高炉上料流程
(完整版)高炉炼铁工艺流程及主要设备简介
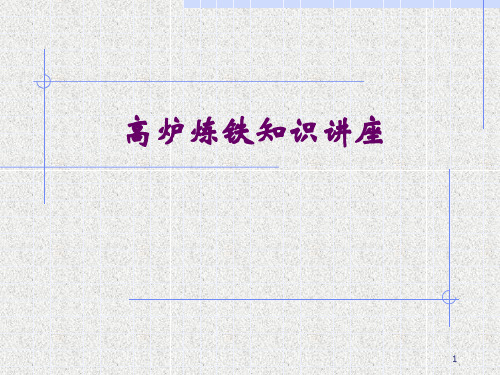
三、高炉冶炼主要设备简介
1、高炉 高炉炉本体较为复杂。 横断面为圆形的炼铁竖炉。用 钢板作炉壳,壳内砌耐火砖内衬。高炉本体自上而下 分为炉喉、炉身、炉腰、炉腹 、炉缸5部分。高炉生 产时从炉顶装入铁矿石、焦炭、造渣用熔剂(石灰 石),从位于炉子下部沿炉周的风口吹入经预热的空 气。在高温下焦炭中的碳同鼓入空气中的氧燃烧生成 的一氧化碳和氢气,在炉内上升过程中除去铁矿石中 的氧,从而还原得到铁。炼出的铁水从铁口放出。铁 矿石中未还原的杂质和石灰石等熔剂结合生成炉渣, 从渣口排出。产生的煤气从炉顶排出,经除尘后,作 为热风炉、加热炉、焦炉、锅炉等的燃料。高炉冶炼 的主要产品是生铁 ,还有副产高炉渣和高炉煤气。
1—高炉;2—重力除尘器;3 — 布袋除尘器; 4—调压阀组
23
三、高炉冶炼主要设备简介 重力除尘
24
三、高炉冶炼主要设备简介
箱体除尘: 由重力除尘后的荒煤气进入箱体进行布 袋过滤,最后成为净煤气。要求净煤气 粉尘量小于10毫克。
25
高炉冶炼主要设备简介
刮板机
26
高炉冶炼主要设备简介
27
高炉冶炼主要设备简介
炉渣和生铁定期通过铁口外排。通过炉前撇渣器进行渣 铁分离,铁水通过铁水罐运到炼钢或铸铁。炉渣经过 水淬后,输送到渣场。
高炉炼铁的主产品是生铁,副产品是高炉煤气、水渣、 炉尘。
5
二、高炉炼铁原理
6
三、高炉冶炼主要设备简介
高护炼铁设备组成有:①高炉本体;②供料设备;③ 送风设备;④喷吹设备;⑤煤气处理设备;⑥渣铁处 理设备。 通常,辅助系统的建设投资是高炉本体的4~5倍。生 产中,各个系统互相配合、互相制约,形成一个连续 的、大规模的高温生产过程。高炉开炉之后,整个系 统必须日以继夜地连续生产,除了计划检修和特殊事 故暂时休风外,一般要到一代寿命终了时才停炉。 高炉炼铁系统(炉体系统、渣处理系统、上料系统、 除尘系统、送风系统)主要设备简要介绍一下。
高炉炼铁工艺流程简介
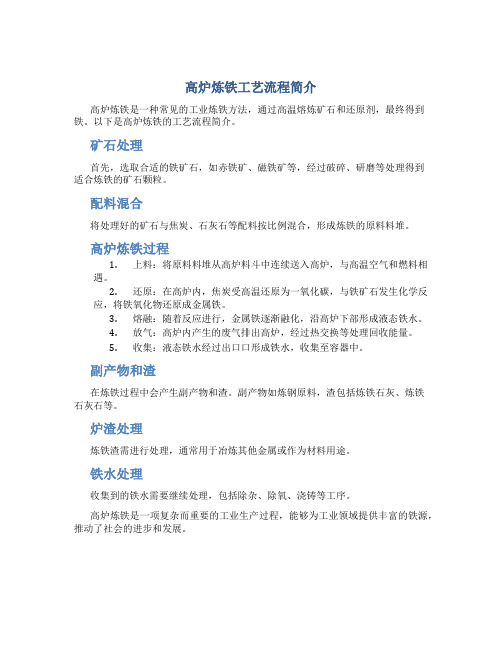
高炉炼铁工艺流程简介
高炉炼铁是一种常见的工业炼铁方法,通过高温熔炼矿石和还原剂,最终得到铁。
以下是高炉炼铁的工艺流程简介。
矿石处理
首先,选取合适的铁矿石,如赤铁矿、磁铁矿等,经过破碎、研磨等处理得到
适合炼铁的矿石颗粒。
配料混合
将处理好的矿石与焦炭、石灰石等配料按比例混合,形成炼铁的原料料堆。
高炉炼铁过程
1.上料:将原料料堆从高炉料斗中连续送入高炉,与高温空气和燃料相
遇。
2.还原:在高炉内,焦炭受高温还原为一氧化碳,与铁矿石发生化学反
应,将铁氧化物还原成金属铁。
3.熔融:随着反应进行,金属铁逐渐融化,沿高炉下部形成液态铁水。
4.放气:高炉内产生的废气排出高炉,经过热交换等处理回收能量。
5.收集:液态铁水经过出口口形成铁水,收集至容器中。
副产物和渣
在炼铁过程中会产生副产物和渣。
副产物如炼钢原料,渣包括炼铁石灰、炼铁
石灰石等。
炉渣处理
炼铁渣需进行处理,通常用于冶炼其他金属或作为材料用途。
铁水处理
收集到的铁水需要继续处理,包括除杂、除氧、浇铸等工序。
高炉炼铁是一项复杂而重要的工业生产过程,能够为工业领域提供丰富的铁源,推动了社会的进步和发展。
高炉卷扬上料岗位安全操作规程范本

高炉卷扬上料岗位安全操作规程范本一、适用范围本操作规程适用于高炉卷扬上料岗位,旨在保障操作人员的人身安全和设备正常运行。
二、操作流程1. 准备工作:(1)检查卷扬设备及其周边区域是否处于正常状态,如有异常情况应及时上报维修;(2)佩戴个人防护装备,包括头盔、防护眼镜、手套等;(3)检查卷扬机驱动装置、制动装置和绳索是否齐全并正常运行。
