上数据是机械加工要求的轧钢机齿轮,由于这齿轮加工成本高,就机械加工齿轮为例,在正常的情况下,单加工齿面的机械加工费需126元左右(未含毛坯材料费、端面及内孔,键槽加工费),而改精铸制造的话,单价计算=单价×重量,铸件每公斤8元,该铸件重13kg×8.00元=104元就可以做出,但铸造能否达到加工件的要求,因为铸造本身有其特有的优势和劣势,就以本人根据这齿轮的用途和工作条件,两种结合取长补短,第一改正常齿为变位齿,第二是由原来的加工精度6级改为8级精度,第三是从铸造工艺出发提高模具精度,改善铸造工艺来保证齿轮各参数,使其能符合齿合传动要求。
铸造工艺实习报告论文

铸造工艺实习报告论文应用铸造有关理论和系统知识生产铸件的技术和方法。
包括铸件工艺,浇注系统,补缩系统,出气孔,激冷系统,特种铸造工艺等内容。
铸造工艺设计内容包括:铸件工艺图的设计,铸件图的设计,铸型装配图的设计以及工艺卡的制作等。
今天店铺要与大家分享:铸造工艺实习报告相关论文。
具体内容如下,希望可以帮到大家!在近二个月的时间内熟悉了铸造工艺、生产组织和生产管理。
深入了解常用铸造合金、熔炼设备和熔炼处理工艺。
熟悉主要铸造设备的结构、特征和工作原理。
对典型零件的铸造工艺有了初步了解,进一步体会到包括铸造工艺及设计要求,在生产中起着重要的作用。
制造企业的动作管理是以产品为中心展开的,主要控制对象是生产进度,产品质量和生产成本。
我就这三个问题其中一点——产品的生产进度,来进行讨论。
下面是这段时间内,我所见到的和所学到的。
车间主要情况车间设计整体比较协调,不管是安生标识的提示,还是人和(叉)车行走的路线及铸件的传输都比较人性化和科学化。
车间布置,以便使铸件、型砂、砂芯等的传输,型砂传至制芯车间、造型车间以及旧砂的回收利用均是有皮带传输;铸件由成型到落砂、抛丸、清理等工序均由链传动;砂芯的成型及烘干到铸件造型车间由链传动。
而铁水由熔炼到浇注则由叉车转运。
铸造厂目前有三个车间,大件车间和中件车间及熔炼车间,两个车间分了四个工部,砂处理工部、制芯工部、造型工部、清理工部。
熔炼车间有25T、80T的工频炉。
主要设备有德国KW 造型线,西班牙制芯机、瑞士抛丸机和瑞士机械手。
大、中件车间主要采用静压气冲紧实方法实现造型,合箱、浇注、冷却等一系列铸造工序的自动化生产。
现阶段生产的主要零件有:机体、缸盖、齿轮室、飞轮等灰铁铸件。
砂处理工部落砂及旧砂的回收利用在回收过程中需经磁选、筛选后进行冷却。
冷却过程中测水分和温度教困难。
从而不能控制加水量。
砂中水分过高回阻碍机器的正常运转。
所以冷却设备的选择极其重要。
一般采用振动沸腾冷却床。
铸造技师论文参考文献范例
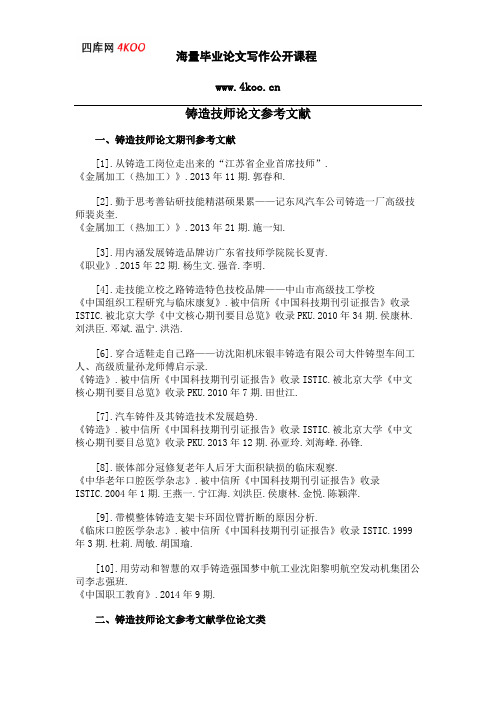
铸造技师论文参考文献一、铸造技师论文期刊参考文献[1].从铸造工岗位走出来的“江苏省企业首席技师”.《金属加工(热加工)》.2013年11期.郭春和.[2].勤于思考善钻研技能精湛硕果累——记东风汽车公司铸造一厂高级技师裴炎奎.《金属加工(热加工)》.2013年21期.施一知.[3].用内涵发展铸造品牌访广东省技师学院院长夏青.《职业》.2015年22期.杨生文.强音.李明.[4].走技能立校之路铸造特色技校品牌——中山市高级技工学校《中国组织工程研究与临床康复》.被中信所《中国科技期刊引证报告》收录ISTIC.被北京大学《中文核心期刊要目总览》收录PKU.2010年34期.侯康林.刘洪臣.邓斌.温宁.洪浩.[6].穿合适鞋走自己路——访沈阳机床银丰铸造有限公司大件铸型车间工人、高级质量孙龙师傅启示录.《铸造》.被中信所《中国科技期刊引证报告》收录ISTIC.被北京大学《中文核心期刊要目总览》收录PKU.2010年7期.