车辆薄板有限元分析中的多因子不完全分解预处理解法
汽车结构的常规有限元分析

汽车结构的常规有限元分析唐述斌本文介绍了与产品研发同步的5个有限元分析阶段,阐述了有限元模型建立过程中应注意的问题,简单介绍了汽车产品的4种常规分析方法,建立汽车设计标准的方法,以及3个强度分析范例。
范例1说明了有限元分析应注意的内容,范例2和3介绍了“应力幅值法”在解决汽车车轮轮辐开裂和汽车发动机汽缸体水套底板开裂问题的应用。
汽车是艺术和技术的结合。
一辆好车的主要特点是造型美观、有时代感、结构设计合理、轻量化、材料利用率高,车辆性能先进并且满足国家法规、标准和环保的要求,质量可靠、保养方便、低成本、用户满意、满足市场需求等。
在竞争日益激烈的汽车市场,汽车性价比已经成为市场竞争的焦点。
采用有限元的常规分析技术,用计算机辅助设计代替经验设计,预测结构性能、实现结构优化,提高产品研发水平、降低产品成本,加快新产品上市。
1. 与产品研发同步的5个有限元分析阶段在汽车产品研发流程中,一般有如下5个同步的有限元分析阶段:第0阶段:对样车进行试验和分析;第1阶段:概念设计阶段的分析;第2阶段:详细设计阶段的分析;第3阶段:确认设计阶段的分析;第4阶段:产品批量生产后改进设计的分析。
有限元分析在产品研发的不同阶段有不同的分析目的和分析内容。
有限元分析和试验分析是互相结合和验证的。
在详细设计阶段,有些汽车公司对白车身和成品车车身都进行有限元分析,有些汽车公司只对白车身进行有限元分析。
2. 有限元分析的关键环节――建立合理的有限元模型有限元模型的建立是有限元分析的关键环节。
通过力学分析,把实际工程问题简化为有限元分析的问题,提出建立有限元模型的具体意见和方法,确定载荷和位移边界条件,使得有限元分析有较好的模拟(仿真)效果。
前处理自动生成的网格可能存在问题。
建立有限元模型的好坏直接影响计算结果的误差和分析结论的正确性。
在结构的几何图形上,划分有限元网格是建立有限元模型的主要内容之一。
在用有限元分析的前处理自动生成网格时,特别是用常应变单元自动生成有限元网格时要非常注意,有可能存在问题,应引起注意,必要时加以改进。
第7章 车身结构有限元分析及优化设计【汽车车身结构与设计】
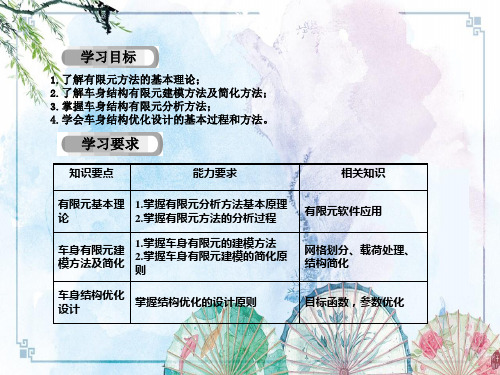
在车身有限元分析中需注意以下几个问题 :
1)复杂曲面网格的划分 2)边界条件的设 有限元法在车身结构分析中的应用
汽车结构有限元分析的应用主要涉及以下内容 : (1)可靠性:在汽车设计中对所有的结构件、主要机械零部件的刚度、
强度、稳定性以及疲劳寿命进行分析; (2)安全性:研究结构耐撞性与乘员安全性等; (3)经济性:研究结构优化及轻量化等; (4)舒适性:进行结构噪声振动分析等。
ANSYS软件实现优化方式: • 批处理方式——APDL语言 • GUI交互方式——一般用户
以GUI优化方式为例,进入优化设计器OPT,执行优化分析过程: 首 先 指定分析文件 ; 声明优化变量,包括设计变量、状态变量和 目标函数 ; 选择优化工具或优化方法 ; 进行优化分析 ; 查看优化设 计序列结果;最后检验设计优化序列。
杆(Bar) 壳单元(Shell)
承受拉伸载荷的细长结构,如某些限位约束可简化为刚性杆,车骨架在拓扑优化 设计等
汽车典型零部件简化模型有限元分析要求及分析计算说明书要求
