MBR池操作规程
mbr膜生物反应器操作规程
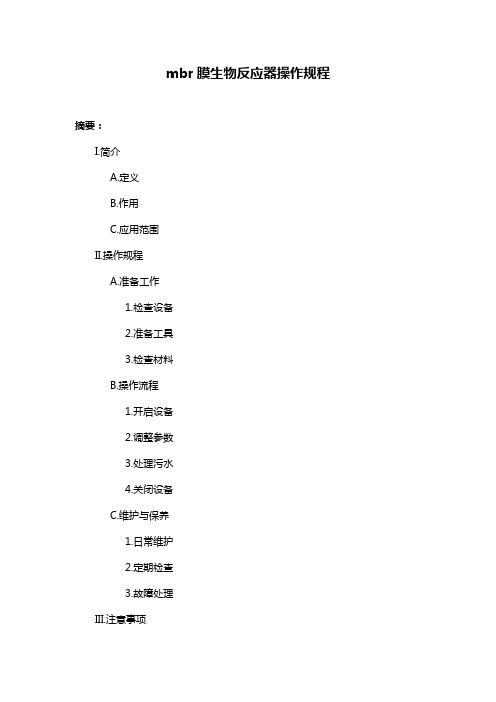
mbr膜生物反应器操作规程摘要:I.简介A.定义B.作用C.应用范围II.操作规程A.准备工作1.检查设备2.准备工具3.检查材料B.操作流程1.开启设备2.调整参数3.处理污水4.关闭设备C.维护与保养1.日常维护2.定期检查3.故障处理III.注意事项A.安全措施B.操作禁忌C.环保要求IV.结语正文:I.简介膜生物反应器(MBR)是一种将高效膜分离技术与传统活性污泥法相结合的新型高效污水处理工艺。
它用具有独特结构的MBR 平片膜组件置于曝气池中,经过好氧曝气和生物处理后的水,由泵通过滤膜过滤后抽出。
它利用膜分离设备将生化反应池中的活性污泥和大分子有机物质截留住,省掉二沉池。
活性污泥浓度因此大大提高,水力停留时间(HRT)和污泥停留时间(SRT)可以分别控制,而难降解的物质在反应器中不断反应、降解。
II.操作规程A.准备工作1.检查设备:在操作MBR 膜生物反应器前,应检查设备是否正常,包括曝气设备、膜组件、泵等。
2.准备工具:准备清洁和维护所需的工具,如刷子、抹布等。
3.检查材料:检查膜组件、曝气设备等是否安装正确。
B.操作流程1.开启设备:按照正确的顺序开启曝气设备、泵等。
2.调整参数:根据处理污水的实际情况,调整相关参数,如曝气量、污泥浓度等。
3.处理污水:开始处理污水,监控各项指标,确保处理效果达到预期。
4.关闭设备:在处理完毕后,按照顺序关闭设备。
C.维护与保养1.日常维护:定期清洁设备,检查各部件的运行状况,发现问题及时处理。
2.定期检查:定期对设备进行详细检查,包括曝气设备、膜组件等,确保其正常运行。
3.故障处理:在设备出现故障时,及时进行处理,防止故障扩大。
III.注意事项A.安全措施:在操作过程中,应遵循安全规程,防止事故发生。
B.操作禁忌:禁止在设备运行过程中进行无关操作,以免影响设备运行。
C.环保要求:在操作过程中,应遵循环保要求,确保不污染环境。
IV.结语MBR 膜生物反应器的操作规程是保证设备正常运行和污水处理效果的关键。
MBR池操作规程
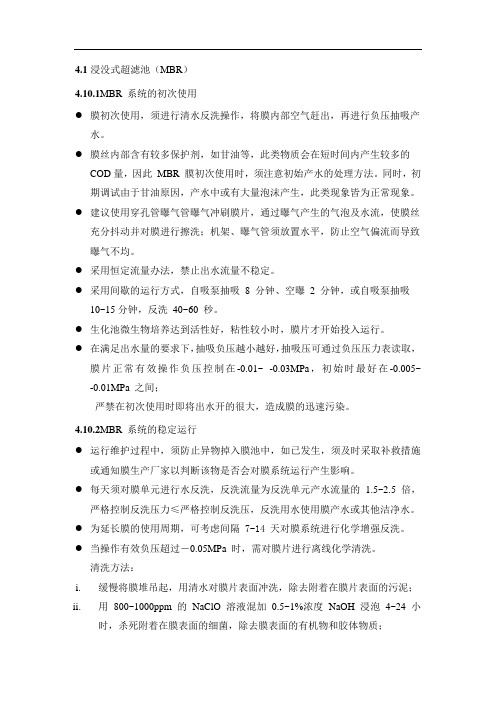
4.1浸没式超滤池(MBR)4.10.1MBR 系统的初次使用●膜初次使用,须进行清水反洗操作,将膜内部空气赶出,再进行负压抽吸产水。
●膜丝内部含有较多保护剂,如甘油等,此类物质会在短时间内产生较多的COD量,因此MBR 膜初次使用时,须注意初始产水的处理方法。
同时,初期调试由于甘油原因,产水中或有大量泡沫产生,此类现象皆为正常现象。
●建议使用穿孔管曝气管曝气冲刷膜片,通过曝气产生的气泡及水流,使膜丝充分抖动并对膜进行擦洗;机架、曝气管须放置水平,防止空气偏流而导致曝气不均。
●采用恒定流量办法,禁止出水流量不稳定。