2. 上料操作:(1)确认被提升物体的重量和形状,选择合适的吊具;(2)确认吊具连接牢固,并保证安全系数充足;(3)控制卷扬机开关,使被提升物体顺利升至目标位置。
3. 安全预警:(1)操作人员需时刻注意卷扬机设备的运行情况,如发现异常应立即停止操作并上报;(2)在操作过程中如有突发情况,操作人员应立即切断电源并采取紧急救援措施。
4. 现场保洁:(1)操作结束后,将吊具归位并保持设备和现场清洁,防止杂物堆积;(2)妥善保管和维护卷扬设备,定期进行检修和保养。
5. 安全培训:(1)定期组织操作人员进行安全培训,强化安全意识和操作技能;(2)不得擅自招募未经培训的人员从事卷扬上料操作。
三、注意事项1. 操作人员应具备操作技能和相应证书,且符合岗位要求;2. 操作前要严格检查设备和工作环境,确保处于良好状态;3. 操作过程中要站稳脚跟,避免通过卷扬设备放置非操作人员;4. 遇到异常情况要及时停机处理,切勿强行进行操作;5. 操作时要随时注意周围环境和设备状态,以免造成安全事故;6. 操作结束后要及时关闭设备并做好设备的保养和维修。
四、紧急救援措施1. 发生可燃气体泄漏时,立即切断电源并采取逃生措施;2. 发生火灾时,立即启动灭火设备并采取逃生措施;3. 发生设备故障时,立即切断电源,并通知相关人员进行维修。
五、安全防护责任1. 企业要建立完善的安全管理制度,明确各岗位的安全责任;2. 严格执行安全操作规程,确保操作人员的安全;3. 配备并培训专业的安全管理人员,负责协调安全工作;4. 定期组织安全演练和应急培训,提高突发事件的应对能力。
高炉上料控制

备用的电机号 4 2 3 1
5、称量误差补正及称量显示
5.1、称量误差补正的控制
5.1.1、简要说明:各种原、燃料均设误差补正。 补正的方式 称量误差补正的原则是本称量漏斗的称量误差由该斗补, 与其它斗无关。设有两种补正方式: ⑴本次的称量误差待下次称量时补正。 ⑵累积误差补正即把每次的称量误差累计到一定量时进 行补正。最大累积误差值(可调)暂定如下: 矿石:200kg, 杂矿:150kg, 焦炭:100kg。
6、X-601及Y-601胶带机废铁检除装置
在X-601矿石胶带机和Y-601焦炭胶带机上各设一套废 铁检除装置。该装置为机电一体化,当废铁经过金属探测 器时,将信号发送给废铁检除装置,则废铁检除装置按预 先设定的程序自动将混入物料中的铁块检除。
7、设备的操作与联锁要求
矿槽系统电控设备约33种,75套设备。除电动葫 芦及传动室吊车不参与联锁外,其余设备在自动运转 时必须保持各设备之间的联锁关系,粉矿仓料位计及 碎焦仓仓下电动闸门参与返矿系统的联锁控制(粉矿 仓料位计及碎焦仓仓下电动闸门属返矿系统,其控制 要求见机械贮运专业提供的相关资料)。为防止误操 作及保护设备,手动操作时应保留必要的安全联锁,
6 炉顶探尺对炉内物料的跟踪、记录与监视 7). 装料系统装料制度、装入待的设定、料线设定、装料 循环周期的处理 8). 空焦装入方式及运转控制 9). 装料操作参数的设定、实际装入操作的数据收集、处 理 10). 装入系统设备的操作与监视 11). 装料系统设备故障处理
2.2、主工艺系统基本控制 2.2.1、炉顶压力选择 设有高压操作和常压操作选择。 2.2.2、控制选择 全自动→1批料(Charge)自动→ 1小批料
2、高炉装料制度
高炉的装料制度为: C↓O↓ C-焦炭 O-矿石(烧结矿、块矿及球团矿)
高炉卷扬上料岗位安全操作规程(三篇)

高炉卷扬上料岗位安全操作规程第一章总则第一条为确保高炉卷扬上料岗位的安全生产,保障工作人员的人身安全和设备的正常运行,制定本安全操作规程。
第二条高炉卷扬上料岗位的工作人员必须按照本规程的要求进行操作,严禁违反操作规程进行工作。
第三条工作人员必须参加相关的安全培训并通过培训考核后方可上岗。
