起重机啃轨分析及处理
桥式起重机车轮啃轨故障的分析及修理方法

桥式起重机车轮啃轨故障的分析及修理方法桥式起重机是一种常用的起重设备,用于搬运和吊装重物。
由于长期使用和工作环境等原因,桥式起重机的车轮可能会出现啃轨故障,导致起重机不能正常行走。
本文将对桥式起重机车轮啃轨故障进行分析,并提出相应的修理方法。
一、故障分析1.车轮啃轨原因分析:(1)轮轨匹配不合理:车辆负载过大,超出了轮轨的承载能力,导致车轮啃轨。
(2)轨道偏斜:轨道的安装不平整,或者在使用过程中由于车轮偏移或震动等因素,使得轨道发生偏斜,导致车轮啃轨。
(3)车轮磨损:车轮长期使用,磨损严重,无法与轨道保持良好的接触,造成车轮啃轨。
2.车轮啃轨故障的表现:(1)车轮和轨道产生共振现象,发出异常声音。
(2)车辆行驶不稳定,左右晃动明显。
(3)车轮与轨道摩擦过大,可能损坏轮轨甚至造成起重机翻车。
二、修理方法1.车轮修理方法:(1)检查车轮磨损情况,如果车轮磨损严重,需要更换新的车轮。
(2)对于磨损较轻的车轮,可以通过磨削车轮轮面,恢复车轮的原有形状和尺寸。
(3)对于轮轨匹配不合理造成的啃轨问题,可以采用车轮加宽、加厚或更换容量更大的车轮解决。
2.轨道修理方法:(1)检查轨道的安装情况,确保轨道平整、牢固。
(2)如发现轨道偏斜,可以采用调整轨道位置或加装垫片的方式进行修复。
(3)对于老化或严重损坏的轨道,需要更换新的轨道。
3.预防措施:(1)定期检查车轮和轨道的磨损情况,及时更换磨损严重的部件。
(2)调整车轮间距,保证车轮与轨道的匹配度。
(3)加强轨道的维护保养工作,确保轨道平整、清洁。
总结:桥式起重机车轮啃轨故障对起重机的正常行走起到很大的影响,并且可能带来严重的安全隐患。
对于车轮啃轨故障,应该及时进行分析,并采取相应的修理方法。
通过定期检查和维护工作,可以预防车轮啃轨故障的发生,确保起重机的安全和正常运行。
桥式起重机啃轨原因分析及解决方式【范本模板】

桥式起重机啃轨原因分析及解决方式起重机是一种常用设备,不仅在陆地上我们可以见到各种类型的起重机,被广泛应用于冶金、矿山、机械制造加工等行业。
随着企业的使用频率越来越高,在正常使用保养中, 桥式起重机会经常出现啃轨的现象。
下文我们将对这一现象进行分析。
1啃轨的定义啃轨是指在起重机大车或小车运行过程中,大车或者小车的车轮轮缘与轨道侧面应该保持一定间隙,但由于车轮轮缘与轨道侧面接触产生水平侧向推力,引起轮缘与轨道的摩擦及磨损,通常称为啃轨。
2啃轨的危害①。
降低车轮的使用寿命由于起重机的车轮的材料一般是使用铸钢,经过淬火等工序之后,一般可以使用10年以上。
但是由于啃轨的原因,车轮的寿命会大大减小,这会严重影响生产安全和生产效率.②.磨损轨道啃轨情况的发生,车轮和轨道由于是刚性接触,会在一定程度上加剧轨道的磨损,随着磨损量的增大,起重机大小车的稳定性减小,严重影响安全。
③.脱轨危险当车轮或轨道磨损严重时,车轮可能会爬到轨道顶面,致使大车或小车脱轨,引发安全事故。
④影响厂房的结构用于起重机啃轨时会发出噪声、引起震动,而且起重机运行时会产生水平侧向力,使起重机产生不正常的振动,从而是厂房建构产生振动,受到一定程度的损害。
3啃轨的判定及表现形式①.在起重机轨道的侧面有很明显摩擦很光亮的平面,导轨上有很锋利的棱角,轨道顶面有雪白色的亮斑.②。
桥式起重机行驶时,轮缘与轨道之间的间隙有明显的变大或者变小现象。
③.桥式起重机在运行中,车体产生歪斜,车轮走偏.④.大车运行时会产生刺耳啃轨声,啃轨严重时,大车不仅会产生刺耳的噪声,而且会引起大车轻微的跳动,这也就是我们通常说的爬轨现象。
4 啃轨原因分析引起起重机啃轨的原因很多,但主要原因有这两个方面:一是轨道变形;二是起重机工业制造技术上存在缺陷以及安装者安装能力及技术不足。
引起轨道形变的原因有以下几个方面:①。
