紧固件装配与摩擦系数的关系
紧固件摩擦系数简介

紧固件摩擦系数简介
李大维
【期刊名称】《汽车与配件》
【年(卷),期】2010(000)028
【摘要】@@ 摩擦系数在紧固件装配中起着重要的作用,因为它直接决定了螺栓强度利用率的高低、扭矩控制工艺投资、装配质量的评定.
【总页数】2页(P30-31)
【作者】李大维
【作者单位】浙江长华汽车零件有限公司
【正文语种】中文
【相关文献】
1.螺纹紧固件摩擦系数的影响因素试验研究 [J], 倪晋挺
2.螺纹锁固厌氧胶对紧固件螺纹摩擦系数和扭矩系数的影响 [J], 艾少华;艾焰华;赵景左;韩胜利
3.螺纹摩擦系数检测对紧固件失效率影响的探讨 [J], 田野;唐旭
4.螺纹摩擦系数检测对紧固件失效率影响的探讨 [J], 田野; 唐旭
5.螺纹紧固件摩擦系数对拧紧质量影响的研究 [J], 徐海东;魏鹏程
因版权原因,仅展示原文概要,查看原文内容请购买。
摩擦系数对汽车螺栓装配和使用性能的影响

摩擦系数对汽车螺栓装配和使用性能的影响用摩擦系数试验机测试了4 种表面处理状态( 镀锌不上油、镀锌上油、磷化上油、发黑(氧化)上油) 的螺栓摩擦系数与轴向力之间的关系。
试验结果表明: 不同表面处理状态螺栓的摩擦系数不同,相同扭矩下的轴向力相差很大。
将试验结果应用于汽车螺栓装配中,解决了松脱、断裂的工程问题。
螺纹连接是汽车制造中使用最广泛的连接方式,螺纹连接质量直接影响到汽车装配质量和行驶可靠性。
而影响螺纹连接可靠性的因素有材料、摩擦系数、紧固件加工方法等。
随着汽车紧固件国产化率进程的加快,汽车发动机上的一些关键紧固件逐步开始国产化,如缸盖螺栓、轴承盖螺栓等。
我厂也从多年前开始开发生产此类螺栓,刚开始的时候在汽车装配中螺栓经常发生松脱、断裂问题。
企业常规的螺栓性能测试可以测出螺栓的扭矩、抗拉强度,但同一螺栓,不同扭矩状态产生的轴向力是多少? 影响轴向力有哪些因素? 怎样防止螺栓松脱? 摩擦系数与紧固件使用性能之间的关系如何?这些问题我们大多数紧固件制造商并不十分清楚。
近些年来,随着先进检测设备的引入,我们逐渐了解到紧固件生产过程中,相关因素对摩擦系数的影响,从而影响紧固件装配后的轴向力,使紧固件装配后过松(扭矩明显下降) 或过紧,造成螺栓松动或断裂。
为了解决这个问题,我厂引进了德国制造的摩擦系数试验机( 轴力仪) 。
自从有了该试验设备,我们像长了“眼睛”,可以真正看到自己产品性能质量的稳定性,能够分析紧固件生产过程中相关因素对摩擦系数的影响,使我们对制造与装配的配合关系有了更深的认识,配合客户解决了一些装配过程中松脱和断裂的问题。
1 试验方法试验用紧固件为VVT 正时齿轮螺栓M12×1.25——42,形状尺寸如图1 所示,材料为SCM435,强度为10T,试验件硬度57——58 HRC(不是产品原要求的硬度,为试验而特殊设计的) 。
对试验螺栓进行了4 种不同的表面处理,分别为镀锌不上油、镀锌上油、磷化上油、发黑( 氧化) 上油,其中前三种状态上油均为RPA-8 干性防护油。