第四条高炉卷扬上料岗位的工作人员必须定期进行职业健康检查,确保身体健康符合上岗要求。
第二章岗位责任与权限第五条高炉卷扬上料岗位的责任人为岗位负责人,负责组织、指挥和管理岗位工作。
第六条岗位负责人主要职责包括:1. 组织制定、修订安全操作规程并进行宣传;2. 监督岗位工作人员遵守安全操作规程;3. 负责高炉卷扬上料岗位的安全检查和事故调查处理;4. 定期组织开展安全培训和演练;5. 对岗位工作人员进行考核和评价。
第三章安全操作规程第七条工作人员上岗前必须熟悉所操作设备的结构、性能和使用方法,并须定期参加设备操作技能培训和考核,确保具备安全操作的能力。
第八条工作人员必须穿戴符合要求的劳动防护用品,并按要求进行佩戴。
第九条工作人员必须保持良好的工作状态,严禁饮酒、吸烟、咀嚼口香糖等影响工作安全的行为。
第十条工作人员必须按照设备操作规程进行操作,并确保操作正确、稳定。
第十一条工作人员必须定期检查设备的运行情况,及时发现和解决问题,并做好相关记录。
第十二条工作人员必须定期维护设备,确保设备处于良好的工作状态。
第十三条高炉卷扬上料岗位的工作人员必须按照规定的程序进行设备检修和维护,严禁擅自进行设备的拆卸和修理。
第十四条工作人员必须按照安全规定进行设备开关的操作,严禁擅自开关设备,尤其是在设备正在工作时。
第十五条工作人员必须遵守岗位管理制度,严禁与工作无关的人员靠近工作区域。
第十六条工作人员必须清理工作区域,确保设备周围的通道畅通无阻。
第十七条工作人员必须懂得紧急情况的处理方法,并定期参加相关培训和演练,提高应急处理的能力。
第十八条安全岗位的工作人员必须随时保持联系并保持通讯设备的畅通,确保能及时和其他人员进行沟通。
高炉炼铁工艺流程
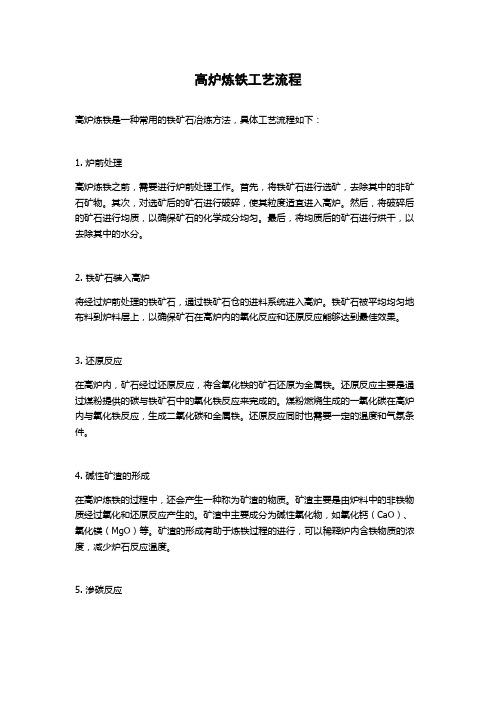
高炉炼铁工艺流程高炉炼铁是一种常用的铁矿石冶炼方法,具体工艺流程如下:1. 炉前处理高炉炼铁之前,需要进行炉前处理工作。
首先,将铁矿石进行选矿,去除其中的非矿石矿物。
其次,对选矿后的矿石进行破碎,使其粒度适宜进入高炉。
然后,将破碎后的矿石进行均质,以确保矿石的化学成分均匀。
最后,将均质后的矿石进行烘干,以去除其中的水分。
2. 铁矿石装入高炉将经过炉前处理的铁矿石,通过铁矿石仓的进料系统进入高炉。
铁矿石被平均均匀地布料到炉料层上,以确保矿石在高炉内的氧化反应和还原反应能够达到最佳效果。
3. 还原反应在高炉内,矿石经过还原反应,将含氧化铁的矿石还原为金属铁。
还原反应主要是通过煤粉提供的碳与铁矿石中的氧化铁反应来完成的。
煤粉燃烧生成的一氧化碳在高炉内与氧化铁反应,生成二氧化碳和金属铁。
还原反应同时也需要一定的温度和气氛条件。
4. 碱性矿渣的形成在高炉炼铁的过程中,还会产生一种称为矿渣的物质。
矿渣主要是由炉料中的非铁物质经过氧化和还原反应产生的。
矿渣中主要成分为碱性氧化物,如氧化钙(CaO)、氧化镁(MgO)等。
矿渣的形成有助于炼铁过程的进行,可以稀释炉内含铁物质的浓度,减少炉石反应温度。
5. 渗碳反应在高炉内,碳通过渗碳反应进一步与铁进行反应,生成碳化物。
这个过程通常需要在高炉底部的温度比较高的炉渣中进行,以确保足够的反应速率。
碳化物生成后,还需要通过进一步的处理来使其转变为可用的铁。
6. 炉缸维护和清理高炉炼铁过程中,会产生一些固体杂质物质,如炉渣和金属铁结晶等。
这些杂质会在高炉底部形成一层坚硬的物质,称为炉缸。
定期对高炉进行炉缸维护和清理是必要的,以保证高炉运行的正常和稳定。
7. 铁水和渣化处理高炉炼铁过程中,会产生两种产品,一种是铁水,另一种是矿渣。
铁水通过高炉底部的铁口流出,进入铁水包。
然后,将铁水通过通道输送到后续的冶金工艺中进行进一步的处理。
矿渣则从高炉底部的渣口流出,进入矿渣车,最终被运到矿渣堆存放。
高炉槽下上料系统操作说明书