由于起重机的大车和小车经常在轨道上来回行走, 轨道上承受的这种压力在外部表现为间歇性的,而在轨道内的应力表现形式为交变应力, 这来来回回反复的作用,就会使轨道产生变形或位移.②。
啃轨的原因分析与处理方法
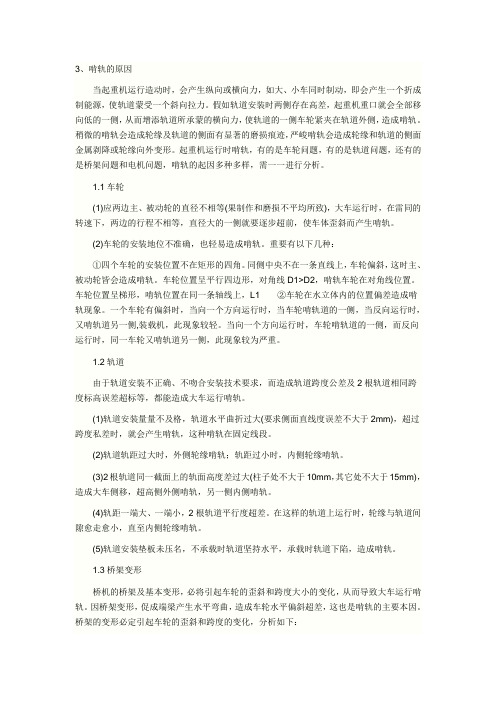
3、啃轨的原因当起重机运行造动时,会产生纵向或横向力,如大、小车同时制动,即会产生一个折成制能源,使轨道蒙受一个斜向拉力。
假如轨道安装时两侧存在高差,起重机重口就会全部移向低的一侧,从而增添轨道所承蒙的横向力,使轨道的一侧车轮紧夹在轨道外侧,造成啃轨。
稍微的啃轨会造成轮缘及轨道的侧面有显著的磨损痕迹,严峻啃轨会造成轮缘和轨道的侧面金属剥降或轮缘向外变形。
起重机运行时啃轨,有的是车轮问题,有的是轨道问题,还有的是桥架问题和电机问题,啃轨的起因多种多样,需一一进行分析。
1.1车轮(1)应两边主、被动轮的直径不相等(果制作和磨损不平均所致),大车运行时,在雷同的转速下,两边的行程不相等,直径大的一侧就要逐步超前,使车体歪斜而产生啃轨。
(2)车轮的安装地位不准确,也轻易造成啃轨。
重要有以下几种:①四个车轮的安装位置不在矩形的四角。
同侧中央不在一条直线上,车轮偏斜,这时主、被动轮皆会造成啃轨。
车轮位置呈平行四边形,对角线D1>D2,啃轨车轮在对角线位置。
车轮位置呈梯形,啃轨位置在同一条轴线上,L1②车轮在水立体内的位置偏差造成啃轨现象。
一个车轮有偏斜时,当向一个方向运行时,当车轮啃轨道的一侧,当反向运行时,又啃轨道另一侧,装载机,此现象较轻。
当向一个方向运行时,车轮啃轨道的一侧,而反向运行时,同一车轮又啃轨道另一侧,此现象较为严重。
1.2轨道由于轨道安装不正确、不吻合安装技术要求,而造成轨道跨度公差及2根轨道相同跨度标高误差超标等,都能造成大车运行啃轨。
(1)轨道安装量量不及格,轨道水平曲折过大(要求侧面直线度误差不大于2mm),超过跨度私差时,就会产生啃轨,这种啃轨在固定线段。
(2)轨道轨距过大时,外侧轮缘啃轨;轨距过小时,内侧轮缘啃轨。
(3)2根轨道同一截面上的轨面高度差过大(柱子处不大于10mm,其它处不大于15mm),造成大车侧移,超高侧外侧啃轨,另一侧内侧啃轨。
(4)轨距一端大、一端小,2根轨道平行度超差。
起重机车轮啃轨原因分析
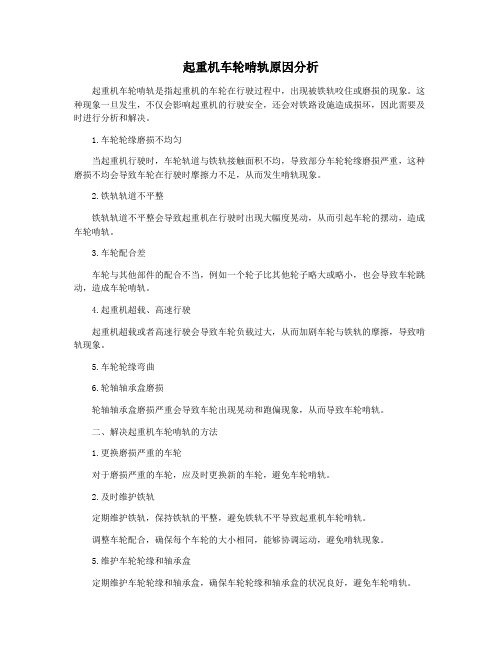
起重机车轮啃轨原因分析
起重机车轮啃轨是指起重机的车轮在行驶过程中,出现被铁轨咬住或磨损的现象。
这种现象一旦发生,不仅会影响起重机的行驶安全,还会对铁路设施造成损坏,因此需要及时进行分析和解决。
1.车轮轮缘磨损不均匀
当起重机行驶时,车轮轨道与铁轨接触面积不均,导致部分车轮轮缘磨损严重,这种磨损不均会导致车轮在行驶时摩擦力不足,从而发生啃轨现象。
2.铁轨轨道不平整
铁轨轨道不平整会导致起重机在行驶时出现大幅度晃动,从而引起车轮的摆动,造成车轮啃轨。
3.车轮配合差
车轮与其他部件的配合不当,例如一个轮子比其他轮子略大或略小,也会导致车轮跳动,造成车轮啃轨。
4.起重机超载、高速行驶
起重机超载或者高速行驶会导致车轮负载过大,从而加剧车轮与铁轨的摩擦,导致啃轨现象。
5.车轮轮缘弯曲
6.轮轴轴承盒磨损
轮轴轴承盒磨损严重会导致车轮出现晃动和跑偏现象,从而导致车轮啃轨。
二、解决起重机车轮啃轨的方法
1.更换磨损严重的车轮
对于磨损严重的车轮,应及时更换新的车轮,避免车轮啃轨。
2.及时维护铁轨
定期维护铁轨,保持铁轨的平整,避免铁轨不平导致起重机车轮啃轨。
调整车轮配合,确保每个车轮的大小相同,能够协调运动,避免啃轨现象。
5.维护车轮轮缘和轴承盒
定期维护车轮轮缘和轴承盒,确保车轮轮缘和轴承盒的状况良好,避免车轮啃轨。
综上所述,起重机车轮啃轨是由多种因素引起的,需要对车轮、铁轨、车轮轮缘、轴承盒等进行维护和调整,才能有效避免此类现象的发生。
桥式起重机车轮啃轨修理

