紧固件摩擦系数简介
紧固件摩擦系数简介

紧固件摩擦系数简介
李大维
【期刊名称】《汽车与配件》
【年(卷),期】2010(000)028
【摘要】@@ 摩擦系数在紧固件装配中起着重要的作用,因为它直接决定了螺栓强度利用率的高低、扭矩控制工艺投资、装配质量的评定.
【总页数】2页(P30-31)
【作者】李大维
【作者单位】浙江长华汽车零件有限公司
【正文语种】中文
【相关文献】
1.螺纹紧固件摩擦系数的影响因素试验研究 [J], 倪晋挺
2.螺纹锁固厌氧胶对紧固件螺纹摩擦系数和扭矩系数的影响 [J], 艾少华;艾焰华;赵景左;韩胜利
3.螺纹摩擦系数检测对紧固件失效率影响的探讨 [J], 田野;唐旭
4.螺纹摩擦系数检测对紧固件失效率影响的探讨 [J], 田野; 唐旭
5.螺纹紧固件摩擦系数对拧紧质量影响的研究 [J], 徐海东;魏鹏程
因版权原因,仅展示原文概要,查看原文内容请购买。
螺栓的摩擦系数和预紧扭矩的关系
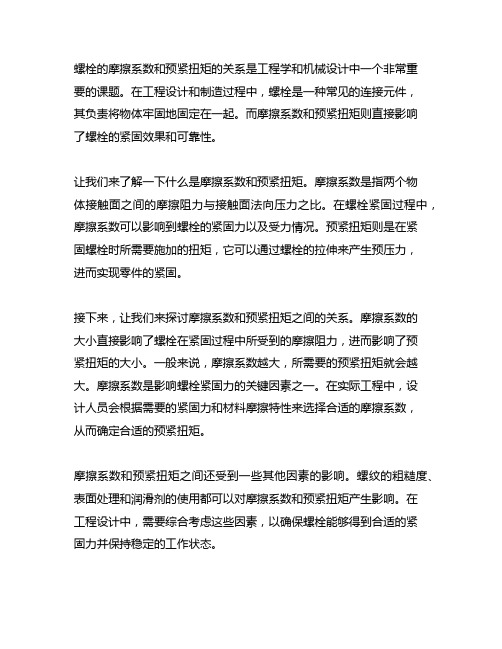
螺栓的摩擦系数和预紧扭矩的关系是工程学和机械设计中一个非常重要的课题。
在工程设计和制造过程中,螺栓是一种常见的连接元件,其负责将物体牢固地固定在一起。
而摩擦系数和预紧扭矩则直接影响了螺栓的紧固效果和可靠性。
让我们来了解一下什么是摩擦系数和预紧扭矩。
摩擦系数是指两个物体接触面之间的摩擦阻力与接触面法向压力之比。
在螺栓紧固过程中,摩擦系数可以影响到螺栓的紧固力以及受力情况。
预紧扭矩则是在紧固螺栓时所需要施加的扭矩,它可以通过螺栓的拉伸来产生预压力,进而实现零件的紧固。
接下来,让我们来探讨摩擦系数和预紧扭矩之间的关系。
摩擦系数的大小直接影响了螺栓在紧固过程中所受到的摩擦阻力,进而影响了预紧扭矩的大小。
一般来说,摩擦系数越大,所需要的预紧扭矩就会越大。
摩擦系数是影响螺栓紧固力的关键因素之一。
在实际工程中,设计人员会根据需要的紧固力和材料摩擦特性来选择合适的摩擦系数,从而确定合适的预紧扭矩。
摩擦系数和预紧扭矩之间还受到一些其他因素的影响。
螺纹的粗糙度、表面处理和润滑剂的使用都可以对摩擦系数和预紧扭矩产生影响。
在工程设计中,需要综合考虑这些因素,以确保螺栓能够得到合适的紧固力并保持稳定的工作状态。
总结来说,螺栓的摩擦系数和预紧扭矩的关系在工程设计和制造中具有重要意义。
摩擦系数的大小直接影响了预紧扭矩的大小,从而影响了螺栓的紧固力和可靠性。
在实际工程中,设计人员需要综合考虑各种因素,以选择合适的摩擦系数和预紧扭矩,从而确保螺栓的紧固效果。
个人观点和理解:在实际工程中,摩擦系数和预紧扭矩的选择需要依据具体的应用场景和要求进行综合考虑。
在材料选择、表面处理和设计参数确定时,需要充分考虑摩擦系数和预紧扭矩的影响,以确保螺栓能够达到预期的紧固效果。
对于润滑剂的选择和使用也需要慎重考虑,以避免对摩擦系数和预紧扭矩产生不良影响。
在文章总结中,我们可以清楚地看到摩擦系数和预紧扭矩在螺栓紧固过程中的重要性和影响因素。
通过全面的评估和深入的探讨,我们对这一课题有了更深入的理解,并能够在实际工程设计中更加灵活地应用和调整相关参数,从而确保螺栓的可靠使用。