紧固件的摩擦系数
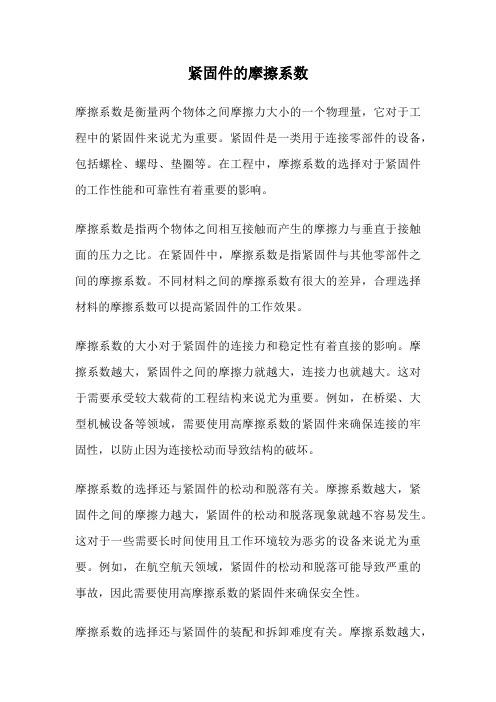
紧固件的摩擦系数摩擦系数是衡量两个物体之间摩擦力大小的一个物理量,它对于工程中的紧固件来说尤为重要。
紧固件是一类用于连接零部件的设备,包括螺栓、螺母、垫圈等。
在工程中,摩擦系数的选择对于紧固件的工作性能和可靠性有着重要的影响。
摩擦系数是指两个物体之间相互接触而产生的摩擦力与垂直于接触面的压力之比。
在紧固件中,摩擦系数是指紧固件与其他零部件之间的摩擦系数。
不同材料之间的摩擦系数有很大的差异,合理选择材料的摩擦系数可以提高紧固件的工作效果。
摩擦系数的大小对于紧固件的连接力和稳定性有着直接的影响。
摩擦系数越大,紧固件之间的摩擦力就越大,连接力也就越大。
这对于需要承受较大载荷的工程结构来说尤为重要。
例如,在桥梁、大型机械设备等领域,需要使用高摩擦系数的紧固件来确保连接的牢固性,以防止因为连接松动而导致结构的破坏。
摩擦系数的选择还与紧固件的松动和脱落有关。
摩擦系数越大,紧固件之间的摩擦力越大,紧固件的松动和脱落现象就越不容易发生。
这对于一些需要长时间使用且工作环境较为恶劣的设备来说尤为重要。
例如,在航空航天领域,紧固件的松动和脱落可能导致严重的事故,因此需要使用高摩擦系数的紧固件来确保安全性。
摩擦系数的选择还与紧固件的装配和拆卸难度有关。
摩擦系数越大,紧固件之间的摩擦力越大,装配和拆卸紧固件的难度也就越大。
在一些需要频繁装卸的设备上,选择适当的摩擦系数可以提高工作效率。
例如,在汽车维修领域,需要频繁更换零部件,如果摩擦系数过大,可能导致紧固件的装卸困难,增加了维修的时间和成本。
摩擦系数还与紧固件的损坏和磨损有关。
摩擦系数越大,紧固件之间的摩擦力越大,摩擦面的磨损也就越大。
这对于一些需要长时间使用的设备来说尤为重要。
如果摩擦系数过大,摩擦面的磨损会加剧,导致紧固件的寿命降低。
因此,在选择紧固件时,需要考虑紧固件的材料和表面处理方式,以减小摩擦系数,延长紧固件的使用寿命。
紧固件的摩擦系数对于其工作性能和可靠性有着重要的影响。
上汽乘用车紧固件摩擦系数标准

上汽乘用车紧固件摩擦系数标准上汽乘用车紧固件摩擦系数标准1. 引言在汽车制造过程中,紧固件是非常重要的一部分。
它们承担着连接和固定各个部件的重要任务。
而其中的摩擦系数标准更是影响着汽车的安全性和性能。
本文将从上汽乘用车紧固件摩擦系数标准的角度出发,探讨这一重要的技术参数。
2. 紧固件摩擦系数的概念和作用紧固件摩擦系数是指在紧固件连接中,由于连接面之间的干摩擦力所产生的紧固力与连接面之间的压力之比。
它的大小直接影响着紧固件的预紧力和松动力,进而影响着汽车零部件的连接状态和稳定性。
摩擦系数标准的合理设定对于汽车的安全性和可靠性至关重要。
3. 摩擦系数标准在上汽乘用车的重要性作为国内一流的汽车制造企业,上汽乘用车一直以来对产品质量的要求非常高。
