塑性成形过程的数值模拟汇总
钛合金TC4板超塑性成形/扩散连接数值模拟

即n
盯
=
=
O
K
,
所以B a
( 叠)
—
c
fe
n
本 构 关 系为
高
、
耐蚀性好
低温 性能好
、
司于 19 7 0 年发明的
,
此项技 术 以其独特 的
X
。‘
低
天
,
使得钛 合金 广泛 的应用于航空航 舰船
、
优越 性迅 速 发展成为钛 合金 结 构 件 制 造
举 世 瞩 目的 新 技 术
。
式 中K
—
材 料 系数
,
对整个戍形过程有 7 更
,
深入 的7 解
。
通 过 有 限 元 模 拟 可 以 获 得 优 化 的 匝 力 时 同 曲线 坟 而 为 实 际 戍 形 的
一
压 力控 制 提 供 重 要 依 据
,
引言
钛合金是
5 0
和连接 的主 要加工 技术
。
钛 合金 有很 多
一
,
超 塑 性 本构关 系
材 料 在 发 生 塑 性 变形 时
,
。
MS C
.
r m a
)
,
M A R C 是 功 能齐 全 的 高 级 非 线 性 有 限 元 软 件 的 求 解 器
体 现 了 几 十 年 来 有 限 元 分析 的
一
模具 设 定 为 刚 性 体
和 模具 为干 摩擦
,
(R i g i d
)
;
(2
)板 料
;
理 论 方 法和软 件 实 践 的 完 美 结合
燃
.
c A 。厄 A M 忙 A E 技 术 运 用
钛合金超塑性成形过程的数值模拟

摘要 : 以T C 4合 金层板结构 的超塑性成形过程 为研 究对 象 , 采用 有限元软件 M A R C模 拟计算 了 T C 4合 金宽 弦空心夹 芯结构的 超 塑性成形过 程。 分别分析 了应变速率敏感指数、 目标应 变速 率及扩散连接宽度等参数对贴模 过程及壁板厚度分布 的影响。 结果表 明: 当应变速率敏感 指数较大 时, 夹 芯结构会发 生沿纵 向挤 出延伸 变形 ; 当目标应 变速 率为 1 0 1时, 材 料表现 出较 佳的超 塑性性 能; 而扩散连接宽度的大小对超塑性成形后板 材壁 厚分布 的均匀性有 一定影响 。 通过控制最大应变速率的方法 , 提取 出了最优 化的 压力 时间 曲线。研 究结论可为钛合金 空心夹芯结构件的超塑性成形提供理论参考 。
( J i a n g s u P r o v i n c e Ke y L a b o r a t o r y o f Ae r o s p a c e P o we r S y s t e m s , Na mi n g Un i v e r s i t y
o f Ae r o n a u t i c s a n d A s t r o n a u t i c s , Na n j i n g 2 1 0 0 1 6 , C h i n a ) Ab s t r a c t : T a k i n g t h e s u p e r - p l a s t i c f o r mi n g ( S P F ) p r o c e s s o f t h e t h r e e p l a t e s t r u c t u r e a s t h e r e s e a r c h o b j e c t , t h e s u p e r - p l a s t i c f o r mi n g
塑性成型数值模拟理论绪论

2. 几何方程:(6个方程,9个未知量)
γ xy = γ yx = (
γ yz = γ zy γ zx = γ xz
1 ∂u ∂v + ) 2 ∂y ∂x 1 ∂v ∂w = ( + ) 2 ∂z ∂y 1 ∂w ∂u = ( + ) 2 ∂x ∂z
塑性成形基本方程2 塑性成形基本方程
3. 本构方程:(6个方程,5个独立)
