高炉矿槽炉顶上料系统的工艺流程
高炉工艺装料制度
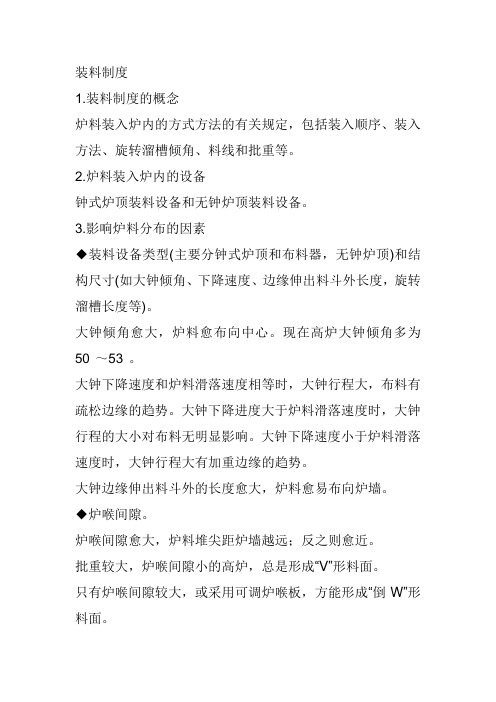
装料制度1.装料制度的概念炉料装入炉内的方式方法的有关规定,包括装入顺序、装入方法、旋转溜槽倾角、料线和批重等。
2.炉料装入炉内的设备钟式炉顶装料设备和无钟炉顶装料设备。
3.影响炉料分布的因素◆装料设备类型(主要分钟式炉顶和布料器,无钟炉顶)和结构尺寸(如大钟倾角、下降速度、边缘伸出料斗外长度,旋转溜槽长度等)。
大钟倾角愈大,炉料愈布向中心。
现在高炉大钟倾角多为50°~53°。
大钟下降速度和炉料滑落速度相等时,大钟行程大,布料有疏松边缘的趋势。
大钟下降进度大于炉料滑落速度时,大钟行程的大小对布料无明显影响。
大钟下降速度小于炉料滑落速度时,大钟行程大有加重边缘的趋势。
大钟边缘伸出料斗外的长度愈大,炉料愈易布向炉墙。
◆炉喉间隙。
炉喉间隙愈大,炉料堆尖距炉墙越远;反之则愈近。
批重较大,炉喉间隙小的高炉,总是形成“V”形料面。
只有炉喉间隙较大,或采用可调炉喉板,方能形成“倒W”形料面。
◆炉料自身特性(粒度、堆角、堆密度、形状等)。
◆旋转溜槽倾角、转速、旋转角。
◆活动炉喉位置。
◆料线高度。
◆炉料装入顺序。
◆批重。
◆煤气流速。
4.钟式炉顶布料的特征◆矿石对焦炭的推挤作用。
矿石落入炉内时,对其下的焦炭层产生推挤作用,使焦炭产生径向迁移。
矿石落点附近的焦炭层厚度减薄,矿石层自身厚度则增厚;但炉喉中心区焦炭层却增厚,矿石层厚度随之减薄。
大型高炉炉喉直径大,推向中心的焦炭阻挡矿石布向中心的现象更为严重,以致中心出现无矿区。
◆不同装入顺序对气流分布的影响。
炉料落入炉内,从堆尖两侧按一定角度形成斜面。
堆尖位置与料线、批重、炉料粒度、密度和堆角以及煤气速度有关。
先装入矿石加重边缘,先加入焦炭则发展边缘。
5.无料钟布料无料钟布料特征◆焦炭平台:高炉通过旋转溜槽进行多环布料,易形成一个焦炭平台,即料面由平台和漏斗组成,通过平台形式调整中心焦炭和矿石量。
平台小,漏斗深,料面不稳定。
平台大,漏斗浅,中心气流受抑制。
基于PLC的高炉上料控制系统研究

2 硬 件 系统及 系统 软件 供料 系统在受料 电气室设有一套 P L C 控制系统 , 在矿焦槽 电气室设有远程 I / O, 采用 s 7 — 4 1 4 , 设1 个 中
央机架 U R 2 , 配有独立 电源模板 P S 4 0 7 I O A, 1 个 C P U 4 1 4 — 2 。I / O系 统 采 用 E T 2 0 0 M, 配置 P R O F I . B U S — D P网 络 访 问 I / O 。P L C组 态 编 程 软 件 用 S I E .
