潜在危害和显著危害的正确判断
HACCP判断树

危害风险分析和CCP判断一、风险评估方法 Risk assessment methos.可能性判断 likelihood危害的严重性 severity页脚内容1风险评估参照表 Risk assessment table风险结果判定为6以上的危害为显著危害。
(包括6)针对显著危害用判断树进行分析,该控制措施是HACCP计划还是OPRP。
其他用前提方案进行管理。
页脚内容2二、风险分析结果判定原辅料:页脚内容3页脚内容4生产过程页脚内容5页脚内容6页脚内容7页脚内容8页脚内容9其他页脚内容10页脚内容11页脚内容12三、控制措施分类判断树(一)原辅料•针对每个显著危害(危害分析单)的步骤的每个危害回答以下问题。
•Q1 的回答参考危害分析的结果. •Q2 – Q5 按照控制措施是需要通过OPRP 还是HACCP 计划进行管理,分类控制措施 •在Q3中,针对危害严重性的控制措施如属于前提方案的范畴,则该措施直接判断为OPRP13包材:生物危害生产用水:生物危害页脚内容1415原料低温豆粕化学危害:农残页脚内容16原料豆粕、辅料盐酸液碱、蛋白酶、、蛋白酶、包材化学危害:重金属入库储存低温豆粕、包装袋:致病菌危害页脚内容18页脚内容19页脚内容20(二)生产过程 设备管道清洗杀菌前致病菌危害:一萃、二萃、酸沉、分离、解碎、中和、A 液过滤等化学危害:润滑油页脚内容22微生物危害:高温瞬时杀菌页脚内容24页脚内容25干燥换热器化学危害:导热油页脚内容26干燥、产品冷却空气:生物危害页脚内容27页脚内容28页脚内容29磁力棒成品包装:生物危害页脚内容31页脚内容32成品包装:化学危害印油、缝纫机油成品包装:金属探测页脚内容34产品储运:生物危害、化学危害、物理危害页脚内容35页脚内容36玻璃及易碎品的控制页脚内容37页脚内容38废弃物的控制:页脚内容39工具:页脚内容40页脚内容41虫害:页脚内容42人员:页脚内容43页脚内容44有毒有害化学物质:页脚内容45(四)PRP、OPRP OR CCP:页脚内容46页脚内容47页脚内容48。
HACCP计划(漂烫)
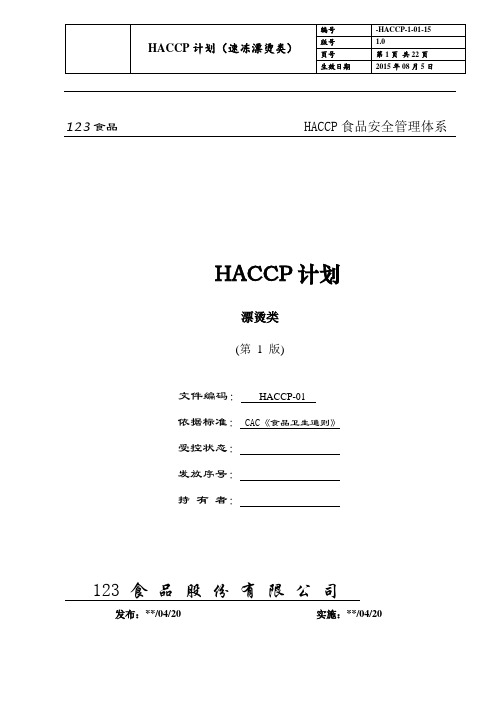
123食品HACCP食品安全管理体系HACCP计划漂烫类(第1 版)文件编码:HACCP-01依据标准: CAC《食品卫生通则》受控状态:发放序号:持有者:123食品股份有限公司发布:**/04/20 实施:**/04/20目录一、颁布令二、企业简介三、公司组织机构图四、术语五、HACCP小组成员及其职责六、产品描述七、加工概述八、工艺流程图九、生产工艺流程图现场验证十、危害分析工作单十一、HACCP方案表十二、纠偏行动十三、HACCP计划的验证十四、 HACCP计划的审核十五、HACCP计划验证程序一发布令为提高**123食品股份有限公司速冻果蔬产品生产的安全管理,持续稳定的生产出高质量、安全卫生的食品,增进顾客满意度,公司依据食品法典《CAC 食品卫生通则》、《危害分析与关键控制点(HACCP)体系及其应用准则》,结合公司速冻果蔬产品安全管理的实际,制定**123食品股份有限公司速冻果蔬产品HACCP计划,它是公司速冻果蔬产品生产的质量管理和改进的保证,是公司速冻果蔬产品食品安全的保证,是进行食品安全质量审核、评审的依据。
