基于机器视觉的零件尺寸测量系统设计
基于机器视觉的微小型零件测量与装配控制

wa e sr cu e h v ey g o e sb lt o a u e nta d a s mb y o n au e p rs r tu t r a e v r o d f a i iiy f rme s r me n se l fmi it r — a . t Ke wo ds: n au e p rs;ma h n iin;pr cs s e l y r mi it r a t c i e v so e ie a s mb y;a tmai a u e n u o tc me s r me t
g er g D l nU ie i f eh o g , ai l6 2 , hn ) i ei , aa n r t o T cnl y D a 0 4 C ia n n i v sy o l n1
Ab t ac : e di nso s o n a u e p rsd fe r a l r s l n n lw f ce c u i g ma u la s mb y a d s r t Th me i n fmii t r a t ifr g e t y e u t g i o e i n y d r n a s e l n i i n
.
i s e u f e a d t e d va i s o me s s ae s me o e u c r n fc o st a f t h s e l r c s f ih d s r c n h e i t n f i n in r o f h n e t i a tr h t f c e a s mbv D o e s n a o d o t a ae t
由精密微小型驱动元件 、 传感元件等组成的器 件或产品 , 以其体积小、 性能可靠 等特点 , 近年来 在 工业 、 军事 、 生物领域得到广泛应用 , 该类产 品往往 不能一次加工完成 , 一般 由微小型零件组装而成 . 微
基于机器视觉的机械零部件尺寸测量技术研究

基于机器视觉的机械零部件尺寸测量技术研究导言近年来,随着机械工业的不断发展,对机械零部件尺寸测量技术的要求也越来越高。
传统的人工测量虽然能够满足一定的需求,但其存在的主观性和不稳定性仍然是主要问题。
为了解决这一问题,基于机器视觉的机械零部件尺寸测量技术应运而生。
本文将探讨基于机器视觉的机械零部件尺寸测量技术的研究现状和未来发展趋势。
一、技术原理基于机器视觉的机械零部件尺寸测量技术是利用计算机和摄像设备对机械零部件进行图像采集和处理,通过图像处理算法获取零部件的尺寸信息。
其技术原理主要分为图像采集、图像处理和尺寸测量三个步骤。
图像采集是基于机器视觉的机械零部件尺寸测量技术的第一步。
通过高分辨率摄像设备对机械零部件进行拍摄,获取清晰的图像。
高分辨率的摄像设备能够提供更多的图像信息,有助于提高尺寸测量的准确性。
图像处理是基于机器视觉的机械零部件尺寸测量技术的核心步骤。
通过图像处理算法对采集到的图像进行分析和处理,去除图像中的噪声和干扰,提取出零部件的边缘特征。
常用的图像处理算法包括边缘检测、二值化、轮廓提取等。
尺寸测量是基于机器视觉的机械零部件尺寸测量技术的最终目标。
通过对图像处理后的图像数据进行尺寸计算,得到机械零部件的尺寸信息。
常用的尺寸测量方法包括长度测量、宽度测量、直径测量等。
二、研究现状基于机器视觉的机械零部件尺寸测量技术已经在工业领域得到广泛应用。
目前,研究人员主要集中在算法改进、设备优化和测量系统的智能化方面进行研究。
在算法改进方面,研究人员提出了许多新的图像处理算法和尺寸测量方法。
例如,基于边缘检测和霍夫变换的尺寸测量方法可以提高测量的准确性和稳定性。