田世江.[7].汽车铸件及其铸造技术发展趋势.《铸造》.被中信所《中国科技期刊引证报告》收录ISTIC.被北京大学《中文核心期刊要目总览》收录PKU.2013年12期.孙亚玲.刘海峰.孙锋.[8].嵌体部分冠修复老年人后牙大面积缺损的临床观察.《中华老年口腔医学杂志》.被中信所《中国科技期刊引证报告》收录ISTIC.2004年1期.王燕一.宁江海.刘洪臣.侯康林.金悦.陈颖萍.[9].带模整体铸造支架卡环固位臂折断的原因分析.《临床口腔医学杂志》.被中信所《中国科技期刊引证报告》收录ISTIC.1999年3期.杜莉.周敏.胡国瑜.[10].用劳动和智慧的双手铸造强国梦中航工业沈阳黎明航空发动机集团公司李志强班.《中国职工教育》.2014年9期.二、铸造技师论文参考文献学位论文类[1].不同饰核瓷厚度比对IPSe.maxPress全瓷修复体断裂载荷及遮色能力的影响.被引次数:1作者:靳海立.口腔医学第四军医大学2012(学位年度)[2].基于ACIS的数字化适形铅模设计技术研究.被引次数:1作者:胡瑛.机械制造及其自动化天津大学2006(学位年度)[3].基于PMAC的义齿加工数控系统的研究.作者:张振东.模式识别与智能系统东北大学2010(学位年度)[4].纯钛金属全冠微渗漏及密合度的研究.作者:任晓娟.口腔临床医学河北联合大学2014(学位年度)三、铸造技师论文专著参考文献[1]上海船厂青铜艺术铸造概述.陈林才,1999中国艺术铸造第一届年会[2]巧用基台重新种植冠修复.刘利苹.张日媚,2011第七届全国口腔种质学术会议[3]稀土元素Gd对Zr基块体非晶合金形成能力的影响.梁顺星.宗海涛.宋爱君.张卫国.马明臻,2008第十二届全国特种铸造及有色合金学术年会、第六届全国铸造复合材料学术年会暨2008年福建省铸造学术年会[4]120t吊架铸件造型模具的设计.贾泽春,20122012年中国铸造活动周[5]原位自生TiCpLD7复合材料高温蠕变应力指数及激活能.嵇峰.宋爱君.张卫国.宗海涛.梁顺星.马明臻,2008第十二届全国特种铸造及有色合金学术年会、第六届全国铸造复合材料学术年会暨2008年福建省铸造学术年会[6]SHS法合成TiCP/2A12基复合材料的组织与性能.马明臻.韦娜.张卫国,2006第十一届全国特种铸造及有色合金学术年会、第五届全国铸造复合材料学术年会、第十二届全国铸钢及熔炼学术年会暨中国有色金属加工工业协会重有色分会技术交流会[7]TiCP/2024复合材料蠕变性能.张卫国.宋爱君.稽峰.马明臻,20072007年中国压铸、挤压铸造、半固态加工学术年会[8]添加Al<,2>O<,3>对重力分离SHS法制备Al<,2>O<,3>/Fe复合管组织的影响.张卫国.王煦.邢剑申.马明臻,20052005年中国压铸、挤压铸造、半固态加工学术年会[9]SiC泡沫/Al双连续相复合材料连续性的研究.赵龙志.何向明.赵明娟.熊光耀.何柏林.张劲松,2007第六届中国功能材料及其应用学术会议。
砂型铸造论文

砂型铸造工艺研究及分析论文——材料成型技术基础摘要:砂型铸造是一种以砂作为主要造型材料,制作铸型的传统铸造工艺。
砂型一般采用重力铸造,有特殊要求时也可采用低压铸造、离心铸造等工艺。
砂型铸造的适应性很广,小件、大件,简单件、复杂件,单件、大批量都可采用。
砂型铸造用的模具,以前多用木材制作,通称木模。
此外,砂型比金属型耐火度更高,因而如铜合金和黑色金属等熔点较高的材料也多采用这种工艺。
但是,砂型铸造也有一些不足之处:因为每个砂质铸型只能浇注一次,获得铸件后铸型即损坏,必须重新造型,所以砂型铸造的生产效率较低;又因为砂的整体性质软而多孔,所以砂型铸造的铸件尺寸精度较低,表面也较粗糙。
本片论文主要对砂型铸造的工艺进行研究分析,以及在工业中的运用进行分析。
