光学视觉检测技术的尺寸测量
光学检测的综述
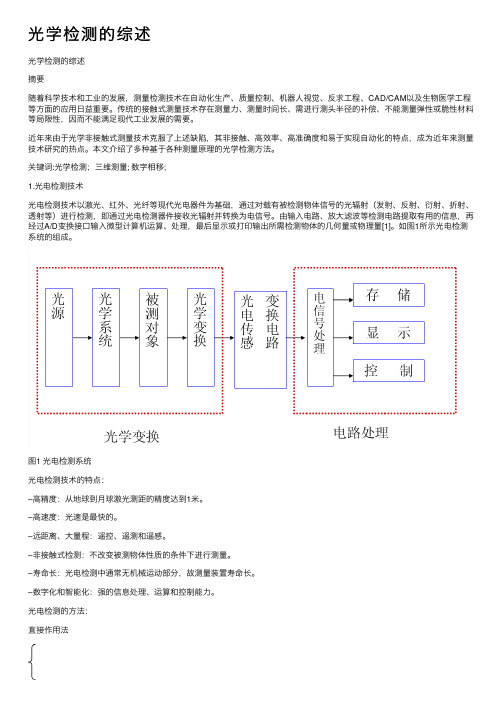
光学检测的综述光学检测的综述摘要随着科学技术和⼯业的发展,测量检测技术在⾃动化⽣产、质量控制、机器⼈视觉、反求⼯程、CAD/CAM以及⽣物医学⼯程等⽅⾯的应⽤⽇益重要。
传统的接触式测量技术存在测量⼒、测量时间长、需进⾏测头半径的补偿、不能测量弹性或脆性材料等局限性,因⽽不能满⾜现代⼯业发展的需要。
近年来由于光学⾮接触式测量技术克服了上述缺陷,其⾮接触、⾼效率、⾼准确度和易于实现⾃动化的特点,成为近年来测量技术研究的热点。
本⽂介绍了多种基于各种测量原理的光学检测⽅法。
关键词:光学检测;三维测量; 数字相移;1.光电检测技术光电检测技术以激光、红外、光纤等现代光电器件为基础,通过对载有被检测物体信号的光辐射(发射、反射、衍射、折射、透射等)进⾏检测,即通过光电检测器件接收光辐射并转换为电信号。
由输⼊电路、放⼤滤波等检测电路提取有⽤的信息,再经过A/D变换接⼝输⼊微型计算机运算、处理,最后显⽰或打印输出所需检测物体的⼏何量或物理量[1]。
如图1所⽰光电检测系统的组成。
图1 光电检测系统光电检测技术的特点:–⾼精度:从地球到⽉球激光测距的精度达到1⽶。
–⾼速度:光速是最快的。
–远距离、⼤量程:遥控、遥测和遥感。
–⾮接触式检测:不改变被测物体性质的条件下进⾏测量。
–寿命长:光电检测中通常⽆机械运动部分,故测量装置寿命长。
–数字化和智能化:强的信息处理、运算和控制能⼒。
光电检测的⽅法:直接作⽤法差动测量法补偿测量法脉冲测量法光电检测系统◆主动系统/被动系统(按信息光源分)–主动系统通过信息调制光源,或者光源发射的光受被测物体调制。
如图2所⽰图2 主动系统的组成框图–被动系统光信号来⾃被测物体的⾃发辐射。
如图3所⽰图3 被动系统的组成框图◆红外系统/可见光系统(按光源波长分)[2]–红外系统多⽤于军事,有⼤⽓窗⼝,需要特种探测器。
–可见光系统多⽤于民⽤◆点探测/⾯探测系统(按接受系统分)–⽤单元探测器接受⽬标的总辐射功率。
机器视觉技术在工业检测中的应用效果评估
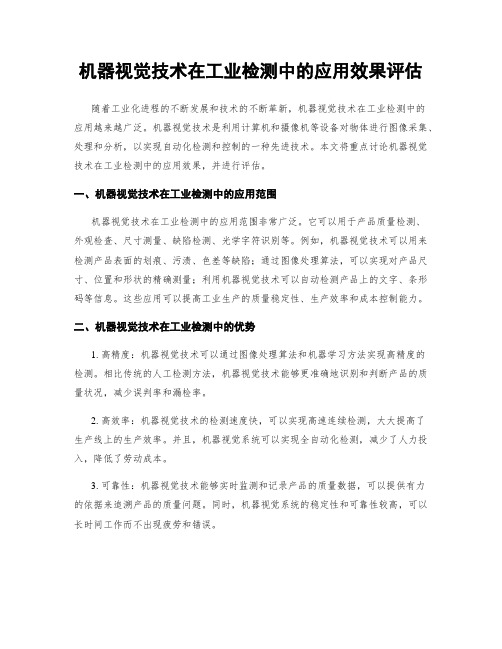
机器视觉技术在工业检测中的应用效果评估随着工业化进程的不断发展和技术的不断革新,机器视觉技术在工业检测中的应用越来越广泛。
机器视觉技术是利用计算机和摄像机等设备对物体进行图像采集、处理和分析,以实现自动化检测和控制的一种先进技术。
本文将重点讨论机器视觉技术在工业检测中的应用效果,并进行评估。
一、机器视觉技术在工业检测中的应用范围机器视觉技术在工业检测中的应用范围非常广泛。
它可以用于产品质量检测、外观检查、尺寸测量、缺陷检测、光学字符识别等。
例如,机器视觉技术可以用来检测产品表面的划痕、污渍、色差等缺陷;通过图像处理算法,可以实现对产品尺寸、位置和形状的精确测量;利用机器视觉技术可以自动检测产品上的文字、条形码等信息。