●采用间歇的运行方式,自吸泵抽吸8 分钟、空曝2 分钟,或自吸泵抽吸10~15分钟,反洗40~60 秒。
●生化池微生物培养达到活性好,粘性较小时,膜片才开始投入运行。
●在满足出水量的要求下,抽吸负压越小越好,抽吸压可通过负压压力表读取,膜片正常有效操作负压控制在-0.01~ -0.03MPa,初始时最好在-0.005~ -0.01MPa 之间;严禁在初次使用时即将出水开的很大,造成膜的迅速污染。
4.10.2MBR 系统的稳定运行●运行维护过程中,须防止异物掉入膜池中,如已发生,须及时采取补救措施或通知膜生产厂家以判断该物是否会对膜系统运行产生影响。
●每天须对膜单元进行水反洗,反洗流量为反洗单元产水流量的1.5~2.5 倍,严格控制反洗压力≤严格控制反洗压,反洗用水使用膜产水或其他洁净水。
●为延长膜的使用周期,可考虑间隔 7-14 天对膜系统进行化学增强反洗。
●当操作有效负压超过-0.05MPa 时,需对膜片进行离线化学清洗。
清洗方法:i.缓慢将膜堆吊起,用清水对膜片表面冲洗,除去附着在膜片表面的污泥;ii.用800~1000ppm 的NaClO 溶液混加0.5~1%浓度NaOH 浸泡4~24 小时,杀死附着在膜表面的细菌,除去膜表面的有机物和胶体物质;iii.清洗结束后用清水对膜片进行漂洗,装入膜池后对膜单元进行3~5 分钟的反冲洗,膜片通量即可恢复。
MBR池操作规程

4.1浸没式超滤池(MBR)4.10.1MBR 系统的初次使用膜初次使用,须进行清水反洗操作,将膜内部空气赶出,再进行负压抽吸产水。
膜丝内部含有较多保护剂,如甘油等,此类物质会在短时间内产生较多的 COD量,因此 MBR 膜初次使用时,须注意初始产水的处理方法。
同时,初期调试由于甘油原因,产水中或有大量泡沫产生,此类现象皆为正常现象。
建议使用穿孔管曝气管曝气冲刷膜片,通过曝气产生的气泡及水流,使膜丝充分抖动并对膜进行擦洗;机架、曝气管须放置水平,防止空气偏流而导致曝气不均。
采用恒定流量办法,禁止出水流量不稳定。
采用间歇的运行方式,自吸泵抽吸 8 分钟、空曝 2 分钟,或自吸泵抽吸 10~15分钟,反洗 40~60 秒。
生化池微生物培养达到活性好,粘性较小时,膜片才开始投入运行。
在满足出水量的要求下,抽吸负压越小越好,抽吸压可通过负压压力表读取,膜片正常有效操作负压控制在-0.01~ -0.03MPa,初始时最好在-0.005~ -0.01MPa 之间;严禁在初次使用时即将出水开的很大,造成膜的迅速污染。
4.10.2MBR 系统的稳定运行运行维护过程中,须防止异物掉入膜池中,如已发生,须及时采取补救措施或通知膜生产厂家以判断该物是否会对膜系统运行产生影响。
每天须对膜单元进行水反洗,反洗流量为反洗单元产水流量的1.5~2.5 倍,严格控制反洗压力≤严格控制反洗压,反洗用水使用膜产水或其他洁净水。
为延长膜的使用周期,可考虑间隔 7-14 天对膜系统进行化学增强反洗。
当操作有效负压超过-0.05MPa 时,需对膜片进行离线化学清洗。