另外,利用深度学习技术进行图像处理和尺寸测量也成为研究热点。
这些算法的出现极大地推动了基于机器视觉的机械零部件尺寸测量技术的发展。
在设备优化方面,研究人员致力于提高摄像设备的性能和精度。
高分辨率、高帧率的摄像设备能够提供更多的图像信息,从而提高尺寸测量的准确性。
基于机器视觉的微米级2D零件自动检测系统

2 5 (0 0 0 5 0万 ) 像素 。
( ) 机 :i2 0 —7 m( 国 b s r 1相 pA 4 01 g 德 al ) e
主要 参 数如 下 , 辨率 5 0万 ( 4 8×2 5 ) 芯 分 0 24 00 , 片 :oy I X 2 , 行 C D, 面 尺 寸 : / ”( = Sn C 6 5 逐 C 靶 23 W 8 8 m, 6 6 m) 像 素 尺寸 :. 5 . r H= . m a , 3 4 m× . 5 3 4 m。 () 2 镜头 镜 头 选 用 日本 C mp t A 工 业 自动 化 镜 头 o ua F r ( 0 8 MP , 格 为 2 3 , 传 感 器 相 配 。焦 距 M5 1 一 ) 规 / ” 和 5 mm, 圈 1 81 C, 平 视角 1 . 。 0 光 . —6 水 05 。 视 场大 小及 镜头 到 被 摄取 物 体 的距 离 的计 算 如
a u tt @ h t i. O 。 t ioo oma[ C r n
21 0 2年 9月
赵 文辉 , : 于机 器视 觉 的微 米级 2 等 基 D零 件 自动检 测 系统
・ 3・ 5
理, 提取测 量 对象 的几 何 信 息 , 合 光 学 系统 的变 换 结
特 性 , 算 出 被 测 尺 寸 。 计
第 9期 21 0 2年 9月
组 合 机 床 与 自 动 化 加 工 技 术
M o ul r M a h ne To l& Aut m a i a f c u i g Te hn qu d a c i o o tc M nu a t r n c i e
No. 9 Se p.2 2 01
线缆 进行 快 速 图像 传 输 , 能 在 不 同厂 商 的 软 、 件 还 硬
基于机器视觉的零部件尺寸检测技术
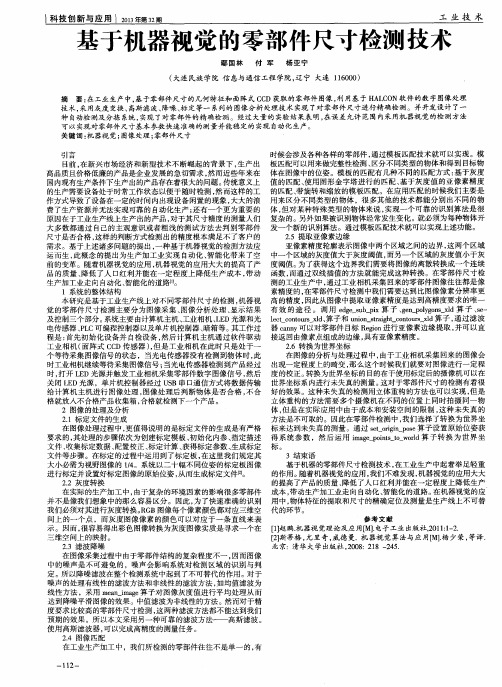
工 业 技 术
基 于机器视 觉 的零部 件尺寸检测 技术
鄢 国 林 付 军 杨 亚 宁
( 大连民族 学院 信 息与通信工程学院, 辽宁 大连 1 1 6 0 0 0 )
摘 要: 在 工业 生 产 中 , 基 于零 部 件尺 寸 的 几何 特征 和 面 阵 式 C C D获取 的零部 件 图像 , 利 用基 于 H A L C O N软 件 的数 字 图像 处理 技术, 采 用灰度 变换、 高斯滤波、 降噪、 标定等一 系列的图像分析处理技术 实现 了对零部件尺寸进行精确检测 。并开发设计 了一 种 自动 检 测及 分拣 系统 , 实现 了对 零部 件 的 精确 检 测 。 经过 大量 的 实验 结 果表 明 , 在误 差允 许 范 围 内采 用机 器视 觉 的检 测 方 法 可 以 实现 对零 部 件尺 寸基 本 参数 快 速 准确 的 测量 并 能稳 定 的 实现 自动 化 生产 。 关键 词 : 机 器视 觉 ; 图像 处 理 ; 零部 件 尺 寸 时候会 涉 及 各种 各 样 的零 部 件 , 通过 模 板 匹 配技 术 就 可 以实 现 。模 区分不同类型 的物体 和得到 目标物 目前 , 在新兴市场经济和新型技术不 断崛起 的背景下 , 生产出 板匹配可 以用来做完整性检测 、 基于灰度 高品质且价格低廉 的产品是企业发展的急切需求 , 然而近些年来在 体在图像 中的位姿 。模板的匹配有几种不同的匹配方式 : 使用 图形金字塔进行 的匹配 、 基于灰度值 的亚像素精度 国内现有生产条件下生产出的产品存在着很大的问题。 