这些应用可以提高工业生产的质量稳定性、生产效率和成本控制能力。
二、机器视觉技术在工业检测中的优势1. 高精度:机器视觉技术可以通过图像处理算法和机器学习方法实现高精度的检测。
相比传统的人工检测方法,机器视觉技术能够更准确地识别和判断产品的质量状况,减少误判率和漏检率。
2. 高效率:机器视觉技术的检测速度快,可以实现高速连续检测,大大提高了生产线上的生产效率。
并且,机器视觉系统可以实现全自动化检测,减少了人力投入,降低了劳动成本。
3. 可靠性:机器视觉技术能够实时监测和记录产品的质量数据,可以提供有力的依据来追溯产品的质量问题。
同时,机器视觉系统的稳定性和可靠性较高,可以长时间工作而不出现疲劳和错误。
4. 自动化:机器视觉技术可以实现全自动化检测,可以在不间断的连续工作环境下进行检测。
机器视觉系统可以通过与其他自动化设备的配合,实现整个生产线的自动化控制和管理。
三、机器视觉技术在工业检测中的应用案例1. 产品质量检测:机器视觉技术可以用来检测产品表面的缺陷、损伤和变形等质量问题。
例如,利用机器视觉系统可以对电子产品的外观进行检测,包括检查产品外壳有无划痕、压痕等等。
2. 尺寸测量:机器视觉技术可以精确测量产品的尺寸和位置信息。
零件光学超精密加工检测技术
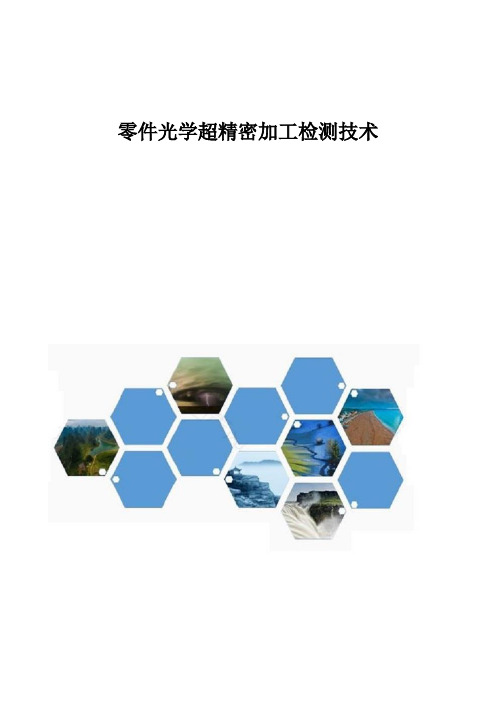
零件光学超精密加工检测技术摘要:随着数字数控机床和加工平台的产生与发展,机械零件的加工方式也向着大批量、专一化方向发展。
导致对机械零件的需求也逐渐加大,零件的尺寸和表面加工质量是否符合标准使用要求是影响机械零件正常工作的关键,因此,对机械零件的光学超精密检测成为主要研究任务。
机械零件表面的加工质量和尺寸大小虽然对零件的正常使用影响较低,但直接影响零件的可靠性、质量和使用寿命,而机械零件使用时间决定零件经济效益。
随着光学超精密加工技术的不断发展,零件光学超精密加工检测技术已成为超精密加工迫在眉睫的关键难题。
人工智能技术是一种新兴的用于模拟、延伸和扩展的智能理论、方法、技术及应用系统的一门新的技术科学。
人工智能技术中的机械学习法,使机械零件的光学超精密检测过程大大简化,并将操作结果保存在存储器中,便于后续光学超精密检测过程的快速执行。
关键词:光学检测;现状;发展引言单参数精密测量是精密测量中最简单的问题,近年来在复杂探测等问题中有了重要应用。
多参数精密测量复杂得多,参数之间存在精度制衡。
如何减少参数之间的精度制衡以实现多参数最优测量,是多参数精密测量的重要问题之一。
为了消除参数之间的精度制衡,研究人员将单参数测量实验中控制增强的次序测量技术应用到多参数测量中,通过调控测量系统动力学演化,完全解决了正演化算法中参数之间的精度制衡问题,实现了最优测量。
1测量系统将四组视觉传感器单元(包括CCD相机和激光器)分别竖直放置于精密零件两侧,垂直于精密零件中轴线,安装在精密零件两侧的立柱上;其中两组视觉传感器单元放置于精密零件一侧立柱上,另外两组视觉传感器单元放置于精密零件另一侧立柱上。
