零件的优化设计
粉末冶金零件的优化设计

详细说明改进前的设计改进后的设计1.应使压模中的粉末受到大致相等的压缩,并能顺利地从压模中取出模压成型的制品。
在零件压制方向如有凸起或凹槽时,则粉末在压制时各部分的密实度不易一致,因此凸起或凹槽的深度以不大于零件总高度的1/5为宜,并有一定的拔模锥度2.当由上向下压制的结构零件较长时,其中间部分和两端的粉末密实度差别比较大。
所以在实际生产中,常现在其长度为直径的2.5~3.5倍,壁愈薄其长度与直径之比的倍数愈低3.当零件的壁厚急剧变化或零件的壁厚悬殊时,零件各部的密度也相差很大,这样烧结时会引起尺寸变化和变形,应尽量避免4.设计带有凸缘或台阶的零件,其内角应设计成圆角,以利于压制时凹模中粉末的流动和便于脱模,并可避免产生裂纹5.尽量避免深窄的凹槽、尖角或薄边的轮廓,避免细齿滚花和细齿形因为这些结构装粉成型都很困难6.避免尖边、锐角和切向过渡7.零件只能设计成与压制方向平行的花纹,菱形的花纹不能成型,应避免8.与压制方向垂直的孔(图a )、径向凹槽(图b )、内螺纹及外螺纹(图c )、倒锥(图d )、拐角处的退刀槽(图f )等结构难以压制成型,当需要时可在烧结后进行切削加工9.底部凹陷的法兰(图a )、外圆中部的凸缘(图b )不能压制成型。
上部凹陷的法兰(图c )为坯件,当埋头孔的面积小于压制面积的1倍左右,深度(H )小于零件全高的1/4左右时,要作5°的拔梢(图d )才可以成型10.从模具强度和压制件强度方面的因素考虑,并从孔与外侧间的壁厚要便于装粉考虑,制品窄条部分的最小尺寸应有一定的限度11.为了使凸模具有必要的刚度,使粉末容易充满型腔和便于从压模内取出制品,零件结构应避免尖锐的棱角,并适当增加横截面的面积12.避免过小的公差13.对于长度大于20mm 的法兰制作,法兰直径不应超过轴套直径的1.5倍,在可能条件下,应尽量减下法兰的直径,以避免烧结后的变形。
法兰根部的圆角半径可参考右图的表,轴套壁厚(δ)与法兰边宽(b )都必须大于1.5mm 设计阶梯形制件时,阶差不应小于直径的1/16,其尺寸不应小于0.9mm轴套直径/mm <12 >12~25 >25~50 >50~65 >65 圆角半径/mm0.81.21.62.4>2.514.粉末冶金制件的端部最好不要有过锐棱角,并避免工具倒圆。
机械优化设计三个案例
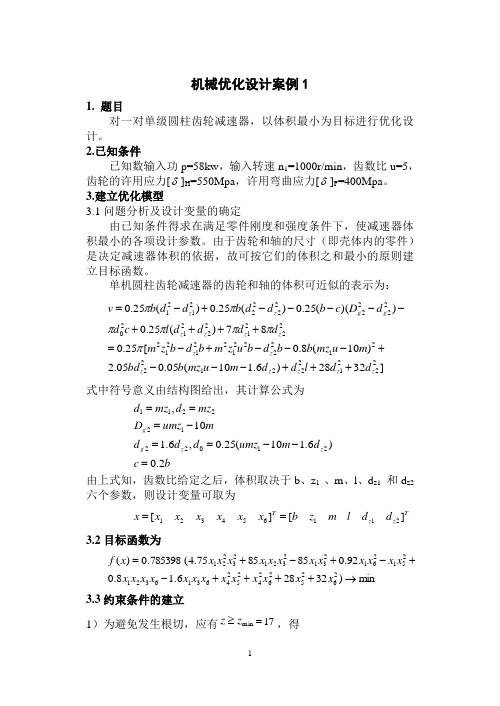
机械优化设计案例11. 题目对一对单级圆柱齿轮减速器,以体积最小为目标进行优化设计。
2.已知条件已知数输入功p=58kw ,输入转速n 1=1000r/min ,齿数比u=5,齿轮的许用应力[δ]H =550Mpa ,许用弯曲应力[δ]F =400Mpa 。
3.建立优化模型3.1问题分析及设计变量的确定由已知条件得求在满足零件刚度和强度条件下,使减速器体积最小的各项设计参数。
由于齿轮和轴的尺寸(即壳体内的零件)是决定减速器体积的依据,故可按它们的体积之和最小的原则建立目标函数。
