直流调速系统的仿真
基于MATLAB的直流调压调速控制系统的仿真
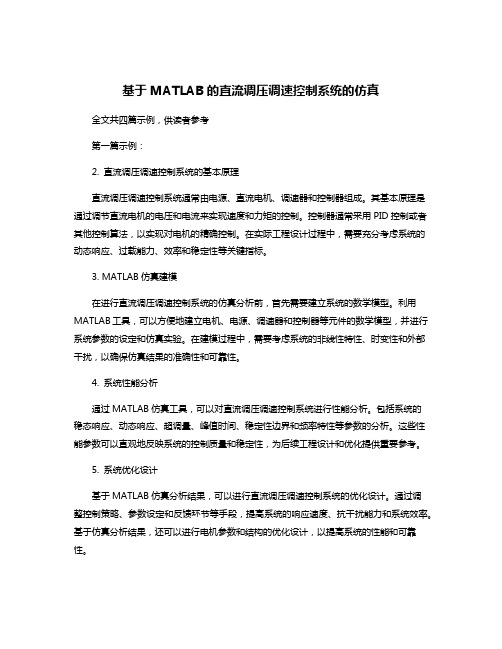
三、MATLAB仿真环境搭建
MATLAB提供了Simulink仿真工具,可以方便地进行控制系统的建模和仿真。在搭建直流调压调速控制系统的仿真环境时,首先需要对电机的特性进行建模,包括电机的电动力学方程、电机的转矩-转速特性曲线等。然后,设计控制器的结构和参数,通过Simulink建立相应的控制模型,最后进行仿真验证。MATLAB还提供了丰富的工具箱和函数库,如控制系统工具箱、电机控制工具箱等,能够方便地进行控制系统设计和分析。
2. 控制系统模型
在直流调压调速控制系统中,控制器起着至关重要的作用。常见的控制器包括PID控制器和模糊控制器。这些控制器可以根据电动机的工作状态和需求信号进行控制,实现对电动机速度和输出电压的精准控制。在进行仿真时,需要将控制器的数学模型结合到整个系统中,以实现对电动机的系统级控制。
在MATLAB中进行直流调压调速控制系统的仿真时,可以利用Simulink工具箱进行建模和仿真。Simulink是MATLAB的一个附加工具箱,提供了丰富的模块和功能,可以方便地对控制系统进行仿真和分析。以下是基于MATLAB的直流调压调速控制系统的仿真步骤:
五、实验结果与分析
通过MATLAB的仿真实验,我们可以得到直流调压调速控制系统的性能指标,如电机的转速曲线、电机的输出功率曲线等。根据仿真结果,我们可以对控制系统进行性能分析和优化,调整控制器的参数,改进控制策略,提高系统的稳定性和响应性能。通过仿真实验可以验证控制系统的设计是否满足实际要求,指导工程实践中的系统调试和优化。
直流调速系统的MATLAB仿真(参考程序)
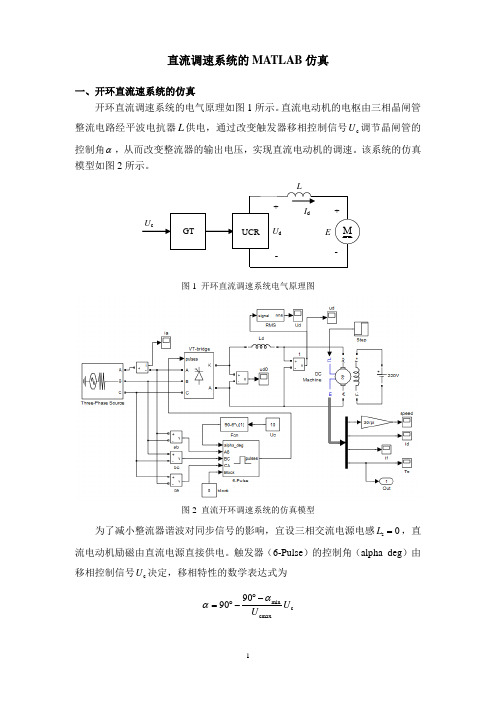
直流调速系统的MATLAB 仿真一、开环直流速系统的仿真开环直流调速系统的电气原理如图1所示。
直流电动机的电枢由三相晶闸管整流电路经平波电抗器L 供电,通过改变触发器移相控制信号c U 调节晶闸管的控制角α,从而改变整流器的输出电压,实现直流电动机的调速。
该系统的仿真模型如图2所示。
图1 开环直流调速系统电气原理图图2 直流开环调速系统的仿真模型为了减小整流器谐波对同步信号的影响,宜设三相交流电源电感s 0L =,直流电动机励磁由直流电源直接供电。
触发器(6-Pulse )的控制角(alpha_deg )由移相控制信号c U 决定,移相特性的数学表达式为minc cmax9090U U αα︒-=︒-在本模型中取min 30α=︒,cmax 10V U =,所以c 906U α=-。
在直流电动机的负载转矩输入端L T 用Step 模块设定加载时刻和加载转矩。
仿真算例1 已知一台四极直流电动机额定参数为N 220V U =,N 136A I =,N 1460r /min n =,a 0.2R =Ω,2222.5N m GD =⋅。
励磁电压f 220V U =,励磁电流f 1.5A I =。
采用三相桥式整流电路,设整流器内阻rec 0.3R =Ω。
平波电抗器d 20mH L =。
仿真该晶闸管-直流电动机开环调速系统,观察电动机在全压起动和起动后加额定负载时的电机转速n 、电磁转矩e T 、电枢电流d i 及电枢电压d u 的变化情况。
N 220V U =仿真步骤:1)绘制系统的仿真模型(图2)。
