六西格玛应用实例
六西格玛经典案例

六西格玛经典案例在六西格玛质量管理方法中,通过分析和改进业务流程,以减少缺陷和提高效率,从而实现优秀质量和高度效益。
以下是三个经典的六西格玛案例。
1. Motorola的六西格玛实践Motorola是六西格玛的奠基者之一、20世纪80年代,Motorola采用六西格玛方法,以改进生产过程并提高质量。
在一个以缺陷率而不是零缺陷为标准的产业中,Motorola在一年内将缺陷率从超过三十万个降低到每百万个产品中只有5个。
六西格玛的成功引起了其他公司的注意,并成为其他公司实施质量管理的典范。
2. General Electric(GE)的六西格玛实施GE是六西格玛的早期采用者,它将六西格玛引入公司的各个部门和业务领域。
公司的首席执行官杰克·韦尔奇在1995年将六西格玛作为公司的战略重点。
GE在实施过程中的一个成功案例是其航空发动机业务部门,该部门通过六西格玛方法降低了生产过程中的缺陷率,并提高了航空发动机的性能和可靠性。
GE的成功证明了六西格玛可以在各种行业中实现卓越的结果。
3.美国政府的六西格玛应用六西格玛方法不仅在企业界取得成功,而且在政府部门中也有很好的应用。
美国政府决定在1995年引入六西格玛方法,以提高效率并减少浪费。
例如,美国联邦航空管理局(FAA)使用六西格玛方法改进了飞行管制和管理过程,减少了航班延误和事故。
美国海军也采用了六西格玛方法来改善军舰维护和修理过程,提高了战斗力和减少了成本。
以上是六西格玛的三个经典案例,它们都展示了通过六西格玛方法来实现质量改进和效益提高的潜力。
这些案例证明了六西格玛是一个非常有力的质量管理方法,可以在各个领域带来显著的结果。
无论是在制造业、服务业还是政府部门,六西格玛都能够提供一个可靠的框架来解决质量和效率方面的挑战。
精益六西格玛的改善案例

精益六西格玛的改善案例案例:汽车制造流程改善背景:汽车制造公司在生产过程中遇到了一些问题。
产品质量不稳定,交付时间延长,成本高涨,因此需要通过改善流程来提高生产效率和降低成本。
目标:-提高产品质量稳定性,降低缺陷率-缩短交付时间,提高客户满意度-降低制造成本,提高利润率方法:1.项目选择:选择一个关键的制造流程进行改善。
在该公司中,组装过程是最关键且容易出现问题的环节,因此选择组装流程作为改善项目。
2.流程分析:通过流程图和价值流图,对组装流程进行详细分析。
识别出每个环节中的瓶颈和浪费,如等待时间、运输时间、不必要的重复工作等。
3.数据收集:收集关于缺陷率、交付时间和成本的数据。
这些数据将成为决策的基础。
4.根本原因分析:使用工具如鱼骨图、五力模型、因果图等,找出导致问题的根本原因。
可能的原因包括不合理的工作流程、不合适的设备、员工技能不足等。
5.解决方案设计:根据根本原因分析的结果,设计出改进方案。
例如,通过优化工作流程、提高设备质量、加强员工培训等。
6.实施改进:在一定范围内进行试点实施改进方案,收集数据并评估效果。
根据数据的结果,对方案进行调整和改进,直到达到预期的效果。
7.控制改进:建立一套监控体系,确保改进效果能够持续。
通过设立关键绩效指标(KPI)和改进计划,对改进方案进行监控和调整。
结果:经过精益六西格玛方法学的改进,该汽车制造公司取得了显著的效果:-产品质量稳定性得到明显提高,缺陷率显著降低。
-交付时间缩短,客户满意度有了显著提升。
-制造成本明显降低,利润率得以提高。
结论:。
服务业六西格玛应用案例
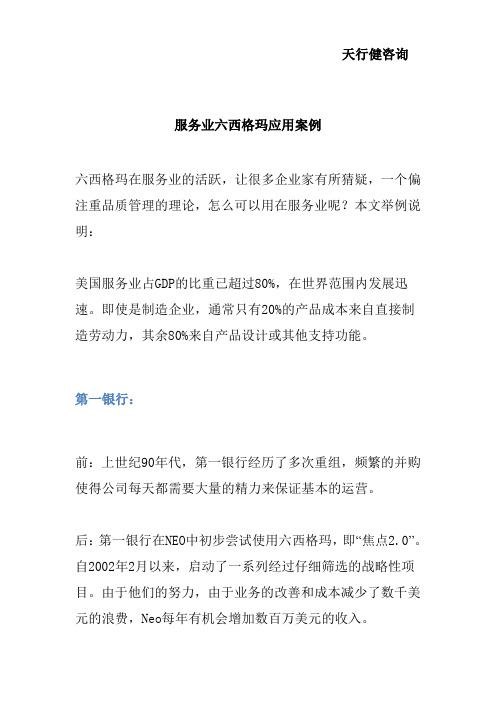