单机圆柱齿轮减速器的齿轮和轴的体积可近似的表示为:]3228)6.110(05.005.2)10(8.0[25.087)(25.0))((25.0)(25.0)(25.0222122212221222212212122221222120222222222121z z z z z z z z z z z g g z z d d l d d m u m z b bd m u m z b b d b u z m b d b z m d d d d l c d d D c b d d b d d b v +++---+---+-=++++-----+-=πππππππ式中符号意义由结构图给出,其计算公式为b c d m u m z d d d mu m z D m z d m z d z z g g 2.0)6.110(25.0,6.110,21022122211=--==-===由上式知,齿数比给定之后,体积取决于b 、z 1 、m 、l 、d z1 和d z2 六个参数,则设计变量可取为T z z T d d l m z b x x x x x x x ][][211654321==3.2目标函数为min)32286.18.092.0858575.4(785398.0)(2625262425246316321251261231232123221→++++-+-+-+=x x x x x x x x x x x x x x x x x x x x x x x x x x f3.3约束条件的建立1)为避免发生根切,应有min z z ≥17=,得017)(21≤-=x x g2 )齿宽应满足max min ϕϕ≤≤d b,min ϕ和max ϕ为齿宽系数d ϕ的最大值和最小值,一般取min ϕ=0.9,max ϕ=1.4,得04.1)()(0)(9.0)(32133212≤-=≤-=x x x x g x x x x g3)动力传递的齿轮模数应大于2mm ,得 02)(34≤-=x x g4)为了限制大齿轮的直径不至过大,小齿轮的直径不能大于max 1d ,得0300)(325≤-=x x x g 5)齿轮轴直径的范围:max min z z z d d d ≤≤得0200)(0130)(0150)(0100)(69685756≤-=≤-=≤-=≤-=x x g x x g x x g x x g 6)轴的支撑距离l 按结构关系,应满足条件:l 2min 5.02z d b +∆+≥(可取min ∆=20),得0405.0)(46110≤--+=x x x x g7)齿轮的接触应力和弯曲应力应不大于许用值,得400)10394.010177.02824.0(7098)(0400)10854.0106666.0169.0(7098)(0550)(1468250)(224222321132242223211213211≤-⨯-⨯+=≤-⨯-⨯+=≤-=---x x x x x x g x x x x x x g x x x x g8)齿轮轴的最大挠度max δ不大于许用值][δ,得0003.0)(04.117)(445324414≤-=x x x x x x g 9)齿轮轴的弯曲应力w δ不大于许用值w ][δ,得5.5106)1085.2(1)(05.5104.2)1085.2(1)(1223246361612232463515≤-⨯+⨯=≤-⨯+⨯=x x x x x g x x x x x g4.优化方法的选择由于该问题有6个设计变量,16个约束条件的优化设计问题,采用传统的优化设计方法比较繁琐,比较复杂,所以选用Matlab 优化工具箱中的fmincon 函数来求解此非线性优化问题,避免了较为繁重的计算过程。
基于CADCAM技术的机械零部件设计与优化

基于CADCAM技术的机械零部件设计与优化在当今科技日新月异的背景下,计算机辅助设计与制造(CADCAM)技术在机械零部件设计与优化领域发挥了重要作用。