桥式起重机车轮啃轨修理啃轨一般是由于车轮的歪斜及车轮的横向滑动产生的。
啃轨将使车轮与钢轨的寿命降低、运行阻力增大,严重时可引发电动机烧坏或扭断传动轴事故;啃轨还可造成脱轨而影响厂房使用寿命。
根据作者经验,现对车轮啃轨的原因及修理方法加以探讨。
一、啃轨的原因1.左右轮传动不同步由于分别驱动的两套传动机构不同步,使车体走斜而啃轨。
这种啃轨的特征是起重机在启动及制动时,车体扭摆并且啃轨。
2.轨道偏差过大由于轨道偏差过大而造成啃轨的特征是,起重机在某些地段产生啃轨。
如果轨道跨距和轨道水平直线性差,在起重机跨距不变的前提下,由于轮缘与轨道侧面间隙减少将造成啃轨;若两条轨道相对标高偏差过大或同一侧两根相邻的轨道顶面不在同一平面内,都有可能引起啃轨。
3.结构变形大、小车的车轮是分别固定在桥架的端梁和小车架的侧梁上。
所以当桥架或小车架发生变形时,必将引起车轮的歪斜和跨度的变化。
因此而引起的啃轨,多发生于大车桥架,现分别加以说明。
(1)因结构变形造成两个车轮的跨度变化或四个车轮的对角线长度超差造成运行啃轨。
(2)因结构变形造成车轮垂直偏斜超差而引起啃轨。
当车轮安装时超出垂直偏斜公差时将可能引起啃轨。
(3)因桥架结构变形促使端梁产生水平弯曲,造成车轮水平偏斜超差。
车轮水平偏斜引起的啃轨,不管是主动轮还是被动轮都会有相同的作用。
但是,若同一端的两个车轮或同一侧的两个车轮,其水平偏斜方向相反,则有明显的相互中和抵消作用,这一点在车轮的修理调整时应加以利用。
4.锥形踏面车轮装配差错采用集中驱动的桥式起重机,为了自行调整大车两端的相互超前或滞后,避免运行啃轨,大车运行机构的主动车轮踏面均采用1:10的锥度。
这种有锥度车轮的安装是有一定方向的,两个车轮的锥度方向应相反。
若装配方向错误,则超前的车轮就会更超前,滞后的更滞后,啃轨将越来越严重,所以有锥度的车轮在安装时必须注意不能装错。
二、啃轨的检查方法1.起重机在运行过程中,在很短的一段距离内,车轮轮缘与钢轨之间的间隙发生明显改变,则起重机会啃轨。
桥式起重机啃轨原因分析及解决方式
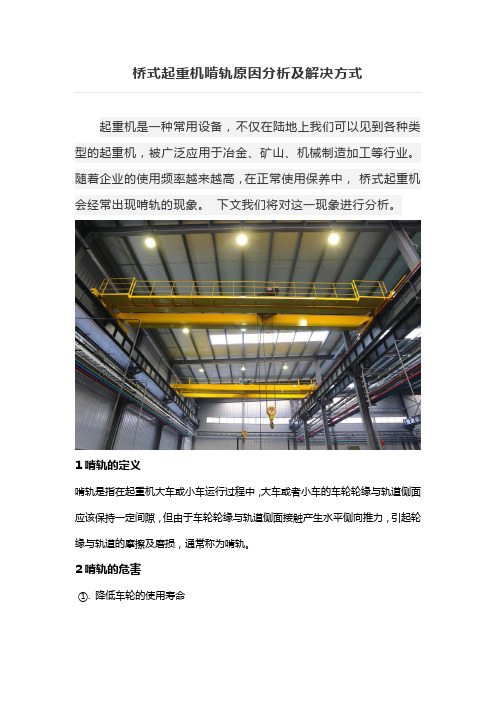
桥式起重机啃轨原因分析及解决方式起重机是一种常用设备,不仅在陆地上我们可以见到各种类型的起重机,被广泛应用于冶金、矿山、机械制造加工等行业。
随着企业的使用频率越来越高,在正常使用保养中,桥式起重机会经常出现啃轨的现象。
下文我们将对这一现象进行分析。
1啃轨的定义啃轨是指在起重机大车或小车运行过程中,大车或者小车的车轮轮缘与轨道侧面应该保持一定间隙,但由于车轮轮缘与轨道侧面接触产生水平侧向推力,引起轮缘与轨道的摩擦及磨损,通常称为啃轨。
2啃轨的危害①. 降低车轮的使用寿命由于起重机的车轮的材料一般是使用铸钢,经过淬火等工序之后,一般可以使用10年以上。
但是由于啃轨的原因,车轮的寿命会大大减小,这会严重影响生产安全和生产效率。
②.磨损轨道啃轨情况的发生,车轮和轨道由于是刚性接触,会在一定程度上加剧轨道的磨损,随着磨损量的增大,起重机大小车的稳定性减小,严重影响安全。
③.脱轨危险当车轮或轨道磨损严重时,车轮可能会爬到轨道顶面,致使大车或小车脱轨,引发安全事故。
④影响厂房的结构用于起重机啃轨时会发出噪声、引起震动,而且起重机运行时会产生水平侧向力,使起重机产生不正常的振动,从而是厂房建构产生振动,受到一定程度的损害。
3啃轨的判定及表现形式①.在起重机轨道的侧面有很明显摩擦很光亮的平面,导轨上有很锋利的棱角,轨道顶面有雪白色的亮斑。
②.桥式起重机行驶时,轮缘与轨道之间的间隙有明显的变大或者变小现象。
③.桥式起重机在运行中,车体产生歪斜,车轮走偏。
④.大车运行时会产生刺耳啃轨声,啃轨严重时,大车不仅会产生刺耳的噪声,而且会引起大车轻微的跳动,这也就是我们通常说的爬轨现象。
4 啃轨原因分析引起起重机啃轨的原因很多,但主要原因有这两个方面:一是轨道变形;二是起重机工业制造技术上存在缺陷以及安装者安装能力及技术不足。