经审定,本计划符合公司速冻果蔬产品食品安全管理体系管理的实际情况,可作为公司食品安全管理体系必须遵守的纲领性文件,现予以公布,自发布之日起实施,公司全体人员必须严格执行。
总经理:日期:**年04月20日二企业简介**123食品股份有限公司,位于*****的综合性食品加工企业,成立于2**年,注册资本***万元,资产总额**亿元。
公司占地面积1**万平方米,现有职工**人,拥有**万吨冷库、1**0吨冷风库,半自动化流水线*条,年加工速冻果蔬1**万吨,保鲜果蔬**吨,自有种植农场1**亩。
公司生产的**个品种,主要出口美国、加拿大、德国、英国、俄罗斯、日本等国家和地区。
*司已获得HACCP、BRC、KOSHER、ISO22000认证证书。
*秉承“质量第一、服务至上、从绿色中来,到社会中去、取之于社会,回报于**”的经营理念,热情欢迎海内外客商。
23巧克力生产危害分析

2.3 巧克力生产危害分析
巧克力生产的危害分析如表1所示:
表1:巧克力生产危害分析表
根据巧克力生产过程中的潜在危害分析,确定原辅料验收、内包装材料验收、精磨、金属探测等4个步骤为巧克力生产过程的关键控制点(CCP)。
2.4 巧克力生产的HACCP计划
通过对上述危害点的分析,根据国家GB19343或国际标准、相应的法律法规、检验结果以及相关的技术资料设定关键限值,确定各CCP的控制程序及纠偏措施,具体内容见表2。
表2:巧克力生产的HACCP计划表
2.5 巧克力生产HACCP计划的执行及记录系统
在巧克力生产加工过程中,应严格按照HACCP计划表的要求执行,做好相应的记录,验证纠偏措施的及时性和实施效果,考察计划表是否合理且切实可行,产品的质量安全是否得到了有效的控制。
同时根据实际情况,决定是否需要对危害分析和HACCP计划表做适当调整,使之更有效运行,迸一步保证产品的质量和安全根据关键控制点的。
HACCP体系如何进行危害分析

HACCP体系如何进行危害分析?原理一:危害分析和确定预防措施食品安全危害:指引起人类使用食品不安全的任何生物的、化学的、物理的特性和因素。
显著危害:有可能发生,可能对消费者造成不可接受的风险。
潜在危害显著性的三个例子1.大肠杆菌O157:H7(失控则产生)2.玻璃(发生的几率低,但后果严重)3.棒曲霉毒素(慢性中毒,但发生的频率高)*极可能发生的危害至少应考虑到:(1)微生物污染;(2)寄生虫;(3)化学污染;(4)法律不允许使用的杀虫剂残留;(5)腐败产生的危害;(6)天然毒素;(7)不允许用于食品的添加剂和色素;(8)未声明的可能引起过敏反应的成分;(9)物理危害*产品风险分类:第一级- 低度风险,主要包括原材料;第二级- 中度风险,包括半成品和货架食品;第三级- 高度风险,即食食品*危害分析的工具:思维风暴(Brainstorm);多角度、反复;风险评估*当产品或加工发生变化,都必须重新进行危害分析。
