单粒磨削过程仿真与工件表面残余应力的离散度分析
磨料流加工中有效磨粒工况对加工结果影响的仿真分析

磨料流加工中有效磨粒工况对加工结果影响的仿真分析发布时间:2023-02-17T02:37:42.150Z 来源:《教育学文摘》2022年第9月19期作者:张志斌[导读] 利用Abaqus软件构建磨料流加工仿真模型,对加工过程中近壁粒子运动状态进行仿真分析。
通过比较可知,有效磨粒所受的压强对Mises应力有显著影响,磨料流速有明显但非线性的影响。
张志斌(安徽水利水电职业技术学院,安徽合肥 230000)摘要:利用Abaqus软件构建磨料流加工仿真模型,对加工过程中近壁粒子运动状态进行仿真分析。
通过比较可知,有效磨粒所受的压强对Mises应力有显著影响,磨料流速有明显但非线性的影响。
结果为后续磨料流加工仿真研究提供理论依据与模型支持。
构建磨料流加工模型研究加工机理提供理论依据与模型支持。
关键词:磨料流加工;Abaqus;数值模拟引言磨料流加工(Abrasive Flow Machining, AFM)是1960年后开发的新型加工工艺,McCarty[1]称其为挤压珩磨法。
随着有限元算法的完善与CAE技术的发展,学者尝试通过仿真手段进行研究。
Junye Li[2]等人研究磨粒流加工工艺中的微孔磨粒流加工技术,通过控制磨粒筒活塞的运动速度来控制工件与磨粒流的相对运动,提高加工精度和效率。
Jain[3]等人采用有限元法分析磨料流加工外表面过程,他们发现当工件所受剪切应力低于屈服应力时,粘塑性物质可视为刚性物质。
超过屈服应力,粘塑性物质可视为牛顿流体。
Bo Tang[4]等人基于液固两相流耦合理论和连续介质理论,建立了面向模具结构面精密加工的软性磨料黏结流动力学模型。
1 磨料流加工仿真研究1.1 基本假设(1)磨料流动为稳定流动;(2)固相、液相均无相变;(3)将磨料中的载体简化为粘弹性边界条件;(4)忽略惯性力作用;(5)满足摩擦条件且摩擦系数保持常数;(6)不考虑热力耦合。
(7)磨粒简化为圆形颗粒。
1.2 模型的建立当使用中低浓度磨料进行抛光时,磨料中的磨粒分布稀疏而均匀,很难形成稳定的力链结构。
硬态切削表面残余应力分析研究
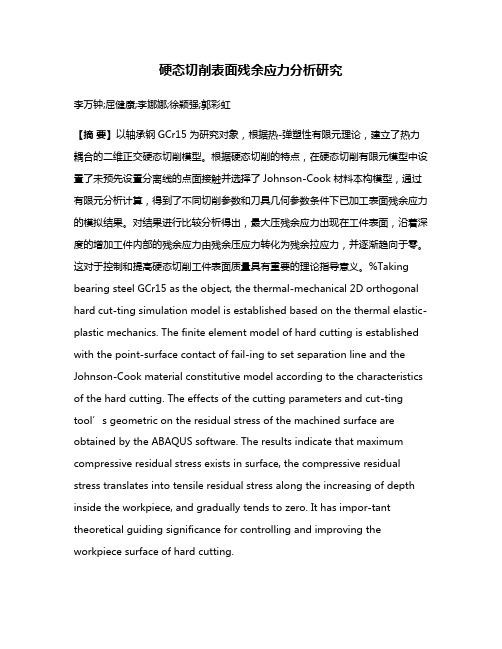
硬态切削表面残余应力分析研究李万钟;屈健康;李娜娜;徐颖强;郭彩虹【摘要】以轴承钢GCr15为研究对象,根据热-弹塑性有限元理论,建立了热力耦合的二维正交硬态切削模型。
根据硬态切削的特点,在硬态切削有限元模型中设置了未预先设置分离线的点面接触并选择了Johnson-Cook材料本构模型,通过有限元分析计算,得到了不同切削参数和刀具几何参数条件下已加工表面残余应力的模拟结果。
对结果进行比较分析得出,最大压残余应力出现在工件表面,沿着深度的增加工件内部的残余应力由残余压应力转化为残余拉应力,并逐渐趋向于零。
这对于控制和提高硬态切削工件表面质量具有重要的理论指导意义。
%Taking bearing steel GCr15 as the object, the thermal-mechanical 2D orthogonal hard cut-ting simulation model is established based on the thermal elastic-plastic mechanics. The finite element model of hard cutting is established with the point-surface contact of fail-ing to set separation line and the Johnson-Cook material constitutive model according to the characteristics of the hard cutting. The effects of the cutting parameters and cut-ting tool’s geometric on the residual stress of the machined surface are obtained by the ABAQUS software. The results indicate that maximum compressive