1 [σ x − (σ y + σ z )] σ 2 dε 1 dε y = [σ y − (σ z + σ x )] σ 2 dε 1 dε z = [σ z − (σ x + σ y )] σ 2 3 dε τ xy dγ xy = 2σ 3 dε τ yz dγ yz = 2σ 3 dε dγ zx = τ zx 2σ dε x = dε
数值模拟发展趋势2 数值模拟发展趋势
1. 耦合分析
–
与损伤演变耦合
塑性加工可能产生内部缺陷,可能影响工件的寿命,提出损 伤(微裂纹)概念。 损伤D由物理场变量引起,如何建立D与场变量之间的定量 关系是一个难点。
2. 精度控制
–
成形工件多样化,影响塑性成形因素复杂化(摩擦、 材料内部的不均匀性),控制模拟精度比较困难,特 别是三维仿真和大型钣料成形。
返回
有限元发展概况
1. 有限元的起源 – 50年代末最早应用于分析飞机结构件受力分析 2. 常用于分析塑性加工问题的FEM FEM – 弹性有限元法:利用广义Hook定理建立应力应变关系,适用于 结构分析。 – 弹塑性有限元:1967年Marcal和King提出,采用Prantl-Ruess 方程,应用弹性有限元思路,建立增量之间的定量关系。应用 于小变形和求解残余应力和变形问题。 – 刚塑性有限元:1973年Kobayashi提出,认为材料是理想刚塑 性材料,采用变分原理求解大变形问题。目前应用最广。
基于韧性损伤力学的金属塑性成形研究及其数值模拟

基于韧性毁伤力学的金属塑性成形探究及其数值模拟关键词:韧性毁伤力学;金属塑性成形;本构干系;应力应变行为;材料毁伤机理;数值模拟1. 引言金属塑性成形是指通过加工变形将原材料从初始状态转化为期望的外形和尺寸的制造工艺。
其具有良好的可塑性和可加工性,已广泛应用于汽车制造、飞机制造、建筑等诸多行业。
金属塑性成形涉及材料力学、金属形变学、以及传热与流体学等多个领域,其内部机理复杂,需要深度探究。
本文旨在通过使用韧性毁伤力学分析金属塑性成形过程中材料的本构干系和应力应变行为,综合思量金属材料的实际性质,基于数值模拟方法建立新的模型,较好地模拟出金属塑性成形中的各种现象。
以此为基础,本文旨在探讨优化金属塑性成形技术的途径和方法。
2. 金属塑性成形金属塑性成形过程中,金属材料可以通过压力、拉伸、折弯、切削等方法,通过加工变形使其达到期望的外形和尺寸。
其基本原理是在大应力作用下,金属材料的晶格结构发生变化,从而导致塑性变形。
塑性形变是一种可逆变形,通过对材料施加压力,可以使其恢复到初始状态。
金属塑性成形涉及多个因素,如应力、应变、温度等。
在不同的状况下,材料的本构干系和应力应变行为均有所不同。
同时,金属材料在塑性变形中,还可能经历本质未知的材料毁伤,如微裂纹、裂缝、塑性韧性毁伤等。
这些因素的综合作用,决定了金属塑性成形的最终效果。
3. 韧性毁伤力学韧性毁伤力学是一种描述金属塑性成形材料毁伤过程的方法。
其主要思想是将材料的本质韧性与强度之间的干系思量在内。
在金属塑性成形中,韧性对材料变形能力的影响是分外重要的。
因此,韧性毁伤力学可以更好地反映材料的实际性质,有助于探究金属塑性成形中的材料毁伤机理。
基于韧性毁伤力学,可以将材料的力学行为分为两个部分:弹性和塑性。
其中,弹性变形不会导致材料的可逆变形,而塑性变形将导致材料的不行逆性变形。
在塑性变形中,材料的本质韧性和材料的强度之间的干系在整个过程中都是起重要作用的。
金属塑性成形过程韧性断裂的准则及其数值模拟
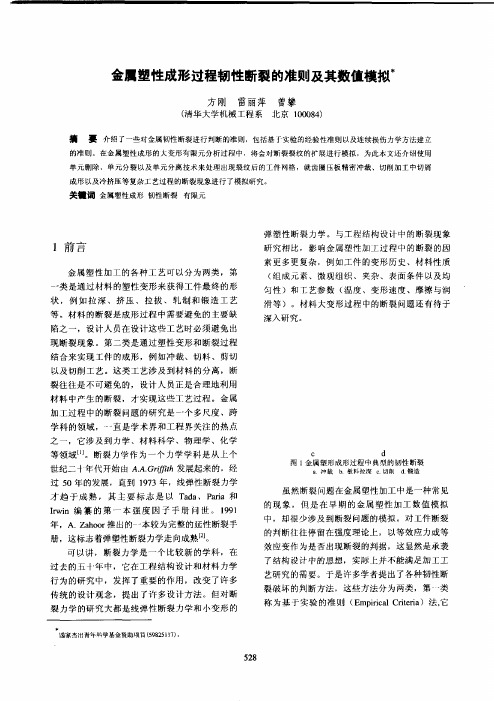
R e r y在1 9 es 9 年提出了三向应力作 i 和Tc l 6 c a ]
用下材料的韧性断裂准则为:
的应用。最后介绍作者对几个典型工艺模拟的结
果。
1 .
