注塑件孔大小设计
注塑模具设计之顶出设计规范

恒模技字(2003)第号电视机模具顶出的设计规范1.目的规范顶出设计,确保安全,顺畅顶出制品2.内容2.1.设计原则a.顶针分布平均.b.应分布在塑件强度较好,尽量接近粘模力较大处。
c.顶针距离哥边或其他零件有3mm。
d.顶针孔尽可能不做成刀口。
e.顶针与模芯间有4个针径或至少20mm以上导向配合。
f.顶针不能半边骑住成品边,不能与定模碰,滑块擦;g.顶针要离开成品哥顶、转接线R位边1mm。
h.顶端有异形之顶针、司筒/针要有销钉防转。
i.顶针高出推方较大时,顶针延迟。
j.司筒针用压片(不是机米螺丝)压着。
k.顶针、司筒/针、推方杆孔离螺丝杯头孔至少2mm。
l.中心K.O孔与唧嘴同轴。
m.顶针、司筒/针、推方杆压台与沉头孔要有0.05~0.15mm的配合间隙。
n.产品倒角留在司筒上,倒角尖端磨平0.2mm。
o.顶针规格不得小于φ8。
p.四角R应在推方上做出。
q.运动推方、角铁之间应有标准连接块连接。
恒模技字(2003)第号电视机模具顶出的设计规范 2.3.顶针的设计形式,2.4 顶针板强制先复位为了保证顶针和滑块的安全,顶针板必须强制先复位.恒模技字(2003)第 号电视机模具顶出的设计规范2.5 推方a.为了方便推方的装拆,推方杆头部采用组合结构,底针板、底板做螺丝装拆孔。
b.推方联接螺丝头部要有堵头螺丝紧固,推方工艺孔在走模前用堵头螺丝堵上,设尺寸如下图。
恒模技字(2003)第号电视机模具顶出的设计规范面壳顶针分布滑块侧的PCB板槽筋脱很困难,顶针分布如图示。
塑料件内嵌螺母孔尺寸

塑料件内嵌螺母孔尺寸1.引言1.1 概述概述部分的内容主要是对本文主题进行简要介绍和背景说明。
在这篇文章中,我们将讨论塑料件内嵌螺母孔尺寸的重要性以及影响其大小的因素。
螺母孔尺寸对于塑料件的可行性和性能具有重要影响,因为它决定了螺栓和螺母之间的紧密程度。
正确的螺母孔尺寸能够确保螺母与塑料件之间的紧固力和稳定性,从而提高产品的可靠性和使用寿命。
因此,准确确定和控制塑料件内嵌螺母孔尺寸是塑料制品设计和生产过程中至关重要的环节。
为此,本文将深入探讨螺母孔尺寸的重要性以及影响因素,并提供相关应对措施和建议。
通过本文的阅读,读者将能够更好地理解塑料件内嵌螺母孔尺寸的意义和作用,并为相关领域的研究和实践提供有益的参考。
文章结构部分的内容应该包括本文的组织结构和章节安排。
具体可以按照以下方式编写:本文共分为引言、正文和结论三个部分,每个部分包含以下内容:1. 引言1.1 概述:简要介绍塑料件内嵌螺母孔尺寸的背景和重要性。
1.2 文章结构:本部分,介绍文章的组织结构和各个章节的内容。
1.3 目的:明确本文的研究目的和意义。
2. 正文2.1 螺母孔尺寸的重要性:详细解释塑料件内嵌螺母孔尺寸在产品设计和制造中的重要作用。
2.2 塑料件内嵌螺母孔尺寸的影响因素:系统阐述影响塑料件内嵌螺母孔尺寸的各种因素,如材料特性、加工方式等。