首先利用激光跟踪仪建立基坐标系统,然后对每个视觉传感器单元进行相机参数标定、光平面参数方程标定以及全局标定,最终得到相机的内参矩阵、相机到基坐标系下的全局标定矩阵以及激光平面在基坐标系下的平面方程,完成系统使用以及测量前的预处理。
探讨图像识别技术在机械零件质量检测中的运用

探讨图像识别技术在机械零件质量检测中的运用随着科技的不断发展,图像识别技术已经在多个领域得到了广泛的应用,其中就包括机械零件质量检测。
图像识别技术可以通过摄像头或光学传感器获取机械零件的图像信息,并利用人工智能、机器学习等算法对图像进行分析和识别,从而实现对机械零件质量的快速、精准检测。
本文将探讨图像识别技术在机械零件质量检测中的运用。
一、图像识别技术在机械零件质量检测中的优势1. 实时快速图像识别技术可以在极短的时间内对机械零件进行检测,从而实现实时快速的质量判定。
与传统的人工检测方式相比,图像识别技术大大提高了检测效率和速度,减少了人力成本和时间消耗。
2. 高精度精准通过机器学习和深度学习等技术,图像识别系统可以不断优化和提升识别准确度,实现对机械零件质量的高精度精准检测。
这对于一些微小的缺陷或异常情况,图像识别系统也可以进行准确的识别和判定,大大提升了检测的准确性。
3. 自动化智能图像识别技术可以实现对机械零件质量检测的自动化处理,减少了人为干扰和误判的可能性。
而且,图像识别系统还可以根据实际情况不断学习和优化,实现智能化的质量检测过程。
2. 尺寸偏差检测图像识别技术可以利用光学传感器进行机械零件尺寸的测量,实现对尺寸偏差的检测。
通过图像识别系统的算法分析,可以快速准确地判断出机械零件的尺寸是否合格,从而实现对尺寸偏差的自动化检测和判定。
3. 异物检测图像识别技术还可以对机械零件进行异物检测,如金属异物、异物颗粒等。
通过图像识别系统的分析和识别,可以实现对异物的快速检测和定位,提高了质检的全面性和准确性。
三、图像识别技术在机械零件质量检测中的发展趋势1. 深度学习技术的应用随着深度学习技术的不断发展,图像识别系统可以通过大量的数据训练和学习,从而提高对机械零件质量的识别准确度和稳定性。
深度学习技术将成为图像识别系统发展的重要方向,为机械零件质量检测提供更加精准和可靠的技术支持。
2. 多模态信息融合图像识别技术将逐渐向多模态信息融合的方向发展,不仅通过视觉信息进行质量检测,还可以结合声音、温度、震动等多种信息进行综合分析和判定。
视觉检测玻璃转盘 平面度测试方法

视觉检测玻璃转盘平面度测试方法
一、视觉检测玻璃转盘:
1、先用手改变转盘转动角度,每转动90度检测尺寸,用望远镜上检定各尺寸是否保持一致;
2、将玻璃转盘摆放平整在台子上,查看外观是否完整,尺寸是否精度可控;
3、用直尺测量转盘各边尺寸是否一致,检测转盘边角是否尖锐,有无锐利突起;
4、用比色计比较转盘的颜色是否过深过浅;
5、用手慢慢转动转盘,观察玻璃材料的均匀度和精细程度;