清洗方法:i.缓慢将膜堆吊起,用清水对膜片表面冲洗,除去附着在膜片表面的污泥;ii.用 800~1000ppm 的 NaClO 溶液混加 0.5~1%浓度 NaOH 浸泡 4~24 小时,杀死附着在膜表面的细菌,除去膜表面的有机物和胶体物质;iii.清洗结束后用清水对膜片进行漂洗,装入膜池后对膜单元进行 3~5 分钟的反冲洗,膜片通量即可恢复。
MBR手动操作
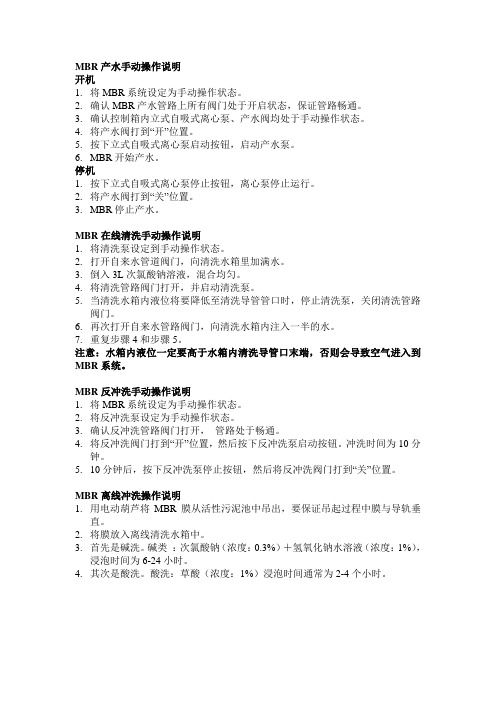
MBR产水手动操作说明开机1.将MBR系统设定为手动操作状态。
2.确认MBR产水管路上所有阀门处于开启状态,保证管路畅通。
3.确认控制箱内立式自吸式离心泵、产水阀均处于手动操作状态。
4.将产水阀打到“开”位置。
5.按下立式自吸式离心泵启动按钮,启动产水泵。
6.MBR开始产水。
停机1.按下立式自吸式离心泵停止按钮,离心泵停止运行。
2.将产水阀打到“关”位置。
3.MBR停止产水。
MBR在线清洗手动操作说明1.将清洗泵设定到手动操作状态。
2.打开自来水管道阀门,向清洗水箱里加满水。
3.倒入3L次氯酸钠溶液,混合均匀。
4.将清洗管路阀门打开,并启动清洗泵。
5.当清洗水箱内液位将要降低至清洗导管管口时,停止清洗泵,关闭清洗管路阀门。
6.再次打开自来水管路阀门,向清洗水箱内注入一半的水。
7.重复步骤4和步骤5。
注意:水箱内液位一定要高于水箱内清洗导管口末端,否则会导致空气进入到MBR系统。
MBR反冲洗手动操作说明1.将MBR系统设定为手动操作状态。
2.将反冲洗泵设定为手动操作状态。
3.确认反冲洗管路阀门打开,管路处于畅通。
4.将反冲洗阀门打到“开”位置,然后按下反冲洗泵启动按钮。
冲洗时间为10分钟。
5.10分钟后,按下反冲洗泵停止按钮,然后将反冲洗阀门打到“关”位置。
MBR离线冲洗操作说明1.用电动葫芦将MBR膜从活性污泥池中吊出,要保证吊起过程中膜与导轨垂直。
2.将膜放入离线清洗水箱中。
3.首先是碱洗。
碱类:次氯酸钠(浓度:0.3%)+氢氧化钠水溶液(浓度:1%),浸泡时间为6-24小时。
4.其次是酸洗。
酸洗:草酸(浓度:1%)浸泡时间通常为2-4个小时。
MBR操作规程

MBR膜池操作规程(参考)1 工艺描述MBR池利用膜对生化反应池内的含泥污水进行过滤,实现泥水分离。
一方面,膜截留了反应池中的微生物,使池中的活性污泥浓度大增加,达到很高的水平,使降解污水的生化反应进行得更迅速更彻底,另一方面,由于膜的高过滤精度,保证了出水清澈透明,得到高质量的产水。
膜区设置MBR膜组件系统及配套的出水、反洗、清洗、吹扫、吊装等系统。
MBR膜区内的吹扫(曝气)有两个用途,一是用于膜组件周围的气水振荡,保持膜表面清洁,二是为提供生物降解所需要的氧气。
生物降解后的水在滤液自吸泵的抽提作用下通过MBR膜组件,滤过液经由MBR集水管汇集送到清水池。