传统意义上 值 的匹配 、 带旋转和缩放的模板匹配 。在应用匹配 的时候我们主要是 的生产需要设备处于时常工作状态以便于随时检测 , 然而这样 的工 的匹配 、 作方式导致了设备在一定的时间内出现设备闲置 的现象 , 大大 的浪 用来区分不 同类型的物体 ,很多其他 的技术都能分别出不同的物 但 对某 种 特 殊 类 型 的 物体 来 说 , 实 现一 个 可 靠 的 识 别 算 法 是 很 费了生产资源并无法实现可靠的 自动化生产 ; 还有一个更为重要的 体 , 另 外 如果 被识 别 物体 经 常 发生 变化 。 就 必 须 为每 种 物体 开 原因在于工业生产线上生产出的产品 , 对于其尺寸精度 的测量人们 复 杂 的 。 大 多 数 都 通 过 自己 的主 观 意识 或 者 粗 浅 的 测试 方 法 去 判 别 零 部 件 发一个新的识别算法。通过模板匹配技术就可以实现上述功能。 2 . 5 提取 亚 像 素边 缘 尺寸是否合格 , 这样的判断方式检测出的精度根本满足不了客户的 需 求 。基 于上 述 诸 多 问题 的提 出 , 一 种 基 于机 器 视觉 的检 测 方法 应 亚像素精度轮廓表示 图像 中两个 区域之间的边界 , 这两个 区域 而另 一 个 区域 的灰 度 值小 于灰 运而生 , 此概念 的提出为生产加工业实现 自动化 、 智 能化带来 了空 中一个 区域 的灰度 值 大 于灰 度 阈 值 , 为了获得这个边界我们需要将图像的离散转换成一个连续 前的变革 。随着机器视觉的应用 , 机器视觉 的应用大大 的提高了产 度阈值 。 品的质量 、 降低 了人 口红利并能在一定程度上 降低生产成本 , 带动 函数 , 而通过双线插值的方法就能完成这种转换 。在零部件尺寸检 测 的工 业 生产 中 , 通 过工 业 相机 采 集 回来 的零 部件 图像 往 往都 是 像 生 产 加工 业 走 向 自动化 、 智 能化 的道路 【 1 】 。 1系 统 的整 体结 构 素精度 的, 在零部件尺寸检测中我们需要达到 比图像像素分辨率更 因此从 图像 中提取亚像素精度是达到高精度要求的唯一 本研 究是 基 于 工业 生 产线 上 对 不 同零 部 件 尺 寸 的检 测 , 机 器视 高 的精度 , 觉 的零 部 件 尺 寸检 测 主 要 分 为 图像 采 集 、 图像 分 析 处 理 、 显 示 结 果 有 效 的途 径 。调 用 e d g e _ s u b _ p i x算 子 、 g e n _ p o l y g o n s _ x l d算 子 、 s e — e c t co nt our s x 及 控 制 三个 部 分 。 系 统主 要 由计 算机 主 机 、 工业 相 机 、 L E D光 源 和光 l l d 、 算子和 u n i o n _ s t r a i g h t _ c o n t o u r s _ x l d 算子, 通过滤波 a n n y 可 以对 零 部件 目标 R e g i o n进行 亚 像 素边 缘 提 取 , 并 可 以直 电传感器 、 P L C可编程控制器以及单片机控制器 、 暗箱等 。 其工作过 器 c 程是 : 首先初始化设备并 自检设备 , 然后计算机主机通过软件驱动 接返回由像素点组成的边缘 , 具有亚像素精度 。 工业相机 ( 面阵式 C C D传 感 器 ) , 但 是 工 业 相 机 在 此 时 只 是处 于一 2 . 