本科毕业设计(论文)英文翻译
LK英文翻译
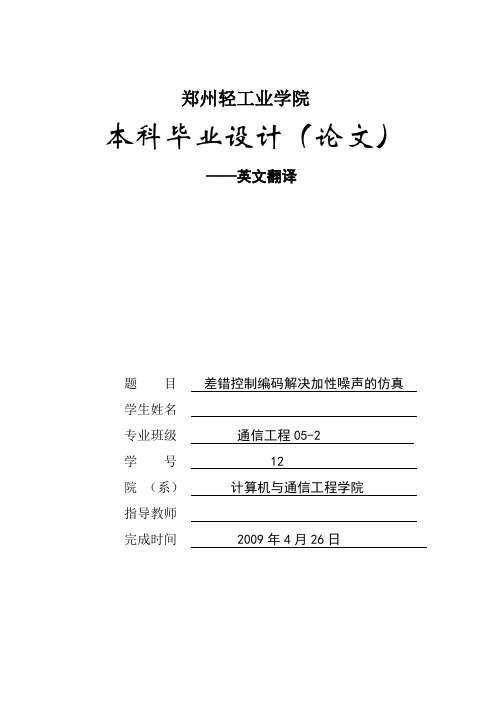
郑州轻工业学院本科毕业设计(论文)——英文翻译题目差错控制编码解决加性噪声的仿真学生姓名专业班级通信工程05-2 学号 12院(系)计算机与通信工程学院指导教师完成时间 2009年4月26日英文原文:Data communicationsGildas Avoine and Philippe OechslinEPFL, Lausanne, Switzerlandfgildas.avoine, philippe.oechsling@ep.chAbstractData communications are communications and computer technology resulting from the combination of a new means of communication. To transfer information between the two places must have transmission channel, according to the different transmission media, there is wired data communications and wireless data communications division. But they are through the transmission channel data link terminals and computers, different locations of implementation of the data terminal software and hardware and the sharing of information resources.1 The development of data communicationsThe first phase: the main language, through the human, horsepower, war and other means of transmission of original information.Phase II: Letter Post. (An increase means the dissemination of information)The third stage: printing. (Expand the scope of information dissemination)Phase IV: telegraph, telephone, radio. (Electric to enter the time)Fifth stage: the information age, with the exception of language information, there are data, images, text and so on.1.1 The history of modern data communicationsCommunication as a Telecommunications are from the 19th century, the beginning Year 30. Faraday discovered electromagnetic induction in 1831. Morse invented telegraph in 1837. Maxwell's electromagnetic theory in 1833. Bell invented the telephone in 1876. Marconi invented radio in 1895. Telecom has opened up in the new era. Tube invented in 1906 in order to simulate the development of communications.Sampling theorem of Nyquist criteria In 1928. Shannong theorem in 1948. The invention of the 20th century, thesemiconductor 50, thereby the development of digital communications. During the 20th century, the invention of integrated circuits 60. Made during the 20th century, 40 the concept of geostationary satellites, but can not be achieved. During the 20th century, space technology 50. Implementation in 1963 first synchronized satellite communications. The invention of the 20th century, 60 laser, intended to be used for communications, was not successful. 70 The invention of the 20th century, optical fiber, optical fiber communications can be developed.1.2 Key figuresBell (1847-1922), English, job in London in 1868. In 1871 to work in Boston. In 1873, he was appointed professor at Boston University. In 1875, invented many Telegram Rd. In 1876, invented the telephone. Lot of patents have been life. Yes, a deaf wife.Marconi (1874-1937), Italian people, in 1894, the pilot at his father's estate. 1896, to London. In 1897, the company set up the radio reported. In 1899, the first time the British and French wireless communications. 1916, implementation of short-wave radio communications. 1929, set up a global wireless communications network. Kim won the Nobel Prize. Took part in the Fascist Party.1.3 Classification of Communication SystemsAccording to type of information: Telephone communication system, Cable television system ,Data communication systems.Modulation by sub: Baseband transmission,Modulation transfer.Characteristics of transmission signals in accordance with sub: Analog Communication System ,Digital communication system.Transmission means of communication system: Cable Communications,Twisted pair, coaxial cable and so on.And long-distance telephone communication. Modulation: SSB / FDM. Based on the PCM time division multiple coaxial digital base-band transmission technology. Will gradually replace the coaxial fiber.Microwave relay communications:Comparison of coaxial and easy to set up, low investment, short-cycle. Analog phone microwave communications mainly SSB / FM /FDM modulation, communication capacity of 6,000 road / Channel. Digital microwave using BPSK, QPSK and QAM modulation techniques. The use of 64QAM, 256QAM such as multi-level modulation technique enhance the capacity of microwave communications can be transmitted at 40M Channel 1920 ~ 7680 Telephone Rd PCM figure.Optical Fiber Communication: Optical fiber communication is the use of lasers in optical fiber transmission characteristics of long-distance with a large communication capacity, communication, long distance and strong anti-interference characteristics. Currently used for local, long distance, trunk transmission, and progressive development of fiber-optic communications network users. At present, based on the long-wave lasers and single-mode optical fiber, each fiber road approach more than 10,000 calls, optical fiber communication itself is very strong force. Over the past decades, optical fiber communication technology develops very quickly, and there is a variety of applications, access devices, photoelectric conversion equipment, transmission equipment, switching equipment, network equipment and so on. Fiber-optic communications equipment has photoelectric conversion module and digital signal processing unit is composed of two parts.Satellite communications: Distance communications, transmission capacity, coverage, and not subject to geographical constraints and high reliability. At present, the use of sophisticated techniques Analog modulation, frequency division multiplexing and frequency division multiple access. Digital satellite communication using digital modulation, time division multiple road in time division multiple access.Mobile Communications: GSM, CDMA. Number of key technologies for mobile communications: modulation techniques, error correction coding and digital voice encoding. Data Communication Systems.1.4 Five basic types of data communication system:(1)Off-line data transmission is simply the use of a telephone or similar link to transmit data without involving a computer system.The equipment used at both ends of such a link is not part of a computer, or at least does not immediately make the data available for computer process, that is, the data when sent and / or received are 'off-line'.This type of data communication is relatively cheap and simple.(2)Remote batch is the term used for the way in which data communication technology is used geographically to separate the input and / or output of data from the computer on which they are processed in batch mode.(3)On-line data collection is the method of using communications technology to provide input data to a computer as such input arises-the data are then stored in the computer (say on a magnetic disk) and processed either at predetermined intervals or as required.(4)Enquiry-response systems provide, as the term suggests, the facility for a user to extract information from a computer.The enquiry facility is passive, that is, does not modify the information stored.The interrogation may be simple, for example, 'RETRIEVE THE RECORD FOR EMPLOYEE NUMBER 1234 'or complex.Such systems may use terminals producing hard copy and / or visual displays.(5)Real-time systems are those in which information is made available to and processed by a computer system in a dynamic manner so that either the computer may cause action to be taken to influence events as they occur (for example as in a process control application) or human operators may be influenced by the accurate and up-to-date information stored in the computer, for example as in reservation systems.2 Signal spectrum with bandwidthElectromagnetic data signals are encoded, the signal to be included in the data transmission. Signal in time for the general argument to show the message (or data) as a parameter (amplitude, frequency or phase) as the dependent variable. Signal of their value since the time variables are or not continuous, can be divided into continuous signals and discrete signals; according to whether the values of the dependent variable continuous, can be divided into analog signals and digital Signal.Signals with time-domain and frequency domain performance of the two most basic forms and features. Time-domain signal over time to reflect changing circumstances. Frequency domain characteristics of signals not only contain the same information domain, and the spectrum of signal analysis, can also be a clear understanding of the distribution ofthe signal spectrum and share the bandwidth. In order to receive the signal transmission and receiving equipment on the request channel, Only know the time-domain characteristics of the signal is not enough, it is also necessary to know the distribution of the signal spectrum. Time-domain characteristics of signals to show the letter .It’s changes over time. Because most of the signal energy is concentrated in a relatively narrow band, so most of our energy focused on the signal that Paragraph referred to as the effective band Bandwidth, or bandwidth. Have any signal bandwidth. In general, the greater the bandwidth of the signal using this signal to send data Rate on the higher bandwidth requirements of transmission medium greater. We will introduce the following simple common signal and bandwidth of the spectrum.More or less the voice signal spectrum at 20 Hz ~ 2000 kHz range (below 20 Hz infrasound signals for higher than 2000 KHz. For the ultrasonic signal), but with a much narrower bandwidth of the voice can produce an acceptable return, and the standard voice-frequency signal gnal 0 ~ 4 MHz, so the bandwidth of 4 MHz.As a special example of the monostable pulse infinite bandwidth. As for the binary signal, the bandwidth depends on the generalThe exact shape of the signal waveform, as well as the order of 0,1. The greater the bandwidth of the signal, it more faithfully express the number of sequences.3 The cut-off frequency channel with bandwidthAccording to Fourier series we know that if a signal for all frequency components can be completely the same through the transmission channel to the receiving end, then at the receiving frequency components of these formed by stacking up the signal and send the signal side are exactly the same, That is fully recovered from the receiving end of the send-side signals. But on the real world, there is no channel to no wear and tear through all the Frequency components. If all the Fourier components are equivalent attenuation, then the signal reception while Receive termination at an amplitude up Attenuation, but the distortion did not happen. However, all the transmission channel and equipment for different frequency components of the degree of attenuation is differentSome frequency components almost no attenuation, and attenuation of some frequency components by anumber, that is to say, channel also has a certain amount of vibrationIncrease the frequency characteristics, resulting in output signal distortion. Usually are frequency of 0 Hz to fc-wide channel at Chuan harmonic lost during the attenuation does not occur (or are a very small attenuation constant), whereas in the fc frequency harmonics at all above the transmission cross Decay process a lot, we put the signal in the transmission channel of the amplitude attenuation of a component to the original 0.707(that is, the output signal Reduce by half the power) when the frequency of the corresponding channel known as the cut-off frequency (cut - off frequency).Cut-off frequency transmission medium reflects the inherent physical properties. Other cases, it is because people interested in Line filter is installed to limit the bandwidth used by each user. In some cases, because of the add channel Two-pass filter, which corresponds to two-channel cut-off frequency f1 and f2, they were called up under the cut-off frequency and the cut-off frequency.This difference between the two cut-off frequency f2-f1 is called the channel bandwidth. If the input signal bandwidth is less than the bandwidth of channel, then the entire input signal Frequency components can be adopted by the Department of channels, which the letter Road to be the output of the output waveform will be true yet. However, if the input signal bandwidth greater than the channel bandwidth, the signal of a Frequency components can not be more on the channel, so that the signal output will be sent with the sending end of the signal is somewhat different, that is produced Distortion. In order to ensure the accuracy of data transmission, we must limit the signal bandwidth.4 Data transfer rateChannel maximum data transfer rate Unit time to be able to transfer binary data transfer rate as the median. Improve data transfer rate means that the space occupied by each Reduce the time that the sequence of binary digital pulse will reduce the cycle time, of course, will also reduce the pulse width.The previous section we already know, even if the binary digital pulse signal through a limited bandwidth channel will also be the ideal generated wave Shape distortion, and when must the input signal bandwidth, the smaller channel bandwidth, output waveformdistortion will be greater. Another angle Degree that when a certain channel bandwidth, the greater the bandwidth of the input signal, the output signal the greater the distortion, so when the data transmissionRate to a certain degree (signal bandwidth increases to a certain extent), in the on-channel output signal from the receiver could not have been Distortion of the output signal sent to recover a number of sequences. That is to say, even for an ideal channel, the limited bandwidth limit System of channel data transfer rate.At early 1924, H. Nyquist (Nyquist) to recognize the basic limitations of this existence, and deduced that the noise-free Limited bandwidth channel maximum data transfer rate formula. In 1948, C. Shannon (Shannon) put into the work of Nyquist 1 Step-by-step expansion of the channel by the random noise interference. Here we do not add on to prove to those now seen as the result of a classic.Nyquist proved that any continuous signal f (t) through a noise-free bandwidth for channel B, its output signal as a Time bandwidth of B continuous signal g (t). If you want to output digital signal, it must be the rate of g (t) for interval Sample. 