服务业六西格玛应用案例
六西格玛在服务业的活跃,让很多企业家有所猜疑,一个偏注重品质管理的理论,怎么可以用在服务业呢?本文举例说明:
美国服务业占GDP的比重已超过80%,在世界范围内发展迅速。
即使是制造企业,通常只有20%的产品成本来自直接制造劳动力,其余80%来自产品设计或其他支持功能。
第一银行:
前:上世纪90年代,第一银行经历了多次重组,频繁的并购使得公司每天都需要大量的精力来保证基本的运营。
后:第一银行在NEO中初步尝试使用六西格玛,即“焦点2.0”。
自2002年2月以来,启动了一系列经过仔细筛选的战略性项目。
由于他们的努力,由于业务的改善和成本减少了数千美元的浪费,Neo每年有机会增加数百万美元的收入。
洛克希德马丁公司:
前:该公司设定了降低成本37亿美元的目标。
它成立于1995年,经过一系列的兼并和收购。
包括20家相对独立的子公司,文化和流程也各不相同。
除了核心制造业务,外围还有一个更大的“服务”部分(采购、行政、设计和工程等)。
公司如何团结我们实现这样一个具有挑战性的目标?
后:他们采用了六西格玛。
在服务时间和成本控制方面,开展了大量项目。
之后,公司债务不断下降,收入状况良好,降低成本的目标正在加快,仍有大量订单。
这些组织意识到一些基本事实:
应用六西格玛可以有效地提高质量;
提高质量可以有效地促进发展;
实施六西格玛可以降低复杂的绩效,提高发展的速度和质量。
六西格玛案例分析
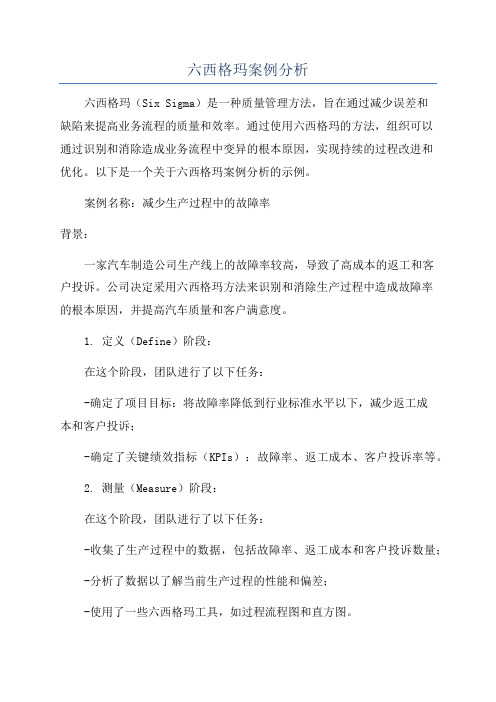
六西格玛案例分析六西格玛(Six Sigma)是一种质量管理方法,旨在通过减少误差和缺陷来提高业务流程的质量和效率。
通过使用六西格玛的方法,组织可以通过识别和消除造成业务流程中变异的根本原因,实现持续的过程改进和优化。
以下是一个关于六西格玛案例分析的示例。
案例名称:减少生产过程中的故障率背景:一家汽车制造公司生产线上的故障率较高,导致了高成本的返工和客户投诉。
公司决定采用六西格玛方法来识别和消除生产过程中造成故障率的根本原因,并提高汽车质量和客户满意度。
1. 定义(Define)阶段:在这个阶段,团队进行了以下任务:-确定了项目目标:将故障率降低到行业标准水平以下,减少返工成本和客户投诉;-确定了关键绩效指标(KPIs):故障率、返工成本、客户投诉率等。
2. 测量(Measure)阶段:在这个阶段,团队进行了以下任务:-收集了生产过程中的数据,包括故障率、返工成本和客户投诉数量;-分析了数据以了解当前生产过程的性能和偏差;-使用了一些六西格玛工具,如过程流程图和直方图。
3. 分析(Analyze)阶段:在这个阶段,团队进行了以下任务:-确定了导致故障率升高的根本原因;-使用了五力分析和鱼骨图等工具,以识别可能的原因;-根据数据和分析结果,确定了一个或多个关键影响故障率的因素。
4. 改进(Improve)阶段:在这个阶段,团队进行了以下任务:-开发了改进计划,包括减少故障率的具体措施和时间表;-实施了改进措施,并记录了结果。
5. 控制(Control)阶段:在这个阶段,团队进行了以下任务:-实施了独立检查和监控措施,以确保改善措施的可持续性;-追踪关键绩效指标,如故障率、返工成本和客户投诉;-确立了持续改进的机制,以确保过程持续优化。
通过使用六西格玛方法,该汽车制造公司成功降低了生产过程中的故障率。
在实施改进措施后,故障率从10%降低到行业标准的3%以下,成功降低了返工成本和客户投诉率。
此外,公司在生产线上建立了严格的质量控制措施和监控机制,以确保持续改进和优化。