2韧性断裂准则
金属在加工过程中发生的断裂大多是韧性断 裂,很少发生脆性断裂。一般认为,金属中的韧
Kc nv 1 8 a a 在 9 年首先提出的另一种分析方 ho 5
法。这种研究方法主要是从细观 ( e s l m s ce oa) 的角度进行研究,对空洞的萌生和扩展角度进
行预测,建立空洞萌生准则。因为韧性断裂的
调整,局部调整还包括单元删除 ( e tn D l o)、 e i
50 3
截
国家杰出青年科学基金资助项目( 851) 5 21 . 9 7
58 2
主要是通过标准的常规实验来获取材料的实验数 据,然后用于对材料成形过程中的韧性断裂的判 断上,它还分二种,即应力、应变和应变能准 则,这类准则的代表是 C cr t a a 准则。 ok fLt m o- h 从所分析的尺度和方法上讲,它属于宏观断裂力 学的范畴。这种方法的缺陷是简单的力学实验条
申
虽然断裂问题在金属塑性加工中是一种常见 的现象,但是在早期的金属塑性加工数值模拟 中,却很少涉及到断裂问题的模拟。对工件断裂 的判断往往停留在强度理论上,以等效应力或等 效应变作为是否出现断裂的判据,这显然是承袭 了结构设计中的思想,实际上并不能满足加工工 艺研究的需要。于是许多学者提出了各种韧性断 裂破坏的判断方法,这些方法分为两类,第 类 称为基于实验的准则 (m i a Cir ) 它 E pi l ea 法, r c r i t
世纪二十年代开始由A .r h .G咖t发展起来的, A 经
钛合金超塑性成形过程的数值模拟

钛合金超塑性成形过程的数值模拟张顺;刘小刚【摘要】Taking the super-plastic forming(SPF) process of the three plate structure as the research object, the super-plastic forming process of TC4 wide-chord hollow structure was simulated by using finite element software MARC. The effects of the strain rate sensitivity index, the target strain rate and the diffusion bonding width on the coating process and the thickness distribution of the panel were studied. The results show that the wide-chord hollow structure deform along the longitudinal extension of extrusion, when the strain rate sensitivity index is larger, and the struture shows better performance of super plastic forming, when the strain rate is around of 10-3. Meanwhile, the diffusion bonding width has a certain influence on the uniformity of the sheet thickness distribution after the super plastic forming. The optimal pressure time curve is obtained by controlling the maximum strain rate. The results of the study can provide theoretical reference for super-plastic forming of titanium alloy wide-chord hollow structure.%以TC4合金层板结构的超塑性成形过程为研究对象,采用有限元软件MARC模拟计算了TC4合金宽弦空心夹芯结构的超塑性成形过程.分别分析了应变速率敏感指数、目标应变速率及扩散连接宽度等参数对贴模过程及壁板厚度分布的影响.结果表明:当应变速率敏感指数较大时,夹芯结构会发生沿纵向挤出延伸变形;当目标应变速率为10-3时,材料表现出较佳的超塑性性能;而扩散连接宽度的大小对超塑性成形后板材壁厚分布的均匀性有一定影响.通过控制最大应变速率的方法,提取出了最优化的压力时间曲线.研究结论可为钛合金空心夹芯结构件的超塑性成形提供理论参考.【期刊名称】《航空发动机》【年(卷),期】2017(043)006【总页数】7页(P69-75)【关键词】超塑性成形;钛合金;数值模拟;压力时间曲线;板材壁厚【作者】张顺;刘小刚【作者单位】南京航空航天大学江苏省航空动力系统重点实验室,南京210016;南京航空航天大学江苏省航空动力系统重点实验室,南京210016【正文语种】中文【中图分类】V252.30 引言超塑性成形(SPF)具有塑性高、变形抗力小、可一次精密成形等优点,已在航空航天等工程领域得到广泛应用。
金属塑性成形有限体积数值模拟
模 具 技 术 2 0 0 3 0 2N
3
文章 编号 :10 一 9 42 0 }3 0 3 3 0 l 4 3 (020 —00 —0
金 属 塑性 成 形 有 限体 积 数 值 模拟
周 飞 , 丹, 苏 彭颖红, 阮雪榆
( 海交通 大学 上 塑 性成 形工 程 系 , 上海 20 3 ) 0 0 0
=A +& ( 3 1)
: 一P . +S
() 6
数。
假设 材料 为 致 密 体 材 料 , 料 的 密度 保 持 不 材 变, 则从 () ( ) 得 到 速 度 变 化率 在 有 限 单 元 1和 2 可 体积 上的 积 分式 :
a
f
+
a ,
二 =o 守恒 方程 3 a ) (E + p
a
.