residual stress exists in surface, the compressive residual stress translates into tensile residual stress along the increasing of depth inside the workpiece, and gradually tends to zero. It has impor-tant theoretical guiding significance for controlling and improving the workpiece surface of hard cutting.【期刊名称】《航空制造技术》【年(卷),期】2015(000)006【总页数】5页(P64-68)【关键词】硬态切削;热力耦合;温度场;残余应力;有限元【作者】李万钟;屈健康;李娜娜;徐颖强;郭彩虹【作者单位】西北工业大学机电学院;西北工业大学机电学院;西北工业大学机电学院;西北工业大学机电学院;中航光电科技股份有限公司【正文语种】中文随着切削技术的发展,尤其是超硬刀具材料陶瓷、聚晶立方氮化硼(PCBN)的出现,使得精密切削加工淬硬钢成为可能,产生了“以车带磨”的硬态切削加工技术。
磨削加工过程中的热影响分析
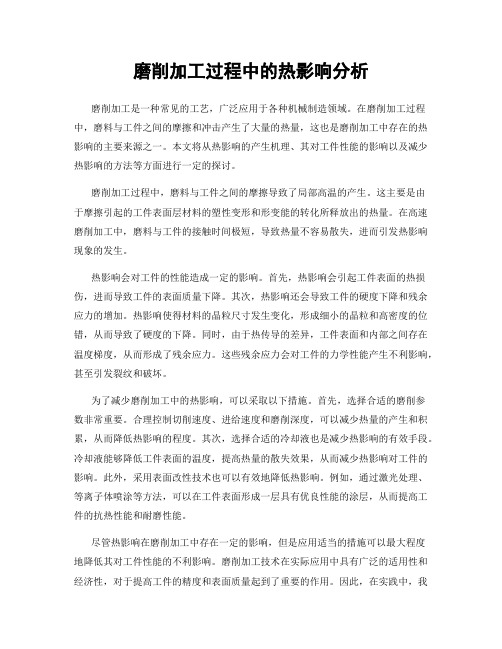
磨削加工过程中的热影响分析磨削加工是一种常见的工艺,广泛应用于各种机械制造领域。
在磨削加工过程中,磨料与工件之间的摩擦和冲击产生了大量的热量,这也是磨削加工中存在的热影响的主要来源之一。
本文将从热影响的产生机理、其对工件性能的影响以及减少热影响的方法等方面进行一定的探讨。
磨削加工过程中,磨料与工件之间的摩擦导致了局部高温的产生。
这主要是由于摩擦引起的工件表面层材料的塑性变形和形变能的转化所释放出的热量。
在高速磨削加工中,磨料与工件的接触时间极短,导致热量不容易散失,进而引发热影响现象的发生。
热影响会对工件的性能造成一定的影响。
首先,热影响会引起工件表面的热损伤,进而导致工件的表面质量下降。
其次,热影响还会导致工件的硬度下降和残余应力的增加。
热影响使得材料的晶粒尺寸发生变化,形成细小的晶粒和高密度的位错,从而导致了硬度的下降。
同时,由于热传导的差异,工件表面和内部之间存在温度梯度,从而形成了残余应力。
这些残余应力会对工件的力学性能产生不利影响,甚至引发裂纹和破坏。
为了减少磨削加工中的热影响,可以采取以下措施。
首先,选择合适的磨削参数非常重要。
合理控制切削速度、进给速度和磨削深度,可以减少热量的产生和积累,从而降低热影响的程度。
其次,选择合适的冷却液也是减少热影响的有效手段。
冷却液能够降低工件表面的温度,提高热量的散失效果,从而减少热影响对工件的影响。
此外,采用表面改性技术也可以有效地降低热影响。
例如,通过激光处理、等离子体喷涂等方法,可以在工件表面形成一层具有优良性能的涂层,从而提高工件的抗热性能和耐磨性能。
尽管热影响在磨削加工中存在一定的影响,但是应用适当的措施可以最大程度地降低其对工件性能的不利影响。
磨削加工技术在实际应用中具有广泛的适用性和经济性,对于提高工件的精度和表面质量起到了重要的作用。
因此,在实践中,我们需要深入研究磨削加工中的热影响机理,不断总结经验,并结合新材料和新工艺,进一步提高磨削加工的精度和效率。
表面残余应力测试技术研究及应用现状
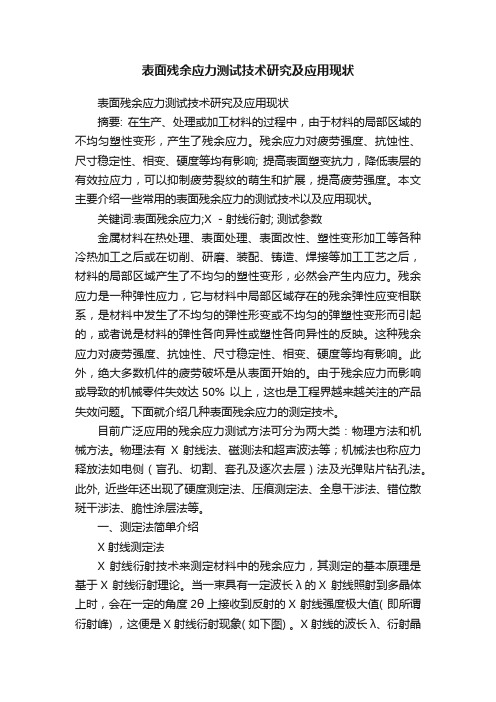
表面残余应力测试技术研究及应用现状表面残余应力测试技术研究及应用现状摘要: 在生产、处理或加工材料的过程中,由于材料的局部区域的不均匀塑性变形,产生了残余应力。
残余应力对疲劳强度、抗蚀性、尺寸稳定性、相变、硬度等均有影响; 提高表面塑变抗力,降低表层的有效拉应力,可以抑制疲劳裂纹的萌生和扩展,提高疲劳强度。
本文主要介绍一些常用的表面残余应力的测试技术以及应用现状。
关键词:表面残余应力;X -射线衍射; 测试参数金属材料在热处理、表面处理、表面改性、塑性变形加工等各种冷热加工之后或在切削、研磨、装配、铸造、焊接等加工工艺之后,材料的局部区域产生了不均匀的塑性变形,必然会产生内应力。
残余应力是一种弹性应力,它与材料中局部区域存在的残余弹性应变相联系,是材料中发生了不均匀的弹性形变或不均匀的弹塑性变形而引起的,或者说是材料的弹性各向异性或塑性各向异性的反映。