2)设置模块参数(表1) ① 供电电源电压N rec N 2min 2200.3136130(V)2.34cos 2.34cos30U R I U α++⨯==≈⨯︒② 电动机参数 励磁电阻:f f f 220146.7()1.5U R I ===Ω 励磁电感在恒定磁场控制时可取“0”。
电枢电阻:a 0.2R =Ω电枢电感由下式估算:N a N N 0.422019.119.10.0021(H)2221460136CU L pn I ⨯==⨯≈⨯⨯⨯电枢绕组和励磁绕组间的互感af L :N a N e N 2200.21360.132(V min/r)1460U R I K n --⨯==≈⋅T e 60600.132 1.262π2πK K ==⨯≈ T af f 1.260.84(H)1.5K L I === 电机转动惯量2222.50.57(kg m )449.81GD J g ==≈⋅⨯③ 额定负载转矩L T N 1.26136171.4(N m)T K I ==⨯≈⋅表1 开环直流调速系统主要模型参数3)设置仿真参数:仿真算法odel5s ,仿真时间5.0s ,直流电动机空载起动,起动2.5s 后加额定负载L 171.4N m T =⋅。
直流调速系统仿真.doc

直流调速系统仿真目录一.直流调速系统仿真1.开环直流调速系统的仿真2.单闭环有静差转速负反馈调速系统的建模与仿真3.单闭环无静差转速负反馈调速系统的建模与仿真4.单闭环电流截止转速负反馈调速系统的建模与仿真5.单闭环电压负反馈调速系统的建模与仿真6.单闭环电压负反馈和带电流正反馈调速系统的建模与仿真7.单闭环转速负反馈调速系统定量仿真8.双闭环直流调速系统定量仿真9.PWM直流调速系统仿真二.双闭环直流调速系统1双闭环直流调速系统的工作原理1.1双闭环直流调速系统的介绍1.2双闭环直流调速系统的组成1.3双闭环直流调速系统的稳态结构图和静特性1.4双闭环直流调速系统的数学模型2系统设计方法及步骤2.1系统设计的一般原则2.2电流环设计2.2.1确定时间常数2.2.2选择电流调节器结构2.2.3选择电流调节器参数2.2.4校验近似条件2.3转速环设计2.3.1确定时间常数2.3.2选择转速调节器结构2.3.3选择转速调节器参数2.3.4校验近似条件三.Simulink环境中的系统模型、仿真结果及分析3.1Matlab和Simulink简介3.2 Matlab建模与仿真3.3电流环的MA TLAB计算及仿真3.3.1电流环校正前后给定阶跃响的MA TLAB计算及仿真3.3.2绘制单位阶跃扰动响应曲线并计算其性能指标3.3.3单位冲激信号扰动的响应曲线3.3.4电流环频域分析的MA TLAB计算及仿真3.4转速环的MA TLAB计算及仿真3.4.1转速环校正前后给定阶跃响应的MA TLAB计算及仿真3.4.2绘制单位阶跃信号扰动响应曲线并计算其性能指标3.4.3单位冲激信号扰动的响应曲线3.4.4转速环频域分析的MA TLAB计算及仿真4V-M双闭环直流不可逆调速系统的电气原理总图摘要直流调速系统有多种调速方法,各种方法各有优缺点。
就性能而言,闭环性能优于开环,双闭环性能优于单闭环,然而对于实际系统,还要考虑系统的成本和复杂性,因此各种方法都有一定的适应场合。
直流调速系统的MATLAB仿真参考程序汇总
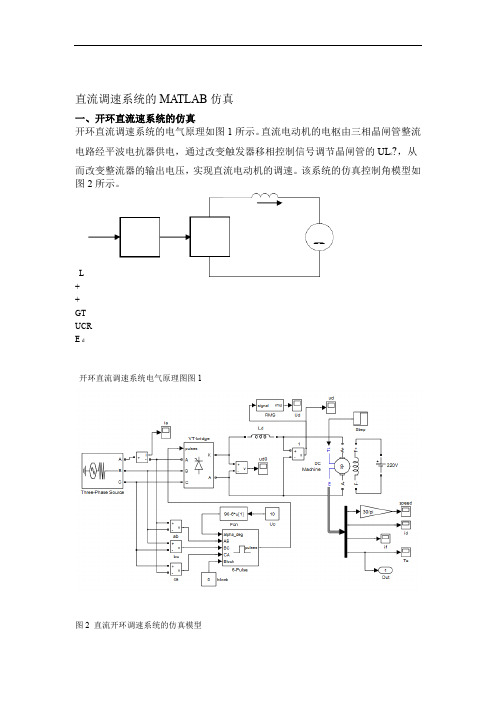