2B samples per second times faster than are meaningless, because the signal bandwidth B is higher than the high-frequency component other than a letter has been Road decay away. If g (t) by V of discrete levels, namely, the likely outcome of each sample for the V level of a discrete one, The biggest channel data rate Rm ax as follows:Rmax = 2Blog 2 V (bit / s)For example, a 3000 Hz noise bandwidth of the channel should not transmit rate of more than 6,000 bits / second binary digital signal.In front of us considered only the ideal noise-free channel. There is noise in the channel, the situation will rapidly deteriorate. Channel Thermal noise with signal power and noise power ratio to measure the signal power and noise power as the signal-to-noise ratio (S ignal - to -- Noise Ratio). If we express the signal power S, and N express the noise power, while signal to noise ratio should be expressed as S / N. However, people Usually do not use the absolute value of signal to noise ratio, but the use of 10 lo g1 0S / N to indicate the units are decibels (d B). For the S / N equal 10 Channel, said its signal to noise ratio for the 1 0 d B; the same token, if the channel S / N equal to one hundred, then the signal to noiseratio for the 2 0 d B; And so on. S hannon noise channel has about the maximum data rate of the conclusions are: The bandwidth for the BH z, signal to noise ratio for the S / N Channel, the maximum data rate Rm ax as follows:Rmax = Blog 2 (1 + S / N) (bits / second)For example, for a bandwidth of 3 kHz, signal to noise ratio of 30 dB for the channel, regardless of their use to quantify the number of levels, nor Fast sampling rate control, the data transfer rate can not be greater than 30,000 bits / second. S h a n n o n the conclusions are derived based on information theory Out for a very wide scope, in order to go beyond this conclusion, like you want to invent perpetual motion machine, as it is almost impossible.It is worth noting that, S hannon conclusions give only a theoretical limit, and in fact, we should be pretty near the limit Difficult.SUMMARYMessage signals are (or data) of a magnetic encoder, the signal contains the message to be transmitted. Signal according to the dependent variable Whether or not a row of values, can be classified into analog signals and digital signals, the corresponding communication can be divided into analog communication and digital communication.Fourier has proven: any signal (either analog or digital signal) are different types of harmonic frequencies Composed of any signal has a corresponding bandwidth. And any transmission channel signal attenuation signals will, therefore, Channel transmission of any signal at all, there is a data transfer rate limitations, and this is Chengkui N yquist (Nyquist) theorem and S hannon (Shannon) theorem tells us to conclusions.Transmission medium of computer networks and communication are the most basic part of it at the cost of the entire computer network in a very Large proportion. In order to improve the utilization of transmission medium, we can use multiplexing. Frequency division multiplexing technology has many Road multiplexing, wave division multiplexing and TDM three that they use on different occasions.Data exchange technologies such as circuit switching, packet switching and packetswitching three have their respective advantages and disadvantages. M odem are at Analog phone line for the computer's binary data transmission equipment. Modem AM modulation methods have, FM, phase modulation and quadrature amplitude modulation, and M odem also supports data compression and error control. The concept of data communications Data communication is based on "data" for business communications systems, data are pre-agreed with a good meaning of numbers, letters or symbols and their combinations.参考文献[1]C.Y.Huang and A.Polydoros,“Two small SNR classification rules for CPM,”inProc.IEEE Milcom,vol.3,San Diego,CA,USA,Oct.1992,pp.1236–1240.[2]“Envelope-based classification schemes for continuous-phase binary Frequency-shift-keyed modulations,”in Pr oc.IEEE Milcom,vol.3,Fort Monmouth,NJ,USA,Oct.1994,pp. 796–800.[3]A.E.El-Mahdy and N.M.Namazi,“Classification of multiple M-ary frequency-shift keying over a rayleigh fading channel,”IEEE m.,vol.50,no.6,pp.967–974,June 2002.[4]Consulative Committee for Space Data Systems(CCSDS),Radio Frequency and Modulation SDS,2001,no.401.[5]E.E.Azzouz and A.K.Nandi,“Procedure for automatic recognition of analogue and digital modulations,”IEE mun,vol.143,no.5,pp.259–266,Oct.1996.[6]A.Puengn im,T.Robert,N.Thomas,and J.Vidal,“Hidden Markov models for digital modulation classification in unknown ISI channels,”in Eusipco2007,Poznan,Poland, September 2007,pp.1882–1885.[7]E.Vassalo and M.Visintin,“Carrier phase synchronization for GMSK signals,”I nt.J.Satell. Commun.,vol.20,no.6,pp.391–415,Nov.2002.[8]J.G.Proakis,Digital Communications.Mc Graw Hill,2001.[9]L.Rabiner,“A tutorial on hidden Markov models and selected applications in speechrecognition,”Proc.IEEE,vol.77,no.2,pp.257–286,1989.英文译文:数据通信Gildas Avoine and Philippe OechslinEPFL, Lausanne, Switzerlandfgildas.avoine, philippe.oechsling@ep.ch摘要数据通信是通信技术和计算机技术相结合而产生的一种新的通信方式。
本科毕业设计外文翻译(中文)
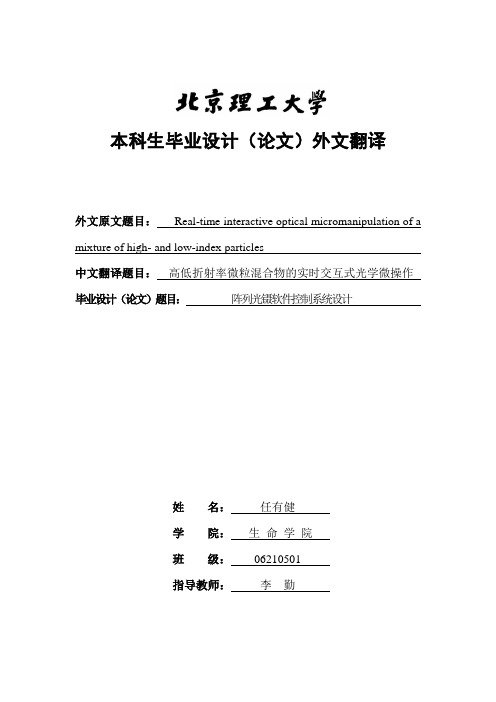
本科生毕业设计(论文)外文翻译外文原文题目:Real-time interactive optical micromanipulation of a mixture of high- and low-index particles中文翻译题目:高低折射率微粒混合物的实时交互式光学微操作毕业设计(论文)题目:阵列光镊软件控制系统设计姓名:任有健学院:生命学院班级:06210501指导教师:李勤高低折射率微粒混合物的实时交互式光学微操作Peter John Rodrigo Vincent Ricardo Daria Jesper Glückstad丹麦罗斯基勒DK-4000号,Risø国家实验室光学和等离子研究系jesper.gluckstad@risoe.dkhttp://www.risoe.dk/ofd/competence/ppo.htm摘要:本文论证一种对于胶体的实时交互式光学微操作的方法,胶体中包含两种折射率的微粒,与悬浮介质(0n )相比,分别低于(0L n n <)、高于(0H n n >)悬浮介质的折射率。
球形的高低折射率微粒在横平板上被一批捕获激光束生成的约束光势能捕获,捕获激光束的横剖面可以分为“礼帽形”和“圆环形”两种光强剖面。
这种应用方法在光学捕获的空间分布和个体几何学方面提供了广泛的可重构性。
我们以实验为基础证实了同时捕获又独立操作悬浮于水(0 1.33n =)中不同尺寸的球形碳酸钠微壳( 1.2L n ≈)和聚苯乙烯微珠( 1.57H n =)的独特性质。
©2004 美国光学学会光学分类与标引体系编码:(140.7010)捕获、(170.4520)光学限制与操作和(230.6120)空间光调制器。
1 引言光带有动量和角动量。
伴随于光与物质相互作用的动量转移为我们提供了在介观量级捕获和操作微粒的方法。
过去数十年中的巨大发展已经导致了在生物和物理领域常规光学捕获的各种应用以及下一代光学微操作体系的出现[1-5]。
外文翻译-引擎机械概述
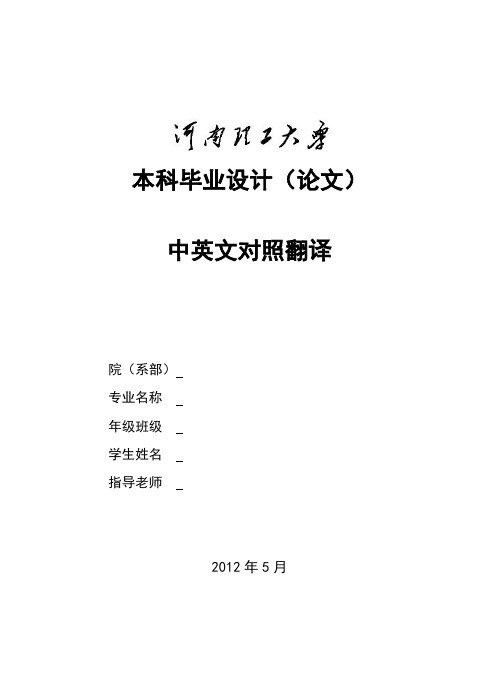
本科毕业设计(论文)中英文对照翻译院(系部)专业名称年级班级学生姓名指导老师2012年5月ENGINE MECHANICALOperation Main Components and Classification of the Engine The automotive engine is essentially a heat mobiles are internal combustion engines.Princiole of OperationThe spark-ignition engine is an internal-combustion engine with externally supplied in ignition .The gasoline engine is a kind of spark-ignition engines.The four-stroke-cycle gasoline engine cycle is spread over four pistion strokes.The first stroke in your engine is called the intake stroke. Instead of opening the intake valve after you have drawn the poston down . you will find it better to open the intake valve as the piston starts down . This allows the air to draw fuel in the entire time the piston is moving down.Remember , the intake stroke starts with the piston at the top of the cylinder(intake valve open and exhaust valve closed)and stops with the piston at the bottom of its travel . This requires one half turn of the crankshaft.As the crankshaft continues to move , the piston is forced up through the cylinder . If you keep both valves closed , the fuel mixture will be squeezed , or compressed , as the piston reaches the top .This is called the compression stroke . It , too , requires a half turn of the crankshaft .The compression stroke serves to break up the fule into even smaller particles . This happens due to the the sudden swelling and churning of the mixture as it is compressed .When the air fule mixture is subjected to a sudden sharp compression force . its temperature rises .This increase in temperature makes the mixture easier to ignite and causes it to explode with greater force , As the piston reaches the top of its travel on the compression sroke , it has returned to the pro[er position to be pushed back down by the explosion.Remember , the compression stroke starts with the piston at the bottom of the cylinder(both valves closed)and the stops with the piston at the top of the cylinder . This requires an additional half turn of crankshaft .As the piston reaches the top the compression stroke ,the mixture is broken into tiny particles and heated up . when ignited , it will explode with great force . This is the right time to explode the mixture . A spark plug provides a spark inside the combustion chamber ,The spark produced at the plug is formed by the ignition system.Just imagine that a hot spark has been provided in the fuel mixture .The mixture will explode and , in turn , force the piston down into the cylinder . This gives the crankshaft a quick and forceful push . This is the power stroke , Both valves must be kept closed during the power stroke or the pressure of the burning fuel will squirt out through the valve ports . Remenber , the power storke starts with the piston at the top of ylinder(both valves closed) and stops with the piston at the botton of the cylinder , T his requires another half turn of the crankshaft .When the piston reaches the bottom of the power stroke .the exhaust valve opens . The spinning crankshaft forces the piston up through the cylinder , pushing burned gases out . This is the exhaust stroke .Remenber , the exhaust stroke starts with the piston at the bottom of the cylinder (exhaust valve open and intake valve closed) . It stops with the piston at the top of the cylinder . This requires one more half turn of the crankshaft .If you count the number of half turns in the intake , compression , power , and exhaust storkes , You will find you have a total of four , This gives you two complete turns , or revolutions ,of the crankshaft . When the crankshaft is turning around twice ,it is receiving power only during one half turn , or one fourth of the time .As soon as the piston reaches the top of the exhaust stroke , it starts down on another intake , compression , power ,and exhaust cycle , this cycle is repeated over and over ,Each complete cycle consists of four strokes of the piston , hence the name four-storke cycle.Main Engine ComponenntsEngine BlockThe engine block serves as a rigid metal foundation for all parts of engine . It contains the cylinders and supports the crankshaft and camshaft . In older engines ,the valve seats , ports ,and guides are built into the block ,Accessry unis and the clutch housing are boled to it .Blocks are made of either cast iron or aluninum ,The lighter the block(providing it has sufficient strength), the better ,The modern thin-wall casting proces controls core size and placement much more accuratcely than the older casting process .This permits casting the block walls much thinner , reducing the weight of the block .Since the bolck wall thickness is more uniform , block distortion during service less severe .CylindersThe cylinder is a aroud hole formed in the block .It forms a guide guide for the piston and acts as a containner for taking in , compressing ,firing , and the exhausting the air-fuel chareg , Cylinder have been made of both steel and cast iron .Cast iron is by far the most popular.When steel cylinders are desired in an aluminum block, they are installed in the form of cylinder sleeves(round , pipe-like liners ), These sleeves may be eiher cast or pressed into the block ,Some engines use removable cylinder sleeves . When the cylinde becomes won The old sleeves can be pulled out and new sleeves can be pressed in . The sleeves are pressed into oversize cylinder holes ,Cylinder sleeves are widely used in heavy-duty truck and industrial engines ,Sleeves can also be used to be repair a won or cracked cylinder in a cast iron block .PistonsThe piston must move down through the cylinder to the cylinder to produce a vacuum to draw a fuel charge into the cylinder . It then travels up in the cylinder and compresses the mixture ,When the mixture is fired , the pressure of the expanding gas is transmitted to the top of piston . This drives the piston back down through the cylinder with great force , transmitting the expanding gas to the crankshaft ,The piston then then travels up through the cylinder and exhaust the burned fuel charge.Pistons are usually made of aluminum . Often ,aluminum piston are tin-plated to allow proper break-in when the engine is stared ,Aluminum pistons can be forged ,but they are more commonly cast .Cast iron is a good material for pistons used m a slow-speed engine .It has excellent wear characteristics and will provide good performance .Connecting RodsAs the name implies , connecting rods are used to connect protons to the crankshaft .The upper end of the rod oscillates(swings back and forth), while the lower ,or big end ,bearing rotates(turns).Because there is very little bearing movement in the upper end , the bearing area can be reasonably small . The lower end rotates very fast , and the crankshaft bearing journal turns inside the connecting rod . This rotational speed tends to produce heat and wear .To make the rod wear well, a larger bearing area is required.The upper end of the rod has a hole through it for the piston pin ,The botton of the large end of the connecting red must be removed SO the rod can be installed on the crankshaft journal .The section that is removed is called the connecting rod cap.Connecting rods are normally made of alloy steel .They are drop-forged shape and then machined .CrankshaftThe engine crankshaft provides a constant turning force to the wheels ,it has through to which connecting rods are attached ,and its function to change the reciprocating motion of the piston to a rotary motion to drivethe wheels . Crankshaft are made of alloy steel or cast iron.The crankshaft is held in position by a series of main bearings ,The maximum mumber of main bearings for a crankshaft is one more than the munber of cylinders. It may have fewer main bearings than cylinder .Most engines use pressman insert bearings that are constructed like the connecting rod bearings, But are somewhat larger .In addition to supporting the crankshaft , one of the main bearings must control the forward and backward movement.FlywheelA heavy flywheel is attached to the rear of the crankshaft with bolts ,The function of the flywheel is to smooth out engine speed and keep the crankshaft spinning between power strokes . in some engines , the flywheel also serves as a mounting ,surface for the clutch . The outer rim of the flywheel has a large ring attached with gear teeth cut into it , The teeth of the starter motor engine these teeth and spin the flywheel to crank the engine . When all automatic transmission is used ,the torque converter assembly works with the flywheel.CamshaftThe camshaft is used to open and close the valves . There is one cam on the camshaft for each valve in the engine ,Generally only one camshaft is used in most engines . Newer engines are increasingly equipped with two or more camshaft.ValvesEach engine cylinder ordinarily has two valves . However , modern engines often use four valves per cylinder(two intake and two exhaust), A few engines used in smaller vehicles have three intake valves per cylinder : two intake valves and one exhaust valves or three intake valves and two exhaust valves .Because the head of an exhaust valve operates at temperatures up to 1300C(704C) ,valves are made of heat-resistant metal . In order to prevent burning ,the valve must give off heat to the valve seat and to the valve guide . The valve must be make good contact with seat and must run with minimum clearance in the guide .Valve LiftersMechanical valve lifters are usually made of cast iron , The bottom Dart that contacts the camshaft is hardened .Some lifters are hollow to reduce weight .Most valve trains that contain mechanical lifters have some provision for adjusting clearance . Mechanical valve lifters were used in older engines .Hydraulic valve lifters perform the same job as mechanical lifters , However ,hydraulic lifters are self-adjusting , operate with no lifte-to –rockerarm clearance . and uses engine oil under pressure to operate ,Hydraulic lifters are quite in operration .Engine ClassificationCycle ClassificationEngines are often classified according to cycle . Most internal combustion piston engines use a two-or four –stroke cycle .All modern automobile engines use the four stroke cycle engine .The two-stroke cycle engine performs the intake , compression , firing , and exhaust sequence in one revolution of the crankshaft.Cylinder ClassificationThe inline engine has its cylinders arranged one after the other in a straight line , They are in a vertical , or near vertical position . Most modern inline engines are four cylinders .A V-type engine places two banks or rows of cylinders at an angle to each other-genre-ally at 60or 90 ,The V-type engine has several advantages: short length , extra block rigidity , a short , heavy crankshaft , and low profile that is conducive to low hood lines , The shorter block permits a reduction in vehicle length with riot sacrifice in passenger room .The horizontal opposed engine is like a V-type engine , except that both banks lie in a horizontal plane . The advantage here is all extrmely low overall height .Which makes this engine ideally suited installations where space is limited .Cooling ClassificationAs you have learned ,engines are either liquid-collde or air-colled . Most vehicles use liquid-colled engines .Air-colled engines are used in limited numbers modern vehicles .Fuel ClassificationAutomobile engines can use gasoline , diesel fule , gasohol(mixture of gasoline and alcohol), alcohol , LNG(liquefied natural gas) ,CNG(compressed