通过膜的高效截留作用,全部细菌及悬浮物均被截流在膜池中,可以有效截留硝化菌,使硝化反应顺利进行,有效去除氨氮;同时可以截留难于降解的大分子有机物,延长其在反应器中的停留时间,使之得到最大限度的降解。
MBR膜组件下部设置专用的吹扫系统,吹扫抖动膜元件,以缓解膜元件周边的污泥浓度累积。
剩余污泥通过膜区剩余污泥泵定期排出,可控制系统内活性污泥的浓度及污泥龄。
同时为了保证MBR膜组件有良好的水通量,能持续、稳定地出水,使用了专有的清水反洗、化学反洗及化学清洗程序对膜组件进行定时清洗。
2 操作及控制控制要点:(1)控制好氧池MLSS稳定在5~6L时,可以打开进水阀,将曝气池中的泥水混合物溢流入膜池。
(2)污水进入膜池前,确认要进行曝气操作的膜池主管阀门处于关位,支管上所有与膜组件相连的阀门处于开位,其它未安装膜组件的阀门处于关位。
开启一台风机对膜池曝气,防止膜池中的曝气管堵塞,然后膜池方可进水。
(3)进水前确认已安装膜组件的膜池的前后闸门全部打开,另外两个廊道闸门关闭,关闭配水渠、污泥渠的连通闸门。
(4)调整鼓风机风量,将池内的溶氧量控制在2mg/L以上。
(5)确认所有膜廊道曝气量均匀,所有膜箱曝气良好,并没有污泥累积在膜丝上。
3 运行时应注意的问题(1)温度污水温度随气温会有变化,可适当投入接种污泥,并控制较低的运行负荷(污泥)。
MBR膜组件安全操作规程范本
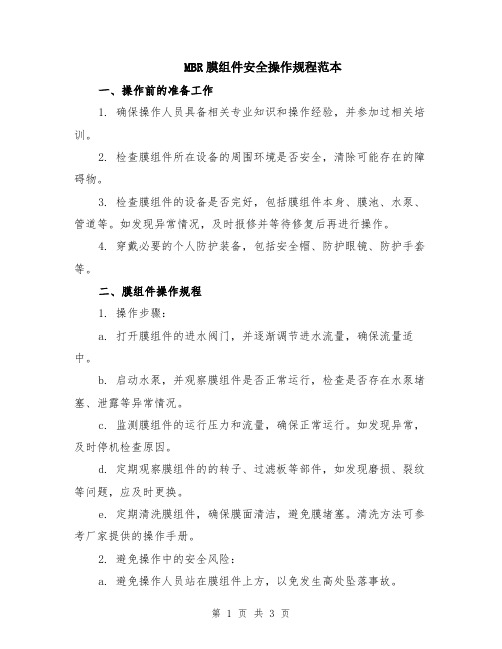
MBR膜组件安全操作规程范本一、操作前的准备工作1. 确保操作人员具备相关专业知识和操作经验,并参加过相关培训。
2. 检查膜组件所在设备的周围环境是否安全,清除可能存在的障碍物。
3. 检查膜组件的设备是否完好,包括膜组件本身、膜池、水泵、管道等。
如发现异常情况,及时报修并等待修复后再进行操作。
4. 穿戴必要的个人防护装备,包括安全帽、防护眼镜、防护手套等。
二、膜组件操作规程1. 操作步骤:a. 打开膜组件的进水阀门,并逐渐调节进水流量,确保流量适中。
b. 启动水泵,并观察膜组件是否正常运行,检查是否存在水泵堵塞、泄露等异常情况。
c. 监测膜组件的运行压力和流量,确保正常运行。
如发现异常,及时停机检查原因。
d. 定期观察膜组件的的转子、过滤板等部件,如发现磨损、裂纹等问题,应及时更换。
e. 定期清洗膜组件,确保膜面清洁,避免膜堵塞。
清洗方法可参考厂家提供的操作手册。
2. 避免操作中的安全风险:a. 避免操作人员站在膜组件上方,以免发生高处坠落事故。
b. 确保膜组件的进水阀门在操作期间处于开启状态,避免发生压力过高的危险。
c. 禁止在膜组件周围进行吸烟等火源活动,防止引发火灾。
d. 避免将腐蚀性、有毒的物质接触膜组件,可采取物理隔离或其他措施。
三、紧急情况处理1. 如发生膜组件堵塞、泄漏等紧急情况,应立即关闭进水阀门,停机检修。
2. 在紧急情况下,一定要确保操作人员的安全。
如果需要,应及时报警,并呼叫专业人员进行处理。
