磨削过程残余应力
(完整版)残余应力

残余应力(Residual Stress)消除外力或不均匀的温度场等作用后仍留在物体内的自相平衡的内应力。
机械加工和强化工艺都能引起残余应力。
如冷拉、弯曲、切削加工、滚压、喷丸、铸造、锻压、焊接和金属热处理等,因不均匀塑性变形或相变都可能引起残余应力。
残余应力一般是有害的,如零件在不适当的热处理、焊接或切削加工后,残余应力会引起零件发生翘曲或扭曲变形,甚至开裂。
或经淬火、磨削后表面会出现裂纹。
残余应力的存在有时不会立即表现为缺陷,而当零件在工作中因工作应力与残余应力的叠加,使总应力超过强度极限时,便出现裂纹和断裂。
零件的残余应力大部分都可通过适当的热处理消除。
残余应力有时也有有益的方而,它可以被控制用来提高零件的疲劳强度和耐磨性能。
[1]工件在制造过程中,将受到来自各种工艺等因素的作用与影响;当这些因素消失之后,若构件所受到的上述作用与影响不能随之而完全消失,仍有部分作用与影响残留在构件内,则这种残留的作用与影响。
也称残余应力。
残余应力是当物体没有外部因素作用时,在物体内部保持平衡而存在的应力。
凡是没有外部作用,物体内部保持自相平衡的应力,称为物体的固有应力,或称为初应力,亦称为内应力。
测试仪器编辑残余应力分析仪其原理是基于著名的布拉格方程2dsinθ=nλ :即一定波长的X射线照射到晶体材料上,相邻两个原子面衍射时的X射线光程差正好是波长的整数倍。
通过测量衍射角变化Δθ从而得到晶格间距变化Δd,根据胡克定律和弹性力学原理,计算出材料的残余应力。
应力方程根据弹性力学理论, 在宏观各向同性晶体材料上角度φ和ψ(见图1)方向的应变可以用如下方程表述:(图1)正应力和剪切应力应力分量σφ和τφ为方向Sφ上正应力和剪切应力:含剪切应力的应力方程和曲线如果在垂直于试样表面上的平面上有剪应力存在(τ13≠0和/或τ23≠0),则εφψ与sin2ψ的函数关系是一个椭圆曲线,在ψ> 0和ψ<0是图形显示为“ψ分叉”(见图3)。
磨削减薄硅片变形测量与残余应力计算
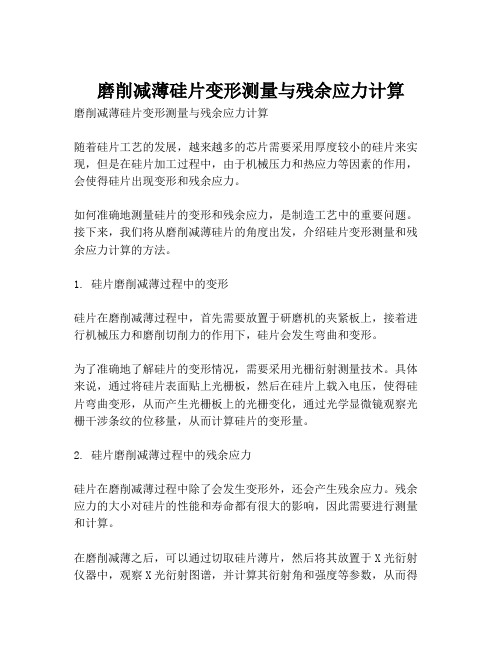
磨削减薄硅片变形测量与残余应力计算磨削减薄硅片变形测量与残余应力计算
随着硅片工艺的发展,越来越多的芯片需要采用厚度较小的硅片来实现,但是在硅片加工过程中,由于机械压力和热应力等因素的作用,会使得硅片出现变形和残余应力。
如何准确地测量硅片的变形和残余应力,是制造工艺中的重要问题。
接下来,我们将从磨削减薄硅片的角度出发,介绍硅片变形测量和残余应力计算的方法。
1. 硅片磨削减薄过程中的变形
硅片在磨削减薄过程中,首先需要放置于研磨机的夹紧板上,接着进行机械压力和磨削切削力的作用下,硅片会发生弯曲和变形。
为了准确地了解硅片的变形情况,需要采用光栅衍射测量技术。
具体来说,通过将硅片表面贴上光栅板,然后在硅片上载入电压,使得硅片弯曲变形,从而产生光栅板上的光栅变化,通过光学显微镜观察光栅干涉条纹的位移量,从而计算硅片的变形量。
2. 硅片磨削减薄过程中的残余应力
硅片在磨削减薄过程中除了会发生变形外,还会产生残余应力。
残余应力的大小对硅片的性能和寿命都有很大的影响,因此需要进行测量和计算。