3. 结论3.1 总结:对本文的研究内容进行总结,概括归纳出关键点。
3.2 对未来研究的展望:提出进一步研究的方向和可能的拓展领域。
通过以上章节的安排,本文对塑料件内嵌螺母孔尺寸的重要性和影响因素进行了系统论述,并对未来的研究进行了展望。
1.3 目的目的:本文旨在探究塑料件内嵌螺母孔尺寸的相关问题,并分析其在实际应用中的重要性和影响因素。
通过对螺母孔尺寸的研究,旨在为塑料制品的设计和生产提供一些可行的指导和参考,以确保螺母的嵌入与紧固工作能够顺利进行,并提高产品的质量和可靠性。
具体而言,本文将对塑料件内嵌螺母孔尺寸的重要性进行阐述,探讨其如何影响螺母的嵌入性能和紧固力。
塑胶孔设计与螺母选择

塑胶孔设计与螺母选择:塑胶孔与螺母的选择参数1、d尺寸为螺母底座,也称导向定位部分,在埋入前与塑胶C部分配合,因此螺母底端d部分要比塑胶内孔径C尺寸小,以方便定位;2、D尺寸为螺母外径,它与塑胶内孔径C尺寸相配,一般手机螺母塑胶内孔径比螺母外径小约0.25-0.3mm;3、L尺寸为螺母长度,它与塑胶孔深度Y尺寸配合,一般塑胶孔深比螺母高(长)度大0.5-1.0mm的深度用于储胶;4、W为塑胶孔壁厚,一般塑胶孔肉厚为0.8-1.0mm以上,螺母尺寸规格越大,肉厚越大。
塑胶孔参考数据:螺母加热温度于塑胶嵌入螺母成品的影响:塑胶孔预留大小于成螺母压入注塑件后的影响若:塑胶与螺母选择上无问题,螺母埋入塑胶后标准状态若:螺母尺寸太小,塑胶孔太大,螺母埋入塑胶后吃不到胶,会产生扭拉力不足现象若:螺母尺寸太大,预留孔太小,会产生溢胶或者爆裂现象如螺母尺寸与塑胶尺寸都没有问题,还有异常现象发生,那我们通常会考虑通过一些优化设计来改善,例:塑胶孔深较浅,会产生扭拉力不足:由于塑胶孔深度较浅,如选择双斜纹的螺母,在螺母各尺寸比例调配下,特别是压花上,压花段差较短,这样的螺母埋入塑胶后,压花吃胶面的塑胶太少,会产生扭拉力不足现象,所以一般建议,将塑胶预留孔深设在2.5mm以上,螺母尺寸长度一般建议做2.0mm以上。
改善方案:类似这种情况,在客户不方便改模情况下,可建议将螺母花形改为单斜BS1,如右图所示,这样将压花段差加大,压花吃胶面的塑胶增大,从而增加扭拉力。
另,如果塑胶孔溢胶,爆裂由于选择左图样式螺母,在埋入塑胶后,A1、A2处膨胀,B处却急剧收缩,造成塑胶排挤困难,螺母上下端容易产生溢胶现象,严重影响了产品处观;改善方案:以“C”部分为导向定位,使螺母能稳妥地放入塑胶孔位中,提高了效率和良品率,由于加了C端导向部分,A2排挤一定的胶料后,也预留了足够的胶料给A1部分,同时因A1、A2部分是呈90°交角为45 °的斜纹,并可交角形成高强度的节点,阻抗圆周上的扭动力,使扭拉力大大的增加。
注塑机ko孔标准尺寸
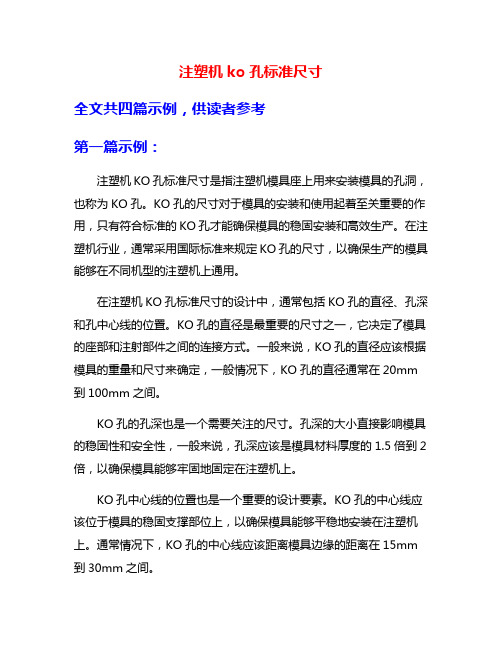
注塑机ko孔标准尺寸全文共四篇示例,供读者参考第一篇示例:注塑机KO孔标准尺寸是指注塑机模具座上用来安装模具的孔洞,也称为KO孔。