具体过程,详见本文的论述。
本篇论文是参考《砂型铸造工艺技术手册》上的工艺过程及相关工艺编写的。
本篇论文的内容包括:目录、正文、参考文献等。
关键词:砂芯砂型硬模铸造1.砂型铸造砂型铸造——在砂型中生产铸件的铸造方法。
钢、铁和大多数有色合金铸件都可用砂型铸造方法获得。
由于砂型铸造所用的造型材料价廉易得,铸型制造简便,对铸件的单件生产、成批生产和大量生产均能适应,长期以来,一直是铸造生产中的基本工艺。
砂型铸造所用铸型一般由外砂型和型芯组合而成。
为了提高铸件的表面质量,常在砂型和型芯表面刷一层涂料。
涂料的主要成分是耐火度高、高温化学稳定性好的粉状材料和粘结剂,另外还加有便于施涂的载体(水或其他溶剂)和各种附加物。
2.铸造成型工艺简介铸造是将金属熔炼成符合一定要求的液体并浇进铸型里,经冷却凝固、清整处理后得到有预定形状、尺寸和性能的铸件的工艺过程。
铸造毛坯因近乎成形,而达到免机械加工或少量加工的目的降低了成本并在一定程度上减少了时间.铸造是现代制造工业的基础工艺之一。
铸件自浇注冷却的铸型中取出后,有浇口、冒口及金属毛刺披缝,砂型铸造的铸件还粘附着砂子,因此必须经过清理工序。
金属铸造工艺论文[五篇范例]
![金属铸造工艺论文[五篇范例]](https://img.taocdn.com/s3/m/3199c111ef06eff9aef8941ea76e58fafab045d4.png)
金属铸造工艺论文[五篇范例]第一篇:金属铸造工艺论文金属铸造工艺论文摘要:铸造是将通过熔炼的金属液体浇注入铸型内,经冷却凝固获得所需形状和性能的零件的制作过程。
铸造是常用的制造方法,铸造是一种古老的制造方法,在我国可以追溯到6000年前。
随着工业技术的发展,铸大型铸件的质量直接影响着产品的质量,因此,铸造在机械制造业中占有重要的地位。
由零件的结构特点,提出多种浇注和分型方案,综合对比分析,选择最为理想的浇注位置及分型面。
制定出详细的铸造工艺方案。
关键字:铸造工艺性;铸造工艺方案;铸造工艺参数;补缩系统;浇注系统铸造工艺种类:铸造工艺可分为重力铸造、压力铸造、砂型铸造、压铸、熔模铸造和消失模铸造。
铸造方法常用的是砂型铸造,其次是特种铸造方法,如:金属型铸造、熔模铸造、石膏型铸造等。
各种特种铸造方法均有其突出的特点和一定的局限性,对铸件结构也各有各自的特殊要求。
重力铸造重力铸造是指金属液在地球重力作用下注入铸型的工艺,也称浇的重力铸造包括砂型浇铸、金属型浇铸、熔模铸造,泥模铸造等;窄义的重力铸造专指金属型浇铸。
压力铸造压力铸造是指金属液在其他外力(不含重力)的作用下注入铸型的工艺。
广义的压力铸造包括压铸机的压力铸造和真空铸造、低压铸造、离心铸造等;窄义的压力铸造专指压铸机的金属型压力铸造,简称压铸。
这几种铸造工艺是目前有色金属铸造中最常用的、也是相对价格最低的。
砂型铸造砂型铸造是一种以砂作为主要造型材料,制作铸型的传统铸造工艺。
砂型一般采用重力铸造,有特殊要求时也可采用低压铸造、离心铸造等工艺。
砂型铸造的适应性很广,小件、大件,简单件、复杂件,单件、大批量都可采用。
砂型铸造用的模具,以前多用木材制作,通称木模。
木模缺点是易变形、易损坏;除单件生产的砂型铸件外,可以使用尺寸精度较高,并且使用寿命较长的铝合金模具或树脂模具。
虽然价格有所提高,但仍比金属型铸造用的模具便宜得多,在小批量及大件生产中,价格优势尤为突出。
铸才网分享铸造专业毕业论文