这种残余应力对疲劳强度、抗蚀性、尺寸稳定性、相变、硬度等均有影响。
此外,绝大多数机件的疲劳破坏是从表面开始的。
由于残余应力而影响或导致的机械零件失效达50% 以上,这也是工程界越来越关注的产品失效问题。
下面就介绍几种表面残余应力的测定技术。
目前广泛应用的残余应力测试方法可分为两大类:物理方法和机械方法。
物理法有X 射线法、磁测法和超声波法等;机械法也称应力释放法如电侧(盲孔、切割、套孔及逐次去层)法及光弹贴片钻孔法。
此外, 近些年还出现了硬度测定法、压痕测定法、全息干涉法、错位散斑干涉法、脆性涂层法等。
一、测定法简单介绍X 射线测定法X 射线衍射技术来测定材料中的残余应力,其测定的基本原理是基于X 射线衍射理论。
当一束具有一定波长λ的X 射线照射到多晶体上时,会在一定的角度2θ上接收到反射的X 射线强度极大值( 即所谓衍射峰) ,这便是X 射线衍射现象( 如下图) 。
X 射线的波长λ、衍射晶面间距d 和衍射角2θ之间遵从著名的布拉格定律:2d sinθ= n λ( n = 1,2,3……)在已知X 射线波长λ的条件下,布拉格定律把宏观上可以测量的衍射角2θ与微观的晶面间距d 建立确定的关系。
对影响机械加工表面质量因素讨论论文
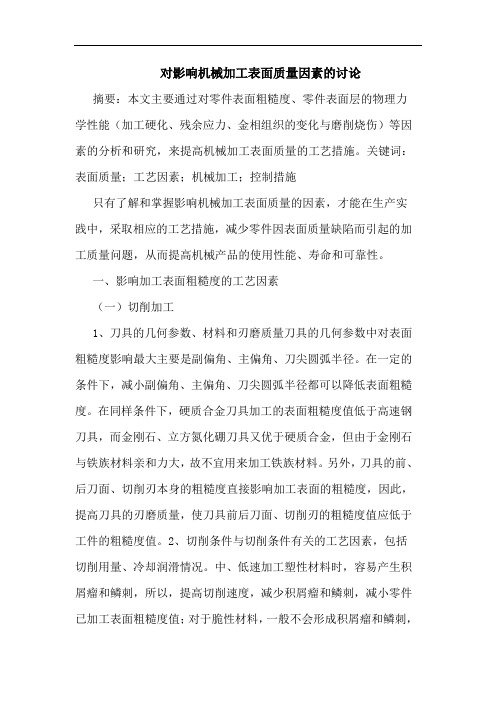
对影响机械加工表面质量因素的讨论摘要:本文主要通过对零件表面粗糙度、零件表面层的物理力学性能(加工硬化、残余应力、金相组织的变化与磨削烧伤)等因素的分析和研究,来提高机械加工表面质量的工艺措施。
关键词:表面质量;工艺因素;机械加工;控制措施只有了解和掌握影响机械加工表面质量的因素,才能在生产实践中,采取相应的工艺措施,减少零件因表面质量缺陷而引起的加工质量问题,从而提高机械产品的使用性能、寿命和可靠性。
一、影响加工表面粗糙度的工艺因素(一)切削加工1、刀具的几何参数、材料和刃磨质量刀具的几何参数中对表面粗糙度影响最大主要是副偏角、主偏角、刀尖圆弧半径。
在一定的条件下,减小副偏角、主偏角、刀尖圆弧半径都可以降低表面粗糙度。
在同样条件下,硬质合金刀具加工的表面粗糙度值低于高速钢刀具,而金刚石、立方氮化硼刀具又优于硬质合金,但由于金刚石与铁族材料亲和力大,故不宜用来加工铁族材料。
另外,刀具的前、后刀面、切削刃本身的粗糙度直接影响加工表面的粗糙度,因此,提高刀具的刃磨质量,使刀具前后刀面、切削刃的粗糙度值应低于工件的粗糙度值。
2、切削条件与切削条件有关的工艺因素,包括切削用量、冷却润滑情况。
中、低速加工塑性材料时,容易产生积屑瘤和鳞刺,所以,提高切削速度,减少积屑瘤和鳞刺,减小零件已加工表面粗糙度值;对于脆性材料,一般不会形成积屑瘤和鳞刺,所以,切削速度对表面粗糙度基本上无影响。
进给速度增大,塑性变形也增大,表面粗糙度值增大,所以,减小进给速度可以减小表面粗糙度值,但是,进给量减小到一定值时,粗糙度值不会明显下降。
正常切削条件下,切削深度对表面粗糙度影响不大,因此,机械加工时不能选用过小的切削深度。
合理选用切削液,对工件起到冷却、润滑作用,减少被加工材料的变形和摩擦,降低切削区温度,抑制积屑瘤和鳞刺的生成,是减少表面粗糙度值有效途径。
3、工艺系统的精度和刚度要想获得很小表面粗糙度,要求工艺系统具有足够的运动精度和刚度。
GH4169材料磨削后数控抛光表面残余应力分析

GH4169材料磨削后数控抛光表面残余应力分析高世民;全芳【摘要】CNC Polishing can have a low roughness with a high consistency.The influence of CNC polishing of wool felt wheel on residual stress is investigated.The normal residual stress in the feed direction shows a trend from rise to decline,while in the vertical feel direction it stays unchanged basically and then decreases.The optimized times of polishing is 3.The "Reinforcing Bar" model is put forward in order to explain the impact on the residual stress from polishing.Another polishing experiment is conducted for verifying roughly the impact relation.