年产2万t机床床身铸件短流程树脂砂工艺铸造车间设计
机床铸件铸造工艺流程
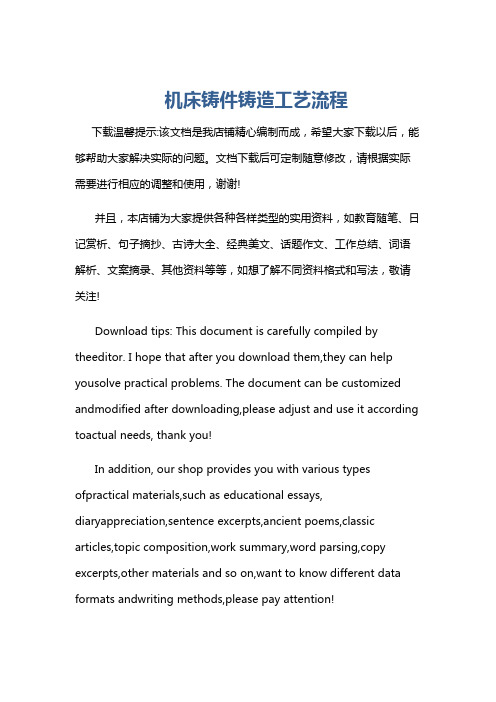
机床铸件铸造工艺流程下载温馨提示:该文档是我店铺精心编制而成,希望大家下载以后,能够帮助大家解决实际的问题。
文档下载后可定制随意修改,请根据实际需要进行相应的调整和使用,谢谢!并且,本店铺为大家提供各种各样类型的实用资料,如教育随笔、日记赏析、句子摘抄、古诗大全、经典美文、话题作文、工作总结、词语解析、文案摘录、其他资料等等,如想了解不同资料格式和写法,敬请关注!Download tips: This document is carefully compiled by theeditor. I hope that after you download them,they can help yousolve practical problems. The document can be customized andmodified after downloading,please adjust and use it according toactual needs, thank you!In addition, our shop provides you with various types ofpractical materials,such as educational essays, diaryappreciation,sentence excerpts,ancient poems,classic articles,topic composition,work summary,word parsing,copy excerpts,other materials and so on,want to know different data formats andwriting methods,please pay attention!机床铸件铸造工艺流程一、设计与准备阶段。
在进行机床铸件铸造之前,首先要进行全面的设计与准备工作。
小型铸造厂树脂砂生产线改造的设计
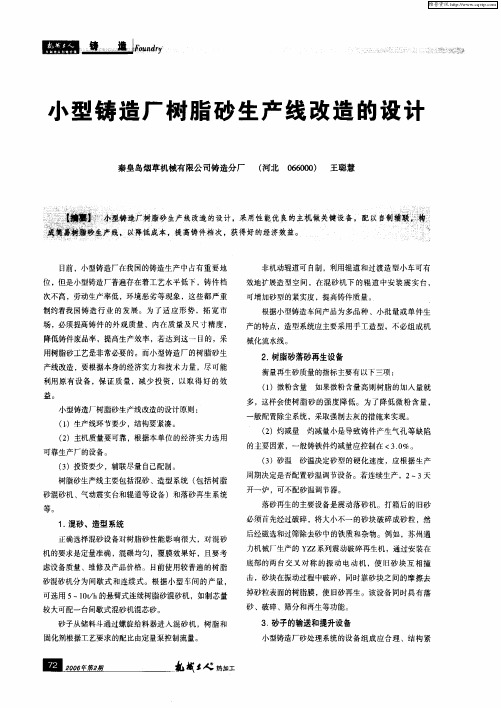
利用原有设备, 保证质量 ,减少投资,以取得好的效
益。
小型铸造厂树脂砂生产线改造的设计原则:
(+ 1 )生产线环节要少 , 结构要 紧凑 。
多,这样会使树脂砂的强度降低。为了降低微粉含量 ,
一
般配置除尘系统 ,采取强制去灰 的措 施来 实现 。
()主机质量要可靠, 2 根据本单位的经济实力选用
机。在输送过程中,要配 置强制去灰 的除尘设备 。砂库
6 设计实例 ( . 见下图)
可旧物利用,若新制可采用圆锥形砂库,其倾角应 > 6。 0,以增加有效容量。
4 除尘与风选设计 .