通过利用CADCAM技术,工程师们可以更加高效、精确地进行零部件设计与优化,从而提高产品质量、降低生产成本并缩短产品开发周期。
本文将就CADCAM技术在机械零部件设计与优化中的应用进行探讨。
首先,CADCAM技术可以帮助工程师们进行机械零部件的三维建模。
通过使用专业的CAD软件,工程师们可以在计算机上建立真实、精确的零部件模型,包括各种几何形状、尺寸和特征。
这种三维建模的优势在于,工程师们可以更加方便地观察和修改设计,避免了传统手绘图纸所带来的工作不便和错误。
同时,三维建模还可以为后续的分析和优化提供基础。
其次,CADCAM技术使得机械零部件的分析和仿真更加容易。
在传统的设计过程中,工程师们需要通过实验或者制造样件来评估零部件的性能和强度。
而借助于CADCAM技术,工程师们可以在计算机上进行各种仿真分析,例如应力分析、热力学分析和流体力学分析等。
通过这些仿真分析,工程师们可以更早地发现问题、改进设计,并且避免了实验过程中的大量时间和资源浪费。
同时,仿真分析还可以为优化设计提供数据支持,使得零部件的设计更加合理和可靠。
另外,CADCAM技术还支持机械零部件的优化设计。
在传统设计过程中,工程师们通常采用试错法,通过多次尝试和修改来不断改进设计。
而CADCAM技术则可以通过优化算法来实现自动优化设计。
通过设定设计目标和约束条件,CADCAM软件可以自动搜索最优解,并给出满足设计要求的最佳设计方案。
这不仅节省了大量的设计时间和人力成本,还可以提高设计效率和设计质量。
最后,CADCAM技术还支持机械零部件的制造和加工。
通过使用CAM软件,工程师们可以将设计模型转化为机床程序,实现零部件的数控加工。
CAM软件可以根据设计模型自动生成刀具路径、加工顺序和进给速度等信息,并生成相应的机床代码。
六西格玛对零件尺寸公差设计中的优化
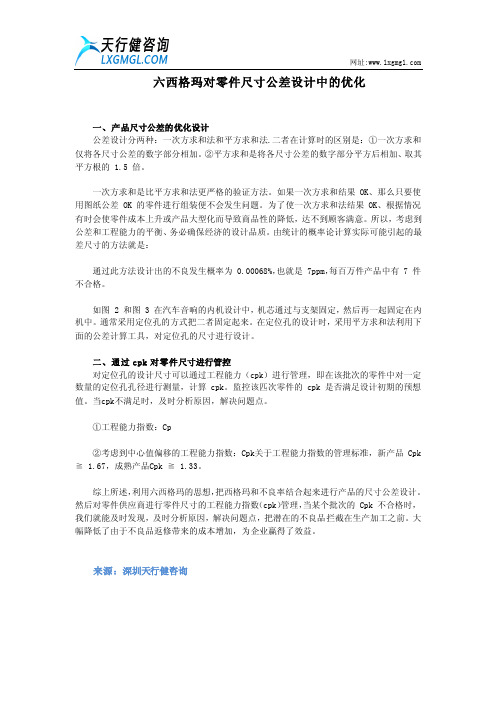
网址: 六西格玛对零件尺寸公差设计中的优化一、产品尺寸公差的优化设计公差设计分两种:一次方求和法和平方求和法.二者在计算时的区别是:①一次方求和仅将各尺寸公差的数字部分相加。
②平方求和是将各尺寸公差的数字部分平方后相加、取其平方根的 1.5 倍。
一次方求和是比平方求和法更严格的验证方法。
如果一次方求和结果 OK、那么只要使用图纸公差 OK 的零件进行组装便不会发生问题。
为了使一次方求和法结果 OK、根据情况有时会使零件成本上升或产品大型化而导致商品性的降低,达不到顾客满意。
所以,考虑到公差和工程能力的平衡、务必确保经济的设计品质。
由统计的概率论计算实际可能引起的最差尺寸的方法就是:通过此方法设计出的不良发生概率为 0.00068%,也就是 7ppm,每百万件产品中有 7 件不合格。
如图 2 和图 3 在汽车音响的内机设计中,机芯通过与支架固定,然后再一起固定在内机中。
通常采用定位孔的方式把二者固定起来。
在定位孔的设计时,采用平方求和法利用下面的公差计算工具,对定位孔的尺寸进行设计。
二、通过cpk 对零件尺寸进行管控对定位孔的设计尺寸可以通过工程能力(cpk)进行管理,即在该批次的零件中对一定数量的定位孔孔径进行测量,计算 cpk。
监控该匹次零件的 cpk 是否满足设计初期的预想值。
当cpk不满足时,及时分析原因,解决问题点。
①工程能力指数:Cp②考虑到中心值偏移的工程能力指数:Cpk关于工程能力指数的管理标准,新产品 Cpk ≧ 1.67,成熟产品Cpk ≧ 1.33。