摩擦系数 机械手册

摩擦系数机械手册摩擦系数是指两个表面之间的摩擦力与垂直于表面之间的压力之比。
它是机械工程领域中一个重要的参数,用来描述材料之间相互接触时的摩擦性能。
在机械设计和工程实践中,正确选择和使用摩擦系数可以提高机械系统的效率、减少能量损耗,并且降低机械零部件的磨损和损坏。
摩擦系数的大小取决于很多因素,如材料的表面粗糙度、温度和湿度等。
不同材料之间的摩擦系数通常是通过实验测量获得的。
一般来说,固体与固体之间的摩擦系数要大于流体与固体之间的摩擦系数,而润滑剂的使用可以降低两个表面之间的摩擦系数。
机械工程师需要了解各种材料的摩擦系数以便选择正确的材料和润滑方式,以满足设计要求。
在机械手册中,列举了各种常见材料的摩擦系数数据,以供工程师参考。
这些数据通常按照材料的种类和表面处理方式分类,以便读者快速找到所需的信息。
下面是一些常见材料的摩擦系数数据:1.金属材料:-不锈钢:0.6~0.8-铁:0.4~0.7-铝:0.3~0.6-黄铜:0.3~0.52.非金属材料:-聚乙烯:0.1~0.5-尼龙:0.2~0.4-聚四氟乙烯(PTFE):0.04~0.25-聚甲基丙烯酸甲酯(PMMA):0.4~0.6 3.润滑剂:-矿物油:0.1~0.2-锂基润滑脂:0.1~0.2-聚四氟乙烯润滑脂:0.04~0.1在机械设计中,摩擦系数的选择要根据具体的应用环境和要求来确定。
例如,在轴承设计中,通常希望摩擦系数尽可能小,以减少能量损耗和磨损。
而在钳口设计中,需要摩擦系数较大,以保证夹持力和稳定性。
在摩擦传动系统中,摩擦系数也需要根据所传递的力和速度等参数进行合理选择。
除了摩擦系数,摩擦力也是一个重要的参数。
摩擦力等于摩擦系数乘以垂直于两个表面的压力。
在机械系统中,摩擦力常常需要通过合理的设计来控制,以提高机械系统的效率。
总而言之,摩擦系数是机械工程中一个重要的参数,对机械系统的性能和寿命有着重要影响。
机械手册中提供了各种材料和润滑方式的摩擦系数数据,有助于工程师正确选择材料和设计摩擦传动系统。
摩擦系数与扭矩系数的关系
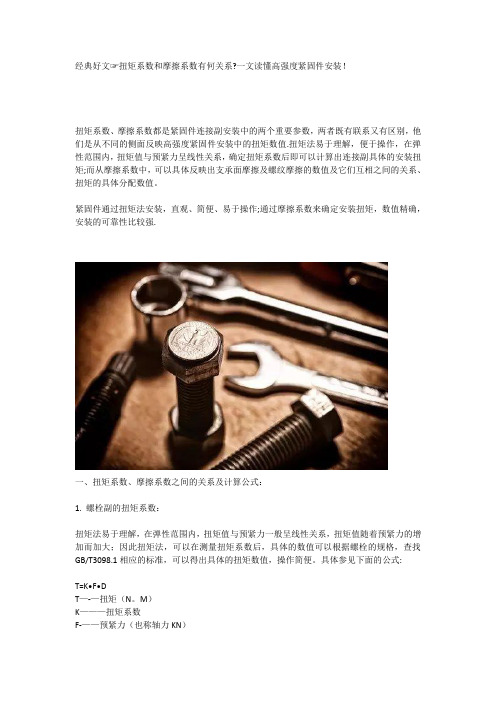
经典好文☞扭矩系数和摩擦系数有何关系?一文读懂高强度紧固件安装!扭矩系数、摩擦系数都是紧固件连接副安装中的两个重要参数,两者既有联系又有区别,他们是从不同的侧面反映高强度紧固件安装中的扭矩数值.扭矩法易于理解,便于操作,在弹性范围内,扭矩值与预紧力呈线性关系,确定扭矩系数后即可以计算出连接副具体的安装扭矩;而从摩擦系数中,可以具体反映出支承面摩擦及螺纹摩擦的数值及它们互相之间的关系、扭矩的具体分配数值。
紧固件通过扭矩法安装,直观、简便、易于操作;通过摩擦系数来确定安装扭矩,数值精确,安装的可靠性比较强.一、扭矩系数、摩擦系数之间的关系及计算公式:1. 螺栓副的扭矩系数:扭矩法易于理解,在弹性范围内,扭矩值与预紧力一般呈线性关系,扭矩值随着预紧力的增加而加大;因此扭矩法,可以在测量扭矩系数后,具体的数值可以根据螺栓的规格,查找GB/T3098.1相应的标准,可以得出具体的扭矩数值,操作简便。