精益六西格玛案例

精益六西格玛案例
精益六西格玛是一种管理方法,它结合了精益生产和六西格玛的优点,旨在提
高效率和质量。
下面我们来看一个实际的案例,了解精益六西格玛是如何在实践中发挥作用的。
某汽车零部件制造公司在生产过程中遇到了一些问题,导致了生产效率低下和
产品质量不稳定。
经过分析,他们决定引入精益六西格玛方法来改善生产流程。
首先,他们进行价值流分析,找出了生产过程中的浪费和瓶颈。
然后,他们采
用精益工具,如5S和Kanban,对生产车间进行了重新布局和标准化。
同时,他们
还对员工进行了培训,让他们更好地理解和运用精益工具。
在改善生产流程的同时,公司还引入了六西格玛的方法,通过数据分析和流程
控制,找出了造成产品质量不稳定的根本原因,并采取了相应的改进措施。
经过一段时间的努力,公司取得了显著的成效。
生产效率得到了提高,产品质
量稳定性也得到了保障。
公司的客户满意度得到了提升,市场竞争力也得到了增强。
通过这个案例,我们可以看到精益六西格玛在实际中的应用效果。
它不仅可以
帮助企业提高效率和质量,还可以带来客户满意度和市场竞争力的提升。
综上所述,精益六西格玛是一种非常有效的管理方法,它可以帮助企业解决生
产过程中的问题,提高效率和质量,实现持续改进和持续增长。
希望更多的企业能够引入精益六西格玛,实现可持续发展。
精益6Σ管理在药企中应用实例

精益6Σ管理在药企中应用实例精益六西格玛是在精益生产和六西格玛管理基础上发展起来的,是一种整合了精益生产和六西格玛管理特点和优势的管理模式;是一种可以发现、解决、预防产品或流程中问题的系统方法论;是一种可以实现成本控制、质量优化、交付及时、利润提升,提升客户满意度的卓越管理体系,是适用于现代制造企业乃至金融、服务等各个行业的管理系统。
目前,越来越多的企业开始选择精益六西格玛作为其改善策略,有数据显示,GE、摩托罗拉、波音、ITT等84家世界级制造企业中有38%的企业选择精益六西格玛作为其改善策略,并取得了显著的改善效果。
近年来,精益六西格玛正逐渐被中国企业所应用,国内制药企业作为制造业的重要组成部分,也在积极地探索和推行精益六西格玛管理,大连辉瑞、广东天普、华润医药、上海医药等多家制药企业(集团)已经取得了较好的效果。
1、精益六西格玛的推进步骤和常用工具1.1推进步骤精益六西格玛的推进一般采用DMAIC模式,即界定阶段(define)、测量阶段(measure)、分析阶段(analyze)、改进阶段(improve)和控制阶段(control)。
①界定阶段:根据客户的关键需求,识别需要改善的产品或过程,要明确问题,确定关键质量或过程特性;②测量阶段:对现状进行测量和评估,识别影响关键质量或过程特性的因素,确定基准和改善目标,并确汄测量系统的有效性;③分析阶段:通过数据分析,确定关键影响因素;④改进阶段:通过改善的实施,消除或减少关键影响因素,优化关键质量或过程特性,以减少缺陷或降低变异;⑤控制阶段:固化改善成果。
1.2常用工具精益六西格玛常用工具包括六西格玛的常用的数据统计和质量管理工具,也包括精益生产常用的管理工具。
具体如表1所示。
2、精益六西格玛在改善产品收率中的应用实例2.1定义、测量阶段2.1.1确定改善对象A产品为某制药企业的主要原料药产品,年产量约占该企业原料产量的20%。
该产品生产车间经改造后,验证及试生产期间,其平均收得率较历史水平有较大幅度下降,下降了约10个百分点,且呈现明显的数值波动。
6西格玛运作实例

