周期式轧管机的工作原理及轧制变形过程
冷轧钢管变形原理
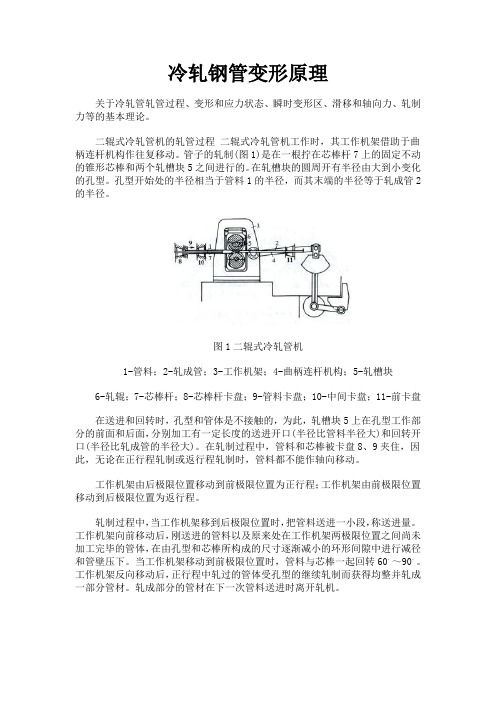
冷轧钢管变形原理关于冷轧管轧管过程、变形和应力状态、瞬时变形区、滑移和轴向力、轧制力等的基本理论。
二辊式冷轧管机的轧管过程二辊式冷轧管机工作时,其工作机架借助于曲柄连杆机构作往复移动。
管子的轧制(图1)是在一根拧在芯棒杆7上的固定不动的锥形芯棒和两个轧槽块5之间进行的。
在轧槽块的圆周开有半径由大到小变化的孔型。
孔型开始处的半径相当于管料1的半径,而其末端的半径等于轧成管2的半径。
图1二辊式冷轧管机1-管料;2-轧成管;3-工作机架;4-曲柄连杆机构;5-轧槽块6-轧辊;7-芯棒杆;8-芯棒杆卡盘;9-管料卡盘;10-中间卡盘;11-前卡盘在送进和回转时,孔型和管体是不接触的,为此,轧槽块5上在孔型工作部分的前面和后面,分别加工有一定长度的送进开口(半径比管料半径大)和回转开口(半径比轧成管的半径大)。
在轧制过程中,管料和芯棒被卡盘8、9夹住,因此,无论在正行程轧制或返行程轧制时,管料都不能作轴向移动。
工作机架由后极限位置移动到前极限位置为正行程;工作机架由前极限位置移动到后极限位置为返行程。
轧制过程中,当工作机架移到后极限位置时,把管料送进一小段,称送进量。
工作机架向前移动后,刚送进的管料以及原来处在工作机架两极限位置之间尚未加工完毕的管体,在由孔型和芯棒所构成的尺寸逐渐减小的环形间隙中进行减径和管壁压下。
当工作机架移动到前极限位置时,管料与芯棒一起回转60。
~90。
工作机架反向移动后,正行程中轧过的管体受孔型的继续轧制而获得均整并轧成一部分管材。
轧成部分的管材在下一次管料送进时离开轧机。
图2多辊式冷轧管机1-柱形芯棒;2-轧辊;3-轧辊架;4-支承板;5-厚壁套筒;6-大连杆;7-摇杆;8-管子多辊式冷轧管机的轧管过程多辊式冷轧管机轧制管材时见(图2),管子在圆柱形芯棒1和刻有等半径轧槽的3~4个轧辊2之间进行变形。
轧辊装在轧辊架3中,其辊颈压靠在具有一定形状的支承板(滑道)4上,支承板装在厚壁套筒5中,而厚壁套筒本身就是轧机的机架,它安装在小车上。
周期式冷轧管机的发展

!"#"$%&’"() %* +%$, - .%$$/(0 1/$0". 2/$$
89 :;)<"= 0 6>9?9=# @9=#AB>=# C=D"AEF9;* 3>GB=)*)#H I>J>*)KL>=E M)$’ 6>9?9=# ,&&&+1’ MB9=; 2
!"#$%&’$N
I>AGF9O>D 9= EB> ;FE9G*> ;F> EB> B9AE)F9>A ;=D G"FF>=E A9E";E9)=A G)=G>F=9=# P Q I )R EB> G)*D 7 F)**9=#