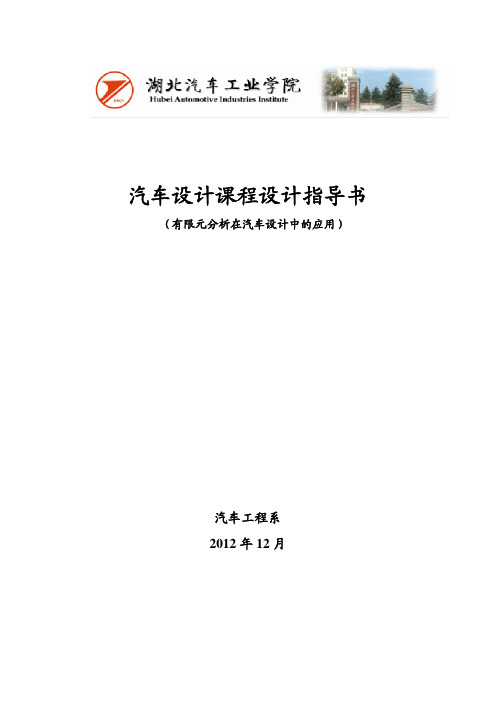
连杆各部位材料、厚度的不同; c. 绘图反映连杆的边界条件; d. 绘出对连杆原设计进行有限元分析后得到的变形图和应力图,安全系数分布
图; e. 收敛分析的结果; f. 结果后处理:结果的多种方法显示,注释任意位置的应力及位移; g. 详细说明对不符合设计要求的结构所作的设计修改;及最终符合设计要求的
周一
建立结构面向有限元分析的三维模型
第Leabharlann 周二讨论结构的三维模型,建立结构的有限元模型
二
周三
继续建立结构的有限元模型
周
周四
结构的有限元分析与模型修正
周五
继续结构的有限元分析与模型修正
5
周一
结果分析、方案优化与对比分析
第
周二
继续结果分析、方案优化与对比分析
三
周三
整理编写分析计算说明书
周
周四
继续整理编写分析计算说明书
定载荷为轴承载荷,分布在小头夹角为 90º 的内壁上;约束施加在连杆大头夹 角为 90º 的内壁上;
6
e. 40Cr 材料的弹性模量:210GPa;泊松比:0.3;屈服极限为:850MPa,设计 安全系数为 6;铜的弹性模量:120GPa,泊松比:0.33;屈服极限为:250MPa; 设计安全系数为 4。
分析的实体建模技术、冻结、切片、参数化建模;梁单元的应用、 二维、轴对称问题的简化与分析、接触区域的处理、Stress Tool 及 Beam Tool 的用法、收敛性问题;参数研究以及目标驱动的优化等。 ¾ 通过文献检索和阅读,结合课程设计对应的结构,明确汽车简化零 部件的简化方案,分析对实际结构进行有限元分析边界条件的合理 设置。 ¾ 掌握对汽车简化零部件进行 CAE 分析的基本方法,完成“汽车典 型零部件简化模型的有限元分析”并写出分析计算说明书。
汽车轴类零件材质非均匀力学特性的有限元分析与数值模拟--优秀毕业论文
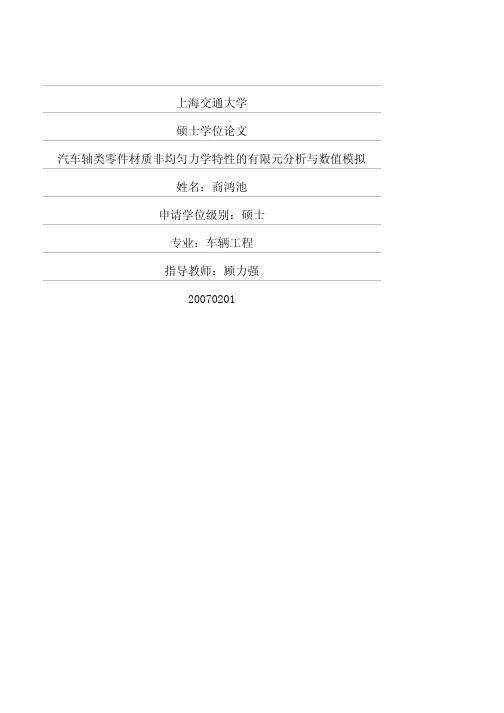
上海交通大学硕士学位论文
英文摘要
material properties, the greater maximum stress is; the impact of one statistical distribution of material properties on the maximum stress varies from another. Fatigue life of the shaft is obtained by ANSYS/Workbench software based on the results of stress analysis. The result indicates that the inhomogeneity of material properties will sharply decrease the operating life of the shaft. KEY WORDS: Inhomogeneity, Shaft, Finite Element Method, Maximum Stress, Fatigue Life
上海交通大学 硕士学位论文 汽车轴类零件材质非均匀力学特性的有限元分析与数值模拟 姓名:商鸿池 申请学位级别:硕士 专业:车辆工程 指导教师:顾力强 20070201
上海交通大学硕士学位论文
摘 要
汽车轴类零件材质非均匀力学特性的 有限元分析与数值模拟