%数控抛光能够达到一致性较高的表面粗糙度要求.试验研究了羊毛毡轮数控抛光层数对磨削后GH4169表面残余应力的影响,进给方向表面残余正应力随深度增加先升高后下降,而垂直进给方向表面残余正应力先基本不变后下降,优化抛光层数为3层.针对磨削后抛光工艺,提出了“加强筋”模型,将羊毛毡轮抛光过程分为两个阶段,解释了抛光对表面残余应力的影响机理,并改变抛光参数进行了初步的试验验证.【期刊名称】《航空制造技术》【年(卷),期】2017(000)007【总页数】4页(P97-100)【关键词】GH4169;抛光;表面完整性;表面残余应力【作者】高世民;全芳【作者单位】北京航空航天大学机械工程及自动化学院,北京100191;北京航空航天大学机械工程及自动化学院,北京100191【正文语种】中文GH4169高温合金在-253~700℃温度范围内具有良好的综合性能,抗疲劳、抗腐蚀、抗氧化性能高[1],广泛应用于航空发动机压气机叶片[2]。
钛合金曲面磨粒流加工扰流流道仿真与试验研究
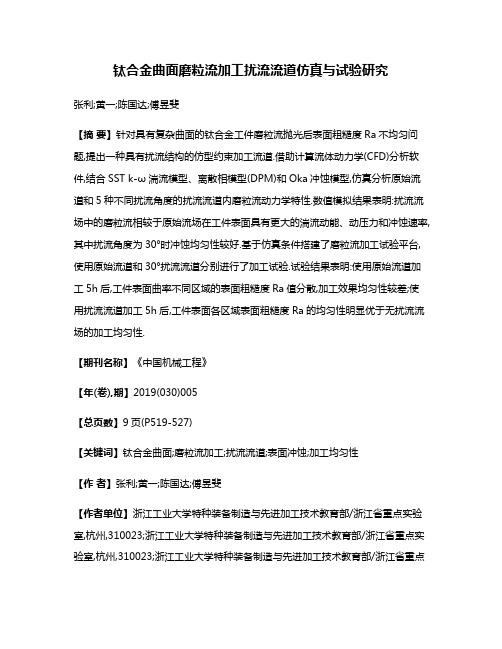
钛合金曲面磨粒流加工扰流流道仿真与试验研究张利;黄一;陈国达;傅昱斐【摘要】针对具有复杂曲面的钛合金工件磨粒流抛光后表面粗糙度Ra不均匀问题,提出一种具有扰流结构的仿型约束加工流道.借助计算流体动力学(CFD)分析软件,结合SST k-ω湍流模型、离散相模型(DPM)和Oka冲蚀模型,仿真分析原始流道和5种不同扰流角度的扰流流道内磨粒流动力学特性.数值模拟结果表明:扰流流场中的磨粒流相较于原始流场在工件表面具有更大的湍流动能、动压力和冲蚀速率,其中扰流角度为30°时冲蚀均匀性较好.基于仿真条件搭建了磨粒流加工试验平台,使用原始流道和30°扰流流道分别进行了加工试验.试验结果表明:使用原始流道加工5h后,工件表面曲率不同区域的表面粗糙度Ra值分散,加工效果均匀性较差;使用扰流流道加工5h后,工件表面各区域表面粗糙度Ra的均匀性明显优于无扰流流场的加工均匀性.【期刊名称】《中国机械工程》【年(卷),期】2019(030)005【总页数】9页(P519-527)【关键词】钛合金曲面;磨粒流加工;扰流流道;表面冲蚀;加工均匀性【作者】张利;黄一;陈国达;傅昱斐【作者单位】浙江工业大学特种装备制造与先进加工技术教育部/浙江省重点实验室,杭州,310023;浙江工业大学特种装备制造与先进加工技术教育部/浙江省重点实验室,杭州,310023;浙江工业大学特种装备制造与先进加工技术教育部/浙江省重点实验室,杭州,310023;浙江工业大学特种装备制造与先进加工技术教育部/浙江省重点实验室,杭州,310023【正文语种】中文【中图分类】TG6640 引言钛合金因具有比强度高、密度低、耐腐蚀性强、热强性好、生物相容性与力学相容性优异等优良特性,已广泛应用于航天航空、船舶、车辆、化工以及医疗等领域,成为材料科学中一个正在发展的新领域[1-4]。
但钛合金工艺性较差,较高的表面硬度使其表面抛光加工困难,尤其是一些具有复杂曲面的钛合金部件(如涡轮叶片、人工关节),目前主要通过手工进行抛光,效率较低且难以保证效果的均匀性,同时传统加工方法对钛合金工件进行抛光时,摩擦热的产生可能会造成金属黏结现象。
基于SIGINI子程序的零件残余应力变形数值模拟研究

不断提高,对航空器结构件的高精度制造提出了越 来越严格的要求。目前飞机普遍采用由大型整块铝 合金毛坯直接“掏空”加工而成的具有复杂槽腔、筋 条、凸台和减重孔等特征的整体结构件。很多零件 从毛坯到成品大概要去除 80% ~90%的材料,现代
[8]MartinWitty,ThomasBergs,AlexanderSchfer,etal.Cut tingtoolgeometryforplungemillingprocessoptimizationfor astainlesssteel[J].ProcediaCIRP,2012(1):506-511.