引起轨道形变的原因有以下几个方面:①.由于起重机的大车和小车经常在轨道上来回行走,轨道上承受的这种压力在外部表现为间歇性的,而在轨道内的应力表现形式为交变应力,这来来回回反复的作用,就会使轨道产生变形或位移。
桥式起重机车轮啃轨现象、原因及改进措施的分析
桥式起重机车轮啃轨现象、原因及改进措施的分析1前言桥式起重机被广泛应用于冶金、矿山、机械制造加工等行业,对于企业的安全生产有着举足轻重的作用。
随着设备投入使用的延长,设备有着不同程度的磨损。
在正常使用及维护中,桥式起重机经常出现大车啃轨的现象,现针对这一现象进行简要分析。
2啃轨的现象(1)桥式起重机长期在线运行,轨道侧面上出现一条明显的亮迹,严重时亮迹上有毛刺;车轮轮缘内侧有亮斑并有毛刺;起重机行驶时,短距离内轮缘与轨道间隙有明显改变,特别是启动与制动时车体走偏,扭摆,啃轨特别严重时发出较响亮的吭吭声。
(2)车轮啃轨是起重机非常严重的故障,轻者会增大运行阻力,缩短车轮寿命,加快轨道磨损,恶化厂房受载状况,重者造车车轮爬轨、脱轨从而酿成重大设备人身事故。
所以,桥式起重机发生车轮啃轨时必须及时调整车轮。
(3)桥式起重机在正常运行时,大车车轮踏面宽度比轨道头宽度大30~40mm,车轮在踏面中间运行,车轮轮缘与轨道之间保持一定的间隙。
但是由于某些原因使车轮不在踏面中间运行,造成轮缘与轨道一侧强行接触,造成车轮啃道。
3啃轨的原因造成车轮啃轨的原因很多,其中有制造工艺问题,也有设计、安装、使用问题,往往是多方面因素综合作用的结果。
现对造成啃轨的几个主要原因进行分析:3.1车轮因素3.1.1 同侧的主动轮直径不等造成啃轨大车运行时,在相同的转速下,两边车轮的行程不等,累积误差过大时造成啃轨。
表现出大车在左右运行过程中啃轨现象时有时无地断续,是比较轻的啃轨现象。
3.1.2 车轮的安装位置不当主要是主被动车轮轨距误差过大。
为安装精度低下造成的啃轨现象。
3.1.3 车轮的安装精度不当主要是主被动车轮垂直和平行精度误差过大。
车轮垂直度精度误差造成车痕不重叠,各行其道。
车轮平行度精度误差造成大车沿对角线斜向行走或划圆弧轨迹行走。
3.1.4 车轮安装的松紧程度不当主要是角轴承箱的安装中心与制造中心不重合,一般是安装中心距偏大,造成轴承间隙过大,影响定位或传力;轴承严重磨损的时候,轴承处的摩擦力过大,啃轨现象就偏重。
起重机啃轨原因及对策分析
起重机啃轨原因及对策分析摘要:起重机在运行一段时间后,会产生不同程度的损坏,啃轨的现象也是常常发生。
为了避免起重机出现啃轨的现象,现在从啃轨的危害出发,对起重机在运行时出现的啃轨原因进行分析,并给出相应的解决对策。
关键字:起重机啃轨原因对策分析起重机正常运行的时候,车轮踏面的宽度会比轨道的宽度大约30-40毫米,车轮在踏面中间工作,车轮边缘和轨道之间要保持一定的间隔。
但因为某些缘由让车轮不在踏面中间工作,使车轮边缘和轨道之间的间隔越来越小,最后出现车轮啃轨的现场发生。
一、啃轨定义所谓的啃轨,是说在起重机大车和小车的工作过程中,车轮边缘和轨道侧边接触造成水平侧边助力,导致车轮边缘和道轨之间产生一定程度的摩擦和损失,这种现象我们就称之为啃轨。
起重机啃轨可能出现的现象有多种多样,包括在轨道边缘有明显的摩擦迹象;摩擦产生的铁屑掉在轨道上;起重机工作过程中短距离内车轮边缘和轨道之间的间隙会慢慢发生变化;起重机在工作时车身会有歪斜情况发生;车轮会出现走偏现象;大车工作时会出现很响的啃轨声;啃轨严重的话会可能还会出现爬轨现象。
啃轨的现象不是单一的,有时会多个车轮同时啃轨,有时则单个车轮啃轨;有时是双向啃轨,有时则是单向的。
二、啃轨现象轻度啃轨,及时查修:控制整个起重机工作的凸轮控制器一档不开启,二档开启;不制动的情况下停车惯性运行距离小;车轮边缘有磨损现象,但没有掉屑和卷边情况发生;车轮工作时间为2-3年。