6、转盘转动时是否平稳,转动后有无变形、抖动或漏光等不良现象;
7、用手把玻璃转盘触摸,检测表面是否有锋利棱角,触摸后检查有无分离、脱落、折断等现象,情况严重者,及时更换。
二、平面度测试方法:
1、平行平面测试:使用接近水准仪和千分测量仪,用来测量平面的正确性,起到平衡的效果;
2、制程平面测试:采用数据采集系统和测量技术,用来测量平面的精度,以及检测产品的稳定性;
3、三角测量测试:使用变形计、三根同长尺或者三根正交杆来测量正六边形形状;
4、误差矩阵分析:利用计算机软件进行各项参数曲面测量,针对特定参数进行平面度方差分析;
5、抽样测试:一般抽取一定数量的样品发送到全自动坐标测量机上进行测量,通过数据统计,最终获得平面度的最终结果;
6、编码平面度测试:利用编码装置和直线光学采用进行绝对测量,检测平面度误差;
7、直线加工方法:使用视觉测量仪和自动加工机,来完成产品的自动直线加工,以获得更高精度的平面度效果。
无损检测技术中的光学检测方法详解

无损检测技术中的光学检测方法详解光学检测在无损检测技术中占据着重要的地位,它不仅能够快速准确地检测材料表面的缺陷,而且具有非破坏性的特点。
本文将详细介绍光学检测在无损检测中的应用及其原理。
光学检测方法主要包括视觉检测、红外热像检测和激光检测等。
其中,视觉检测是最常用的一种方法,通过人眼观察材料表面的变化来判断是否存在缺陷。
这种方法简单直观,适用于对表面缺陷进行初步检测,但对于微小缺陷的检测效果有限。
红外热像检测则利用物体发出的热能辐射来探测其表面的温度变化。
通过红外热像仪,可以将物体的表面温度转化为可见的图像,从而判断是否存在缺陷。
由于热像检测可以实时观测到物体的温度分布,因此可以非常准确地检测到潜在的缺陷。
激光检测是一种利用激光光源和光学传感器对材料进行扫描的方法。
通过测量激光的反射或散射,可以判断材料表面是否有缺陷。
激光检测具有高分辨率、高灵敏度和快速检测的特点,可以对微小缺陷进行准确的定位和识别。
除了以上几种方法,还有一些高级的光学检测技术,如照相测距法、摄影测距法、干扰法等。
这些方法利用光学原理和成像技术,对材料进行更加细致和精确的检测。
例如,照相测距法通过测量物体在两张照片上的位置差异来计算出物体的大小和形状。
摄影测距法则通过测量摄影图像中物体的像素大小来推测物体的实际大小。
干扰法则利用干涉现象来观察材料表面的微小变化,从而判断是否存在缺陷。
光学检测技术在无损检测中的应用非常广泛。
在制造业中,光学检测可以用来检测产品的外观缺陷、尺寸偏差和形状变化等。
在航空航天领域,光学检测可以用来检测飞机表面的裂纹和疲劳损伤。
在医学领域,光学检测可以用来检测人体表面的皮肤病变和眼睛疾病等。
在光学检测技术的发展过程中,还出现了一些新的技术和方法,如数字图像处理、光学成像和机器视觉等。
这些技术的应用使得光学检测更加智能化和自动化,大大提高了检测的准确性和效率。
