精益生产推进计划表方案
精益生产TPS推进计划表方案

﹡完善设备异常发生处理流程和后续管理流程
﹡完善设备保养专家培养制度
﹡着手编制《故障词典》
﹡建立设备管理指标体系
﹡QCC活动开展 —10
-小组成立
-改善步骤明确
-现状分解与对策
﹡不合理List —3
质量管理 -标准质量动作
不良率降低15%
-不合理行为寻找活动
-改善方法的提案
﹡监控体制搭建 —2
-评比与激励
﹡布局调整计划与实施—3人天 -员工多技能交叉训练 -工装器具改进 -标准作业OJT -生产节拍控制器
二阶段: 精益示范
﹡快速换模(SMED)优化设备效 率—5人天 -作业要素分析 -内外变换拆解 -快速换模流程制定 -模具优化
﹡系统效率提升—10人天 -系统资源配置评估 -系统异常评估 -工段“孤岛”对策 -排场方式小批量优化
﹡检讨和持续改进—2人天 -作业效率管理 -不足点持续改进
﹡物品三定与目视化—2人天 ﹡制定目视管理基准—2人天 现场基础改善 ﹡建立班组活动园地—2人天 ﹡快速反应质量控制—2人天
3
5 换模时间压缩40%
生产交期压缩35%
现场评价80分以上
2 2 2 2
10 2
三阶段: 成果巩固
﹡改善提案活动导入—5人天
-工序能力时间测量 -现状Layout图 -工序能力平衡分析 -产品批量分析 -全品种作业转换时间测量 -最佳生产模式研讨
﹡设计新的线体布局方案—5人天 -确定生产节拍TT -提出布局草案 -计算标准人力 -标准作业组合 -操作平衡分析
量化指标
9月 10月 11月 12月 1月 2月 3月 4月 5月 6月 7月 8月
精益生产推行计划拆解 (时间段)
精益生产组织图

精益生产组织图
一、管理组织
班长班长班长班长班长班长班长班长班长班长班长班长班长班长班长班长班长班长班长班长全员全员全员全员全员全员全员全员全员全员全员全员全员全员全员全员全员全员全员全员
二、工作内容:
①、可视化控制
②、流动式生产
③、标准化生产
④、人类智慧的自働化
⑤、多能工化工序
⑥、少人化生产
⑦、平准化生产
⑧、改善
三、标准:
①、可视化控制:
A、进行5S生产
B、看板管理(循环及时性)
C、目视管理(安灯、防呆装置)
②、流动式生产
A、规程进行顺序
B、无间断生产流程
③、多能工化
A、员工的安排培训、评比
B、流程设置科学化
C、省力化、省人化
④、平准化生产
A、数量的平准化
B、种类的平准化
C、缩短准备时间
⑤、标准化生产
A、制定作业时间
B、制定作业步骤
C、作业程序中作业员所需物料数量
⑥、人类智慧的自働化
A、无缺点制造
B、省人工
C、缩短品检时间
⑦、改善
A、作业设备的改善
B、作业环境的改善
C、排除浪费
四、培训学习:
①、每月进行一次安规测试(20日以前)
②、每月进行一次运规测试(15日以前)
③、每月至少一次企业文化学习(利用学班)
④、每月至少一次“精益生产”学习(利用学班)
各专业授课人拿出培训内容及计划进展表,测试成绩纳入升级、升档参考.