树脂砂生产中,灰尘来源主要有以下几个方面 : ( )树脂膜烧灼后形成的灰尘。 1 ()涂料烧灼后形成的粉末。 2
可靠生产厂的设备 。 ()投资要少 ,辅联 尽量 自己配制 。 3 树脂砂生产线主要包 括}砂 、造型 系统 ( 昆 包括树 脂
()灼减量 灼减量小是导致铸件产生气孔等缺陷 2
的主要因素,一般铸铁件灼减量应控制在 < .%。 30 ()砂温 砂温决定砂型的硬化速度,应根据生产 3 周期决定是否配置砂温调节设备。若连续生产,2 天 3
囵 2堡盟 垒 筮 鳗
缸槭 l
工
维普资讯
f■— 嘲■ _ —■■■ ■ I | —■●■ ■ —■■一 L 生 ■■ ^ I I
III III III
凑。为降低成本, 尽量利用原砂处理系统改制,水平输 送选用带有磁选的皮带输送机,垂直输送可选斗式提升
目前,小型铸造厂在我国的铸造生产中占有重要地
非机动辊道可 自制 ,利用辊道 和过渡造 型小车可 有 效地扩展造型空 间 ,在混砂 机下 的辊 道 中安装震 实 台 , 可增加砂型的紧实度 ,提高铸 件质 量。
年产20万台发动机气缸体铸件的砂处理工部设计
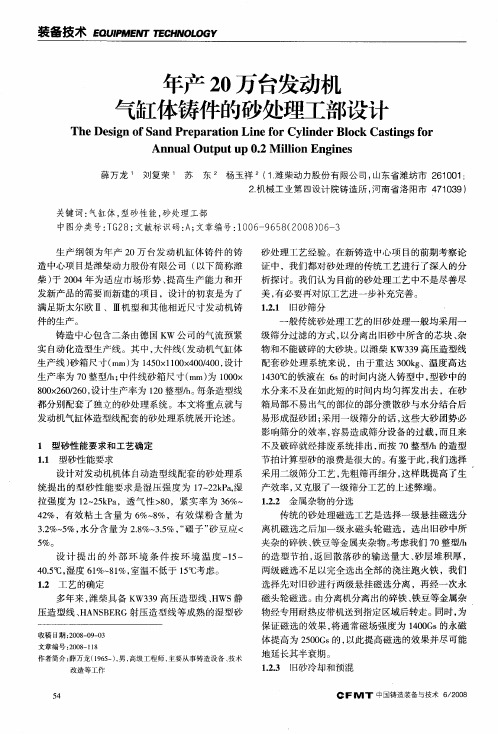
级筛分过滤的方式 , 以分离出旧砂中所含的芯块 、 杂 物 和不能 破碎 的大砂 块 。以潍柴 K 3 W39高压造 型线 配 套砂 处 理 系统 来说 ,由于 重达 30 g 0k 、温 度高 达
3 %~ %, 分 含 量 为 28 35 “ 子 ” 豆应 < . 5 水 2 . %~ .%, 礓 砂
5% 。
设 计 提 出 的 外 部 环 境 条 件 按 环 境 温 度 一5 1~ 4 .℃, 0 5 湿度 6 %一 1 室 温不低 于 1q考 虑 。 1 8 %, 5C 1 工艺 的确定 . 2 多年来 , 柴 具备 K 3 压 造型 线 、 WS静 潍 W39高 H 压造 型线 、 AN B R H S E G射 压造 型 线 等成 熟 的湿 型砂
13%的铁 液在 6 的时 间内浇 人铸 型 中 , 40 s 型砂 中 的 水 分来 不及 在如 此短 的时 间 内均匀 挥发 出去 ,在砂 箱 局部 不易 出气 的部 位 的部分 溃散 砂 与水 分结 合后 易 形成 湿砂 团 ; 用 一级筛 分 的话 , 采 这些 大 砂 团势必 影 响筛 分 的效率 , 易造 成筛 分设 备 的过载 , 且来 容 而 不 及破 碎就 经排 废 系统排 出 , 而按 7 型/ 0整 h的造 型 节 拍计算 型砂 的浪 费是很 大 的。有鉴 于此 , 们选择 我 采 用二 级筛 分工 艺 , 先粗 筛再 细分 , 样 既提高 了生 这 产 效率 , 又克 服 了一 级筛分 工艺 的上 述弊端 。 1 . 金 属 杂物 的分选 .2 2 传 统 的砂处 理磁 选工 艺是 选 择一 级悬 挂磁 选 分