重度啃轨,尽快查修:控制整个起重机工作的凸轮控制器一档不开启,二档开启缓慢;不制动的情况下停车没有惯性动作;车轮边缘磨损比较严重,既有掉屑也有卷边情况发生;车轮工作时间为半年到一年。
严重啃轨,停运查修:控制整个起重机工作的凸轮控制器二档都不能开启;起重机工作时车轮边缘和轨道之间的摩擦声音很大,严重时车轮会爬上轨顶;车轮工作时间不到半年。
三、啃轨危害1、啃轨对桥结构的危害:起重机在工作时出现啃轨现象时会出现水平侧向力,这种力会使得轨道发生横向移位,导致设备的振动,进而导致固定的轨道被破坏出现螺丝松动,最终导致整个起重机的振动。
桥式起重机啃轨原因分析与解决措施
桥式起重机啃轨的综合分析与解决措施一、前言桥式起重机俗称“行车”、“天车”,被广泛应用于工业企业、港口车站、仓库料场、水电站、冶金制造等行业。
以电炉炼钢生产为例,废钢的兑料、钢水的吊运、电炉炼钢设备的安装与维修都是由行车来完成的,所以行车的正常运行是生产进行的唯一保障。
“啃轨”又称啃道、咬道,是天车在运行过程中极其常见的现象。
所谓啃轨是指行车的大车或小车在运行过程中车轮轮缘与轨道侧面严重挤压,产生侧向推力,并引起轮缘与轨道的摩擦及磨损的现象。
二、啃轨现象的判断方法天车正常运行时,轮缘与轨道侧面之间是保持一定的间隙(20~30mm),啃轨是轮缘与轨道相对歪斜运行到一定程度后产生的结果,同时也是车体走斜的过程。
检查行车是否啃轨,可以根据以下现象进行判断:1、行车啃轨,轨道侧面经常会出现一条明亮的痕迹,严重时轨道一侧存在台阶。
2、行车车轮的内侧有明显的磨损痕迹,并会伴有毛刺及铁屑。
3、行车在行走的过程中会发出嘶嘶的声音,并伴随着钢轨左右扭摆。
4、行车在行走过程中,尤其是启动与制动时车体是否存在跑偏与扭摆。
5、行车在行驶时,在短距离内轮缘与轨道间隙有明显变化。
三、啃轨对设备与生产的影响1、加剧行车轨道磨损行车啃轨运行会导致轨道磨损成台阶状,当支撑车轮的轨道翼缘宽度磨损量达到原尺寸的5%时,便给与报废,大大减小了轨道的使用寿命。
2、缩短车轮组的使用寿命如果车轮组安装与使用正常,经过淬火与调质处理的车轮其使用寿命约为10年左右。
而啃轨严重的车轮,其使用寿命只有1到2年,甚至几个月的时间。
3、增加传动机构的运行阻力测验表明,当天车在严重啃轨的条件下运行时,其传动机构所受到的运行阻力比正常运行时增大 1.5~3.5倍。
由于运行阻力增加,使驱动电机与传动机构超载运转,严重时会烧坏电机,扭断传动轴。
4、损坏厂房结构行车啃轨必然产生水平侧向力,这种侧向力将直接导致轨道横向位移,造成轨道紧固螺栓松动。
同时由于啃轨,天车在运行过程中,产生不正常的振动,将不同程度的损坏厂房结构。
起重机啃轨分析及处理
起重机啃轨原因分析及处理方法摘要:叙述桥式起重机大车运行中的啃轨现象及造成后果,从轨道缺陷、车轮缺陷、桥架变形等方面分析了桥式起重机的啃轨原因,对各个方面的问题提出了处理措施,并对板带厂热轧车间的五号行车进行了整改,现今运行正常。
关键词:桥式起重机车轮啃轨原因分析整改前言:桥式起重机是起重设备的主要机种,国家列入特殊设备管理,在冶金生产中已成为必不可少的设备。
桥式起重机在使用一定的时间后,由于工况条件和运行频繁,都会出现不同程度的大车或小车运行啃轨现象。
起重机运行过程车或小车的轮缘与钢轨侧面接触,发生强烈的磨损,称为啃轨。
轻微的啃轨不影响使用,常常被人们忽视,严重的啃轨,使车轮与轨道剧烈磨损,并且大大增加附加载荷,运行阻力比正常状态时增大三倍左右,致使起重机运行扭摆,发出响声,运行电动机和传动机构超载运转,随着啃轨的加重,会发生烧坏电动机或扭断传动轴的设备事故,还有脱轨的危险。
啃轨严重可影响企业的正常生产,引发安全隐患,所以要及早发现及早修复,下面针对桥式起重机大车运行啃轨现象进行探讨分析。
1、啃轨现象及其造成不良的后果1.1啃轨现象1.1.1通常车轮轮缘与轨道侧面之间设计有一定的间隙,在正常运行情况下,它们不会接触。