五、推进计划:
六、监督考核:。
精益管理详细工作计划

一、前言为了进一步提高企业内部管理效率,降低成本,提升客户满意度,特制定本精益管理工作计划。
本计划将围绕以下几个方面展开:二、总体目标1. 提高生产效率,降低生产成本;2. 提升产品质量,减少不良品率;3. 优化工作流程,缩短生产周期;4. 提高员工满意度,激发团队凝聚力。
三、具体措施1. 精益生产培训(1)组织全体员工参加精益生产培训,提高员工对精益管理的认识;(2)邀请外部专家进行授课,讲解精益生产工具、方法及实施步骤;(3)鼓励员工积极参与培训,分享学习心得。
2. 5S现场管理(1)对生产现场进行整理、整顿、清扫、清洁、素养活动;(2)建立标准化的现场管理流程,规范员工操作;(3)定期检查5S执行情况,对未达标者进行整改。
3. 精益生产工具与方法(1)推广应用看板管理、快速换模、TPM等精益生产工具;(2)优化生产流程,缩短生产周期;(3)开展价值流分析,识别并消除浪费环节。
4. 质量管理(1)加强质量意识教育,提高员工质量意识;(2)实施全面质量管理,严格把控生产过程中的质量关;(3)对不合格品进行追溯,查找原因并采取措施防止再次发生。
5. 人力资源优化(1)加强员工培训,提高员工技能水平;(2)优化人力资源配置,合理调整人员结构;(3)建立激励机制,激发员工工作积极性。
6. 持续改进(1)设立精益管理推进小组,负责日常工作;(2)定期召开精益管理会议,总结经验,发现问题,持续改进;(3)设立精益管理奖励机制,对优秀团队和个人进行表彰。
四、时间安排1. 第一阶段(1-3个月):开展精益生产培训,实施5S现场管理,推广应用精益生产工具;2. 第二阶段(4-6个月):优化生产流程,加强质量管理,实施人力资源优化;3. 第三阶段(7-9个月):持续改进,总结经验,提升管理水平;4. 第四阶段(10-12个月):总结评估,持续优化,实现精益管理目标。
五、预期效果1. 生产效率提高20%以上;2. 成本降低15%以上;3. 质量不良品率降低30%以上;4. 员工满意度提高20%以上。
精益生产项目实施大计划表

项目区分 推进目的
推进工作事项
主要内容
7月 8月
1.全体人员掌 握精益理念 2.形成精益推 进运营及管理 启动阶段 机制 3.确定精益推 进目标 4.详细方案及 计划确定
1.精益理念宣贯
1)精益基础培训 2)精益氛围营造
1)精益推进组织建立
2.构筑精益推进运 2)各级推进组织职责制定
布局优化
1、效率提升 2、周期缩短
1、板簧车间
9)物流系统设计
布局优化
1、效率提升 2、周期缩短
10)方案细化及最终确认 11)设备搬迁方案及计划确定
12)线平衡及标准作业分析改善
13)设备改造及搬迁
14)新产线试运行,问题解决
15)产线改善效果确认
16)新产线运行管理机制及绩效体系建立
1)现状调查
营及管理模式 3)精益会议运营管理(周例会、月总结
4)精益推进管理制度制定
1)评价指标设计
3、精益推进目标 2)指标现状调查
制定
3)指标统计渠道梳理
4)制定总体目标及阶段性目标
4、项目实施方案 1)推进方案及计划初稿审核
及实施大计划确定 2)推进方案及计划修改定稿
1)5S推进方式与方法培训
2)5S推进委员会成立及相关制度建立
8)微缺陷的查找与改善
1)建立定期定量保全计划书板式
1、设备机能恢
2)培训定期定量保全计划书的编写方法
TPM初期 复
导入 2、设备可动率
提升
TPM初期 导入
1、设备机能恢 复 2、设备可动率 提升
2、专业保全启 动
1、班组基础管理
2、班组长标准作
1、现场基础管 业编制
精益生产推行行动计划及项目追踪表
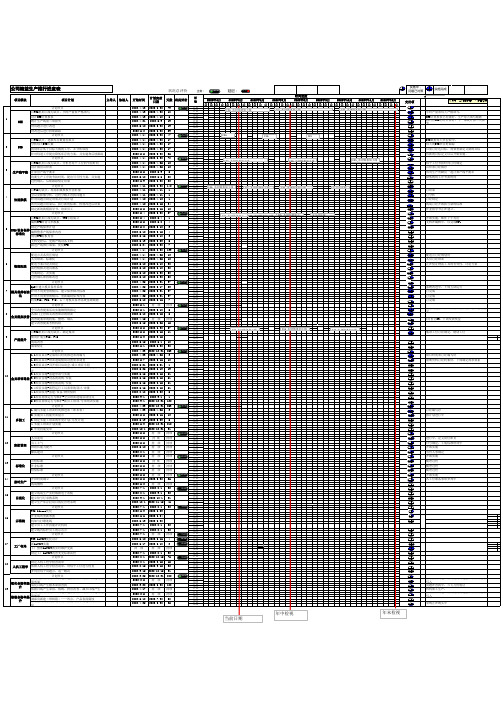