总之,光学检测技术在无损检测中具备独特的优势,它能够快速准确地检测材料表面的缺陷,为生产和生活中的各个领域提供了重要的支持。
ecar和ocr检测流程简书
ecar和ocr检测流程简书
ECAR是一种车辆损伤评估系统,OCR则是一种光学字符识别技术。
这两种技术可以用于车辆事故处理和保险理赔中,以帮助鉴定车辆损伤和信息确认。
以下是ECAR和OCR的检测流程:
ECAR检测流程:
1. 视觉检查:检查车辆外观,包括外观损伤、漆面破损、车身变形等。
2. 尺寸测量:使用工具进行尺寸测量,确定车辆各个部位的变形程度。
3. 影像采集:通过拍摄照片或视频,采集车辆损伤、车内部件损坏等信息。
4. 损伤评估:结合视觉检查和尺寸测量结果,对车辆损伤进行评估和分类。
5. 生成报告:根据评估结果生成报告,包括车辆损伤照片、损伤评估结果等。
OCR检测流程:
1. 影像采集:使用摄像头或扫描仪等设备,将需要识别的文字信息拍摄或扫描下来。
2. 预处理:对采集的影像进行预处理,包括去除噪声、图像增强等。
3. 文字分割:将影像中的文字分割成单独的字符或单词,为后续识别做准备。
4. 字符识别:采用OCR识别技术,对影像中的字符进行识别,输出文字信息。
5. 结果校验:对识别结果进行校验,确保准确性和完整性。
6. 生成报告:根据识别结果生成报告,包括文字信息和影像信息等。
轴类检测说明方法
轴类检测说明方法
轴类检测是一种常见的质量检测方法,主要用于检测轴类产品的尺寸、形状、表面质量等方面的问题。
轴类产品广泛应用于机械、汽车、航空航天等领域,其质量的好坏直接影响到整个产品的性能和寿命。
因此,轴类检测显得尤为重要。
轴类检测的方法主要有以下几种:
1. 视觉检测法
视觉检测法是一种简单、直观的检测方法,通过肉眼观察轴类产品的表面质量、尺寸等方面的问题。
这种方法适用于一些简单的轴类产品,但对于一些复杂的轴类产品,视觉检测法的准确性和可靠性就会受到影响。
2. 量具检测法
量具检测法是一种常见的轴类检测方法,通过使用各种量具,如卡尺、游标卡尺、外径千分尺等,对轴类产品的尺寸进行测量。
这种方法准确性高,但需要专业的技术人员进行操作,且对于一些形状复杂的轴类产品,量具检测法的应用也会受到限制。
3. 光学检测法
光学检测法是一种高精度的轴类检测方法,通过使用光学仪器,如显微镜、投影仪等,对轴类产品的形状、表面质量等方面进行检测。
这种方法准确性高,且可以对形状复杂的轴类产品进行检测,但需要专业的技术人员进行操作,且设备价格较高。
4. 影像检测法
影像检测法是一种新兴的轴类检测方法,通过使用高清晰度的摄像机和图像处理软件,对轴类产品的尺寸、形状、表面质量等方面进行检测。
这种方法准确性高,且可以对形状复杂的轴类产品进行检测,且操作简单,但需要专业的技术人员进行操作,且设备价格较高。
轴类检测是一项非常重要的质量检测工作,其方法多种多样,需要根据具体的产品特点和检测要求选择合适的检测方法。
同时,需要专业的技术人员进行操作,以确保检测结果的准确性和可靠性。