摘 要
轴类零件是汽车动力传动系统中重要的部件。由于加工制造过程中 各种随机因素的影响,多数轴类零件的材质是非均匀的。传统的有限元 方法假设材料是均匀的,这种方法无法反映材料性质的非均匀性;现有 的非均匀模型通过将本构关系赋给每个单元来模拟材料的非均匀性,这 种确定性模型无法反映材料性质的随机性。需要建立新的模型对材质非 均匀轴类零件的力学性能进行分析计算,以便给出比较可靠的结构安全 设计。本文结合统计技术建立了新的轴类零件计算模型,采用有限元方 法模拟了汽车轴类零件的材质非均匀力学特性。模拟方法对非均匀力学 的数值模拟有一定的参考意义,模拟结果对于工程计算和提高整车可靠 性具有一定的指导作用。 在分析了汽车轴类零件常见材质非均匀特征的基础上,推导了表征 非均匀特征的刚度矩阵和有限元方法。通过一定的简化,利用 UG 和 ANSYS 软件建立了轴类零件的模型并进行了网格划分。 单元的弹性模量 和泊松比由按照统计分布生成的相应离散序列随机地确定以反映材料性 质的非均匀性。 对该模型施加适当的约束和载荷,通过预前共轭梯度法,计算得到 了轴类零件在常见工况-弯曲和扭转载荷作用下的位移、应力、应变等力 学特性。结果表明:杨氏模量的非均匀对轴的总位移影响较小,对轴的 应力、应变影响较大;材料性质越不均匀,轴的最大应力越大,整体性 能越差;材料性质的不同概率分布对最大应力的影响存在一定的差别。 基于应力分析结果, 通过 ANSYS/Workbench 软件, 计算得到了材质
车架有限元分析

1前言车架是汽车的主要部件。
深人解车架的承载特性是车架结构设计改进和优化的基础。
过去汽车设计多用样车作参考,这种方法不仅费用大,试制周于精确解。
因此,正确建立结构的力学模型,是分析期长,而且也不可能对多种方案进行评价。
现代车架设计已发展到包括有限元法、优化、动态设计等在内的计算机分析、预测和模拟阶段。
计算机技术与现代电子测试技术相结合已成为汽车车架研究中十分行之有效的方法。
实践证明,有限元法是一种有效的数值计算方法,利用有限元法计算得到的结构位移场、应力场和低阶振动频率可作为结构设计的原始判据或作为结构改进设计的基础。
2车架的静态分析力学模型的选择有限元分析的基本思想,是用一组离散化的单元组集,来代替连续体机构进行分析,这种单元组集体称之为结构的力学模型;如果已知各个单元体的力和位移(单元的刚度特性),只需根据节点的变形连续条件与节点的平衡条件,来推导集成结构的特性并研究其性能。
有限元的特点是始终以矩阵形式来作为数学表达式,便于程序设计,大量工作是由电子计算机来完成,只要计算机容量足够,单元的剖分可以是任意的,对于任何复杂的几何形状,多样化的载荷和任意的边界条件都能适应。
然而,由于有限元是一种数值分析方法,计算结果是近似解,其精度主要取决于离散化误差。
如果结构离散化恰当,单元位移函数选取合理,随着单元逐步缩小,近似解将收敛于精确解。
因此,正确建立结构的力学模型,是分析工作的第一步目前采用有限元分析模型一般有如下两种:梁单元模型和组合模型等。
梁单元模型是将车架结构简化为由一组两节点的梁单元组成的框架结构,以梁单元的截面特性来反映车架的实际结构特性。
其优点是:划分的单元数目和节点数目少,计算速度快而且模型前处理工作量不大,适合初选方案。
其缺点是:无法仔细分析车架应力集中问题,因而不能为车架纵、横梁连接方案提供实用的帮助。