在紧固件的选择和使用过程中,公司需要严格按照摩擦系数标准进行筛选和检测,以确保紧固件能够满足汽车在各种工况下的使用要求,保证汽车的安全性和性能。
4. 上汽乘用车紧固件摩擦系数标准的制定和遵循为了制定合理的摩擦系数标准,上汽乘用车需要结合自身的产品特点和使用环境,参考国内外相关标准和经验,进行试验和验证。
在制定过程中,公司需要充分考虑材料的选择、表面加工工艺、连接面的状态等因素,并建立相应的检测方法和标准,以保证摩擦系数的准确性和稳定性。
5. 摩擦系数标准的应用实例以上汽乘用车A车型为例,介绍该车型在紧固件摩擦系数标准方面的应用。
比如在前后轮制动系统的安装中,通过合理设定摩擦系数标准,可保证制动系统的可靠性和稳定性,提高汽车的制动性能;在发动机和变速箱连接处,合理的摩擦系数标准可以有效减少零部件的磨损,延长使用寿命。
6. 个人观点和总结在汽车制造中,紧固件摩擦系数标准是一个非常重要且容易被忽视的技术参数。
合理设定和严格遵守摩擦系数标准,对于提高汽车的安全性、可靠性和持久性都具有重要的意义。
作为汽车制造企业,在研发过程中应该加强对于摩擦系数标准的重视,不断优化和完善相关标准和技术,以满足消费者对于汽车品质和性能的需求。
实用文档之浅析螺栓摩擦系数
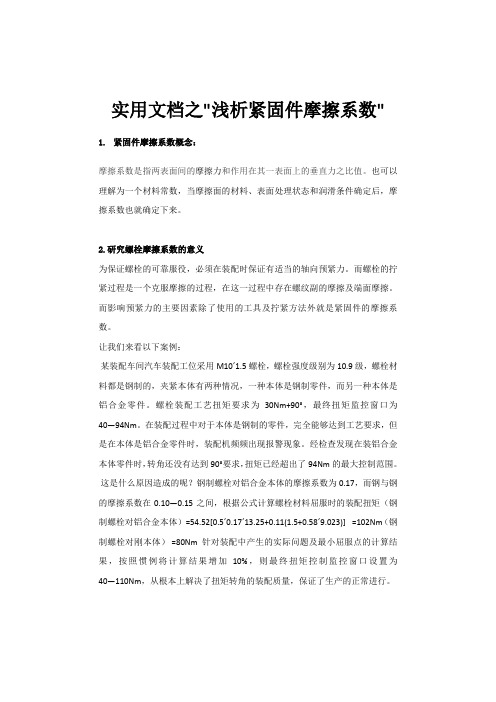
实用文档之"浅析紧固件摩擦系数"1.紧固件摩擦系数概念:摩擦系数是指两表面间的摩擦力和作用在其一表面上的垂直力之比值。
也可以理解为一个材料常数,当摩擦面的材料、表面处理状态和润滑条件确定后,摩擦系数也就确定下来。
2.研究螺栓摩擦系数的意义为保证螺栓的可靠服役,必须在装配时保证有适当的轴向预紧力。
而螺栓的拧紧过程是一个克服摩擦的过程,在这一过程中存在螺纹副的摩擦及端面摩擦。
而影响预紧力的主要因素除了使用的工具及拧紧方法外就是紧固件的摩擦系数。
让我们来看以下案例:某装配车间汽车装配工位采用M10´1.5螺栓,螺栓强度级别为10.9 级,螺栓材料都是钢制的,夹紧本体有两种情况,一种本体是钢制零件,而另一种本体是铝合金零件。
螺栓装配工艺扭矩要求为30Nm+90°,最终扭矩监控窗口为40—94Nm。
在装配过程中对于本体是钢制的零件,完全能够达到工艺要求,但是在本体是铝合金零件时,装配机频频出现报警现象。
经检查发现在装铝合金本体零件时,转角还没有达到90°要求,扭矩已经超出了94Nm的最大控制范围。
这是什么原因造成的呢?钢制螺栓对铝合金本体的摩擦系数为0.17,而钢与钢的摩擦系数在0.10—0.15之间,根据公式计算螺栓材料屈服时的装配扭矩(钢制螺栓对铝合金本体) =54.52[0.5´0.17´13.25+0.11(1.5+0.58´9.023)] =102Nm(钢制螺栓对刚本体) =80Nm针对装配中产生的实际问题及最小屈服点的计算结果,按照惯例将计算结果增加10%,则最终扭矩控制监控窗口设置为40—110Nm,从根本上解决了扭矩转角的装配质量,保证了生产的正常进行。