在磨削减薄之后,可以通过切取硅片薄片,然后将其放置于X光衍射仪器中,观察X光衍射图谱,并计算其衍射角和强度等参数,从而得
到硅片的应力分布。
除此之外,还可以采用拉伸测试和椭圆偏振仪等技术进行测量和计算,得到硅片的残余应力分布情况。
总之,硅片在磨削减薄过程中,不可避免地会出现变形和残余应力。
只有通过精确的测量和计算,才能有效地评估硅片的质量和性能。
希
望以上内容对读者有所帮助。
金属切削的基础知识

切削过程: 三个变形区
(1)第一变形区
(2)第二变形区: (3)第三变形区:
制造技术
切屑种类:
1)带状切屑
外形连绵不断,与前刀 面接触的面很光滑,背面呈毛 茸状。用较大前角、较高的切 削速度和较小的进给量切削塑 性材料时,容易得到带状切屑。
制造技术
2)崩碎切屑 切削铸铁等脆性材料
制造技术
二、切削热的传散
在一般干切削的情况下,大部分的切削热由切屑传散出 去,其次由工件和刀具传散,而周围介质传散出去的热量很 少。但各种传散热量的比例,随着工件材料、刀具材料、切 削用量、刀具角度及切削方式等切削条件的不同而异。 切削热传散给切削及周围介质,对切削加工没有影响, 且传散得越多越好。 切削热传散给刀具切削部分,使刀具磨损加快,缩短刀 具的使用寿命;切削热传散给工件,影响工件的加工精度和 表面质量。 为了减小切削热对工件加工质量的不良影响,可采取的 两方面工艺措施:一是减小工件材料的变形抗力和摩擦阻力, 降低功率消耗和减少切削热;二是要加速切削热的传散,以 降低切削温度。
面粗糙度;严重时,会引起崩刀打刀,加速刀具的磨损。 二、表层材质变化
1.加工硬化
加工硬化是指在切削过程中,工件已加工表面受刀刃和后 面的挤压和摩擦而产生塑性变形,使表层组织发生变化,硬度 显著提高的现象。硬化层深度可达到0.02~0.03mm,表层硬度 约为工件材料的1.2~2倍。
制造技术
对加工硬化的影响因素:刀具几何参数、切削条件、工件
制造技术
2.润滑作用 金属切削加工液(简称切削液)在切削过程中的润滑作用, 可以减小前刀面与切屑,后刀面与已加工表面间的摩擦,形成部 分润滑膜,从而减小切削力、摩擦和功率消耗,降低刀具与工件 坯料摩擦部位的表面温度和刀具磨损,改善工件材料的切削加工 性能。在磨削过程中,加入磨削液后,磨削液渗入砂轮磨粒-工 件及磨粒-磨屑之间形成润滑膜,使界面间的摩擦减小,防止磨 粒切削刃磨损和粘附切屑,从而减小磨削力和摩擦热,提高砂轮 耐用度以及工件表面质量。 3.清洗和排屑作用 在金属切削过程中,要求切削液有良好的清洗作用。除去生 成切屑、磨屑以及铁粉、油污和砂粒,防止机床和工件、刀具的 沾污,使刀具或砂轮的切削刃口保持锋利,不致影响切削效果。 对于油基切削油,粘度越低,清洗能力越强,尤其是含有煤油、 柴油等轻组份的切削油,渗透性和清洗性能就越好。含有表面活 性剂的水基切削液,清洗效果较好,因为它能在表面上形成吸附
磨削过程残余应力
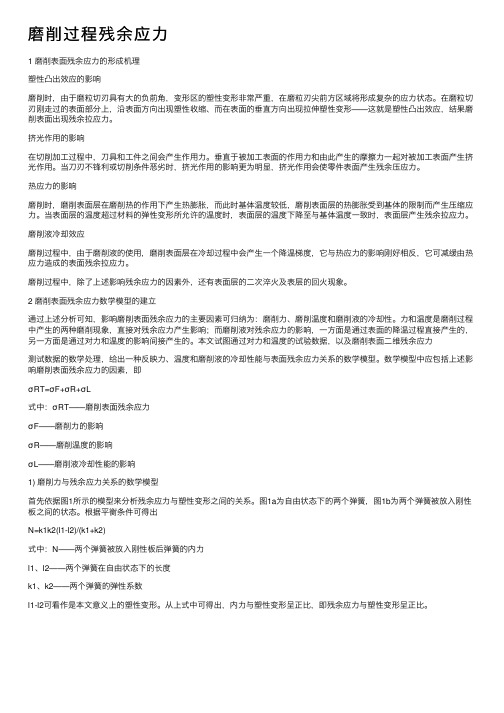
磨削过程残余应⼒1 磨削表⾯残余应⼒的形成机理塑性凸出效应的影响磨削时,由于磨粒切刃具有⼤的负前⾓,变形区的塑性变形⾮常严重,在磨粒刃尖前⽅区域将形成复杂的应⼒状态。
在磨粒切刃刚⾛过的表⾯部分上,沿表⾯⽅向出现塑性收缩、⽽在表⾯的垂直⽅向出现拉伸塑性变形——这就是塑性凸出效应,结果磨削表⾯出现残余拉应⼒。