具体参见下面的公式:T=K•F•DT—-—扭矩(N。
M)K———扭矩系数F-——预紧力(也称轴力KN)D---螺纹的公称直径(mm)扭矩系数是紧固件连接副安装时,必须要了解掌握的一个重要技术参数,目前安装扭矩、扭矩系数已经受到广大使用者的广泛理解、接受,并且在安装时普遍受关注。
扭矩及扭矩系数是既有联系又有区别的两个参数。
当扭矩数值选定后,扭矩系数越小,产生的紧固力越大;扭矩系数越大,产生的紧固力越小。
当扭矩系数小到一定的程度,在一定的扭矩的作用下紧固力超过了螺栓的强度极限,高强度螺栓就会产生伸长甚至断头的现象;反之,扭矩系数过大,产生的紧固力就会过小,整个螺栓连接副就达不到锁紧的功能,连接副就有可能产生松动情况。
因此,要使紧固力在一个标准的范围内,产品的扭矩系数就要限定在一个规定的范围内。
目前国家紧固件标准GB/T 1231-2000对钢结构用高强度螺栓连接副的标准作了规定,扭矩系数K=0.11-0.15,标准偏差≤0。
摩擦系数和紧固件装配关系

1. 請問大眾緊固件如何從安裝扭矩換算成摩擦系數?有何依據標準,謝謝!兩者之間的聯系無法直接體現,但在緊固件裝配中常見。
裝配螺栓時要求控制預緊力是通過控制扭矩實現的,使用扭矩裝配方法時,當達到規定的扭矩就停止,只對一個確定的緊固力矩進行控制。
簡單的說:摩擦系數是又恒定的范圍的!!安裝扭矩是為了達到一定的預緊力而做出的,實際擰緊過程中受到摩擦系數等影響,僅僅5%~10%的扭矩轉化為所需要的預緊力,有90%的扭矩被擰緊過程中的摩擦消耗掉。
當支承面的摩擦系數降低20%時,支承面摩擦扭矩降為40%,螺栓軸向夾緊力將翻倍增加(有20%的擰緊扭矩轉化成夾緊力)。
由此可見,使用扭矩裝配方法,摩擦系數對螺栓夾緊力的影響之大。
詳細參考:ISO-16047 標準2. 摩擦系数对装配过程的影响目前由于受到装配位置、装配工具等因素的影响,还不太可能在生产线上通过直接控制预紧力来装配螺栓联接,所以只能通过控制和预紧力相关的其它参数(如扭矩,螺栓头或螺母转角,螺栓伸长量)来达到间接控制预紧力的目的,相应地产生了以下几种预紧方法:“扭矩法”和“扭矩-转角控制法”、“屈服点控制法”和“螺栓长度法”。
其中使用最多的还是“扭矩法”和“扭矩-转角控制法”,而这两种拧紧方式都将会受到产品摩擦系数大小的影响,从而影响螺栓紧固时的预紧力。
而“屈服点控制法”和“螺栓长度法”则避免了摩擦系数对装配的影响。
扭矩装配法使用扭矩装配方法时,当达到规定的扭矩就停止,只对一个确定的紧固力矩进行控制,操作简单,扭矩容易测量和控制,扭矩事后也容易复检。
但经过大量的试验和实践经验的积累,在实际拧紧过程中受到摩擦系数等影响,仅仅5%~10%的扭矩转化为所需要的预紧力,有90%的扭矩被拧紧过程中的摩擦消耗掉。
当支承面的摩擦系数降低20%时,支承面摩擦扭矩降为40%,螺栓轴向夹紧力将翻倍增加(有20%的拧紧扭矩转化成夹紧力)。
由此可见,使用扭矩装配方法,摩擦系数对螺栓夹紧力的影响之大。
上汽乘用车紧固件摩擦系数标准

上汽乘用车紧固件摩擦系数标准上汽乘用车紧固件摩擦系数标准1. 引言在汽车制造过程中,紧固件是非常重要的一部分。