KO孔的尺寸对于模具的安装和使用起着至关重要的作用,只有符合标准的KO孔才能确保模具的稳固安装和高效生产。
在注塑机行业,通常采用国际标准来规定KO孔的尺寸,以确保生产的模具能够在不同机型的注塑机上通用。
在注塑机KO孔标准尺寸的设计中,通常包括KO孔的直径、孔深和孔中心线的位置。
KO孔的直径是最重要的尺寸之一,它决定了模具的座部和注射部件之间的连接方式。
一般来说,KO孔的直径应该根据模具的重量和尺寸来确定,一般情况下,KO孔的直径通常在20mm 到100mm之间。
KO孔的孔深也是一个需要关注的尺寸。
孔深的大小直接影响模具的稳固性和安全性,一般来说,孔深应该是模具材料厚度的1.5倍到2倍,以确保模具能够牢固地固定在注塑机上。
KO孔中心线的位置也是一个重要的设计要素。
KO孔的中心线应该位于模具的稳固支撑部位上,以确保模具能够平稳地安装在注塑机上。
通常情况下,KO孔的中心线应该距离模具边缘的距离在15mm 到30mm之间。
注塑机KO孔标准尺寸的设计需要考虑多个方面因素,包括KO孔的直径、孔深和中心线位置。
只有正确设计和制造符合标准要求的KO 孔,才能确保模具能够在注塑机上平稳、稳固地安装和使用,提高生产效率和产品质量。
第二篇示例:注塑机ko孔标准尺寸是指在注塑机上开设的用于固定模具的孔洞尺寸标准。
在注塑加工中,模具的固定是非常重要的一环,好的固定方式可以确保注塑机的稳定运行,提高生产效率和产品质量。
注塑机ko孔标准尺寸是一个非常重要的技术参数。
注塑机ko孔的标准尺寸通常是根据注塑机的型号和规格来确定的。
不同型号的注塑机有不同的ko孔标准尺寸,一般来说,大型注塑机的ko孔尺寸要比小型注塑机的ko孔尺寸大。
这是因为大型注塑机需要承受更大的模具重量,因此需要更大的ko孔来固定模具。
注塑模具技术规范要求

A: 模具外观1: 铭牌内容要打印模具编号、模具重量(KG)、模具外形尺寸(mm),字符均用1/8英寸的字码打上,字符清晰、排列整齐。
2: 铭牌要固定在模腿上靠近后模板和基准角的地方(离两边各有15mm的距离),用四个柳钉固定,固定可靠,不易剥落。
3; 冷却水嘴要用塑料块插水嘴,¢10管,规格可为G1/8″、G1/4″、G3/8″。
如合同有特殊要求,按合同。
4: 冷却水嘴要伸出模架表面,水嘴头部凹进外表面不超过3mm。
5: 冷却水嘴避空孔直径要为¢25、¢30、¢35mm三种规格,孔外沿有倒角,倒角大于1.5×45,倒角一致。
6: 冷却水嘴要有进出标记,进水为IN,出水为OUT,IN、OUT后加顺序号,如IN1、OUT1。
7: 标识英文字符和数字要大写(5/6″),位置在水嘴正下方10mm处,字迹清晰、美观、整齐、间距均匀。
8:进出油嘴、进出气嘴要同冷却水嘴,并在IN、OUT前空一个字符加G(气)、O(油)。
9: 模具安装方向上的上下侧开设水嘴,要内置,并开导流槽或下方有支撑柱加以保护。
