甲烷化操作规程
化工公司合成工段操作规程(含甲烷化、冰机岗位)

化工公司合成工段操作规程工作流程(含甲烷化、冰机岗位)目录第一章规章制度一、安全生产基本要求【4】二、交接班制度【5】三、巡检制度【5】四、岗位责任制【6】第二章合成工序工艺流程简介一、合成工序的任务【6】二、工艺原理及流程简介【6】第三章工艺操作规程一、电器仪表的试运行【7】二、系统吹除方案【7】三、合成塔触媒装填方案【9】四、合成循环机试车方案【9】五、试气密试压及系统置换方案[10]六、升温还原方案(见触媒厂家升温方案)[10]七、工艺指标[10]八、正常操作要点[11]九、正常开停车步骤[111十、一般事故的判断与处理[12] 十一、事故危害及处理办法[13] 第四章应急事故处理措施一、事故应急处理措施[16]二、有毒有害物质及预防措施[17] 第五章安全规程一、安全操作规程[17]二、检修安全规程[18]三、防冻防凝安全规程[20]四、安全阀、压力表安全规程[21] 甲烷化工序操作规程第一章工艺简介一、主要任务[22]二、工艺流程[22]三、设备一览表[22] 第二章试车方案一、试车前的准备工作[23]二、吹除清扫方案[23]三、水压试验[24]四、仪表控制系统调试[25]五、单体试车[25]六、系统水联动试车[25] 第三章开车方案一、开车前的检查工作[25]二、开车前的准备工[25]三、开车前仪表控制系统的调试[26]四、系统置换[26]五、气密试验【26】六、开车步骤[27]七、生产控制[27]第四章正常开停车方案一、正常开车步骤[28]二、正常停车步骤【28】第五章安全注意事项一、本工段的主要有毒有害物质及防护措施[28]二、本工段试车过程中的安全注意事项[:28] 第六章冰机岗位操作规程本工序任务[28]二、正常操作规程【29】三.冰机注意事项[29]四、冰机岗位事故应急预防措施[29] 第七章合成工段各岗位工作流程(含甲烷化、冰机工序)合成工段主任工作流程【32】二.合成工段氨合成班长工作流程[33]三.合成工段氨合成主操作工作流程[35]四.合成工段氨合成副操作工作流程[36]五.合成工段氨合成分析工工作流程[37]六.合成工段冰机操作工工作流程[38] 第八章安全消防应急预案【39】第九章危化品事故应急预案[42]第一章规章制度一、安全生产基本要求1“安全生产,人人有责”,企业的各部门、各级负责人都要对分管部门的安全生产负责。
(完整版)甲烷化操作规程

甲烷化操作规程甲烷化岗位作业指导书拟稿:审核:批准:公布日期:目录一、岗位任务 (2)二、工艺指标(2)三、工艺原理及流程 (2)四、主要设备 (3)五、正常开车步骤(4)六、正常停车步骤 (5)七、紧急停车步骤 (5)八、异常现象及处理方法(5)九、安全注意事项(6)一、本岗位任务甲烷化岗位的主要任务:在适当的压力、温度、催化剂的作用下把甲醇后的CO和CO2与H2合成为CH4和H2O,并把H2O分离下来,把CO+CO2含量控制在25ppm以下,送往合成岗位。
二、工艺指标(一)新鲜气温度30-40℃(二)催化剂热点温度250℃± 5 ℃(三)甲烷化塔一入温度≤130℃(四)塔壁温度≤150℃(五)甲烷化塔二入温度250℃-270℃。