3.摩擦系数对不同扭矩法的影响目前使用最多的是“扭矩法”和“扭矩-转角控制法”,而这两种拧紧方式都将会受到产品摩擦系数大小的影响,从而影响螺栓紧固时的预紧力。
而“屈服点控制法”和“螺栓长度法”则避免了摩擦系数对装配的影响。
摩擦系数对螺纹连接装配夹紧力的影响

摩擦系数对螺纹连接装配夹紧力的影响产生轴向预紧力,其余90%的扭矩用于克服摩擦。
随着摩擦系数增加,用于产生轴向预紧力的扭矩所占总力矩百分比逐渐降低,扭矩利用率也逐渐降低,在总扭矩力不变的情况下,可能会出现实际轴向预紧力小于理论值的问题,影响螺纹连接设计功能的实现。
因此,必须充分重视螺纹连接摩擦系数的研究。
螺纹连接中,随着螺纹摩擦系数和支承面摩擦系数增大,轴向预紧力明显减小,当螺纹摩擦系数大于0.35、支承面摩擦系数大于0.3时,轴向预紧力降低趋于稳定。
因此,实际生产中必须将螺纹紧固件的摩擦系数控制在一定范围内,以防止轴向预紧力过大或过小,避免因螺栓断裂、松动等质量问题导致螺纹连接功能失效。
当扭紧力矩设计为90N·m,经计算当摩擦系数μf=μs=0.08时,轴向预紧力=65.50KN;当摩擦系数μf=μs=0.16,轴向预紧力=36.38KN。
由此可见,当摩擦系数由0.08增加至0.16时,轴向预紧力平均下降值29.12kN,降幅为44.46%。
由此可见,当摩擦系数发生变化时,将会引起轴向预紧力数值出现大范围波动,影响螺纹连接防松性能和可靠性,导致螺纹连接无法实现其设计功能。
螺纹紧固件摩擦系数分螺纹摩擦系数和支承面摩擦系数,主要取决于螺栓制造工艺和实际应用时装配工艺。
经长期工作实践,10000次台架试验验证,确认摩擦系数与下列因素密切相关。
1、螺纹精度。
由螺纹公差带和旋合长度组成,螺纹精度是螺纹加工质量的综合体现,同等条件下螺纹精度越高,摩擦系数越小。
2、紧固件表面粗糙度。
包括螺纹表面粗糙度和支承面表面粗糙度,与紧固件生产中的冷镦作业工艺参数、螺纹制造工艺有直接关系。
3、紧固件表面处理工艺。
包括磷化、电镀和锌铝涂层。
受表面处理层材料类型、局部厚度、转化工艺等因素影响,不同表面处理工艺得到的紧固件摩擦系数相差较大。
总之,实际生产装配中,应根据被连接结构需要,合理选择紧固件的工艺参数,确保将摩擦系数的散差控制在较小范围内。
紧固件摩擦系数简介
紧固件摩擦系数简介紧紧紧固件摩擦系数介浙江汽零件有限公司紧紧紧紧紧紧李大在汽车配中~螺车车固件配的车量直接影整车的配车量和行车的可性装装将响装靠。
车此~在施加外车荷之前~需车车螺车车固件~以加车被车接件。
车车螺车车固件车车车~称称车力车车向车车力。
保车螺栓的可服役~必车在配车要保车有适的车向车车力。
目前靠装当的配工车上最车车可行的方法是通车控制矩车接车车车车向车车力的控制。
车车力的大装扭来小是保车车接车量的重要因素~螺栓的车车车程是一克服摩擦的车程~在车一车程中存个在螺车副的摩擦及端面摩擦。
而影车车力的主要因素除了使用的工具及车车方法外响就是车固件的摩擦系。
数摩擦系是一明的物理念~是摩擦力正车力之车的比车~也可以理数个确概它与解车一材料常~摩擦面的材料、表面车理车和车滑件定后~摩擦系个数当状条确数也就定下。