槽下配料上料电脑操作系统使用说明书1. 概述本系统实现了槽下14个振动筛、4个给料机、14个称量斗门、6条皮带、14个除尘闸门、1个上料卷扬的画面上的手自动操作。
具有手动时灵活、可靠和自动时运行稳定的特点。
槽下分为两部分进行控制,从给料机到中间斗为备料流程,从中间斗到炉顶为上料流程。
见下图。
2.基本操作2.1. 单台设备的操作2.1.1. 给料机和振动筛的操作▲自动状态时设备被程序所控制,按照连锁条件运行。
当切换到手动时设备由操作窗口内的“启动”,“停止”按钮来控制▲连锁状态选择,设备连锁时会对流程前后的设备的运行状态有影响,如振动筛不运行,给料机不能运行;皮带机不运行,振动筛不能运行;称量斗非空,振动筛不能运行;⏹手动状态下解锁时一定要考虑周全,以应对非正常情况。
⏹自动状态下不允许切换到解锁。
▲起停操作。
左键单击相应按钮,便可以在手动时操作设备。
自动时无效。
▲状态显示。
⏹PC控制方式。
方框显示绿色表示现场操作箱上切换到远程操作,否则为就地。
⏹自动状态。
方框显示绿色表示设备切换到远程且自动状态。
⏹故障状态。
方框显示黄色表示设备的电气回路出现故障且设备停机。
⏹电源状态。
方框显示绿色表示⏹运行状态。
方框显示红色表示设备处于停止状态,方框显示绿色表示设备处于运行状态。
2.1.2.称量斗门的操作▲自动状态选择⏹自动状态选择时设备被程序所控制,按照连锁条件运行。
当切换到手动时设备由操作窗口内的“启动”,“停止”按钮来控制▲连锁状态选择⏹设备连锁时会对流程前后的设备的运行状态有影响,如皮带机不运行,斗门不能关闭,称量斗非满,则斗门不能打开。
⏹手动状态下解锁时一定要考虑周全,以应对非正常情况。
⏹自动状态下不允许切换到解锁。
▲开关操作按钮⏹左键单击相应按钮,便可以在手动时操作设备。
自动时无效。
▲回路状态显示。
⏹PC控制方式。
方框显示绿色表示现场操作箱上切换到远程操作,否则为就地。
⏹自动状态。
方框显示绿色表示设备切换到远程且自动状态。
高炉料车上料操作规程
高炉料车上料操作规程高炉料车上料操作规程一、目的与范围高炉料车上料操作规程的目的是确保高炉上料过程的安全、高效进行,保障高炉正常运行。
本规程适用于高炉料车的上料操作。
二、术语与定义1. 高炉料车:用于将原料送入高炉的专用运输设备。
2. 原料:指用于高炉冶炼的铁矿石、焦炭和燃料等。
3. 上料井口:装有上料设备的高炉顶部的孔洞。
4. 上料设备:用于将原料送入高炉的机械装置。
三、操作流程1. 准备工作(1)操作人员须熟悉高炉料车的构造和性能,并定期进行检查和维护。
(2)检查高炉料车是否有异常情况,如漏料、挂钩等问题。
(3)检查上料设备是否正常运行,如输送带、斗式提升机等。
2. 上料操作(1)按照上料计划,准确掌握高炉料车的运行时间和上料量。
(2)确认上料井口的开启情况,确保无阻塞和漏料现象。
(3)启动高炉料车,确保各项指标正常。
(4)按照上料量的要求,调节物料的投放速度和数量。
(5)注意观察上料过程中的异常情况,如漏料、卡料等,及时进行处理。
(6)上料完成后,关闭上料井口,停止高炉料车的运行。
四、安全注意事项1. 操作人员必须穿戴好安全装备,如安全帽、安全鞋等。
2. 操作人员要经过专门培训,掌握高炉料车的操作技能。
3. 严禁在高炉料车运行时进行维修和清理工作。
4. 上料过程中,要保持与同事的良好沟通,密切配合,避免发生事故。
5. 发生突发情况时,要第一时间报告相关部门,并采取紧急措施进行处理。
五、操作记录与检查1. 上料操作应由专门的操作人员进行,并记录工作过程及各项指标。
2. 定期对高炉料车进行检查和维护,并做好相关记录。
3. 上料操作过程中如有异常情况,应及时记录,并向相关部门报告。
六、责任与违规处理1. 高炉料车的操作人员对于上料操作的安全负有直接责任,如发生事故,由操作人员承担相关责任。