但有时车轮不在轨道中心部位运行,从而发生车轮轮缘与轨道侧面相接触(摩擦)的啃轨现象。
1.1.2轨道侧面或车轮轮缘侧有斑痕,严重时痕迹上有毛刺或掉铁屑。
1.1.3桥式起重机行驶时,在短距离轮缘与轨道间隙有明显的改变。
1.1.4桥式起重机在运行中,车体产生歪斜,车轮走偏。
1.1.5大车运行时会发出较响亮的“嘶嘶”啃轨声。
1.1.6啃轨特别严重时,大车运行会发出“坑坑”的撞击声,甚至出现爬轨。
1.2车轮啃轨造成不良的后果1.2.1缩短车轮使用寿命。
在正常情况下,中级(A4—A5)工作级别的桥式起重机其车轮可以使用15年以上,重级(A6—A8)及冶金桥式起重机的车轮可使用8年左右,但是对于一些啃轮较严重的桥式起重机,车轮只能使用1-2年。
- 1、下载文档前请自行甄别文档内容的完整性,平台不提供额外的编辑、内容补充、找答案等附加服务。
- 2、"仅部分预览"的文档,不可在线预览部分如存在完整性等问题,可反馈申请退款(可完整预览的文档不适用该条件!)。
- 3、如文档侵犯您的权益,请联系客服反馈,我们会尽快为您处理(人工客服工作时间:9:00-18:30)。
起重机啃轨原因分析及处理方法摘要:叙述桥式起重机大车运行中的啃轨现象及造成后果,从轨道缺陷、车轮缺陷、桥架变形等方面分析了桥式起重机的啃轨原因,对各个方面的问题提出了处理措施,并对板带厂热轧车间的五号行车进行了整改,现今运行正常。
关键词:桥式起重机车轮啃轨原因分析整改前言:桥式起重机是起重设备的主要机种,国家列入特殊设备管理,在冶金生产中已成为必不可少的设备。
桥式起重机在使用一定的时间后,由于工况条件和运行频繁,都会出现不同程度的大车或小车运行啃轨现象。
起重机运行过程中大车或小车的轮缘与钢轨侧面接触,发生强烈的磨损,称为啃轨。
轻微的啃轨不影响使用,常常被人们忽视,严重的啃轨,使车轮与轨道剧烈磨损,并且大大增加附加载荷,运行阻力比正常状态时增大三倍左右,致使起重机运行扭摆,发出响声,运行电动机和传动机构超载运转,随着啃轨的加重,会发生烧坏电动机或扭断传动轴的设备事故,还有脱轨的危险。
啃轨严重可影响企业的正常生产,引发安全隐患,所以要及早发现及早修复,下面针对桥式起重机大车运行啃轨现象进行探讨分析。
1、啃轨现象及其造成不良的后果1.1啃轨现象1.1.1通常车轮轮缘与轨道侧面之间设计有一定的间隙,在正常运行情况下,它们不会接触。
但有时车轮不在轨道中心部位运行,从而发生车轮轮缘与轨道侧面相接触(摩擦)的啃轨现象。
1.1.2轨道侧面或车轮轮缘内侧有斑痕,严重时痕迹上有毛刺或掉铁屑。
1.1.3桥式起重机行驶时,在短距离内轮缘与轨道间隙有明显的改变。
1.1.4桥式起重机在运行中,车体产生歪斜,车轮走偏。
1.1.5大车运行时会发出较响亮的“嘶嘶”啃轨声。
1.1.6啃轨特别严重时,大车运行会发出“坑坑”的撞击声,甚至出现爬轨。
1.2车轮啃轨造成不良的后果1.2.1缩短车轮使用寿命。
在正常情况下,中级(A4—A5)工作级别的桥式起重机其车轮可以使用15年以上,重级(A6—A8)及冶金桥式起重机的车轮可使用8年左右,但是对于一些啃轮较严重的桥式起重机,车轮只能使用1-2年。
1.2.2加快轨道磨损。
啃轨产生的侧向力能使轨道位置偏移或磨出台阶。
1.2.3增大运行阻力,增大电动机功率消耗和机构的传动负荷。
1.2.4对房梁结构的影响。
由于起重机运行啃轨,必然产生水平侧向力,这种侧向力将导致轨道横向位移,致使固定轨道的压板及螺栓松动。
另外,由于运行啃轨,将引起整台起重机较大的震动,这些都不同程度的影响房梁结构。
2、啃轨的原因分析啃轨原因是多种多样的,轨道的原因、车轮的原因、桥架变形而引起的,还有可能是几者之间的问题。
据相关资料,由于轨道问题,车轮问题引起的啃轨情况占大部分。
2.1轨道2.1.1轨道安装质量不合格:“轨道承轨梁安装时倾斜导致轨道安装在承轨梁上时随着倾斜,使运行中的车轮侧移,一侧车轮磨内侧,另一侧车轮磨外侧”。