6 转换 为世 界 坐标 个等待采集图像信号的状态 ,当光 电传感器没有检测到物体 时, 此 在图像的分析与处理过程 中, 由于工业相机采集回来 的图像会 那 么 这个 时 候 我们 就 要 对 图像 进 行 一 定程 时工业相机继续等待采集图像信号 ; 当光 电传感器检测到产品经过 出现 一定 程 度上 的 畸变 , 转 换 为世 界 坐标 的 目的在 于使 用标 定 后 的摄 像机 可 以 在 时, 打开 L E D光源并触发工业相机采集零部件数字图像 信号 , 然后 度 的校 正 。 关闭L E D光源,单片机控制器经过 U S B串口通信方式将数据传输 世界坐标系 内进行未失真的测量。 这对于零部件尺寸的检测有着很 但是 给计算机 主机进行图像处理 , 图像处理后判断物体是否合格 , 不合 好 的效果 。这种未失真的检测用立体重构 的方法 也可 以实现, 格就放入不合格产 品收集箱 , 合格就检测下一个产品。 立 体 重 构 的方 法需 要 多 个 摄像 机在 不 同的 位 置 上 同 时拍 摄 同一 物 2 图像 的 处理 及分 析 体, 但是在实 际应用中由于成本和安装空 间的限制 , 这种未失 真的 2 . 1标 定文 件 的 生成 方法是不可取的。因此在零部件检测 中, 我们选择 了转换 为世界坐 在图像处理过程 中, 更值得说明的是标定文件 的生成是有严格 标来达到未失真的测量。通过 s e t o r i g i n p o s e 算子设置原始位姿获 m a g e — p o i n t s _ t o _ w o r l d算 子 转 换 为 世 界 坐 要求 的, 其处理 的步骤依次为创建标定模板 、 初始化内参 、 指定描述 得 系 统 参 数 ,然 后 运 用 i 文件、 收集 标定 数 据 、 配 置校 正 、 标 定 计算 、 获得 标 定参 数 、 生成 标 定 标 。 文件 等 步 骤 。在标 定 的 过程 中运 用 到 了标定 板 , 在这 里 我 们规 定 其 3结 束 语 大 小必 需 为视 野 图像 的 1 / 4 。系统 以二 十 幅不 同位 姿 的标 定板 图像 基 于机 器 的零 部件 尺寸 检测 技 术 , 在 工 业 生产 中起着 举 足 轻重 的作 用 。 随着 机 器 视觉 的应 用 , 我 们不 难 发 现 , 机 器 视觉 的应 用 大 大 进 行标 定 并设 置好 标 定 文件 目 。 2 . 2 灰 度转 换 的提高了产 品的质量 、 降低了人 口红利并能在一定程度上降低生产 在实际的生产加工中 , 由于复杂的环境 因素的影 响很多零部件 成 本 , 带 动 生产 加 工业 走 向 自动 化 、 智 能 化 的道 路 。 在机 器 视觉 的应 物体特征 的提取和尺寸的精确定位及测量是生产线上不可替 并不是像我们想象中的那么容易 区分。因此 , 为了快速准确的识别 用中, 我们必须对其进行灰度转换 。 R G B图像每个像素颜色都对应三维空 代 的环 节 。 参 考 文献 间上的一个点 ,而灰度图像像素 的颜色可以对应 于一条直线来表 示。因而 , 很容易得出彩色 图像转换为灰度 图像实质是寻求一个在 [ 1 】 赵鹏. 机 器视 觉理 论及 应 用[ M 】 . 电子 工业 出版 社 , 2 0 1 1 : 1 — 2 . 三 维空 间 上 的映 射 。 [ 2 】 斯蒂格 , 尤里奇 , 威德曼. 机器视觉算, a - -  ̄应 用[ MI . 杨少荣, 等译 2 - 3滤波降噪 北京: 清 华 大学 出版社 , 2 0 0 8 : 2 1 8— 2 4 5 . 在 图像采集过程 中由于零部件结构 的复杂程度不一 , 因而图像 中的 噪 声是 不可 避 免 的 ,噪声 会 影 响 系 统 对检 测 区域 的识 别 与判 定。 所以降噪滤波在整个检测系统 中起 到了不可替代的作用 。对于 噪 声 的处 理 有线 性 的滤 波 方法 和 非 线性 的滤 波方 法 , 如 均 值 滤 波为 线性方法 ,采用 m e a n _ i m a g e 算子对 图像灰度值进行平均处理从而 达到降噪平滑图像 的效果 。中值滤波为非线性的方法。然而对于精 度要求 比较高的零部件尺寸检测 , 这两种滤波方法都不能达到我们 预 期 的效 ��
基于机器视觉的端子尺寸检测系统

0引言
机器视觉( M a c h i n e v i s i o n ) 是研究用计算机来模
拟 生 物外 显 或 宏 观 视觉 功 能 的科 学 和技 术 ,用 摄
时间要能够和整个生产线 的生产周期的要求。
1 系统工作原理
端子 尺寸 检测 系统 由 C C D传 感 器 、光 学 系
像机( 即图像摄取装置 ,分 C M O S 和C C D 两种) 和计
算机等ห้องสมุดไป่ตู้器代替人眼对 目标进行测量 、跟踪和识 别 ,并加 以判断 。用图像来创建和恢复现实世界 模 型 ,最终用于实际检测 、测量和控制 。简单地 说 ,机器 视觉可 以理解 成 给机器 加装 上视觉 装 置 ,或 者 是 加 装 有 视觉 装 置 的机 器 ,就 是 用 机 器 代 替人 眼来做测量和判断 。给机器加装视觉装置 的 目的 ,是为 了使机器具有类似于人类 的视觉功 能 ,从而提高机器的自动化和智能化程度u 。 端子零件作为连接件 ,在汽车电子产 品领域 大量使用 ,然后 由于金属端子 的厚度很 薄 ,在接 触力 的作用下 回产生大 的变形 ,从 而产生很大的 检测误差 ,所 以只能采用非接触的检测方法进行
L E I Mi n — h u a ,C HE N L i a n g 2
( 1 . Gu a n g z h o u O TI S El e v a t o r Co . ,L t d, Gu a n g z h o u 51 0 4 2 5, C h i n a; 2 . Ha n g z h o u Wa n x i a n g P o l y t e c h n i c ,
基于双目视觉的机械零件位姿检测系统研究

算法实现:使用编 程语言实现算法, 并进行测试和验证
算法评估:对算法 进行评估,比较与 其他算法的优劣
测试目的:验证机械零件位姿 检测系统的准确性和可靠性
测试环境:实验室和实际生产 线
测试方法:对比实验、重复测 试和异常测试
测试结果:高准确率和低误差 率
相机标定是确定相机内 部参数和外部参数的过 程,通过标定可以获得 相机的高精度模型。
双目立体标定:确定左右相机之间的相对位置和姿态,以及基线距离等参数
优化算法:采用优化算法对标定结果进行优化,提高标定精度
优化算法:采用先进的优化算法,提高标定精度和速度 参数调整:根据实际情况调整相机参数和标定板规格,提高标定效果 多视角标定:采用多视角标定方法,提高标定结果的稳定性和可靠性 实践应用:将双目视觉系统应用于实际生产中,不断优化和改进系统性能
常见的相机标定方法包括 张氏标定法、两步法等, 这些方法都需要使用已知 尺寸和位置的标定板作为 参照物。
相机标定的精度直接影 响到双目视觉系统的测 量精度,因此需要进行 高精度的相机标定。
在进行相机标定时,需 要注意消除相机的畸变, 以提高标定精度和双目 视觉系统的测量精度。
相机内参标定:确定相机内部参数,如焦距、光心等 相机外参标定:确定相机相对于标定物的位置和姿态
触、低成本
挑战:光照条 件、目标遮挡、 复杂背景、实
时性
硬件部分:包 括双目视觉相 机、机械零件、
标定板等
软件部分:包 括图像采集、 预处理、特征 提取、位姿计
算等模块
算法部分:采 用基于特征匹 配的位姿计算 方法,实现机 械零件的位姿
检测
应用部分:将 位姿检测结果 应用于机械零 件的自动化装 配和质量控制
基于机器视觉的复杂零件外观尺寸检测
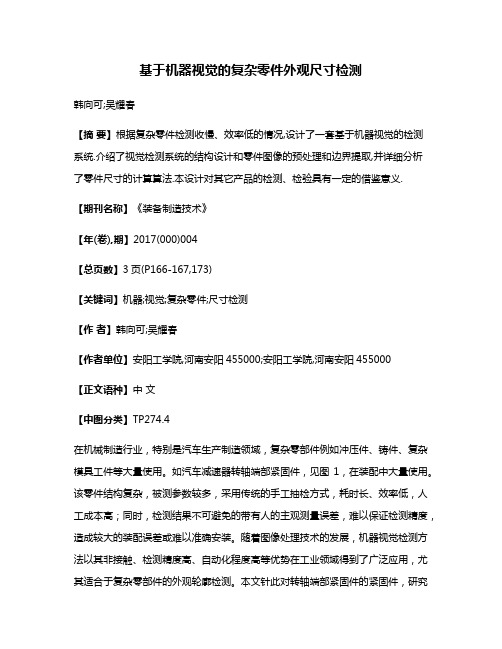