这种变化可能包括、但不限于:- 因为原料或原料来源;- 产品配方、工艺的设计;- 加工方法或系统;(加工中每一步骤;加工间、设备的设计和布局)- 产量;- 包装;- 卫生方面;- 成品流通系统;- 成品的预期使用或消费的变化。
*高风险食品:容易支持产毒型和感染型微生物繁殖生长的一类食品;高蛋白、高水分、高PH的食品;加工、处理的时间长、温度高;即食食品*危害分析:与产品、工艺有关——显著危害、CCP、HACCP 计划与人员、环境有关——SSOP 计划*危害分析表1、加工步骤2、确定本步引入、控制或增加的危害3、潜在的食品安全危害显著吗?4、说明对第3栏的判断依据5、应用什么预防措施来防止危害?6、本步骤是关键点控制码?原理二:确定关键控制点*关键控制点:能实施控制,从而对食品安全的危害加以预防、消除或把其降低到可接受水平的加工点、步骤或工序。
HACCP小组应明确加工中的每一步骤是否是关键控制点一种危害可以有一个以上的关键控制点来控制,同样地,一种以上的危害可以有一个关键控制点来控制。
危害分析
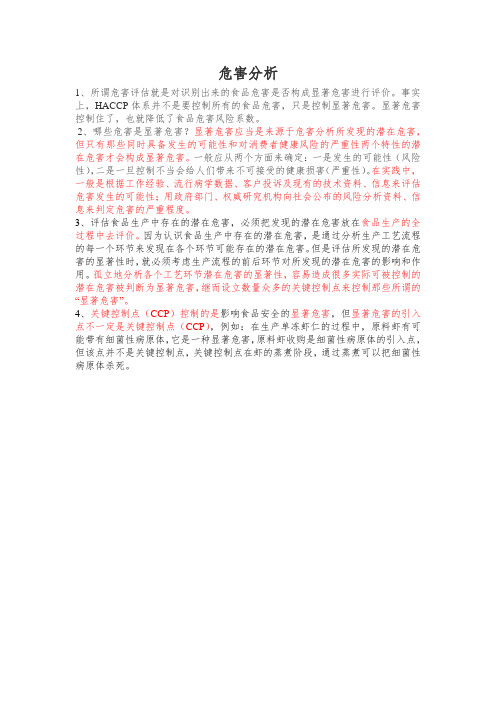
危害分析
1、所谓危害评估就是对识别出来的食品危害是否构成显著危害进行评价。
事实上,HACCP体系并不是要控制所有的食品危害,只是控制显著危害。
显著危害控制住了,也就降低了食品危害风险系数。
2、哪些危害是显著危害?显著危害应当是来源于危害分析所发现的潜在危害,但只有那些同时具备发生的可能性和对消费者健康风险的严重性两个特性的潜在危害才会构成显著危害。
一般应从两个方面来确定:一是发生的可能性(风险性),二是一旦控制不当会给人们带来不可接受的健康损害(严重性)。
在实践中,一般是根据工作经验、流行病学数据、客户投诉及现有的技术资料、信息来评估危害发生的可能性;用政府部门、权威研究机构向社会公布的风险分析资料、信息来判定危害的严重程度。
3、评估食品生产中存在的潜在危害,必须把发现的潜在危害放在食品生产的全过程中去评价。
因为认识食品生产中存在的潜在危害,是通过分析生产工艺流程的每一个环节来发现在各个环节可能存在的潜在危害。
但是评估所发现的潜在危害的显著性时,就必须考虑生产流程的前后环节对所发现的潜在危害的影响和作用。
孤立地分析各个工艺环节潜在危害的显著性,容易造成很多实际可被控制的潜在危害被判断为显著危害,继而设立数量众多的关键控制点来控制那些所谓的“显著危害”。
4、关键控制点(CCP)控制的是影响食品安全的显著危害,但显著危害的引入点不一定是关键控制点(CCP),例如:在生产单冻虾仁的过程中,原料虾有可能带有细菌性病原体,它是一种显著危害,原料虾收购是细菌性病原体的引入点,但该点并不是关键控制点,关键控制点在虾的蒸煮阶段,通过蒸煮可以把细菌性
病原体杀死。
酱油生产HACCP体系的建立
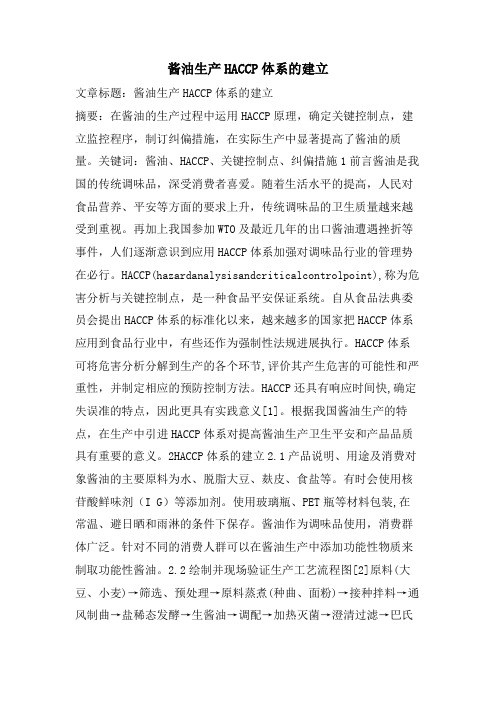
酱油生产HACCP体系的建立文章标题:酱油生产HACCP体系的建立摘要:在酱油的生产过程中运用HACCP原理,确定关键控制点,建立监控程序,制订纠偏措施,在实际生产中显著提高了酱油的质量。