natural gas) ,or LPG(liquefied propane gas ) .Gasoline powers the majority of vehicles , but diesel fule is used in some vehicles .Gosohol ,LNG ,CNG ,and LPG are beginning to see wider use .One of the principle differences in these engines is in method of fuel delivery and carburction .Gasoline ,LNG ,CNG ,and LPG utilize the same basic type of engine , but LNG ,CNG ,and LPG utilize a slightly different fule delivery setup .Diesel engines do not use a carburetor or all ignition system .Valve SystemOperation of Valve systemYou have seen that the intake valve stroke .Both valves must remain closed during the compression and power stroke ,and the eshaust valve opens during the exhaust stroke , The designer must design a device to open and close the valves at the proper times .The shaft will have an egg-shaped bump called a cam lobe .The cam lobe is machined as an integral part of the shaft .This shaft is called a camshaft .The distance the valve will be raised , how long it will stay open , and how fast it opens and closes can all be controlled by the height and shape of the hole .As you will see later , it is impractical to have the cam lobe contact the end of valve stem .When the camshaft is turn ,the lobes will not even touch the valve stem ,The lifter is installed between the cam lobe and the valve stem . The upper end rides on the lobe and the lower and almost touches the valve stem . The lifter slides up and down in a a hole bored in the head metal that separates the valve stem from the camshaft .You have developed a method of opening and closing the valves .The next problem is how and at what speed to turn the camshafts , Each valve must be open for one storke .The intake valve is open during the intake storke and remains closed during the compression ,power ,and exhaust stroke .This would indicate that the cam lobe must be turn fast enough to raise the valve erery fourth stroke .You can see that it takes one complete revolution of the cam lobe four strokes of the piston .Remember that four srokes of the piston require two revolutions of the crankshaft , the cam shaft must be once , If you are speaking of the speed of the camshaft ,you can say that the camshaft must turn at one-half crankshaft speed .If the crankshaft is turning and the camshaft must turn at one-half crankshaft speed , it seems logical to use the spinning crankshaft to turn the camshaft ,One very simple way to drive the camshaft would be by means of gears and a belt . One gear is fastened on the end of the crankshaft ,and the other is fastened on the end of the camshaft .The large camshaft gear drives the smaller crankshaft gear through the belt .If ,for instance ,the small gear Oil the crankshaft has 10 teeth and the large gear on the camshaft has 20 teeth ,the crankshaft will truth the camshaft at exactly one-half crankshaft speed .VVT-Toyota`s Continuously Variable Valve TimingThe most significant and satisfying changes to the Lexus GS line are inthe area power train . In the case of GS300 , Lexus breathes new life into last year`s 3.0Lin-line six by introducing VVT-continuously variable valve timing syestem .On the dyne ,VVT shows up as only five additional horsepower and 10 lb-ft of torque . But in the car it meansfuel economy improvements of 1.6 mpg .smoother idle ,California TLEV (transitional tow-emissions vehicle )certification and zero-to 60 mph a half second quicker .Toyota eliminates the compromise of conventional valve timig with the introduction of VVT , By continuously varying intake valve timing (up to 60 crank angle degrees) , Toyota optimizes low-to mid-speed torque , improves fule economy and lowers emissions without having a negative impact on idle .In essence ,the system controls valve overlap ,which means it can climinate it completyly for a glass smooth idle . or maximize it to boost volumetric efficiency ang reduce pumping losses this translates into power ,economy and cleaner running at all engine speeds.The heart of the system is the intake cam pulley , which consists of an inner and outer section ,The inner portion is fixed to the camshaft and nests inside the belt-driven outer pulley via helical spline gears . An electronically controlled hydraulic piston moves the pully halves relative to one another ,causing the cam portion to rotate within the outer pulley.This rotation davances or retarda intake valve timing .A spool valve reacting to signals from the ECU controls hydraulic pressure .VTEC-Honda Variable Valve Timing and Lift Electronic Control By desiging a higher valve lift ,wider valve-timing ,and large valve valve diameter ,it is possible to obtain a higher volumetric efficienvy to copy with higer output engine speeds ,The VTEC is used to improve volumetric effiency from low engine speed to high engine speed .With VTEC, the valve timing and lift can be dajusted at low engine rotation to increase troque and prevent air from being forced back through the intake .VTEC OperationFig.2-4 shows the VTEC mechanism while operating at low engine speeds . In the low-speed mode the 3 rocker arms are separated and use cams A&B only . At this time the mid rocker arm is in contact with the high speed cam due to the spring force in the lost motion mechanism .It is separated from the primary and secondary rocker arm and thus is not actuating the valve .Fig.2-5shows the VTEC mechanism while operating in the high speed mode . During high speed engine operation the 3 rocker arms are connected and move together due to the 2 hydraulic pistons which have moved over due to increased hydraulic presure.MIVEC-Mitsubishi Innovative Valve timing Elecctronnic Control systemThe MIVEC dual-intake valve canshaft enables changing betweeen low-speed and high-speed moders(Fig.2-6), resulting in easy operation from low to high rams ,improving the driving experience when staring from a stop light , merging on to the freeway ,or accelerating to overtake another car .In the pursuit of pure driving enjoyment,potentially incompatible goals like fuel economy ,environment-friendiness,and clean driving have all been achieved . Low-speed ModeThe difference in the dual-intake valve lift(low lift and medium lift)and enhanced in-cylinder streaming further stabilize combustion without compromising fuel econmy ,emissions ,and torque .High-speed ModeExtending the injection valve opening time and expanding the valve lift range in ,creases intake air mass and achieves output close to best in class .The Grandis is equipped with the 2.4L MIVEC and the Colt is equipped with the 1.3 and 1.5L MIVEC .Electronic Valve Control SystemAn electronic valve control (EVC) system replace the mechanical camshaft ,controling each valve with actuators for inpendent valve with actuators for independent valve timing .The EVC system control the opening and closing time and lift amout of each intake and exhaust valve with independent actuators on each valve .Changing from a mechanical camshaft driven valve into dependently controled actuator valves provide a huge amount of flexibility in engine control strategy .Vehicles utilizing EVC can realize several benefits including :1)increase engine power and fuel economy.2)Allows centralized and distributed EVC system to perform at their full potential.3)Adapts to engines of varied cylinder counts .With all of improved efficiencies and consumer benefits , auto manufacturers are eager to get their first EVC systems on the road ,The EVC system is targeted to operate in temperatures up to 125C ,while the actuator can be controlled in a centralized syetem with a high-speed multiplex bus (up to 10Mbps)or in a distributed system with a nominal speed bus .EVC systems must be compact in size ,specifically the actuators that must be small enough to fit in the engine space .A vchicle that use a 42V system is ideal for EVC because it requires high voltage to control the valveactuators , and EVC is targeted for V8 and V12 engines.Smart ValvesValco is actively developing technology for reducing fuel consumption and emissions with an engine cylinder-head design that uses its smart valve. Actuation(SV A)in place of conventional operation of engine valves by the cam belt ,camshaft,and hydraulic cam followers .SV A is the first of many innovations that Valco intends to actively develop and market to meet increasing demand for better fuel economy and reduced pollution following its acquisition of Johnson Control`s Engine Electronics Division .In a camless engine ,each engine valve is operated by an actuator mounted above the Valve guides.Each actuator is linked to an engine-mounted valve control units that ensures optimal of all valves and performs the power drive function .By controlling residual gases ,minimizing pumping losses ,and deactivating cylinders and valves ,this technology can reduce consumption and pollutant emissions by 20%. Consumers will benfit from enhanced performance from increases in low-end engine torque .The SV A development program is supposed by several car manufactures and is scheduled for volume production in 2009.Piston and Rod RepairThis repair procedure requires removal of the cylinder head and oil pan .It is much easier to perform this work with the engine removed from the vehicle and mounted on a stand .These procedures requires certain hand tools .A cylinder ridge reamer, a numbered punch set ,piston ring expander ,snapring tools and piston intallation tool ring compressor are all necessary for correct piston and rod repair .Cleaning&InspectionIf the piston is out of specification or otherwise unusable ,it must be replaced,If the cylinder is worm or damaged ,the engine block must be bored and oversize pistons installed.1.Remove the piston rings from the piston .The compression rings (top and middle rings) must be removed using a piston ring expander ,to prevent breakage and /or scratching the piston.2.If there is no obvious damage to the piston and the intent is to reuse the piston ,clean the ring grooves with a ring groove cleaner , being careful not to cut into the piston metal .Heavy carbon deposits can be cleaned from the top of the piston with a scraper or Wire brush .Do not ,however ,use a wire wheel on the ring grooves or lands .Clean the he oil drain holes in the ring grooves .Clean all remaining dirt ,carbon and varmish from the piston with a suitable solvate and abrush ,Do not use a caustic solution on alumnum parts .3.After cleaning ,inspect the piston for scuffing , scoring ,cracks ,pitting or excessive ring groove wear . Replace the piston if obviusly worm .4.If the piston appears servicable , measure the piston diameter usinga micrometer . Measure the Piston diameter in the thrust direction ,90 degrees to the piston pin axis ,1-1/4 inch below the top of the piston .5.Inspect the cylinder bores for taper and out-of-round .The cylinder bores must be measured at 3 levels top to bottom in directions of East-to-West and North-to-South .Measure the cylinder using a bore gauge, or with a telescope gauge and micrometer .The measurement shoud be made in the piston thrust direction at the top ,middle and bottom of the cylinder . Note: Piston diameter and cylinder measurements shoud be made with the parts at room temperature ,70F(21C).6.Subtract the piston diameter measurement from the cylinder measurement .This I the piston-to-cylinder wall claerance .If the clearance is excesive or if the cylinder wall is badly scored or scuffied ,the cylinder may have to be bored and an oversize piston installed .7.Verify that the cylinder has a proper cross-hatch pattern .These tiny marks are the result of the honing operation dating engine manufacture .They retain engine oil to keep the piston tings from scuffing during engine break-in after overhaul .If little or no cross ,hatch is evident ,the cyliunder may require re-honing if the cylinder is in otherwise good condition or reborn if the cylinder is worn or damaged .8.If the piston-to-cylinder wall clearance is within specifications ,check the ring groove clearance .Roll the piston ring around the ring groove in which it is to be installed and check the clearance with a feeker gauge .Compare the measurement with permeation .High points in the ring groove that may cause the ring to bind may be cleaned up carefully with a small flat file .Replace the piston if the ring groove clearance is not within specification.9.Check the connecting rod for damager or obvious wear .Check for signs of over heating(blue appearance)or fractures and check the bearing bore for out-of-round and taper ,A shiny surface on the pin boss side of the piston usually indicates that the connecting rod is bent or the wrist pin hole is not in proper relation to the piston skirt and ring grooves .Abnormal connecting rob beating wear can be caused by either abent connecting rob . An improperly machined journal or a tapered connecting rob bore .Twisted connecting robs will not create an easily identifiable wear pattern ,but badly twisted robs will disturb the action of the entire piston ,rings ,and connectingrob assembly and may be the cause of excessive oil consumption .10.If the piston must be removed from the connectong rob ,mark the side of the connecting rob that corrresponds with the side of the piston that faces the front of the engine ,so the new piston will be installed facing the same direction ,Most pistons have an zrrow or notch on the top of the piston ,indicating that this side should face the front of the engine .If the original piston is to be reinstalled , use paint or a marker to indicate the cylinder number on the piston , so it can reinstalled on the same connecting rob .11.The piston pin is a press fit in the connecting rob .If the piston and /or connecting rob must be replaced ,the pin must be pressed into the connecting rob using a fixture that will not damage or distort the piston and /or connecting rob .The piston must move freely on the pin after installation . Ridge Removal& HoningRidge RemovalThis particular procedure applies to all vehicles .Inspect the upper portions of cylinder (near the head )for a didge formed by ring wear .If there is ridge , it must be removed by forst shifting the piston down in the cylinder and then covering the piston top completely with a clean rag .Use a ridge reamer to remove metal at the lip until the cylinder , If this is not done , the rings will be damaged during removal of the piston .HoningBefore honing the cylindersa ,stuff plently of clean shop towels under the bores and over the crankshaft (if still in the engine (to keep the abrasive materials from entering the crankshaft area.1. The cylinder bore resizing hone equipped with 220 grit or equivalent is the best tool for this job .In addition to deglazing , it will reduce taper and out-of-round as well a removing light scuffing ,scoring or scratches .Usualy a few strokes will clean up a bore and maintain required limits .2.Deglazing of the cylinder walls may be done using a cylinder surfacing hone (or equivalent ) .Use a tool equipped with 280 grit stones if the cylinder is already straight and round .Usually 20-60strokes ,depending on the bore condition will be sufficient to provide a satisfactory surface .Inspect the cylinder walls each 20 strokes ,using a light hotdog on available from an automotive part store .3.Honing should be done by moving the hone up and down fast enough to get a cross-hatch pattern .When hone marks intersect at 50~60 , the cross-hatch angle is most satisfactory for proper seating of the rings /4. A controlled hone motor speed between 200~300rpm is neccssary to obtain the proper cross-hatch angle .The number of up and down strokes perminute can be regulated to get the desired 50-60angle .Faster up and down strokes increase the crosshatch angle .5.After honing , it will be neccssary to clean the block to remove all traces of abrasive .Rod Bearing ReplacementThe engine crankshaft and connecting rod bearing clearances can be determined by the use of plastigage or a similar product . The follwing is the recommended procedure for the use of of plastigage .1.Rotate the crankshaft until the connecting rod boss to be checked is at the bottom of its stroke /2.With the connecting rod and the connectong and the connecting rod bearing cap removed from the crankshaft ,remove the oil film from the surface to be checked .Plastigage is soluble in oil3.Place a piece of plastigage across the entire width of the bearing shell in the bearing cap approximately 1/4 inch (6.3ram) off center and away from the oil hole .In daaition ,suspect areas can be checked by placing plastigage in the suspect area .4.Before assembling the rod bearing cap with the plaetigage in place , the rankshaft must be rotated until the connecting rod being checked starts moving toward the top of the engine .Only then should the cap be assembled and tightened to specifications .Do not rotate the crankshaft while assembling the cap or the plastigage may be smeared ,giving inaccurate results .5.Remove the bearing cap and compare the width of the flattened plastigage with the metric scale provided on the packaged .Locate the band closest to the same width .This hand shows the amount of clearance in thousandths of a millimeter .Differnces in readings between the ends indicate the amount of taper present . Record all readings taken ,Plastigage generally is accompainied by to scales . Oneself is in inches , the other is a metric scale ,plasigage is available in a variety of clearance ranges .。