钣金加工中的智能检测和测量技术
钣金加工中的智能检测和测量技术随着钣金加工行业的发展壮大,智能检测和测量技术也逐渐成为了一个重要的方向和趋势。
钣金加工行业涉及到的很多制造工艺都需要通过高精度的测量和检测技术来保证产品质量和工艺效率。
本文将着重介绍最新的智能检测和测量技术在钣金加工中的应用,包括光学测量、机器视觉、三维扫描等方面。
一、光学测量技术目前在钣金加工行业中应用较广的光学测量技术主要有两种:一种是激光投影仪测量,另一种是光栅测量。
激光投影仪是利用激光光束通过相机成像,根据三角测量原理测量任意平面上的二维尺寸与三维尺寸,精度可达到0.01mm。
在产品加工全过程中,利用激光投影仪对工件进行在线的实时检测,能够发现加工过程中的误差和偏差,并进行及时的校正和修正。
光栅测量主要利用光栅技术来测量工件表面的形状、曲率、平整度等参数。
通过将光线投射到工件表面上,测量表面反射的光线,便可得到工件表面的形状信息。
相比于传统的机械式测量方法,光栅测量具有非接触、高精度、高效率等优点,被广泛应用于各类高精度钣金加工中。
二、机器视觉技术在钣金加工行业中,机器视觉技术的应用范围非常广泛,涉及到自动化生产线上的工件检测、尺寸测量、缺陷检测等方面。
机器视觉技术参照了人类视觉的特点,通过自动光学检测、数字信号处理等技术手段,将图像信息转换成数字信号,并在此基础上进行尺寸测量和缺陷检测,可以达到较高水平的自动化控制效果。
机器视觉技术在钣金加工中的应用主要有两种:一种是基于二维图像处理的机器视觉技术,另一种是基于三维点云的机器视觉技术。
基于二维图像处理的机器视觉技术主要用于检测工件表面的形状、颜色、位置等参数,通过特定的算法和模型,实现对工件的自动检测和分类。
基于三维点云的机器视觉技术主要利用三维扫描仪获取工件表面的三维数据,以及相应的点云信息,通过计算和比对,实现对工件表面的高精度尺寸测量。
三、三维扫描技术当前,在钣金加工行业中应用最广泛的三维扫描技术主要有两种:一种是激光三维扫描技术,另一种是结构光三维扫描技术。
制造工艺中的精密测量与检测技术
制造工艺中的精密测量与检测技术在制造工艺中,精密测量与检测技术是非常重要的环节。
它可以确保产品的质量和性能达到要求,同时也有助于提高生产效率和降低成本。
本文将介绍几种常用的精密测量与检测技术,并探讨它们在制造工艺中的应用。
首先,光学测量技术是一种常见的精密测量方法。
它利用光的传播和反射原理,通过测量光的特性来获取目标物体的尺寸、形状和表面质量等信息。
例如,在机械零件加工过程中,可以使用光学测量技术来检测零件的平整度、圆度和直线度等参数,从而确保零件的加工精度达到要求。
其次,电子测量技术也是一种常用的精密测量方法。
它利用电子信号的传输、转换和处理来实现对目标物体的测量。
电子测量技术广泛应用于电子设备、通信设备和汽车等行业。
例如,在半导体制造过程中,可以使用电子测量技术来检测芯片的电性能参数,如电压、电流和频率等,从而确保芯片的质量和性能稳定可靠。