基于 P L C的高炉上料控制系统研究
苏海 东
( 山西太钢不锈钢 股份 有限公 司 ,山西 太原 0 3 0 0 0 3 )
摘
要: 介绍 了太钢 5 # 4 3 5 01 1 1 高炉矿槽 炉顶 上料 系统的工艺流程。以及西 门子公 司S 7系列P L C ̄ 1 系统的特点 、
硬件 组态及软件功能 , 并详细介 绍 了P L C 控 制 系统的主要 控制功能 。 关键 词 : P L C ; 自动控制 ; 上料 系统 ; 高炉
第1 期( 总第l 3 1 期)
机 械 管 理 开 发
2 0 1 3 年2 月
N o . 1 ( S U M N o . 1 3 1 )
M E C H A N I C A L M A N A G E M E N T A N D
垦 1
F e b . 2 03
文献标识码 : A
文章编号 :1 0 0 3 — 7 7 3 X ( 2 0 1 3 ) 0 1 - 0 0 5 1 - 0 2
0 引 言
太钢 5 # 4 3 5 0 m 高炉矿槽炉顶上料系统设计采用 西 门子公 司 s 7 系列 P L C , 该 控制系统实现了对矿石 、 球团 、 烧结 、 焦碳 、 杂矿等原料的 自动称量 , 并完成称量 误差的 自动补偿 。实现了炉顶各阀门的顺序 自动开关 O / 、 、 , , 的角度 自动设定 以及其他相关辅助设备的 自动 控制 。实现了对高炉矿槽炉顶上料系统 的数据采集 、 数据显示与数据控制 。该系统包括 : 烧结矿受料设施 , 落地烧结 矿受料设施 , 大皮带受料设 施 , 焦 粉返 回系 统, 小粒矿 回收系统 , 汽车受料设施 , 大皮带受料设施 和焦炭受料设施。 1 高炉矿槽炉顶上料系统工艺流程 太钢5 #4 3 5 0 m 。 高炉 炉顶采用无 料 钟 串罐式 炉 顶, 分为受料斗 、 料罐 、 气密箱等组成部分 。在上料过 程 中, 炉料先投进受料斗里 , 随后放人料罐 中, 在这个 过程 中 , 由于高炉 不 能和 大气 相通 , 通 过控 制炉 顶放 散 阀、 均压 阀 、 上密 阀 、 柱塞 阀 、 下密 阀 的顺序 开关 来实 现 高炉 的正常下 料 , 通过控制 、 、 来实现 高炉布料 。 料面检测设备采用机械探尺与雷达探尺相配合u 。 1 . 1 装料 流程 焦炭 、 烧结矿等各种人炉原料 由料车运到炉顶 , 倒 人受 料斗中 , 受料斗最多可装 4 车料。料罐放散完毕 后打开上密阀和柱塞 阀向料罐装料 。装料完成后料罐 进行均压 。一旦 高炉准备接 受下一批炉料就进行布 料, 首先打开下密 阀并将料流调节阀打开至设定开度 , 料罐 中的炉料通过料 流调节 阀流到旋转的布料溜槽 上。在布料期间 , 通过 谢 线探测料流 , 该装置可发 出 料罐清空信号 。一旦料罐清空 , 关 闭料流调节 阀和下 密封 阀 , 打 开放 散 阀进 行放 散 , 准备 下 一次装 料 。 1 . 2 布料 流程 批 料 中, 允 许 焦 矿 设 定 两 个 不 同 的料 线 位 置 。 当探尺达到规定的料线位置后 , 自动提升到位 , 发出布 料信号 , 下密封 阀打开 , 布料溜槽进行启动。口 角旋转 到设定速度并且到达布料位置 , 开启料流调节阀, 按照 批重及规定 的布料程序 , 调节料流调节 阀开度和溜槽 倾角 , 使每圈料流均匀 、 重量相等和首尾相接地 向炉喉 任意布料 。为 了减少料头料尾不均匀现象 , 每批料布 完后 , 布料角度 自动步进 6 0。 。
高炉炼铁生产工艺流程
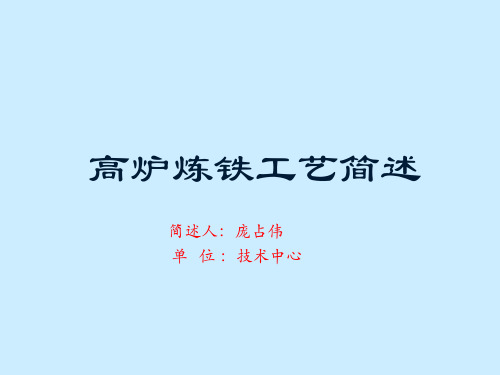