1文档来源为:从网络收集整理.word版本可编辑.欢迎下载支持.10: 无法内置的油嘴或水嘴下方要有支撑柱加以保护。
11: 模架上各模板要有基准角符号,大写英文DATUM,字高5/16″,位置在离边10mm处,字迹清晰、美观、整齐、间距均匀。
12: 各模板要有零件编号,编号在基准角符号正下方离底面10mm处,要求同11号。
13: 模具配件要影响模具的吊装和存放,如安装时下方有外漏的油缸、水嘴、预复位机构等,应有支撑腿保护。
14: 支撑腿的安装要用螺丝穿过支撑腿固定在模架上,或过长的支撑腿车加工外螺纹紧固在模架上。
15: 模具顶出孔要符合指定的注塑机,除小型模具外,原则上不能只用一个中心顶出(模具长度或宽度尺寸有一个大于500mm时),顶出孔直径应比顶出杆大5-10mm。
16: 定位圈要可靠固定(一般用三个M6或M8的内六角螺丝),直径一般为¢100或¢150mm,高出顶板10mm。
多腔注塑模具设计说明
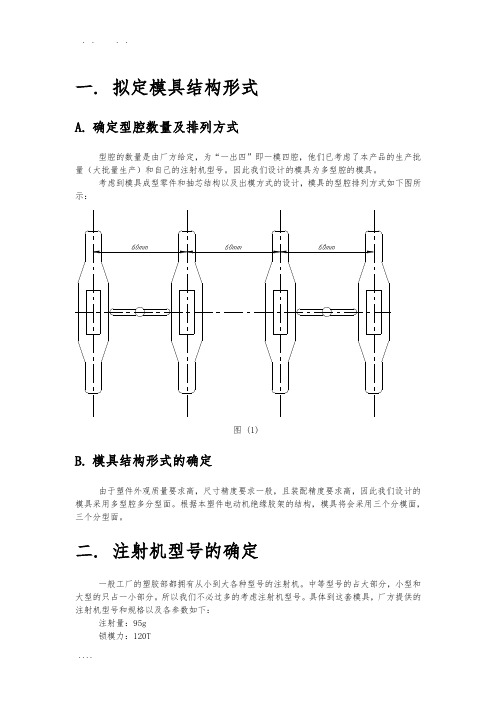
一.拟定模具结构形式A.确定型腔数量及排列方式型腔的数量是由厂方给定,为“一出四”即一模四腔,他们已考虑了本产品的生产批量(大批量生产)和自己的注射机型号。
因此我们设计的模具为多型腔的模具。
考虑到模具成型零件和抽芯结构以及出模方式的设计,模具的型腔排列方式如下图所示:图 (1)B.模具结构形式的确定由于塑件外观质量要求高,尺寸精度要求一般,且装配精度要求高,因此我们设计的模具采用多型腔多分型面。
根据本塑件电动机绝缘胶架的结构,模具将会采用三个分模面,三个分型面。
二.注射机型号的确定一般工厂的塑胶部都拥有从小到大各种型号的注射机。
中等型号的占大部分,小型和大型的只占一小部分。
所以我们不必过多的考虑注射机型号。
具体到这套模具,厂方提供的注射机型号和规格以及各参数如下:注射量:95g锁模力:120T模板大小:400×550开模距离:推出形式:推出位置:推出行程:三.分型面位置的确定如何确定分型面,需要考虑的因素比较复杂。
由于分型面受到塑件在模具中的成型位置、浇注系统设计、塑件的结构工艺性及精度、嵌件位置形状以及推出方法、模具的制造、排气、操作工艺等多种因素的影响,因此在选择分型面时应综合分析比较,从几种方案中优选出较为合理的方案。
选择分型面时一般应遵循以下几项原则:1)分型面应选在塑件外形最大轮廓处。
2)便于塑件顺利脱模,尽量使塑件开模时留在动模一边。
3)保证塑件的精度要求。
4)满足塑件的外观质量要求。
5)便于模具加工制造。
6)对成型面积的影响。
7)对排气效果的影响。
8)对侧向抽芯的影响。
其中最重要的是第5)和第2)、第8)点。
为了便于模具加工制造,应尽是选择平直分型面工易于加工的分型面。
如下图所示,采用A-A这样一个平直的分型面,前模(即定模)做成平的就行了,胶位全部做在后模(即动模),大简化了前模的加工。
A-A分型面也是整个模具的主分模面。
下图中虚线所示的B-B和C-C分型面是行位(即滑块)的分型面。
注塑模具标准件