挤光作⽤的影响在切削加⼯过程中,⼑具和⼯件之间会产⽣作⽤⼒。
垂直于被加⼯表⾯的作⽤⼒和由此产⽣的摩擦⼒⼀起对被加⼯表⾯产⽣挤光作⽤。
当⼑刃不锋利或切削条件恶劣时,挤光作⽤的影响更为明显,挤光作⽤会使零件表⾯产⽣残余压应⼒。
热应⼒的影响磨削时,磨削表⾯层在磨削热的作⽤下产⽣热膨胀,⽽此时基体温度较低,磨削表⾯层的热膨胀受到基体的限制⽽产⽣压缩应⼒。
当表⾯层的温度超过材料的弹性变形所允许的温度时,表⾯层的温度下降⾄与基体温度⼀致时,表⾯层产⽣残余拉应⼒。
磨削液冷却效应磨削过程中,由于磨削液的使⽤,磨削表⾯层在冷却过程中会产⽣⼀个降温梯度,它与热应⼒的影响刚好相反,它可减缓由热应⼒造成的表⾯残余拉应⼒。
磨削过程中,除了上述影响残余应⼒的因素外,还有表⾯层的⼆次淬⽕及表层的回⽕现象。
2 磨削表⾯残余应⼒数学模型的建⽴通过上述分析可知,影响磨削表⾯残余应⼒的主要因素可归纳为:磨削⼒、磨削温度和磨削液的冷却性。
⼒和温度是磨削过程中产⽣的两种磨削现象,直接对残余应⼒产⽣影响;⽽磨削液对残余应⼒的影响,⼀⽅⾯是通过表⾯的降温过程直接产⽣的,另⼀⽅⾯是通过对⼒和温度的影响间接产⽣的。
本⽂试图通过对⼒和温度的试验数据,以及磨削表⾯⼆维残余应⼒测试数据的数学处理,给出⼀种反映⼒、温度和磨削液的冷却性能与表⾯残余应⼒关系的数学模型。
数学模型中应包括上述影响磨削表⾯残余应⼒的因素,即σRT=σF+σR+σL式中:σRT——磨削表⾯残余应⼒σF——磨削⼒的影响σR——磨削温度的影响σL——磨削液冷却性能的影响1) 磨削⼒与残余应⼒关系的数学模型⾸先依据图1所⽰的模型来分析残余应⼒与塑性变形之间的关系。
磨削缺陷分析与解决

磨削缺陷分析与解决1.产生原因及影响因素零件的磨削精度指零件在磨削加工后,其形状、尺寸及表面相互位置三方面与理想零件的符合程度。
一般说来,形状精度高于尺寸精度,而位置精度也应高于尺寸精度。
磨削加工中的误差主要来源与两方面。
一是磨床-夹具-砂轮组成的工艺系统本身误差;二是磨削过程中出现的载荷和各种干扰:包括力变形、热变形、振动、磨损等引起的误差。
而在磨削过程中,使砂轮与工件位置改变以降低磨削精度的主要原因有:⑴.由磨削力引起的磨床和工件弹性变形;⑵.磨床和工件的热变形;⑶.磨床和工件的振动;⑷.砂轮磨损后其形状、尺寸变化;⑸.工装、夹具的损坏或变形;⑹.导轨、轴承和轴等部件的非弹性变形。
其中磨削过程中的弹性变形是主要的影响因素,它会使砂轮的实际切入深度与输入切入深度不一致,这一变化是由“砂轮架—砂轮轴承-砂轮轴-工件-工件支承”的弹性系统刚性决定。
一般为消除这种原因带来的误差常在行程进给磨削后,停止相互间的进给,仅依靠弹性回复力维持磨削,即光磨阶段(又叫清火花磨削),从而消除残留余量。
当然造成磨削误差的其它因素液很多如:工件磨削形状误差,工件热变形,磨粒切刃引起的塑性变形,砂轮的磨损等。
2.对工件的影响:降低工件使用寿命;降低工件抗疲劳强度;特殊特性的尺寸精度误差易影响工件使用,如轴承孔尺寸的控制,尺寸过小,安装不到轴上;过大,易引起振动,影响轴承使用寿命等。