铸才⽹分享铸造专业毕业论⽂⽬录1 绪论 (1)1.1 选题背景和研究意义 (1)1.2 计算机模拟在铸造中的应⽤现状 (3)1.2.1 国外研究现状 (3)1.2.2 国内研究现状 (5)1.3 ProCAST软件介绍 (6)1.3.1 ProCAST软件主要模块功能 (6)1.3.2 ProCAST软件结构 (7)1.4 研究⽬的及内容 (8)2 铸造铝合⾦缩孔形成理论 (8)2.1 铸造分类及特点 (8)2.2 铸造的缺陷 (9)2.3 铝合⾦铸件缩孔形成机理 (9)2.4 铝合⾦铸件中影响缩孔形成的因素 (10)2.5 数值模拟技术概论 (10)2.5.1 铸造过程数值模拟软件的发展现状 (10)2.5.2 温度场 (11)2.6 铝合⾦铸件缩孔形成的部位 (13)3 低压铸造下的缩孔缺陷数值模拟 (13)3.1 数值模拟凝固过程缩孔缺陷预测 (13)3.2 铝合⾦铸件缩孔的预测⽅法 (15)3.3 低压铸造中缩孔预测 (17)3.4 运⽤Pro/E绘图软件绘制双头锤试件 (17)3.5 利⽤EasyCAST模拟结果分析 (19)3.6 ProCAST软件模拟分析 (21)3.6.1 ⽹格剖分 (21)3.6.2 进⼊PreCAST界⾯设置条件 (22)3.6.3 模拟计算 (23)4 模拟结果对⽐ (24)4.1 双头锤低压铸造结果 (24)4.2 ProCAST软件模拟结果和EasyCAST模拟对⽐ (25)4.3 ⼩结 (26)5 结论 (26)参考⽂献 (28)致谢 (30)1 绪论1.1 选题背景和研究意义铸造⾏业作为⼀个古⽼的⾏业,在数千年⼈类发展过程中,曾经为⼈类⽂明的发展与进步作出了巨⼤贡献。
早在5000年前的殷商时代,可以铸造饮酒⽤的杯,当作乐器⽤编钟,祭祀⽤的铜⿍,打仗⽤的武器等,被誉为世界奇迹。
青铜器的铸造就很发达,湖北隋县出⼟的⼀套青铜全套64⽀,总重5吨多,⽓势磅礴,铸造精美,纹路精细,敲击时铿锵悦⽿,深沉浑厚,乐⾳和谐,扣⼈⼼弦。
铸造专业的毕业论文
铸造专业的毕业论文随着工业的快速发展,不断有更高效、更环保、更节能的新工艺路线和新技术出现,铸造技术也在不断发展和更新。
本篇毕业论文将从铸造技术、材料、工艺三个方面进行研究,探讨现代铸造技术的发展和应用。
一、现代铸造技术的发展铸造技术是一种重要的制造工艺,在汽车、机械、航空、船舶等行业中都有广泛的应用。
随着技术的不断进步,铸造技术经历了许多变化和发展。
1. 全自动化铸造技术随着计算机和自动化技术的应用,铸造技术也有了很大的进步。
全自动化铸造技术采用自动铸造机,实现了金属熔炼、浇注、晾凉、清理后的整个铸造流程的自动控制。
这种技术大大提高了产量和质量,节省了人力和材料,减少了环保污染。
2. 数值模拟铸造技术数值模拟铸造技术是通过计算机模拟软件,将真实的铸造过程抽象成数学模型,进行数值模拟,并通过模拟结果对实际铸造过程进行优化和控制。
该技术可以预测铸件的内部缺陷,优化喷砂、涂料等工艺,避免金属流动中的缺陷和失误。
3. 智能铸造技术智能铸造技术是将计算机、控制、通讯等先进技术与铸造技术相结合,形成智能化、自动化的铸造生产网络。
这种技术不仅能监控铸造过程中的数据,还可以根据数据预测问题的解决方案并进行控制,大大提高了产品的质量和稳定性。
二、现代铸造材料的应用1. 高强度铸造合金高强度铸造合金是现代铸造材料的一种,其具有高强度、高韧性、高温稳定性等特性。
这种材料在国防、航空、航天等领域得到广泛应用。
2. 稀土元素稀土元素是一类具有重要物理、化学和生物学性质的元素,具有遮蔽轻有害辐射、提高合金耐热性能、增强弹性等优异特性,因此,稀土元素在铸造中应用广泛。
3. 新型材料随着材料科学的发展,新型材料的不断涌现和应用,使得铸造技术也更加精密和全面。
例如,金属陶瓷材料、碳纤维等,这些材料在汽车、飞行器、高速列车等轻质化方面具有广泛的应用前景,为铸造技术带来了新的发展机遇。
三、现代铸造工艺的探索1. 小型化和精密化随着科学技术的不断发展,小型化和精密化成为了现代工业发展的趋势和方向。