1周2周3周4周1周2周3周4周1周2周3周4周1周2周3周4周1周2周3周4周1周2周3周4周1周2周3周4周1周2周3周4周1周2周3周4周计划实绩`计划实绩计划实绩计划实绩计划实绩计划实绩计划实绩`计划实绩`计划实绩计划实绩计划实绩计划实绩`计划实绩计划实绩计划实绩计划实绩计划实绩计划实绩`计划实绩计划实绩计划实绩计划实绩计划实绩计划实绩`计划实绩计划实绩计划实绩计划实绩计划实绩计划实绩计划实绩`计划实绩计划实绩计划实绩计划实绩计划实绩计划实绩计划实绩计划实绩`计划实绩计划实绩计划实绩计划实绩计划实绩`计划实绩计划实绩计划实绩计划实绩计划实绩`计划实绩计划实绩计划实绩计划实绩计划实绩计划实绩计划实绩计划实绩计划实绩计划实绩计划实绩计划实绩计划实绩计划实绩计划实绩计划实绩计划实绩`计划实绩计划实绩计划实绩计划实绩计划实绩计划实绩计划实绩计划实绩计划实绩计划实绩计划实绩计划实绩计划实绩计划实绩计划实绩计划实绩计划实绩计划实绩计划实绩计划实绩计划实绩计划实绩计划实绩计划实绩计划实绩计划实绩计划实绩计划实绩计划实绩计划实绩计划实绩计划实绩计划实绩计划实绩计划实绩计划实绩计划`实绩计划实绩计划实绩计划计划计划实绩计划实绩计划实绩计划节点计划节点计划节点交付项计划节点计划节点计划节点计划节点计划节点计划节点计划节点计划节点问题在查找中,六七月份验证口号确定,工装标准培训中计划节点计划节点计划节点计划节点计划节点计划节点计划节点计划节点梳理过程梳理过程梳理过程等待人事确定进行中,定义岗位职责已完成各工位准备事项罗列中已经编写好按计划进行中系统改进中,下周五试运行已完成山积表已经做好协同生产贺瞬良一起计算产线平衡率降低铣切工序节拍时间配送点已经规划好已结束已经制定现场已经开始执行新的标准已分析作业指导书正在建立、开始实施,邮件下午发出文档在编辑中,以完成30%小时产量表每天严格填写,四月份OEE已经计算好,下一部统计前三大损失OEE计算报表已经做好,生产每天填写数据DTD数据每天在拉取中,每天的DTD在实时跟踪待新的目标定义以后开始实施、每个工位节拍时间已经确定目前已经达目标,需要重新定义新的目标正在验证物流工具的有效性,讨论方案开始实施开始实施人员已经培训项目时间表已经编写好前期资料已经收集好,下周确定需求要素瓶颈工位已经确定,铣切工位已完成内容确定好,下一步打印出来没,各个层级签字4月份已OK,下周发放奖金开始实施实施完成延迟:实施中,问题已对策正常:待机加工生产,持续分析问题,新发现的问题会在项目计划中写入持续分析问题,新发现的问题会在项目计划中写入采购正在购买中活动153231282持续100持续持续5035状况评价持续32323146323232持续42持续3276253312521231持续持续持续持续持续持续持续持续持续持续26155711183025331011961616161511227139121230305050372337377持续55持续2022/5/30天数791861919294717171726781212528221421113412271434352022/8/12022/8/1持 续2022/6/162022/6/18持 续2022/8/12022/10/152022/8/152022/9/152022/10/152022/12/31持 续2022/6/30持 续持 续2022/7/30持 续持 续持 续持 续持 续持 续持 续2022/5/30持 续2022/8/12022/9/12022/10/12022/11/152022/8/12022/6/232022/6/242022/6/302022/6/132022/8/152022/8/152022/8/152022/8/152022/8/222022/9/12022/12/312022/12/312022/4/252022/5/162022/5/232022/12/312022/12/31持 续持 续持 续2022/5/312022/5/312022/5/16持 续2022/5/102022/5/15持 