直流调速系统的MA TLAB仿真一、开环直流速系统的仿真开环直流调速系统的电气原理如图1所示。
直流电动机的电枢由三相晶闸管整流电路经平波电抗器供电,通过改变触发器移相控制信号调节晶闸管的U L c ,从而改变整流器的输出电压,实现直流电动机的调速。
该系统的仿真控制角模型如图2所示。
L++GTUCRE d--开环直流调速系统电气原理图图1图2 直流开环调速系统的仿真模型L?0,直为了减小整流器谐波对同步信号的影响,宜设三相交流电源电感s流电动机励磁由直流电源直接供电。
触发器(6-Pulse)的控制角(alpha_deg)由U 决定,移相特性的数学表达式为移相控制信号c???90?min U?90??c U cmax 1??。
在直流电动机的负载,所以,在本模型中取U?10V6??30?90U?ccmaxmin转矩输入端用Step模块设定加载时刻和加载转矩。
T L仿真算例1已知一台四极直流电动机额定参数为,,136AIU?220V?NN22。
励磁电压,励磁电,,220VminUR?0.2??1460rn?/m?22.5NGD?fNa流。
采用三相桥式整流电路,设整流器内阻。
平波电抗器??1.5A0.3RI?recf。
仿真该晶闸管-直流电动机开环调速系统,观察电动机在全压起动20mHL?d n、电磁转矩、电枢电流和起动后加额定负载时的电机转速及电枢电压的uTi ded变化情况。
220V?U N仿真步骤:1)绘制系统的仿真模型(图2)。
2)设置模块参数(表1)①供电电源电压U?RI220?0.3?136NNrec130(V)U???2?2.34?cos302.34cos?min②电动机参数励磁电阻:U220f)146.7(?R???f I1.5f励磁电感在恒定磁场控制时可取“0”。
电枢电阻:?0.2R?a电枢电感由下式估算:CU0.4?220N?19.1?L?19.1?0.0021(H)a2pnI2?2?1460?136NN L:电枢绕组和励磁绕组间的互感af U?RI220?0.2?136NNa?K?0.132(V?min/r)?e n1460N 2 6060K??0.132?K?1.26eTπ2π2K1.26T0.84(H)??L?af1.5I f电机转动惯量222.5GD2 )??0.57(kg?mJ?9.814?4g 额定负载转矩③模块参数名参数,直流电动机空载起动,5.0s3)设置仿真参数:仿真算法odel5s,仿真时间m171.4N??T 。
直流调速系统的仿真研究

一、转速反馈控制直流调速系统的仿真仿真各环节参数:直流电动机:额定电压UN=220V,额定电流IdN=55A,额定转速nN=1000r/min,电动机电动势系数Ce=0.192V·min/r。
假定晶闸管整流装置输出电流可逆,装置的放大系数Ks=44,滞后时间常数Ts=0.00167s。
电枢回路总电阻R=1.0Ω,电枢回路电磁时间常数Tl=0.00167s,电力拖动系统机电时间常数Tm=0.075s。
转速反馈系数α=0.01V·min/r。
对应额定转速时的给定电压Un*=10V。
1、转速负反馈闭环调速系统仿真仿真框图:(1)突加负载空载启动分析:由以上两图,根据动态性能指标可以知道空载启动电流环响应速度快于转速环,电流环产生的超调量很大,转速环稳定后实现无静差。
转速能够跟紧紧跟随给定的变化。
(2)去掉积分作用仿真框图:分析:如果把积分部分取消,改变比例系数,可以得到不同静差率的响应曲线甚至振荡曲线。