(六)甲烷化塔二出温度≤190℃(七)出系统CO+CO2含量≤25PPM三、工艺原理及流程(一)工艺原理:本工段主要作用是脱除工艺气的CO和CO2。
在催化剂的作用下使少量CO、CO2加氢生成CH4和H2O,把工艺气的CO和CO2的含量脱除到25PPM 以下.由于该反应是放热反应,本工段充分利用其反应热以加热合成塔入口气体.甲烷化催化剂是以镍为活性组分,以稳定活性氧化铝为载体。
反应原理:CO+3H2= CH4+H2O +206.24kJ/molCO2+4H2= CH4+2H2O +165.4kJ/mol(二)流程:1、工艺介质主流程:从压缩机六段来的氢氮气进油分离器,油水分离后气体进入预热器与合成塔出口气体进行热量交换,加热后经合成塔环隙进塔底换热器与出口气体进一步换热,然后出合成塔进加热器,经蒸汽加热后再经合成塔心管到内件顶部进触媒层进行反应。
出口气体经塔底换热器换热后进预热器管内继续换热,然后进水冷排冷却,再进水分离器分离水后送合成。
注:(1)入工段阀门处增设旁路,主要目的是开停车时使用老系统的精练气。
(2)系统入口阀门前接循环机来气管线;增设放空管线。
(3)去合成阀门前增设去甲醇管线,为甲醇开车使用。
甲烷化岗位操作规程
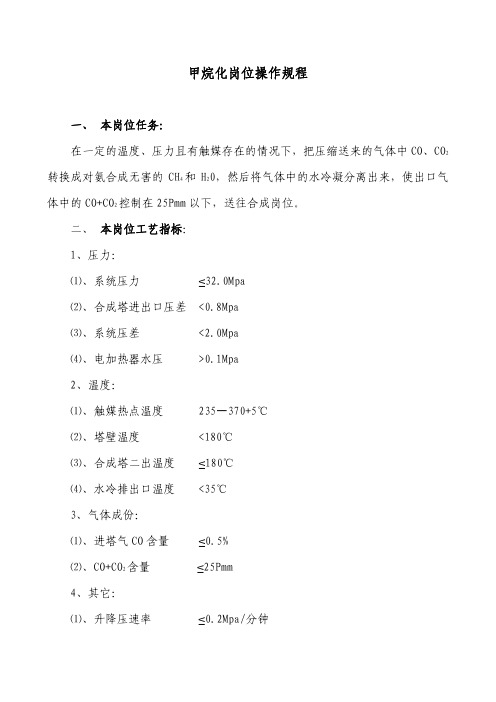
⑶活塞杆螺帽松动,连杆 车处理
轴瓦吻合不匀,十字头销 ⑵紧急停车处理
松动
⑶检修
⑷气缸余隙过小
9 循 环 机 油 泵 出 口 油 ⑴油过滤器堵塞
⑴清洗过滤器
⑵、合成塔进出口压差 <0.8Mpa
⑶、系统压差
<2.0Mpa
⑷、电加热器水压
>0.1Mpa
2、温度:
⑴、触媒热点温度
235—370+5℃
⑵、塔壁温度
<180℃
⑶、合成塔二出温度 ≤180℃
⑷、水冷排出口温度 <35℃
3、气体成份:
⑴、进塔气 CO 含量 ≤0.5%
⑵、CO+CO2 含量
≤25Pmm
⑴、打开付线阀,关闭出口阀,关闭进口阀,打开放空阀卸压。
⑵、停下循环机,关闭冷却水阀门。
七、本岗位常见事故及处理:
序号 发生现象
常见原因
处理方法
1 触 媒 层 温 度 增 高 过 醇后 CO、CO2 含量升高 ⑴加大副线流量,
快
调低电加热器电流
⑵启用循环机
⑶切气
2 触 媒 层 温 度 突 然 下 ⑴主线和副线气比例不 ⑴减少副线流量
②、立即与压缩岗位联系,停止送气。迅速关闭补气阀门。按紧急停车步 骤停循环机(如电加热器在用时,须先停用电加热器)。
③、迅速关闭系统进、出口阀门。 ④、按短期停车方法处理。 四、 本岗位安全操作规程: 1、严格按工艺开停车程序,不得超指标操作。 2、严格按工艺指标进行,不得超指标操作。 3、系统放空要缓慢,以免产生静电着火。 4、电机启动前注意盘车,并注意各电机电流、温升。 5、注意检查安全装置、压力表是否灵敏可靠。 6、严格按升降温速率升降温。 7、严格按升降压速率升降压。 8、加强岗位间联系,确保信号准确无误。 9、加强巡回检查。 五、本岗位正常操作要点: 1、触媒层温度的调节,使温度控制在指标以内,稳定其操作。 2、塔壁温度的控制,绝对不允许超指标操作。 3、CO+CO2 含量的控制。 4、系统压力的控制。 5、系统压差的控制。 六、本岗位主要运转设备的操作规程: 1、循环机开车:
甲烷化工艺流程

甲烷化工艺流程
《甲烷化工艺流程》
甲烷化工艺是一种将甲烷转化为更有用化学物质的过程。
甲烷是一种富含碳和氢的简单有机化合物,是天然气的主要成分。
甲烷化工艺可以将甲烷转化为甲烷醇、甲醛、丙烷等更有用的化学品。
甲烷化工艺通常包括以下几个步骤:
1. 蒸汽重整:甲烷和水蒸汽经过反应生成一氧化碳和氢气。
这一步骤是甲烷化工艺的起始阶段,产生的一氧化碳和氢气可作为后续反应的原料。
2. 甲烷蒸氨:甲烷和氨气在催化剂的作用下发生反应,生成甲胺。
甲胺可以用于生产甲胺醛等化学品。
3. 碳氢化合物的加氢:甲烷和氢气通过催化剂反应,生成其他碳氢化合物,如丙烷、丁烷等。
4. 甲基化反应:甲烷和一氧化碳在高温下发生反应,生成甲醇。
这是甲烷化工艺中的重要步骤,因为甲醇是一种重要的工业原料。
以上是甲烷化工艺的基本流程,通过不同的反应组合可以得到各种不同的化学品。
甲烷化工艺在化工领域具有广泛的应用,
不仅可以提高甲烷的利用率,还可以生产出更多有用的化学品,为化工行业的发展做出贡献。
甲烷化技术
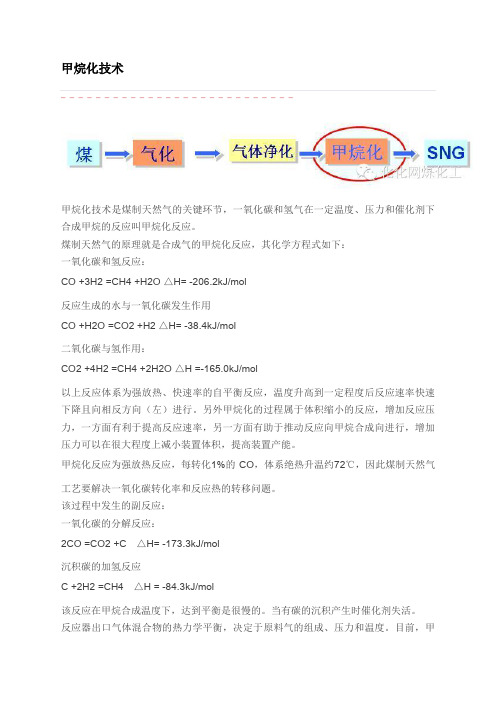
甲烷化技术¯ ¯ ¯ ¯ ¯ ¯ ¯ ¯ ¯ ¯ ¯ ¯ ¯ ¯ ¯ ¯ ¯ ¯ ¯ ¯ ¯ ¯ ¯ ¯ ¯ ¯ ¯甲烷化技术是煤制天然气的关键环节,一氧化碳和氢气在一定温度、压力和催化剂下合成甲烷的反应叫甲烷化反应。
煤制天然气的原理就是合成气的甲烷化反应,其化学方程式如下:一氧化碳和氢反应:CO +3H2 =CH4 +H2O △H= -206.2kJ/mol反应生成的水与一氧化碳发生作用CO +H2O =CO2 +H2 △H= -38.4kJ/mol二氧化碳与氢作用:CO2 +4H2 =CH4 +2H2O △H =-165.0kJ/mol以上反应体系为强放热、快速率的自平衡反应,温度升高到一定程度后反应速率快速下降且向相反方向(左)进行。
另外甲烷化的过程属于体积缩小的反应,增加反应压力,一方面有利于提高反应速率,另一方面有助于推动反应向甲烷合成向进行,增加压力可以在很大程度上减小装置体积,提高装置产能。
甲烷化反应为强放热反应,每转化1%的CO,体系绝热升温约72℃,因此煤制天然气工艺要解决一氧化碳转化率和反应热的转移问题。
该过程中发生的副反应:一氧化碳的分解反应:2CO =CO2 +C △H= -173.3kJ/mol沉积碳的加氢反应C +2H2 =CH4 △H = -84.3kJ/mol该反应在甲烷合成温度下,达到平衡是很慢的。
当有碳的沉积产生时催化剂失活。
反应器出口气体混合物的热力学平衡,决定于原料气的组成、压力和温度。
目前,甲烷化技术已经用在大规模的合成气制天然气上,最大的问题是催化剂的耐温和强放热反应器的设计制作上。
甲烷化工艺有两步法和一步法两种类型。
甲烷化合成操作注意事项

合成现场安全操作
污染物安全:
1.装置漏油必须统一收集,除杂做循环利用。 2.现场废水不能随意排放,必须接管指定排放
3.废弃药瓶要统一摆放归集,不可乱扔
4.废弃保温材料同一地点堆置
巡检安全:
1.现场巡检人员必须配备四合一检测仪,实 行双人双检,佩戴防爆对讲机 2.随时注意现场报警装置,注意跑冒滴漏, 及 时发现,处理 3. 必须佩戴劳动防护用品,认真巡检,严格交接 班 4.冬季巡检注意防滑摔伤