续2022/5/252022/6/302022/5/152022/9/152022/6/12022/6/302022/12/312022/4/252022/5/162022/5/212022/5/302022/5/42022/5/82022/5/102022/5/152022/5/182022/5/232022/5/302022/8/302022/4/252022/4/252022/6/102022/6/102022/6/302022/6/302022/5/312022/5/172022/9/152022/3/252022/2/52022/3/202022/4/172022/2/52022/6/102022/4/25计划完成日期2022/6/302022/4/302022/4/182022/5/92022/5/302022/6/302022/5/302022/4/302022/4/302022/4/302022/5/302022/6/302022/4/252022/4/252022/5/92022/6/62022/6/302022/8/302022/4/112022/4/112022/4/122022/5/152022/5/162022/8/12022/9/12022/10/12022/7/12022/6/32022/6/62022/6/192022/7/12022/7/12022/7/12022/6/122022/6/17持 续2022/7/12022/8/12022/8/12022/8/152022/5/52022/5/192022/6/32022/12/12022/5/52022/5/52022/5/52022/5/122022/8/12022/5/52022/5/52022/5/52022/5/52022/5/52022/5/52022/6/22022/7/12022/6/32022/5/152022/6/12022/4/232022/4/232022/5/72022/5/212022/5/262022/6/162022/6/162022/6/162022/6/162022/8/182022/9/12022/9/12022/4/232022/4/232022/4/142022/5/122022/5/122022/5/122022/5/122022/4/252022/4/252022/4/252022/4/252022/5/102022/5/12022/5/12022/5/102022/4/152022/5/152022/5/52022/5/52022/6/92022/4/112022/4/112022/4/112022/4/122022/4/122022/5/52022/5/42022/5/42022/5/52022/5/82022/5/122022/5/162022/5/192022/5/242022/4/142022/4/14开始时间2022/4/132022/4/132022/4/132022/4/212022/5/122022/6/22022/4/142022/4/142022/4/142022/4/142022/5/52022/4/142022/4/142022/4/142022/5/52022/5/10协助人罗列出每个问题点,逐一解决氧化周报每周对TOP5问题点进行分析、对策,并追踪对策效果氧化白线产生根本原因查找依据白线产生原因,熔铸、挤出改善、减少白线产生涂装周报每周对TOP5问题点进行分析、对策,并追踪对策效果剥漆房新建(带烘箱)——凹点、产品表面腐蚀压缩空气改善为涂装专用,杜绝气压不稳造成的品质不良主导人检验标准开班时间确立现场稽核建立现场生产实时数据电子看板建立信号灯求救系统建立生产库存拉动目视化管理系统F26 Layout优化作业场所重新布置机加与打磨连线建立员工工作技能评比机制建立线内标杆员工的示范点F23 LAYOUT优化设计新LAYOUT实施工厂整体LAYOUT图实时维护更新制定工厂LAYOUT改善变更标准流程制定人机工程学检查清单依据人机工程学检查清单,对每个工位进行检查3.2项目实施-设备的请购/安装3.3项目实施-物资的请购/安装3.4项目实施-流程运行工具表单的设计/审批4.1项目收尾-基建/设备/物资验收5.1项目持续运行与维护-全员培训道场启动仪式5.2项目持续运行与维护-新员工培训/专项培训实施1.