(3)当kp=0.25,1/T=3,得到的转速相应曲线如下分析:系统的转速响应无超调,但调节时间很长。
(4)当kp=0.8,1/T=15得到的仿真曲线如下:分析:系统的转速响应的超调较大(18%),但快速性较好。
(5)0.6s后突减负载仿真框图:分析:0.6s之前系统已经趋于稳定,在0.6s时突加负载,使得转速稍有降落,但最终通过双闭环,系统转速稳定下来,较之前比不变,系统电流有所升高,但最终通过双闭环调节稳定下来,且电流较之前升高(E不变,Ra减小,I增大)。
(6)0.6s后突加扰动仿真框图:分析:0.6s之前系统已经趋于稳定,在0.6s时突加扰动,转速上升,电流上升,经过双闭环调节,二者最后都趋于稳定,较之前数值都没有发生变化。
二、转速、电流反馈控制直流调速系统的仿真仿真各环节参数直流电动机:额定电压=220V,额定电流=308A,额定转速=1000r/min,电动机电动势系数=0.196V*min/r。
直流调速系统的MATLAB仿真(参考程序)

直流调速系统的MATLAB 仿真一、开环直流速系统的仿真开环直流调速系统的电气原理如图1所示。
直流电动机的电枢由三相晶闸管整流电路经平波电抗器L 供电,通过改变触发器移相控制信号c U 调节晶闸管的控制角α,从而改变整流器的输出电压,实现直流电动机的调速。
该系统的仿真模型如图2所示。
MU d+I dGTU cE +--UCR图1 开环直流调速系统电气原理图图2 直流开环调速系统的仿真模型为了减小整流器谐波对同步信号的影响,宜设三相交流电源电感s 0L =,直流电动机励磁由直流电源直接供电。
触发器(6-Pulse )的控制角(alpha_deg )由移相控制信号c U 决定,移相特性的数学表达式为minc cmax9090U U αα︒-=︒-在本模型中取min 30α=︒,cmax 10V U =,所以c 906U α=-。
在直流电动机的负载转矩输入端L T 用Step 模块设定加载时刻和加载转矩。
仿真算例1 已知一台四极直流电动机额定参数为N 220V U =,N 136A I =,N 1460r /min n =,a 0.2R =Ω,2222.5N m GD =⋅。
励磁电压f 220V U =,励磁电流f 1.5A I =。
采用三相桥式整流电路,设整流器内阻rec 0.3R =Ω。
平波电抗器d 20mH L =。
仿真该晶闸管-直流电动机开环调速系统,观察电动机在全压起动和起动后加额定负载时的电机转速n 、电磁转矩e T 、电枢电流d i 及电枢电压d u 的变化情况。
N 220V U =仿真步骤:1)绘制系统的仿真模型(图2)。
2)设置模块参数(表1) ① 供电电源电压N rec N 2min 2200.3136130(V)2.34cos 2.34cos30U R I U α++⨯==≈⨯︒② 电动机参数 励磁电阻:f f f 220146.7()1.5U R I ===Ω 励磁电感在恒定磁场控制时可取“0”。
实验一、开环直流调速系统的仿真实验
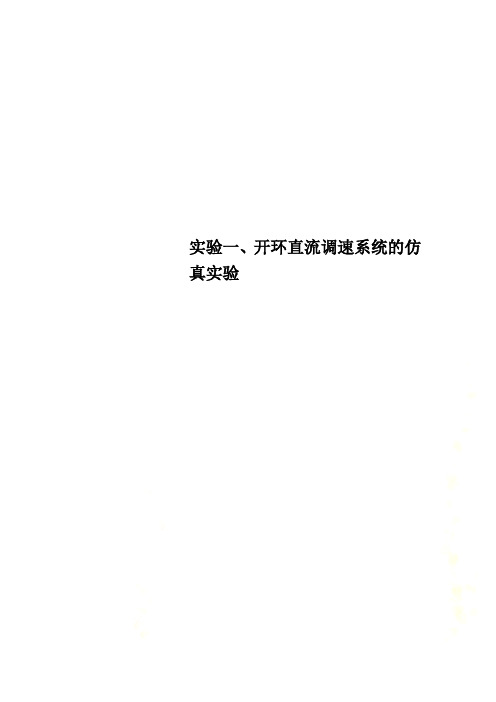
实验一、开环直流调速系统的仿真实验实验一 开环直流调速系统的仿真一、实验目的 1、熟悉并掌握利用MATLAB 中Simulink 建立直流调速系统的仿真模型和进行仿真实验的方法。
2、掌握开环直流调速系统的原理及仿真方法。