MnS少量溶于铁中,大量溶于渣中,FeS既溶于铁中,也溶于渣中。;炉渣的脱硫作用 就是渣中的CaO、MgO等碱性氧化物与生铁中的硫反应生成只溶于渣中的稳定化合物 CaS、MgS等从而减少生铁中的硫。 4.3硫的分配系数。硫在渣中的质量分数与在铁水中的质量分数之比。用LS=w(S)/ w[S]表示。 4.4影响炉渣脱硫能力的因素:炉渣碱度、MgO含量(提高渣的稳定性和流动性,有利 于脱硫)、Al2O3、FeO、渣铁温度(脱硫反应是吸热反应,提高温度有利于脱硫,提 高温度降低炉渣黏度)、提高硫的分配系数、高炉操作。
2.4送风制度:通过选用合适的风口面积,风量、风温、 喷吹量、富氧率等参数达到适宜的风速和鼓风动能及理论 燃烧强度,使初始煤气流分布合理,炉缸工作均匀活跃热 量充沛稳定。
6、高炉基本操作制度的宗旨: “上稳下活”。
3、炉况的判断:在实际生产中原燃料的物理性能、 化学成分经常会产生波动,气候条件的不断变化, 入炉料的称量可能发生误差,操作失误与设备故 障也不可能避免,炉况判断就是判断这些影响程 度及顺行的趋向,即炉况是向凉还是向热,是否 会影响顺行,它们的影响程度如何等等。判断的 手段基本是两种,一是直接观察,如看入炉原料 外貌,看出铁、出渣、风口情况,二是利用高炉 数以千计、百计的检测点上得到的信息在仪表或 计算机上显示重要数据曲线,例如风量、风温、 风压等鼓风参数、各部位的温度静压力、料线变 化、透气性指数变化、风口前理论燃烧温度等等。
5.6炉顶压力曲线平稳、没有较大的尖峰。
5.7炉喉、炉身、炉腰各部温度正常、稳定、无大波动, 炉体各部冷却水温差正常。
安钢炼铁厂高炉工艺简介

2、工艺流程
4800m3高炉工艺布置图
3、主要工艺参数
序号 1 2 3 4 5 6 7 8 9 10 12 13 14 15 16 17 18 项目 有效容积 利用系数 焦比 煤比 富氧率 熟料率 烧结矿配比 球团矿配比 块矿配比 入炉矿品位 入炉风量 热风温度 炉顶温度 炉顶压力 渣铁比 日产生铁 年产生铁 单位 m3 t/(m3·d) kg/t铁 kg/t铁 1# 2200 2.36 350 169 5.10% 95% 80% 15% 4.50% 55.91% 4200 1185 150~260 0.21 368 5200 187 3# 4800 2.3 305 200 4% 86% 91% 75% 73.30% 16% 13% 9% 13.60% 59.20% 55.47% 7000 5800 1250 1250 150~260 150~250 0.25 0.22 310 365 10918 6500 382 237
1#、2#高炉,矿、焦槽单独设置,各用一条运 输胶带机(供矿皮带和供焦皮带),共用一条上 料主皮带,构成两个独立、并列的系统。
4.1矿焦槽系统
3#高炉,矿、焦槽呈双排布置,不设中间斗, 矿石、焦炭在槽下筛分称量后共用一条胶带机运 入上料主胶带输送机,然后运至高炉炉顶设备。
4#、5#高炉,矿、焦槽单独设置,矿石筛分 后经皮带机运输到两个矿石集中斗,焦炭由焦槽 直接进入焦炭集中斗,称量后装入料车,然后运 至高炉炉顶设备。
4.5炉体系统
4.5炉体系统
4.5.4炉底、炉缸内衬
2200m3 和2800m3 高炉采用陶瓷杯炭砖水冷炉底炉缸结构。 炉底中心下部立砌两层国产炭砖,其中下层为半石墨炭 砖,上层为微孔炭砖;上部砌两层低导热刚玉莫来石砖,炉 缸内侧砌低导热刚玉莫来石砖,外侧炉缸采用进口微孔炭 砖,在进口微孔炭砖与风口组合砖之间砌筑3层国产微孔炭 砖;在炉缸,炉底交接处采用加厚陶瓷质耐火材料和进口 微孔炭砖砌筑结构。 在风口区采用大块组合砖砌筑,以加强结构的稳定性; 铁口通道采用大块和小块相结合特殊组合砖结构。