和 /[ 时,冷轧后可分别减到 1[ 和 5[ 2 。 0 . 2 管子的显微组织得到改善。 0 5 2 由于采用精加工的轧辊和芯棒,因而所轧 的管子内、外表面质量好,尺寸精度高,内、外径 的公差可达 \ &$ ,LL,甚至达到 \ &$ &&/LL。 0 1 2 可减少压头、酸洗、脱脂、退火等一部分 中间工序,从而相应减少了部分操作人员和生产占 地面积,各种消耗也相应降低。 0 Y 2 在冷轧过程中没有金属损失,因而成材率 有所提高。 0 / 2 此生产方法可以有条件地加大锭坯重量与 管坯长度,从而大幅度地提高了成材率和生产效率 0 锭坯重量已达 5&&T#,轧管坯长可达 %1&L 2 。 0 X 2 采用电子计算机进行程序控制,操作实现 自动化,由此减少了操作人员 0 一人监控 2 ,降低了 劳动强度。 但是,冷轧方法也存在一次性投资高、设备复 杂、操作和维修技术要求高以及噪声较大等问题。 周期式冷轧管机开发至今已有 1& 年历史,其
冷轧钢管变形原理
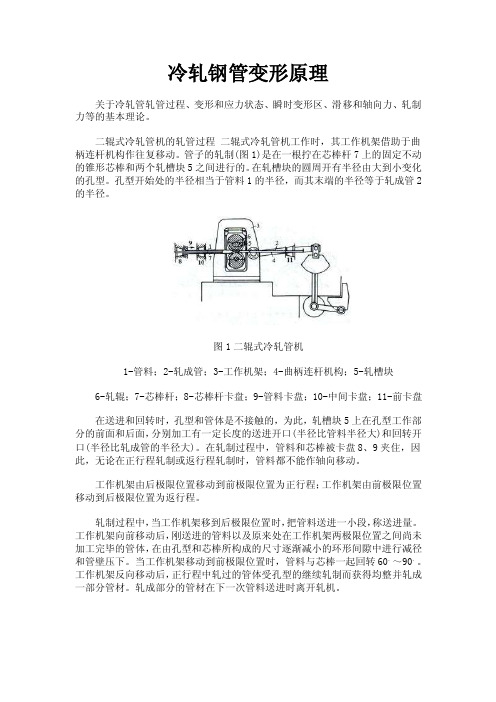
冷轧钢管变形原理关于冷轧管轧管过程、变形和应力状态、瞬时变形区、滑移和轴向力、轧制力等的基本理论。
二辊式冷轧管机的轧管过程二辊式冷轧管机工作时,其工作机架借助于曲柄连杆机构作往复移动。
管子的轧制(图1)是在一根拧在芯棒杆7上的固定不动的锥形芯棒和两个轧槽块5之间进行的。
在轧槽块的圆周开有半径由大到小变化的孔型。
孔型开始处的半径相当于管料1的半径,而其末端的半径等于轧成管2的半径。
图1二辊式冷轧管机1-管料;2-轧成管;3-工作机架;4-曲柄连杆机构;5-轧槽块6-轧辊;7-芯棒杆;8-芯棒杆卡盘;9-管料卡盘;10-中间卡盘;11-前卡盘在送进和回转时,孔型和管体是不接触的,为此,轧槽块5上在孔型工作部分的前面和后面,分别加工有一定长度的送进开口(半径比管料半径大)和回转开口(半径比轧成管的半径大)。
在轧制过程中,管料和芯棒被卡盘8、9夹住,因此,无论在正行程轧制或返行程轧制时,管料都不能作轴向移动。
工作机架由后极限位置移动到前极限位置为正行程;工作机架由前极限位置移动到后极限位置为返行程。
轧制过程中,当工作机架移到后极限位置时,把管料送进一小段,称送进量。
工作机架向前移动后,刚送进的管料以及原来处在工作机架两极限位置之间尚未加工完毕的管体,在由孔型和芯棒所构成的尺寸逐渐减小的环形间隙中进行减径和管壁压下。
当工作机架移动到前极限位置时,管料与芯棒一起回转60。
~90。
工作机架反向移动后,正行程中轧过的管体受孔型的继续轧制而获得均整并轧成一部分管材。
轧成部分的管材在下一次管料送进时离开轧机。
图2多辊式冷轧管机1-柱形芯棒;2-轧辊;3-轧辊架;4-支承板;5-厚壁套筒;6-大连杆;7-摇杆;8-管子多辊式冷轧管机的轧管过程多辊式冷轧管机轧制管材时见(图2),管子在圆柱形芯棒1和刻有等半径轧槽的3~4个轧辊2之间进行变形。
轧辊装在轧辊架3中,其辊颈压靠在具有一定形状的支承板(滑道)4上,支承板装在厚壁套筒5中,而厚壁套筒本身就是轧机的机架,它安装在小车上。
冷轧管变形原理

冷轧管变形原理deformation theory of cold rolling tube process关于冷轧管轧管过程、变形和应力状态、瞬时变形区、滑移和轴向力、轧制力等的基本理论。
二辊式冷轧管机的轧管过程二辊式冷轧管机工作时,其工作机架借助于曲柄连杆机构作往复移动。
管子的轧制(图1)是在一根拧在芯棒杆7上的固定不动的锥形芯棒和两个轧槽块5之间进行的。
在轧槽块的圆周开有半径由大到小变化的孔型。
孔型开始处的半径相当于管料1的半径,而其末端的半径等于轧成管2的半径。