二、实验内容开环直流调速系统的仿真框图如图1所示,根据系统各环节的参数在Simulink 中建立开环直流调速系统的仿真模型,按照要求分别进行仿真实验,输出直流电动机的电枢电流Id 和转速n 的响应数据,绘制出它们的响应曲线,并对实验数据进行分析,给出相应的结论。
+—*n ()U s s s 1K T s +1/1l R T s +m R T se1C ()n s Ed ()I s +dL ()I s _图1 开环直流调速系统的仿真框图开环直流调速系统中各环节的参数如下:直流电动机:额定电压UN = 220 V ,额定电流IdN = 55 A ,额定转速nN = 1000 r/min ,电动机电势系数Ce= 0.192 V ·min/r 。
假定晶闸管整流装置输出电流可逆,装置的放大系数Ks = 44,滞后时间常数Ts = 0.00167 s 。
电枢回路总电阻R =1.0 Ω,电枢回路电磁时间常数Tl = 0.00167 s ,电力拖动系统机电时间常数Tm = 0.075 s 。
对应额定转速时的给定电压Un*=4.364V 。
三、实验步骤 1、根据开环直流调速系统的各环节参数建立空载时的Simulink 仿真框图,如图2所示。
图2 空载时开环直流调速系统的仿真框图2、设置合适的仿真时间,利用out 器件或示波器将相关数据输出到MATLAB 的Workspace中,并在MATLAB中利用plot(X,Y)函数绘制出空载时直流电动机的电枢电流Id和转速n的响应曲线,记录并分析实验数据,给出相应的结论。
3、根据开环直流调速系统的各环节参数建立带负载时的Simulink仿真框图,如图3所示。
转速反馈控制直流调速系统仿真.pptx

调节器参数的调整
K p 0.25
1 3
系统转速的响应是无超调、 但调节时间很长;
图2-56 无超调的仿真结果
16
第17页/共20页
K p 0.8
1 15
系统转速的响应的超 调较大、但快速性较 好。
图2-57 超调量较大的仿真结果
17
第18页/共20页
• SIMULINK软件的仿真方法为系统设计提供了仿真平台,可以选择合适的PI参数,满足系统的跟随性能指 标。
• 把鼠标移到期望的分支线的起点处,按下鼠标的右键,看到光 标变为十字后,拖动鼠标直至分支线的终点处,释放鼠标按钮, 就完成了分支线的绘制。
11
第12页/共20页
仿真启动按钮
图2-53 比例积分控制的无静差直流调速系统的仿真模型
12
第13页/共20页
仿真模型的运行
• (1)仿真过程的启动:单击启动仿真工具条的菜单项,则可启动仿真过程,再双击示波器模 块就可以显示仿真结果。
图2-45 比例积分控制的直流调速系统的仿真框图
1
第2页/共20页
仿真模型的建立
• 进入MATLAB,单 击MATLAB命令窗 口工具栏中的 SIMULINK图标,
• 或直接键入 SIMULINK命令,打 开SIMULINK模块浏
图览2-46器SI窗MU口LI口N,K模块浏览器窗 2 第3页/共20页
- 1、下载文档前请自行甄别文档内容的完整性,平台不提供额外的编辑、内容补充、找答案等附加服务。
- 2、"仅部分预览"的文档,不可在线预览部分如存在完整性等问题,可反馈申请退款(可完整预览的文档不适用该条件!)。
- 3、如文档侵犯您的权益,请联系客服反馈,我们会尽快为您处理(人工客服工作时间:9:00-18:30)。
直流调速系统的仿真1、直流电动机开环调速系统仿真直流开环调速系统的电气原理如图1所示。