• 止回阀使用注意 注意阀门方向,箭头与介质流向一致,如 介质易结晶可能造成阀片不能压下起不到 指挥、止回的作用。
主要设备的操作
锅炉给水泵组
启用步骤: 1.启动前的检查及准备 稀油站 油系统 冷却水系统 注水排气
2.锅炉给水泵的暖泵 正暖 (启动时) 倒暖(备用时) 在泵启动前暖泵时间不小于2小时,用测温 枪测量上下壳体温度差为15—20℃。 3.中控确认泵组启动条件 进口阀开 润滑油压力 冷却水压力 回流阀开 除氧槽液位
• 操作注意:
1.当阀杆开闭到位时,不能再强行用力,否则会 拉断内部螺纹或插销螺丝,使阀门损坏 2.开闭阀门时手不能直接开动时可用F扳手开闭 3.开闭阀门时注意观察阀门的密封面,尤其是填 料压盖处防止泄漏
截止阀
截止阀是用于截断介质流动的,截止阀的阀杆 轴线与阀座密封面垂直,通过带动阀芯的上下 升降进行开断。截止阀一旦处于开启状态,它 的阀座和阀瓣密封面之间就不再有接触,并具 有非常可靠的切断动作,因而它的密封面机械 磨损较小,由于大部分截止阀的阀座和阀瓣比 较容易修理或更换密封元件时无需把整个阀门 从管线上拆下来,这对于阀门和管线焊接成一 体的场合是很适用的。
4.泵的启动及注意事项 按启动按钮,当电流从高值下降,泵压上 升稳定后,缓慢打开泵的出口阀 若给水泵管道内无水,开始时不能全开出 口阀,应用此阀控制进入主管道流量,决 不能用进口阀来控制泵的流量。
甲烷化操作实操

1、甲烷合成反应器的反应机理?在甲烷化反应器中主要进行的是甲烷的合成反应,即一氧化碳、二氧化碳与氢在催化剂的作用下转化成甲烷。
甲烷合成反应是个强放热反应,伴随甲烷合成反应同时还发生了一氧化碳的氧化还原。
总反应方程式如下:CO + 3H2 = CH4 + H2OCO2 + 4H2 = CH4 + 2H2OCO + H2O = CO2 + H22.在氨厂典型的甲烷化炉操作条件下,毎1%CO转化的绝热温升为72℃,每1%CO2转化的绝热温升60℃,反应炉的总温升可由下式计算:ΔT=72╳[CO]入+60╳[CO2]入式中:ΔT----分别为进口气中CO、CO2的含量,%(体积分数)3甲烷化设备主要有哪些?甲烷化设备主要有硫吸收器、甲烷化反应器、高压废热锅炉、低压废热锅炉、甲烷化换热器、高压蒸汽过热器、开车加热器、循环压缩机、水冷器、水分离器等设备。
4、甲烷化催化剂的组成及主要组分的作用是什么?甲烷化催化剂是以镍为活性组分在载体上,为获得催化剂的活性和热稳定性有添加了一些促进剂。
主要组分有Ni、Al2O3、MgO、Re2O3等Al2O3是一种普遍使用的载体。
Al2O3具有多种结构形态,用于甲烷化的是具有大孔的Al2O3。
MgO是一种良好的的结构稳定剂。
Re2O3为稀土氧化物,具有良好的活性与稳定性。
5、为什么要对甲烷化催化剂进行还原?还原过过程中有哪些化学反应?①甲烷化催化剂使用前,是以镍(Ni)的氧化物形式纯在,所以使用时,必须还原活化。
在还原剂(H2、CO)被氧化的同时,多组分催化剂中的NiO被还原具有活性的金属镍(Ni),并在还原过程中形成了催化剂的孔道。