6西格玛运作实例在企业管理领域中,6西格玛是一种重要的质量管理方法,它旨在通过减少变异和改进流程,提高产品和服务的质量。
本文将以一个实例来说明6西格玛的实际运作。
在某电子产品制造公司,他们一直致力于提高生产线的效率和减少产品缺陷率。
为了解决这些问题,他们决定引入6西格玛方法来改进他们的生产流程。
第一步是选取一个重要的生产指标作为改进目标。
在这个例子中,公司选择了产品的缺陷率作为改进目标,因为这直接影响到产品的质量和客户满意度。
第二步是进行数据收集和分析。
公司收集了过去一年的产品缺陷数据,并将其整理成表格和图表,以便更好地分析。
通过分析数据,他们发现主要的缺陷问题是在产品组装过程中出现的。
接下来,公司成立了一个改进团队,由不同部门的员工组成,包括生产、质量控制和工程师等。
团队利用6西格玛工具中的DMAIC(定义、测量、分析、改进、控制)方法来引导改进过程。
首先,团队定义了缺陷问题的范围和目标,并明确定义了改进的关键要素。
他们使用质量流程图来细化产品组装过程,并识别出潜在的问题环节。
然后,团队测量了当前的缺陷率,收集了更多的数据来评估该问题的严重程度,并确定了改进的重点。
他们使用直方图和散点图等统计工具来对数据进行分析。
在分析阶段,团队通过根因分析确定了导致缺陷的主要原因。
他们使用鱼骨图来追溯问题,并运用5W1H(谁、什么时候、为什么、在哪里、怎样、如何)方法来深入挖掘问题的根本原因。
在确定了根本原因后,团队开始制定改进方案并进行实施。
他们设计了一个新的组装工艺流程,并对关键环节进行了改进。
此外,他们也培训了生产工人,以提高他们的操作技能和质量意识。
最后,团队制定了一系列的控制措施,以确保改进效果的持续性和稳定性。
他们建立了一套产品检验机制,定期对生产线进行检查,并对关键环节进行监控。
经过数个月的改进实施和控制,该公司的产品缺陷率得到了显著降低。
他们通过6西格玛方法的应用,实现了生产效率的提高和产品质量的提升。
六西格玛改进案例

六西格玛改进案例以六西格玛改进案例为题,列举如下10个案例:1. 生产流程改进案例:在一个制造业公司,生产流程中存在着许多瑕疵品。
为了提高产品质量,该公司采用了六西格玛方法进行改进。
通过分析生产过程中的关键环节,确定了引起瑕疵品的主要原因,并通过改进工艺和设备,减少了瑕疵品的产生率。
2. 供应链管理改进案例:一家零售公司的供应链管理存在着库存过剩和缺货的问题,导致了销售额下降。
为了解决这个问题,该公司运用了六西格玛方法,对供应链中的各个环节进行了优化。
通过提高库存预测的准确性,优化订货策略,以及改进供应商管理,该公司成功解决了库存过剩和缺货问题。
3. 客户投诉处理改进案例:一家电信运营商的客户投诉率较高,影响了公司的声誉。
为了改善客户满意度,该公司运用了六西格玛方法,对客户投诉处理流程进行了改进。
通过提高投诉处理的效率和质量,该公司成功降低了客户投诉率,并提升了客户满意度。
4. 销售流程改进案例:一家保险公司的销售流程存在着繁琐和低效的问题,导致了销售人员的工作效率低下。
为了提高销售业绩,该公司采用了六西格玛方法,对销售流程进行了改进。
通过简化流程、优化销售工具和培训销售人员,该公司成功提升了销售人员的工作效率和销售业绩。
5. 质量管理改进案例:一家制药公司的质量管理体系存在着缺陷,导致了产品质量不稳定。
为了提高产品质量,该公司采用了六西格玛方法,对质量管理体系进行了改进。
通过加强质量控制、改进检验方法和加强员工培训,该公司成功提升了产品质量的稳定性。