直流电动机电枢由三相晶闸管整流电路经平波电抗器L供电,并通过改变触发器移相控制信号U c调节晶闸管的控制角,从而改变整流器的输出电压实现直流电动机的调速。
该系统的仿真模型如图2所示。
在仿真中为了简化模型,省略了整流变压器和同步变压器,整流器和触发同步使用同一交流电源,直流电动机励磁由直流电源直接供电。
触发器(6-Pulse图1 直流开环调速系统电气原理图2 直流电动机开环调速系统的仿真模型图3 移相特性Generator)的同步电压连接。
触发器的控制角(alpha —deg 端)通过了移相控制环节(shifter ),移相控制模块的输入是移相控制信号Uc (图2中Uc ),输出是控制角,移相控制信号Uc 由常数模块设定。
移相特性如图3所示。
移相特性的数学表达式为Uc Uc a a maxmin 9090-︒+︒= 在本模型中取︒=30min a ,V Ucm 10±=,所以Uc a 690+︒=。
在电动机的负载转矩输入端TL 接入了斜坡(Ramp )和饱和(Satutration)两个串联模块,斜坡模块用于设置负载转矩上升速度和加载的时刻,饱和模块用于限制负载转矩的最大值。
【例1】 已知直流电动机额定参数为U nom =220V ,I nom =136A ,nnom =1460r/min ,4级,Ra=0.21Ω,GD2=22.5N ·㎡。
励磁电压U f =220V ,励磁电流I f =1.5A 。
采用三相桥式整流电路,整流器内阻Rrec =1.3Ω。
平波电抗器Lp =200mH 。
仿真该晶闸管-整流电动机开环调速系统,观察电动机在全压起动和起动后加额定负载时电动机的转速、转矩和电流变化。
仿真步骤如下:(1)绘制系统的仿真模型如图2所示。
(2)设置模块参数1)供电电源电压为V V I R U U nom rec nom 12330cos 34.213621.0220cos 34.2min 2=︒⨯++=α 2)电动机参数如下:励磁电阻为Ω===7.1465.1/220/f f f I U R 励磁电感在恒定磁场控制时可取0。
电枢电阻Ω=21.0a R ,电枢电感由下式估算,即H H I pn CU L nom nom nom a 00021.01361460222204.01.1921.19=⨯⨯⨯⨯⨯== 电枢组和励磁af L 组互感为 因为r V r V n I R U C n o noa n o e m 132.0min/146013621.0220⋅=⋅⨯-=-=26.1132.0260260=⨯∑=∑e C K π所以H I K L f af 84.05.1/26.1/===∑ 电动机转动惯量为 22257.08.94/5.224/m kg m kg g GD J ⋅=⋅⨯==3)额定负载转矩为m N m N I C T n o m e L ⋅=⋅⨯⨯==225.17132.055.955.9(3)设置仿真参数。
仿真算法采用ode15s ,仿真时间为4s ,电动机空载起动,起动2.5s 后突加额定负载。
(4)启动真并观察结果。
仿真的结果如图4所示。
其中图4 所示为整流器输出端的电压波形(局部),图4 所示为经平波电抗器后电动机电枢两端电压波形,该波形较整流器输出端的电压波形脉动减少了许多,电压平均值在225V 左右符合设计要求。
图4c 和图4d 所示为电动机电枢回路电流和转速变化过程,在全压直接起动情况下,起动电流很大,在2.5s 左右起动电流下降为零(空载起动),起动过程结束,这时电动机转速上升到最高值。