组合单元模型则是既采用梁单元也采用板壳单元进行离散。
在实际工程运用中,由于车架是由一系列薄壁件组成的结构,且形状复杂,宜离散为许多板壳单元的组集,其缺点是前处理工作量大,计算时间长,然而随着计算机技术的不断发展,这个问题已得到了较好的解决,而且由于有大型有限元软件支撑,巨大的前处理工作量绝大部分可由计算机完成,也不是制约板壳元模型实际运用的困难了。
有限元分析法在汽车后备箱盖冲压成形中的应用
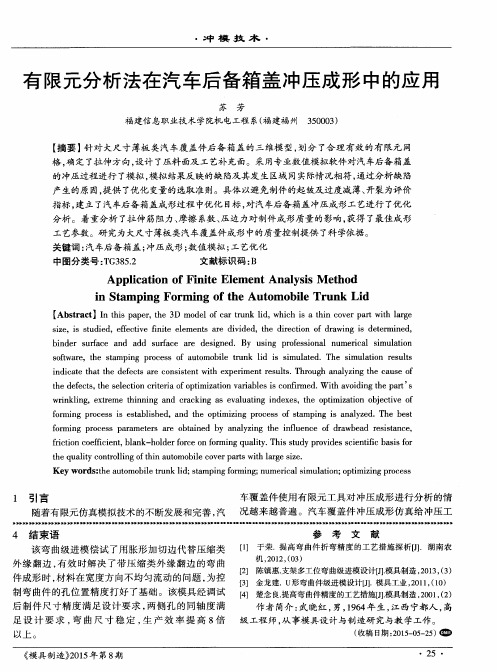
i n S t a mp i n g Fo r mi n g o f t h e Au t o mo b i l e Tr u n k Li d
【 A b s t r a c t 】 I n t h i s p a p e r , t h e 3 D m o d e l o f c a r t r u n k l i d , w h i c h i s a t h i n c o v e r p a r t w i t h l a r g e
f o r mi n g p r o c e s s i s e s t a b l i s h e d ,a n d t h e o p t i mi z i n g p r o c e s s o f s t a mp i n g i s a n a l y z e d . T h e b e s t f o m i r n g p r o c e s s p a r a me t e r s a r e o b t a i n e d b y a n a l y z i n g t h e i n l f u e n c e o f d r a wb e a d r e s i s t a n c e ,
f r i c t i o n c o e ic f i e n t , b l a n k - h o l d e r f o r c e o n or f mi n g q u a l i t y . T h i s s t u d y p r o v i d e s s c i e n t i f i c b a s i s f o r
汽车白车身检具精度有限元分析

z z z PsgiolePfrp
Equipm ent M anufacturing Technology No.07,2016
首先测量检具底板的平面度 (检具 出厂要求 为平 面 挠度 。通 过增 加 可 以调整 高 度 的支撑 点后 ,上 下调 整
度 ≤0.15 mm,仅 针 对 该 检具 )。实 际 测 量平 面度 为 底 板 的平 面 度 ,最 终使 检 具 的底 板 平 面度 可 以调 整
所 示 ,整 个 检具 底 板 结构 在 支 撑脚 的作 用 下 ,将 整个 3 国 内测 量 技 术 发 展 展 望 检 具 底板 结 构 视 为 简支 梁 结构 。根 据 简支 梁 在均 布
荷 载 下 的最 大 挠度 在 跨 中【l1,根 据简 支 梁挠 度 的计算 公 式 : y一 =5q14/(384EI),式 中 :y一 为 梁跨 中的 最 大 挠 度 (mm),q为 均 布线 荷 载标 准 值 (kN/m),E为 钢 的弹性 模量 ,,为 钢 的截 面惯 矩 (mm ),可 在 型钢 表 中 查得 。根据计算公式可知 ,当 f减小时 ,即跨度减小