上料工操作规程
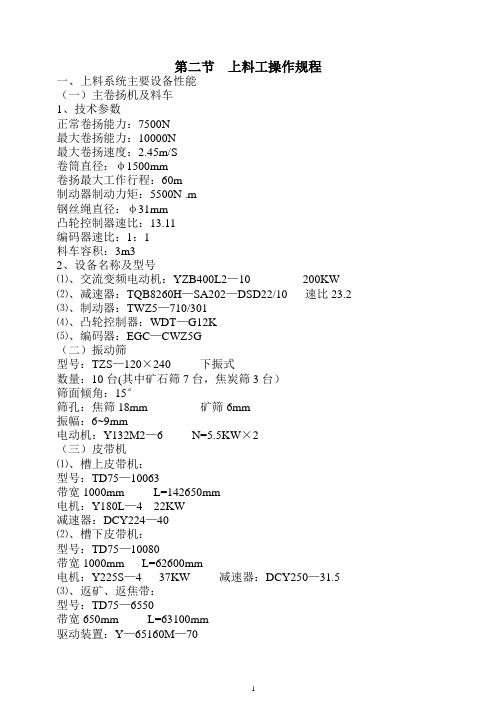
第二节上料工操作规程一、上料系统主要设备性能(一)主卷扬机及料车1、技术参数正常卷扬能力:7500N最大卷扬能力:10000N最大卷扬速度:2.45m/S卷筒直径:φ1500mm卷扬最大工作行程:60m制动器制动力矩:5500N .m钢丝绳直径:φ31mm凸轮控制器速比:13.11编码器速比:1:1料车容积:3m32、设备名称及型号⑴、交流变频电动机:YZB400L2—10 200KW⑵、减速器:TQB8260H—SA202—DSD22/10 速比23.2⑶、制动器:TWZ5—710/301⑷、凸轮控制器:WDT—G12K⑸、编码器:EGC—CWZ5G(二)振动筛型号:TZS—120×240 下振式数量:10台(其中矿石筛7台,焦炭筛3台)筛面倾角:15°筛孔:焦筛18mm 矿筛6mm振幅:6~9mm电动机:Y132M2—6 N=5.5KW×2(三)皮带机⑴、槽上皮带机:型号:TD75—10063带宽1000mm L=142650mm电机:Y180L—4 22KW减速器:DCY224—40⑵、槽下皮带机:型号:TD75—10080带宽1000mm L=62600mm电机:Y225S—4 37KW 减速器:DCY250—31.5 ⑶、返矿、返焦带:型号:TD75—6550带宽650mm L=63100mm驱动装置:Y—65160M—70(四)斗式提升机:型号:TD315 输送量:60M3/h 提升高度:13.33m 驱动方式:左装C3制法电机:Y160L—4 15KW减速器:ZQ500—V—5Z(五)矿槽除尘器:⑴、除尘器技术性能参数:型号:LDMM2520 离线清灰脉冲袋式除尘器处理风量:280000m3/h 过滤面积:2520—2600m2⑵、配套风机、电机:风机型号:G4—73N020D 右旋45°离心通风机配电机:Y450—6 560KW 6Kv二、上料系统工艺流程及操作规程(一)上料系统工艺流程图(二)上料系统岗位职责及操作规程A、上料系统岗位职责(1)上料组长岗位职责1、严格执行操作规程,服从车间与值班工长的双重领导。
高炉上料控制

备用的电机号 4 2 3 1
5、称量误差补正及称量显示
5.1、称量误差补正的控制
5.1.1、简要说明:各种原、燃料均设误差补正。 补正的方式 称量误差补正的原则是本称量漏斗的称量误差由该斗补, 与其它斗无关。设有两种补正方式: ⑴本次的称量误差待下次称量时补正。 ⑵累积误差补正即把每次的称量误差累计到一定量时进 行补正。最大累积误差值(可调)暂定如下: 矿石:200kg, 杂矿:150kg, 焦炭:100kg。
6、X-601及Y-601胶带机废铁检除装置
在X-601矿石胶带机和Y-601焦炭胶带机上各设一套废 铁检除装置。该装置为机电一体化,当废铁经过金属探测 器时,将信号发送给废铁检除装置,则废铁检除装置按预 先设定的程序自动将混入物料中的铁块检除。
7、设备的操作与联锁要求
矿槽系统电控设备约33种,75套设备。除电动葫 芦及传动室吊车不参与联锁外,其余设备在自动运转 时必须保持各设备之间的联锁关系,粉矿仓料位计及 碎焦仓仓下电动闸门参与返矿系统的联锁控制(粉矿 仓料位计及碎焦仓仓下电动闸门属返矿系统,其控制 要求见机械贮运专业提供的相关资料)。为防止误操 作及保护设备,手动操作时应保留必要的安全联锁,
6 炉顶探尺对炉内物料的跟踪、记录与监视 7). 装料系统装料制度、装入待的设定、料线设定、装料 循环周期的处理 8). 空焦装入方式及运转控制 9). 装料操作参数的设定、实际装入操作的数据收集、处 理 10). 装入系统设备的操作与监视 11). 装料系统设备故障处理