Keywords:aluminum alloydieforging;residualstress;stressrelease;finiteelement;subroutine;deformation
引言
随着航空工业的发展和航空飞行器综合性能的
基金项目: 国 家 自 然 科 学 基 金 (51675417);国 家 科 技 重 大 专 项 (2017ZX04011015) 收稿日期:2019年 1月
力仿真模型,采用用户子程序 SIGINI施加初始应力场,运用生死单元法对分层材料进行去除。结果表明,通过表
层残余应力试验数据逆向构建初始残余应力分布场计算变形的可行性,同时可以直观分析生死单元法逐层杀死单
元过程中,初始残余应力的释放过程,与零件加工后的变形测量结果对比,有较高的吻合性。
关键词:铝合金模锻件;残余应力;应力释放;有限元;子程序;变形
MaLiangdong,YinJia,AnPan,ZhangJun,GaoLongfei,ZhaoWanhua
Abstract:Inordertoimprovetheperformanceofaircraft,theintegralstructureiswidelyusedasthemainloadbear ingcomponent,andtheblankoftheintegralstructureisoftendeformedaftermachiningduetotheexistenceofresidual stress,whichaffectstheprecisionoftheparts.Basedontheexperimentaldataofresidualstresstestofdieforgingblank,the initialstresssimulationmodelisconstructedinthispaper.TheinitialstressfieldisappliedbytheusersubprogramSIGINI, andthestratifiedmaterialisremovedbythebirthanddeathelementmethod.Thesimulationresultsverifythefeasibilityof inverseconstructingtheinitialresidualstressdistributionfieldthroughthesurfaceresidualstressexperimentaldatatocal culatethedeformation.Atthesametime,thereleaseprocessoftheinitialresidualstresscanbeanalyzedintuitivelyinthe processofkillingtheunitlayerbythebirthanddeathelementmethod.Comparedwiththeresultsofdeformationmeasure mentaftermachining,theresultsareingoodagreementwitheachother.
- 1、下载文档前请自行甄别文档内容的完整性,平台不提供额外的编辑、内容补充、找答案等附加服务。
- 2、"仅部分预览"的文档,不可在线预览部分如存在完整性等问题,可反馈申请退款(可完整预览的文档不适用该条件!)。
- 3、如文档侵犯您的权益,请联系客服反馈,我们会尽快为您处理(人工客服工作时间:9:00-18:30)。
第43卷第5期 2009年5月上海交通大学学报J OU RNAL OF SHAN GHA I J IAO TON G UNIV ERSIT YVol.43No.5 May 2009 收稿日期:2008205227基金项目:国家自然科学基金资助项目(50705061)作者简介:张雪萍(19722),女,河南平顶山人,副教授,主要从事精密制造工艺研究.电话(Tel.):021*********;E 2mail :zhangxp @ .cn. 文章编号:100622467(2009)0520717205单粒磨削过程仿真与工件表面残余应力的离散度分析张雪萍, 王和平, 高二威(上海交通大学机械与动力工程学院,上海200240)摘 要:基于有限元软件Deform 22D ,建立了具有负前角特征的单颗磨粒磨削热力耦合有限元模型.仿真模拟了磨粒磨削工件时的温度场和应力场分布,分析了工件某点应力在磨削过程中的变化情况及该点最终形成的残余应力.结果表明:随着磨粒负前角的绝对值增加,工件表面残余应力值增大,当磨粒负前角由-15°到-35°时,工件表面残余应力差值达到284M Pa ;当磨粒采用负前角为-15°、-25°和-35°时,工件表面产生的残余应力标准差达到145.76M Pa.该研究证明了磨粒几何角度的随机性或离散性是影响磨削工件表面残余应力离散度的重要原因.关键词:单颗粒磨削;负前角;残余应力;离散度中图分类号:T G 580 文献标识码:ASimulation of Single Abrasive Particle G rinding Proce ss andAnalysis on the Residual Stre sses ScatterZ H A N G X ue 2pi n g , W A N G He 2pi n g , GA O Er 2w ei(School of Mechanical Engineering ,Shanghai Jiaotong U niversity ,Shanghai 200240,China )Abstract :A coupled t hermal 2mechanical model was established for t he grinding p rocess of a single abrasive characteristic wit h negative rake angle based on t he Deform 22D FEM software.The temperat ure and st ress dist ributio n were demonst rated ,t he st ress history of one point in t he machined workpiece