铸造技术论文
铸造技术论⽂铸造技术论⽂ 应⽤铸造有关理论和系统知识⽣产铸件的技术和⽅法。
包括铸件⼯艺,浇注系统,补缩系统,出⽓孔,激冷系统,特种铸造⼯艺等内容。
今天⼩编为⼤家准备了铸造技术论⽂,欢迎阅读! 浅谈快速成型技术 【摘要】本篇⽂章简单介绍了快速成型技术的起源、优点和特点,同时分析了快速成型制造技术的应⽤及未来发展⽅向,⼯业产品造型设计及制造利⽤了此项技术,可以很⼤程度的提⾼设计及制造⽔平、缩短设计开发、⽣产制造周期、降低产品开发期间的成本,具有⼴泛的应⽤前景。
【关键词】快速成型制造技术;产品造型设计;特点;优越性;应⽤;发展趋势 【引⾔】随着经济的飞速发展,⼈们的⽣活⽔平不断提⾼,⼈们要求可以实现产品功能的同时,对产品的造型也提出了更⾼的要求。
⼀个成功的产品必须注意造型的设计,产品造型体现了设计者的意图和使⽤者的权利,只有把设计者的意图与使⽤者的需求统⼀起来,产品才能成为⼀个成功的产品。
这样,对产品造型设计及制造提出了更⾼的要求,此时,快速成型制造技术便引⼊到产品造型设计和制造中。
起源 快速成形技术⼜可以叫做快速原型制造(Rapid Prototyping Manufacturing,简称RPM)技术,产⽣于20世纪80年代的后期,是基于材料堆积法的⼀种⾼新制造技术,被认为是近20年来制造领域的⼀个重⼤成果。
它集机械⼯程、CAD、逆向⼯程技术、分层制造技术、数控技术、材料科学、激光技术于⼀⾝,可以⾃动、直接、快速、精确地将设计思想转变为具有⼀定功能的原型或直接制造零件,从⽽为零件原型制作、新设计思想的校验等⽅⾯提供了⼀种⾼效低成本的实现⼿段。
即,快速成形技术就是利⽤三维CAD的数据,通过快速成型机,将⼀层层的材料堆积成实体原型。
快速成型技术发展⾄今,以其技术的⾼集成性、⾼柔性、⾼速性⽽得到了迅速发展,传统的快速成形技术使⽤的是“去除”加⼯法,即部分去除⼤于⼯件的⽑坯上的材料来得到⼯件。
⽽全新的快速成型技术使⽤的是“增长”加⼯法——⽤⼀层层的⼩⽑坯逐步叠加成⼤⼯件,将复杂的三维加⼯分解成简单的⼆维加⼯的`组合。
铸造技师技术总结范文
尊敬的领导:您好!在过去的一年里,我在公司担任铸造技师一职,主要负责铸造工艺的技术指导和生产管理。
现将我过去一年的工作情况进行总结,以便更好地提高自身技能,为公司的发展贡献力量。
一、工作回顾1. 不断学习,提高自身素质过去的一年,我深知自身在专业知识和技能方面还有待提高,因此我积极参加各类技术培训,学习新技术、新工艺,努力提高自己的业务水平。
通过学习,我对铸造行业的发展趋势有了更深入的了解,为公司的技术创新和工艺改进提供了有力支持。
2. 优化工艺,提高产品质量针对生产过程中出现的问题,我积极与生产一线员工沟通,分析原因,制定改进措施。
通过对铸造工艺的优化,提高了铸件的质量,降低了生产成本。
具体表现在以下几个方面:(1)改进铸造工艺,提高铸件尺寸精度。
通过对铸造模具的优化设计和改进,使铸件尺寸精度得到显著提高。
(2)优化熔炼工艺,提高铸铁成分质量。
通过调整熔炼温度、时间等参数,使铸铁成分达到国家标准,提高铸件性能。
(3)加强铸件后处理,提高铸件表面质量。
通过严格控制铸件热处理工艺,使铸件表面质量得到有效改善。
3. 强化团队建设,提高团队凝聚力作为铸造技师,我深知团队协作的重要性。
在日常工作中,我注重与同事沟通交流,关心团队成员的成长,积极参与团队活动,增强团队凝聚力。
通过以下措施,提高了团队整体素质:(1)定期组织技术交流活动,分享经验,共同提高。
(2)关心员工生活,解决实际问题,增强团队凝聚力。
(3)加强内部培训,提高员工技能水平。
二、不足与反思1. 在新技术、新工艺的运用方面,还有待进一步提高。
今后,我将更加关注行业动态,不断学习,紧跟时代步伐。