而Al2O3不会被还原,起着间接支持催化剂结构的助构作用,使镍处于均匀分散的微晶状态,使催化剂具有较大的比表面、较高的活性和稳定性。
②甲烷化催化剂还原时发生如下反应:NiO + H2 = Ni + H2O - 2.55KJ/molNiO + CO = Ni + CO2 - 30.25 KJ/mol这些都不是强放热反应,还原过程本身不会引起催化剂床层大的温升。
低变及甲烷化
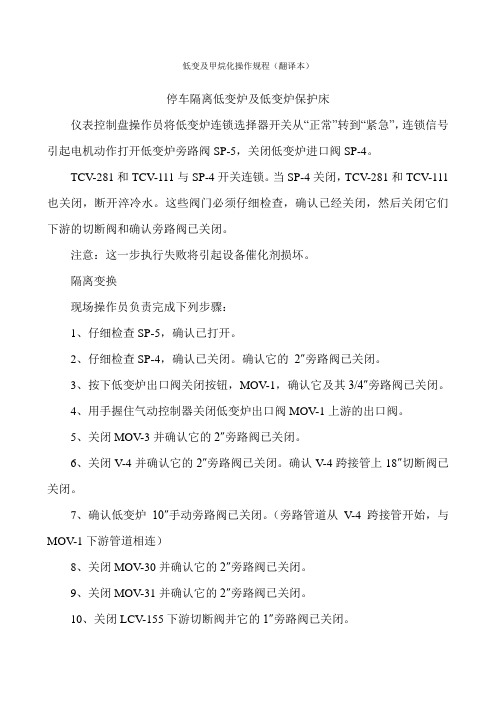
低变及甲烷化操作规程(翻译本)停车隔离低变炉及低变炉保护床仪表控制盘操作员将低变炉连锁选择器开关从“正常”转到“紧急”,连锁信号引起电机动作打开低变炉旁路阀SP-5,关闭低变炉进口阀SP-4。
TCV-281和TCV-111与SP-4开关连锁。
当SP-4关闭,TCV-281和TCV-111也关闭,断开淬冷水。
这些阀门必须仔细检查,确认已经关闭,然后关闭它们下游的切断阀和确认旁路阀已关闭。
注意:这一步执行失败将引起设备催化剂损坏。
隔离变换现场操作员负责完成下列步骤:1、仔细检查SP-5,确认已打开。
2、仔细检查SP-4,确认已关闭。
确认它的2″旁路阀已关闭。
3、按下低变炉出口阀关闭按钮,MOV-1,确认它及其3/4″旁路阀已关闭。
4、用手握住气动控制器关闭低变炉出口阀MOV-1上游的出口阀。
5、关闭MOV-3并确认它的2″旁路阀已关闭。
6、关闭V-4并确认它的2″旁路阀已关闭。
确认V-4跨接管上18″切断阀已关闭。
7、确认低变炉10″手动旁路阀已关闭。
(旁路管道从V-4跨接管开始,与MOV-1下游管道相连)8、关闭MOV-30并确认它的2″旁路阀已关闭。
9、关闭MOV-31并确认它的2″旁路阀已关闭。
10、关闭LCV-155下游切断阀并它的1″旁路阀已关闭。
11、关闭LCV-263下游切断阀并它的11/2″旁路阀已关闭。
在变换炉被隔离后应放空泄压并用氮气保护催化剂。
低温变换炉放空与氮气吹扫1、低温变换炉可以用三种方式放空。
前两种最有效。
a、慢开低变炉进口管接出的2″放空管线上的两个放空阀。
(一个阀大开度,另一个慢开以控制放空的量)这样气体放空到位于103-C上方管架的小放空罐。
b、打开V-4下游的两个2″导淋阀(一个阀大开度,另一个慢开以控制放空的量)这样气体放空到103-C与104-C之间的放空烟囱。
c、打开位于低变炉出口管上4″和6″两个放空阀。
这样气体放空到PIC-5放空消音器。
(一个阀大开度,另一个慢开以控制放空的量)确认到102-J进口的4″阀门已关闭。
- 1、下载文档前请自行甄别文档内容的完整性,平台不提供额外的编辑、内容补充、找答案等附加服务。
- 2、"仅部分预览"的文档,不可在线预览部分如存在完整性等问题,可反馈申请退款(可完整预览的文档不适用该条件!)。
- 3、如文档侵犯您的权益,请联系客服反馈,我们会尽快为您处理(人工客服工作时间:9:00-18:30)。
1)减少循环量
2)调整补入原料气中CO+CO2含量
3)减少循环量或增加生产负荷
4)加强油分排油水
5)减少生产负荷
6)停车检修
7)精心调节,调节电炉功率,维持温度
3
甲烷化塔塔壁温度升高
1)内件保温脱落,塔内同平面温差太大
2)内件筒体椭圆,气体偏流