综上所述,利用六西格玛的思想,把西格玛和不良率结合起来进行产品的尺寸公差设计。
然后对零件供应商进行零件尺寸的工程能力指数(cpk)管理,当某个批次的 Cpk 不合格时,我们就能及时发现,及时分析原因,解决问题点,把潜在的不良品拦截在生产加工之前。
大幅降低了由于不良品返修带来的成本增加,为企业赢得了效益。
来源:深圳天行健咨询。
机械零部件的疲劳寿命分析与优化设计

机械零部件的疲劳寿命分析与优化设计概述机械零部件的疲劳寿命分析和优化设计对于确保机械设备的可靠性和使用寿命至关重要。
疲劳失效是导致机械零部件损坏和事故的主要原因之一。
本文将介绍疲劳寿命的概念和常见分析方法,并探讨如何通过优化设计提高零部件的疲劳寿命。
疲劳寿命概念疲劳寿命是指机械零部件在循环应力的作用下失效之前能够承受的循环应力次数。
循环应力是指零部件在交变荷载作用下所受到的应力变化。
疲劳寿命可以通过应力-寿命(S-N)曲线来表示,该曲线描述了应力水平和所能承受的循环次数之间的关系。
疲劳分析方法1. 应力分析:对于机械零部件,必须首先进行应力分析,确定零部件在使用条件下所受到的应力水平和变化。
2. 材料特性分析:机械材料的疲劳寿命与其材料特性密切相关。
通过对材料的化学成分和热处理工艺等进行分析,可以确定材料的疲劳强度和寿命。
3. 循环载荷分析:确定作用在机械零部件上的循环载荷,包括振动载荷、冲击载荷等。
在实际情况中,往往会有多种载荷同时作用在零部件上,需要综合考虑不同载荷对疲劳寿命的影响。
4. 疲劳寿命预测:根据应力分析和材料特性,利用疲劳寿命预测模型,可以预测机械零部件在给定载荷下的疲劳寿命。
优化设计方法1. 材料选择:选择具有较高疲劳强度和寿命的材料,可以提高零部件的疲劳寿命。
例如,使用高强度钢材代替低强度钢材,可以提高零部件的抗疲劳能力。
2. 结构设计:通过优化零部件的结构设计,可以降低应力集中和应力变化幅度,从而延长疲劳寿命。
例如,合理设计零部件的圆角和倒角,可以缓解应力集中现象。
3. 表面处理:通过表面处理方法,如喷砂、磨削等,可以改善零部件表面的粗糙度和残余应力分布,提高疲劳强度。
4. 使用条件优化:调整机械设备的使用条件,如减小振动幅度、合理控制载荷大小等,可以减小零部件的疲劳应力,延长其寿命。
案例分析以一台发动机连接杆为例,进行疲劳分析和优化设计。
首先,进行应力分析并确定连接杆在使用条件下的应力水平和变化。
机械零件设计与优化

机械零件设计与优化机械零件设计是机械工程中的重要一环,它直接关系到机械设备的性能和效能。
为了提高机械设备的效率和可靠性,我们需要对机械零件进行合理的设计和优化。
首先,在机械零件设计中,我们需要考虑材料的选择。
选择合适的材料可以提高零件的强度和耐久性。
例如,在汽车发动机的曲轴设计中,使用高强度的合金钢可以增加曲轴的承载能力,从而提高发动机的输出功率和使用寿命。
其次,在机械零件设计中,我们需要考虑零件的形状和尺寸。
通过合理的形状设计和尺寸确定,可以减少零件的重量和体积,并提高零件的结构刚度和稳定性。
例如,在飞机的机翼设计中,通过采用翼面的变厚度设计,可以在保证结构强度的同时,减少机翼的重量,提高飞机的燃油效率和飞行性能。
另外,机械零件的设计还需要考虑零件之间的连接方式。
合适的连接方式可以确保零件之间的紧密连接,提高机械设备的整体稳定性和可靠性。
例如,在机械传动系统中,合理选择齿轮的齿距、齿形等参数,可以减小齿轮啮合时的摩擦损失和传动误差,提高传动效率和运行平稳性。