6. 项目管理改进案例:一个IT项目存在着进度延误和成本超支的问题,导致了项目无法按时交付。
为了解决这个问题,该公司采用了六西格玛方法,对项目管理进行了改进。
通过优化项目计划、加强资源管理和改进沟通机制,该公司成功提高了项目的进度控制和成本控制能力。
7. 售后服务改进案例:一家家电企业的售后服务存在着响应速度慢和问题解决率低的问题,导致了客户的不满意。
- 1、下载文档前请自行甄别文档内容的完整性,平台不提供额外的编辑、内容补充、找答案等附加服务。
- 2、"仅部分预览"的文档,不可在线预览部分如存在完整性等问题,可反馈申请退款(可完整预览的文档不适用该条件!)。
- 3、如文档侵犯您的权益,请联系客服反馈,我们会尽快为您处理(人工客服工作时间:9:00-18:30)。
六西格玛管理战略
为每一家追求卓越的企业提供绩效快速突破的理念和工具
企业运营千头万绪,管理与质量是永远不变的至理。
在全球化经济背景下,一项全新的管理模式在美国摩托罗拉和通用电气两大巨头中试行并取得立竿见影的效果后,逐渐引起了欧美各国企业的高度关注,这项管理便是六西格玛模式。
六西格玛是一种能够严格、集中和高效地改善企业流程管理质量的实施原则和技术。
它包含了众多管理前沿的先锋成果,以”零缺陷”的完美商业追求,带动质量成本的大幅度降低,最终实现财务成效的显著提升与企业竞争力的重大突破。
西格玛即希腊字σ的译音,是统计学家用语衡量工艺流程中的变化性而使用的代码。
企业也可以用西格玛的级别来衡量在商业流程管理方面的表现。
传统的公司一般品质要求已提升至3sigma.这就是说产品的合格率已达至99.73%的水平,只有0.27%为次货。
又或者解释为每一千货产品只有2.7件为次品。
很多人认为产品达至此水平已非常满意。
可是,根据专家研究结果证明,如果产品达到99.73%合格率的话,以下事件便会继续在现实中发生:每年有20,000次配错药事件;每年不超过15,000婴儿出生时会被抛落地上;每年平均有9小时没有水、电、暖气供应;每星期有500宗做错手术事件;每小时有2000封信邮寄错误。
由此可以看出,随着人们对产品质量要求的不断提高和现代生产管理流程的日益复杂化,企业越来越需要象六西格玛这样的高端流程质量管理标准,以保持在激烈的市场竞争中的优势地位。
事实上,日本已把”6 Sigma”作为他们品质要求的指标。
六个西格玛的管理方法重点是将所有的工作作为一种流程,采用量化的方法分析流程中影响质量的因素,找出最关键的因素加以改进从而达到更高的客户满意度。
如果你正在寻找一种使企业降低质量缺陷和服务偏差并保持持久性的新方法,那么不用犹豫了。
六西格玛将以重大的财务成效证明你的选择是正确的。
美国通用电气公司首席执行官韦尔奇先生在2000年年报中指出:
六西格玛所创造的高品质,已经奇迹般地降低了通用电气公司在过去复杂管理流程中的浪费,简化了管理流程和降低了材料成本。
六西格玛的实施已经成为介绍和承诺高品质创新产品的必要战略和标志之一。
实施六西格玛对于一个企业来说,不仅仅只是一系列的训练。
它意味着整个企业文化从防护性的标准化管理到放开思想改革创新的突破性理念。
六西格玛在提供行之有效的管理方法和流程技术的基础上,为企业培养了具备组织能力、激励能力、项目管理技术和数理统计诊断能力的领导者,这些人才是企业适应变革和竞争的核心力量。
他们将最先进的工作方法和最新的电脑技术,应用到一个简单的流程模式DMAIC中,通过追求零缺陷运行和改善流程达到使顾客满意的快速突破性改善。
以达到每一个环节的不断改善(Continuous Improvement)的战略目标。