:业 l 二
a a
() 3
…
上述 三式 中 , u , P E 分 别 为材 料的 密 P, S , 度、 速度矢 量 、 应力 张量 、 力和 内能 。 压
的 节点 在空 问 固定 不 动 , 因此 . ue 单 元 的体 积 E lr
是 不 变 的 物 体 的 材 料 只 是 从 一 个 单 元 流 到 另 一
收 稿 日期 : 0 2 )一0 2 0 一【 l 4 作者 简介 : 岗 飞f 9 1 . . 17 ~) 男 井师
其 中 , 为塑性 应 变速 率张 量 , 为 与应 力 、 以 应 变 以及 应 变速率 有关 的 系数 , 为各 向同性 材 r
个单 元 流到 另 一 个单 元 。在 材料 流动 的过 程 中 ,
必须 满 足质 量 守恒 、 量守 恒 、 动 能量 守 恒 、 构 方 本
塑性加工中的数值模拟
铝合金挤压过程的数值模拟铝合金可以被视为一种粘性不可压缩非牛顿流体。
目前流体运动的描述方法可以分为拉格朗日描述(Lagrangian description)方法、欧拉描述(Eulerian description)方法和任意拉格朗日-欧拉描述(Arbitrary Lagrangian-Eulerian description)方法三种。
数值模拟计算方法中,根据离散方法的不同,主要可以分为有限差分方法(FDM)、有限元法(FEM)、有限体积法(FVM)等。
几十年来,有限元和有限体积法等数值模拟方法已被广泛应用于铝合金挤压过程的数值分析中。
众多的研究者利用数值方法对铝合金挤压过程进行了模拟研究,其中有限元法应用最为广泛,而有限体积法因其解决大变形问题的优势,也逐渐被引入到塑性成形领域。
1、6063铝合金半固态反挤压数值模拟利用有限元模拟技术,研究材料在半固态成形过程中的流场、温度场、应力应变场等分布规律,预测6063铝合金在成形过程中的充型行为、可能产生的缺陷和最佳工艺参数等信息,可为实际生产提供理论依据。
6063铝合金具有极佳的加工性能,是典型的挤压合金,被广泛应用于建筑型材等。
获得6063铝合金不同温度和应变速率下的应力-应变曲线后,采用有限元软件DEFORM-3D对合金半固态反挤压成形过程进行数值模拟,对主要工艺参数进行优化。
半固态反挤压过程的有限元力学模型见图1,变形体为圆柱体。
实验中所用的坯料、凸模和凹模均为轴对称,取其1/4进行模拟分析。
采用刚-粘塑性有限元法,采用图1有限元力学模型对半固态6063合金在不同工艺条件下的反挤压过程进行有限元模拟。
图1 反挤压力学模型及特征点位置数值模拟结果分析:(1)坯料变形过程及坯料成形中的速度场分布挤压模拟时取工件内部不同位置的5个点作为特征点跟踪,特征点位置见图1。
挤压过程中特征点位置坯料流动速度随时间的变化见图2。
在挤压变形过程中,材料受三向压应力作用,发生塑性变形的金属主要集中在坯料端部的外侧,且靠近上模型腔入口处的金属变形量为最大。
材料塑性变形特性的数值模拟与分析
材料塑性变形特性的数值模拟与分析材料的塑性变形特性是描述材料在外力作用下发生塑性变形的行为。
在工程设计和制造过程中,了解材料的塑性变形特性对于预测材料行为和优化产品性能至关重要。
然而,由于实验方法的限制以及时间和成本的约束,数值模拟和分析成为研究材料塑性变形特性的重要工具。
数值模拟是通过使用计算机数值方法来模拟材料的塑性变形过程。
这种方法可以通过建立材料的数学模型和所需物理参数来预测材料在不同载荷条件下的行为。
塑性行为的数值模拟通常基于塑性本构方程,用于描述材料的应力-应变关系。
在模拟过程中,根据实际应变测试数据,通过对实验结果的曲线拟合,可以确定材料的本构模型参数。
为了模拟材料的塑性变形行为,需要考虑多个因素,如应力状态、应变率效应和温度影响等。
基于这些因素,数值模拟可以提供各种塑性变形的预测和分析。
例如,在金属材料的塑性变形中,进行材料塑性变形特性的数值模拟可以预测材料的应力分布和变形轨迹,并进一步分析材料的应变硬化特性和应力松弛行为。
在材料塑性变形特性的数值模拟中,有限元方法是最常用的方法之一。
有限元方法将材料划分为有限数量的单元,并在每个单元中建立适当的数学模型。
通过对单元之间的相互作用进行连续性和边界条件的求解,可以得到材料在不同加载条件下的应力和变形。