如图1所示垂线轨道承轨梁α图12.1.2轨道水平弯曲(要求其侧面直线度不大于3mm),超过跨度公差时就会产生啃轨,啃轨现象是固定在某一线段上的。
水平弯曲就是所谓的“轨道蛇弯”,蛇弯的轨道有上述所提到的安装问题,但在轨道的使用中由于啃道产生的水平侧向力,这种侧向力导致轨道横向位移,致使固定轨道的压板螺栓松动,断裂,脱落,在水平侧向力与温度下的热变形力作用下致使轨道向内,向外弯曲加大。
也就形成轨道的水平弯曲。
且温度的影响,使轨道变形,(因为轨道的热膨胀量△L=L0α(t2-t1),轨道受温度影响高达80-90摄氏度,△L均大于11毫米,因此,标准的轨道接头缝隙量已不能满足要求,经查由于缝隙量不够,导致轨道顶死,并向内外两侧弯曲。
如图2所示轨道弯图22.1.3轨道轨距过大或过小(超出跨度标准值)时,过大,外侧轮缘啃道;过小,内侧轮缘啃道。
如图3所示走轮图 32.1.4两根轨道同一截面上轨面高度差过大(柱子处不大于10mm,其它处不大小15mm)造成侧移,超高外侧啃道,另一侧内侧啃道。
如图4示图 4(过大)走轮轨道2.1.5轨距一端大,另一端小,两根轨道平行度超差,在这样的轨道上运行的车轮。
轮缘与轨道间的间隙愈走愈小,直至内侧轮缘啃道,向相反方向运行,才慢慢好转,继续运行,外侧轮缘又开始啃道。
如图5所示。
图 5 大车轨道跨距2.1.6轨道与承轨梁间有大的间隙或轨道安装垫板(压轨器)未压实,不承载时,轨道保持水平,承载时轨道下陷,车轮侧移,形成间断性的啃道。
2.2车轮2.2.1两主动轮直径相差过大,如果桥式起重机两主动轮直径不同,则每转行走的距离就不等,直径大的一侧就要逐渐超前(线速度不等)使车体歪斜从而产生啃轨。
2.2.2四个轮的安装位置不是矩形的四角,同侧两车轮中心不在同一直线上,不管是主动轮还是被动轮,当两轮中心线不在同一直线上时,都会造成啃轨,车轮位置呈平行四边形,但两车轮中心线不在同一直上的四顶点布置(如图6所示),对角线D1>D2啃轨车轮在对角线位置,车轮位置呈梯形四顶点布置(如图7所示)。
D1D2车轮D1D2车轮图 6 图 72.2.3车轮的水平偏斜超差,轮的水平偏斜即踏面中心线与轨道中心线在水平方向有一夹角,这时车轮运行速度“V”可分解为两个方向的力,一是平行于车轮轨道的Vx力,使车体向前运行;一个是垂直于车轮轨道V y力,使车体产生横向滑动,如图8所示,超出规定值时将引起啃轨。
β图 8 车轮水平偏斜2.2.4车轮的垂直偏斜超差,即车轮踏面中心与铅垂线形成夹角“α“,如图9所示,超出规定值时将引起啃轨。
垂直偏斜超差的原因是:增加了车轮的运行半径,原运行半径为”R”,车轮运行一周所走的路程为2πR,产生垂直偏斜后其运行半径变为“R1”此时车轮运行一周所走的路程为“2πR1”每运行一周,车轮多运行2πR1-2πR=2π(R1-R)的路程,此即车轮的超前量,但因有轮缘限制,不能过量超前,而形成了啃轨。
α图 9 垂直偏斜车轮垂直偏斜超差引起啃轨,是指主动轮,与被动轮无关,尽管被动轮垂直偏斜超差不会引起啃轨,但从车轮轴承应均匀受力及车轮踏面与轨道的接触面积等方面考虑,亦不允许被动轮的垂直偏斜超出公差。
每一对主动轮的垂直偏斜若是同一方向,并两车轮的垂直偏斜量相等,此时在空载时,A、B两轮的运行半径值是一样的不产生啃轨,如图10所示:图 10但是承载后,A轮的垂直偏斜将进一步增大,运行半径也进一步增大,而B轮垂直偏斜将减少,运行半径也将减少,所以这种两主动轮同方向的垂直偏斜将由空载时的不啃轨,变成承载后的啃轨。
因此,同一组车轮(主动或被动)的垂直偏斜方向均应向外偏斜,如图11所示:因为这种垂直偏斜当桥架承载后,将减少车轮的垂直偏斜。
图 112.2.5目前生产的桥式起重机为了自行调节大车两端的相互超前或滞后,避免运行啃轨,大车运行机构的主动轮踏面采用1:10锥形轮(当主动轮为两个时才采用)。