3. 在紧急情况得到解决后,应对膜组件及相关设备进行全面检查,确保无隐患后再进行操作。
四、设备维护与保养1. 定期对膜组件及相关设备进行检修与保养,保持其正常运行。
2. 定期更换膜组件,确保其过滤效果。
3. 注意清洁膜组件的周围环境,防止灰尘和污物进入设备。
4. 定期监测设备的运行参数,如压力、流量等,及时检修异常现象。
五、操作记录与安全培训1. 操作人员应按规定填写操作记录,记录操作时间、操作内容、设备状况等信息。
MBR废水操作规程
M B R废水操作规程(总10页) -CAL-FENGHAI.-(YICAI)-Company One1-CAL-本页仅作为文档封面,使用请直接删除****社区废水处理工程操作规程****环保设备有限公司地址:****电话:**** 邮编:****传真:**** 日期:****第一章工艺流程描述废水经过格栅格除漂浮物后,进入调节池,污水在调节池中进行均质、均量调节,内部设置污水提升泵,一级提升进入水解酸化池,在水解酸化池内通过兼养微生物进行初步预处理,上清液进入接触氧化池,污水在接触氧化池中通过鼓风曝气为微生物生长提供所需的氧气,来降解污水中的有机污染物,出水进入BMR池,进行泥水分离,上清液经自吸泵进入消毒水池,经消毒后达标排放。
第二章系统运转一.开机前的准备工作1.各设备的检查(1)检查各单体设备是否能正常运转,管道阀门是否存在漏水问题;(2)检查各池子中注水情况,保证各水泵不空转;(3)检查各药剂的配置情况,保证一定浓度,控制药剂量;(4)检查液位计的液位控制情况;2.药剂配制及检查消毒设备中使用的消毒粉剂储量是否足够,浓度是否符合使用要求。
二、运行1.开机污水处理系统:(1)把相应设备(如阀门等)开启到正常运行位置,确保当设备开始运转,污水的正常流向;(2)开启污水站总电源开关;(3)污水进入污水处理站的同时开启风机,对污水进行曝气调节,防止悬浮物沉淀;(4)废水经调节完毕后,根据液位控制情况,手动或自动开启污水提升泵,一级提升污水进入水解酸化池;(5)污水进入曝气池后,开启曝气池曝气阀门。
(6)调节内回流泵阀门,根据出水中氨氮的浓度适当调整回流比。
若氨氮过高,则增大回流比;若氨氮较低,则减小回流比以减少能耗。
(7)污水进入二沉池的同时开启污泥回流泵,回流沉淀污泥到曝气池前端,维持曝气池中的污泥沉降比在30%-35%之间,如果超出这个数值,可开启相关阀门,把剩余污泥排入污泥浓缩池中。
(8)二沉池出水进入中间水池,经过滤提升泵进入活性炭过滤罐,过滤罐出水经二氧化氯消毒后达标排放。
MBR膜组件安全操作规程范本(2篇)
MBR膜组件安全操作规程范本一、操作前的准备工作1. 确保操作人员具备相关专业知识和操作经验,并参加过相关培训。
2. 检查膜组件所在设备的周围环境是否安全,清除可能存在的障碍物。
3. 检查膜组件的设备是否完好,包括膜组件本身、膜池、水泵、管道等。
如发现异常情况,及时报修并等待修复后再进行操作。