was simulated ,and t he residual stress generation was analyzed by t he single 2abrasive grinding process simulation.The re 2sult s indicate t hat t he workpiece ’s residual stress increases wit h t he negative rake angle absolute value.The workpiece ’s residual st ress variation arrives at 284M Pa when t he negative rake angle value of an abra 2sive particle varies from -15°to -35°.The standard deviation is 145.76M Pa when t he negative rake an 2gle adopt s -15°,-25°and -35°respectively.It validates t hat t he abrasive geomet ry randomness is an important factor to determine t he workpiece residual stress scatter during t he grinding process.Key words :single 2abrasive grinding ;negative rake angle ;residual st ress ;scatter 精密磨削是工件加工的最后工序,工件表面残余应力对其诸如耐疲劳、抗腐蚀、耐磨等性能具有很大影响[1,2].因此,磨削表面残余应力及其离散度日渐成为零件表面完整性研究的重要内容.磨削加工同一批或同一零件时,机床特性、磨削工艺参数、磨削液及其注入方式等均能够影响残余应力的分布特性[3,4],而当磨削加工的机床特性、工艺参数和润滑方式等都确定时,砂轮磨粒几何角度的随机性就成为最重要的影响因素.金属切削加工的有限元模拟综合考虑了工件材料、刀具材料、加工方式及工艺参数等,能够定量分析切削力、切削温度、残余应力等物理量[5].Deform 软件能够分析考虑热力耦合的非等温变形问题[6],具有网格自动划分与自动再划分模块.当网格重划分后,能够在新旧网格之间实现应力、应变、速度场及边界条件等数据的传递,从而保证计算的连续性.单颗磨粒磨削是认识复杂磨削作用的重要手段,其可以在相似的磨削加工过程中不受其他磨粒的影响,采用较大的载荷以及放大磨削的程度[7].因此,,综合利用切削加工过程中有限元模拟技术仿真单颗磨粒磨削过程.1 单颗磨粒磨削过程磨削加工时,砂轮与工件相互接触与滑动,逐渐切除工件和砂轮相互干涉部分,从而形成加工表面.砂轮作为磨削加工刀具而具有磨粒排列不规则性,其间距和高低随机分布;磨削区内有效磨粒数目不确定;磨粒形状各异,且其切削刃不规则,切削面积不相同;磨粒切削刃存在不同形式和不同程度的磨损.通过研究发现,磨削过程的实质是切削、刻划和摩擦抛光的综合作用过程.粗磨时以切削作用为主,精磨时切削作用和摩擦抛光作用并存.由于磨削过程中磨损和磨削区的不断变化,磨削时以不同的负前角切削,这是磨削加工的一大特点[8].基于以上分析,本文以单颗粒磨削过程为切入点,以具有负前角磨粒为切削刃,采用有限元法分析单颗磨粒切削过程中残余应力的产生过程,同时研究磨削后工件残余应力离散度的变化规律.2 热力耦合FEM模型的建立2.1 磨粒与工件网格划分在切削过程中,起切削作用的磨粒较为锋利,相当于刀具,其前角为-45°~-15°[8].如图1(a)所示,磨粒的前角为-15°,后角为5°;由于磨粒的刚度比工件的刚度大,采用刚体模型并划分四面体网格单元.由于切削达到稳态的时间较短,瞬态切削热源影响的区域较小,故取工件的一部分区域进行建模,工件的几何尺寸为3mm×1mm,对此区域进行细密网格划分,如图1(b)所示.工件材料采用Deform 材料库中所对应的高碳铬轴承钢GCr15,型号为A ISI52100.(a)磨粒网格(b)工件网格图1 磨粒与工件的有限元网格划分Fig.1 Original mesh of abrasive grit and workpiece2.2 刀具与工件之间接触摩擦关系切削过程中主要存在2对摩擦副:①刀具前刀面与切屑底层的摩擦;②刀具后刀面与已加工表面之间的摩擦.由于摩擦情况非常复杂,在有限元仿真中一般采用修正的Coulomb摩擦定律,该方法将摩擦区分为滑动区和黏着区[6],其表达为τfr=μσn, τfr<τ-max(滑动区)τ-max, τfr≥τ-max(黏着区)(1)式中:τfr为刀具与切屑接触面的摩擦力;τfr≥τ-max为材料临界剪切应力;μ为滑动区的摩擦系数;σn为刀具与切屑接触面的法向应力.在切削过程中,切削热主要来自于切屑的塑性变形功和刀具与切屑之间的摩擦功.定义磨粒为主件,工件为从件,磨粒与工件之间为库仑摩擦,μ= 0.1[5].2.3 切屑分离和断裂准则切屑的有效分离是实现切削加工过程有限元仿真的关键.仿真采用无量纲Normalized Cockcroft &Lat ham切屑分离准则,分离系数为0.2.根据刀尖处工件有限元网格单元的应变能达到设定值时材料失效[6]的准则,该准则属于宏观断裂力学的范畴,其定义为∫εf0σ3dε=c(2)式中:εf为材料发生断裂时的应变值;σ3为最大应力;ε为等效应变;c为材料临界破坏值.同时,切屑817上 海 交 通 大 学 学 报第43卷 形成时切削区工件网格畸变严重,通过网格自动重新再划分功能保证了网格的相对均匀.3 仿真结果与分析采用的分析类型为弹塑性,并获得工件表面的残余应力.通过设置传热和变形来建立切削过程的热力耦合仿真模型,主要考察塑性变形对残余应力的影响,选择较低的切削速度以降低切削温度对残余应力的影响程度,所用切削速度v c =50mm/s ,切削厚度0.1mm ,仿真步长5μm ,仿真总步数600步.3.1 切削力和切削温度单颗磨粒切削过程中沿切削方向的切削力F 的变化曲线如图2所示.可见:在切削的初始阶段,切削力随切削进程快速增大,但很快到达稳定状态,历经的切削时间和路径都非常短;当刀具刚切入工件时,切削力逐渐上升,之后进入稳态切削阶段,切削力也存在一定范围的波动,这是由切屑与刀具前刀面接触、分离和切屑卷曲所引起的.