基于机器视觉的复杂零件外观尺寸检测韩向可;吴耀春【摘要】根据复杂零件检测收慢、效率低的情况,设计了一套基于机器视觉的检测系统.介绍了视觉检测系统的结构设计和零件图像的预处理和边界提取,并详细分析了零件尺寸的计算算法.本设计对其它产品的检测、检验具有一定的借鉴意义.【期刊名称】《装备制造技术》【年(卷),期】2017(000)004【总页数】3页(P166-167,173)【关键词】机器;视觉;复杂零件;尺寸检测【作者】韩向可;吴耀春【作者单位】安阳工学院,河南安阳455000;安阳工学院,河南安阳455000【正文语种】中文【中图分类】TP274.4在机械制造行业,特别是汽车生产制造领域,复杂零部件例如冲压件、铸件、复杂模具工件等大量使用。
如汽车减速器转轴端部紧固件,见图1,在装配中大量使用。
该零件结构复杂,被测参数较多,采用传统的手工抽检方式,耗时长、效率低,人工成本高;同时,检测结果不可避免的带有人的主观测量误差,难以保证检测精度,造成较大的装配误差或难以准确安装。
随着图像处理技术的发展,机器视觉检测方法以其非接触、检测精度高、自动化程度高等优势在工业领域得到了广泛应用,尤其适合于复杂零部件的外观轮廓检测。
本文针此对转轴端部紧固件的紧固件,研究分析了其外观轮廓尺寸的机器视觉检测方法。
视觉检测硬件系统如图2所示,它由工件检测平台、光源系统、CCD相机、图像采集卡、计算机、系统软件等组成[1]。
其中光源系统包括光源控制器和LED,可根据工作环境调整光照亮度。
软件系统采用Visual C++开发,用于采集到的图像处理、显示和尺寸检测等。
系统工作原理:当工件平放在检测台时,按下检测按钮,由CCD相机进行图像采集,通过软件系统对图像进行分析,在计算机上显示出被测工件轮廓尺寸和偏差等信息。
在检测系统的设计中,关键是软件系统的设计。
在计算机图像处理中主要由噪声去除、图像边界轮廓提取、尺寸计算、结果显示等部分组成[2]。
基于机器视觉的零件尺寸检测与测量

基于机器视觉的零件尺寸检测与测量导语:随着制造业的快速发展,零件的精确尺寸检测与测量成为了生产过程中的关键环节。
传统的尺寸检测方法往往需要人工参与,并且效率低下且不够精确。
而基于机器视觉的零件尺寸检测与测量则提供了一种快速、准确且可靠的解决方案。
一、机器视觉技术在零件尺寸检测中的应用随着机器视觉技术的迅猛发展,其在零件尺寸检测方面的应用也逐渐成为一种趋势。
机器视觉系统能够通过摄像机获取零件的影像信息,并通过图像处理算法来实现尺寸的检测与测量。
这种非接触式的测量方式在一定程度上消除了人为因素对结果的影响,大大提高了测量的准确性。
二、基于机器视觉的零件尺寸检测与测量的优势1. 自动化:基于机器视觉的零件尺寸检测与测量可以实现自动化,无需人工操作,从而提高了生产效率。
2. 高精度:机器视觉系统通过高分辨率的摄像机和精确的算法,能够实现对零件尺寸的亚毫米级别的准确度。
3. 实时监控:机器视觉系统可以实时监控零件的尺寸变化,及时发现生产过程中的异常情况并进行调整,提高了生产质量。
4. 多样性:基于机器视觉的零件尺寸检测与测量可以适用于不同形状、大小和材质的零件,具有较大的适应性。
三、基于机器视觉的零件尺寸检测与测量的实施步骤1. 系统设计:根据具体的生产需求,设计适合的机器视觉系统,包括选择合适的摄像机、光源和图像处理算法。
2. 数据采集:通过摄像机采集零件的图像数据,并传输至图像处理系统进行处理。
3. 图像处理:通过图像处理算法对采集到的图像进行处理,提取出零件的特征与边界,并计算出其尺寸。
4. 尺寸分析:根据所得到的尺寸数据进行分析,判断是否符合要求,并生成结果报告。
5. 反馈控制:根据分析结果,及时反馈给生产线控制系统,进行相应的调整和控制,确保生产过程的稳定性。