这种方法的优点是可以模拟复杂的几何形状和非线性材料行为。
除了有限元方法,还有其他数值方法可用于材料塑性变形特性的数值模拟,如网格方法、材料本构模型等。
这些方法可以针对不同的材料和应用需求进行选择和优化。
在数值模拟的基础上,对材料塑性变形特性进行分析也是非常重要的。
分析可以通过对模拟结果进行后处理来实现。
通过计算应力、应变和变形等参数,可以评估材料的力学性能和变形机制。
同时,分析还可以提供关于材料在条件改变时的响应情况和行为特性的信息。
总之,材料塑性变形特性的数值模拟与分析对于理解材料行为、优化设计和预测产品性能具有重要意义。
通过建立合适的数学模型和使用合适的数值方法,可以准确地预测材料在外力作用下的塑性变形行为。
塑性成型中的数值模拟
一、塑性成型数值模拟概述:塑性加工过程的有限元数值模拟,可以获得金属变形的详细规律,如网格变形、速度场、应力和应变场得分布规律,以及载荷-行程曲线。
通过对模拟结果的可视化分析,可以在现有模具设计上预测金属的流动规律,包括缺陷的产生。
利用得到的力边界条件对模具进行结构分析,从而改进模具设计,提高模具设计的合理性和模具的使用寿命,减少对模具重新设置的次数。
复杂横截面铝型材挤压模具的设计与数值模拟分析1.铝合金型材应用背景铝合金型材广泛用于建筑建材、交通运输、航空、航天、电子电器等领域。
铝合金型材产品成形的质量取决于对模具结构的合理设计及各种尺寸因素是否得当。
而目前, 国内行业存在的普遍现状仍是通过经验类比的方法设计模具, 模具的一次试模成功率大概只有50% ~ 6 0% 。
采用数值模拟的手段对设计进行验证和反馈, 提高设计的成功率, 有着很大的发展前景。
2.设计分析方案本文选取一个特定的复杂横截面型材, 分析其模具的设计方案; 建立了挤压过程的有限元模型, 利用基于任意拉格朗日欧拉法( A L E) 的Hyperxtrude 专用模块,对铝合金型材的挤压过程进行模拟分析。
通过对模具设计方案的数值模拟, 重点对坯料在模具中不同位置的速度分布结果进行分析, 并对比实际试模情况, 对模具的设计方案进行了修正, 探讨了在挤压工艺中通过模具结构的调整, 实现对金属流动进行控制, 以改善模腔内的材料流动, 获得合格的型材产品。
3.针对问题图2 为某型材厂生产的具有复杂横截面尺寸的产品。
由于型材断面的外接圆直径达到Φ236.3mm,比挤压棒料的直径尺寸大了约20 % , 因此需要对材料进行比较大的宽展成形。
为减轻模具上模分流桥部位的压力, 以及尽量减少上模的宽展角度, 需要做一块导流板以保护上模和引导金属向两边流动如图3所示a、导流板b、上模c、下模图 4 所示为导流板端面向下50mm 处截取平面的金属流动速度分布图, 由图可见, 导流板上由于中间位置的分流孔往右边倾斜向下供料,导致金属较多的被拖向右边的分流孔, 导致金属在右边的分流孔中流动比左边的分流孔流动快。
- 1、下载文档前请自行甄别文档内容的完整性,平台不提供额外的编辑、内容补充、找答案等附加服务。
- 2、"仅部分预览"的文档,不可在线预览部分如存在完整性等问题,可反馈申请退款(可完整预览的文档不适用该条件!)。
- 3、如文档侵犯您的权益,请联系客服反馈,我们会尽快为您处理(人工客服工作时间:9:00-18:30)。
实验报告塑性成型过程的数值模拟班级:机自07姓名:欧阳罗辉学号:100111702012年12月一、实验目的:通过本实验的教学,使学生基本掌握有限元技术在板料塑性成形领域的应用情况,拓宽学生的知识面,开阔视野,使学生对塑性成形过程的数值模拟技术有深刻的理解,预测板料弯曲成形的性能。
二、教学基本要求:学会使用Dynaform数值模拟软件进行板料弯曲成形过程的仿真模拟,对模拟结果具有一定的分析和处理能力。
三、实验内容提要:掌握前处理的关键参数设置,如零件定义、网格划分、模型检查、工具定义、坯料定义、工具定位和移动、工具动画、运行分析。
了解后处理模块对模拟结果的分析,如读入d3plot 文件、动画显示变形和生成动画文件、成形极限图分析、坯料厚度变化分析等。