关键词:酱油、HACCP、关键控制点、纠偏措施1前言酱油是我国的传统调味品,深受消费者喜爱。
随着生活水平的提高,人民对食品营养、平安等方面的要求上升,传统调味品的卫生质量越来越受到重视。
再加上我国参加WTO及最近几年的出口酱油遭遇挫折等事件,人们逐渐意识到应用HACCP体系加强对调味品行业的管理势在必行。
HACCP(hazardanalysisandcriticalcontrolpoint),称为危害分析与关键控制点,是一种食品平安保证系统。
自从食品法典委员会提出HACCP体系的标准化以来,越来越多的国家把HACCP体系应用到食品行业中,有些还作为强制性法规进展执行。
HACCP体系可将危害分析分解到生产的各个环节,评价其产生危害的可能性和严重性,并制定相应的预防控制方法。
HACCP还具有响应时间快,确定失误准的特点,因此更具有实践意义[1]。
根据我国酱油生产的特点,在生产中引进HACCP体系对提高酱油生产卫生平安和产品品质具有重要的意义。
2HACCP体系的建立2.1产品说明、用途及消费对象酱油的主要原料为水、脱脂大豆、麸皮、食盐等。
有时会使用核苷酸鲜味剂(I G)等添加剂。
使用玻璃瓶、PET瓶等材料包装,在常温、避日晒和雨淋的条件下保存。
酱油作为调味品使用,消费群体广泛。
针对不同的消费人群可以在酱油生产中添加功能性物质来制取功能性酱油。
2.2绘制并现场验证生产工艺流程图[2]原料(大豆、小麦)→筛选、预处理→原料蒸煮(种曲、面粉)→接种拌料→通风制曲→盐稀态发酵→生酱油→调配→加热灭菌→澄清过滤→巴氏灭菌→装瓶→成品2.3危害分析危害分析需要对酱油生产的各个环节进展分析,包括原料接收贮存、原料蒸煮、制曲、发酵、提取、配兑、灭菌和灌装等各个环节可能存在生物、化学、物理的危害及危害产生的原因,针对造成这些危害的原因制定出预防控制措施。
显著危害的概念

显著危害的概念显著危害是指可能对个体、群体或环境造成严重伤害或损失的潜在危险。
这个概念通常用于描述或评估有潜在风险的活动、产品、技术或其他因素。
显著危害通常包括风险严重程度高、潜在影响范围广、持续时间长、难以修复或逆转等特征。
以下将详细探讨显著危害的概念及其在不同领域中的应用。
首先,显著危害的概念在环境领域中尤为重要。
许多人类活动如工业生产、化石燃料的使用、森林砍伐等都对自然环境产生显著危害。
例如,大气中排放的废气和二氧化碳会导致气候变化,引发极端天气事件和全球海平面上升的风险。
水体被污染也会影响人类和其他生物的健康,破坏水生生态系统。
同时,土地开垦和过度开采对生物多样性和生态系统的破坏也是显著危害的表现。
因此,环境保护和可持续发展的重要目标之一就是减少或消除对环境造成显著危害的活动。
其次,显著危害的概念在工业安全和职业健康领域也有重要应用。
许多工业过程和职业环境中都存在着一些潜在的危险因素,例如有毒化学物质、高温、高压、噪音等。
这些危险因素如果没有得到妥善管理,可能会对工人的健康和安全产生显著危害。
例如,长期接触有毒化学物质可能导致慢性中毒,而高温和高压可能导致火灾、爆炸和严重的身体伤害。