3.解决方法:增加系统刚性;减少上工序加工留量,以减小磨削厚度,从而减小磨削力降低残留应力;增加光磨时间;及时修整砂轮,及时检查工装、夹具、轴承完好性及电主轴的振动性等;精细的选择砂轮,如挑选细粒度,硬度较大,组织稍紧密的砂轮;选用导热性好的砂轮(如CBN 砂轮);采用冷却性能优良的磨削液以减少因热变形引起的误差。
二、工件表面粗糙度1.产生原因及影响因素表面粗糙度指加工表面具有较小间距和峰谷所组成微观几何形状特征。
它是大量磨粒在工件表面进行切削后留下的微观痕迹的集合。
GH4169材料磨削后数控抛光表面残余应力分析

GH4169材料磨削后数控抛光表面残余应力分析高世民;全芳【摘要】CNC Polishing can have a low roughness with a high consistency.The influence of CNC polishing of wool felt wheel on residual stress is investigated.The normal residual stress in the feed direction shows a trend from rise to decline,while in the vertical feel direction it stays unchanged basically and then decreases.The optimized times of polishing is 3.The "Reinforcing Bar" model is put forward in order to explain the impact on the residual stress from polishing.Another polishing experiment is conducted for verifying roughly the impact relation.%数控抛光能够达到一致性较高的表面粗糙度要求.试验研究了羊毛毡轮数控抛光层数对磨削后GH4169表面残余应力的影响,进给方向表面残余正应力随深度增加先升高后下降,而垂直进给方向表面残余正应力先基本不变后下降,优化抛光层数为3层.针对磨削后抛光工艺,提出了“加强筋”模型,将羊毛毡轮抛光过程分为两个阶段,解释了抛光对表面残余应力的影响机理,并改变抛光参数进行了初步的试验验证.【期刊名称】《航空制造技术》【年(卷),期】2017(000)007【总页数】4页(P97-100)【关键词】GH4169;抛光;表面完整性;表面残余应力【作者】高世民;全芳【作者单位】北京航空航天大学机械工程及自动化学院,北京100191;北京航空航天大学机械工程及自动化学院,北京100191【正文语种】中文GH4169高温合金在-253~700℃温度范围内具有良好的综合性能,抗疲劳、抗腐蚀、抗氧化性能高[1],广泛应用于航空发动机压气机叶片[2]。
磨削淬硬技术的工艺性能
磨削淬硬技术的工艺性能切削深度在平面磨削中,如进给速度不变,则材料去除率和切屑等效厚度与切削深度ae成正比,增加切深通常会使切削力增大。
用刚玉砂轮磨削40CrMnMo钢(切削速度:Vc=35m/s,进给速度Vft=0.5m/min ,无切削液)的试验及理论计算结果表明,随着切削深度的增加,切向力增大,但单位切削功率却减小。