编写多能工培训时间推进表(即本表)2.实施员工技能资质盘点3.制定多能工培训的年度计划/月度计划4.多能工培训计划实施5.年度技能复审人员走动员工土气班组长能力提升梯队建设点检标准作业标准QAD中建立模具保养系统针对不同类型的模具,建立保养频次标准针对不同类型的模具,重新编制保养内容收集F16,F26,F45,后三角模具保养系统基础数据全员改善提案活动实施细则的拟定各部门主管相关改善知识的培训改善提案单的收集、整理、确认建立改善提案考核机制以F26机加工线为试点,确定瓶颈横向扩展至F16、F45现场改善成果验证1.1项目启动-完成项目时间推进表的编写1.2项目启动-培训道场模块设置需求调查1.3项目启动-召开项目启动会/成立项目小组2.项目计划-编写/报批培训流程设计及细分功能模块设计3.1项目实施-基建申请与实施氧化合格率提升涂装合格率提升项目计划以F26机加工线为试点,小时产量表严格填写设计OEE计算报表统计生产线前三项损失对问题点进行改进对改进后进行持续跟踪以F26试点,选取库存数量拉取点分析每天DTD天数找到库存低于目标天数的工序,并分析原因针对每道工序提出降低库存的方案,并实施和后续跟踪以F26机加工线为试点,分析出每个工位的节拍时间设计做出山积表计算出产线平衡率均衡生产工序的节拍时间,提出可行性方案,并实施过程确认,后续跟踪验证结果以F16为试点,现场拍摄换模作业影像会议室影像分析,过程分解并查找问题点针对问题点制定对策及行动计划所有问题点结束后,执行新的标准,检视改进后结果制定新的换模指导书,培训员工以F26机加工线为试点,TPM小组成立编辑TPM所需文档模板制定产线保养计划编辑整条产线保养内容规划TPM看板内容文档受控后,更换产线设备文档跟进产线推行成果,优化TPM配送点及备货区规划人员培训、标准化配送方案讨论及制定78910111213141516171819项目模块OEEDTD生产线平衡快速换模TPM/设备保养标准化物流配送模具保养标准化全员提案改善产能提升全员培训道场多能工班组管理标准化按时生产目视化示范线工厂布局人机工程学状况总评价时间进度2022年4月2022年5月2022年6月2022年7月2022年8月2022年9月2022年10月2022年11月2022年12月123456流程模拟及道具准备方案制定、及实施过程确认和持续改进:要改善公司精益生产推行进度表○:良好△:局部改善×:改善必要年中检视年末检视当前日期F26_水切饰条加工线F16_水切饰条加工线F45_水切饰条加工线F16_水切饰条加工线F45_水切饰条加工线F26_水切饰条加工线F26_水切饰条加工线F45_水切饰条加工线F16_水切饰条加工线F26_水切饰条加工宝马冲压线F16_水切饰条加工线F45_水切饰条加工宝马冲压线F16F45F26F16_水切饰条加工线F45_水切饰条加工线F26_水切饰条加工线。
精益生产流程表

⑩分包
裁片名称 床号 等资料 规格 件数
⑾粘合工序: 粘合工艺参数 技术含量高低 批量大小 设备、人员配备
⑿ 安排生产线
编制工艺 ②产前样
1、明确产品内容、顺序、时间、 设备 2、有利于生产线的平衡,便于大货 生产,可以提高产品质量和效率 1、“日程计划”控制整个服装 生产的日期 2、“部门计划表”分批量控制 生产件数日期 3“缝制管理版”控制个人及小组 的质量
⑥铺布
布面平整 布边对齐 减少拉力 保证面料方向性 格条对准 铺底放纸 记录原始辅料过程整理编号
1、 ①合同评审
避免同一件衣服出现色差 ⑨编号
2、 保证缝制加工中同规格衣片 的缝号,防止出现混号,保 正规格一致性。 (此工序适用梭织工厂) 证剪刀精度 ②各层衣片之间的误差 ③剪口、钉眼等位置的准确度 二控制剪切温度
⒀ 进度管理
⒁ 缝制过程的质量检验 (劣质产品不生产,劣质产品不出厂的理念)
⒂ 后 整 理 误工现象
①应急措施
②积极措施 ⒃成品检验 ⒄包装、检针 ⒅出货
加班 班长支援 停止别的工作来补救 外发加工或请求其他部门支援 保证出勤率 及早发现误工的倾向 查明误工的原因,明确责任所在 编制“误工报表”留作参考