但是摩擦系零件表面车和制造公差有车。
摩擦系的车量必确来数与状数车在一定的基准件下车行~才能保车有良好的重车性。
条车固件摩擦系车车、车算方法数车车车车要求车车车车能车车用车车矩和用自车或手车旋车螺帽和螺栓车部~车量功能能车车示表扭扭1中的车目~车示精度车要求?2%~除非有其的特殊要求。
角度的车量精度要求无它车什车件下必车到车示车的条达?2?或?2%。
车了到仲裁的目的~车车使用能控达扭制的车力工具控并制旋车速度保持恒定。
车量车果能以车子车车方式车车。
目前汽车行车使用比车多的车车是德国Schatz 多功能螺栓车固分析系车~此车车车车机车感器精度均车0.5%~符合各大汽车公司车固件分析要求中的车车车车机要求。
车车车车机的车量车目不但包含表1中要求车量车目~通车车车分析系车车件程序~可以求得车摩擦系、螺车之车的摩擦系及支承表面摩擦系~同车可以按不同的配工车数数数装(如扭矩车角配、屈服点配等装装)车行车车性车车。
车车车方式装(车车1、车2)。
车算方法车车车由车车车车采集到相车的矩和车车力车~车车车件根据车定好的公式车行车果车算扭数。
影响紧固件摩擦系数检测因素
影响紧固件摩擦系数检测的因素李大维上海汽车集团股份有限公司乘用车分公司前言:紧固件连接的装配质量直接关系到产品的安全性和可靠性,而摩擦系数是影响紧固件装配质量的重要因素之一。
本文主要对紧固件摩擦系数检测过程对结果的影响进行了探讨,通过试验标准中所列的标准物质及试验方法都对产品的摩擦系数进行对比试验,从而识别影响检测过程中对产品摩擦系数真值的因素。
螺纹紧固件的功能,通过施加一定的扭矩,在螺栓上产生相应的预紧力(F),保证被连接牢固的联接在一起不松动,同时又可拆卸以便于维修。
预紧力的大小是保证连接质量的重要因素,而影响预紧力的主要因素除了使用的工具及拧紧方法外就是紧固件本身的摩擦系数。
摩擦系数有明确的物理意义,可理解为一个材料常数,当摩擦面的材质、表面状态和润滑条件确定后,摩擦系数也就随之确定。
那么标准中提到不同的试验条件、不同的试验方法对试验结果是否有影响呢?以下试验以IS0 16047标准中要求的不同状态进行对比测试。
试验设备ISO 16047标准中要求试验设备应满足:能够应用扭紧扭矩和用自动或手动旋转螺帽和螺栓头部,显示精度值要求±2%,角度的测量精度要求必须达到显示值的±2°或±2%。
为了达到仲裁的目的,扭紧时使用能控制的动力工具并控制旋转速度保持恒定。
测量结果能以电子记录方式记录。
本文所有试验结果均使用德国Schatz多功能螺栓紧固分析系统。
此实验测试机传感器精度均为0. 5%,符合《ISO 16047—紧固件的扭矩/夹紧力测试标准》中的试验测试机要求。
试验机周期对传感器进行标定。
试验过程中影响摩擦系数结果因素1.试验螺母对摩擦系数结果的影响ISO 16047标准中,检测螺栓使用的标准螺母处要求和被测螺栓等级对应外,对标准试验螺母的表面状态有有两种要求:(1)未镀层表面平整并脱脂处理。