2.2、主工艺系统基本控制 2.2.1、炉顶压力选择 设有高压操作和常压操作选择。 2.2.2、控制选择 全自动→1批料(Charge)自动→ 1小批料
2、高炉装料制度
高炉的装料制度为: C↓O↓ C-焦炭 O-矿石(烧结矿、块矿及球团矿)
炼铁生产工艺流程

均压
上料小车 绳轮
过滤、消音
鼓风机
高炉工艺路线 2—送风系统
放风阀
燃烧室
煤气
蓄热室(格子砖)
送风阀
冷风总管
热风炉
高炉本体
送风装置
热
倒
助燃风机
风流
休
热风围管
热风总管
风 阀
高炉炉顶
高炉工艺路线 3—喷煤系统
煤气 上升管
粗煤气
煤气 下降管
煤气柜 热风炉
布袋 除尘器
重力 除尘器
放渣 出铁箅渣
高炉工艺路线四—水渣系统
炉喉 炉身
炉腰 炉腹 渣口 炉缸
高炉本体
高炉炼铁过程是连续 不断进行的,高炉上部 不断装入炉料和有煤气 导出,下部不断鼓入空 风口 气和定期放出渣铁。
铁口
高炉工艺路线 1—上料系统
碎矿
原料场
碎焦
电除尘
皮带机 高炉矿烧结矿
布料
炉顶料罐
振动筛
斜桥
上料
称重料斗
皮带机
料斗
气密箱 溜槽 探尺
图 2-4
炼铁生产工艺流程
高炉主要分为以下几大系统
·高炉本体
·上料系统
·送风系统
·出铁场
·煤气系统
·水渣系统
※ 喷煤系统
高炉生产新技术
软水密闭循环冷却
富氧喷煤
球团矿
焦碳 烧结矿
高炉炼铁工艺总路线
上料
布料
冶
热送 化验 出铁
炼
炼钢
铸铁
放渣
送风 喷煤 煤气
水渣系统
图 2-4 炼 铁 生 产 工 艺 流 程(续一)
干渣沟 冲渣泵
水渣沟
高炉无钟炉顶装料工艺技术要求

承钢4号高炉无料钟炉顶装料系统“三电”工艺技术要求一、概述1.1、高炉主要设计指标和设计参数高炉有效容积:2500立方米采用并罐无钟炉顶装料设备,料罐有效容积55立方米;1.2、炉顶装料设备主要技术参数无钟炉顶装料设备:布料器溜槽摆角、节流阀、上、下密封阀、均压放散阀等,均采用液压传动,布料器回转采用电机传动;炉顶及上料设备见附图;主要技术参数如下:1.2.1、受料漏斗受料漏斗为皮带头轮收料的固定料斗,存料容积55m3;1.2.2、翻板阀在受料漏斗下方装有翻板阀,通过翻板可以分别向左、右料罐装料;翻板阀上装有左、右液压缸,分别控制左、右侧翻板位置。
1.2.3、Φ1000上密封阀左、右料罐上装有Φ1000上密封阀,由液压缸控制。
1.2.4、节流阀左、右料罐的节流阀为八角形。
节流阀开度大小由炉料品种和重量来决定,由液压缸控制。
采用比例方向控制阀进行方向及速度控制。
为保证安全起见,备用一套三位四通电磁阀进行控制。
1.2.5、Φ800下密封阀左右料罐的Φ800下密封阀, 由液压缸控制。
1.2.6、Φ400一次均压阀左右料罐均压采用半净化煤气,通过Φ400均压阀进行一次均压,由液压缸控制。
1.2.7、Φ250二次均压阀和调节阀左右料罐二均采用氮气通过Φ250二次均压阀和调节阀实现,二均阀由液压缸控制。
1.2.8、Φ400放散阀左右料罐采用Φ400均压放散阀进行放散,由液压缸控制。
1.2.9、布料器①布料器溜槽旋转a、旋转速度8rpm,每圈7.5秒。
b、可以正反方向旋转。
②溜槽摆动a、摆角速度:正常要求1.6度/秒;b、工作角度:α=10~450c、最大摆动角度:α=450③传动系统a、布料器回转由一台7.5KW电机(自带减速机)拖动布料器旋转,布料器上方有两套可供布料器旋转的接手。
正常情况下一套接手与减速机电机连接,另一套架空备用。
正常情况下布料器为常转工作制。