(1)合 理 设 计 检 具 结 构 ,在 设 计 时 ,应 用 有 限 元 仿真分析 ,优化检具结构 ,提高检具 的刚度 。如底板 的框架结构可以参考桁架结构 ,因桁架结构刚性好 , 在起 重机 中广泛应 用 [21。
(2)提高检具的制造质量 ,特别是焊接质量及热
实际测量检具的位移变化量要 比仿真结果 的位 处 理 质 量 ,减 小检 具 本 体 内部 应 力 ,减 小检 具 本 体 的 移量更大 ,实际应用的环境复杂 ,很多因素均会影 响 变形 量 。
根 据检 具 的 布置情 况 ,近似 为 均布 载荷 。如 图 1
汽车有限元法
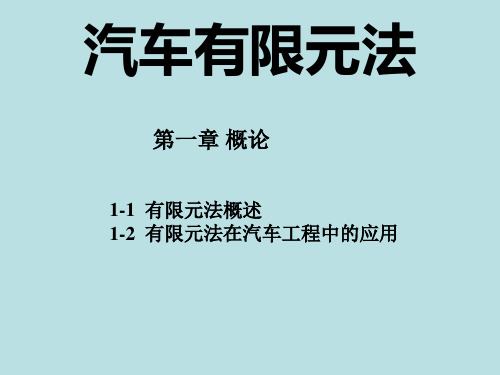
• 常用大型通用有限元软件
ADINA、 ABAQUS、 ANSYS、 MSC/Marc、 MSC/Nastran
• 一些专用有限元软件
LS_DYNA、 PAM-CRASH、 MSC/Dytran (碰撞) Autoform、 DYNAFORM、、PAM-STAMP(冲压)、 DEFORM(体积成形)、 SysWeld(焊接) MOLDFLOW(注塑)、 ProCast (铸造)、AdvantEdge (切削) SimFact(体积成形)
结构有限元模型
结构有限元模型实例
结构有限元模型实例
结构有限元模型实例
结构有限元分析重要性
汽车CAE技术的应用面向整车开发的 全过程,在汽车开发过程(概念设计-详细 设计-样机验证-定型生产)中实现全过程、 整车及部件级虚拟样机仿真,减少原型车 试验次数,降低生产成本、缩短新车研发 周期。随着CAE应用深度及广度的提高, 实现CAE工作的规范化和制度化是提升企 业的技术能力和市场竞争力的有力保证。
• 一个新产品的问题有60%以上可以在设计阶段消 除,如果人们有先进的精确分析手段。
• 目前,国际上有90%以上的机械产品和装备都要 采用有限元方法进行分析,进而进行设计修改和 优化。
• 有限元分析已成为替代大量实物试验的数值化 “虚拟试验”,基于该方法的大量计算分析与典 型的验证性试验相结合可以做到高效率和低成本。
52
55
55 55 51
有限元软件的主要发展趋势
– 并行运算 – 单元库、材料库 – 多物理场耦合、多体耦合、多尺度耦合分析 – 增进前后处理能力及与CAD软件的集成技术 – 优化技术
有限元分析的作用及地位
• 现代工业的进步,完全得力于计算机科技 的突飞猛进。将计算机、计算机软件应用 于产品的开发、设计、分析与制造,已成 为近代工业提升竞争力的主要方法。
- 1、下载文档前请自行甄别文档内容的完整性,平台不提供额外的编辑、内容补充、找答案等附加服务。
- 2、"仅部分预览"的文档,不可在线预览部分如存在完整性等问题,可反馈申请退款(可完整预览的文档不适用该条件!)。
- 3、如文档侵犯您的权益,请联系客服反馈,我们会尽快为您处理(人工客服工作时间:9:00-18:30)。
车辆薄板有限元分析中的多因子不完全分解预处理解法姚 松 田红旗1中南大学轨道交通安全教育部重点实验室,湖南长沙,410075dynacn@摘要:薄板是轨道车辆结构的主要形式,本文基于离散Kirchhoff 假设的DKT 弯曲板单元推导了四边形弯曲板单元DKQ 的构造过程,并进一步阐述了用于一般薄板问题分析的平板单元的构造。
提出了一种“多因子不完全分解” 的预处理方法,与共轭梯度迭代法结合能够大大加快薄板问题大型稀疏方程组的收敛速度,经过数值试验,说明该方法是稳定可靠的。