停车检修,消除同平面温差;校正
4
系统出口CO+CO2含量超标
≤180℃
3
氨冷器出口气体温度
<15℃
4
水冷器出口气体温度
<35℃
5
甲烷化塔壁温度
<120℃
6
循环机进口温度
≤40℃
7
循环机出口温度
≤50℃
三
气体成份
1
进塔气:
CO+CO2≤0.5%
2
出塔气:
CO+CO2≤25ppm
四
电流
1
循环机电机电流
<336A
2
电炉丝最大电流
<1200A
第四节开、停车操作要点及注意事项
3)内件保温层脱落
1)降低生产负荷,待机停车更换催化剂
2)停车检修清理换热器
3)停车修理
6
电炉短路
1)中心管有异物
1)停车吹除中心管
7
断水、断电
紧急停车处理
2008-6-26
3.2防止有毒物质进入合成塔,其措施主要是提高原料气的脱硫效率,控制原料气中的总硫含量小于0.1PPM。同时加强除油效率,确保原料气的质量。
3.3由于甲烷化反应中要消耗H2生成CH4,造成进氨合成工段的补充气CH4含量增加,从而加大氨合成工段的放空量,因此,在一般情况下保证进塔原料气成分CO+CO2≤0.5%.
3.4正常情况下甲烷化合成塔温升很少,需借助电炉供热维持热点温度稳定.
3.5铁系触媒耐热性能好,操作弹性大,即便短时超温,活性不受影响.性价比比镍系触媒好得多.
第五节不正常现象判断及处理
序号
现象
原因
处理
1
催化剂床层温度急剧上升
1)循环量锐减
2)补入原料气中CO+CO2含量升高
3)生产负荷增加
4)操作不当
CO2+3H2→CH3OH + H2O +59.45kJ
上述反应都是强放热反应,它们可造成非常显著的温升,在绝热情况下,每1%的组分可造成的温升如下:CO为72℃,CO2为61℃。而且甲基化的反应程度相当彻底,得以保证出塔气体成分合格(做到PPM级)。
第二节工艺流程
从氢氮压缩机六段送来的(≤31.4Mpa)醇后气,气体成分:CO+CO2≤0.5%,经甲烷化工段的油水分离器,分离油污后,进入1#塔塔外换热器管间(上进下出),经初步加热后的气体(一进气)由上部进入甲烷化合成塔环隙,经环隙加热(一出气)后去2#塔塔外换热器管间(上进下出),加热后进入甲烷化合成塔(二进气),通过塔下部的换热器管间,与管内的出塔气体换热,温度升高后经中心管上升,然而进入触媒层发生甲基化反应;在甲烷化合成塔内,原料气中少量的CO和CO2在铁系催化剂作用下,分别与H2进行甲基化反应生成甲烷及甲醇和水等混合物;出甲烷化合成塔的气体(二出气)进入2#塔塔外换热器管内(下进上出),与进塔气(原料气)换热降温,然后进入软水加热器,继续降温,同时加热软水;出软水加热器的气体进入1#塔塔外换热器管内(下进上出);出塔气去水冷器进一步用水冷却降温;最后经过氨冷器再降温,进入气水分离器,经分离醇和水后的净化气CO+CO2≤25ppm作为补充气去氨合成工段。该工段设置的循环机正常生产时不使用,只是在开车升温或甲烷化合成塔内触媒层超温时启用。为防止塔内触媒层超温,设置冷气副线,用于控制床层温度。
2.2甲烷化合成塔采用循环降温;降温速率:在200℃以上,每小时降20℃~30℃;200℃以下,每小时降30℃~40℃
3、注意事项:
3.1正常操作时观察进出口温差,以及热点的变化。如果其他条件正常,进出口温差逐渐由大变小,意味着触媒衰老;如热点下移,或进出口温差突然变小意味着触媒中毒;如进出口温差突然较快增长,这主要是进塔气中CO+CO2含量超标所至。
B、按循环机开车程序开启循环机;启动电炉升温,升温速率为30~40℃/h;
C、当催化剂床层热点达200℃时,缓慢补气升压,并调整电炉功率,提
压速率≤5.0Mpa/h。控制床层温度在指标范围内,当压力升到25Mpa时,分析系统出口CO+CO2≤25ppm,即可投入生产;
2、系统停车:
2.1与外工段联系,停止本系统的气体补入,同时关闭系统出口阀,切断与外界的关联;
第三节主要工艺指标
序号
主要工艺指标名称
范围
备注
甲
烷
化
系
统
一
压力:
1
进补气油分压力
≤31.4MPa
2
甲烷化塔压差
≤1.0MPa
3
系统压差
≤2.5MPa
4
循环机油压
0.15MPa~0.3MPa
5
系统升降压速率
≤5.0Mpa/h
二
温度:
1
甲烷化塔催化剂床层热点温度
初期235±5℃后期285±5℃
2
甲烷化塔出口温度
甲烷化岗位操作规程
(目录)
第一节主要任务与工作原理
第二节工艺流程
第三节主要工艺指标
第四节开、停车操作要点及注意事项
第五节不正常现象判断及处理
第一节主要任务与工作原理
甲烷化工段的主要任务是:将醇后气中含CO+CO2≤0.5%的原料气,经压缩机加压至31.4Mpa后,进入甲烷化工段,醇后气中的CO和CO2在铁系催化剂作用下,分别与H2进行甲基化反应生成甲烷及甲醇,甲烷化系统的出口气体经过冷却分离出甲醇和水等混合物后,净化气中CO+CO2≤25ppm。然后送至氨合成工段。本工段以净化为主,并副产低浓度粗甲醇。
1)操作不当垮温
2)催化剂床层温度波动太大,最低小于200℃
3)甲烷化塔或塔外换热器相关填料泄漏
4)进塔气中CO+CO2含量超标
1),调节电炉功率,维持温度
2)精心操作,稳定催化剂床层温度
3)查找泄漏点,维修
4)控制醇后气体CO+CO2含量在指标范围内
5
甲烷化塔压差增大
1)甲烷化塔催化剂粉化严重
2)内件换热器列管堵
5)补入原料气中O2含量升高
1)加大循环量或增开循环机
2)要求调度适时调整补气中CO+作。
5)及时排除O2含量升高的原因
2
催化剂床层热点温度急剧下降
1)循环量太大
2)补入原料气中CO+CO2含量降低
3)生产负荷锐减
4)油分带水
5)催化剂严重中毒
6)内件局部泄漏
本工段管辖范围:甲烷化合成塔、塔外预热器、循环机、油分离器、水分离器、氨冷器、软水加热器、水冷器及所属设备、管道、阀门、仪表。
甲烷化工段反应的工作原理:
CO +3H2→CH4+ H2O +115.69kJ
CO2+4H2→CH4+2 H2O +72.77kJ
CO +2H2→CH3OH +102.37kJ
1、系统开车:
1.1系统原始开车:
A、系统设备、管道安装、催化剂装填结束,所有电器、仪表完好;
B、管道应另行制定分段吹除方案进行管道吹除;
C、系统置换和气密性试验另行制定方案进行;
D、系统置换、气密性试验合格后,按《催化剂升温还原方案》开车
1.2系统正常开车:
A、系统检修完毕、置换和气密性试验,未发现任何泄漏为合格,系统补入合格的原料气,充压至5.0Mpa,准备升温;