此外,机械零件设计中的优化也是非常重要的。
通过优化设计,可以最大程度地发挥机械零件的性能,提高机械设备的工作效率。
优化设计涉及到多个方面,包括材料的优化、结构的优化和工艺的优化等。
例如,在汽车发动机的气缸设计中,通过优化气缸壁的厚度和形状,可以提高发动机的热效率和动力输出。
此外,计算机辅助设计和仿真技术在机械零件设计中也发挥着重要作用。
通过使用计算机软件进行三维建模和仿真分析,可以快速准确地评估不同设计方案的性能和效果。
例如,使用有限元分析软件可以预测零件在工作载荷下的受力情况,帮助设计人员提前发现潜在的故障点,避免零件的失效和损坏。
总之,机械零件的设计与优化是机械工程领域的核心内容之一。
合理的材料选择、形状设计和连接方式选择可以提高机械设备的性能和可靠性。
优化设计和计算机辅助设计技术则能够帮助设计人员更好地发挥机械零件的性能,提高机械设备的工作效率。
基于有限元方法的机械零部件结构优化设计
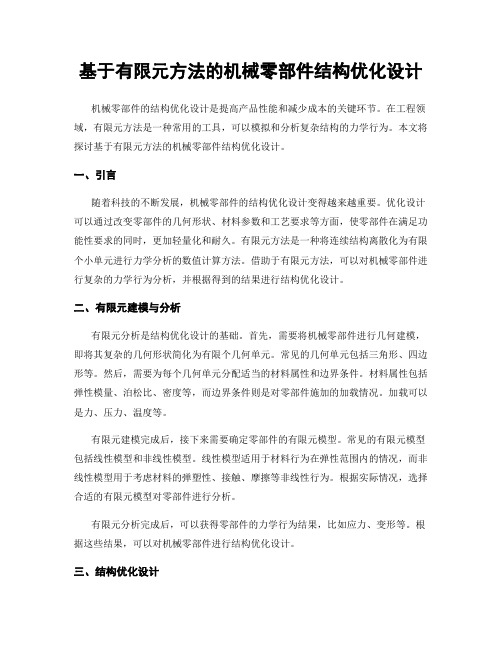
基于有限元方法的机械零部件结构优化设计机械零部件的结构优化设计是提高产品性能和减少成本的关键环节。
在工程领域,有限元方法是一种常用的工具,可以模拟和分析复杂结构的力学行为。
本文将探讨基于有限元方法的机械零部件结构优化设计。
一、引言随着科技的不断发展,机械零部件的结构优化设计变得越来越重要。
优化设计可以通过改变零部件的几何形状、材料参数和工艺要求等方面,使零部件在满足功能性要求的同时,更加轻量化和耐久。
有限元方法是一种将连续结构离散化为有限个小单元进行力学分析的数值计算方法。
借助于有限元方法,可以对机械零部件进行复杂的力学行为分析,并根据得到的结果进行结构优化设计。
二、有限元建模与分析有限元分析是结构优化设计的基础。
首先,需要将机械零部件进行几何建模,即将其复杂的几何形状简化为有限个几何单元。
常见的几何单元包括三角形、四边形等。
然后,需要为每个几何单元分配适当的材料属性和边界条件。
材料属性包括弹性模量、泊松比、密度等,而边界条件则是对零部件施加的加载情况。
加载可以是力、压力、温度等。
有限元建模完成后,接下来需要确定零部件的有限元模型。
常见的有限元模型包括线性模型和非线性模型。
线性模型适用于材料行为在弹性范围内的情况,而非线性模型用于考虑材料的弹塑性、接触、摩擦等非线性行为。
根据实际情况,选择合适的有限元模型对零部件进行分析。
有限元分析完成后,可以获得零部件的力学行为结果,比如应力、变形等。
根据这些结果,可以对机械零部件进行结构优化设计。
三、结构优化设计1. 基于强度和刚度的优化强度和刚度是机械零部件两个重要的性能指标。
强度是指零部件在外部加载下不发生破坏的能力,而刚度则是指零部件在外部加载下不发生过大变形的能力。
通过在有限元模型中设置约束和目标函数,可以进行强度和刚度的优化设计。
优化设计的目标是在满足强度和刚度要求的前提下,尽可能减小零部件的重量。
2. 基于模态和动力学的优化模态和动力学是机械零部件另外两个重要的性能指标。
机械元件的拓扑优化设计

机械元件的拓扑优化设计现如今,在制造业不断追求效率和质量提升的背景下,机械元件的设计也正发生着翻天覆地的变化。
其中,拓扑优化设计作为一种新兴的设计方法,逐渐受到了广大工程师和研究人员的重视。
本文将探讨机械元件的拓扑优化设计及其应用案例,以展现其巨大潜力。
首先,我们需要明确什么是拓扑优化设计。
拓扑优化设计是一种通过优化材料分布实现机械元件结构优化的方法。