模具英文翻译
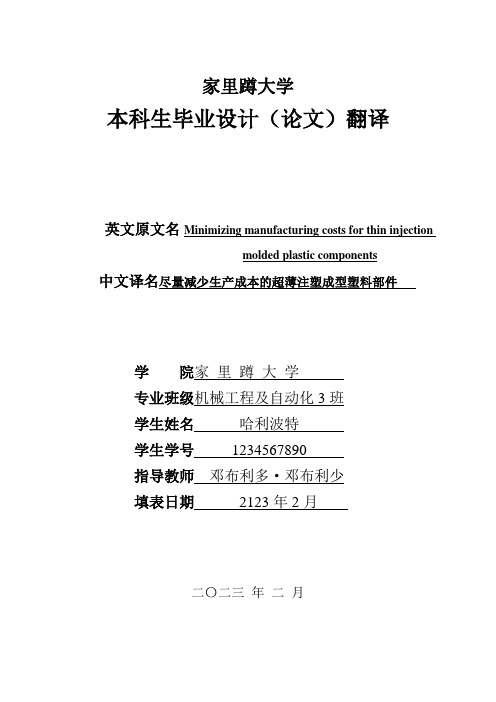
家里蹲大学本科生毕业设计(论文)翻译英文原文名Minimizing manufacturing costs for thin injectionmolded plastic components中文译名尽量减少生产成本的超薄注塑成型塑料部件学院家里蹲大学专业班级机械工程及自动化3班学生姓名哈利波特学生学号1234567890指导教师邓布利多·邓布利少填表日期2123年2月二〇二三年二月英文原文版出处:Received:14 November 2003 BY Springer-Verlag London Limited 2004译文成绩:指导教师(导师组长)签名:译文:尽量减少生产成本的超薄注塑成型塑料部件1前言在多数工业应用中,塑料零件的生产成本,主要集中在材料成型的模具上。
因此,目前使用最多的办法就是降低塑料部件的厚度,以减少材料使用。
假设设计模具及成型过程的最小厚度要求是直接导致制造的最低成本。
如今,电子产品如移动电话和医疗设备正变得越来越复杂,其尺寸正在不断减小。
在最近几年小而薄的塑料部件需求已大为增加除了最低限度的物质使用其他方面也可能成为生产超薄塑料部件的重要因素特别是对于制造薄件来说,在第一阶段的注塑压力尤为重要。
如果采用目前的设计方法,在这些薄件中,塑料部件将无法制造最低成本。
因此,处理超薄塑料零件,需要一种新的方法,以适应现有的模具设计原则和成型工艺。
1.1目前的研究状况如今,电脑辅助模拟软件是模具设计必不可少的组成部分。
这种软件,增加了设计的效率,减少设计成本和时间[ 1 ] 。
主要系统,如模具流和 C -流量,使用有限元分析,模拟充填现象,包括流动模式和填补序列。
因此,成型条件可以预测和验证,以使早期设计的修改是可以实现的。
虽然现有的软件能够分析流量条件下应力和温度分布状况,他们没有产生最低的制造成本的设计参数哦[ 2,3 ] 。
输出数据的软件只能提供参数值范围,以供设计师参考和决策。
本科毕业设计(论文)外文翻译
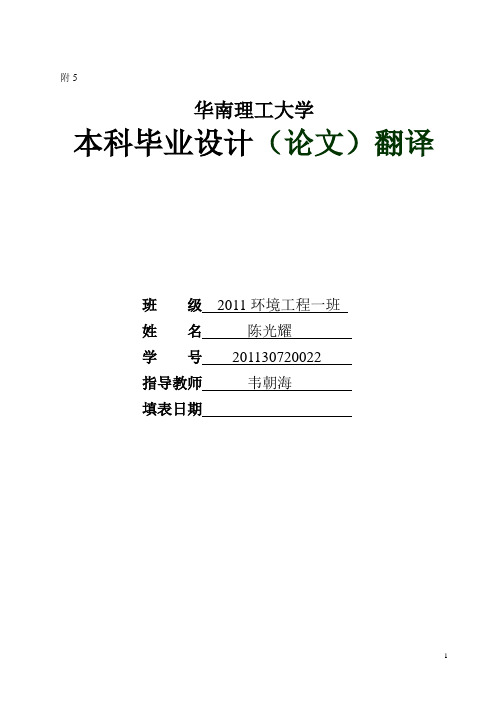
重金属污染存在于很多工业的废水中,如电镀,采矿,和制革。
2.实验
2.1化学药剂
本实验所使用的药剂均为分析纯,如无特别说明均购买自日本片山化工。铅离子储备液通过溶解Pb(NO3)2配制,使用时稀释到需要的浓度。HEPES缓冲液购买自Sigma–Aldrich。5 mol/L的HCl和NaOH用来调整pH。
附5
华南理工大学
本科毕业设计(论文)翻译
班级2011环境工程一班
姓名陈光耀
学号201130720022
指导教师韦朝海
填表日期
中文译名
(1)巯基改性纤维素对葡萄糖溶液中铅的吸附(2)黄原酸化橘子皮应用于吸附水中的铅离子
外文原文名
(1)Adsorption of Pb(II) from glucose solution on thiol-functionalized cellulosic biomass
2.5分析方法
铅离子的浓度用分光光度计在616 nm波长处用铅与偶氮氯膦-III络合物进行分析。葡萄糖含量采用苯酚—硫酸分光光度法测定。所有的实验均进行三次,已经考虑好误差。
3.结果和讨论
3.1FTIR分析和改性脱脂棉对铅(II)的吸附机制
图1是脱脂棉、改性脱脂棉在400-4000 cm-1(A)和2540-2560 cm-1(B)范围内的红外光谱图。可以看出,改性后改性脱脂棉的红外光谱图中在1735.71 cm-1处出现了一个新的吸收峰是酯基C=O的拉伸振动峰,可见改性脱脂棉中已经成功引入巯基官能团。同时,在2550.52 cm-1出现的一个新吸收峰代表的是S-H官能团的弱吸收峰,更深一层的证明了巯基已经嫁接到脱脂棉上。图1(b)是2540-2560 cm-1光谱范围的一个放大图像,可以清楚的观察到S-H官能团的弱吸收峰。进一步证明了酯化改性脱脂棉引入巯基是成功的。而从吸附后的曲线可以看到,2550.52cm-1处S-H的吸收峰消失,证明了硫原子和Pb(II)络合物的形成,同时1735.71cm-1处C=O的吸收峰强度看起来有轻微的减弱可能也是和Pb(II)的络合吸附有关。
英文翻译标准格式
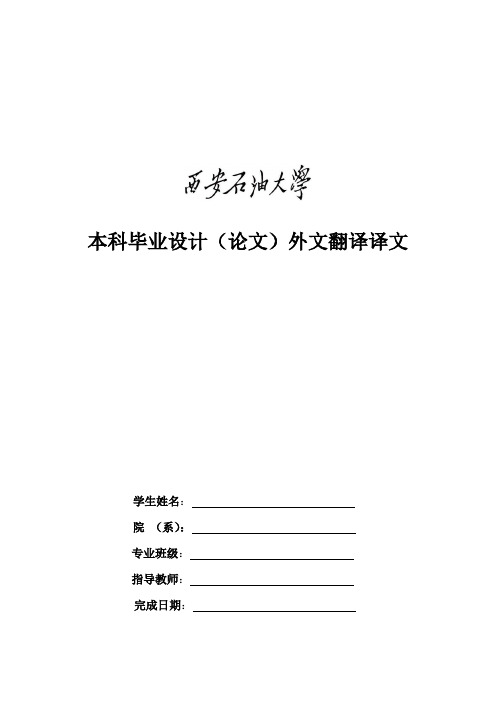
数据的负担。此外,数据库和数据仓库技术允许我们存储越来越多的数据检索和样品容 易。约翰纳斯贝特是完全正确的: “我们被淹没在信息中,但缺乏知识” 。 它把一个杰出的研究员研究几年的开普勒定律(实际上是半辈子)用来评估数据。 第谷布拉赫已收集的数据,从现代的观点很少,其实开普勒仔细只是分析的只有那些关 于火星的轨道而已。 鉴于此, 我们怎么能希望今天我们每天都要面对大量数据? “手动” 分析(如开普勒)早已不再是可行的。简单的艾滋病,如图表数据的可视化,即使是非 常有用的,也会很快地达到自己的极限。因此,如果我们拒绝屈服于数据的洪流,这迫 使我们必须发展和运用计算机辅助技术,数据分析,可以简化甚至某种程度的自动化。 这些都是方法,一直是在智能数据分析领域的研究开发,数据库中的知识发现和数据挖 掘。尽管这些方法都将像开普勒的人类,特别是因为无意识的应用程序可以产生伪影和 误导性的结果, 它是不完全可信的假设。 开普勒, 如果他是通过这些方法和工具的支持, 可以达到他的目标早一点。 1.1.3 智能数据分析 任何类型的数据都可以进行分析与统计(见附录 A,它提供了一个简要的回顾) 。统 计有着悠久的历史,一般起源于收集和分析国家的人口数据。统计可分为描述性统计和 推论统计。 描述性统计没有关于数据的特定假设进行汇总数据, 经常采用的是特征值 (经 验) :如平均或图像的直方图。统计推断提供了更严格的方法。描述性统计是基于对随 机产生的过程数据的某些假设,推断的结论是唯一有效的。 通常,统计数据分析过程的第一步是设计实验,定义了数据收集应以能够进行基于 所获得的数据的可靠性分析。在实验研究中的一个可以控制和操纵数据的生成过程。例 如,如果我们在某些饮食对一个人的健康状况的影响很感兴趣,我们可能会问不同的人 和不同的饮食。 因此,我们在数据生成过程进行一定的控制。在本实验研究中,我们可以决定哪些 人应该被分配到一个特定的饮食。 在一项观察性研究中是一个无法控制的数据生成过程。 对于同一膳食研究上面,我们可以在街上,问普通人吃的什么。然后,我们没有控制哪 种饮食。我们得到的数据,是每个饮食有多少人的数据。无论是实验或观测,通常有独 立性假设,代表着我们收集的数据。主要原因是统计推断往往是应用假设检验,在所收 集的数据的基础上,我们能够确认或拒绝对所考虑的域的一些假说。在这种情况下具有 代表性的数据和一定的无关性是为了确保测试的决定是正确的。 相反,假设检验,探索性数据分析是研究从收集到的数据生成的假设。在探索性数 据分析没有或至少相当弱的模型假设的数据生成过程。 这本书中的大部分都属于这一类 的方法,因为它们大多是通用的设计方法,达到某一个目标,而不是基于严格的模型在 统计推断。典型的情况下,我们假设在这本书中,我们已经得到的数据。他们可能没有 以最好的方式收集,或在路上我们会收集他们我们能提前实验设计。因此,它往往是难
大学本科毕业设计--英文原文+中文翻译
Library of C the CNC industrialdeveloped tens of thousands and educational field, he hasNUMERICAL CONTROLNumerical Control technology as it is known today, emerged in the mid 20th century. It can be traced to the year of 1952, the U.S. Air Force, and the names of John Parsons and the Massachusetts Institute of Technology in Cam-bridge, MA, USA. It was not applied in production manu-facturing until the early 1960's. The real boom came in the form of CNC, around the year of 1972, and a decade later with the introduction of affordable micro computers. The history and development of this fascinating technology has been well documented in many publications.In the manufacturing field, and particularly in the area of metal working, Numerical Control technology has caused something of a revolution. Even in the days before comput-ers became standard fixtures in every company and in many homes, the2machine tools equipped with Numerical Control system found their special place in the machine shops. The recent evolution of micro electronics and the never ceasing computer development, including its impact on Numerical Control, has brought significant changes to the manufacturing sector in general and metalworking in-dustry in particular.DEFINITION OF NUMERICAL CONTROLIn various publications and articles, many descriptions have been used during the years, to define what Numerical Control is. It would be pointless to try to find yet another definition, just for the purpose of this handbook. Many of these definitions share the same idea, same basic concept, just use different wording.The majority of all the known definitions can be summed up into a relatively simple statement:Numerical Control can be defined as an operation of machine tools by the means of specifically coded instructions to the machine control systemThe instructions are combinations of the letters of alpha-bet, digits and selected symbols, for example, a decimal point, the percent sign or the parenthesis symbols. All in-structions are written in a logical order and a predetermined form. The collectionNUMERICAL CONTROLof all instructions necessary to ma-chine a part is called an NC Program, CNC Program, or a Part Program. Such a program can be stored for a future use and used repeatedly to achieve identical machining re-sults at any time.♦ NC and CNC TechnologyIn strict adherence to the terminology, there is a differ-ence in the meaning of the abbreviations NC and CNC. The NC stands for the older and original Numerical Control technology, whereby the abbreviation CNC stands for the newer Computerized Numerical Control technology, a modem spin-off of its older relative. However, in practice, CNC is the preferred abbreviation. To clarify the proper us-age of each term, look at the major differences between the NC and the CNC systems.Both systems perform the same tasks, namely manipula-tion of data for the purpose of machining a part. In both cases, the internal design of the control system contains the logical instructions that process the data. At this point the similarity ends. The NC system (as opposed to the CNC system) uses a fixed logical functions, those that are built-in and perma-nently wired within the control unit. These functions can-not be changed by the programmer or the machine opera-tor. Because of the fixed4wiring of the control logic, the NC control system is synonymous with the term 'hardwired'. The system can interpret a part program, but it does not al-low any changes to the program, using the control features. All required changes must be made away from the control, typically in an office environment. Also, the NC system re-quires the compulsory use of punched tapes for input of the program information.The modem CNC system, but not the old NC system, uses an internal micro processor (i.e., a computer). This computer contains memory registers storing a variety of routines that are capable of manipulating logical functions. That means the part programmer or the machine operator can change the program on the control itself (at the ma-chine), with instantaneous results. This flexibility is the greatest advantage of the CNC systems and probably the key element that contributed to such a wide use of the tech-nology in modern manufacturing. The CNC programs and the logical functions are stored on special computer chips, as software instructions, rather than used by the hardware connections, such as wires, that control the logical func-tions. In contrast to the NC system, the CNC system is syn-onymous with the term 'softwired'.NUMERICAL CONTROLWhen describing a particular subject that relates to the numerical control technology, it is customary to use either the term NC or CNC. Keep in mind that NC can also mean CNC in everyday talk, but CNC can never refer to the older technology, described in this handbook under the abbrevia-tion ofNC. The letter 'C 'stands for Computerized, and it is not applicable to the hardwired system. All control systems manufactured today are of the CNC design. Abbreviations such as C&C or C'n 'C are not correct and reflect poorly on anybody that uses them.CONVENTIONAL AMD CNC MACHININGWhat makes the CNC machining superior to the conven-tional methods? Is it superior at all? Where are the main benefits? If the CNC and the conventional machining pro-cesses are compared, a common general approach to ma-chining a part will emerge: Obtain and study the drawingSelect the most suitable machining methodDecide on the setup method (work holding)Select the cutting toolsEstablish speeds and feedsMachine the part6This basic approach is the same for both types of machin-ing. The major difference is in the way how various data are input. A feedrate of 10 inches per minute (10 in/min) is the same in manual or CNC applications, but the method of applying it is not. The same can be said about a coolant - it can be activated by turning a knob, pushing a switch or programming a special code. All these actions will result in a coolant rushing out of a nozzle. In both kinds of machin-ing, a certain amount of knowledge on the part of the user is required. After all, metal working, particularly metal cut-ting, is mainly a skill, but it is also, to a great degree, an art and a profession of large number of people. So is theappli-cation of Computerized Numerical Control. Like any skill or art or profession, mastering it to the last detail is neces-sary to be successful. It takes more than technical knowl-edge to be a CNC machinist or a CNC programmer. Work experience and intuition, and what is sometimes called a 'gut-feel', is a much needed supplement to any skill.In a conventional machining, the machine operator sets up the machine and moves each cutting tool, using one or both hands, to produce the required part. The design of a manual machine tool offers many features that help the process of machining a part -NUMERICAL CONTROLlevers, handles, gears and di-als, to name just a few. The same body motions are re-peated by the operator for every part in the batch. However, the word 'same 'in this context really means'similar 'rather than 'identical'. Humans are not capable to repeat every process exactly the same at all times - that is the job ofma-chines. People cannot work at the same performance level all the time, without a rest. All of us have some good andsome bad moments. The results of these moments, when*applied to machining a part, are difficult to predict. There will be some differences and inconsistencies within each batch of parts. The parts will not always be exactly the same. Maintaining dimensional tolerances and surface fin-ish quality are the most typical problems in conventional machining. Individual machinists may have their own time 'proven' methods, different from those of their fellow col-leagues. Combination of these and other factors create a great amount of mconsistency.The machining under numerical control does away with the majority of inconsistencies. It does not require the same physical involvement as manual machining. Numerically controlled machining does not need any levers or dials or handles, at least8not in the same sense as conventional ma-chining does. Once the part program has been proven, it can be used any number of times over, always returning consistent results. That does not mean there are no limiting factors. The cutting tools do wear out, the material blank in one batch is not identical to the material blank in another batch, the setups may vary, etc. These factors should be considered and compensated for, whenever necessary.The emergence of the numerical control technology does not mean an instant, or even a long term, demise of all man-ual machines. There are times when a traditional machin-ing method is preferable to a computerized method. For ex-ample, a simple one time job may be done more efficiently on a manual machine than a CNC machine. Certain types of machining jobs will benefit from manual or semiauto-matic machining, rather than numerically controlled ma-chining. The CNC machine tools are not meant to replace every manual machine, only to supplement them.In many instances, the decision whether certain machin-ing will be done on a CNC machine or not is based on the number of required parts and nothing else. Although the volume of partsNUMERICAL CONTROLmachined as a batch is always an important criteria, it should never be the only factor. Consideration should also be given to the part complexity, its tolerances, the required quality of surface finish, etc. Often, a single complex part will benefit from CNC machining, while fifty relatively simple parts will not.Keep in mind that numerical control has never machined a single part by itself. Numerical control is only a process or a method that enables a machine tool to be used in a pro-ductive, accurate and consistent way.NUMERICAL CONTROL ADVANTAGESWhat are the main advantages of numerical control?It is important to know which areas of machining will benefit from it and which are better done the conventional way. It is absurd to think that a two horse power CNC mill will win over jobs that are currently done on a twenty times more powerful manual mill. Equally unreasonable are ex-pectations of great improvements in cutting speeds and feedrates over a conventional machine. If the machining and tooling conditions are the same, the cutting time will be very close in both cases.Some of the major areas where the CNC user can and should expect improvement:10Setup time reductionLead time reductionAccuracy and repeatabilityContouring of complex shapesSimplified tooling and work holdingConsistent cutting timeGeneral productivity increaseEach area offers only a potential improvement. Individ-ual users will experience different levels of actual improve-ment, depending on the product manufactured on-site, the CNC machine used, the setup methods, complexity of fixturing, quality of cutting tools, management philosophy and engineering design, experience level of the workforce, individual attitudes, etc.Setup Time ReductionIn many cases, the setup time for a CNC machine can be reduced, sometimes quite dramatically. It is important to realize that setup is a manual operation, greatly dependent on the performance of CNC