显然,接触长度增加的影响超过了切削力增大的影响,因此单位切削功率不适合于描述磨削加工工件表面的淬硬结果。
在切深ae=1mm时,进入工件的单位能量达到最大(ec=150J /mm2,由于切削深度的增加使热作用时间加长,虽然单位切削功率降低,但单位能量稳定增加,所以随着切削深度的增加,进入工件表面的能量也相应增加。
因此在切深ae=1mm时,硬度层深度可达1.8mm。
X 射线分析表明,磨削淬硬零件的淬硬表层存在残余压应力。
磨削已淬硬钢时,热影响以及由此引起的相变(马氏体转化为珠光体)将引起残余拉应力。
而磨削淬硬工艺中的相变(珠光体转化为马氏体)将产生残余压应力,砂轮的机械作用也会在工件表面形成残余压应力。
珠光体转化为马氏体是磨削淬硬过程中形成残余应力的主要机制。
在淬硬层以下会检测到残余拉应力,通常磨削淬硬后的残余应力分布类似于表面感应淬火后的残余应力分布。
进给速度增大进给速度Vft通常会使磨削力增大,在磨削淬硬工艺中也是如此。
为分析进给速度对磨削淬硬工艺的影响,用刚玉砂轮对40CrMnMo钢进行了磨削试验研究(切削速度:Vc=35m/min,切削深度ae=0.1mm,无切削液)。
由式(1)可知,在其它参数不变的条件下,切向磨削力的增大会使功率消耗增大。
在进给速度Vft=5m/min 时,单位切削功率Pc=160W/mm2。
虽然磨削功率有所增加,但进入工件的单位能量计算结果却显示出完全相反的现象。
进给速度从Vft=0.01m/min增加到Vft=5.0m/min时,单位能量的计算结果由ec=1150J/mm2骤减至25J/mm2。
整体硬质合金刀具磨削裂纹的原因分析及其工艺改进
整体硬质合金刀具磨削裂纹的原因分析及其工艺改进1 引言整体硬质合金刀具在航空航天业、模具制造业、汽车制造业、机床制造业等领域得到越来越广泛的应用,尤其是在高速切削领域占有越来越重要的地位。
在高速切削领域,由于对刀具安全性、可靠性、耐用度的高标准要求,整体硬质合金刀具内在和表面的质量要求也更加严格。
而随着硬质合金棒材尤其是超细硬质合金材质内在质量的不断提高,整体硬质合金刀具表面的质量情况越来越受到重视。
众所周知,硬质合金刀具的使用寿命除了与其耐磨性有关外,也常常表现在崩刃、断刃、断裂等非正常失效方面,磨削后刀具的磨削裂纹等表面缺陷则是造成这种非正常失效的重要原因之一。
这些表面缺陷包括经磨削加工后暴露于表面的硬质合金棒料内部粉末冶金制造缺陷(如分层、裂纹、未压好、孔洞等)以及磨削过程中由于不合理磨削在磨削表面造成的磨削裂纹缺陷,而磨削裂纹则更为常见。
这些磨削裂纹,采用肉眼、放大镜、浸油吹砂、体视显微镜和工具显微镜等常规检测手段往往容易造成漏检,漏检的刀具在使用时尤其是在高速切削场合可能会造成严重的后果,因此整体硬质合金刀具产品磨削裂纹缺陷的危害很大。
因此对整体硬质合金刀具磨削裂纹的产生原因进行分析和探讨,并提出有效防止磨削裂纹的工艺改进措施具有很重要的现实意义。
2 整体硬质合金刀具磨削裂纹的原因分析1.整体硬质合金刀具的磨削加工特点硬质合金材料由于硬度高,脆性大,导热系数小,给刀具的刃磨带来了很大困难,尤其是磨削余量很大的整体硬质合金刀具。
硬度高就要求有较大的磨削压力,导热系数低又不允许产生过大的磨削热量,脆性大导致产生磨削裂纹的倾向大。