图1二辊式冷轧管机1-管料;2-轧成管;3-工作机架;4-曲柄连杆机构;5-轧槽块6-轧辊;7-芯棒杆;8-芯棒杆卡盘;9-管料卡盘;10-中间卡盘;11-前卡盘在送进和回转时,孔型和管体是不接触的,为此,轧槽块5上在孔型工作部分的前面和后面,分别加工有一定长度的送进开口(半径比管料半径大)和回转开口(半径比轧成管的半径大)。
在轧制过程中,管料和芯棒被卡盘8、9夹住,因此,无论在正行程轧制或返行程轧制时,管料都不能作轴向移动。
工作机架由后极限位置移动到前极限位置为正行程;工作机架由前极限位置移动到后极限位置为返行程。
轧制过程中,当工作机架移到后极限位置时,把管料送进一小段,称送进量。
工作机架向前移动后,刚送进的管料以及原来处在工作机架两极限位置之间尚未加工完毕的管体,在由孔型和芯棒所构成的尺寸逐渐减小的环形间隙中进行减径和管壁压下。
当工作机架移动到前极限位置时,管料与芯棒一起回转60。
~90。
工作机架反向移动后,正行程中轧过的管体受孔型的继续轧制而获得均整并轧成一部分管材。
轧成部分的管材在下一次管料送进时离开轧机。
图2多辊式冷轧管机1-柱形芯棒;2-轧辊;3-轧辊架;4-支承板;5-厚壁套筒;6-大连杆;7-摇杆;8-管子多辊式冷轧管机的轧管过程多辊式冷轧管机轧制管材时见(图2),管子在圆柱形芯棒1和刻有等半径轧槽的3~4个轧辊2之间进行变形。
Φ720mm周期轧管机组的工艺和设备

炉和机械式室式加热炉、淬火水池、控冷设施,超 声波探伤机、磁粉探伤机,压力矫直机和内外修磨 机等多台设备。
2 主要设备组成和特点
Φ720 mm 周期轧管机组的主要设备有:环形 加热炉、立式水压冲孔机、二辊桶形辊穿孔机、喂 料器、周期轧管机、热锯、步进式再加热炉、5 机 架三辊定径机。其主要设备的特点如下。
1) 立式水压冲孔机 25 MN 水压冲孔机本体主要部件组成如图 2 所示。 主工作缸为柱塞缸,在压力为 28 MPa 的介质 作用下,产生的公称压力为 25 MN。回程缸为差 动式柱塞缸,缸体安装在机架的两侧,生产回程力 3.45 MN。活动横梁主要用来传递冲压力,同时起 冲杆的导向作用。活动横梁上部用压圈与主柱塞连 接定位,下部安装有冲杆,活动横梁导向形式为 X 形,当活动横梁或机架热胀冷缩时,导向可以沿 X 方向自由伸缩,保持活动横梁运动灵活。导向装置 安装在机架的四侧,作活动横梁和定位脱料装置导 向用。定位脱料装置在机架内做升降运动,主要起 冲杆的模口定位和回程脱料作用。移动工作台在由 工作台支座和辅助座组成的导向面上移动,工作台 移动由移动油缸驱动。工作台上装有冲孔凹模,工 作台两个工位(冲孔位和上料位,上料位同时也是
偿,能精确保证 90°翻转,保证产品质量,减少咬 入打头次数。
(4) 制动刷具备调节功能,可灵活实现轧制节 奏同步,并保证芯棒上的毛管处于正确的位置。
(5) 油作为制动介质,在制动和冷却空气活塞 时可防止生锈。
(6) 机械限制可调喂入量,可实现每一个轧制 周期都有一个均匀而准确的喂入量,以保证钢管尺 寸精度。
Key words:Pilger pipe mill;Sizing mill;Vertical hydraulic piercing;Process flow;Technical parameters