b、布料器摆角传动布料器摆角采用三个直线油缸传动。
- 1、下载文档前请自行甄别文档内容的完整性,平台不提供额外的编辑、内容补充、找答案等附加服务。
- 2、"仅部分预览"的文档,不可在线预览部分如存在完整性等问题,可反馈申请退款(可完整预览的文档不适用该条件!)。
- 3、如文档侵犯您的权益,请联系客服反馈,我们会尽快为您处理(人工客服工作时间:9:00-18:30)。
本文介绍了莱钢1#1000m3高炉矿槽炉顶上料系统的工艺流程,施耐德公司昆腾系列PLC控制系统的特点、硬件组态及软件功能,并详细介绍了该PLC控制系统的主要控制功能。
Abstract:This paper mainly discuss the process control system of feeding syste m for blast furnace based on Schneider TSX Quantum series PLC. Configuration so ftware Concept2.6 are adopted to monitor and manage process data. The whole sys tem well satisfies the technical requiments for control.关键词:PLC;自动控制;上料系统;昆腾Key words:PLC;automation;feeding system;Quantum1、概述莱钢1#1000m3高炉2005年投产,矿槽炉顶上料系统设计采用施耐德公司昆腾系列PLC,该控制系统实现了对矿石、球团、烧结、焦碳等原料的自动称量,并完成称量误差的自动补偿;实现了炉顶各阀门的顺序自动开关,α、β、γ的角度自动设定以及其他相关辅助设备的自动控制;实现了对高炉矿槽炉顶上料系统的数据采集、数据显示与数据控制。
该系统投运以来,运行稳定,效果良好。
2、高炉矿槽炉顶上料系统工艺流程简述2.1 槽上控制工艺流程:高炉槽上设计13个料仓,4个烧结矿仓(3#、4#、5#、6#),2个焦炭仓(7#,8#),3个球团仓(9#、10#、11#),2个杂矿仓(1#、2#),1个焦丁仓。
槽上有3条打料皮带机,每条皮带机对应一辆卸料小车,采用卸料小车可以将胶带机输送的原料卸至不同的料仓,当采用卸料小车进行卸料时,卸料小车先开至所选择的料仓上方,然后启动胶带机,原料就经卸料小车卸到小车下方的料仓内。
2.2 槽下控制工艺流程:高炉槽下设两个大烧结矿仓,两个小烧结矿仓,两个杂矿仓,三个球团仓,一个备用仓。
每个矿仓下都有振动筛,筛除小于5mm的碎矿,大烧结矿仓的矿经过筛分后分别进入料坑的左右中间称量斗,小烧结矿仓的矿经筛分后分别进入各自配套的称量斗,然后经矿石皮带机集中运送,经料坑上方的翻板进入料坑中的矿石中间斗,经筛分后的5mm烧结矿经返矿皮带机运到碎矿仓。
焦炭设左右两个焦仓,仓下装有振动筛和振动给料机,焦炭经筛分后,大于20mm的块焦,分别直接进入料坑内的左右焦炭称量斗,筛下小于20mm的碎焦经SJ1、SJ2胶带机倒运到SJ3碎焦胶带机上,送至碎焦仓上振动筛,将碎焦分级成8mm以上和8mm以下两种产品,大于8mm的焦丁由SJ4胶带机运至焦丁仓,再经焦丁给料机到焦丁称量斗,然后到供料胶带机与烧结矿一起进入料坑中间斗。
小于8mm的碎焦落入焦粉仓等待汽车外运。
当料车到底后,相应的矿石中间斗或焦炭斗向料车装料。
2.3 炉顶控制工艺流程:莱钢1#1000m3高炉炉顶采用无料钟串罐式炉顶,分为受料斗、料罐、气密箱等组成部分。