四、机器视觉技术在零件尺寸检测中的挑战与解决方案1. 光照条件:不同的光照条件可能对图像质量产生影响,需要选择适当的光源和光照方式,或者采用图像增强算法进行处理。
- 1、下载文档前请自行甄别文档内容的完整性,平台不提供额外的编辑、内容补充、找答案等附加服务。
- 2、"仅部分预览"的文档,不可在线预览部分如存在完整性等问题,可反馈申请退款(可完整预览的文档不适用该条件!)。
- 3、如文档侵犯您的权益,请联系客服反馈,我们会尽快为您处理(人工客服工作时间:9:00-18:30)。
基于机器视觉的零件尺寸测量系统设计
作者:王保军
来源:《电子技术与软件工程》2017年第04期
摘要设计了一套基于机器视觉的零件尺寸在线测量系统。
完成了硬件设备的选型和平台的搭建;采用Matlab语言实现了图像处理算法;采用Matlab GUI完成了测量系统软件的设计。
实验结果表明:测量系统的测量精度可以达到2um以下,满足零件尺寸在线检测要求,具有很好的应用前景。
【关键词】机器视觉 Matlab 图像处理尺寸测量
在工业生产中,测量是进行质量管理的手段,是贯彻质量标准的技术保证。
机械零件的尺寸检测作为产品加工的一个关键环节,其检测结果不仅影响产品的质量,而且对后续零件的再加工和装配产生决定性的作用。
目前,常规的零件尺寸测量手段主要采用游标卡尺、激光测量仪和轮廓仪等完成检测环节。
以上零件尺寸测量方法要么受测量工具限制,其测量精度有限;要么检测仪器过于昂贵且操作复杂,同时其准确率往往受人为因素的影响。
鉴于当前机器视觉技术的快速发展以及其在工业检测方面的成功应用,论文构想利用摄像机替代人眼,让计算机替代人脑,从而研制出一套针对零件常规尺寸的自动化测量系统。
1 系统概述
在充分遵循系统的完整性、可靠性、经济性和实时性等原则的基础上,本文设计出了一套基于机器视觉的零件常规尺寸测量系统。
该测量系统主要由图像摄取、图像处理、图像特征提取和分析、图像常规尺寸测量和结果输出几部分组成。
其工作原理图如图1所示。
2 硬件设计
基于机器视觉的零件常规尺寸测量系统的硬件主要包括:照明装置、摄像机、计算机和透明工作台。
各部件的主要功能是:照明装置主要为零件图像采集提供合适的光照环境;摄像机用来采集零件数字图像并传送到计算机,然后保存为相应图片格式;计算机通过系统软件实现对零件图像的预处理、边界提取、特征提取、相机标定和常规尺寸计算;透明工作台用来承载被测零件。
3 算法设计
图像处理算法对机器视觉测量系统会产生决定性的影响。
为了能满足零件尺寸测量的要求,针对零件产品图像的特点,我们设计了一套合理的图像处理算法流程。
其流程图如图2所示。
首先对获取的零件图像进行预处理,包括图像灰度化、图像去噪、图像分割和边界提取;然后提取零件的几何特征;最后通过对系统的标定,实现了零件图像常规尺寸的测量和结果显示。
3.1 图像预处理
3.1.1 图像灰度化
经过摄像机采集到的零件图像是24位真彩色RGB图像,该图像中的每个像素由R、G、B三个分量决定,而灰度图像的每个像素由一个值确定。
为了减少后续操作过程中的计算量,需要对采集到的零件图像进行灰度化处理。
3.1.2 图像去噪
采集系统获取的待检零件图像由于受照明程度、环境温度、电源变化、电磁辐射和振动等随机因素的干扰,图像会包含大量的噪声,表现为图像模糊、失真和大量斑点等。
为了消除和抑制噪声对零件图像后续处理的影响,必须对图像进行滤波处理。
由于中值滤波既能消除噪声又能保持图像的细节,符合本系统检测的需求。
3.1.3 图像分割
在所采集到的零件图像中,我们只对零件区域本身感兴趣,对于图像中的其他要素则要尽量消除。
图像分割就是指把图像分成各具特性的区域,并提取出感兴趣目标的技术和过程。
经过大量的实验验证,本文采用迭代阈值分割法实现对零件图像的分割,达到了预期的处理效果。
3.1.4 边界提取