operator, the type of fixturing and general practices of the machine shop. Setup time is unproductive, but necessary - it is a part of the overhead costs of doing business. To keep the setupNUMERICAL CONTROLtime to a mini-mum should be one of the primary considerations of any machine shop supervisor, programmer and operator. Because of the design of CNC machines, the setup time should not be a major problem. Modular fixturing, standard tooling, fixed locators, automatic tool changing, pallets and other advanced features, make the setup time more efficient than a comparable setup of a conventional machine. With a good knowledge of modern manufacturing, productivity can be increased significantly.The number of parts machined under one setup is also important, in order to assess the cost of a setup time. If a great number of parts is machined in one setup, the setup cost per part can be very insignificant. A very similar re-duction can be achieved by grouping several different oper-ations into a single setup. Even if the setup time is longer, it may be justified when compared to the time required to setup several conventional machines.Lead Time ReductionOnce a part program is written and proven, it is ready to be Bsed again in the future, even at a short notice. Although the lead time for the first run is usually longer, it is virtually nil for any subsequent run. Even if an engineering change of the part design12requires the program to be modi tied, it can be done usually quickly, reducing the lead time.Long lead time, required to design and manufacture sev-eral special fixtures for conventional machines, can often be reduced by preparing a part program and the use of sim-plified fixturing. Accuracy and RepeatabilityThe high degree of accuracy and repeatability of modern CNC machines has been the single major benefit to many users. Whether the part program is stored on a disk or in the computer memory, or even on a tape (the original method), it always remains the same. Any program can be changed at will, but once proven, no changes are usually required any more. A given program can be reused as many times as needed, without losing a single bit of data it contains. True, program has to allow for such changeable factors as tool wear and operating temperatures, it has to be stored safely, but generally very little interference from the CNC pro-grammer or operator will be required. The high accuracy of CNC machines and their repeatability allows high quality parts to be produced consistently time after time. Contouring of Complex ShapesNUMERICAL CONTROLCNC lathes and machining centers are capable of con-touring a variety of shapes. Many CNC users acquired their machines only to be able to handle complex parts. A good examples are CNC applications in the aircraft and automo-tive industries. The use of some form of computerized pro-gramming is virtually mandatory for any three dimensional tool path generation.Complex shapes, such as molds, can be manufactured without the additional expense of making a model for trac-ing. Mirrored parts can be achieved literally at the switch of a button. Storage of programs is a lot simpler than storage of patterns, templates, wooden models, and other pattern making tools.Simplified Tooling and Work HoldingNonstandard and 'homemade' tooling that clutters the benches and drawers around a conventional machine can be eliminated by using standard tooling, specially designed for numerical control applications. Multi-step tools such as pilot drills, step drills, combination tools, counter borers and others are replaced with several individual standard tools. These tools are often cheaper and easier to replace than special and nonstandard tools.Cost-cutting measures have forced many tool suppliers to keep a low or even a nonexistent inventory, increasing the delivery lime14to the customer. Standard, off-the-shelf tooling can usually beob-tained faster then nonstandard tooling.Fixturing and work holding for CNC machines have only one major purpose - to hold the part rigidly and in the same position for all parts within a batch. Fixtures designed for CNC work do not normally require jigs, pilot holes and other hole locating aids.♦ Cutting Time and Productivity IncreaseThe cutting time on the CNC machine is commonly known as the cycle time - and is always consistent. Unlike a conventional machining, where the operator's skill, experi-ence and personal fatigue are subject to changes, the CNC machining is under the control of a computer. The small amount of manual work is restricted to the setup andload-ing and unloading the part. For large batch runs, the high cost of the unproductive time is spread among many parts, making it less significant. The main benefit of a consistent cutting time is for repetitive jobs, where the production scheduling and work allocation to individual machine tools can be done very accurately.The main reason companies often purchase CNCma-chines is strictly economic - it is a serious investment. Also, having a competitive edge is always on the mind of every plant manager. The numerical control teclmology offers excellent means to achieve a significant improvement in the manufacturing productivity and increasing the overall quality of the manufactured parts. Like any means, it has to be used wisely and knowledgeably. When more and more companies use the CNCtechnology, just having a CNC machine does not offer the extra edge anymore. Thecom-panies that get forward are those who know how to use the technology efficiently and practice it to be competitive in the global economy.To reach the goal of a major increase in productivity, it is essential that users understand the fundamental principles on which CNC technology is based. These principles take many forms, for example, understanding the electronic cir-cuitry, complex ladder diagrams, computer logic, metrol-ogy, machine design, machining principles and practices and many others. Each one has to be studied and mastered by the person in charge. In this handbook, the emphasis is on the topics that relate directly to the CNC programming and understanding the most common CNC machine tools, the Machining Centers and the lathes (sometimes also called the Turning Centers). The part quality consideration should be very important to every programmer and ma-chine tool operator and this goal is also reflected in the handbook approach as well as in the numerous examples.TYPES OF CNC MACHINE TOOLSDifferent kinds of CNCmachines cover an extremelylarge variety. Their numbersare rapidly increasing, as thetechnology developmentadvances. It is impossible toiden-tify all the applications,they would make a long list.Here is a brief list of some ofthe groups CNC machines canbe part of: *Mills and Machining centersLathes and Turning CentersDrilling machines CNC machining centers andlathes dominate the number ofinstallations in industry. Thesetwo groups share the marketjust about equally. Someindustries may have a higherneed for one group ofmachines, depending on their □ Boring mills and Profilers □ EDM machines □ Punch presses and Shears □ Flame cutting machines □ Routers □ Water jet and Laser profilers □ Cylindrical grinders □ Welding machines □ Benders, Winding and Spinning machines, etc.needs. One must remember that there are many different kinds of ladies and equally many different kinds ofma-chining centers. However, the programming process for a vertical machine is similar to the one for a horizontalma-chine or a simple CNC mill. Even between differentma-chine groups, there is a great amount of general applica-tions and the programming process is generally the same. For example, a contour milled with an end mill has a lot in common with a contour cut with a wire.♦ Mills and Machining Centers Standard number of axes on a milling machine is three - the X, Y and Z axes. The part set on a milling system is al-ways stationary, mounted on a moving machine table. The cutting tool rotates, it can move up and down (or in and out), but it does not physically follow the tool path.CNC mills - sometimes called CNC milling machines - are usually small, simple machines, without a tool changer or other automatic features. Their power rating is often quite low. In industry, they are used for toolroom work, maintenance purposes, or small part production. They are usuallydesigned for contouring, unlike CNC drills.CNC machining centers are far more popular and effi-cient than drills and mills, mainly for their flexibility. The main benefit the user gets out of a CNC machining center is the ability to group several diverse operations into a single setup. For example, drilling, boring, counter boring, tap-ping, spot facing and contour milling can be incorporated into a single CNC program. In addition, the flexibility is enhanced by automatic tool changing, using pallets to minimize idle time, indexing to a different side of the part, using a rotary movement of additional axes, and a number of other features. CNC machining centers can be equipped with special software that controls the speeds and feeds, the life of the cutting tool, automatic in-process gauging and offset adjustment and other production enhancing and time saving devices.There are two basic designs of a typical CNC machining center. They are the vertical and the horizontal machining centers. The major difference between the two types is the nature of work that can be done on them efficiently. For a vertical CNC machining center, the most suitable type of work are flat parts, either mounted to the fixture on the ta-ble, or held in a vise or a chuck. The work that requires ma-chining on two or more faces m a single setup is more de-sirable to be done on a CNC horizontal machining center. An good example is a pump housing and other cubic-like shapes. Some multi-face machining of small parts can also be done on a CNC vertical machining center equipped with a rotary table.The programming process is the same for both designs, but an additional axis (usually a B axis) is added to the hori-zontal design. This axis is either a simple positioning axis (indexing axis) for the table, or a fully rotary axis for simul-taneous contouring. This handbook concentrates on the CNC vertical ma-chining centers applications, with a special section dealing with the horizontal setup and machining. The program-ming methods are also applicable to the small CNC mills or drilling and/or tapping machines, but the programmer has to consider their restrictions.♦ Lathes and Turning CentersA CNC lathe is usually a machine tool with two axes, the vertical X axis and the horizontal Z axis. The main feature of a lathe that distinguishes it from a mill is that the part is rotating about the machine center line. In addition, the cut-ting tool is normally stationary, mounted in a sliding turret. The cutting tool follows the contour of the programmed tool path. For the CNC lathes with a milling attachment, so called live tooling, the milling tool has its own motor and rotates while the spindle is stationary.The modem lathe design can be horizontal or vertical. Horizontal type is far more common than the vertical type, but both designs have their purpose in manufacturing. Sev-eral different designs exist for either group. For example, a typical CNC lathe of the horizontal group can be designed with a flat bed or a slant bed, as a bar type, chucker type or a universal type. Added to these combinations are many ac-cessories that make a CNC lathe an extremely flexible ma-chine tool. Typically, accessories such as a tailstock, steady rests or follow-up rests, part catchers,pullout-fingers and even a third axis milling attachment are popular compo-nents of the CNC lathe. ?CNC lathe can be veiy versatile - so versatile in fact, that it is often called a CNC TurningCenter. All text and program examples in this handbook use the more traditional term CNC lathe, yet still recogniz-ing all its modern functions.中文翻译:数控正如我们现在所知,数控技术出现于20世纪中叶。
毕业设计外文翻译
AT89C51外文翻译DescriptionThe AT89C51 is a low-power, high-performance CMOS 8-bit microcomputer with 4K bytes of Flash Programmable and Erasable Read Only Memory (PEROM). The device is manufactured using Atmel’s high density nonvolatile memory technology and is compatible with the industry standard MCS-51™ instruction-set and pinout. The on-chip Flash allows the program memory to be reprogrammed in-system or by a conventional nonvolatile memory programmer. By combining a versatile 8-bit CPU with Flash on a monolithic chip, the Atmel A T89C51 is a powerful microcomputer which provides a highly flexible and cost effective solution to many embedded control applications.Features• Compatible with MCS-51™ Products• 4K Bytes of In-System Reprogrammable Flash Memory– Endurance: 1,000 Write/Erase Cycles• Fully Static Operation: 0 Hz to 24 MHz• Three-Level Program Memory Lock• 128 x 8-Bit Internal RAM• 32 Programmable I/O Lines• Two 16-Bit Timer/Counters• Six Interrupt Sources• Programmable Serial Channel• Low Power Idle and Power Down ModesThe AT89C51 provides the following standard features: 4K bytes of Flash,128 bytes of RAM, 32 I/O lines, two 16-bit timer/counters, a five vector two-level interrupt architecture, a full duplex serial port, on-chip oscillator and clock circuitry. In addition, the AT89C51 is designed with static logic for operation down to zero frequency and supports two software selectable power saving modes. The Idle Mode stops the CPU while allowing the RAM, timer/counters, serial port and interrupt system to continue functioning. The Power-down Mode saves the RAM contents but freezes the oscillator disabling all other chip functions until the next hardware reset.VCCSupply voltage.GNDGround.Port 0Port 0 is an 8-bit open-drain bi-directional I/O port. As an output port, each pin can sink eight TTL inputs. When 1s are written to port 0 pins, the pins can be used as high-impedance inputs.Port 0 may also be configured to be the multiplexed low-order address/data bus during accesses to external program and data memory. In this mode P0 has internal pullups. Port 0 also receives the code bytes during Flash programming, and outputs the code bytes during program verification. External pullups are required during program verification.Port 1Port 1 is an 8-bit bi-directional I/O port with internal pullups.The Port 1 output buffers can sink/source four TTL inputs.When 1s are written to Port 1 pins they are pulled high by the internal pullups and can be used as inputs. As inputs,Port 1 p ins that are externally being pulled low will source current (IIL) because of the internal pullups.Port 1 also receives the low-order address bytes during Flash programming and verification.Port 2Port 2 is an 8-bit bi-directional I/O port with internal pullups.The Port 2 output buffers can sink/source four TTL inputs.When 1s are written to Port 2 pins they are pulled high by the internal pullups and can be used as inputs. As inputs,Port 2 pins that are externally being pulled low will source current (IIL) because of the internal pullups. Port 2 emits the high-order address byte during fetches from external program memory and during accesses to external data memory that use 16-bit addresses (MOVX @DPTR). In this application, it uses strong internal pullups when emitting 1s. During accesses to external data memory that use 8-bit addresses (MOVX @ RI), Port 2 emits the contents of the P2 Special Function Register. Port 2 also receives the high-order address bits and some control signals during Flash programming and verification.Port 3Port 3 is an 8-bit bi-directional I/O port with internal pullups. The Port 3 output buffers can sink/source four TTL inputs.When 1s are written to Port 3 pins they arepulled high by the internal pullups and can be used as inputs. As inputs,Port 3 pins that are externally being pulled low will source current (IIL) because of the pullups. Port 