年产2万吨汽车铸造零部件生产线扩建及技术改造产业化升级项目项目可行性报告

一、项目背景和目标随着汽车行业的快速发展,汽车铸造零部件的需求量不断增加。
为满足市场需求,公司计划进行年产2万吨汽车铸造零部件生产线的扩建及技术改造产业化升级项目。
该项目的目标是通过扩建生产线和进行技术改造,提高生产效率和产品质量,满足市场需求,提升公司的竞争力。
二、项目内容和规模1.项目内容扩建年产2万吨的汽车铸造零部件生产线,包括铸造车间、加工车间、整备车间等。
进行技术改造,引进先进的自动化设备和生产工艺,提高生产效率和产品质量。
2.项目规模扩建的生产线年生产能力为2万吨,主要生产汽车铸造零部件。
三、市场分析1.需求分析目前汽车市场持续增长,汽车铸造零部件的需求量不断增加。
而且随着汽车制造技术的提升,对铸造零部件的要求也越来越高。
因此,扩建生产线和进行技术改造是满足市场需求的必然选择。
2.竞争分析目前市场上存在较多的汽车零部件生产厂商,竞争激烈。
但随着技术的进步和产业升级,高品质、高效率的铸造零部件将受到更多市场认可。
四、技术分析1.生产工艺引进先进的自动化铸造设备和工艺,提高生产效率和产品质量。
2.质量控制建立严格的质量控制体系,对生产过程中的每个环节进行管控,确保产品质量。
五、经济效益分析1.投资估算项目总投资估算为XX万元,其中包括设备购置费、修建费、人力资源费等。
2.销售收入预测根据市场需求和公司的营销能力,预计年销售收入为XX万元。
3.经济效益分析通过扩建和技术改造,提高生产效率和产品质量,预计年利润为XX 万元,投资回收期为XX年。
六、社会效益分析1.提供就业机会,促进当地经济发展。
2.引进先进技术,提高本地员工的技术水平和工作经验。
3.改善产品质量,提升消费者的购买满意度。
七、风险分析1.市场竞争风险:市场竞争激烈,公司需要提升产品质量和品牌知名度。
2.技术风险:技术改造可能存在一定的难度和风险,需要严密的技术研发和管理。
3.经济风险:市场环境和经济形势变化可能会影响项目的盈利能力。
年产10000吨铸件PEPSET树脂砂铸造车间的设计
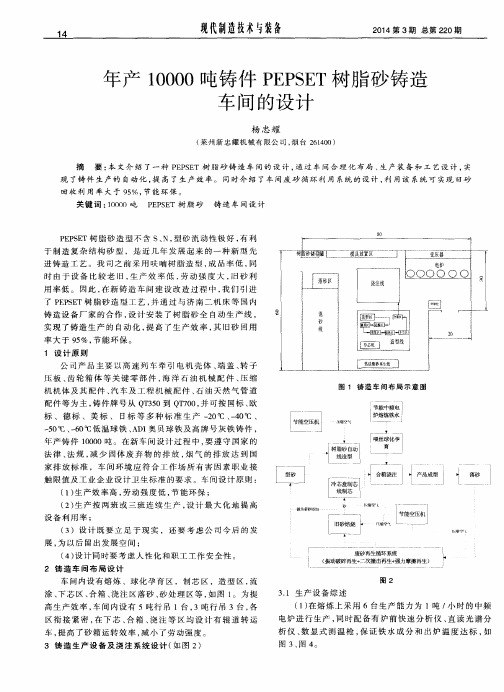
1 6
现 代 制 造技 术 与 装 备
2 0 1 4 第3 期总 第2 2 0 期
车 ,运 回 落 砂 机 ; 大 于 5 m m 的 块 状 物 料 留 在 振 动 破 碎 机
经 风 选 调 温 的 再 生 砂 由发 送 罐 进 人 由焙 烧 炉 的 加 料 口加 入 到焙 烧 炉预 热 室 中 , 由预 热 系统 加 热 , 使 砂 子 温 度
图 2
1 .