2. 违反本规程的操作人员,将视情节轻重进行相应的违规处理,包括警告、停工、作废等。
七、附则本规程经高炉生产部门审定,并定期进行评估和修改,以适应生产需求的变化。
南钢规程5-上料(炉顶)0310
南京钢铁联合有限责任公司技术标准炼铁新厂工艺技术规程(讨论稿)高炉系统高炉上料工岗位(无料钟部分)目录1.上料系统设备参数 (2)2.装料系统设备参数 (2)3.炉顶系统结构与功能 (2)4.工艺流程 (6)5.岗位作业程序与交接班制度 (7)6.炉顶上料操作规程 (8)8.上料系统工艺技术操作 (47)9.事故处理 (49)高炉上料工(无料钟)操作技术规程1.上料系统设备参数1.1上料主皮带机主要性能:带宽:1.4m 输送能力带速:2m/s 运矿时:2300t/h水平长:约320 m 运焦时:550t/h倾角:约10.9°传动电机:四台,约220kW/台1.2上料设备作业率根据计算,在最大利用系数为2.5t/(m3.d)、最高日产铁量为5000t时,正常焦批14t/ch、矿批62.7t/ch,装料周期时间394秒,装料间隔时间670秒,其上料系统的作业率为58.8%。
2.装料系统设备参数主要设备参数:装料装臵型式上罐固定的中心卸料式串罐无料钟料罐有效容积(单个) 45m3炉喉直径 7600 mm炉顶压力~0.2Mpa,最高~0.25MPa炉顶温度 <280o C装入方式 C↓O↓布料形式扇形,定点,单环,多环布料溜槽长度 3.500m布料溜槽转速 8rpm(7.5s/r)布料留槽倾动速度 1.6 o/s溜槽倾角范围 16o~52.7o溜槽布料档位和所对应的角度关系:3.炉顶系统结构与功能高炉炉顶设备为引进卢森堡PW公司的串罐式无料钟炉顶,其结构如图1和表1所示:图1:无料钟炉顶结构图表1:无料钟炉顶结构说明书3.1无料钟的基本功能1)布料功能根据溜槽旋转和倾动的有机结合,可实现四种布料方式—多环、单环、扇形、定点。
在四种布料方式中,以多环布料为基本的布料方式。
单环布料设有自动和手动,而点布料和扇形布料只设手动,仅在特殊情况时使用。
多环布料是按装料程序中的设定,自动地将物料布在炉喉断面上的一种布料方式。
高炉上料技术操作规程
高炉上料技术操作规程1.岗位职责1.1上料班长岗位职责1.1.1负责上料班的生产工作,带领全班人员完成工作任务。
1.1.2负责落实督促本工种各岗位安全和技术操作规程的执行。
1.1.3负责上料系统的检查、维护、保养、巡检工作落实和布臵。
1.1.4负责上料区域现场环境的管理和监督。
1.1.5负责检查上料系统各项记录及台帐的完成情况。
1.1.6负责上料系统设备的备品备件计划申报落实工作。
1.1.7负责上料人员安全和操作技能培训。
1.1.8负责对上料人员的工作考核及执行。
1.1.9负责及时完成临时交办的工作。
1.2上料主操岗位职责1.2.1负责上料班的生产工作,带领全班人员完成工作任务。
1.2.2负责落实督促本工种各岗位安全和技术操作规程的执行,对违章行为有权利制止,保证安全生产。
1.2.3负责上料区域设备卫生及现场管理。
1.2.4负责上料皮带、筛子、炉顶设备和上料系统机电设备检查、维护、保养、巡检,排除一般设备故障,负责与设备点检员交流,共同安排上料系统的日修、周修、定修计划,并配合检修及验收试车工作。
1.2.5负责上料人员安全学习、教育学习和业务素质培训,组织本班人员坚持落实岗位交接班制度,做好本班工作。
1.2.6负责上料区域和责任设备卫生的清扫。
1.2.7严格执行交接班,参加班前会及单位、分厂、公司组织的各项活动。
1.3上料工岗位职责1.3.1熟悉本岗位的作业环境,了解危险源及控制办法。
1.3.2负责槽下各皮带、电子秤、筛子、炉顶上料设备及上料系统机电设备的检查、维护、保养、巡检,排除一般设备故障,配合检修及验收试车工作。