图2 切削过程中切削力变化曲线Fig.2 Cutting force in the cutting process against time 切削过程中工件的温度变化如图3所示.可见,刀具与切屑接触处的温度梯度较大,切屑温度最高.随着刀具的切削运动,工件的温度梯度区域沿切削方向推进.因此,已形成的加工表面不再与刀具接触摩擦,温度逐渐下降,相当于一个冷却过程,由此形成由切削温度变化引起的残余应力.3.2 残余应力在单颗磨粒切削过程中,工件在切削方向(x 方向)主要承受剪切和挤压作用,其受力远大于工件的深度方向(y 方向),因此,在此重点分析切削过程中沿切削方向的残余应力分布.在切削过程的某一时刻,工件沿切削方向的应力分布如图4所示.可见,最大压应力约为-1.16GPa ,发生在切屑底层和刀具前刀面之间,说明切削过程中工件与切屑分离部分承受了较大的压应力;位于刀具前方工件待加工(a )切削步为268(b )切削步为559图3 切削过程中的切削温度分布Fig.3 Cuttingtemperature distribution in the cuttingprocess图4 切削过程中工件沿切削方向的应力分布Fig.4 Stress distribution along cutting direction in thecutting process表面也承受着较大的压应力,其幅值约为-330~-535M Pa ,表层压应力较大,出现塑性变形区域;在刃口区的磨粒与工件接触区的已加工表面作用着拉应力,表层拉应力较小,约为183M Pa ,沿深度方向其拉应力逐渐增大,为357~552M Pa. 在单颗粒磨削过程中,切削力、切削温度及其传导和回弹等均会影响工件最终形成的残余应力,且各因素对工件表面各点的影响规律相同.图5为远离刀具处工件已加工表面某点的应力随时间变化的关系曲线.当刀具未达到该点时,由于挤压作用,该点的应力状态为压应力;当刀具达到该点时,压应力转变为拉应力,但是由于该点受到切削力和切削温度的耦合影响,其应力值存在波动;随着磨粒沿切削方向运动,该点成为已加工表面,同时由于切削力和切削温度对该点的耦合影响逐渐降低,工件材料弹性回复,故该点应力逐渐变化并最终达到稳定值,即为该点在单颗磨粒切削中形成的最终残余应力.917 第5期张雪萍,等:单粒磨削过程仿真与工件表面残余应力的离散度分析 图5 已加工表面某点的应力变化情况Fig.5 Stress history of a point in finished surface3.3 磨粒前角对残余应力的影响磨削仿真中单颗磨粒的前角分别取α=-15°,-25°,-35°,而切削速度、切削深度和磨粒后角等其他参数保持不变.当磨粒负前角不同时工件的应力分布情况见图6.可见磨粒负前角对应力影响显著.随着磨粒负前角的绝对值增加,残余压应力值增大.这是因为刀具负前角值的增加有助于提高推挤作用,降低刀具切割作用,增大加工工件的塑性变形范围和程度,从而使已加工表面的残余应力增大.(a )α=-15°(b )α=-25°(c )α=-35°图6 不同负前角时工件的应力分布情况Fig.6 Stress distribution vs.negative rake angle3.4 磨削残余应力离散度实际磨削加工的砂轮表面磨粒负前角值差异较大,且在同一时刻,工件表面位置不同时所对应的磨削磨粒负前角度也不同.假设工件表面随机一点仅由一个磨粒完成加工,则该点可视为一个单粒磨削过程.如图7所示,设在同一时刻,具有不同前角的3个磨粒A 、B 、C 分别加工同一工件的不同点a 、b 和c ,则a 、b 和c 各点最终形成的残余应力分别与A 、B 和C 磨粒的前角相关联.图7 磨粒前角的残余应力离散度分析Fig.7 Residual stress scatter induced by differentnegative rake angle 仿真中假设磨粒A 、B 和C 的α=-15°、-25°、-35°,则a 、b 和c 点处的残余应力分别为-263,-462,-547M Pa ,该工件表面残余应力的极差为284M Pa ,标准差为145.76M Pa.这表明磨粒前角的随机性是导致工件表面残余应力存在离散度的重要原因.在实际磨削加工过程中,工件表面某点所形成的残余应力还受到单颗磨粒的其他参数(磨粒后角和磨粒切入深度等)的影响.因此,实际残余应力值是包括前角影响在内的叠加.此外,工件表面某点还将持续受到其他磨粒的影响,在空间上是一个平均化的过程,但由于单个磨粒的影响范围有限,某点应力主要受到某个磨粒的作用,因此,不同点之间的残余应力仍存在离散度.4 结 语根据磨粒磨削过程建立了基于Deform 22D 的单颗磨粒切削热力耦合有限元模型,仿真研究了具有负前角特征的单颗粒磨粒对工件残余应力场的影响规律.结果表明,当磨粒的负前角分别为-15°、-25°和-35°时,磨粒切削工件表面的残余应力差值达到284M Pa ,标准差约145.76M Pa ,表明磨粒几何角度的随机性是造成磨削工件表面残余应力离散度的重要原因.借助该模型,揭示了工件某点应力在刀具未到达之前、刀具正在切削以及刀具远离该点时的切削变化历程,并指出工件某点的残余应力是其远离刀具时处于稳定平衡状态的应力.此外,通过模拟工件的温度场和应力场,证明该模型是系统研究各种加工参数对磨削工件表面离散度影响的有效手段.同时,对优化磨削工艺参数、预测残余应力分布、提高加工表面质量以及减少试验次数都具有27上 海 交 通 大 学 学 报第43卷 重要意义.参考文献:[1] Webster G A,Ezeilo A N.Residual stress distribu2tions and their influence on fatigue life times[J].I n2 ternational Journal of F atigue,2001,23(1):3752383. [2] 张雪萍,赵国伟,蒋 辉,等.精密干切削淬硬零件表面完整性试验分析[J].