在上料过程中,炉料先投进受料斗里,随后放入料罐中,在这个过程中,由于高炉不能和大气相通,通过控制炉顶放散阀、均压阀、上密阀、柱塞阀、下密阀的顺序开关来实现高炉的正常下料,通过控制α、β、γ来实现高炉布料。
料面检测设备采用机械探尺与雷达探尺相配合。
装料流程:焦炭、烧结矿等各种入炉原料由料车运到炉顶,倒入受料斗中,受料斗最多可装4车料。
料罐放散完毕后打开上密阀和柱塞阀向料罐装料。
装料完成后料罐进行均压。
一旦高炉准备接受下一批炉料就进行布料,首先打开下密阀并将料流调节阀打开至设定开度,料罐中的炉料通过料流调节阀流到旋转的布料溜槽上。
在布料期间,通过γ射线探测料流,该装置可发出料罐清空信号。
一旦料罐清空,关闭料流调节阀和下密封阀,打开放散阀进行放散,准备下一次装料。
布料流程:一批料中,允许焦矿设定两个不同的料线位置。
当探尺达到规定的料线位置后,自动提升到位,发出布料信号,下密封阀打开,布料溜槽进行启动。
β角旋转到设定速度并且到达布料位置,开启料流调节阀,按照批重及规定的布料程序,调节料流调节阀开度和溜槽倾角,使每圈料流均匀、重量相等和首尾相接的向炉喉任意布料。
为了减少料头料尾不均匀现象,每批料布完后,布料角度自动步进60度。
图一高炉上料系统工艺流程图3、控制系统硬件配置整个上料系统采用一套PLC系统,两台上位机完成对整个上料系统的监控及数据采集等。
自动控制系统采用Schneider TSX Quantum 系列PLC硬件组成基础自动化系统。
采用M P7监控软件,编程软件采用Concept2.6,Windows 2000作为系统平台界面,组成计算机化的操作系统,实现人机通讯。
控制器与上位机之间采用环形工业以太网进行通讯。
主机控制单元接受由I/O接口收集的信号进行开关量和模拟量的处理后,将信号经I/O接口实现对设备的控制,与监控站及上位机通讯。
这个系统配置如图二所示:其中处理器采用昆腾系列140-CPU-534-14A,电源模块采用140-CPS-114-20,远程通讯模版采用140-NOE-771-01,I/O模板配置如下:数字量输入模板为140-DAI-753-00、140-D DI-353-00;数字量输出模板为140-DDO-353-00;模拟量输入模板为140-ACI-040-00;模拟量输出模板为140-ACO-130-00,远程I/O模版采用140 CRP 931 10、140 CRA 931 00。
4、矿槽炉顶上料系统控制功能4.1 槽下控制部分4.1.1 槽下控制范围及内容(1)实现对矿石、球团、烧结、焦炭等入炉原料的自动称量,并完成称量误差的自动补偿。
(2)实现槽下12个矿仓、12个称量斗、2条成品带、2条碎矿皮带、12台振动筛、4台给料机、1个翻板及碎焦系统的自动控制,实现自动备料和放料。
(3)可使用监控画面对上料系统设备的运行状态进行监视,对设备的运行进行软手/自动切换及手动启停设备,进行料单设定及更改等。
(4)对装料超时、放料超时、超满及设备运行故障等情况在“工艺流程画面”进行报警显示。
图二控制系统硬件配置4.1.2 矿石称量斗的称量控制当排料程序发出后,矿石称量斗闸门开,料排出。
当称量值为控制值(初始时为设定值的95%)的5%时,发出料空信号并关闭闸门,当闸门关好并称空好后,振动筛或给料机开始启动。
称量值到控制值(经补正)时,振动筛或给料机停机,进行满称量。
若达110%控制值(经补正)时发出声光报警信号。
振动筛或给料机启动Ts后,还未发出斗“满”信号,就发出上卡料报警信号。
4.1.3 矿石称量斗的排料顺序根据预先选定的装料程序,矿石中间称量斗一“空”且闸门关好,槽下翻板翻到位,矿石皮带机启动后,开始排料。
排料顺序:球团、杂矿单装时按料单内所填仓号的先后顺序进行排料(矿石称量斗排料最多不同时超过三个)。