轧管机的工作原理简介

轧管机的工作原理简介1. 轧管机的工作原理简介轧管机是一种用于制造金属管材的机械设备。
它通过将金属材料经过多次轧制,使其形成所需的管材形状和尺寸。
在轧制过程中,轧管机主要通过热轧或冷轧两种不同的工艺来完成。
下面将介绍轧管机的工作原理以及它的关键组成部分。
2. 热轧轧管机的工作原理热轧轧管机主要用于加工高温金属坯料,如钢坯。
它的工作原理可以概括为以下几个步骤:步骤一:物料预热将钢坯通过加热炉等设备进行预热。
这么做的目的是提高钢材的可塑性,使其更容易塑性变形。
步骤二:入口端对齐将预热后的钢坯送入轧管机,通过辊道和辊缝的定位,将钢坯的入口端对齐,以确保轧制的准确度和稳定性。
步骤三:辊道轧制在钢坯进入辊道后,它会被传送到辊缝之间。
辊道上的辊子组按照一定规律布置,当钢坯经过时,辊子组作用下的压力使得钢坯逐渐变薄并改变形状。
这一步骤通常需要多个辊子组的连续作用,以实现所需的深度和形状。
步骤四:尺寸定型经过一系列的轧制后,钢坯的形状和尺寸已经接近最终要求。
此时,进一步通过调整和矫正辊缝间距、辊子组的排布等方式,以确保钢坯的精度和尺寸满足要求。
步骤五:产出经过尺寸定型后,经过轧制的钢坯被切割成所需长度,并通过传送带等方式将成品管材输送到下一个制造环节,如焊接或后续的加工工艺。
3. 冷轧轧管机的工作原理与热轧轧管机相比,冷轧轧管机主要用于加工室温下的金属坯料,如冷轧钢板。
其工作原理与热轧轧管机类似,但有一些区别。
冷轧轧管机不需要对金属坯料进行预热,因为它们已经处于室温下。
在入口端对齐之后,钢坯进入辊道,经过一系列的辊子组轧制,使其形成所需形状和尺寸。
不同之处在于,冷轧过程中对钢板施加的压力较小,以避免在金属坯料加工过程中出现塑性变形不良或其他结构性问题。
冷轧轧管机通常需要进行多次轧制,以逐渐达到所需尺寸和形状。
与热轧相比,冷轧后的成品管材表面更加光滑,并且具有更高的尺寸精度。
4. 轧管机的关键组成部分无论是热轧还是冷轧轧管机,它们都由一些关键组成部分构成,以实现其工作原理。
周期轧管工艺技术

周期轧管工艺技术2006年7月什么是周期式轧管机组?▪在热轧无缝钢管生产中,采用周期式轧管机作为中间延伸机来完成轧管工序的整套机组,叫做周期式轧管机组。
▪该机组可采用钢锭作坯料,能适应于生产大、中型口径的无缝钢管(如石油套管)以及一些大直径厚壁管等。
周期轧管机组的诞生、演变及改进▪1884年曼内斯曼兄弟提出了用周期轧制法生产无缝钢管的设想,1891年获得专利。
▪1892年试验并成功地轧出了第一根钢管,但因该周期轧管机未考虑芯棒的复位和机械化运送,仍不能投入工业化生产。
▪直到1896年解决了机械化运送芯棒,1900年解决了芯棒复位问题之后,于1912年起在欧洲开创了世界上第一使用真正工业化方式生产无缝钢管的时代。
周期轧管工艺的演变过程▪周期轧管机组是世界上第一代无缝钢管轧管机组。
早期的周期轧管机组仅包含穿孔加轧管两个基本工序。
▪1936年卡尔梅斯对周期轧管工艺进行了重大改造,即波浪多角形钢锭+水压(机械)冲孔+延伸+周期轧制+定径。
但增加了二次再加热的火次,周期轧管工艺就进入第二代,也就是目前得到广泛使用的典型的周期轧管工艺。