表2-7 标准复位杆(摘自GB/T 4169.13—2006)
mm
表面粗糙度以微米为单位
未注表面粗糙度Ra=6.3um。 a 可选砂轮越程槽或R0.5mm~R1mm圆角。 b 端面允许留有中心孔。 标记示例:直径D=10mm、长度L=100mm的复位杆: 复位杆 10×100 GB/T 4169.13—2006
未注表面粗糙度Ra=6.3μm;未注倒角1mmX45°. a 可选砂轮越程槽或R0.5mm~R1mm圆角。 b 允许开油槽。 c 允许保留两端的中心孔。 d 圆弧连接,R2mm~R5mm。 标记示例:直径D=12mm、长度L=50mm、与模板配合长度L1=20mm 的带头导柱:带头导柱 12×50×20 GB/T 4169.4—2006
盲孔会增加模具闭合时的阻力,并使模具不能紧密
闭合,带导套的模具应采用带肩导柱。生产实际中
使用的导套如所示。
图1-5 导套实例
导套常用的结构形式也有两种,一种不带安装
凸肩,另一种带安装凸肩,相应地称为直导套和带
头导套,GB/T 4169.2—2006和GB/T 4169.3—
2006分别规定了他们的尺寸规格和公差,同时给出了
mm
注:① 材料由制造者选定,推荐采用4Cr5MoSiV1、3Cr2W8V。 ② 硬度45HRC~50HRC。 ③ 淬火后表面可进行渗碳处理,渗碳层深度为0.08mm~ 0.15mm,心部硬度40HRC~44HRC,表面硬度≥900HV。 ④ 其余应符合GB/T 4170--2006的规定。
四、推板
表1-2 标准带肩导柱(摘自GB/T 4169.5—2006)
mm
表面粗糙度以微米为单位
未注表面粗糙度Ra=6.3um;未注倒角1mmX45°. a 可选砂轮越程槽或R0.5mm~R1mm圆角。 b 允许开油槽。 c 允许保留两端的中心孔。 d 圆弧连接,R2mm~R5mm 标记示例:直径D=16mm、长度L=50mm、与模板配合长度L1=20mm 的带肩导柱:带肩导柱 16×50×20 GB/T 4169.5—2006 .
注塑件自攻螺钉与螺钉柱设计规范

一、螺钉与螺钉柱参数说明:
p——螺距 k——螺钉末端尺寸 φd——配孔内径(大端) φD——配孔外径(小端) φT——倒角后孔径
h——通孔深度
H——盲孔深度
Байду номын сангаас
二、螺钉与螺钉柱设计规范
螺钉与螺钉柱设计规范主要有两点:
1.螺钉柱尺寸必须满足标准要求。 2.螺钉嵌入尺寸必须大于最小嵌入尺寸。 3.螺钉柱尺寸及最小嵌入尺寸标准见下页表。
说明:生产中很多打滑丝的问题均为嵌入尺寸过小所致,第2点需引起格外重视!
螺钉柱尺寸标准
注:通孔孔深中n表示有效螺纹圈数,HIPS材料n取5,其它材料n取3,p 和k的值见下页表2。
最小嵌入尺寸标准
备注: (1).有效螺纹圈数是指螺钉嵌入螺钉柱中去掉螺钉末端尺寸后的圈数, HIPS不低 于5圈,其它材料不低于3圈。 (2). 嵌入尺寸是指螺钉嵌入螺钉柱中的全部尺寸。