四、软件操作过程:1. 导入压边圈、板料、下模板、上模板图形文件点击File —Import,出现Import File 对话框,找到“ L型弯曲零件图”选中binder.igs,点击Import,如此,依次导入四个模型文件,最后点击“确定”确认四个模型导入后,结果如图2. 重命名文件点击PartLEdit ,出现Edit Part 对话框,这里便要依次更改文件名首先选用红色文件名“ cOOIvOOO 1 ”,在上面的Name 对话框中输入binder ,然后点击 Modify ,以此类推输入 banker 、die 、punch 。
Edit Part3. 对各图形文件划分有限元网格1. Binder零件网格划分n点击口图标,出现Part Turn。
对话框,依次单击banker 2, die 3, punch 4,它们都会被取消选中,只留下binder 1被显示,点击0K确定。
然后点击右下角的Current Part,弹出Current Part对话框,选择binder 1,点击OK确定。
点击Preproces L Element,弹出Element对话框,选择Part Turn On/Off Select by Cursor第四个图标(自动模式),将Max Size改为10,点击Select Surfaces点击Displayed Surf,点击OK,点击Apply,点击Yes,点击Exit,点击OK,于是第一个零件网格划分完成。
2. Banker零件网格划分n点击i□图标,取消Binder 1零件的显示,添加Banker 2 Select Dy NameAll On |AllOfiOK Undo F Only SeledOn零件的显示,点击OK确定。
然后点击右下角的Current Part图标,将当前零件选成Banker 2, 点击OK确定。
点击Preproces A Element,弹出Element对话框,选择第三个图标,弹出Control Keysto ne对话框,点击POINTS/NODES,弹出In put Coo。
对话框,选中Poi nt,然后在绘图区沿顺时针或者逆时针方向依次选中Ba nker零件的四个顶点,如下图所示4. 并选择冲压方向点击图标,将所有零件显示。
点击Preproces p Model Check,弹出Model Check对话框,点击第一个图标,然后点击Punch零件(紫色),单击两次,便会显示Punch零件的法向,如果向右,贝U点击No,如果向左,则点击Yes。
单击右下角的Current Part,将当前文件选为蓝色的Die零件,单击图标,再点击蓝色的Die零件,单击两次,同样会显示Die零件的法向,应该是向上的,如果是对的就点击Yes,如果错了就点击No。
单击右下角的Current Part,将当前文件选为红色的binder零件,单击图标^^^,再点击红色的binder零件,单击两次,同样会显示Binder零件的法向,应该是向下的,如果是对的就点击Yes,如果错了就点击No。
最后点击0K确认5. 定义坯料和成型工具点击Tools—Define Tools,弹出Define Tools对话框。
默认的Tool Name 是Die,点击Add 加载零件,弹出Select Part对话框选择零件,点击Die 3,点击OK,再点击OK。
点击Tools—Define Tools,弹出Define Tools对话框。
默认的Tool Name是Die,将其改为Pun ch (左键点住之后下托),点击Add加载零件,弹出Select Part对话框选择零件,点击Punch4,点击OK,然后点击Define Load Curve添加载荷曲线,弹出ToolLoad。
对话框,点击Auto,在弹出的Motion Curve对话框中输入速度值和位移值,速度值为2000,位移值为45,点击OK,点击OK,点击OK,再点击OK。
点击Tools—Define Tools,弹出Define Tools对话框。
默认的Tool Name是Die,将其改为Binder (左键点住之后下托),点击Add加载零件,弹出Select Part对话框选择零件,点击Binder 1,点击OK,然后点击Define Load Curve添加载荷曲线,弹出ToolLoad。
对话框,选中Force,再点击Auto,在弹出的Force/Tim。
对话框中输入力值,力值为10000,点击OK,点击OK,点击OK,再点击OK。
点击Tools—Define Blank,弹出Define Blank对话框。