上海交通大学学报,2006,40(6):9222926.ZHAN G Xue2ping,ZHAO Guo2wei,J IAN G Hui,etal.Experimental investigation on the surface integrity of hard machined components by super2finish turning[J].Journal of Shanghai Jiaotong U niversity,2006,40(6):9222926.[3] Liu C R,Yang X P.The scatter of residual stressesproduced by face2turning and grinding[J].Machining Science and T echnology,2001,5(1):1221.[4] 高二威.精密磨削表面残余应力离散度试验研究与数值分析[D].上海:上海交通大学机械与动力工程学院,2008.[5] Liu C R,Guo Y B.Finite element analysis of theeffect of sequential cuts and tool2chip f riction on resid2 ual stresses in a machined layer[J].I nternational Journal of Mechanical Sciences,2000,42(6):10692 1086.[6] J eff rey Fluhrer.DEFORM TM22D Version8.1User’sManual[M].Columbus O H,USA:Scientific Form2 ing Technology Corporation Ed.,2005.[7] 冯宝富,赵恒华,蔡光起,等.高速单颗磨粒磨削机理的研究[J].东北大学学报,2002,23(5):4702473.FEN G Bao2fu,ZHAO Heng2hua,CA I Guang2qi,et al.Study on the single grain high2speed grinding mechanism[J].Journal of N ortheastern U niversity,2002,23(5):4702473.[8] 张 磊.单程平面磨削淬硬技术的理论分析和试验研究[D].山东:山东大学机械工程学院,2006. (上接第716页)参考文献:[1] Park K S,Van Tyne C J,Moon Y H.Process analysisof multistage forging by using finite element method[J].Journal of Materials Processing T echnology,2007,1872188:5862590.[2] Lv C,Zhang L W,Mu Z J,et al.3D FEM simulation ofthe multi2stage forging process of a gas turbine com2 pressor blade[J].Journal of Materials Processing T ech2 nology,2008,198(123):4632470.[3] Hino R,Sasaki A,Y oshida F,et al.A new algorithmfor reduction of number of press2forming stages in forging processes using numerical optimization and FEsimulation[J].I nternational Journal of Mechanical Sci2 ences,2008,50(5):9742983.[4] Thiyagarajan N,Grandhi R V.Multi2level designprocess for32D preform shape optimization in metal forming[J].Journal of Materials Processing T echnolo2 gy,2005,170(122):4212429.[5] Srikanth A,Zabaras N.Shape optimization and pre2form design in metal forming processes[J].ComputerMethods in Applied Mech anics and E ngineering,2000, 190(13214):185921901.[6] Zhao G Q,Ma X W,Zhao X H,et al.Studies on opti2mization of metal forming processes using sensitivity a2 nalysis methods[J].Journal of Materials Processing T echnology,2004,147(2):2172228.[7] 汤禹成,周雄辉,陈 军.基于神经网络响应曲面的预锻模具形状优化与再设计方法[J].上海交通大学学报,2007,41(4):6242628. TAN G Yu2cheng,ZHOU Xiong2hui,CH EN J un.The optimum preform design and redesign based on neuralnetwork response surface methodology[J].Journal ofShanghai Jiaotong U niversity,2007,41(4):6242628. [8] 陈学文,王 进,陈 军,等.基于最小损伤值的齿轮毛坯锻造成形过程工艺参数优化设计[J].上海交通大学学报,2005,39(7):107021072. CH EN Xue2wen,WAN G Jin,CH EN J un,et al.The technological parameter optimization of gear billet hot forming process with damage minimization[J].Journal of Shanghai Jiaotong U niversity,2005,39(7):10702 1072.127 第5期张雪萍,等:单粒磨削过程仿真与工件表面残余应力的离散度分析 。