车 间 内设 有熔 炼 、球 化 孕 育 区 ,制芯 区 ,造 型 区 , 流
涂、 下芯区 、 合箱 、 浇 注 区落 砂 、 砂处 理 区 等 。 如图 1 。为 提 高 生 产效 率 , 车 间 内设 有 5吨行 吊 1台 , 3吨行 吊 3台 , 各
区 衔接 紧 密 , 在下芯 、 合箱 、 浇 注 等 区均 设 计 有 辊 道 转 运 车, 提 高 了砂 箱 运转 效 率 , 减 小 了劳动 强 度 。
( 2 ) 生 产按 两班 或 三 班 连 续 生 产 , 设 计 最 大 化 地 提 高
做为 新砂漆加
树 脂砂 自动
-
育
线 造 型 『
薹¨
蝴空
一 一
1
l l 珊
一
]
设 备 利用 率 ;
( 3)设 计 既 要 立 足 于 现 实 , 还 要 考 虑 公 司 今 后 的 发
中, 停 机 后 清 出 系统 ; 小于 2 a r m 的砂 粒输 送 到过 渡 斗 中 ,
过 渡 斗 中 的砂 子 经 发 送 罐 送 到再 生 砂 库 中 。直 到 再 生 砂
库 上 料位 满 料 , 再 生 系统 自动 依 次 停机 , 完 成 破碎 撞 击 再
年产2.5万t铸件的砂型铸造车间设计

1 /。 5t h
关键词 : 砂型铸造 ; 铸造车间 ; 车间设计
中 图 分 类 号 :G 8 T 2 文 献标 识 码 : A 文 章 编 号 :0 3 84 (0 2 0 — 0 9 0 1 0 — 3 5 2 1 )3 0 8 — 4
( ) 获 得好 的制 芯 效 果 , 3要 除芯 盒 的合 理 设
计 、 造精 度 和 正 确 的制 芯 工 艺参 数 外 , 必 须 制 还 保 持 芯盒 型腔 表面 的清 洁和排气 通 畅 。 为此 专 门
配置 了干 冰清 洗机 , 期对 芯盒 型 腔表 面的树 脂 定
到制芯生产率 、 砂芯质量和制芯成本 , 中射 口 其 的形状大小 、 数量 、 布置位置 的设计和排气装置 ( 气塞 、 气槽 、 芯杆间隙 ) 排 排 顶 的设 计是 获 得 优
h b c s n swa nrd cd: 1 d cdn rd cin po rm n ein picpe ( s lcig a po r t q ime t a d u a t g sito u e ( ) e iig po u t rga a d d sg r il; 2)ee t p rpi ee up ns n i o n n a
收 稿 日期 :0 1 1— 3 2 1— 10
修 定 日期 :0 2 0 — 3 2 1- 3 2
作者简介 : 王跃( 9 61 一 , 汉族 , 1 7 .0 ) 男, 安徽泗县人 , 毕业 于长安大学材料塑性 成型专业, 从事铸造 工艺和工程设计工作。
年产2万吨铸件树脂砂生产线的设计
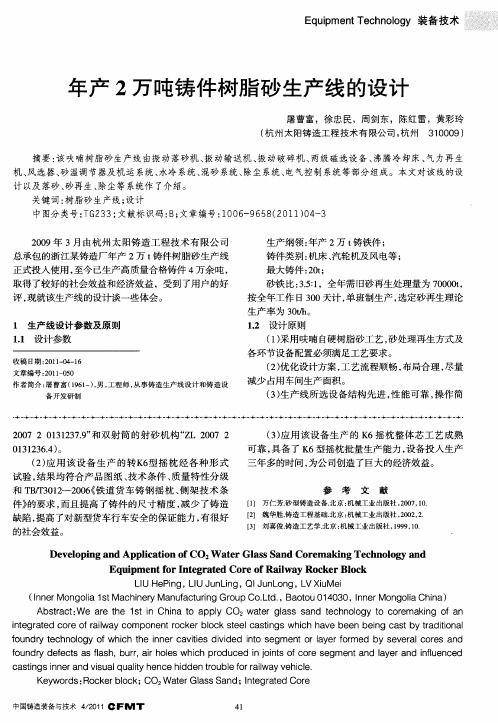
中图分类号: G 3 : T 2 3 文献标识码: ; B 文章编号 :0 6 9 5 ( 0 1 0 - 1 0 — 6 8 2 1 )4 3
20 0 9年 3月 由杭 州 太 阳铸 造 工 程 技 术 有 限公 司
总承包的浙江某铸造厂年产 2 t 万 铸件树脂砂生产线 正式投入使用 , 至今已生产高质量合格铸件 4万余吨 , 取得 了较 好 的社会 效 益和 经济 效 益 ,受到 了用 户 的好 评, 现就该生产线 的设计谈一些体会。
生产 率 为 3t 。 0/ h 12 设 计 原则 .