因此,工业企业和雇主需要采取必要的措施来减轻这些显著危害,例如提供个人防护装备、进行培训和监测等。
此外,在社会领域中也存在着许多与显著危害相关的问题。
例如,恶劣的社会环境和生活条件会对居民的健康和安全产生显著危害。
例如,恶劣的住房条件、滥用毒品和犯罪率高的社区都可能对个体和家庭的福祉和安全产生负面影响。
此外,社会不平等和贫困也可以被视为一种显著的危害。
贫困与健康和教育不平等、社会排斥和社会不稳定等问题密切相关,对社会的稳定和发展构成显著危险。
最后,显著危害的概念在食品安全和医疗保健领域中也有重要意义。
食品安全是确保食品安全和卫生的重要任务,而显著危害是评估食品中可能存在的微生物、化学和物理污染物的潜在风险的重要标准。
危害分析及关键控制点

危害分析及关键控制点(Hazard Analysis & Critical Control Point, HACCP),是由食品的危害分析(Hazard Analysis, HA)和关键控制点(Critical Control Point, CCPs)两部分组成的一个质量保证系统的管理方式。
通过对食品的加工生产包括从原料到消费者的整个过程的危害控制,将食品安全卫生危害消除或降低至安全的水平。
HACCP的概念起源于廿十世纪五十年代,由美国航空航天局(NASA)与美国部队的Natick实验室共同提出,主要运用于航空制造工业,当时称为“故障类型与后果分析”。
1971年,Pillsbury公司(为美国太空计划提供食品的公司)、NASA 和Natick实验室联合提出了食品生产的过程控制推理方法,试图将零缺陷程序应用于宇航员食物的卫生质量控制,以确保宇航食品的安全。
当时,大多数食品的质量和安全性多以终产品检验方式检验,要确保食品的安全,就要扩大检验的范围甚至对所有的成品进行检验,结果能为宇宙飞行计划提供的食品已经很少了。
所以,要确保安全的维一方法,就是开发一个预防性体系,防止生产过程中危害的产生,这就促使HACCP的诞生。
目前已在越来越多的国家,尤其是发达国家的食品加工行业中得到采用,并且已经得到欧盟、美国、加拿大、澳大利亚、新西兰和日本等国家和地区食品卫生主管机构,以至联合国FAO/WHO的食品法典委员会的认可。
七十年代初,美国国家食品及药物管理局(FDA)要求罐头食品生产厂在产品加工过程中实施HACCP控制,1995年12月18日,FDA颁布了强制性的水产品HACCP法规(21CFR-123,1240)要求从1997年12月18日起所有对美国出口的水产品企业必须建立HACCP;2002年1月22日美国的果蔬汁产品的HACCP法规(21CFR-120)生效,欧共体从1994年开始要求水产品加工厂建立与HACCP等效的“自查系统”;日本厚生省先后制定了用于食用鸡、水产品等几十种食品生产加工的HACCP模式。
- 1、下载文档前请自行甄别文档内容的完整性,平台不提供额外的编辑、内容补充、找答案等附加服务。
- 2、"仅部分预览"的文档,不可在线预览部分如存在完整性等问题,可反馈申请退款(可完整预览的文档不适用该条件!)。