它们承担着连接和固定各个部件的重要任务。
而其中的摩擦系数标准更是影响着汽车的安全性和性能。
本文将从上汽乘用车紧固件摩擦系数标准的角度出发,探讨这一重要的技术参数。
2. 紧固件摩擦系数的概念和作用紧固件摩擦系数是指在紧固件连接中,由于连接面之间的干摩擦力所产生的紧固力与连接面之间的压力之比。
它的大小直接影响着紧固件的预紧力和松动力,进而影响着汽车零部件的连接状态和稳定性。
摩擦系数标准的合理设定对于汽车的安全性和可靠性至关重要。
3. 摩擦系数标准在上汽乘用车的重要性作为国内一流的汽车制造企业,上汽乘用车一直以来对产品质量的要求非常高。
在紧固件的选择和使用过程中,公司需要严格按照摩擦系数标准进行筛选和检测,以确保紧固件能够满足汽车在各种工况下的使用要求,保证汽车的安全性和性能。
4. 上汽乘用车紧固件摩擦系数标准的制定和遵循为了制定合理的摩擦系数标准,上汽乘用车需要结合自身的产品特点和使用环境,参考国内外相关标准和经验,进行试验和验证。
在制定过程中,公司需要充分考虑材料的选择、表面加工工艺、连接面的状态等因素,并建立相应的检测方法和标准,以保证摩擦系数的准确性和稳定性。
5. 摩擦系数标准的应用实例以上汽乘用车A车型为例,介绍该车型在紧固件摩擦系数标准方面的应用。
比如在前后轮制动系统的安装中,通过合理设定摩擦系数标准,可保证制动系统的可靠性和稳定性,提高汽车的制动性能;在发动机和变速箱连接处,合理的摩擦系数标准可以有效减少零部件的磨损,延长使用寿命。
6. 个人观点和总结在汽车制造中,紧固件摩擦系数标准是一个非常重要且容易被忽视的技术参数。
合理设定和严格遵守摩擦系数标准,对于提高汽车的安全性、可靠性和持久性都具有重要的意义。
作为汽车制造企业,在研发过程中应该加强对于摩擦系数标准的重视,不断优化和完善相关标准和技术,以满足消费者对于汽车品质和性能的需求。
实用文档之浅析螺栓摩擦系数
实用文档之"浅析紧固件摩擦系数"1.紧固件摩擦系数概念:摩擦系数是指两表面间的摩擦力和作用在其一表面上的垂直力之比值。
也可以理解为一个材料常数,当摩擦面的材料、表面处理状态和润滑条件确定后,摩擦系数也就确定下来。
2.研究螺栓摩擦系数的意义为保证螺栓的可靠服役,必须在装配时保证有适当的轴向预紧力。
而螺栓的拧紧过程是一个克服摩擦的过程,在这一过程中存在螺纹副的摩擦及端面摩擦。
而影响预紧力的主要因素除了使用的工具及拧紧方法外就是紧固件的摩擦系数。
让我们来看以下案例:某装配车间汽车装配工位采用M10´1.5螺栓,螺栓强度级别为10.9 级,螺栓材料都是钢制的,夹紧本体有两种情况,一种本体是钢制零件,而另一种本体是铝合金零件。
螺栓装配工艺扭矩要求为30Nm+90°,最终扭矩监控窗口为40—94Nm。
在装配过程中对于本体是钢制的零件,完全能够达到工艺要求,但是在本体是铝合金零件时,装配机频频出现报警现象。
经检查发现在装铝合金本体零件时,转角还没有达到90°要求,扭矩已经超出了94Nm的最大控制范围。