在起动0.5s 后加额定负载,电动机的转速下降,电流增加。
图4e 所示为电动机的转矩变化曲线,转矩曲线与电流曲线成比例。
图4f 给出了工作过程中电动机的转矩-转速特性曲线。
通过仿真反映了开环晶闸管-直流电动机系统的空载起动和加载工作情况。
图4 晶闸管-直流电动机系统仿真结果a)整流器输出电压b)电枢两端电压c)电枢电流d)电动机转速e)电动机转矩曲线f)转矩-转速特性2、转速闭环控制的直流调速系统仿真晶闸管-直流电动机系统可以通过调节晶闸管控制角改变电动机电枢电压实现调速,但是存在两个问题,第一,全压起动时,起动电流大。
第二,转速随负载变化而变化,负载越大,转速降落越大,难以在负载变动时保持转速的稳定,而满足生产工艺的要求。
为了减小负载波动对电动机转速的影响可以采取带转速负反馈的闭环调速系统,根据转速的偏差来自动调节整流器的输出电压,从而保持转速的稳定。
带转速负馈的有静差直流调速系统的结构如图5所示。
系统由转速给定环节Un ,放大倍数为Kp的放大器、移相触发器CF、晶闸管整流器和直流电动机M、测速发电机TG等组成。
该系统在电机负载增加时,转速将下降,转速反馈Un减小,而转速的偏差△Un将增大(△Un=Un-Un),同时放大器输出Uc增加,并经移相触发器使整流器输出电压Ud增加,电枢电流Id增加,从而使电动机电磁转矩增加,转速也随之升高,补偿了负载增加造成的转速降。
带转速负反馈的直流调速系统的稳态特性方程为图5 带转速负反馈的有静差直流调速系统的结约)1()1(K C RI K C U K K n e d e n s p +-+*=电动机转速降为)1(K C RI n e d +=∆式中,K=KpKs α/Ce ,Kp 为放大器放大倍数;Ks 为晶闸管整流器放大倍数;Ce 为电动机电动势常数;α为转速反馈系数;R 为电枢回路总电阻。
从稳态特性方程可以看到,如果适当增加放大器放大倍数Kp ,电机的转速降△n 将减小,电动机将有更硬的机械特性,也就是说在负载变化时,电动机的转速变化将减小,电动机有更好的保持速度稳定的性能。
如果放大倍数过大,也可能造成系统运行的不稳定。
转速负反馈有静差调速系统的仿真模型如图6所示。
模型在图2所示的开环调速系统的基础上增加了转速给定un 、转速反馈n-feed 、放大器Gain1和反映放大器输出限幅的饱和特性模块Saturation1,饱和限幅模块的输出是移相触发器的输入uc ,其中转速反馈直接取自电动机的转速输出,没有另加测速发电机,取转速反馈系数α=Un/nN 。
图6 转速负反馈有静差直流调速系统仿真模型【例2】在例1的基础上观察带转速负反馈系统,在不同放大器放大倍数时对转速变化的影响。
在额定转速Un=10时,Kp=5、10、20时的转速响应曲线如图7a所示图7 额定转速时的响应曲线a)不同放大倍数时的响应曲线b)电流响应曲线(图中为kp),随着放大器放大倍数的增加,系统的稳态转速提高,即稳态转速降减小。
图7b所示为Kp=10时的电流响应波形,从波形可以看到由于没有电流的限制措施,在起动过程中电流仍很大可达370A左右。
图8b所示为1/2额定转速Un=5时的转速响应曲线,以Kp=10和200两种情况比较,在Kp=200时,稳态转速降减小但是调节过程中的振荡次数增加,这从相应的移相控制信号变化也可以看到相同的情况(见图8a),由于晶闸管整流器控制的非线性,其输出电压只能在0~Ud范围内变化,尽管放大倍数很高,转速还没有出现严重的不稳定现象。