因此,对硬质合金刀具刃磨,既要求砂轮有较好的自砺性,又要有合理的刃磨工艺,还要有良好的冷却,使之有较好的散热条件,减少磨削裂纹的产生。
一般在刃磨硬质合金刀具时,温度高于600℃,刀具表面层就会产生氧化变色,造成程度不同的磨削烧伤,严重时就容易使硬质合金刀具产生裂纹。
【金属切削原理】第12章:磨削详解
《金属切削原理》第十二章:磨削加工详解磨削用于加工坚硬材料及精加工、半精加工内圆磨削外圆磨削平面磨削普通平面磨削圆台平面磨削超精磨削加工第一节砂轮的特性及选择砂轮由磨料、结合剂、气孔组成特性由磨料、粒度、结合剂、硬度、组织决定一、磨料分为天然磨料和人造磨料人造磨料氧化物系刚玉系(Al2O3)碳化物系碳化硅系碳化硼系超硬材料系人造金刚石系立方氮化硼系二、粒度表示磨粒颗粒尺寸的大小>63µm号数为通过筛网的孔数/英寸(25.4mm)机械筛分一般磨粒<63µm号数为最大尺寸微米数(W)显微镜分析法微细磨粒精磨细粒降低粗糙度粗磨粗粒提高生产率高速时、接触面积大时粗粒防烧伤软韧金属粗粒防糊塞硬脆金属细粒提高生产率国标用磨粒最大尺寸方向上的尺寸来表示三、结合剂作用:将磨料结合在一起,使砂轮具有必要的强度和形状1、陶瓷结合剂(A)常用由黏土等陶瓷材料配成特点:粘结强度高、耐热、耐酸、耐水、气孔率大、成本低、生产率高、脆、不能承受侧向弯扭力2、树脂结合剂(S)切断、开槽酚醛树脂、环氧树脂特点:强度高、弹性好、耐热性差、易自砺、气孔率小、易糊塞、磨损快、易失廓形、与碱性物质易反应、不易长期存放3、橡胶结合剂(X)薄砂轮、切断、开槽、无心磨导轮人造橡胶特点:弹性好、强度好、气孔小、耐热性差、生产率低4、金属结合剂(Q)磨硬质合金、玻璃、宝石、半导体材料青铜结合剂(制作金刚石砂轮)特点:强度高、自砺性差、形面成型性好、有一定韧性四、硬度在磨削力作用下,磨粒从砂轮表面脱落的难易程度分为超软、软、中软、中、中硬、硬、超硬工件材料硬砂轮软些防烧伤工件材料软砂轮硬些充分发挥磨粒作用接触面积大软砂轮精度、成形磨削硬砂轮保持廓形粒度号大软砂轮防糊塞有色金属、橡胶、树脂软砂轮防糊塞五、组织磨粒、气孔、结合剂体积的比例关系分为:紧密(0~3)、中等(4~7)、疏松(8~14)(磨粒占砂轮体积%↘)气孔、孔穴开式(与大气连通)占大部分,影响较大闭式(与大气不连通)尺寸小、影响小开式空洞型蜂窝型前两种构成砂轮内部主要的冷却通道管道型5~50µm六、砂轮的型号标注形状、尺寸、磨料、粒度号、硬度、组织号、结合剂、允许最高圆周线速度P300x30x75WA60L6V35外径300,厚30,内径75第二节磨削运动一、磨削运动1、主运动砂轮外圆线速度 m/s2、径向进给运动进给量fr 工件相对砂轮径向移动的距离间歇进给 mm/st 单行程mm/dst 双行程连续进给 mm/s3、轴向进给运动进给量fa 工件相对砂轮轴向的进给运动圆磨 mm/r平磨 mm/行程4、工件速度vw线速度 m/s二、磨削金属切除率ZQ=Q/B=1000·vw·fr·fa/B