它与传统的几何优化设计不同,不再考虑设计形状的变化,而是通过调整结构的材料分布,将材料只应用在需要承受载荷的区域,从而提高结构的强度和刚度,同时减少材料的使用量,达到轻量化的目标。
拓扑优化设计可以应用于各种机械元件的设计中,如飞机翼、汽车车身、机械零件等。
为了更好地说明拓扑优化设计的优势,以下以飞机翼为例进行论述。
在传统的飞机翼设计中,工程师往往会根据经验和常识制定翼型的设计方案,然后通过试制和测试不断优化。
这种方法虽然能够得到一定的效果,但过程缓慢且需要大量的试验和测试。
而拓扑优化设计则完全不同。
通过将初始设计输入计算机软件,软件可以基于数值分析和优化算法进行计算,并给出一个最优的拓扑分布方案。
这样,工程师只需要根据计算结果进行调整和优化,不再需要大量的实验和试验,大大减少了试制的时间和成本。
同时,拓扑优化设计可以考虑更多的设计约束条件,如结构强度、刚度、材料的疲劳寿命等,使得设计结果更加可靠和优化。
除了飞机翼,拓扑优化设计在汽车工业中也有着广泛的应用。
例如,在车身结构设计中,拓扑优化设计可以帮助工程师在结构刚度和重量之间找到最佳平衡点。
通过合理调整各个结构部件的材料分布,既可以保证车身的刚度,又可以降低车身的重量,提高燃油经济性能和行驶稳定性。
此外,拓扑优化设计还可以用于汽车零部件的设计,如发动机支撑架、悬架系统等。
通过对零部件结构的精细调整,可以提高零部件的强度和寿命,减少零部件的重量和成本,提高整个汽车系统的性能。
尽管拓扑优化设计在机械元件设计中具有巨大的潜力,但也面临一些挑战。
- 1、下载文档前请自行甄别文档内容的完整性,平台不提供额外的编辑、内容补充、找答案等附加服务。
- 2、"仅部分预览"的文档,不可在线预览部分如存在完整性等问题,可反馈申请退款(可完整预览的文档不适用该条件!)。
- 3、如文档侵犯您的权益,请联系客服反馈,我们会尽快为您处理(人工客服工作时间:9:00-18:30)。
(1)在允许的范围内;
(2)当零件的真实值为标定值时,粒子分离器的指标 y 偏离目标值 y0 最小;
基于此,使用 lingo 优化软件(程序见附录一)求得一组最优标定值 1,2,..., 7 ;
由假设 2 和假设 3 以及求得最优标定值,我们可以计算出每一个容差等级对应零件参 数值方差计算过程和公式如下:(程序见附录三)
利用计算机仿真的优势,对粒子分离器参数设计进行计算机仿真模拟,并用计算机 统计出 20 次(每次 1000 个零件)的仿真结果,从结果中找出统计规律来确定粒子分离 器的参数选择,得到了【B B B C C B B】的零件容差等级选择方案。
使用该方案得到的平均总费用为 495182 元,而平均最小损失费用为 220182 。并通 过计算求得原始方案费用,总费用共减少了 4391818 元,可以得出结论:使用所得方案 可获得较大的效益。
Cmin :计算机仿真的最小总费用; Clost:计算机仿真的最小损失费用; Cminy:原始设计的最小总费用; Closty:原始设计的最小损失费用。
五、模型的建立
由题意,零件的标定值必须在一定范围内,且由模型的假设 1 可知,标定值为零件 参数的中心值,也即出现概率最大的值,因此,标定值的选取必须满足下列条件:
八、模型的优缺点分析及改进方向
8.1 模型的优缺点分析 (1)建模使用了计算机仿真的方法,模型构成简单,具有很强的可操作性,切合实
际情况,所得结果正确。 (2)计算机计算复杂度较高,若生产 106 数量级以上的产品需要较长的运算时间。