轮廓是对物体形状的有力描述,对图像分析和识别十分有用,而通过边界提取算法就可以得到物体的边界轮廓。
目标图像边界提取的方法很多,主要包括链码表示法、标记图法以及多边形近似法等。
论文采用8连通链码法对待测零件进行了边界提取,为后续零件尺寸的检测奠定了很好的基础。
3.2 图像分析
3.2.1 特征检测
要测量零件的尺寸,首先应该检测出零件所包含的直线和圆等基本的几何特征。
目前常用的几何特征检测方法有Hough变换法、拟合法和模板匹配法等。
本文采用最小二乘法实现了对直线和圆的拟合,其拟合具体过程如下:
(1)采用最小二乘法实现对直线的拟合。
(2)采用最小二乘法实现对圆和圆弧的拟合。
采用最小二乘法对圆和圆弧的拟合过程与直线的拟合求解过程类似。
设所求拟合圆的方程为:。
根据最小二乘法应满足的条件,可以求出拟合圆的三个参数:u、v和r。
这样,通过基于最小二乘法的直线和圆拟合方法,可以顺利检测到直线和圆弧几何特征,为后续零件尺寸的测量奠定了基础。
3.2.2 系统的标定
相机拍摄到的图像是以像素为单位的,要得到待检零件的实际尺寸,需要将像素尺寸转换为长度尺寸,这个过程称为系统的标定。
本文使用0级精度量块,采用二次标定法实现了对系统的标定过程。
被测零件的实际尺寸L与像素尺寸N之间应满足如下关系式:L=KN+b
式中,b为系统误差,K为标定系数;
在摄像机固定的情况下,求取参数K和b值的具体步骤如下:
(1)在被测位置放置一长度为L1的标准量块;
(2)对标准量块进行扫描、处理,得到对应的像素尺寸N1;
(3)在被测位置放置另一长度为L2的标准量块,重复步骤2,得到对应像素尺寸N2;
(4)求取参数值:
4 软件设计
本着稳定、可靠、合理、高效、简洁和易于操作的原则,我们采用面向对象的Matlab程序语言,实现了基于Matlab GUI的测量系统软件的设计。
本测量系统软件主要包括用户登录模块、文件管理模块、图像处理模块、参数设置模块、数据浏览模块和帮助模块等。
其中,用户登录模块可以完成用户的注册、登陆、密码修改和账号管理;文件管理模块主要包括待测零件图像的打开、关闭和保存等功能;图像处理模块不仅
包含文中所涉及到的算法,还增加了其他算法功能;参数设置模块可以实现对摄像机、零件和图像参数的设置;数据浏览模块可以完成对实时数据、历史数据和操作记录的查看;软件帮助模块主要用来说明软件的使用和系统的更新问题。
5 实验结果
为了验证测量系统的适应性、稳定性和可靠性,本文选用工作面距离为1.49mm的0级量块和直径为2.03mm的标准环规对系统进行了可靠性测试。
实验的测量结果如表1所示。
采用概率与数理统计的方法对测量结果进行了处理。
由处理结果可以看到,采用本测量系统,其测量精度可以达到微米级,可以满足在线实时测量的需要。
6 结论
作者设计了一套基于机器视觉的零件几何尺寸在线检测系统,克服当前人工检测的不足,提高了产品的检测精度。
同时,完成了系统硬件、软件和图像处理算法的设计。
实验结果表明:该测量系统的测量精度可以达到2um以下,满足零件尺寸非接触在线测量要求,具有很好的应用前景。
参考文献
[1]王保军.基于机器视觉的药瓶封装缺陷检测系统研究[D].沈阳:东北大学(硕士学位论文),2014.
[2]李岩,花国梁.精密测量技术[M].北京:中国计量出版社,2001.
[3]章毓晋.图像工程(上册)——图像处理和分析[M].北京:清华大学出版社,1999,5-120.
[4]张铮,王艳平,薛桂香.数字图像处理与机器视觉[M].北京:人民邮电出版社,2012(12):63-160.
作者简介
王保军(1988-),男,山西省忻州市人。
硕士研究生学历。
现为山西机电职业技术学院助理讲师。
主要研究方向为基于机器视觉的零件在线检测。
作者单位
山西机电职业技术学院山西省长治市 046000。