该方法避免了常规不完全分解不适用于薄板这样的 “病态”结构的情况。
在此基础上,编写了一般薄板问题分析的有限元程序,程序对结构刚度矩阵采用压缩存贮的方法,节约了大量内存空间。
本文还对分解算法中的可选参数进行了优化研究。
通过一个数值试验,本程序计算结果与商业有限元软件ANSYS5.7的结果完全一致。
关键词:薄板结构,DKQ 单元,预处理,不完全分解,共轭梯度法1 概 述有限元单元法已经成为结构分析的重要方法,薄板结构是轨道车辆的主要结构形式,因此薄板结构有限元分析已成为车辆结构分析中的重大课题。
早期的弯曲板单元大多基于经典的薄板理论,在以该理论为基础的板单元的能量泛函中,包含位移的二阶偏导数,要求位移为类连续。
这给构造板单元带来了困难,由此研究人员将注意力转向了中厚板单元,大多采用中厚板理论,其能量泛函仅包含位移的一阶导数,只要求位移是类连续,但是用厚板理论建立的单元仅对中厚板有效,当板逐渐变薄时,单元刚度矩阵中的剪切项占主导地位,计算出的弯曲变形远小于实际变形;当板非常薄时,求得的位移趋向于零,从而产生了“剪切闭锁”现象。
1C issner Mindlin Re −0C 基于离散的假设,通过挠度和转角分别独立插值,然后在若干个离散点上强迫挠度与转角满足薄板经典理论中的约束,构造出三角形(DKT )和四边形(DKQ )薄板弯曲单元,其泛函的表达式又回复为经典薄板理论的泛函表达式,又自然解决了“剪切闭锁现象”问题。
多个文献表明DKT 元与DKQ 元在求解薄板弯曲问题时都显示出良好的性能,具有较高的精度。
在对实际车辆结构进行有限元分析时,由于结构受力复杂,在承受板平面内的载荷的同时,也有可能板平面外的载荷,因此在进行分析时所采用的平板单元是平面应力单元与DKT 弯曲单元的组合而成。
由于三角形平面应力单元为常应变单元,为了提高分析的精度,在本文中我们讨论由四边形膜单元和DKQ 单元组合而成的平板单元。
Kirchhoff Kirchhoff1 教育部博士点基金(20020533007)项目资助1采用有限元法求解薄板弯曲问题最终归结为求解一组稀疏对称正定的线性方程组,,b u K =⋅K 为整体刚度矩阵,为待求解的位移向量,b 为载荷向量。
有限元求解主要分为直接求解器和迭代求解两大类u [1-2],直接求解是当前应用最为广泛的求解技术,其存贮方案多采用一维变带宽,通过对总体刚度矩阵直接进行或分解,然后再回代求解,采用这类技术经过长期使用比较成熟,但是该方法的劣势在于:分解后不再是稀疏矩阵,在分解的过程中会产生大量的“填入”元,因此对于大型稀疏矩阵的分解不仅耗费时间,而且占用内存。
在求解大型结构问题时速度比较缓慢,而且所需存贮空间和计算量随结构规模增大而急剧增加,以致于限制了求解规模。
T LL TLDL L Cholesky 对于象整车结构分析问题,有限元离散方程组的阶数可以达到几十万阶,采用迭代算法可以仅仅保存刚度矩阵中的非零元素,由给定初值通过若干迭代步骤获得满足一定精度的近似解。
传统的迭代法包括:,Jacobi seidel Gauss −,SOR 等等,这些方法收敛速度过慢而且没有保证,实际运用不多。