mm^3/(s·mm)ZQ:单位砂轮宽度切除率Q:每秒金属切除量用以表示生产率B:砂轮宽度三、砂轮与工件加工表面接触弧长lc=sqrt(fr·d0)影响参加磨削磨粒数目及磨粒负荷,容屑,冷却条件四、砂轮等效直径将外圆(内圆)砂轮直径换算成接触弧长相等的假想平面磨削的砂轮直径结论:对砂轮耐用度影响内圆>平面>外圆第三节磨削的过程一、单个磨粒的磨削过程磨粒的模型锐利120°圆锥钝化半球实际磨粒:大的负前角,大的切削刃钝圆半径滑擦、耕犁、切削滑擦:(不切削,不刻划)产生高温,引起烧伤裂纹耕犁:(划出痕迹)磨粒钝或切削厚度小于临界厚度,工件材料挤向两侧隆起切削:切削厚度大于临界厚度,形成切屑v↑→隆起↓(线性)塑性变形速度<磨削速度二、磨削的特点1、精度高、表面粗糙度小高速、小切深、机床刚性2、径向分力Fn较大多磨粒切削3、磨削温度高磨粒角度差、挤压和摩擦、砂轮导热差4、砂轮的自砺作用三、磨削的阶段1、初磨阶段实际磨深小于径向进给量2、稳定阶段实际磨深等于径向进给量3、清磨阶段实际磨深趋向于0提高生产率缩短1、2提高质量保证3第四节磨削力及磨削功率一、磨削力的特征分解成三个分力Ft切向力 Fn法向力 Fa轴向力特征:1、单位切削力k很大磨粒几何形状的随机性和参数的不合理性7000~20000kgf/mm^2 其他切削方式k<700kgf/mm^22、Fn值最大Fn/Ft 通常2.0~2.5工件塑性↓、硬度↑→Fn/Ft↑切深小,砂轮严重磨损 Fn/Ft 可达5~103、磨削力随磨削阶段变化初磨、稳定、光磨二、磨削力及磨削功率摩擦耗能占相当大的比例(70~80%)切向力(N):Ft=9.81·(CF·(vw·fr·B/v)+µ·Fn)径向力(N):Fn=9.81·CF·(vw·fr·B/v)·tan(α)·(π/2) vw:工件速度v:砂轮速度fr:径向进给量B:磨削宽度CF:切除单位体积切屑所需的能 kgf/mm^2µ:工件-砂轮摩擦系数α:假设粒度为圆锥时的锥顶半角磨削功率P=Ft·v/1000 Kw理论公式精度不高,常用实验测定(顶尖上安装应变片)第五节磨削温度耕犁、滑擦和形成切屑的能量全部转化成热,大部分传入工件一、磨削温度砂轮磨削区温度θA:砂轮与工件接触区的平均温度影响:烧伤、裂纹的产生磨粒磨削点温度θdot:磨粒切削刃与切屑接触部分的温度温度最高处,是磨削热的主要来源影响:表面质量、磨粒磨损、切屑熔着工件温升:影响:工件尺寸、形状精度受影响二、影响磨削温度的因素切削液为降温的主要途径1、工件速度对磨粒磨削点温度的影响大于砂轮速度vw↑→acgmax↑→F↑→θdot↑大v↑→acgmax↓→θdot↑小→摩擦热↑↗acgmax:单个磨粒最大切削厚度 mm假设:磨粒前后对齐,均匀分不在砂轮表面平面磨:acgmax=(2·vw·fa/(v·m·B))sqrt(fr/dt)外圆磨:acgmax=(2·vw·fa/(v·m·B))sqrt((fr/dt)+(fr/dw))dt:砂轮直径m:每毫米周长磨粒数用于定性分析2、径向进给量Frfr↑→acgmax↑→θdot↑fr↑→接触区↑→同时参加切削磨粒数↑→θA↑3、其他因素fa↑→θdot↑、θA↑工件材料硬度↑、强度、↑韧性↑→θdot↑、θA↑θA↑→工件温升↑vw↑→被磨削点与砂轮接触时间↓→工件温升↗三、磨削温度的测量(热电偶)第六节砂轮的磨损及表面形貌一、砂轮的磨损类型磨耗磨损磨粒磨损破碎磨损磨粒或结合剂破碎(取决于磨削力与磨粒、结合剂强度)破碎磨损消耗砂轮多磨耗磨损通过磨削力影响破碎磨损阶段初期磨损磨粒破碎磨损(个别磨粒受力大,磨粒内部应力与裂纹)二期磨损磨耗磨损三期磨损结合剂破碎磨损二、砂轮的耐用度T砂轮相邻两次修整期间的加工时间 