图8 转速给定Un=5时的波形a)移相控制信号b)转速响应曲线3、转速电流双闭环控制的直流调速系统仿真转速电流双闭环控制的直流调速系统是最典型的直流调速系统,其原理结构如图9所示。
双闭环控制直流调速系统的特点是电动机的转速和电流分别由两个独立的调节器分别控制,且转速调节器的输出就是电流调节器的给定,因此电流环能够随转速的偏差调节电动机电枢的电流。
当转速低于给定转速时,转速调节器的积分作用使输出增加,即电流给定上升,并通过电流环调节使电动机电流增加,从而使电动机获得加速转矩,电动机转速上升。
当实际转速高于给定转速时,转速调节器的输出减小,即电流给定减小,并通过电流环调节使电动机电流下降,电动机将因为电磁转矩减小而减速。
在当转速调节器饱和输出达到限幅值时,电流环即以最大电流限制Idm实现电动机的加速,使电动机的起动时间最短,在可逆调速系统中实现电动机的快速制动。
在不可逆调速系统中,由于晶闸管整流器不能通过反向电流,因此不能产生反向制动转矩而使电动机快速制动。
图9 转速电流双闭环控制的直流调速系统原理图直流双闭环系统的仿真可以依据系统的动态结构图进行,也可以用Power System的模块来组建。
两种仿真不同在于主电路,前者晶闸管和电动机是用传递函数来表示,后者晶闸管和电动机是使用Power System 的模块,而控制部分是相同的。
下面分别对两种方法进行介绍。
3.1按直流双闭环系统动态结构图仿真依据系统的动态结构图的仿真模型如图10所示,仿真模型与系统动态结构图的各个环节基本上是对应的,需要指出的是,双闭环系统的转速和电流两个调节器都是有饱和特性和带输出限幅的PI 调节器,为了充分反映在饱和和限幅非线性影响下调速系统的工作情况,需要构建考虑和和输出限幅的PI 调节器,过程如下: 线性PI 调节器的传递函数为s s K s K K s W P i P PI ττ+=+=11)(式中,Kp 为比例系数;Ki 为积分系数; =KpKi 。
图10 直流双闭环调速系统动态结构图和仿真模型a )结构图b )仿真模型上述PI 调节器的传递函数可以直接调用SIMULINK 中的传递函数或零极点模块。
而考虑饱和和输出限幅的PI 调节器模型如图11a 所示。
模型中比例和积分调节分为两个通道,其中积分调节器integrate 的限幅表示调节器的饱和限幅值,而调节器的输出限幅值由饱和模块Saturation 设定。
当该调节器用作转速调节器ASR 时,在起动中由于开始转速偏差大,调节器输出很快达到输出限幅值,在转速超调后首先积分器退饱和,然后转速调节器输出才从限幅值开始下降。
为了使系统模型更简洁,利用了SIMULINK 的打包功能(Great Subsystem )将调节器模型缩小为一个分支模块,如图11b 所示。
图11 带饱和和输出限幅的PI 调节器及分支模块a )调节器模型b )分支模块【例3】以例1的晶闸管-直流电动机系统为基础,设计一转速电流双闭环控制的调速系统,设计指标为电流超调量σI%≤5%,空载起动到额定转速时的转速超调量σn%≤10%。
过载倍数 =1.5,取电流反馈滤波时间常数 Toi=0.002s ,转速反馈滤波时间常数Ton=0.01s 。
取转速调节器和电流调节器的饱和值为12V ,输出限幅值为10V ,额定转速时转速给定Un=10V 。
仿真观察系统的转速、电流响应和设定参数变化对系统响应的影响。