以预条件共轭梯度法[4-11](preconditioned Conjugate Gradient Method ,简称为PCG )为代表的迭代法是近十几年来逐渐兴起并开始得到应用的一类迭代方法,PCG 法的基础是共轭梯度法(CG ), CG 方法的收敛速率取决于条件数,当矩阵K 的条件数接近1时,CG 法的迭代速度很快,而当矩阵K 的条件数()210>K Con 时,CG 法的迭代就非常慢。
为了提高收敛速度,必须通过使用预条件技术把原先的方程组转换成一个等价的,但是系数矩阵条件数更小、更易于收敛的方程组。
即选择对称正定矩阵M ,考虑等价方程,若b M Ku M 11−−=K M 1−的条件数比K 要好的话,再运用CG 法求解收敛速度就会很快,问题的关键是如何选取M ,使得谱条件数能够得到较大改善。
在本文中针对薄板这样的病态问题提出了一种预条件器。
2 多因子不完全分解预处理算法Meijerink 和于1977年基于“不完全” 分解提出了预条件算子Vorst der van Cholesky M ,T L D L M ⋅⋅=,其中矩阵为单位下三角阵,,L ()()⎪⎩⎪⎨⎧==≠≠==00001ij ij ij K if K if j i L ()0≠=ij ij ij K if K M ,D 为对角矩阵,该方法对于对称正定且对角占优的矩阵比较有效,能够大大提高CG 法的收敛速度,计算又非常简单。
但是对于薄板这样的“病态”结构,刚度矩阵并不是严格的对角占优矩阵,在分解过程中矩阵的对角线元素可能会出现负值,从而不能保证预条件矩阵D M 为正定矩阵。
在本文中针对薄板问题提出了如下的“多因子不完全分解法”[3]。
将K 矩阵分解为对角矩阵和非对角矩阵的叠加,B D K −=,其中矩阵为D K 矩阵的对角矩阵,构造出下式:()()FBF B FBF D K −−−=,其中:,(),其中为可选择的参数乘子。
记矩阵i d n d d d d diag F L L 321,,=10<<i d 2()FBF D −为W ,可以看到:()ij j i ij n k n m mj km ik ij ij ij ij B d d D F B F D FBF D W −=−=−=∑∑==11由上式可以得到:,可以看出W 与有相同的稀疏结构,其对角元素与矩阵相同,在非对角元素上由于有和两个小乘子,因此有。
因此矩阵也是一个对称正定矩阵。
的计算公式如下:⎩⎨⎧≠==j i K d d j i D W ijj i ii ij A A i d j d ij ij A W <W i d 1,11>=t td 为可选择参数 对: n i ,,2L =∑−==1122i m mm im m a K d s ,若2t K s ii >,则有s K t d ii i 1=,若2t K s ii ≤,则t d i 1= 当K 对称正定,在的情况下,W 的不完全分解存在,记为,1>t E L L W T−⋅⋅=σE 为误差矩阵,且对角元素i σ均大于零。
那么有()()FBF B E L L FBF B W K T −+−⋅⋅=−−=σ,将的不完全分解也可作为总体刚度矩阵W T L L ⋅⋅σK 的不完全分解,而且由于对角元素i σ均大于零,该分解可以作为预条件算子,其算法如下:111W =σjj m jm m im ij ij L L W L σσ⎟⎟⎠⎞⎜⎜⎝⎛⋅⋅−=∑−=11 m i m im ii i L W σσ⋅−=∑−=112得到上述预条件矩阵后,将薄板结构有限元方程转化为:,其中,,,通过这样的变换,由于误差矩阵的忽略,实际上T y C =⋅()TL K L C 111−−−⋅⋅⋅=σx L y T ⋅=b L T ⋅⋅=−−11σ(FBF B E −+)I C ≠,但是其条件数与K 相比有明显改善。