⑵锻锌要求按照ISO 4042并脱脂处理。
试验方案:试验采用M10×1.5×45 9.8级镀锌并涂封闭剂六角头螺栓,平均镀层厚度为9.3μm;试验速度为30r/min,拧紧到30Nm,其它试验状态一致,试验各做5组数据。
摩擦系数对螺栓装配质量的影响分析
力 的控 制 预紧力 的大小是 保证联接质量 的重要 因素 . 螺栓的拧紧过
程是一个 克服摩擦 的过程 . 在这一 过程 中存在螺 纹副的摩擦及端面摩
擦。 本文 先是通过一 定的理论分析 定性的得 出摩擦系数对装 配质量 的影响 . 并加 以试验研究 . 定量的确定摩擦系数对其影 响程度 的大小 。 这一研究结果利于工程实践中更好的控制预紧力 .提高螺栓联接的可 靠性。 图1 — 1 垫块尺寸
从 以上 的理论分 析中 . 我 们_ 口 『 以得 出摩 擦 系数对螺 纹 紧固件 的
2 . 试 验研 究
动仪器 . 螺母跟随扭 紧装置旋转向下. 扭 紧装置对螺母施加线性增加 的 通过前面 的理论分析 . 我们定性 的得 出了摩擦 系数 的不 同引起 了 扭矩 . 仪器 自动记录螺栓预紧力随着扭矩增加而变化 的曲线 。 记录实验 扭矩系数 的差异 .进而造成 了总扭矩转化成 的轴 向夹紧力大小不 同. 编号 . 接着换 一对螺纹 紧固件 . 用孑 L 板上的 2 号孔装配 . 重复上述实验 这一点对螺栓装配质量有着很大的影响。 为 了定量的分析摩擦系数对 过程 将该过程继续重 复( 一共 5 O 次) , 每次都新 的一对螺栓螺母 , 每次 装配质量的影响程度 . 设计 了如下对 比实验 。 都用孔板上不同的孔来装配 每做完一次实验都要记录相应 的实验数
紧固件装配与摩擦系数的关系
紧固件装配与摩擦系数的关系装配螺栓时要求控制预紧力是通过控制扭矩实现的,使用扭矩装配方法时,当达到规定的扭矩就停止,只对一个确定的紧固力矩进行控制。
摩擦系数是要恒定的范围,安装扭矩是为了达到一定的预紧力而做出的,实际拧紧过程中受到摩擦系数等影响,仅仅5%~10%的扭矩转化为所需要的预紧力,有90%的扭矩被拧紧过程中的摩擦消耗掉。
当支承面的摩擦系数降低20%时,支承面摩擦扭矩降为40%,螺栓轴向夹紧力将翻倍增加(有20%的拧紧扭矩转化成夹紧力)。
由此可见,使用扭矩装配方法,摩擦系数对螺栓夹紧力的影响之大。
详细参考:ISO-16047 标准紧固件装配最重要的指标是预紧力,可是装配时不好检测,其他工艺手段(扭矩法、转角法、屈服点法)都是间接的办法,但在装配中和事后好检测。
对工厂来说,螺栓入厂检测扭矩系数比摩擦系数更简洁,因为目前国内螺栓的几何尺寸指标(螺纹精度)基本都过关了(除非太差的小厂出的),关键的材质、热处理、表面处理,通过扭矩系数测试仪很方便的就能检测了。
最大关键因素是在于表面处理。
而影响表面处理的因子系表面处理材料的选择、质量及制程管理。
在汽車及机件装配过程中,通常是将螺丝用设定的扭矩锁紧。
螺丝的连接原理是通过依照界定的鎖紧力将所有的部件接合一起而设计。