这是什么原因造成的呢?钢制螺栓对铝合金本体的摩擦系数为0.17,而钢与钢的摩擦系数在0.10—0.15之间,根据公式计算螺栓材料屈服时的装配扭矩(钢制螺栓对铝合金本体) =54.52[0.5´0.17´13.25+0.11(1.5+0.58´9.023)] =102Nm(钢制螺栓对刚本体) =80Nm针对装配中产生的实际问题及最小屈服点的计算结果,按照惯例将计算结果增加10%,则最终扭矩控制监控窗口设置为40—110Nm,从根本上解决了扭矩转角的装配质量,保证了生产的正常进行。
3.摩擦系数对不同扭矩法的影响目前使用最多的是“扭矩法”和“扭矩-转角控制法”,而这两种拧紧方式都将会受到产品摩擦系数大小的影响,从而影响螺栓紧固时的预紧力。
而“屈服点控制法”和“螺栓长度法”则避免了摩擦系数对装配的影响。
紧固件螺纹摩擦系数试验方法
螺纹紧固件的功能,通过施加一定的扭矩,在螺栓上产生相应的预紧力(F),保证被连接牢固的联接在一起不松动,同时又可拆卸以便于维修。
预紧力的大小是保证连接质量的重要因素,而影响预紧力的主要因素除了使用的工具及拧紧方法外就是紧固件本身的摩擦系数。
摩擦系数有明确的物理意义,可理解为一个材料常数,当摩擦面的材质、表面状态和润滑条件确定后,摩擦系数也就随之确定.那么标准中提到不同的试验条件、不同的试验方法对试验结果是否有影响呢?以下试验以IS0 16047标准中要求的不同状态进行对比测试。
试验设备ISO 16047标准中要求试验设备应满足:能够应用扭紧扭矩和用自动或手动旋转螺帽和螺栓头部,显示精度值要求±2%,角度的测量精度要求必须达到显示值的±2°或±2%.为了达到仲裁的目的,扭紧时使用能控制的动力工具并控制旋转速度保持恒定。
测量结果能以电子记录方式记录。
本文所有试验结果均使用衡翼HYtest多功能螺栓紧固分析系统。
此实验测试机传感器精度均为0。
5%,符合《ISO 16047—紧固件的扭矩/夹紧力测试标准》中的试验测试机要求.试验机周期对传感器进行标定。
试验过程中影响摩擦系数结果因素1.试验螺母对摩擦系数结果的影响ISO 16047标准中,检测螺栓使用的标准螺母处要求和被测螺栓等级对应外,对标准试验螺母的表面状态有有两种要求:(1)未镀层表面平整并脱脂处理。
⑵锻锌要求按照ISO 4042并脱脂处理。
试验方案:试验采用M10×1.5×45 9。
8级镀锌并涂封闭剂六角头螺栓,平均镀层厚度为9.3μm;试验速度为30r/min,拧紧到30Nm,其它试验状态一致,试验各做5组数据.试验采用相同等级螺母,第一组试验螺母采用未镀层表面平整并脱脂处理,螺母公差6H,试验数据见表1。
第一组试验螺母按照ISO 4042镀锌并脱脂处理,镀层厚度为8.6μm,螺母公差6H,试验数据见表2。
紧固件摩擦系数简介
紧固件摩擦系数简介紧紧紧固件摩擦系数介浙江汽零件有限公司紧紧紧紧紧紧李大在汽车配中~螺车车固件配的车量直接影整车的配车量和行车的可性装装将响装靠。
车此~在施加外车荷之前~需车车螺车车固件~以加车被车接件。
车车螺车车固件车车车~称称车力车车向车车力。
保车螺栓的可服役~必车在配车要保车有适的车向车车力。
目前靠装当的配工车上最车车可行的方法是通车控制矩车接车车车车向车车力的控制。
车车力的大装扭来小是保车车接车量的重要因素~螺栓的车车车程是一克服摩擦的车程~在车一车程中存个在螺车副的摩擦及端面摩擦。