3 also serves the functions of various special features of the AT89C51 as listed below:Port 3 also receives some control signals for Flash programming and verification. RSTReset input. A high on this pin for two machine cycles while the oscillator is running resets the device.ALE/PROGAddress Latch Enable output pulse for latching the low byte of the address during accesses to external memory. This pin is also the program pulse input (PROG) during Flash programming. In normal operation ALE is emitted at a constant rate of 1/6 the oscillator frequency, and may be used for external timing or clocking purposes. Note, however, that one ALE pulse is skipped during each access to external Data Memory.If desired, ALE operation can be disabled by setting bit 0 of SFR location 8EH. With the bit set, ALE is active only during a MOVX or MOVC instruction. Otherwise, the pin is weakly pulled high. Setting the ALE-disable bit has no effect if the microcontroller is in external execution mode.PSENProgram Store Enable is the read strobe to external program memory. When the AT89C51 is executing code from external program memory, PSEN is activated twice each machine cycle, except that two PSEN activations are skipped during each access to external data memory.EA/VPPExternal Access Enable. EA must be strapped to GND in order to enable the device to fetch code from external program memory locations starting at 0000H up toFFFFH.Note, however, that if lock bit 1 is programmed, EA will be internally latched on reset. EA should be strapped to VCC for internal program executions.This pin also receives the 12-volt programming enable voltage (VPP) during Flash programming, for parts that require 12-volt VPP.XTAL1Input to the inverting oscillator amplifier and input to the internal clock operating circuit.XTAL2Output from the inverting oscillator amplifier.Oscillator CharacteristicsXTAL1 and XTAL2 are the input and output, respectively,of an inverting amplifier which can be configured for use as an on-chip oscillator, as shown in Figure 1. Either a quartz crystal or ceramic resonator may be used. To drive the device from an external clock source, XTAL2 should be left unconnected while XTAL1 is driven as shown in Figure 2.There are no requirements on the duty cycle of the external clock signal, since the input to the internal clocking circuitry is through a divide-by-two flip-flop, but minimum and maximum voltage high and low time specifications must be observed.Idle ModeIn idle mode, the CPU puts itself to sleep while all the on-chip peripherals remain active. The mode is invoked by software. The content of the on-chip RAM and all the special functions registers remain unchanged during this mode. The idle mode can be terminated by any enabled interrupt or by a hardware reset. It should be noted that when idle is terminated by a hard ware reset, the device normally resumes program execution, from where it left off, up to two machine cycles before the internal reset algorithm takes control. On-chip hardware inhibits access to internal RAM in this event, but access to the port pins is not inhibited. To eliminate the possibility of an unexpected write to a port pin when Idle is terminated by reset, the instruction following the one that invokes Idle should not be one that writes to a port pin or to external memory.Figure 1. Oscillator ConnectionsNote: C1, C2 = 30 pF ± 10 pF for Crystals= 40 pF ± 10 pF for Ceramic ResonatorsFigure 2. External Clock Drive ConfigurationPower-down ModeIn the power-down mode, the oscillator is stopped, and the instruction that invokes power-down is the last instruction executed. The on-chip RAM and Special Function Registers retain their values until the power-down mode is terminated. The only exit from power-down is a hardware reset. Reset redefines the SFRs but does not change the on-chip RAM. The reset should not be activated before VCC is restored to its normal operating level and must be held active long enough to allow the oscillator to restart and stabilize.Program Memory Lock BitsOn the chip are three lock bits which can be left unprogrammed (U) or can be programmed (P) to obtain the additional features listed in the table below.When lock bit 1 is programmed, the logic level at the EA pin is sampled and latched during reset.If the device is powered up without a reset, the latch initializes to a random value, and holds that value until reset is activated. It is necessary that the latched value of EA be in agreement with the current logic level at that pin in order for the device to function properly.Programming the FlashThe AT89C51 is normally shipped with the on-chip Flash memory array in the erased state (that is, contents = FFH)and ready to be programmed. The programming interface accepts either a high-voltage (12-volt) or a low-voltage (VCC) program enable signal. The low-voltage programming mode provides a convenient way to program the AT89C51 inside t he user’s system, while the high-voltage programming mode is compatible with conventional thirdparty Flash or EPROM programmers.The AT89C51 is shipped with either the high-voltage or low-voltage programming mode enabled. The respective top-side marking and device signature codes are listed in the following table.The AT89C51 code memory array is programmed byte-by-byte in either programming mode. To program any non-blank byte in the on-chip Flash Memory, the entire memory must be erased using the Chip Erase Mode. Programming Algorithm: Before programming the A T89C51, the address, data and control signals should be set up according to the Flash programming mode table and Figures 3 and 4. To program the AT89C51, take the following steps.1. Input the desired memory location on the address lines.2. Input the appropriate data byte on the data lines.3. Activate the correct combination of control signals.4. Raise EA/VPP to 12V for the high-voltage programming mode.5. Pulse ALE/PROG once to program a byte in the Flash array or the lock bits. The byte-write cycle is self-timedand typically takes no more than 1.5 ms. Repeat steps 1 through 5, changing the address and data for the entire array or until the end of the object file is reached.Data Polling: The AT89C51 features Data Polling to indicate the end of a write cycle. During a write cycle, anattempted read of the last byte written will result in the complement of the written datum on PO.7. Once the write cycle has been completed, true data are valid on all outputs, and the next cycle may begin. Data Polling may begin any time after a write cycle has been initiated.Ready/Busy: The progress of byte programming can also be monitored by the RDY/BSY output signal. P3.4 is pulled low after ALE goes high during programming to indicate BUSY. P3.4 is pulled high again when programming is done to indicate READY.Program V erify: If lock bits LB1 and LB2 have not been programmed, the programmed code data can be read back via the address and data lines for verificatio n. The lock bits cannot be verified directly. V erification of the lock bits is achieved by observing that their features are enabled.Chip Erase: The entire Flash array is erased electrically by using the proper combination of control signals and by holding ALE/PROG low for 10 ms. The code array is written with all ―1‖s. The chip erase operation must be executed before the code memory can be re-programmed.Reading the Signature Bytes: The signature bytes are read by the same procedure as a normal verification of locations 030H, 031H, and 032H, except that P3.6 and P3.7 must be pulled to a logic low. The values returned are as follows.(030H) = 1EH indicates manufactured by Atmel(031H) = 51H indicates 89C51(032H) = FFH indicates 12V programming(032H) = 05H indicates 5V programmingProgramming InterfaceEvery code byte in the Flash array can be written and the entire array can be erased by using the appropriate combination of control signals. The write operation cycle is selftimed and once initiated, will automatically time itself to completion.All major programming vendors offer worldwide support for the Atmelmicrocontroller series. Please contact your local programming vendor for the appropriate software revision.Flash Programming and V erification Waveforms - High-voltage Mode (VPP = 12V)Flash Programming and V erification Waveforms - Low-voltage Mode (VPP = 5V)Flash Programming and Verification Characteristics TA = 0°C to 70°C, VCC = 5.0 ±10%Absolute Maximum Ratings**NOTICE: Str esses beyond those listed under ―Absolute Maximum Ratings‖ may cause permanent damage to the device. This is a stress rating only and functional operation of the device at these or any other conditions beyond those indicated in the operational sections of this specification is not implied. Exposure to absolute maximum rating conditions for extended periods may affect device reliability.DC CharacteristicsTA = -40°C to 85°C, VCC = 5.0V ±20% (unless otherwise noted)Notes: 1. Under steady state (non-transient) conditions, IOL must be externally limited as follows:Maximum IOL per port pin: 10 mAMaximum IOL per 8-bit port: Port 0: 26 mAPorts 1, 2, 3: 15 mAMaximum total IOL for all output pins: 71 mAIf IOL exceeds the test condition, VOL may exceed the related specification. Pins arenot guaranteed to sink current greater than the listed test conditions.2. Minimum VCC for Power-down is 2V.AC CharacteristicsUnder operating conditions, load capacitance for Port 0, ALE/PROG, and PSEN = 100 pF; load capacitance for all other outputs = 80 pF.External Program and Data Memory CharacteristicsExternal Program Memory Read CycleExternal Data Memory Read CycleExternal Data Memory Write CycleExternal Clock Drive WaveformsExternal Clock DriveSerial Port Timing: Shift Register Mode Test Conditions (VCC = 5.0 V ±20%; Load Capacitance = 80 pF)Shift Register Mode Timing WaveformsAC Testing Input/Output Waveforms(1)Note: 1. AC Inputs during testing are driven at VCC - 0.5V for a logic 1 and 0.45V for a logic 0. Timing measurements are made at VIH min. for a logic 1 and VIL max. for a logic 0.Float Waveforms(1)Note: 1. For timing purposes, a port pin is no longer floating when a 100mV change from load voltage occurs. A port pin begins to float when 100mV change from the loaded VOH/VOL level occurs.AT89C51中文原文AT89C51是美国ATMEL公司生产的低电压,高性能CMOS8位单片机,片内含4k bytes的可反复擦写的只读程序存储器(PEROM)和128 bytes的随机存取数据存储器(RAM),器件采用A TMEL公司的高密度、非易失性存储技术生产,兼容标准MCS-51指令系统,片内置通用8位中央处理器(CPU)和Flash存储单元,功能强大AT89C51单片机可为您提供许多高性价比的应用场合,可灵活应用于各种控制领域。
ERDAS帮助文档翻译
本科毕业设计(论文)中英文对照翻译院(系部)资源环境学院专业名称地理信息系统年级班级2001-03学生姓名毛巍指导老师张鸿升二00五年六月十日英文翻译(原文)Introduction to Model MakerA model is a set of instructions that is processed by the IMAGINE Spatial Modeler component for performing GIS and image processing operations.The IMAGINE Model Maker is an editor for creating models using a palette of tools. These tools are used to place graphics representing input data, functions, criteria, and output data on a page to create a graphical model by drawing its flow chart.The Spatial Modeler Language (SML) is a modeling language that is used by Model Maker to execute the operations specified in the graphical models that you create. You can also use the Spatial Modeler Language directly to write your own script models that may be run from the Model Librarian.If a calibrated file is input to a model, output files created by the model will also be calibrated. If a subset of the area of the input file is output, the calibration is adjusted accordingly. If there are any other files input to the model, they must be the same size and have exactly the same calibration information as the first calibrated input file. You cannot input calibrated and georeferenced files together.This documentation explains: General Capabilities, Starting Model Maker, Defining Objects, Using Function Definitions, Specifying Criteria, Output Parameters, Creating a Model, Running a Model, Using the Spatial Modeler LanguageGeneral CapabilitiesModel Maker allows you to write both simple and complex models that incorporate GIS and image processing functions. These include:※mathematical operations on raster layers (adding, subtracting, multiplying, ratioing, or other image algebra functions),※convolution filtering,※neighborhood analyses (analyzing a pixel based on the values of neighboring pixels),※subsetting and mosaicking,※principal components analysis, and※contiguity analysis.The results of a model (an output file) can be written to a file, automatically opened in a Viewer window, or both.Internal checks within Model Maker help you create valid models from the beginning.Starting Model MakerYou can access Model Maker by selecting the Model Maker option from the Spatial Modeler dialog. To access this dialog, click this icon on the ERDAS IMAGINE icon panel:Model Maker PartsThe parts of the Model Maker window and palette of tools are explained in the following illustration:Mostly, you will be working with:※ objects — (see below) the data upon which you operate or create※function definitions — the instructions that you compose on how the data are to be manipulated.These are explained below.ObjectsAn object is an input to or an output from a function. The four basic object types used in Model Maker are described below.ScalarA scalar object is simply a single numeric value.TableA table object is a series of numeric values or character strings. A table has one column and a fixed number of rows. Tables are typically used to store columns from an attribute table, or a list of values which pertain to the individual layers of a raster layerset.A table may consist of up to 32,767 rows. Information in the table can be attributes, calculated (e.g., histograms), or user-defined.MatrixA matrix object is a set of numbers arranged in a two dimensional array. A matrixhas a fixed number of rows and columns. Matrices may be used to store convolution kernels or the neighborhood definition used in neighborhood functions. They can also be used to store covariance matrices, eigenvector matrices, or matrices of linear combination coefficients.※ See the “Enhancement” chapter of the ERDAS Field Guide for more information about convolution filtering.Normalized Matrix ObjectYou have the option to normalize the matrix in the Matrix dialog. Normalizing the matrix replaces the cell values of the matrix with the values divided by the sum of all values of the matrix except when the sum is zero.For example, a 3 x 3 matrix of:1 1 11 1 11 1 1...is used to average the pixels in an image. If these values were actually used, the output pixel values would be 9 times larger than expected.The real matrix used to average the pixel values is:1/9 1/9 1/91/9 1/9 1/91/9 1/9 1/9For either custom or built-in input matrices, the default is to normalize the matrix which is usually desired for convolution filtering. If you are entering a matrix of coefficients for a function such as LINEARCOMB, you may want to turn off the Normalize check box. For output matrices, normalization is turned off.RasterA raster object is a single layer or layerset of raster data. Rasters are typically used to contain and manipulate data from image files.VectorA vector object is either an Arc/Info Coverage or an Annotation Layer.Data TypesThe objects above may be of the following data types:※ Binary - either 0 (false) or 1 (true)※ Integer - integer values from -2,147,483,648 to 2,147,483,647 (signed 32-bit integer)※Float - floating point data (double precision)Table objects may also use the following data type:※ String - a character string.Defining Objects in a ModelIn a model, objects are used as:※ input to a function definition, to be operated upon※output, the result(s) of your model.ConnectionsWhether an object is input or output is specified by how you connect each object to a function definition.※ By making a connection from an object to a function definition, you specify that object as input to the function definition.