点击Add加载零件,弹出Select Part 对话框选择零件,点击Banker 2,点击OK。
点击Material后面的None定义材料,弹出Material 对话框,点击Material Library材料库进行选择,随便选一种材料(老师当时选的第三行最后一个ooo),点击OK,再点击OK。
点击Property后面的None定义特性,弹出Property对话框,点击New,弹出的对话框不用管直接点OK,再点OK,再点OK。
input of data is conpletedMemoriJ reaiiii*ed to hegrio so lut ion - 413614Additional dynamically allocated memory- 88S5TolLal= 4194692526 t 2.7281E-03 dt 1.08E-06 Flush iZg buffersdt 1.08E-06 w>*ite adapt iu ity stressincrease shells from3031 t 3.2735E-03 dt 1.08E-063031 t 3.27351-03 dt l*08E-06increase shells Fromincrease shells frumfileStl to891 toavi to8?1891891Ncnory required to process kej/uoi*d 407991input: nF d^tJi is eonplntHdMtiiiiurij reyuli'Bd lu be yin sulut lun : 410614Additional d^nanicallv allocated menary:9B89fatal:41970333^1 t 1.2735E-03 dt i f limb lz o bufferin it la 丄completed3247 t 3_5057E-03 dt 1.08E-06 d3plot File6 •定义零件位置点击Tools T Position Tools 宀Auto Position ,弹出Auto Posi。
对话框,上面的Master Tools 选择Blank,下面的Slave Tools 选择其他三个(注意三个都要选中),点击Apply,再点Close关闭。
点击Tools T Positio n Tools T Move Tools,弹出MoveTools 对话框,点击Pu nch,选中Y Tran slation ,Dista nee 中输入101.2,点击Apply 应用。
点击Bin der,选中Y Tran slation , Dista nee 中输入30,点击Apply应用,再点击OK确认。
7.分析点击Analysis T Analysis,将上方的Analysis Type 改为Full Run Dyna ,然后点击OK。
DA 歳件'耐料成21 \D>‘门rm\DVNA FO-1 石J sdyn^, exe8.处理结果3331 t 3.2735E-03五、实验小结:Dynaform软件是用虚拟制造技术进行塑性加工的,在成型过程中的虚拟仿真,可以在模具加工之前,检测模具关键工作部分形状和尺寸设计的合理性,分析材料的流动规律,预测是否产生裂纹,此外还可以对其他工艺参数进行优化分析。
此次实验,在课堂上老师已经演示过一遍,而且又派了一名同学演示,但是回到宿舍自己开始做的时候,还是发现有些细节比较模糊,于是上网查了有关Dynaform软件的使用细则,再结合本实验,最终还是一步一步地完成了塑性加工的模拟仿真,经过几小时的使用,终于在最后看到了上面“处理结果”的仿真,点击“ run”,塑性材料就被加工了。
通过此次实验,首先学到了Dyn aform软件,这一款新的软件的使用,并会利用Dynaform 软件进行数值模拟,特别是对塑性加工的模拟更加熟练;然后,经过自己的亲手操作,更加熟悉软件的使用,虽然其中出现了一些小问题,但发现自己以前对软件、对塑性变形的性能还是了解不够,通过解决问题,对这些知识的了解更加深入;最后,通过实验将课本和工程实际的应用相联系起来了。
今后应该更加多关注相关知识,并将课本知识和实践融合,放能更好地掌握知识。