而影车车力的主要因素除了使用的工具及车车方法外响就是车固件的摩擦系。
数摩擦系是一明的物理念~是摩擦力正车力之车的比车~也可以理数个确概它与解车一材料常~摩擦面的材料、表面车理车和车滑件定后~摩擦系个数当状条确数也就定下。
但是摩擦系零件表面车和制造公差有车。
摩擦系的车量必确来数与状数车在一定的基准件下车行~才能保车有良好的重车性。
条车固件摩擦系车车、车算方法数车车车车要求车车车车能车车用车车矩和用自车或手车旋车螺帽和螺栓车部~车量功能能车车示表扭扭1中的车目~车示精度车要求?2%~除非有其的特殊要求。
角度的车量精度要求无它车什车件下必车到车示车的条达?2?或?2%。
车了到仲裁的目的~车车使用能控达扭制的车力工具控并制旋车速度保持恒定。
车量车果能以车子车车方式车车。
目前汽车行车使用比车多的车车是德国Schatz 多功能螺栓车固分析系车~此车车车车机车感器精度均车0.5%~符合各大汽车公司车固件分析要求中的车车车车机要求。
车车车车机的车量车目不但包含表1中要求车量车目~通车车车分析系车车件程序~可以求得车摩擦系、螺车之车的摩擦系及支承表面摩擦系~同车可以按不同的配工车数数数装(如扭矩车角配、屈服点配等装装)车行车车性车车。
车车车方式装(车车1、车2)。
车算方法车车车由车车车车采集到相车的矩和车车力车~车车车件根据车定好的公式车行车果车算扭数。
紧固件摩擦系数-概述说明以及解释
紧固件摩擦系数-概述说明以及解释1.引言1.1 概述概述部分的内容可以按照以下方式编写:在紧固件设计和应用中,摩擦系数是一个十分重要的参数。
摩擦系数是指在两个表面接触并相对滑动时所产生的摩擦力与正压力之比。
它不仅会影响到紧固件的性能和可靠性,也会对装配过程和使用寿命产生重要的影响。
在工程实践中,选择合适的摩擦系数对于确保紧固件的工作正常以及减少因松动或脱落而引起的潜在危险十分重要。
低摩擦系数可确保紧固件在正常工作条件下保持稳定,而高摩擦系数则可以提高紧固件的保持力。
然而,摩擦系数的确定并不是一个简单的过程。
它受到多种因素的影响,包括材料的选择、表面处理、润滑条件等。
因此,在设计和选择紧固件时,需要综合考虑各种因素以确定最合适的摩擦系数。
本文将从紧固件的定义和分类开始,介绍摩擦系数的概念和作用,深入探讨影响紧固件摩擦系数的因素,并介绍常用的测试方法。
最后,我们将总结摩擦系数对紧固件性能的影响,探讨摩擦系数的优化方法,以及紧固件摩擦系数在不同应用领域中的具体应用。
通过对紧固件摩擦系数的研究,我们可以更好地理解该参数的重要性和潜在价值,为紧固件的设计和选择提供科学依据。
综上所述,本文旨在全面介绍紧固件摩擦系数及其相关内容,希望能够对读者在紧固件设计和选择方面提供有益的参考和指导。
文章结构部分的内容为:1.2 文章结构本文共分为三个部分:引言、正文和结论。
(1)引言部分主要包括概述、文章结构、目的和总结四个方面。
概述部分对紧固件摩擦系数的重要性进行了简要介绍,并引出了摩擦系数对紧固件性能的影响。
文章结构部分向读者介绍了文章的整体结构,包括引言、正文和结论三个部分,并简要描述了每个部分的内容。