2. 在团队管理方面,还需加强沟通与协调,提高团队执行力。
三、展望未来在新的一年里,我将继续努力,充分发挥自身优势,为公司的发展贡献自己的力量。
具体目标如下:1. 深入学习新技术、新工艺,提高自身业务水平。
2. 优化铸造工艺,提高铸件质量,降低生产成本。
铸造论文---技师专业论文
铸铁件砂芯制造工艺对铸件质量的影响姓名:***学号:**********专业:车辆工程—09日期:2011、09、27摘要:造芯材料的合理选用,合理的工艺制造砂芯,保证铸件质量。
关键词:强度、透气性、退让性、粘砂、铸件质量。
一、引言砂芯的主要作用是用来形成铸件的内腔,有时也用于组成铸件的外形。
由于砂芯的四周被高温金属液所包围,受到的冲刷及烘烤比砂型厉害。
通常要在干态下工作,有较大的吸湿性,从而使强度降低,发气量增加。
在金属液高温作用下,砂中的粘结剂粘力若不失去,砂芯取出困难,同时在冷却过程中由于凝固收缩,受到很大压缩力。
因此砂芯制造工艺要比砂型严格,砂芯应具有良好的透气性、溃散性、退让性和更高的强度。
才能有效防止铸件的气孔、粘砂、夹砂、变形等缺陷。
二、造芯材料1、硅砂的选用铸铁的熔点低于铸钢,浇注温度一般在1200—1400℃左右,因此,对硅砂耐火度的要求比铸钢低,粒度也可以细一些。
铸铁用的硅砂种类范围较宽:一般用93、90、85级硅砂,而大件砂芯用93或90硅砂,小件砂芯可用85级硅砂。
粒度可用30/50、40/70、50/100、70/140、100/200粗粒、中粒和细粒砂。
铸铁用硅砂,并不是Si02含量越高越好,Si02含量高,耐火度高,对防止某些铸造缺陷烧结有好处;但是砂子受热后体积变化大,铸件易产生夹砂。
因此;铸铁一般选用Si02含量为85级硅砂。
1)粒度。
硅砂粒度越大,芯砂耐火度越高,透气性越好。
但是芯砂强度低,铸件表面粗糙。
2)均匀度。
砂粒集中则粒度均匀,粒度均匀则透气性好。
铸造用硅砂主要粒度组成部分三筛不小于75%,四筛不小于85%。
3)颗粒形状。
用角形因数描述硅砂颗粒形状的圆整程度。
角形因数越大,则砂粒形状越偏向于尖角形。
圆形砂粒组成的空隙最大,透气性最好,尖角形砂粒表面往往粗糙,易粘附粘结剂,利于获得较高的强度。
2、粘土。
是一种比砂子细得很多的粒径为1—2μm天然土状细颗粒材料,一般为白色或灰白色。
- 1、下载文档前请自行甄别文档内容的完整性,平台不提供额外的编辑、内容补充、找答案等附加服务。
- 2、"仅部分预览"的文档,不可在线预览部分如存在完整性等问题,可反馈申请退款(可完整预览的文档不适用该条件!)。
- 3、如文档侵犯您的权益,请联系客服反馈,我们会尽快为您处理(人工客服工作时间:9:00-18:30)。
减少DZ2侧架自硬树脂砂立柱面补砂芯报
废的控制要点探讨
企业名称:
姓名:
考评职业:铸造技师
减少DZ2侧架自硬树脂砂立柱面补砂芯报废的控制要点探讨
摘要:本文结合南车长江铜陵公司铸造车间自硬铬矿砂芯在制芯过程中经常出现的制芯质量隐患并结合我们采取的预防措施,着重介绍在DZ2侧架生产过程中,由于操作手法差异、不同生产节奏下树脂加入量偏差等因素导致立柱面铬铁矿砂补砂芯大批量不合格从而导致DZ2侧架立柱磨耗板安装面大面积多肉的成因以及采取的改进措施,目的在于降低铬矿补砂芯不合格率,减少由于自硬铬铁矿砂(立柱面补砂芯)制芯不合格导致的铸件不合格的情况发生,从而达到理顺生产流程、降低质量损耗的目的,并为类似的自硬树脂砂制芯提供参考。
关键词:铸造;自硬树脂砂;铬铁矿砂;固化剂;硬化时间;碗型碾砂机
一、DZ2侧架自硬铬铁矿砂芯制芯简介
2014年3月份,中国铁路总公司紧急采购5000辆C80E货车进行批量运行试验,DZ2摇枕侧架关键零部件由长江铜陵公司负责生产,由于订单紧、任务重、要求高,几乎全部员工都要面临一次大