周期式轧管机特点▪周期式轧管机(又称皮尔格轧机)是一台带有送料机构的二辊式不可逆轧机。
▪周期轧管机是基于把钢管轧制中各道次变形分阶段集中在同一轧槽中的设想而设计的。
▪周期式分段轧制工艺,轧辊的旋转方向与毛管前进方向恰好相反,是不多见的返向轧制工艺。
▪周期式轧管机把所有圆孔型集中在一对轧辊的梨型孔型中,上下轧辊上对称地刻有变断面的轧槽(即可变孔型),若把其孔型的横断面剖开来看,就是许多连续不断的圆孔型,就像纵向连轧管机组孔型一样。
▪周期式轧管机的轧管孔型接触金属时,其管径逐渐减少,壁厚减薄一次完成。
当轧辊旋转一周时管坯就通过轧槽实现锻轧、精轧、定径等工序而成管子。
▪一支荒管就是经过这样若干道次的周期性轧制而成的,所以称为周期式轧管机(又名皮尔格轧管机)。
周期轧管机的工艺特点▪周期轧管机属连续分段纵轧工艺,即在一个机架上完成了相当于连轧机多个机架的变形,更换规格时,只需换一对轧辊而不是多对轧辊,生产组织十分灵活。
轧制变形基本原理

1 第四章 轧制变形基本原理金属塑性加工是利用金属能够产生永久变形的能力,使其在外力作用下进行塑性成型的一种金属加工技术,也常叫金属压力加工。
基本加工变形方式可以分为:锻造、轧制、挤压、分为:热加工、冷加工、温加工。
金属塑性加工的优点(1)因无废屑,可以节约大量的金属,成材率较高;(2)可改善金属的内部组织和与之相关联的性能;(3)生产率高,适于大量生产。
第一节 轧钢的分类轧钢是利用金属的塑性使金属在两个旋转的轧辊之间受到压缩产生塑性变形,从而得到具有一定形状、尺寸和性能的钢材的加工过程。
被轧制的金属叫轧件;使轧件实现塑性变形的机械设备叫轧钢机;轧制后的成品叫钢材。
一、根据轧件纵轴线与轧辊轴线的相对位置分类轧制可分为横轧、纵轧和斜轧。
如图1、2、3。
横轧:轧辊转动方向相同,轧件的纵向轴线与轧辊的纵向轴线平行或成一定锥角,轧制时轧件随着轧辊作相应的转动。
它主要用来轧制生产回转体轧件,如变断面轴坯、齿轮坯等。
纵轧:轧辊的转动方向相反,轧件的纵向轴线与轧辊的水平轴线在水平面上的投影相互垂直,轧制后的轧件不仅断面减小、形状改变,长度亦有较大的增长。
它是轧钢生产中应用最广泛的一种轧制方法,如各种型材和板材的轧制。
斜轧:轧辊转动方向相同,其轴线与轧件纵向轴线在水平面上的投影相互平行,但在垂直面上的投影各与轧件纵轴成一交角,因而轧制时轧件既旋转,又前进,作螺旋运动。
它主要用来生产管材和回转体型材。
图1 横轧简图1—轧辊;2—轧件;3—支撑辊图2 纵轧示意图图3 斜轧简图1—轧辊;2—坯料;3—毛管;4—顶头;5—顶杆二、根据轧制温度不同又可分为热轧和冷轧。
所有的固态金属和合金都是晶体。
温度和加工变形程度对金属的晶体组织结构及性能都有不可忽视的影响。
金属在常温下的加工变形过程中,其内部晶体发生变形和压碎,而引起金属的强度、硬度和脆性升高,塑性和韧性下降的现象,叫做金属的加工硬化。
把一根金属丝固定于某一点在手中来回弯曲多次后,钢丝就会变硬、变脆进而断裂,这就是加工硬化现象的一个例子。
- 1、下载文档前请自行甄别文档内容的完整性,平台不提供额外的编辑、内容补充、找答案等附加服务。
- 2、"仅部分预览"的文档,不可在线预览部分如存在完整性等问题,可反馈申请退款(可完整预览的文档不适用该条件!)。