混装时先排一斗的球团或杂矿(排料单内球团或杂矿对应仓号的第一个斗),再排小烧或振大烧。
当前一个称量斗闸门开启,发出空信号后,发出下一个斗排料指令。
排料斗的闸门开到位延时Ts后,还未发出斗“空”信号,则发出下卡料报警信号。
4.1.4 矿石中间称量斗称量控制矿石中间称量斗称量控制分三种情况:①大烧结矿振动筛供料:当矿石中间称量斗“空”,闸门关好,设定好则发出同侧烧结筛运转指令,称量值达到控制值(初始时为设定值的95%)时,烧结筛停机,称量结束。
称量值达110%控制值时发出音响报警信号。
振筛启动延时Ts后,还未发出斗“满”信号,则发出“上卡料”信号。
②矿石皮带机供料:当矿石中间斗料一“空”,并且闸门关好,槽下翻板翻好,便发出矿石皮带机运转指令,当排料斗均放过料后,发出矿石中间斗装好信号,并发出皮带机停机指令。
③矿石皮带机和大烧结振动筛完成混装当矿石中间斗料一“空”,并且闸门关好,槽下翻板翻好,便发出矿石皮带机运转指令,当相应的一个矿石排料斗放过料后,发出大烧结振筛启动指令,同时发出皮带机停机指令。
当称量发出“满”信号时,发出矿石中间斗装好信号。
4.1.5 焦炭称量控制当焦炭称量斗一“空”,闸门关好并设定好后,发出焦炭振动筛运转指令,开始称量,称量值达到控制值时(初始时为设定值的95%),发出振动筛停机指令,称量结束,若达110%控制值时,发出报警信号。
振筛启动延时Ts后,还未发出斗“满”信号,则发出“上卡料”信号。
4.2 炉顶控制部分4.2.1 炉顶控制范围及内容(1)炉顶上至料罐下至探尺各设备的顺序控制。
(2)无料钟串罐式炉顶的装料及均压、放散控制。
(3)料流调节阀开度(γ角)、布料溜槽倾动角(α角)、布料溜槽旋转角(β角)的控制。
4.2.2 炉顶装料控制上次布料结束且下密阀关到位后,程序发出申请装料信号,料车开始装料,受料斗满且料罐空,放散阀打开,在放散过程中,一旦打开放散阀并料罐内压力等于大气压力,则认为放散OK。
放散OK后开上密阀,上密阀开到位后开柱塞阀,料车开始下料。
延时一定时间后柱塞阀关闭,关放散阀,关上密阀,炉料装入料罐中后开均压阀开始均压。
这时受料罐发允许料车上行信号。
4.2.3 炉顶布料控制料罐满且上密关到位后,程序发出申请布料信号,此时探尺探测到设定料线后提探尺至零位。
均压好后关均压阀。
探尺提到零位后开始转动α、β。
布料溜槽倾动的正常工作角度范围是13-53度。
就地操作可以使溜槽倾角达到70度以便于拆卸溜槽。
当溜槽倾角小于12度或大于54度时,溜槽停止移动和转动并发出报警,只有在报警清除后才可以继续移动。
一旦降下探尺或探尺在高炉中时,溜槽倾角如果大于45度,必须锁定溜槽。
为了使溜槽的定位精度达到±0.2度的要求,在程序中对溜槽的倾动速度进行处理,溜槽开始以最大速度倾动,当与目标位置只相差2度时,以最大速度的三分之一倾动,这样可以精确的定位到目标位置。
溜槽的旋转由变频器驱动的交流电机驱动。
正常情况下溜槽不停的旋转,如果溜槽的倾角位置达到了上限或下限,或者探尺在炉内时溜槽倾角大于45度,溜槽要立即停止旋转并报警。
溜槽每4小时改变一次旋转方向,这样可以确保溜槽磨损平衡。
PLC根据炉顶料单和槽下传送来的布料代号给出料流调节阀γ的设定开度,控制料流调节阀打开到设定开度开始布料,当接受到料罐清空信号,料流调节阀首先完全打开才能关闭。
清空信号由射线检测和PLC的定时器共同完成,如果在料流阀打开后规定的时间后发出清空信号,则认为料罐已经清空,如果在规定的时间之前发出清空信号则认为是料罐堵塞,PLC将发出报警信号,该信号一直保持,只有料流阀完全打开并且确保料罐完全排空后才能解除。