1 设计参数 . 1
收稿 日期 :0 1 0 — 6 2 1 - 4 1 文章编 号 :0 1 0 0 2 1-5 作 者简介 : 曹富 (9 1 , , 程师 , 事铸造生 产线 设计和铸 造设 屠 16 一)男 工 从 备 开发研 制
( ) 化设 计 方案 , 艺 流程顺 畅 , 局合 理 , 2优 工 布 尽量 减 少 占用 车 间生产 面积 。 ( ) 产线 所 选 设 备 结构 先 进 , 能可 靠 , 作 简 3生 性 操
一 —-
・ -
+ ” ” 4 - 4 ”— . — - . — 4 - - -- - 一 - - + 4
L U He ig,L U J n ig, u L n I Pn I u Ln QI n o g,L u J V XiMe i
(n e n oi 1 t c ieyMa ua t r gGru .t . B oo 1 0 0 In r n oi Chn ) In r Mo g l s hn r n fcui o pCoLd , a tu0 4 3 , n e g l i a Ma n Mo6摇枕整体芯工艺成熟 可靠 , 具备了 K 型摇枕批量生产能力 , 6 设备投入生产
年产2万吨铸件项目可行性研究报告

【项目背景】近年来,我国铸件行业发展迅猛,成为国民经济中不可或缺的一部分。
为了满足国内工业对铸件的需求,促进铸件行业的发展,开展年产2万吨铸件项目的可行性研究是至关重要的。
【市场需求分析】根据工业发展的趋势和需求预测,我国对铸件的需求量将持续增长。
随着制造业的升级和产能的扩大,铸件作为机械零部件的重要组成部分,将会有更广泛的应用。
同时,近年来国家对环保要求的提高,推动了铸件行业的技术升级和设备更新,进一步增加了市场的需求。
【技术可行性分析】年产2万吨铸件项目的实施需要先进的生产工艺和设备。
根据市场需求,我们计划采用最新的模具技术和数字化铸造工艺,提高铸件生产效率和质量。
同时,引进先进的铸造设备和自动化生产线,减少人工操作,提高生产效率和降低生产成本。
【经济可行性分析】基于市场需求和技术可行性,我们进行了项目的经济可行性研究。
根据初步估算,年产2万吨铸件项目的投资规模约为XX万元。
项目预计年销售收入约为XX万元,年净利润约为XX万元。
综合考虑项目的投资收益率、回收期以及财务风险等因素,项目在经济上是可行的。
【社会可行性分析】年产2万吨铸件项目的实施将带动相关产业的发展,促进当地经济增长。
未来,项目将创造大量的就业机会,提高当地群众的收入水平。
同时,项目还将推动铸件行业的技术升级,提高产品质量和可靠性,为国家的工业发展做出贡献。
【环境可行性分析】在项目实施过程中,我们将遵守环保法规,采取先进的环保设施和技术措施,尽量减少对环境的影响。
通过优化生产工艺和资源利用,减少废气、废水和固体废物的排放,保护周围的环境质量。
同时,项目还将推动铸件行业向低能耗、环境友好的方向发展,符合国家的节能减排政策。
【风险分析】项目实施过程中存在一定的风险,如市场竞争风险、原材料价格波动风险和管理风险等。
为降低风险,我们将制定详细的市场营销策略,积极开拓市场份额;建立稳定的供应链和原材料采购渠道,控制成本;加强项目管理,建立健全的财务和风险管理制度,提高项目的透明度和可控性。
- 1、下载文档前请自行甄别文档内容的完整性,平台不提供额外的编辑、内容补充、找答案等附加服务。
- 2、"仅部分预览"的文档,不可在线预览部分如存在完整性等问题,可反馈申请退款(可完整预览的文档不适用该条件!)。
- 3、如文档侵犯您的权益,请联系客服反馈,我们会尽快为您处理(人工客服工作时间:9:00-18:30)。
平 均砂 铁 比 , 3: ; 取 1
.