精 益 生 产 流 程 图
返 回 ② 投料 面辅料入库 面料合格 辅料合格待用 松布(24小时以上) ④领布 ③检验 不合格 供应商
⑤ 排料
制定裁剪方案 根据大小不同的幅宽分别进行排料 掌握本批任务的件数和相应的规格 每件衣服的衣片样板数 技术部门下达的用料指标等要求 ①衣片的对称性②面料的方向性 本着节约用料的主要目的来做
附表:
缝
制
管
理
板
年 月 日
精益工作计划
精益工作计划精益工作计划1精益管理、顺利启动20__年,伴随着公司的新增项目,自动化改造推进项目加快,对各部门提出了更高的管理要求和挑战。
对此,公司年度制定了以精益管理为平台全面推动精益改善的培训项目,该项目于5月启动。
从精益生产理念、方法和体系、TPM的管理运用、精益管理的主要原则、识别浪费问题的方法等方面进行了学习。
理论学习后,各部门主任和梯队组成行动小组,就10个议题,开展了为期6个月的项目改善工作,共开展了30多次讨论,参与人员达60多人。
同时,为更好地为各精益改善行动小组提供帮助与支持,人事行政部于7月份结合行动教练的学习情况,选择了12名主任、骨干员工作为各部门行动催化师的人选,结合大家普遍反映改善行动中出现的问题,如“非专业人员参与度不高”、“目标发散”等给予解答,为各个精益小组改善活动提供支持。
经过半年的持续行动实践,年度精益管理改善行动项目进入收官阶段,为检验各个行动小组的学习效果、巩固精益改善成果,提炼和推广改善经验,我们于11月24日开展了精益改善项目验收评估总结。
精益项目、全体研讨此次评估邀请管理层及各部门经理作为评委,从“目标的设定”、“现状的分析”、“行动方案的制定”、“项目目标的达成”等方面进行评估,最终、“报销单据合格率改善小组”荣获一等奖、“纸箱到货率改善小组”荣获二等奖、“小包装皱标改善小组”荣获三等奖,同时共有3个行动小组荣获行动奖。
前进14名?、勇夺冠军其中,“报销单据合格率改善小组”三个月内将报销单据合格率由70%提升至90%,集团排名从27名提升到13名,不仅保障了工厂共享报销的及时性,也提升了工厂人员对报销工作的满意度。
“纸箱到货率改善小组”达成了纸箱按计划到货及时率从83%提高至97%目标,节省近6万元成本。
“小包装皱标改善小组”将产品皱标现象从0.36%降到0.18%,为产品的营销提供了良好的支持。
精彩答辩、精辟点评在验收评比过程中,评委对各个精益改善项目进行了深入点评,从改善项目的价值点,到后期实现效果的意义,进行了直接提问和到位点评,并鼓励大家持续改进,稳步提高,形成固定的运转机制,巩固改善项目成果。
精益生产规划方案
采用流畅和连续的动作。 工作地和座椅的高度最好布置得可以交替坐和站立着工作,还
应具备适宜的光线,使操作者尽可能舒适。
三角形原理
物料(或工具)放置点、产品组装点、 操作者手的位置形成的三角形的边长 越小越好。
3、设定时间标准方法
现 场
3.不找借口,从否定现有的做法开始
改 4.不求完美,马上去做
善 的
5.立即改正错误
基 6.从不花钱的项目开始改善
本 原
7.遇难而进,凡事总有办法
则 8.问5次”为什么?”,找出根本原因
9.众人拾柴火焰高
10.改善无止境
用看不惯的眼光找出问题项目
➢ 在生产上属于瓶颈(或问题最多)的工作 ➢ 占大量时间或人工的工作 ➢ 反复性的工作 ➢ 消耗大量材料的工作 ➢ 看起来不合理的工作 ➢ 放置不当或搬运不便的工作
自我问答:为何要等待?
改善:制品别生产(U 字型) 愚巧化 自恸化 平准化生产 什么都不给做 对浪费的认知
造成等待浪费的原因
造成等待浪费的原因:
➢ 生产线的品种切换 ➢ 每天的工作量变动 ➢ 时常因缺料而使机器闲置 ➢ 上游工序延误导致下流工序闲置 ➢ 机器设备时常发生故障 ➢ 生产线未能取得平衡 ➢ 存在劳逸不均的现象
5、库存的浪费
内容:材料、零件、加工品的停滞,不单只有仓库,车间内的半成品 也是。导致交期的长期化,,空间的使用浪费,重复统计的浪费 搬运、检查的产生,周转资金的增加。
自我问答:为何会有库存?是否有更好的改善措施?