以上述变换公式代入CG 方法,即可以求出结构位移向量,流程如下:00x K b r ⋅−=, 为第一次迭代值的余差010r M p ⋅=−0r 0x 那么第次迭代为:k ()()()k T k k T k k p K p p r ⋅⋅=αk k k k p x x ⋅+=+α1 k k k k p K r r ⋅⋅−=+α1()(()())k T k k T k k r r r r ⋅⋅=++11β k k k k r r p ⋅+=++β11迭代过程直至和二者的差别“足够”小时,计算过程就收敛了。
1+k x k x 3从上面的流程可见,整个计算流程只要求计算刚度矩阵K 与一个列向量的乘积,而刚度矩阵K 对称而且各行的零元素对于乘积是没有任何贡献的,因此可以按照压缩存贮的格式将整体刚度稀疏矩阵的下三角矩阵“按行或按列”的方式压缩存贮,在本文中采用了实数型数组存放非零元素的值,整型数组存放非零元素所在的列,整型数组存放“每一行或每一列”起始非零元素的位置,其中为结构刚度矩阵下三角矩阵中非零元素的总数,ND 为结构总自由度数。
采用这样的压缩存贮方式能够最大限度地节约内存空间。
)(NZ stiffvalue )(NZ newcolumn )1(_+ND lower total NZ 3 DKQ 弯曲板单元及平板单元DKQ 四边形弯曲板单元基于四个DKT 三角形弯曲板单元[12],如下图1所示:图1 DKQ 单元 图2 DKT 单元根据虚功原理,四边形单元(1234)的虚功可以由上图所划分的①、②、③、④四个三角形的虚功相叠加之后除2。
因此DKQ 单元的构造是通过组成四边形的四个三角形DKT 单元的构造组集以后得到。
DKT 单元采用和w x θ,y θ的独立插值,w 和x θ,y θ之间的约束方程通过在三角形的三个角节点和三个中节点位置强迫实现,因此其泛函表达式恢复为经典薄板理论的泛函表达式:∫∫∫∫ΩΩ⋅⋅−⋅⋅⋅=Πdxdy w q dxdy D T κκ21, κ为板弯曲的广义应变 每个角节点有参数,i w xi θ,yi θ()3,2,1=i ,一共9个自由度构成单元的节点位移向量,边中节点有参数xi θ,yi θ()6,5,4=i ,直法线的假设通过下述方式引入:Kirchhoff 在角节点:(3,2,100=⎪⎪⎩⎪⎪⎨⎧=−⎟⎟⎠⎞⎜⎜⎝⎛∂∂=−⎟⎠⎞⎜⎝⎛∂∂i y w x w yi i xi i θθ) 在中间节点:()()6,5,4210=⎪⎪⎩⎪⎪⎨⎧+==−⎟⎠⎞⎜⎝⎛∂∂k s w nj ni nk sk k θθθθ 通过约束条件将各边中间节点的转角参数“凝聚”掉,不但提高了位移场的精度,而且保证了相邻单元之间的协调性。
将弯曲板单元和平面膜单元组合起来就得到了平板单元的单元刚度矩阵,在局部坐标系中,节点位移参数本不包含zi θ,但是为了进行总刚集成时避免共面单元组集后出现zi θ方向刚度为零的情况,在组合过程中给zi θ方向赋予单位刚度,组集过程如下图3:4图3 板单元刚度组集示意图图4 薄板例题4 数值试验针对薄板有限元问题,本文编制了一个有限元程序,该程序采用压缩存贮的方法,将整体刚度矩阵中的非零元素存贮在三个一维数组中。