4. 穿戴必要的个人防护装备,包括安全帽、防护眼镜、防护手套等。
二、膜组件操作规程1. 操作步骤:a. 打开膜组件的进水阀门,并逐渐调节进水流量,确保流量适中。
b. 启动水泵,并观察膜组件是否正常运行,检查是否存在水泵堵塞、泄露等异常情况。
c. 监测膜组件的运行压力和流量,确保正常运行。
如发现异常,及时停机检查原因。
d. 定期观察膜组件的的转子、过滤板等部件,如发现磨损、裂纹等问题,应及时更换。
e. 定期清洗膜组件,确保膜面清洁,避免膜堵塞。
清洗方法可参考厂家提供的操作手册。
2. 避免操作中的安全风险:a. 避免操作人员站在膜组件上方,以免发生高处坠落事故。
b. 确保膜组件的进水阀门在操作期间处于开启状态,避免发生压力过高的危险。
c. 禁止在膜组件周围进行吸烟等火源活动,防止引发火灾。
d. 避免将腐蚀性、有毒的物质接触膜组件,可采取物理隔离或其他措施。
三、紧急情况处理1. 如发生膜组件堵塞、泄漏等紧急情况,应立即关闭进水阀门,停机检修。
2. 在紧急情况下,一定要确保操作人员的安全。
如果需要,应及时报警,并呼叫专业人员进行处理。
3. 在紧急情况得到解决后,应对膜组件及相关设备进行全面检查,确保无隐患后再进行操作。
四、设备维护与保养1. 定期对膜组件及相关设备进行检修与保养,保持其正常运行。
2. 定期更换膜组件,确保其过滤效果。
3. 注意清洁膜组件的周围环境,防止灰尘和污物进入设备。
4. 定期监测设备的运行参数,如压力、流量等,及时检修异常现象。
五、操作记录与安全培训1. 操作人员应按规定填写操作记录,记录操作时间、操作内容、设备状况等信息。
mbr膜生物反应器操作规程
mbr膜生物反应器操作规程MBR膜生物反应器是一种有效的废水处理设备,通过生物反应和膜分离技术,能够高效地去除废水中的悬浮物、有机物和微生物等污染物。
为了保证MBR膜生物反应器的正常运行和良好的处理效果,需要严格遵守以下操作规程:1. 操作前的准备:a. 确保反应器周围的环境整洁,无杂物和异味。
b. 检查设备各部位的接口和密封性,确保没有泄漏。
c. 检查进水、出水和气体管道是否畅通。
d. 检查电源是否正常,并确保设备接地良好。
2. 启动系统:a. 打开进水阀门,使废水缓慢进入反应器,并逐渐增加流量至正常工作流量。
b. 打开空气供应系统,提供足够的曝气以维持生物反应器内的氧气供应。
c. 启动膜组件和搅拌器,确保膜组件正常工作。
3. 监测操作:a. 定期检测进水和出水的COD、BOD、总悬浮固体等指标,确保处理效果符合要求。
b. 定期检查膜组件的通透率和污染程度,如有需要,进行清洗或更换膜组件。
c. 监测温度、pH值和溶解氧等参数,保持反应器内的环境稳定。
4. 维护清洁:a. 定期清洗反应器内部,去除废水中的沉淀物和污泥。
b. 定期检查反应器内部的搅拌器、气体供应系统和膜组件,确保其无损坏和漏水现象。
c. 定期对膜组件进行清洗,去除附着在膜面上的污染物。