- 3、如文档侵犯您的权益,请联系客服反馈,我们会尽快为您处理(人工客服工作时间:9:00-18:30)。
潜在危害和显著危害的正确判断
上海出入境检验检疫局钟一亮
潜在危害和显著危害是危害分析的主要内容,也是选择关键控
制点的前提条件。
所谓的危害是指可引起人类食用不安全的任何生
物的、化学的或物理的特性和因素。
就HACCP 应用而言,危害仅指食品中能够导致人体伤害或损伤的污染和情况。
食品中出现的杂质(昆虫、头发、污物)、品质缺陷,只要这些缺陷不是直接地影响到食品的安全,一般不属于危害的范畴。
日常生活中诸如食品的腐败变质,细菌超标并不一定有危害。
而真正的危害是从结果来认定,
看看是不是最终造成安全问题,例如:肉毒杆菌食物中毒导致腹泻、呕吐、腹疼,严重时,呼吸道肌肉麻痹并导致死亡等。
在危害分析
中根据原理可分为潜在危害和显著危害,其中潜在危害的作用在于
其分析的充分性,由于在任何食品的加工操作过程中都不可避免地
存在一些具体危害,这些危害与所用的原料、操作方法、储存条件
及销售方式有关。
即使生产同类产品的企业,原料配方、工艺设备、加工方法、加工日期和储存条件有及操作人员的生产经验,知识水
平和工作态度等不同,各企业在生产加工过程中存在的危害也是不
同的,需要HACCP 小组针对实际情况查找潜在危害,由于分析性
的思维抑制创造性,HACCP 小组成员在受分析性或科学性的培训时,其横向思维和创造性思维有可能受到抑制,再加上小组成员对整个
生产过程非常熟悉并形成习惯性认识的情况下,难以对头脑中已有
的经验或知识提出质疑,因此为了达到潜在危害充分性的要求,要
鼓励小组成员大胆的想象,突破常规思维的局限,寻找的危害是否
正确并不重要,但决不放走一个危害,例如:在油炸食品的工艺中,
我们可以从食品原料本身的成分中分析,它是否有生物,物理化学
的危害,也可以从加工过程中分析是否遭到污染或油炸温度未到规
定要求可能会导致病菌残存,或最终产品不经过金探可能会导致物
理危害的遗漏等等。
但往往会忽视油炸过程中油的反复使用会造成
化学危害的问题,因此潜在危害在危害分析中的重点在于不能遗漏
危害,因为有可能漏掉的危害恰恰是重要的危害。
而危害分析过程中的显著危害是HACCP 控制的主要问题,因为不控制显著危害必将导致食品安全问题的出现。
显著危害的判断是
查找潜在危害为基础的,潜在危害的特点是发散而显著危害是潜在
危害的集中,具有可能性和严重性的潜在危害构成显著危害。
如果
潜在危害确实存在,但其不具有危害的严重性,就不能成为显著危害,同样具有严重性的潜在危害不存在,也就不能判断为显著危害,因此唯有同时具备可能性和严重性的潜在危害才能最终判为显著危害。
那么如何理解可能性和严重性呢?首先,可能性是指存在、具有
的意思。
严重性是指消费有该危害的产品后产生后果的严重程度,
如后遗症、疾病和伤害的程度和持续时间。
在实际的食品加工过程中,由于企业已建立了符合GMP 中有关卫生要求的SSOP,所以一
般认为与食品接触表面的交叉污染的问题,例如:毛发、苍蝇、冷凝
水污染、工器具消毒剂残留等,完全可通过SSOP 控制,因此问题存在的可能性不大,也不会造成严重的安全后果。
所以这些交。