s各因素通过平均切削厚度来影响T经验公式:T=6.67·(dw^0.6)·km·kt/(10000·(vw·fa·fr)^2)dw:工件直径kt:砂轮直径修正系数km:工件材料修正系数粗磨时间常用单位时间内磨除金属体积与砂轮磨耗体积之比来选择砂轮三、砂轮的修整作用去除钝化磨粒或糊塞住的磨粒,使新磨粒露出来增加有效切削刃,提高加工表面质量工具单颗金刚石、单排金刚石、碳化硅修整轮、电镀人造金刚石滚轮、硬质合金挤压轮等使用单颗金刚石:导程小于等于磨粒平均直径,每颗磨粒都能修整深度小于等于磨粒平均直径,提高砂轮寿命四、表面形貌单位面积上磨粒数目越多→acgmax↓→磨粒受力↓→磨粒寿命↑→T↑磨粒高度分布越均匀→粗糙度↓磨粒间距均匀性越好→粗糙度↓第七节磨削表面质量与磨削精度一、表面粗糙度比普通切削小小于 Ra2~4µmvw↓、v↑、R工↑、R砂↑、细粒度→粗糙度↓细粒度→m↑→粗糙度↓B↑→acgmax↓→粗糙度↓磨粒等高性好→粗糙度↓二、机械性能1、金相组织变化烧伤:C↑、合金元素↑→导热性↓→易烧伤高温合金↑→磨削功率↑→θA↑→易烧伤影响:破坏工件表层组织,产生裂纹,影响耐磨性和寿命2、残余应力原因:相变引起金相组织体积变化温度引起热胀冷缩和塑性变形的综合结果光磨10次残余应力减少2~3倍光磨15次残余应力减少4~5倍fa↓、fr↓→拉应力↓3、磨削裂纹磨削速度垂直方向上的裂纹(局部高温急冷造成热应力)三、磨削精度1、磨床与工件的弹性变形2、磨床与工件的热变形3、砂轮磨损导致形状尺寸变化3、磨床与工件振动研磨加工是应用较广的一种光整加工。
残余应力基本知识
拉伸作用引起凸出效应
垂直于表面的塑性“凸出”, 按照波松比关系,必然会产生 平行于表面的塑性收缩,而表 面之下未收缩,所以,
在被切削平面产生残余拉 应力
耕犁阶段
材料塑性滑移阶段
即“塑性凸出”,表面塑性收缩阶段
表一 残余应力峰值与喷丸预应力的关系
p(Kgf/mm2) +100 +75 +50 0 -98 rp(Kgf/mm2) -91 -88 -83 -63 +5
rp 51.30.5p(Kgf/mm2) (1)
上式的线性回归相关系数为0.973。
然后,对施加不同预应力喷丸,得到不 同残余应力的的钢板弹簧进行疲劳试验, 得到了这样的S—N曲线
残余应力基本知识简介
• 残余应力概念界定 • 残余应力的产生 • 残余应力的作用 • 残余应力的测量方法
一、残余应力的基本概念
定义
• 内应力:没有外力或外力矩作用而在物体内部存在并自身保持平衡的应力。
•历史回顾 1860年 Woehler 指出火车轴的断裂有内应力作用这个因素 1925年 Masing 首次提出将内应力分为三类。 1935年 Давиденков依据各类内应力对晶体的X射线衍射
内
外
残余 应力 (MPa)
实际测试得到的分布曲线却是这样的
400
300
200
100
剥层深度 (mm)
0
10
8
6
4
2
0
-100
-200
实测曲线与理论分析所得曲线 形状相似,区别在于表层及其 以下区间多了显著的拉应力。
实际情况是:钢板弯折 并没有达到90度,焊接 时施加外力,强制焊接 成型,于是把弹性变形 固定下来。