这种锥形车轮的安装,是有一定方向,且两锥度方向相反,如图12所示:图 12 锥形车轮2.3桥架由于桥架的变形必然引起车轮的歪斜和跨度的变化:2.3.1桥架变形造成端梁水平弯曲或对角线长度超差,跨度超差均会引起啃轨,造成车轮水平偏斜超差(允许不大于测量长度的1/1000)车轮宽度中心线与轨道中心线形成一夹角,两主动轮同向偏斜,造成啃轨。
2.3.2桥架产生垂直变形,造成车轮垂直偏斜超差,(允许偏差不大于测量长度的1/400)或安装时,超差。
车轮的踏面中心,与铅垂线产生夹角,如图9示,改变了车轮的滚动半径。
由于桥架变形,致使端梁水平偏斜,导致一对主动轮向同一方向垂直偏斜,且偏斜方向相同时,如图10所示,则在空载时A,B两车轮运行半径增大值相等,不会产生啃轨,但是承载后,A轮的垂直偏斜进一步增大,B轮垂直偏斜减小,形成两主动轮的滚动半径不相等,车轮发生啃轨。
2.4其它2.4.1两组车轮装配的松紧程度不一致而产生不同的阻力,从而使驱动电机不同步,造成车体歪斜,形成车轮啃轨。
2.4.2分别驱动的大车运行机构中两台电机转速不一致,导致左右车轮线速度的差异,造成车体跑偏啃轨。
2.4.3两端联轴器传动间隙差过大,引起车轮不能同时驱动,造成啃轨。
2.4.4分别驱动的大车运行机构两制动器,调整间隙不同,造成制动力矩不等,步调不一致。
2.4.5不合理操作的影响,小车经常在一侧工作,使该侧的大车轮压阻力变大而产生啃轨。
启动或停车过猛,会使车轮空转打滑,易造成啃轨。
2.4.6轨道顶面有油污,冰霜,杂物等,引起两侧车轮的行进速度不一样,必然引起车轮轮缘与轨道侧面摩擦,即引起运行啃轨。
总而言之,造成起重机运行啃轨的因素是很多的,有的是几个因素同时作用综合造成的。
因此,应视具体情况加以分析,采取措施综合处理。
3、排除啃轨的处理措施3.1轨道,对于轨道安装水平弯曲过大或轨道的局部变形过大或轨道安装八字形造成的啃轨,应重新调整轨道,使之达到规定的标准。
对于同一截面两根轨道相对高度差过大造成的啃轨,应调整高低误差,采用加垫板法来调整,选用普通钢板,其厚度按轨道实测高低误差选定,垫板要求表面平整、无凹凸,外形尺寸宽度不得超过轨道压板20mm,轨道下面要填实,不得有悬空现象,用带螺栓的压板固定在下面梁上,这种方法结构经济、可靠、效果好,简单易行。
3.2桥架,运输或安装吊运等原因造成桥架变形,使大车的水平偏斜,垂直偏斜,对角线超差过大,因此,首先因矫正桥架,使其符合技术要求,否侧不能从根本上解决啃轨问题。
在桥架和传动机构基本符合技术要求或桥架虽有变形但不大时,调整车轮是最容易最便捷解决啃轨的方法。
3.3车轮,有时调整一个车轮可以同时解决车轮的水平偏斜,垂直偏斜,跨度和对角线超差等几个方面的问题,所以应检查分析,确定调整哪一个车轮能使工作量小而达到目的。
特别要注意的是,因为主动车轮与传动机构相联接,调整主动轮的工作量较大,容易造成传动机构不同心,所以除必须外,以调整被动车轮为好。
3.3.1车轮水平偏斜的调整,如图13及图14所示,可看出A,C,D三个车轮的偏斜量符合规定,侧只将B 轮的偏斜方向调整一下即可,无需四个车轮全部调整。
图 13 调整前图 14 调整后3.3.2关于车轮的垂直偏斜的调整,在空载时应使两车轮的边向外偏斜。
如图11所示,当起升载荷逐渐增大时,车轮正好趋向于垂直受力。
调整车轮前,首先用千金顶把端梁顶起,使车轮悬空,然后松开紧固螺栓,再调整。
轻微的调整,可松开紧固螺栓后,在角型轴承箱的槽内加垫即可。
调整跨度和对角线时,应将一个车轮的四块板全部铲平,调整好后再把定位键板焊接在端梁弯板上。
需要调整的量较大时,应将定位键铲开,在键板与端梁弯板间加垫调整。
调整水平偏斜应在垂直键板处加垫;调整垂直偏斜应在水平键板处加垫。
3.4两侧电机转速不一致,换为同型号同厂家的电机。
3.5两侧制动器间隙不一样调整制动器。
3.6联轴器传动间隙过大,更换联轴器或减速机。