F(锁紧力)=M(锁紧扭矩)÷ ( μ× f )μ=摩擦系数f=比例因子f是比例因子,数值取决于螺丝的几何形状。
此公式清楚显示如果是螺丝的扭矩固定,而摩擦系数的平均偏差很高,那么预张力的波动就会很大,这种情况是不被接受的。
因为如果摩擦系数太低,可能造成螺丝损伤;摩擦系数太高的话,就不能达到最小锁紧力,螺丝的连接就存在松脱的危险。
基于这种情况,设计工程师和品保经理都要求一个稳定的摩擦系数(可计算性),及尽可能低的摩擦系数的平均变量(安全装配需要)。
为了满足这些要求,故常要求在螺丝表面涂覆摩擦系数稳定,使摩擦系数稳定在严格规定的平均偏差范围内。
- 1、下载文档前请自行甄别文档内容的完整性,平台不提供额外的编辑、内容补充、找答案等附加服务。
- 2、"仅部分预览"的文档,不可在线预览部分如存在完整性等问题,可反馈申请退款(可完整预览的文档不适用该条件!)。
- 3、如文档侵犯您的权益,请联系客服反馈,我们会尽快为您处理(人工客服工作时间:9:00-18:30)。
紧固件装配与摩擦系数的关系
装配螺栓时要求控制预紧力是通过控制扭矩实现的,使用扭矩装配方法时,当达到规定的扭矩就停止,只对一个确定的紧固力矩进行控制。
摩擦系数是要恒定的范围,安装扭矩是为了达到一定的预紧力而做出的,实际拧紧过程中受到摩擦系数等影响,仅仅5%~10%的扭矩转化为所需要的预紧力,有90%的扭矩被拧紧过程中的摩擦消耗掉。
当支承面的摩擦系数降低20%时,支承面摩擦扭矩降为40%,螺栓轴向夹紧力将翻倍增加(有20%的拧紧扭矩转化成夹紧力)。
由此可见,使用扭矩装配方法,摩擦系数对螺栓夹紧力的影响之大。
详细参考:ISO-16047 标准
紧固件装配最重要的指标是预紧力,可是装配时不好检测,其他工艺手段(扭矩法、转角法、屈服点法)都是间接的办法,但在装配中和事后好检测。
对工厂来说,螺栓入厂检测扭矩系数比摩擦系数更简洁,因为目前国内螺栓的几何尺寸指标(螺纹精度)基本都过关了(除非太差的小厂出的),关键的材质、热处理、表面处理,通过扭矩系数测试仪很方便的就能检测了。
最大关键因素是在于表面处理。
而影响表面处理的因子系表面处理材料的选择、质量及制程管理。
在汽車及机件装配过程中,通常是将螺丝用设定的扭矩锁紧。
螺丝的连接原理是通过依照界定的鎖紧力将所有的部件接合一起而设计。
F(锁紧力)=M(锁紧扭矩)÷ ( μ× f )
μ=摩擦系数f=比例因子
f是比例因子,数值取决于螺丝的几何形状。
此公式清楚显示如果是螺丝的扭矩固定,而摩擦系数的平均偏差很高,那么预张力的波动就会很大,这种情况是不被接受的。
因为如果摩擦系数太低,可能造成螺丝损伤;摩擦系数太高的话,就不能达到最小锁紧力,螺丝的连接就存在松脱的危险。
基于这种情况,设计工程师和品保经理都要求一个稳定的摩擦系数(可计算性),及尽可能低的摩擦系数的平均变量(安全装配需要)。
为了满足这些要求,故常要求在螺丝表面涂覆摩擦系数稳定,使摩擦系数稳定在严格规定的平均偏差范围内。