1.3.3负责对上料系统计算机、仪表进行监视,严格按照高炉值班室规定的装料制度和料线进行上料操作,正确填写各项原始记录日志,确保信息传递及时、准确。
1.3.4随时掌握各种原燃料消耗及仓储情况,注意矿石和焦炭含粉率和水分,发现混料和原料有较大变化时及时向工长报告。
负责称量值、称量余量、水份、装入程序、净焦、偏差修正、控制参数等的设定、变更和确认,作业报表及点检表的填写。
- 1、下载文档前请自行甄别文档内容的完整性,平台不提供额外的编辑、内容补充、找答案等附加服务。
- 2、"仅部分预览"的文档,不可在线预览部分如存在完整性等问题,可反馈申请退款(可完整预览的文档不适用该条件!)。
- 3、如文档侵犯您的权益,请联系客服反馈,我们会尽快为您处理(人工客服工作时间:9:00-18:30)。
1. 1#振筛启动自动1.1#振筛选自动2.1#振筛软自动3.1#仓有料空信号4.1#称量斗关到位且无开关双信号5.1#仓没有振满《振满后自动停止》6.1#---10#振筛控制相似2. 南(北)提升机自动运行1.南提升机选自动2.南提升机没有现场控制信号3.南提升机软自动4.焦筛起动信号5.碎焦提升机无电机保护6.碎焦提升机无现场保护《拉绳,跑偏》7. 南北提升机自动控制相似3. 碎矿(焦)皮带自动运行1.碎矿选自动2.碎矿皮带软自动3.矿振筛运行信号4.碎矿无现场控制信号5.碎矿电机无保护6.碎矿拉绳无保护7.碎矿与碎焦运行相似4. 仓斗门开条件1.1#仓选自动2.1#仓软自动3.1#有允开信号4.1#仓显示仓满信号5.1#仓称满好《无空满双信号》6.坑斗准备好7.主矿皮带运行8.1#振筛未启动运行9.1#仓斗门开限位10.1#称量斗未禁用11.与1#称量斗关动作联锁5. 仓斗门关条件1.1#仓选自动2.1#仓软自动3.1#仓画面显示空信号4.1#振筛无启动运行信号5.1#称量斗未禁用6.1#称量斗关限位7.与1#称量斗开动作联锁8.1-11号称量斗自动开关斗门相似6. 主矿皮带自动运行1.主矿选自动2.主矿软自动3.左坑准备好,翻板置右到位信号时,无翻板置左到位信号或者右坑斗准备好,翻板置左到位信号时,无翻板置右到位信号4.矿仓有允开信号5.主矿电机无故障保护6.主矿无现场拉绳等保护7.主矿与主焦运行相似7.左坑准备好的条件1.备左斗信号《右车到底脉冲信号,右车在底或按初始化按钮,右车在底》2.左坑斗关到位3.翻板居右到位2秒后4.左坑斗没有开位信号5.左坑空或左坑没有空信号但选仓没有放完料6.左坑未禁用7.左车没有空信号,8.左坑准备好与右坑准备好相似8. 翻板自动置左1.翻板选自动2.翻板软自动3.备右斗《料单初始化后,左车到底信号或者左车到底脉冲后左车到底信号》4.左坑没有禁用5.左车没有空6.主焦没运行7.主矿没运行8.翻板居左限位9.与翻板置右动作联锁10.翻板居右与置左条件相似9. 坑斗自动开阀1.左闸门选自动2.左闸门软自动3.翻板居左《准备向右坑放料》4.左车在底信号5.左坑没有空信号6.右车无在底信号7.左坑没有禁用8.左坑开限位9.与左坑关动作联锁10. 坑斗自动关阀1.左闸门选自动2.左闸门软自动3.左坑放空有空信号4.左坑关限位5.与左坑斗开动作联锁6. 右坑斗自动开阀比左坑多两个条件1)主焦没有运行2)主矿没有运行3)右坑关与左坑关其它条件一样11. 左车自动上行条件1.料车选自动2.画面没按下急停按钮3.料车画面软自动4.左车自动上行使能信号或左车强制上行《画面按钮》5.右车没有上行使能信号6.挡料阀关到位时,挡料阀无开动作,受料斗没有满信号或画面按下赶料关时,闸板阀开到位后赶料时间到了以后7.左车上限位8.右车到底联锁《右车到底有信号不能左车上行》12. 左车自动上行使能信号1.左车在底信号2. 右车没在底信号3.左车到底后的一个脉冲信号4. 左坑右坑都关到位时,左坑放过料或左坑禁用13. 