改善:库存的意识改革 U 字型设备的配置 平准化生产 单一化 生产整流化 看板的彻底实行
按照过去的管理理念,人 们认为库存虽然是不好的 东西,但却是必要的。精 益生产的观点认为,库存 是没有必要的,甚至认为 库存是万恶之源。
精益生产文件计划表
JQEOS-RZ03-B-001
JQEOS-RZ03-B-002 JQEOS-RZ03-B-003
工时控制与考勤管理 制度 干部K1&K2工资制度 非计件人员薪资制度
JQEOS-RZ03-B-004 提案改善制度
JQEOS-RZ03-B-005 优秀员工评选办法
JQEOS-RZ03-B-006 员工申述管理办法
JQEOS-PB01-B-002
JQEOS-PB01-B-003
JQEOS-PB01-B-004 JQEOS-PB01-B-005 JQEOS-PB01-B-006
JQEOS-PB01-B-007
JQEOS-PB01-B-008 JQEOS-PB01-B-009
JQEOS-PB01-B-010
JQEOS-PB02-B-001
JQEOS-ZZ01-B-002 JQEOS-ZZ01-B-003 JQEOS-ZZ01-B-004 JQEOS-ZZ01-B-005
JQEOS-ZZ01-B-006
JQEOS-SG01-B-001 JQEOS-SG01-B-002 JQEOS-SG01-B-003 JQEOS-PB01-B-001
50
51
52
53
54
总务课
55
56 57
58
59 60
61
62
63
64 65
66
67 68 69
70
71 72 73 74
制造课
75
76
77
制造课
78
79
80
81
生管课
82
83
84
85
86
87 88
生产部
89
精益生产年度工作计划范文
精益生产年度工作计划范文第一章:引言1.1 背景介绍精益生产是一种企业管理方法,旨在通过消除浪费、优化流程、提高生产效率和质量,实现企业的可持续发展。
本文将为您介绍精益生产年度工作计划的编写步骤和内容要点,帮助您制定出科学合理、有效可行的工作计划。
1.2 工作计划编写的目的工作计划是指按照一定的时间顺序安排和组织工作内容的详细安排表,它明确了年度目标、计划内容、工作重点和时间安排等,有助于组织开展工作并实现预期目标。
第二章:工作计划编写的基本步骤2.1 年度目标设定2.1.1 分析企业现状首先要了解企业的当前状况,包括生产状况、市场需求、竞争对手等,为目标设定提供依据。
2.1.2 确定年度目标根据企业现状和未来发展方向,确定年度目标。
目标要具体、可测量、可实施,并与企业战略、经验和资源相适应。
2.2 决定工作内容2.2.1 分解目标将年度目标分解为具体的工作任务,明确每个任务的目的、内容和关键要点。
2.2.2 制定工作计划根据目标分解的结果,确定具体的工作计划,包括工作内容、责任人、工作流程、时间安排和预算等。
2.3 评估资源需求2.3.1 评估人力资源根据工作计划确定的工作内容和工作量评估人力资源需求,包括人数、专业能力、培训需求等。
2.3.2 评估物质资源评估工作过程中需要使用的各项物质资源的需求,如原材料、设备、工具等。
2.3.3 评估财务资源评估工作计划实施过程中需要使用的财务资源,如预算、资金等。
2.4 制定时间安排2.4.1 制定时间节点将工作计划中的各项任务按照时间先后顺序进行排列,确定每个任务的开始时间和结束时间。
2.4.2 确定关键节点确定工作计划中的关键节点,即重要的工作和评估的时间节点,有助于掌握工作进度和风险。
第三章:工作计划内容要点3.1 目标和策略明确工作计划的目标和策略,包括年度目标、实现路径、关键成功因素等。
3.2 工作计划和资源需求明确工作计划中的工作内容、任务分解、工作流程和资源需求,包括人力资源、物质资源和财务资源等。