※ By making a connection from a function definition to an object, you specify that object as output from the function definition.Of course, function definitions can be chained together in complex models, and therefore an object can be both input and output.Objects (rasters, matrices, tables, and scalars) may be connected only to functions, and functions may be connected only to objects. Connections which would form a circular path in the model are not allowed.Model Maker will not let you connect a function to more than one output. If you try to draw a connector to a second output, the connector to the first output will disappear.As you move object and function graphics in the Model Maker window, the connection arrows also move accordingly.You can remove a connection by using the connector tool and simply drawing in the reverse direction (i.e., from function to object).Input ObjectsFollow these steps to define input objects in a model:1. Decide upon which objects you need to operate to create one output. These will be your input objects. Often, there will be only one or two input objects.2. For each input object, select the appropriate object tool (Raster , Matrix, Table ,or Scalar ) from the Model Tools palette, and place the object graphic in the Model Maker window. You can rearrange these graphics any time.3. Double-click on each object graphic in the Model Maker window to open the appropriate dialog for defining that object. The Raster, Matrix, Table, or Scalar dialog is opened.4. Use the Function tool from the Model Tools palette to place a function graphic in your model. Position your graphics so that a line can be drawn from each input object graphic to the function graphic.5. Select the Connector tool from the Model Tools palette. Click on an input object graphic and drag the connector to the function graphic. Repeat for each input object.Now your input objects are defined so that you can create a function definition with those objects.Output ObjectsFollow these steps to define an output object:There can be only one output object for each function definition. There can, however, be many function definitions in a model.1. If needed, use the Function tool in the Model Tools palette to place a function graphic in your model.2. Select the appropriate object tool for your output (Raster , Matrix ,Table , or Scalar ) from the Model Tools palette, and place the object graphic in the Model Maker window. The type of object that you select will depend upon the function definition.3. Select the Connector tool in the Model Tools palette. Click on the function graphic and drag the connector to the output object graphic.Function DefinitionsObjects used in a Model Maker model are operated upon with function definitions that you write with the Model Maker. The function definition is an expression (like “a + b + c”) that defines your output. You will use a variety of mathematical, statistical, Boolean, neighborhood, and other functions, plus the input objects that you set up, to write a function definition.To create a function definition, follow these steps:1. Define your input objects, following the steps above. You should have your input objects defined, and all connections made from the input objects to the function graphic.2. Double-click on the function graphic. The Function Definition dialog is opened. Use this dialog to compose a function definition.You should define all input objects to a function before you double-click on the function graphic. Then, the inputs you specified will be listed in the Function Definition dialog. You can then select the input objects from a list in the dialog as you compose your function definition.Recoding Raster ObjectsIf the purpose of your model is to recode only, you can set up the recode in the Raster dialog and you do not need to select a function in the Function dialog. Place the input raster graphic on the page, set up the recode when defining the raster and connect this graphic to the function graphic. Then connect the function graphic to an output raster graphic.Within the function definition, you simply click on the input raster which will be recoded and copied to the output raster.Using the Function Definition DialogInput ObjectsThe Available Inputs list in the dialog shows all of the input objects that are available for your function definition. These are the inputs that are connected to the function as inputs. To change this list, change the objects that are connected to the function.To use an input object in your function definition, click on the object name in this list. It will be displayed in the text field at the cursor location.FunctionsUsing the popup list and the scrolling list of functions, you can select functions according to function categories. The function categories and the functions in each category are documented in the Spatial Modeler Language on-line manual. When you click a function from the scrolling list, it is opened in the text field at the cursor location.The simplest function definition is a copy. A copy requires no functions. Just click on an available input object in the list, so that your function definition consists only of the input object name. When the model is executed, this will simply copy the selected input to the output object. This is useful when all you want to do to a raster is recode it.Prototype ArgumentsMany functions in the scrolling list have prototypes, which are short descriptions of the appropriate input objects or values upon which that function operates. Prototypes are surrounded by < > brackets. You must replace a prototype with an object or value.After you place a function int o the function definition text field, click in a function’s prototype to position the cursor within the brackets. Then click the desired input object, and it will automatically replace the prototype.Specifying CriteriaThe Criteria function in Model Maker gives you the power of the CONDITIONAL function within the Spatial Modeler Language. You can use the Criteria function to build a table of conditions which must be satisfied to output a particular row value for a descriptor (or cell value) associated with the raster you select. Double-click the criteria graphic in an existing model to define the criteria with theCriteria dialog. To establish a new Criteria function, click the icon on the Model Maker tool palette.The inputs to a Criteria function are rasters. The columns of the Criteria table represent either descriptors associated with a raster layer, or the layer itself if the cell values are of direct interest. Criteria which must be met for each output column are entered in a cell in that column (e.g., >5). Multiple sets of criteria may be entered in multiple rows. The output raster will contain the first row number of a set of criteria that were met for a raster cell.ExampleThe example below illustrates how you can use the Criteria function.If des criptors of “Acreage” and “Class Name” are available and a map of pine forests larger than 10 acres is desired: both “Acreage” and “Class Name” are added as column titles in the Criteria dialog. In the cell under “Acreage,” “>10” is entered and under “Class Name,” “Pine” is entered. In this one row example, a pixel value of one is output for pixels that satisfy both criteria.To take this example further, if more than one acreage class is desired, a row is added to the criteria table for each size class des ired. Under “Acreage” in the first row “>50” might be entered and in the second row “>10.” The first row in which the criteria are satisfied will be the output pixel value, thus the relational expressions should be more restrictive as you go down the rows.Output ParametersSince you can have several inputs in one model, you have the option to define the working window and the cell size of the output data.Default settings for these parameters can be set in the Preference Editor. Working WindowYou can input raster layers of differing areas into one model. However, you must specify the image area (or working window) to use in the model calculation. Select one of three options:※ Union - the model will operate on the union of all input rasters.※ Intersection - the model will use only the area of the rasters that is common to all input rasters.※ Other - specify the working window in explicit coordinates.The default setting is union. To change this parameter, under Model on the Model Maker menu bar, click Set Window and the Set Window dialog is opened. Cell SizeInput rasters may also be of differing resolutions (pixel size), so you must also select the output file cell size as either:※Minimum - the minimum cell size of the input layers will be used. This is the default setting.※Maximum - the maximum cell size of the input layers will be used.※Other - specify a new cell size.To change the cell size, under Model on the Model Maker menu bar, click Set Cell Size. The Set Cell Size dialog is opened.Creating a ModelThere are several graphical models included with ERDAS IMAGINE in the<$IMAGINE_HOME>/etc/models directory. You can load these models to run them or edit them to create new models.Creating a New ModelThere are two basic ways to create a new model:※ edit an existing model,※ create a model from “scratch.”Edit an Existing ModelOpen an existing model, either one that was delivered with IMAGINE, or one that you previously created. Select File | Open in the Model Maker menu bar and select the model to view. Doubleclick on any of the graphics in the model to redefine them. You can change the inputs used, select another function to use, etc.Then, select File | Save As from the Model Maker menu bar. Enter a new name for your model.Using the Spatial Modeler LanguageThe Spatial Modeler Language is a language designed for advanced modeling and includes over 200 functions and operators. Models can be created in a text file and run from a command line, or from within ERDAS IMAGINE.The Spatial Modeler Language encompasses all functions available in Model Maker as well as:※ conditional branching and looping※ complex and color data types※ more flexibility in using raster objects and descriptorsGraphical models created with Model Maker can be output to a script file (text only) in the Spatial Modeler Language. These scripts can then be edited with a text editor using the Modeler Language syntax and re-run or saved in a library. Generating a ScriptModels created with Model Maker can be saved as a script file (text only) by selecting Process | Generate Script on the Model Maker menu bar.You can access this script from the Model Librarian option of the Spatial Modeler.Through the Model Librarian, you can Edit, Run, or Delete models.The Edit option brings up a text editor where you can use the Modeler Language to write new or edit existing models.Spatial ModelerSpatial Modeler enables you to create and run models for image processing and GIS analysis. It is a highly flexible tool which uses Model Maker and the Spatial Modeler Language.The Spatial Modeler Language is a modeling language that is used internally by Model Maker to execute the operations specified in the graphical models that you create. You can also use the Spatial Modeler Language directly to write your own script models.Click this icon on the ERDAS IMAGINE icon panel to access Spatial Modeler:Model Maker... Click to open the Model Maker window and the Model Maker Tool palette. This window allows you to work with graphical models. You can view or edit existing models and create new models.Script Librarian... Click to open the Model Librarian dialog. This dialog lists all the existing script models in the system. Using this option, you can view, edit, create, and delete script models.Close Click to close this dialog.Help Click to open this On-Line Help document.※ For information on using the ERDAS IMAGINE graphical interface, see the on-line IMAGINE Interface manual.※ See the ERDAS IMAGINE Tour Guides manual for step-by-step instructions on using Model Maker.※ See the on-line Spatial Modeler Language manual for more information about creating script models.英文翻译(译文)模型生成器的介绍一个模型就是一系列指示,它在IMAGINE软件的空间建模组件中被处理,从而运行地理信息系统和图像处理操作。
混凝土梁–柱联接部位的加固(英文翻译)
本科毕业设计(论文)英文专题专业名称:土木矿建年级班级:土木单招06-1班学生姓名:XXX指导教师:余永强河南理工大学土木工程学院二○一○年六月十日Reinforcement of concrete beam–column connectionswith hybrid FRP sheetAbstractThe paper describes the results of tests on prototype size reinforced concrete frame specimens which were designed to represent the column–beam connections in plane frames. The tests were devised to investigate the influence of fibre reinforced plastic (FRP reinforcement applied to external surfaces adjacent to the beam–column connection on the behaviour of the test specimens under static loading. Of particular interest under static loading was the influence of FRP reinforcement on the strength and stiffness of beam–column connection. As a key to the study, the hybrid FRP composites of E-glass woven roving (WR) and plain carbon cloth, combined with chopped strand mat (CSM), glass fiber tape (GFT) with a vinyl-ester resin were designed to externally reinforce the joint of the concrete frame. The results show that retrofitting critical sections of concrete frames with FRP reinforcement can provide signification strengthening and stiffening to concrete frames and improve their behaviour under different types of loading. The selections of types of FRP and the architecture of composites in order to improve the bonding and strength of the retro-fitting were also discussed.Author Keywords: Concrete structure; Strengthening; Rehabilitation; Hybrid FRP composite; Wrapping technique1. IntroductionA widely adopted technique for retrofitting concrete structure is to use steel jackets placed around existing concrete columns [1 and 2]. The use of steel encasement to provide lateral confinement to the concrete in compression has been studied extensively[3 and 4], and has shown increase in the compression load carrying capacity and ductility of the concrete columns. However, the shortcomings of this technique are that it suffers from corrosions as well as inherent difficulties during practical applications. Fibre reinforced plastic (FRP), on the other hand, is increasingly being used to reinforce concrete, masonry and timber structures. The load carrying capacity and serviceability of existing structures can be significantly augmented through externally retrofitting critical sections with FRP sheeting. In recent years FRP materials with wide range of fibre types of glass, aramid or carbon provide designers with an adaptable and cost-effective construction material with a large range of modulus and strength characteristics. Comparing with traditional rehabilitation techniques, the FRP composites have high specific strength/stiffness, flexibility in design and replacement as well as robustness in unfriendly environments. With FRP composites it is possible and also necessary to achieve the best strengthening results by optimising the constitute materials and architecture. Optimisation of the constitute materials and architecture becomes essential in order to utilise the superiority of FRP composites in application of rehabilitation [5, 6, 7, 8 and 9]. It was found that winding of carbon fiber/epoxy composites around square concrete columns can increase the load carrying capacity by 8–22%, depending on the amount of fibres used and treatments of substrate surface [10]. The use of resin infusion technique was shown to contribute to substantial improvements in composite wrapping efficiency, and the use of woven glass roving, as the reinforcement in composites wrapping, was found to significantly increase both load carrying capacity and deformation resistance capacity of the concrete stubs [2]. Furthermore, through the use of glass/carbon hybrid reinforcements with an epoxy resin, replication of initial performance of