5. 故障处理:a. 发现设备故障时,应立即停止废水的进水和继续操作,并通知维修人员进行维修。
b. 在维修期间,应关闭废水的进水阀门,以防止故障扩大和影响其他设备的正常工作。
6. 定期维护:a. 每年对MBR膜生物反应器进行全面维护和检修,包括更换损坏或寿命到期的设备和部件。
b. 定期对设备进行润滑和保养,保证其正常运行并延长使用寿命。
7. 安全操作:a. 操作人员应经过专业培训,了解设备的操作规程和安全事项。
b. 操作人员应佩戴防护装备,如手套、防护面罩等,以防止接触有害物质和化学品。
c. 在操作过程中,严禁吸烟、饮食和乱扔垃圾,保持操作区域的整洁和安全。
MBR操作规程及药洗步骤
MBR操作规程及药洗步骤一、MBR操作规程MBR(膜生物反应器)是一种利用微孔膜进行生物处理的技术,具有高效、稳定、节能等优点,已广泛应用于废水处理领域。
为了保证MBR系统的正常运行,需制定相应的操作规程,以下是MBR操作规程的内容:1.检查设备:每天开始操作前,必须检查设备是否正常,如泵、搅拌器、气体供应等,必要时进行维护和修理。
2.检查膜组件:每天开始操作前,必须检查膜组件是否有破损或污染,必要时进行清洗和更换。
3.控制进水水质:进水水质的稳定对MBR系统的运行非常重要,必须严格控制进水COD、BOD、SS等指标,避免过高或过低的水质影响系统的处理效果。
4.控制气泡供应:MBR系统需要气泡来提供氧气,必须保持气泡的稳定和均匀,以确保生物反应器中的生物好氧反应的正常进行。
5.控制通气时间:生物好氧反应需要给予足够的通气时间,通常需要系统运行24小时来保证足够的气体供应。
6.控制搅拌时间:MBR系统需要搅拌来保持生物颗粒的悬浮状态,必须保持搅拌的时间和强度适宜,避免颗粒沉降和碰撞造成阻塞。
7.控制通气量:MBR系统需要提供足够的气体来保持生物颗粒的悬浮状态,必须根据MBR反应器的规模和运行情况来控制通气量。
8.控制回流量:MBR系统需要回流一部分污泥来保持MBR反应器中的污泥浓度,必须根据MBR反应器的规模和运行情况来控制回流量。
9.控制出水水质:出水水质的稳定对MBR系统的运行非常重要,必须严格控制出水COD、BOD、SS等指标,避免超标排放。
10.定期维护:定期进行设备的维护和检修,如清洗膜、更换膜组件等,必要时进行系统的大修。
二、MBR药洗步骤MBR系统在长期运行后,由于膜组件会受到沉积物的污染,需要进行药洗来恢复膜组件的通透性。
以下是MBR药洗的步骤:1.预备工作:准备好药洗用的化学品、设备和人员。
确保操作人员穿戴好相应的个人防护装备。
2.排除污水:将MBR系统的进水阀门关闭,排除污水,将膜组件暴露。
- 1、下载文档前请自行甄别文档内容的完整性,平台不提供额外的编辑、内容补充、找答案等附加服务。
- 2、"仅部分预览"的文档,不可在线预览部分如存在完整性等问题,可反馈申请退款(可完整预览的文档不适用该条件!)。