—
—
铸件 废 品率 , 3 取 %; 废 型率 , 2 取 %;
1 炉体 以熔化功率( 30 w) # 1 5 供电, 1 炉体进入 k 使 #
T AN l X 一 h s e,xUE L u h GA0 i - u, x讥一q i
( n c e gGre atn s ac n v l me tC ne ,ic e gS a x 4 1 0, hn Ya g h n e nC sig Reer ha d De eo p n e trJn h n h n i 8 0 C ia) 0
要: 介绍 了年产 2万 t 机床床 身及相 关配套铸件 的铸造 车间采 用短 流程树脂砂工 艺的 车间设计过程与
思路 。 设计采用高炉与 6t 并联谐振式双供 电中频感应升温、 保温 电炉熔化 , 树脂砂造型制芯和旧砂 再生生产线。 车间厂房结构采用轻钢彩板、 架结构 , 排 厂房 长 1 8m, 6 四连跨 , 中造 型与清理 隔开 , 0 宽 9m 其 有利于车 间改善
(+ % ) 7 5 a 1 5 = 5 7t , 0 /
艺温度后 ,将功率降至保温功率并进入保温状态 ,
如 此 两 炉交 替 生 产 。若 在 熔 化 中一个 炉体 出现 故 障, 可断 开两 台 电源 , 其 中一 台开动 。两 台电源总 将 功率 在变 压器 额定 容量 240k A不超 载 的情 况下 0 V
1 生产 纲 领
211 熔化 工部 ..
设 计 根据 建设 方 拥有 高 炉 的有 利条 件 , 用 高 采 炉铁水 轨 道 电平 车运 输 , 热装 直 接人 中频感 应 电炉 加 热 。 炉 出铁制 度为 8t , 高 2h 铁水 出炉 温度 一般 为 /
铸 造 车 间 以生产 机 床大 中型铸 铁件 为 主 , 年产
各类冲床床身及相关零部件 2万 t ,单重最小件几
收稿 日期 :0 2 0 一 8 2 1— 1 l 作者简 介 : 田新社( 9 9 ) 山西省 阳城县人 , 15 一 , 工程师 , 主要从事铸 造工艺方面的技术工作 。
1 5 左右 , 0o 3 C 通过 中频 感应 电炉使 铁水过 热 至 15 0℃进行 铁水 调质 处理 , 5 然后 出炉浇注 。工艺衔 接 要求 为 : 中频感 应 电炉 2h之 内必须 完 成 8 铁水 t 从人炉到出炉的全部熔化过程 。 高炉将定期放铁水
2 工 艺设 计与设 备选 型
21 工 艺 设 计 .
照省经信委的要求 , 作为铸造高炉保留必须延伸产 业链配套短流程铸造 ,该公司 2 1 年在省发改委 0 1 立项 , 拟建 设 5万 t 流程铸 造项 目, 中一期 工程 短 其 为建设 年 产 2万 t 机床 床身 铸件 项 目。项 目规 划 占 地 1 0 总建筑面积 6 5 I 其中铸造车间 0 0m, 0 8T , 2 1 建筑 面积 604i 。在 厂 区现有 高炉 周 围予 留场地 1 n 建设 。
・
7 ・
A r02 №2 D. 1 2
铸 造 设 备 与 工 艺
2 1 年第 2 02 期
进人下一个循环 , 铸造车间接纳铁水最大设计能力 为 8t 因设 备 故 障 不 能按 时接 纳 铁 水 时 , 炉 2h, / 高
铁 水 流入 铸铁 机 浇注 商 品 面包 铁外 销 ,将 空过 2 h 接 下 一次 铁水 。 中频 电炉选 用两 台 6t 体 ,配 置 炉 特 点为 双 电源与 双炉体 +功率 分配器 方式 ,即 1台
每 天造型制 芯 时问 :0 ~ 2 , 1 . 1 1 取 0h h h 设备 年时基 数 :
( + %)6 8 a 1 5 = 61 8 /, t
度后 , l #电源功率降至保温功率 , l 炉进入保温 使 # 状态 。同时 2 #电源将功率从 7 0 W 升至 1 5 k , 5k 0W 3
对2 #炉供 电 , 其 进入熔 化状 态 。 #炉铁 水达 到工 使 2
Q= 26 0×3×( + %) 1 2 )× 22 8 1 3 ×( + %