- 1、下载文档前请自行甄别文档内容的完整性,平台不提供额外的编辑、内容补充、找答案等附加服务。
- 2、"仅部分预览"的文档,不可在线预览部分如存在完整性等问题,可反馈申请退款(可完整预览的文档不适用该条件!)。
- 3、如文档侵犯您的权益,请联系客服反馈,我们会尽快为您处理(人工客服工作时间:9:00-18:30)。
﹡快速换模(SMED)优化设备效 率—5人天 -作业要素分析 -内外变换拆解 -快速换模流程制定 -模具优化 换模时 间压缩 40%
5
二阶段: 精益示范
﹡系统效率提升—10人天 -系统资源配置评估 -系统异常评估 -工段“孤岛”对策 -排场方式小批量优化 生产交 期压缩 35%
﹡检讨和持续改进—2人天 -作业效率管理 -不足点持续改进 ﹡物品三定与目视化—2人天 ﹡制定目视管理基准—2人天 现场基础 ﹡建立班组活动园地—2人天 改善 ﹡快速反应质量控制—2人天 ﹡改善提案活动导入—5人天 TPM0、1 Step导入—15 5 15 现场评 价80分 以上 2 2 2 2
﹡TPM样板区域[针对改善设备/Line] 标准制定 ﹡对全员说明基本活动方法,带动实施1次 ﹡建立自主管理机制,实施分级 点检制度 ﹡TPM活动中[含生产中故障发生] 问题点整理,分析 ﹡利用科学的方法树立改善对策 设备管理 机制 ﹡设备备品管理分析,合理库 存,保证供给 ﹡完善设备异常发生处理流程和 后续管理流程 ﹡完善设备保养专家培养制度 ﹡着手编制《故障词典》 ﹡建立设备管理指标体系 ﹡QCC活动开展 —10 -小组成立 -改善步骤明确 -现状分解与对策 ﹡不合理List —3 质量管理 -标准质量动作 -不合理行为寻找活动 -改善方法的提案 ﹡监控体制搭建 -评比与激励 -现有监控方法的优化 —2 2 不良率 降低15% 3 10
减少设 备异常 30%,减 少对生 产效率 影响
﹡完善“标准作业管理” 标准化 ﹡编写示范线《现场管理基准》 ﹡编写《精益指标体系》 三阶段: 成果巩固 项目总结 ﹡制订后期拓展计划 ﹡项目评价和结束会议 JIT&价值流图 5S与目视化管理 QC基本工具应用 培训 (计划 内) 班组管理技能提升-TWI 标准作业与作业标准 基础工业工程-IE 2 全面生产维护-TPM 1 1 1 ﹡完成项目总结报告 ﹡整理主要输出文件
精益生产 推行计划方案 9月 10月 11月 12月1月 2月 第一阶段 0.5 第二阶段
阶段
项目 倡导者培训
子项目 ﹡精益生产基本理念 ﹡精益变革过程中管控注意事项 ﹡精益办公室设立
量化指标
0.5 项目定义 ﹡项目团队组建 ﹡项目启动会议 ﹡课题现状数据统计方法指导 现状评估 ﹡课题管控表格填写 一阶段: 实施准备 ﹡课题影响因素评估 ﹡核心指标设立 目标设定 ﹡指标基线测定 ﹡初级及革新目标设定 ﹡项目进度目视管理板 项目监控 ﹡精益月报及例会管理 绩效管控 ﹡精益改善绩效管理办法制定 ﹡组装效率优化—3人天 -工序能力时间测量 -现状Layout图 -工序能力平衡分析 -产品批量分析 -全品种作业转换时间测量 ### 3 1 1 0.5 0.5 建立3人 0.5 或3人以 上的专 0.5 职推进 组织 0.5 0.5 0.5
3月 4月 5月 6月 7月 8月 第二阶段 第三阶段
顾问师
1
3
5
10
2
15
1 1 1
2
Hale Waihona Puke -最佳生产模式研讨﹡设计新的线体布局方案—5人天 -确定生产节拍TT -提出布局草案 -计算标准人力 -标准作业组合 -操作平衡分析 -员工多技能评估矩阵 -工位器具标准化 -标准手持设定 -物流供应方案 -方案约束事项检讨及对策 -最佳组装生产模式确定 生产效 率提升 30%
5
效率优化 ﹡布局调整计划与实施—3人天 -员工多技能交叉训练 -工装器具改进 -标准作业OJT -生产节拍控制器 3