8.2 模型的改进方向 本模型是通过计算机编程仿真建立的,算法的优化方面做得不充分,本模型的求解
表 1 各零件参数的标定值范围、容差等级及其相应的加工成本
标定值容许范 围
C等
B等
A等
X1
[0.075,0.125 ]
/
25
/
X2
[0.225,0.375 ]
20
50
/
X3
[0.075,0.125 ]
20
50
200
X4
[0.075,0.125 ]
50
100
500
X5
[1.125,1.875 ]
50
/
通过检验的结果可知,最优标定值已经达到一个比较理想的值。
3、计算机仿真零件的参数: 通过 matlab 编程仿真 20 组数据(主程序见附录四),结果如下:
1 2 3 4 5 6 7 8 9 10 11 12 13 14 15 16 17 18 19 20
X1 B B B B B B B B B B B B B B B B B B B B X2 C B B B C B B C B B B C B B C B B B B B X3 B B B B B B B B B B B B B B B B B B B B X4 C C C C C C C C C C C C C C C C C C C C X5 C C C C C C C C C C C C C C C C C C C C X6 C B B B C C C C B B B C C C B B B B B B X7 B B B B B B B B B B B B B B B B B B B B
景德镇陶瓷学院
第四组 钟哲 卢彧文 吴俊杰
粒子分离器零件参数设计的计算机仿真模型
摘要
本文建立起模型对离子分离器参数优化问题进行讨论。参照与原始的标定值选择区 间,用 lingo 进行求解计算的到最佳标定值为[0.075 0.2993 0.075 0.125 1.125 12 0.5812]。然后需要对 7 个零件的加工等级进行讨论,综合考虑零件加工成本和由零件误 差导致的离子分离器的质量损失与废品损失。
大概需要 60 分钟。本模型用的是枚举法,算法的空间复杂度以及时间复杂度方面存在 较大的改进空间,模型可以在这方面进行改进。
参考文献
[1]谢金星,优化建模与 LINDO/LINGO 软件,清华大学出版社,[M],2005 [2]陈桂明,MATLAB 数理统计(6.x),科学出版社,[M],2002 [3]盛骤,概率论与数理统计(第四版),高等教育出版社,[M],2008
四、符号的说明
xi :第 i 个零件的参数;(i=1,2,...,7) y :粒子分离器的实际指标值;
y0 :粒子分离器指标值的目标值;
i :第 i 个零件的标定值;(i=1,2,...,7) ij :第 i 个零件选第 j 个容差等级时参数的方差(i=1,2,...,7; j=1,2,3);
Rij1 :第 i 个零件选第 j 个容差等级时的参数变化区间上限; Rij 2 :第 i 个零件选第 j 个容差等级时的参数变化区间下限;
附录二: function [malo,y,drift]=partfun(x) %计算粒子分离器的参数y值,损失费用malo,偏离值drift % x为给定的一组固定的零件参数 for i=1:7
eval(['x',int2str(i),'=x(',int2str(i),');']); end y=174.42*(x1/x5)*(x3/(x2-x1))^0.85...