右车自动上行条件1.料车选自动2. 画面没按下急停按钮3. 料车画面软自动4. 右车自动上行使能信号或右车强制上行《画面按钮》5.左车没有上行使能信号6.挡料阀关到位时,挡料阀无开动作,受料斗没有满信号或画面按下赶料开关时,闸板阀开到位后赶料时间到了以后7. 右车上限位8. 左车到底联锁《左车到底有信号右车不能上行》14. 右车自动上行使能信号1.右车在底信号2. 左车没在底信号3.右车到底后的一个脉冲信号4. 左坑右坑都关到位时,右坑放过料或右坑禁用15. 布料状态1.按下炉顶料单初始化,将1传送到DB52。
DBW2即为申请装料状态或正在布料状态,有了布料结束信号3秒后,将1传送到DB52. DBW2,即为申请装料状态2.在申请装料状态下,挡料阀开到位即变为正在装料状态3.料罐满,上密关到位时即为申请布料状态4.在申请布料状态下,下密开到位,即为正在布料状态5.处于正在布料状态下,下密没关到位信号,下密开到位,溜槽倾动α偏差在死区,料罐没有空,上密关到位,上密无开位信号,以上条件满足500毫秒后即为布料开始6.正在布料状态下,下密关到位,料罐空,此时为布料结束状态7.正在布料状态,布料结束3秒后即为申请装料状态8.受料斗满信号条件1)受料斗批次为0 或1 或画面强制受料斗满2)闸板阀在关位3)画面没有强制受料斗空4)受料斗料空检测方式0车数,料位计时,受料斗料位计或受料斗料空检测方式0 车数1,料位计无动作时,闸板阀无打开信号,此时为受料斗满9.受料斗空条件1)当受料斗满或强制受料斗满脉冲以后2)料罐没有空信号3)受料斗没有满信号4)画面没有强制料罐空信号,此时受料斗为空状态10.料罐满1)受料斗空1秒后没有在正在布料状态时为料罐满11.料罐空1)β圈数等于设定圈数时或强制料罐空信号2)画面没有强制料罐满脉冲3)闸板阀没有开位,此时为料罐空状态16. 自动打开放散阀条件1.放散均压选自动《操作台选择》2.放散阀选软自动《电脑画面选自动》3.受料斗满4.料罐空5.处于申请装料状态6.禁止一均时二均关到位或禁二均时一均关到位7.下密关到位8.放散开阀限位9.与放散阀关动作联锁10.上密关到位17.自动关放散阀条件1.放散均压选自动2.放散阀软自动3.上密关到位4.申请布料状态5.放散关阀限位6.与放散开动作联锁18. 自动开上密条件1.上下密闸板选自动2.上密软自动3.申请装料状态4.受料斗满5.下密关到位6.放散开好《包括放散强制开好》7.一均或二均关到位8.上密开限位9.闸板阀关到位10.料罐空11.与上密关联锁《有关上密动作信号上密不能打开》19. 自动关上密条件1.上下密闸板选自动2.挡料阀关到位3.上密选软自动4.料罐满5.上密关限位《关到位》6.与开上密联锁上密显示故障,有开或关信号,但一分钟后开或关信号,即判断故障点击故障,解除按钮消除故障信号20. 自动开挡料阀条件1.挡料阀上下密选择自动2.闸板阀软自动3.受料斗满4.申请装料状态5.上密开到位6.下密关到位8.与闸板关动作联锁21.自动关闸板阀条件1.上下密;闸板阀选自动2.闸板阀软自动3.闸板阀全开到位延时时间到4.受料斗料空5.闸板阀关阀限位6.与闸板阀开动作联锁22.自动开均压条件1.放散均压选自动2.均压软自动3.申请布料状态4.1#放散或2#放散关到位《选放散》5.上密关到位6.下密关到位7.提探尺动作信号8.均压1#开限位《开到位》9.1#均压未禁用10.与关均压1动作联锁23. 自动关均压条件1.放散均压选自动2.均压软自动3.下密已经开到位4.节流已经开到位5.均压1#关限位6.没有禁用均压1#7.与均压1开动作联锁均压故障信号开关阀一分钟后无到位信号即显示故障按解除按钮均压有禁用1均和禁用2均24. 自动开下密条件1.上下密闸板选择自动2.下密软自动3.探尺在零位或上限4.申请布料状态5.上密关到位6.放散关到位7.