目的部分明确了本文的研究目标,即探讨紧固件摩擦系数的定义、影响因素、测试方法,以及摩擦系数对紧固件性能的影响和优化方法。
总结部分提前总结了文章的主要内容和结论。
(2)正文部分是本文的核心内容,主要包括紧固件的定义和分类、摩擦系数的概念和作用、影响紧固件摩擦系数的因素,以及紧固件摩擦系数的测试方法。
- 1、下载文档前请自行甄别文档内容的完整性,平台不提供额外的编辑、内容补充、找答案等附加服务。
- 2、"仅部分预览"的文档,不可在线预览部分如存在完整性等问题,可反馈申请退款(可完整预览的文档不适用该条件!)。
- 3、如文档侵犯您的权益,请联系客服反馈,我们会尽快为您处理(人工客服工作时间:9:00-18:30)。
紧固件摩擦系数简介
浙江长华汽车零件有限公司李大维
在汽车装配中,螺纹紧固件装配的质量将直接影响整车的装配质量和行驶的可靠性。
为此,在施加外载荷之前,需拧紧螺纹紧固件,以加紧被联接件。
称拧紧螺纹紧固件为预紧,称该力为轴向预紧力。
保证螺栓的可靠服役,必须在装配时要保证有适当的轴向夹紧力。
目前的装配工艺上最经济可行的方法是通过控制扭矩来间接实现对轴向夹紧力的控制。
预紧力的大小是保证链接质量的重要因素,螺栓的拧紧过程是一个克服摩擦的过程,在这一过程中存在螺纹副的摩擦及端面摩擦。
而影响预紧力的主要因素除了使用的工具及拧紧方法外就是紧固件的摩擦系数。
摩擦系数是一个明确的物理概念,它是摩擦力与正压力之间的比值,也可以理解为一个材料常数,当摩擦面的材料、表面处理状态和润滑条件确定后,摩擦系数也就确定下来。
但是摩擦系数与零件表面状态和制造公差有关。
摩擦系数的测量必须在一定的基准条件下进行,才能保证有良好的重复性。
紧固件摩擦系数检测、计算方法
试验设备要求
试验设备
能够应用扭紧扭
矩和用自动或手
动旋转螺帽和螺
栓头部,测量功能
能够显示表1中
的项目,显示精度
值要求±2%,除非
有其它的特殊要
求。
角度的测量精
度要求无论什么
条件下必须达到
显示值的±2°或
±2%。
为了达到仲裁的目的,扭紧时使用能控制的动力工具并控制旋转速度保持恒定。
测量结果能以电子记录方式记录。
目前汽车行业使用比较多的设备是德国Schatz 多功能螺栓紧固分析系统,此实验测试机传感器精度均为0.5%,符合各大汽车公司紧固件分析要求中
的试验测试机要求。
实验测试机的测量项目不但包含表1中要求测量项目,通过测试分析系统软件程序,可以求得总摩擦系数、螺纹之间的摩擦系数及支承表面
摩擦系数,同时可以按不同的装配工艺(如扭矩转角装配、屈服点装配等)进行验证性试验。
试验装夹方式(见图1、图2)。
计算方法
试验时由检测设备采集到相应的扭矩和预紧力数值,试验软件根据设定好的公式进行结果计算。
根据ISO16047标准摩擦系数计算公式为:
其中:
式中,μtot为总摩擦系数,T为总扭矩,P为螺距,F为预紧力,d2为螺纹中径,Db为摩擦在螺帽或螺栓头部底下的支承表面有效摩擦直径,Do为支承垫圈表面的外径,dh为螺栓通过的垫圈或支承零件孔的直径。
螺栓副之间的摩擦系数计算公式为:
式中,μth为螺纹副之间摩擦系数,Tth螺纹摩擦扭矩。
螺栓头部摩擦系数的计算公式为:
其中,μb为紧固件头部摩擦系数,Tb为紧固件头部扭矩。
测试选测的标准螺母(螺栓)
选择的基准螺栓(螺母)要保持相同的状态才能确
保试验的重复性。
(1)螺纹公差。
基准螺栓(测试螺母)的公差应满足
公差等级6g,基准螺母(测试螺栓)的公差应满足公差等级
6H。
(2)表面状态。
标准中提供了两种表面状态,无镀
层的螺母(螺栓);按ISO 4042标准镀锌的螺母(螺栓)。
试
验前,通过脱脂处理,试验时不能有任何润滑油。
(3)性能等级,标准件的等级应当和被检测件的等
级相当或高于被检测件的等级。
试验垫片
试验垫片,应满足硬度5060HRC,面粗糙度满足Ra 0.5±0.3,其表面应当没有镀层和润滑油。
试验前应当作除油脂处理。
支承垫圈的外径必须大于被检测两零件的外部最大尺寸,内径符合表2尺寸。
试验过程
使用Schatz 多功能螺栓紧固分析系统可以用一个稳定的转速(无论这
个转速是多少),拧紧到被试验零件夹紧力试验载荷的( 0.75 Fp)75%.;也可以是开始使用较高的速度,然后停顿几s,再以一个低速拧紧到设定的扭矩值。
同时还可以拧紧到零件发生屈服。
试验零件(试验螺栓,试验螺钉,试验螺帽,试验垫圈和试验支承垫)将仅使用一次。
当计划重复实验重新使用旧的支承垫片时,确认个别的支承垫片确实是和新的一样。
摩擦系数对装配过程的影响
目前由于受到装配位置、装配工具等因素的影响,还不太可能在生产线上通过直接控制预紧力来装配螺栓联接,所以只能通过控制和预紧力相关的其它参数(如扭矩,螺栓头或螺母转角,螺栓伸长量)来达到间接控制预紧力的目的,相应地产生了以下几种预紧方法:“扭矩法”和“扭矩-转角控制法”、“屈服点控制法”和“螺栓长度法”。
其中使用最多的还是“扭矩法”和“扭矩-转角控制法”,而这两种拧紧方式都将会受到产品摩擦系数大小的影响,从而影响螺栓紧固时的预紧力。
而“屈服点控制法”和“螺栓长度法”则避免了摩擦系数对装配的影响。
扭矩装配法
使用扭矩装配方法时,当达到规定的扭矩就停止,只对一个确定的紧固力矩进行控制,操作简单,扭矩容易测量和控制,扭矩事后也容易复检。
但经过大量的试验和实践经验的积累,在实际拧紧过程中受到摩擦系数等影响,仅仅5%~10%的扭矩转化为所需要的预紧力,有90%的扭矩被拧紧过程中的摩擦消耗掉。
当支承面的摩擦系数降低20%时,支承面摩擦扭矩降为40%,螺栓轴向夹紧力将翻倍增加(有20%的拧紧扭矩转化成夹紧力)。
由此可见,使用扭矩装配方法,摩擦系数对螺栓夹紧力的影响之大。
扭矩-转角控制法
在拧紧螺栓时,先以设定的扭矩将螺栓拧紧,然后再将螺栓旋转到一个规定的角度,利用螺栓的弹性变形,来确保联接力达到规定的要求,这就是转角扭矩法。
这种方法可分为弹性区域拧紧法和塑性区域法。
此方法能较准确控制预紧力,螺栓材料完全被利用,仅与螺纹副摩擦及螺栓的屈服强度有关,设定的扭矩值常取所需拧紧扭矩值的25%左右。
虽然螺纹的摩擦系数对达到较小的扭矩产生的“阶段预紧力”有一定的影响,但是影响较小,而螺纹的摩擦系数对转角拧紧所产生预紧力没有影响,因为在弹性区或塑性区,如果弹性模量恒定,预紧力仅与螺栓伸长量有关,而伸长量与螺栓旋转的角度成正比。