Cminy=4887000(1000 组) 原始方案平均最小损失费用:
Closty=4687000(1000 组)
七、模型结果分析
通过上面模型求解的结果可知,计算机仿真的模型能够减少总费用 4391818 元, 相对应原方案减少损失费用 4466818 元,在很大程度上减小了生产的成本,因此本模型 有比较好的适应性。
合 。对应 11 次容差组合,有对应的 11 组最小费用,我们取其平均值做为统计的最小 费用 。 平均最小总费用为:
Cmin=495182(1000 组) 平均最小损失费用为:
Clost=220182 (1000 组) 同时,我们对原始设计的参数及选择也进行了 20 次的计算机仿真(程序见附录六),并 计算出其平均最小总费用为:
*sqrt((1-2.62*(1-0.36*(x4/x2)^(-0.56))^(3/2)*(x4/x2)^1.16)/(x6*x7)); drift=abs(y-1.50); malo=0; if drift>=0.1&drift<0.3
malo=1000; elseif drift>=0.3
malo=9000; End 此附录为一个matlab函数求粒子分离器的参数,损失费用以及偏离值
1、计算第 i 个零件选第 j 个容差等级时的参数变化区间上限和下限
Ri11 i (11%) 0.99*i ;
同理:
Ri21 1.Leabharlann 1 * i ;Ri12 0.95 * i ; Ri22 1.05 * i ;
Ri13 0.9 * i; Ri23 1.1* i . (i=1,2,...,7)
y=174.42 x1
x3
0.85
x5 x2 x1
1
2.621
0.36
x4
0.56
3/ 2
x4
1.16
x2 x2
x6 x7
y 的目标值(记作 y0)为 1.50。当 y 偏离 y0 0.1 时,产品为次品,质量损失为 1,000 元;当 y 偏离 y0 0.3时,产品为废品,质量损失为 9,000 元。各零件参数的标定值范 围、容差等级及其相应的加工成本如表 1 所示:
附录三: function deta=qiudeta %此函数为求每一个零件对应等级容差的正态分布的方差 % 程序中的x值为选定的标定值 %A:A等级容差的零件参数变化范围 %B:B等级容差的零件参数变化范围 %C:C等级容差的零件参数变化范围 %x:参数的标定值 x=[0.075 0.2993 0.075 0.125 1.125 12 0.5812]; A(:,1)=0.99*x;A(:,2)=1.01*x; B(:,1)=0.95*x;B(:,2)=1.05*x; C(:,1)=0.9*x;C(:,2)=1.10*x; for i=1:7
/
X6
[12,20]
10
X7
[0.5625,0.93 5]
/
25
100
25
100
现批量生产粒子分离器,每批 1000 个,在原设计中,7 个零件参数的标定值为: x1=0.1,x2=0.3,x3=0.1,x4=0.1,x5=1.5,x6=16,..x7=0.75;容差均取最便宜的等级。
现在问题是: 1、综合考虑 y 偏离的 y0 造成的损失和零件成本,为该粒子分离器设计出合理的零 件参数,与原设计比较总费用降低了多少。 2、给出了一般产品的零件参数设计方法。
最后分析了模型的优缺点,并对模型进行了一定范围的推广,为其他同类问题提供 相似的解决方案。
关键词:计算机仿真 计算机统计 统计规律
一、问题的重述
一件产品通常由若干零件组装而成,这些零件的参数决定着标志产品性能的某个 参数,进而影响到产品的合格率,产品的合格率低将会给企业造成一定的经济损失。零 件参数包括标定值(即设计值)和容差(即最大允许误差)两部分,标定值有一定的容 许变化范围:容差一般以相对于标定值的误差表示,分为若干个等级,零件参数的容差 越小,则组装的产品的质量越高,即质量损失越小,但相应的零件加工成本越高,反之 亦然。因此,合理地设计零件参数的标定值和容差等级,是降低生产成本及质量损失, 提高企业经济效益的关键。 例如,粒子分离器的性能参数(记作 y)由 7 个零件的参数(记作 x1,x2……,x7)决定, 经验公式为:
六、模型的求解
1、通过使用 lingo 优化软件,计算出一组最优标定值为(程序见附录一):
1,2,..., 7 =[0.075 0.2993 0.075 0.125 1.125 12 0.5812]