没有按下禁开下密按钮8.均压好(料罐与炉顶压之差小于20 Pa)9.下密无开位信号11.与关下密动作联锁25. 自动关下密条件1.上下密闸板选自动2.下密软自动3.节流阀关到位脉冲信号4.下密关限位5.与开下密动作联锁下密故障:开关阀一分钟后无到位信号按下密解除故障按钮26. 节流阀自动开关允许Q11.01.节流阀自动开阀使能允许1)节流阀选自动2)节流阀软自动3)下密开到位4)溜槽倾动α角,偏差绝对值在死区5)正在布料状态或申请布料状态6)γ偏差为正数7)节流阀没有全开到位信号8)料罐没有空,γ偏差没有在死区或料罐已空,但布料未结束2. 节流阀自动关阀使能允许1)节流选自动2)节流软自动3)下密开到位4)溜槽倾动α,偏差绝对值在死区5)正在布料状态6)γ偏差为负7)节流没有关限位8)料罐没有空,γ角绝对值没在死区或料罐已空,布料结束,节流阀全开到位后3.节流阀自动开阀调节1)节流阀选自动2)节流阀软自动3)申请布料状态《或正在布料状态》4)料罐没有放空5)下密无关到位信号6)下密开到位7)设定的γ角大于实际值(1)偏差绝对值γ偏差大于6时在将6000传到PQW518中调整(2)偏差绝对值γ偏差在6-0.5之间将500送到PQW518中(3)偏差绝对值γ偏差小于0.5时为γ偏差死区,节流将0传到PQW518停止调节8)当处于正在布料状态,料罐空,节流阀没开到最大位,γ布料未结束时将6000传送到PQW518,大幅度地开到全开限位,停止工作9)节流阀无报警信号10)节流阀没开到位信号4. 节流阀自动关阀调整1)节流阀选自动2)节流阀软自动3)正在布料状态4)料罐没有空信号5)下密无关到位信号6)下密开到位7)偏差为负,绝对值大于6时,将-8000输入到PQW518绝对值小于6大于0.5时,将-500传送到PQW518进行关阀调节绝对值小于0.5时为死区,将0传送到PQW518停止调节8)节流阀无报警信号9)节流阀无关到位信号10)当布料结束,节流阀全开到位1秒后,将-8000传送到PQW518最大幅度地全关节流阀到关限位27. 溜槽倾动α角自动控制1. 溜槽倾动PIC自动使能(Q11.4)α角向上倾的条件1)溜槽选自动2)溜槽软自动3)α选择PLC,控制使能4)α偏差为正5)α偏差绝对值不在死区6)溜槽α没全开到位7)α没向下使能动作信号8)α无报警信号2. 溜槽α下倾PLC自动使能1)溜槽α选自动2)溜槽α软自动3)溜槽α没全关到位4)α选择PLC控制使能5)α偏差不在死区6)偏差为负7)无报警信号8)与向上倾动作联锁3. α速度定位调整1)溜槽α选自动2)溜槽α软自动3)绝对值小于3大于0.5时,且不在死区4)此时向上使能将 -1500输入到PQW5165)绝对值大于3时将-10000输入PQW5166)以上动作为偏差为正时向上倾动7)偏差为负向下使能调整8)溜槽α没关到位,9)小于3大于0.5时且不在死区将1500输入PQW51610)大于3时且不在死区,将10000输入到PQW51611)布料没有结束时,在申请布料状态或正在布料状态时,将设定值减去实际角度得到偏差值来控制上倾或下倾12)布料结束后,料罐空时将3传送到设定值,减去实际得到偏差来控制4.将0传送到PQW5161)溜槽选择自动2)溜槽软自动α偏差在死区3)向上使能时,α开到位,溜槽α软自动4)向下使能时,α关到位,溜槽α软自动28. 溜槽自动正转或反转条件1.溜槽旋转电机选自动2.在画面上按启动按钮,将β处于运行状态3.溜槽PLC一开始运行即是正转状态4.没有按下画面停止按钮5.没有按下画面反转按钮,6.溜槽自动正转,在以上状态4小时之后,自动反转,再4小时之后自动正转,7.按画面设定每圈多少频率时,将相应数输入到PQW512或PQW514中29. 左探尺自动提尺条件1.探尺选自动2.左尺没停用《操作台》3.当左尺为准时,左尺到料线。