另外,机器视觉技术也是一种常用的精密测量技术。
它利用计算机图像处理和分析技术来获取目标物体的图像信息,并通过比较和匹配来实现对目标物体的测量和检测。
机器视觉技术广泛应用于自动化制造和品质检测等领域。
例如,在汽车制造过程中,可以使用机器视觉技术来检测汽车零件的外观缺陷和尺寸偏差等问题,从而提高产品质量和工作效率。
此外,激光测量技术也是一种常用的精密测量方法。
它利用激光束的特性来实现对目标物体的高精度测量。
激光测量技术广泛应用于制造工艺中的尺寸测量、位移测量和形状测量等方面。
例如,在航空航天领域,可以使用激光测量技术来检测飞机外壳的变形和表面缺陷,以确保飞机的飞行安全。
总之,精密测量与检测技术在制造工艺中起着至关重要的作用。
它能够帮助制造商实现对产品质量和性能的精确控制,从而提高产品的市场竞争力。
在未来,随着科技的进步和创新,精密测量与检测技术将不断发展和完善,为制造业的发展做出更大的贡献。
- 1、下载文档前请自行甄别文档内容的完整性,平台不提供额外的编辑、内容补充、找答案等附加服务。
- 2、"仅部分预览"的文档,不可在线预览部分如存在完整性等问题,可反馈申请退款(可完整预览的文档不适用该条件!)。
- 3、如文档侵犯您的权益,请联系客服反馈,我们会尽快为您处理(人工客服工作时间:9:00-18:30)。
光学视觉检测技术的尺寸测量
机器视觉检测系统的优势主要体现在,非接触检测测量、长时间稳定工作等,利用机器视觉解决方案,可以节省大量劳动力资源,为公司带来可观利益,因此其应用也越来越广泛。
机器视觉系统具有测量功能,能够自动测量产品的外观尺寸,比如外形轮廓、孔径、高度、面积等尺寸的测量。
尺寸测量无论是在产品的生产过程中,还是产品生产完成后的质量检验中都是必不可少的步骤,而机器视觉在尺寸测量方面有其独特的技术优势。
比如,这种非接触测量方法既可以避免对被测对象的损坏又适合被测对象不可接触的情况,如高温、高压、流体、环境危险等场合;同时机器视觉系统可以同时对多个尺寸一起测量,实现了测量工作的快速完成,适于在线测量;而对于微小尺寸的测量又是机器视觉系统的长处,它可以利用高倍镜头放大被测对象,使得测量精度达到微米以上。
机器视觉之尺寸测量是基于相对测量法,通过溯源、倍率标定、自动提边和屏幕图像测量来推算出实物大小。
在精密测量中,倍率要求35*以上以获得微米级精度,此时的视觉线宽度不到5mm,对于测量5mm以上的物件需要移位解析读数与视窗测量合成来完成。
对于微小尺寸的精密测量,利用机器视觉系统通过安装高倍工业镜头或显微镜头,从微小的生物细胞直径、数量,到细小的装配缝隙大小,再到较小的机械零件、电子产品的尺寸测量等各个领域都是机器视觉系统的用武之地。
虽然实现尺寸测量的方法很多,但大多数测量重复性、高效性和鲁棒性不高。
事实表明,基于机器视觉技术的尺寸测量具有良好的连续性和高精度,大大提高了工业在线测量的实时性和准确性,同时生产效率和产品质量控制也得到明显提升。