考,没有成熟的生产工艺,大量工装模具需要重新改造,产品质量只能在试制过程中探索解决。
车间自硬铬铁矿砂芯制芯工序为造型首道工序,砂芯的制作情况直接影响着后道工序能否顺利完成。
在DZ2侧架生产中,立柱面补砂芯采用自硬树脂砂(铬铁矿砂)制芯,混砂设备(图1.1)为碗型间歇式树脂砂混砂机,每次混砂前通过固定在混砂机上方的定量斗量取铬铁矿砂25kg,按照工艺要求树脂组分Ⅰ加入量为25kg*(0.35-0.55)%=(87.5-137.5)g;活化剂组分Ⅱ加入量为25kg*(0.25-0.45)%=(62.5-112.5)g;催化剂组分Ⅲ加入量为(1~5)%*组分Ⅰ=(0.875-6.875)g;将定量好的PZ-Ⅲ(组分III)加入PZ-Ⅰ(组分I)中搅拌5-10秒混均匀,加入到铬铁矿砂中搅拌,再加入PZ-II(组分II),在混砂机中搅拌30~50s,混砂机在混砂工作时通过碗形容器内高速旋转的叶片,将砂以涡流运动翻起,碗型上方斜口盖板再将砂反射下来,这样反复循环使砂与固化剂、树脂砂粘剂快速搅拌,在瞬间内,使砂与固化剂和树脂砂粘接剂充分混合,混好芯砂后通过固定在碗型下方的出砂口放出芯砂,用容器承装到制芯工位将砂填入准备好的芯盒中,待砂芯硬化到一定程度后,按照操作要求翻模,取出砂芯。
图1.1 碗型混砂机 二、自硬铬铁矿砂硬化原理及立柱面补砂芯制芯工艺分析 硬化原理:在树脂的硬化反应中,首先是树脂中的碱与酯反应,形成碱金属的碳酸盐,释放醇。
树脂中的碱形成碳酸盐后,即处于反应状态,可在常温下发生交联反应,将砂粒粘结,使砂芯具有必要的强度。
由于作为固化剂(组分II )有机酯是参与树脂硬化反应的组分,不同于活化剂(组分Ⅲ)只起催化作用,不参与反应的其他树脂自硬砂,不能通过改变活化剂(组分Ⅲ)的加入量来调整自硬砂的硬化速率和起模时间。
树脂加入量不足,则砂芯难以硬化;树脂加入量太高,则会感到混成砂和砂型腻滑,而且可能导致铸型一金属界面处发生反应,影响铸件表面质量。
固化剂的加入量首先取决于本身酸性强弱,其次根据砂型(芯)的硬化速度和硬化强度的要求决定。
在树脂相同的情况下,随着固化剂加图1.2 立柱面补砂芯芯盒
图1.3 立柱面补砂芯起模板
入量的增加,树脂砂的硬化速度显著加快,型砂强度也随之提高,脱模时间缩短,但是固化剂加入量到一定限度,型砂终强度下降(如图2.1)。
[1]有机酯硬化的酚醛树脂砂,在有机酯的作用下,树脂在常温下只发生部分交联反应,起模时型砂仍然保持一定的塑性,也就是我们常说的未完全硬化。
[2]
立柱面补砂芯工艺分析:如下图(图2.3)所示,立柱面补砂芯长290mm,宽240mm,平均厚度约30mm,砂芯芯头配合面在120mm 处中部分段,上部40 mm厚,下部20mm厚,形成台阶芯头搭接结构,上下边缘共有4只成型冷铁,单个砂芯重量约为8kg,砂芯工作面有一定弧度。
制芯至浇注过程中砂芯涉及主要工步(动作):前期准备工作→制芯(芯盒清理→混制芯砂→摆放冷铁→填砂→压实→刮砂→起模→清理砂刺→摆放)→转运到修整工位→安装到整体芯→涂料淋涂→表干窑烘干→整体下芯→合箱浇注。
在以上工步中,制芯、安装补砂芯、整体下芯三个工步为立柱面补砂芯涉及到的主要质量控制工序。
图2.1 固化剂量与24小时强度关系图2.2 固化剂量与强度关系
立柱面补砂芯
图2.3 DZ2侧架下芯后状态及立柱面补砂芯位置图
三、DZ2侧架立柱面补砂芯制芯到合箱浇注工序存在的问题及原因分析
DZ2侧架从试制到批量生产以来,手工制芯(自硬铬铁矿砂)工序由于受到芯盒模具数量配套不佳、砂芯设计结构、辅助工装缺失、混砂机一次混砂量与芯盒数量不匹配等原因限制,造成劳动生产组织困难,立柱面补砂芯质量难以保证,以及暴露出的诸多其它问题,尤其是立柱面补砂芯合格率较低,铸件立柱磨耗板安装面大面积多肉等问题一直制约着下道工序的生产,并对日产量计划的兑现产生较大影响,现在列举主要问题如下:
1、树脂砂混砂不均匀,树脂未完全包覆砂粒,导致立柱面补砂芯硬化速度、局部强度存在较大差异,砂芯成型不良,即使看似成
型良好,在起模或转运过程中很容易破碎,造成大量的人力、财力浪费,如果下芯合箱浇注还有造成铸件报废的风险;
2、立柱面补砂芯上下成型冷铁容易松动甚至掉落,在制芯操作时,由于砂芯上下边缘分别只有40mm、20mm厚,成型冷铁厚度约15mm,冷铁区域吃砂量较小,在立柱面补砂芯安装到整体芯上后,下边缘(铸件无字面)成型冷铁处于悬空状态,仅靠约5mm 的吃砂量拉住冷铁挂砂脚固定,如若砂芯成型不良、强度不足或是砂芯受到强烈震动很容易导致此处冷铁掉落;
3、砂芯容易从芯头台阶处变形开裂,导致砂芯尺寸偏差,甚至直接从台阶处折断(如图3.1),如制芯工艺分析,制芯、安装补砂芯、整体下芯为立柱面补砂芯涉及到的主要质量控制工序,三个主要工序都没能控制住砂芯开裂,不合格砂芯流到下道工序将很有可能导致严重的后果,如6月2号、3号两天就因该砂芯断裂导致铸件报废40余只(如图3.2)。
多肉
图3.1立柱面补砂芯开裂报废图3.2铸件磨耗板安装面大面积多
6月初批量出现由于立柱面补砂芯断裂导致铸件报废的质量事故后,对制芯工序、安装补砂芯、整体下芯工序进行观察并结合清理场地的铸件统计发现:○140余只立柱磨耗板多肉的铸件全部都是补砂芯下芯前从台阶处断裂掉落,导致此处浇注时多肉,○2将近60%铸件立柱磨耗板安装面下部壁厚不均匀,且留有较大披锋,○3不同班组制芯班组的砂芯质量存在差异,○4不同混砂人员对混砂机的操作熟练程度、对树脂砂的基本性能了解程度不一样,○5不同制芯人员在制作立柱面补砂芯时操作手法、硬化时间、起模方式存在差异;由以上统计和分析得出,导致以上缺陷发生的主要原因有:1、该砂芯在工艺设计时存在一定的缺陷,设计时将砂芯工作面设计为弧面,未能考虑到制芯后砂芯取模、摆放等步骤,由于工装有限,左右两块砂芯配合摆放后,砂芯未完全硬化,仍然有一定的塑性变形,当形变量超出即时塑性变形极限时砂芯开裂;
2、碗型混砂机性能不稳定,员工操作手法差异等,导致树脂混碾不均匀,砂芯强度分布差异大,在起模或转运过程中砂芯很容易破碎。
3、混砂人员对自硬树脂砂性能和混砂工艺了解不足,在产量大幅度增加的情况下,妄图通过增加各组分树脂配比,来增加砂芯强度、缩短砂芯硬化时间,从而加快制芯效率。
四、改进方案及实施
为保障DZ2摇枕侧架生产,减低砂芯报废,减少质量损失,强化有效劳动,降低由于立柱面补砂芯断裂导致DZ2侧架报废的概率,针对立柱面补砂芯制芯、补砂芯安装、整体芯下芯出现的问题及产生的原因,确定了改进方案:
1、对辅助工装进行完善,增加模具数量并配套补砂芯起模翻板(如图1.3),保证砂芯充足的硬化时间。
在原有2副立柱面补砂芯芯盒的基础上再增加一副芯盒,保证3副芯盒一人同时使用,砂芯在起模板上基本硬化定型后在摆放上架。
2、混砂工艺进行了重新探索和规定;确定树脂加入最佳比例满足砂芯强度要求,并严格按照树脂加入比例碾砂,在原来生产实际过程中,树脂组分Ⅰ加入量为90g左右;活化剂组分Ⅱ加入量为110g左右;催化剂组分Ⅲ加入量为5g,组分Ⅰ: 组分Ⅱ=9:11=0.82,经过试验探索,将组分Ⅰ加入量调整为110g左右,组分Ⅱ加入量调整为90g左右,组分Ⅲ加入量不变,组分Ⅰ: 组分Ⅱ=11:9=1.22,经过此次调整后,树脂加入总量不变,但砂芯质量有了明显的提高,冷铁掉落、成型不良等缺陷明显减少。
3、对碗型混砂机混砂叶片进行修复完善;原有叶片磨损严重且结构不合理,叶片与混砂机碗壁间隙较大,部分芯砂不易被翻起,不能。