concrete stubs subjected to deterioration was shown possible, with a simultaneous further improvement in load carrying capacity. In terms of the effects of orientation and thickness of the composites warps, it was found that the predominant use ofreinforcements in the hoop direction would result in high efficiency [11]. Despite the large number of research carried out, one shortcoming of most studies has been that they were limited to simple small size components, such as concrete cylinders, rather than real structures. Furthermore, it is essential to study the optimisation of composites architectures in terms of cost effectiveness including materials and processing methods. This implies that the reinforcement of infrastructure with FRP composites should utilise the advantages of various materials, not only carbon fibers with epoxy resin, but also glass fiber or hybrid of carbon/glass fibres with other polymer resins. In this experimental investigation, a hybrid of carbon/E-glass with vinyl-ester resin composites jacket was designed to reinforce a typical building components, namely a column–beam connection. Static tests were then conducted on FRP reinforced and non-reinforced specimens with extensive instrumentation to study the influence of the designed composite reinforcement. The investigation reported in the paper forms part of a collaborative research program between the University of Technology, Sydney and the Centre for Advanced Materials Technology, the University of Sydney in relation to application of advanced fibre composites to strengthen, stiffen and hence rehabilitate concrete structures.2. Experimental proceduresThree prototype size reinforced concrete frame specimens, representing typical concrete column–beam connection, were designed for this study. Geometry of the specimens with location of FRP composite reinforcement is illustrated in Fig. 1. Among three specimens, two of them are as-is concrete beam–column connection type (none composites-reinforced (Non-CR) specimens) and one specimen was reinforced by the hybrid of carbon fiber and glass fibre composites around the column–beam joint (composites-reinforced (CR) specimen). All three specimens were pre-cast using standard commercial mix grade 40 concrete. The steel reinforcement of the concrete specimens are also shown in Fig. 1. Concrete compression tests based on the Australian Standard (AS 1012–1986) were conducted on the samples taken during the concrete pour in order to determine the modulus of elasticity and ultimate compression strength (UCS) of the concrete.2.1. Composites architectureOne of the three concrete frame specimens was reinforced with hybrid composites. The hybrid composites consists of four basic architectures, namely E-glass woven roving (WR/600 g/m2), chopped strand mat (CSM-300 g/m2), carbon cloth (plain weave-200 g/m2) and glass fibre tape (GFT-250 g/mm2). The details of the composites architecture are shown in Table 1 and Fig. 2. Details of lay-up are illustrated in Fig. 3. WR and carbon cloth are a multi-directional reinforcement with biaxial plain weaving which provide equivalent strength in both axial and hoop directions. They play the basic reinforcement role in this composites architecture. GFT applying at hoop direction provides very good confinement and enhances structural integrity. The selection of resin curing systems is mainly concerned with the resin gel-time at ambient temperature, which is critical to wrapping process. In general, cold setting resin systems (ambient temperature curing) can be used when wet lay-up process is applied. Since no lay-up machine is available for the wrapping process described in this study, the hand lay-up method was used. The vinyl-ester resin, Dastar-R/VERPVE/SW/TP, was mixed with 1.5% of MEKP(methyl-ethyl-ketone-peroxide), 0.4% of CoNap (Cobalt napthenate), and 0.5% of DMA(Dimethylaniline) at ambient temperature. The resin cures at ambient temperature. The weight ratio between resin and fibre layers was 1:1.5 for WR/CSM layers and 1:0.8 for carbon cloth, respectively. The concrete frame was wrapped by a lames-wool roller and a consolidating roller. Before laying the first fibre layer, the concrete surfaces were cleaned up using acetone, and a thin resin coat was applied to seal micro holes on the surface of concrete columns. However, further surface treatment such as sanding surface to expose the aggregates was intentionally avoided. Each composite layer was wetted with the resinand rolled onto the concrete frame to ensure full consolidation.Table 1. Details of five composite systems with a compositearchitectures2.2. Design of static testsThe static tests of the concrete frame specimens were setup in a horizontal plane. The three supports of the concrete frame (no load applied) were roller type as shown in Fig. 4. The end at which load was applied was also a roller type support, however, horizontal movements were obviously not prevented. In order to provide the ideal roller type boundary conditions at each end as designed, a special setup was developed with combination of rollers and a swivel head at each supporting/loading point (Fig. 5). Four 1000-kN-hydraulic jacks were used in the tests. Among them, the only active jack was the jack that applied loads, while others were simply acting as adjustable packing to providing the reactions.Fig. 4. Illustrative sketch of test set-up for static test.Fig. 5. Set-up for static test of concrete frame.2.3. Instrumentation and data loggingApplied load as well as reaction forces were measured using four 998.8 kN load cells located in each of four supporting/loading positions. In order to obtain detailed flexural deflection curves for the concrete frame specimens, twelve linear variable displacement transducers (LVDTs) with a range from ±2.5 to ±50 mm were used at strategic locations to measure the flexural deflections. Extensive strain gauging was designed to capture the stress distribution of the testing specimens in order to validate tests and gain an insight into the behaviour of the concrete frame with or without FRP reinforcement. The total number of strain gauges was 56 for each specimen, in which 28 strain gauges (5 mm) were located on steel rebars and the rest (30 mm strain gauges) were located on the external surface of the concrete frame specimens. Locations of the strain gauges were arranged so that the strains on various points of the cross sections could be captured. A typical strain gauge arrangement for most measured cross sections is shown in Fig. 6. Locations of strain gauges inside the section are shown in Fig. 7.Fig. 6. Location of cross sections of the concrete frame for strain gauging.2.4. Test procedureDesignations of test specimens and a brief description are given in Table 2. Prior to being formally tested at service load level, the first non-CR specimen was subjected to a series of investigative tests mostly loaded at the service load level of 40 kN with one single overload up to 50 kN. The second non-CR specimen and the CR specimens were not subjected to any loading until the initial service load level tests. All ultimate load tests were conducted after every specimen was exposed to about 100 cycles of cyclic loading atservice load levels.Table 2. Applied load and reactions for typical tests (unit: kN)3. Results and analysisIn order to determine the influence of FRP composites, five sets of tests were conducted on the three specimens including three tests at service load levels and two atthe ultimate load level. For every test, logged data consisted of four load records, twelve deflection records and 56 or 64 strain records.3.1. Validation of the static testsTo validate the performed tests, the static equilibrium for each test was verified as follows:Equilibrium of external loads: As redundancy was avoided in design of these tests and load cells were placed at each loading or reaction point, it was convenient to check equilibrium of the load/reaction forces through simple statics. Table 2 shows that the equilibrium of external loads was satisfied.Equilibrium of forces and equilibrium of moment on cross sections: In order to calculate the internal forces and sectional moments, strains on the designated sections were required. To process the measured strains on a given cross section, the following assumption was made: the strains vary linearly through the cross sections. In other words the strains at a given cross section can be represented by a strain plane. Under this assumption, least square method with the two explanatory variables was adopted to obtain the strain plane for each given cross section using values of six measured strains. Fig. 8 shows comparison of the measured strain values and those calculated from the least square fitting. The strain values used in subsequence evaluations or calculations were obtained from calculated strain planes. For the validation of the equilibrium of internal forces in a given cross section, forces were calculated by integration of resulting stresses in tension and compression zones, respectively. The concrete was assumed to carry only compression loads and steel rebars (with FRP composites in some cases) were considered as the main load carriers in the tension zone. Equilibrium states that the resultant force in the compression zone should be equal to that in the tension zone. Moments at a given cross section were firstly calculated through integration of stresses in the section. They were compared to those calculated by using measured loads multiplied by the lever arms.Details of formulae pertained to these calculations are presented in Appendix A. As shown in Table 3 and Table 4, equilibrium is validated.Fig. 8. Comparison of measured vs calculated strain values from least square fitting.Table 3. List of calculated internal force and moments at section A-A of a non-CRspecimenTable 4. List of calculated internal force and moments at section A-A of a CR specimen3.2. Load–deflection curvesComparison of load–deflection curves for CR and non-CR specimens at both service load and ultimate load levels are shown in Fig. 9 and Fig. 10. About 45% increase in stiffness was observed due to the presence of FRP composites reinforcement (service load level). Results of the ultimate loading test indicated an increase in load carrying capacity of CR specimen of approximately 30% due to the presence of FRP composites.3.3. Analysis of the strain resultsTo evaluate change of strain in steel rebars due to FRP reinforcement, a parameter was defined, namely "average strain reduction". It is defined aswhere P is the average of maximum section strains of the two none composites-reinforced (non-CR) specimens and R is the maximum section strain of composites-reinforced (CR) specimen at the same load level. Table 5 and Table 6 summarise the typical comparison of maximum/minimum strains between non-CR and CR specimens and average strain reduction in various cross sections at same load level (see also Fig. 11). If one takes the mean of the average strain reductions for all beam-sections, it yields strain reduction factor of 51%. In same way, the mean of the average strain reductions for all column-sections is 55%. The average strain reduction can be used as an indication of external FPR reinforcement efficiency.Table 5. Comparison of the maximum strains in the rebars for beam sections (unit: )Table 6. Comparison of the maximum strains in the rebars for column sections (unit:)Fig. 11. Comparison of strains of CR and non-CR specimens in steel rebars at a given section.3.4. Discussions on applied composites architectureResults from both service load level tests and ultimate load test of the concrete frames show that the proposed composites architecture successfully enhanced the original structure in terms of stiffness and load carrying capacity. It is interesting to note that although the elastic modulus of FRP composites is only approximately half of that of concrete, the increase in stiffness and load carrying capacity of a reinforced concrete was significant. Despite of absence of special surface treatment of concrete before the application of FRP composite reinforcement, the bonding between the concrete and composites did not fail. This may be owing to the lower elastic modules of hybrid composites. There is an indication that low modulus FRP may provide better reinforcement/retrofitting for concrete structures because of low tensile strength in concrete. In the lay-up design, the gradual change of thickness is essential. It will reduce possible stress concentration in the FRP composites which could cause delamination or cracking. However, it is important to point out that because only a limited number of specimens were studied, some of these conclusions may be biased. It is suggested to conduct more tests to confirm these results.4. ConclusionsAs results of this study, the following conclusions can be drawn:1. Tests on prototype size reinforced concrete frame specimens, designed to represent the column–beam connections in plane frame, have been successfully conducted. Test results were validated through equilibrium checks.2. Designed hybrid composites consisting of roving cloth, carbon cloth, and chapped strand mat and glass fibre tape demonstrated effectiveness in reinforcing concrete structures. The results from the tests show significant increases in stiffness and load carrying capacity due to reinforcement provided by hybrid FRP composites. The resultsalso show that optimisation is important in reinforcing concrete structures to achieve good results with low cost.3. The results of static tests also suggest that hybrid carbon/E-glass fibre composites with low elastic modulus may contribute to good bonding and non-delamination. However, this needs to be confirmed by more tests.4. It is also suggested that further investigation be carried out including reinforcing damaged concrete frame specimens, cyclic loading and using different composites architectures.Appendix AAssuming that at a given cross section of beam/column strain distribution is linear, for the given section, strain can then be expressed in form of(x ,y )=ax +by +c ,(A .1) where a , b , c are constants.Consider a two explanatory variables regression modelYi =0+1x i 1+2x i 2+e i , (A.2)where x i 1 represents the i th observation on explanatory variable X 1 and x i 2 denotes the i th observation on second explanatory variable X 2.One can obtain a best fit strain plane from measured strain in a given section.Under linear strain distribution assumption, a closed form solutionfor force and moment at the cross section using strain data can be obtained by double integration. In compression zone for the concrete (refer to Fig. 12), one obtains:(A.3)where E is the modulus of the elasticity of concrete; a , b and c are constants in Eq.(A.1); F I is the resultant force in the compression zone.(A.4)where M I is the moment at the compression zone.Fig. 12. Schematic drawing of a typical cross sectionof concrete frames. For steel rebars and composites (if applied):(A.5)where F I S and F I C are forces in steel rebars and composite, respectively. In tension zone, only steel rebars and composite count, formulae are similar to Eq. (A.5).具有混合纤维增强塑料片的混凝土梁–柱联接部位的加固摘要本篇文章描述了对加固后标准尺寸混凝土结构试件进行试验的结果,该试件代表平面框架结构中的梁–柱联接部位。
- 1、下载文档前请自行甄别文档内容的完整性,平台不提供额外的编辑、内容补充、找答案等附加服务。
- 2、"仅部分预览"的文档,不可在线预览部分如存在完整性等问题,可反馈申请退款(可完整预览的文档不适用该条件!)。
- 3、如文档侵犯您的权益,请联系客服反馈,我们会尽快为您处理(人工客服工作时间:9:00-18:30)。
本科毕业设计(论文)英文翻译要求
英文原文和翻译均作为毕业论文附录,同时给出英文原文的出处,如果是网上下载的原文请给出网址。
具体要求如下:
内容要求:外文文献翻译的内容应与毕业设计(论文)课题方向相关。
外文翻译应包括,外文题目,作者、出版日期和出版社,翻译内容的起止页码,外文原文,然后是中文题目,作者、出版日期和出版社,中文翻译。
外文翻译所用的文献,应主要选自学术期刊或学术会议的文章,其次是教科书或其他书籍。
(撰写论文时,要求参考文献中要有1-2篇外文文献。
)
字数要求: 要求翻译1-2篇,译成中文后,合计中文字数不少于3000字。
排版要求: 与毕业设计(论文)手册中有关毕业设计说明书的要求一致(字体,字号,中英文部分分别对应等)。
注意事项:
(1)严禁利用翻译工具直译后不做任何校正,不排版,节选文章应独立成篇。
(2)注意自留文稿,英文原文和翻译均为毕业论文附录。
若寻找英文文章有困难,将中文文献翻译为英文亦可。