p ae, a l t f me- e t sr cu eI h s 1 8 m l t ln , 9 m d h, u o n ci g c mp n e . e mo li g w r s o d ce n n r b n tu t r . a 0 p a o g 6 wit f r c n e t o a i s t n o n h T udn ok h p a la ig n w r s o s s p r t d i a o f i r vn h n i n n ft e wok h pT e d sg mp a ie n io me tl p o e t n, r o k h p i e aa e ,n f v r o mp o i g t e e vr me t o h r s o . h e i n e h sz s e v r n n a r tc i f e o o i c nr l s f , e l e e g a i g me s r s tr t e o l t n o h o k h p,h e t r n w s o ma . h et r e o o c o to , ae h at n r y s v n a u e . e h c mp ei f t e w r s o t e t s u a n r 1 e b t c n mi , h, Af o T e e v r n na r tc in e e g a i g a d s ca e e t w r e u r d n i me tlp oe t ,n r s vn o il n f s e e r q i . o o y n b i e Ke wo d : h r p c s ,e i a d p o e s f u d y w r s o y r s s o r e s r s s n r c s ,o n r o k h p t o n
某公 司现 有 38m 及 19 m 高 炉 各 一 座 , 1 3 7 3 按
十千克 , 大件单 重 8t其 中大部 分 为灰 铸铁 件 , 最 , 少 部 分 为球铁 件 和合金铸 铁 件 。典 型铸件 ( 冲床 床身 ) 主要 尺寸 为 35i×25 ×1 , 重 8t28 i× .n .i .i 单 n 0n .n ; 1 l . m, . n×0 单重 5 ;.m×1 ×0 , 8 9 t 0 2 .I .I 单重 3. 5 n 8 n t
环境。设计中注重环保、 消防、 安全 、 卫生、 节能各项措施 。车间建成后试运行正常 , 取得 了良好 的经济、 环保 、 节
能、 会综合效益。 社
关键词: 短流程 ; 树脂砂工艺; 铸造车间 中图分类号 :G 8 T 2 文献标识码 : A 文章编号 :64 6 9 (0 2 0 — 0 7 0 17 — 6 4 2 1 )2 0 0 — 5
干炉 。
1混砂机 能力 计算 : )
全 年型砂 混砂 量 Q C (+ ( ) 1y) = S 1 ) 1 (+
的炉 体 , 台炉 体 通过 功 率 分 配 器 同时 工 作 , 两 总功 率 4210k 0 W.工作 时 可实 现一 个 炉体 升温 熔 化铁 水, 一个 炉体 保温 铁水 。两 个炉 体 同时 出铁 为 1 , 2t 满 足最 大单重 8 铸件生 产 。工作 方式 :#电源对应 t l
i e m e a e fe u nc u a ntr dit q e y f r ce,e i s n c rn n od s n e e r to o d t n lneTh r h p s h oorlg t se l r n r sn a d oi g a d l a d r g nea in pr uci i . e wo ks o u est e c l ih te o
任 意分配 之 。 中频 电炉冷 料 ( 钢 、 材 ) 炉选用 5 起 重机 废 返 人 t 配 N 5 1 0 一 电磁吸盘 ( t, K — 1L 1 1 )铁水入 炉选用 1 t 6 冶
全年 生产 日 = 0 . 30d
每 天型芯砂 量 为 :
6 8 /0 — 5 5 /0 = 2 0 2 0 t , 6183 0 7 73 0 ( 2 ~ 5 )d 0 /
The De i n fRe i S n Ca tng W o k h p 、 h 2 0 sg o sn a d s i r s o t 0 0 0 t Ann lPr d to fM a h ne To lBe Ca tng ua o uc i n o c i o d si
2 0 V 0 A变压器 + 4 k 2台 1 5 W 中频 电源 + 0k 3 2台 6 t
高 了生 产效 率 。 砂 芯 涂 料 采 用 醇 基 涂 料 , 工 喷涂 , 备 柱 式 手 配 悬 臂 吊以方便 砂 芯 的起 吊 、 翻转 。为保 证 砂 芯涂料 的干燥 , 特别 在 制芯 工 部配 备 了 1台贯 通 式煤 气 烘