- 3、如文档侵犯您的权益,请联系客服反馈,我们会尽快为您处理(人工客服工作时间:9:00-18:30)。
周期式轧管机的工作原理及轧制变形过程
一、工作原理
周期式轧管机的工作过程是一个特殊的纵轧过程,它是利用变直径、变宽度的轧槽,配合稍有锥度的长芯棒,一般大头和小头直径差1〜2mm,对毛管进行辗轧加工。
图1是其工作过程示意图。
图1周期式轧管机工作过程示意图
当轧辊处于轧槽的工作阶段时,孔型高度比毛管直径大 1.0〜2.0mm,此时送料机将毛管送进一段(图1-a)。
送进过程结束后轧辊刚好转到轧槽孔型尺寸较小的工作段,此时轧件被咬人(图1-b)。
轧辊继续转动,由于其直径逐渐增大,孔型高度相应减小,毛管被压缩产生减径和减壁变形(图1-c)。
在轧制过程中,随着轧辊的转动,毛管往送进相反的方向退出,直到轧辊再次转到非工作段与毛管脱离接触时为止。
第一个工作循环结束后,喂料机除了将上一工作循环中得到延伸的那部分钢管送回外,还要把一段未经加工过的毛管送进,送进量m=20~40mm,在送进的同时将毛管翻转约90°,然后重复上述的工作循环。
周期式轧管机就是这样一段段地直至将整根毛管轧完为止。
它的变形量大,总延伸系数可达10〜12,最大可达16。
二、周期式轧管的变形过程
轧辊的工作段承担主要变形任务,它由三部分组成。
(1)压缩段α=60°~90°,这一段从开始咬入毛管到压缩延伸至轧
后尺寸,它负担着主要变形任务。
(2)压光段α=90°〜110°,这一段主要任务是对前几个工作循环中被压缩轧过的毛管进一步辗轧压光,消除波棱和楠圆度,使其达到成品的要求。
(3)出口段αc=10°〜20°,这一段不承担变形任务,只起保证顺利地使钢管脱离轧辊的作用。
工作段占轧辊断面的总包角为200°~210°,非工作段所占的轧辊断面的总包角保持在150°~160°范围内。
图2 周期式轧管机的变形过程
压缩段的工作过程如图2所示。
在压缩段开始进入工作状态之前(图2-a),轧槽表面几乎处于与毛管表面相平行的位置。
轧辊继续转动到C点与毛管接触开始咬入(图2-b)。
与之相对应的轧辊半径R c称之为咬人半径。
称R0为压缩开始半径,当R0转到上、下辊中心连线处,即垂直位置时,轧辊便对毛管施加类似锤击式的冲击压缩(图2-c)。
随着轧辊的继续转动,由
于轧辊直径的逐渐增加而将毛管辗薄(图2-d)。
在变形过程中,轧辊一方面把处于其下的毛管压缩变形,另一方面也将一部分未变形的金属挤向相反方向(图3)。
当轧辊最大直径部分转过垂直部位后,全部压缩过程即工作循环也随之结束。
图3 周期式轧管机压缩过程中轧件的变形
三、周期式轧管机常见的产品缺陷及其产生缺陷的原因
周期式轧管机常见的产品缺陷有壁厚不均、内折、外折、内外结疤、内麻坑、竹节等。
壁厚不均是周期式轧管机经常产生的缺陷,主要产生原因有:来料的壁厚不均;孔型错位;上下辊不平行;上下辊辊径差大,使其锻轧起点不一致;芯棒前后直径差大,造成钢管纵向壁厚不均等。
外折产生的原因是:孔型设计不合理,锻轧段孔型开口角小,金属变形过充满,在孔型的辊缝中造成的尖锐耳子,下次轧制时耳子被轧成外折;孔型错位;辊缝太大;喂人量过大;轧辊磨损严重等都可能产生外折缺陷。
内折产生的原因是:钢质内折,穿孔毛管已有内折。