- 3、如文档侵犯您的权益,请联系客服反馈,我们会尽快为您处理(人工客服工作时间:9:00-18:30)。
4.1浸没式超滤池(MBR)
4.10.1MBR 系统的初次使用
●膜初次使用,须进行清水反洗操作,将膜内部空气赶出,再进行负压抽吸产
水。
●膜丝内部含有较多保护剂,如甘油等,此类物质会在短时间内产生较多的
COD量,因此MBR 膜初次使用时,须注意初始产水的处理方法。
同时,初期调试由于甘油原因,产水中或有大量泡沫产生,此类现象皆为正常现象。
●建议使用穿孔管曝气管曝气冲刷膜片,通过曝气产生的气泡及水流,使膜丝
充分抖动并对膜进行擦洗;机架、曝气管须放置水平,防止空气偏流而导致曝气不均。
●采用恒定流量办法,禁止出水流量不稳定。
●采用间歇的运行方式,自吸泵抽吸8 分钟、空曝2 分钟,或自吸泵抽吸
10~15分钟,反洗40~60 秒。
●生化池微生物培养达到活性好,粘性较小时,膜片才开始投入运行。
●在满足出水量的要求下,抽吸负压越小越好,抽吸压可通过负压压力表读取,
膜片正常有效操作负压控制在-0.01~ -0.03MPa,初始时最好在-0.005~ -0.01MPa 之间;
严禁在初次使用时即将出水开的很大,造成膜的迅速污染。
4.10.2MBR 系统的稳定运行
●运行维护过程中,须防止异物掉入膜池中,如已发生,须及时采取补救措施
或通知膜生产厂家以判断该物是否会对膜系统运行产生影响。
●每天须对膜单元进行水反洗,反洗流量为反洗单元产水流量的1.5~2.5 倍,
严格控制反洗压力≤严格控制反洗压,反洗用水使用膜产水或其他洁净水。
●为延长膜的使用周期,可考虑间隔 7-14 天对膜系统进行化学增强反洗。
●当操作有效负压超过-0.05MPa 时,需对膜片进行离线化学清洗。
清洗方法:
i.缓慢将膜堆吊起,用清水对膜片表面冲洗,除去附着在膜片表面的污泥;
ii.用800~1000ppm 的NaClO 溶液混加0.5~1%浓度NaOH 浸泡4~24 小时,杀死附着在膜表面的细菌,除去膜表面的有机物和胶体物质;
iii.清洗结束后用清水对膜片进行漂洗,装入膜池后对膜单元进行3~5 分钟的反冲洗,膜片通量即可恢复。
●在处理部分含盐量高的废水时还要考虑用0.5~2%的HCl/柠檬酸溶液浸泡 2
小时,用以去除无机盐污染。
●运行维护过程中,需有详细的操作记录、数据记录,并通过责任到人的工作
原则来规范员工的工作态度,以期达到设备稳定、良好的运行状态。
4.10.3系统日常维护
●压力表
按期校准,必要时及时调整。
●水泵
定期检查泵的温度,同时检查泵的垫圈以及其它防止泵泄漏的结构。
●鼓风机
定期检查皮带松紧情况,适时更换和补充机油。
●流量仪表
每三个月校正一次,按说明书。
●自动切换阀
每月检查一次,同时检查阀体是否有泄漏。
●膜系统
按常规要求检查进水水质。
同时检测系统的产水流量和运行压力。
按常规检查系统的泄漏情况,一旦发现立即维护。
4.10.4系统故障分析。