《材料成型基本原理》刘全坤版塑性部分课后答案
材料成形基本原理课后习题答案

第一章习题1 . 液体与固体及气体比较各有哪些异同点?哪些现象说明金属的熔化并不是原子间结合力的全部破坏?(2)金属的熔化不是并不是原子间结合力的全部破坏可从以下二个方面说明:①物质熔化时体积变化、熵变及焓变一般都不大。
金属熔化时典型的体积变化∆V m/V为3%~5%左右,表明液体的原子间距接近于固体,在熔点附近其系统混乱度只是稍大于固体而远小于气体的混乱度。
②金属熔化潜热∆H m约为气化潜热∆H b的1/15~1/30,表明熔化时其内部原子结合键只有部分被破坏。
由此可见,金属的熔化并不是原子间结合键的全部破坏,液体金属内原子的局域分布仍具有一定的规律性。
2 . 如何理解偶分布函数g(r) 的物理意义?液体的配位数N1、平均原子间距r1各表示什么?答:分布函数g(r) 的物理意义:距某一参考粒子r处找到另一个粒子的几率,换言之,表示离开参考原子(处于坐标原子r=0)距离为r的位置的数密度ρ(r)对于平均数密度ρo(=N/V)的相对偏差。
N1 表示参考原子周围最近邻(即第一壳层)原子数。
r1 表示参考原子与其周围第一配位层各原子的平均原子间距,也表示某液体的平均原子间距。
3.如何认识液态金属结构的“长程无序”和“近程有序”?试举几个实验例证说明液态金属或合金结构的近程有序(包括拓扑短程序和化学短程序)。
答:(1)长程无序是指液体的原子分布相对于周期有序的晶态固体是不规则的,液体结构宏观上不具备平移、对称性。
近程有序是指相对于完全无序的气体,液体中存在着许多不停“游荡”着的局域有序的原子集团(2)说明液态金属或合金结构的近程有序的实验例证①偶分布函数的特征对于气体,由于其粒子(分子或原子)的统计分布的均匀性,其偶分布函数g(r)在任何位置均相等,呈一条直线g(r)=1。
晶态固体因原子以特定方式周期排列,其g(r)以相应的规律呈分立的若干尖锐峰。
而液体的g(r)出现若干渐衰的钝化峰直至几个原子间距后趋于直线g(r)=1,表明液体存在短程有序的局域范围,其半径只有几个原子间距大小。
《材料成型基本原理》刘全坤版 第九章 答案

第九章液态金属的净化与精炼1、何谓沉淀脱氧?试述生产中常用的几种沉淀脱氧反应。
答:(1)沉淀脱氧是指溶解于液态金属中的脱氧剂直接和熔池中的[FeO]起作用,使其转化为不溶于液态金属的氧化物,并析出转入熔渣的一种脱氧方式。
(2)生产中几种常用的沉淀脱氧反应:a 锰的脱氧反应,[Mn]+[FeO]=[Fe]+(MnO)b 硅的脱氧反应,[Si]+2[FeO]=2[Fe]+(SiO2)c 硅锰联合脱氧反应。
2、试述铸造与焊接冶金工艺中常用的脱氧方式及特点。
答:(1)先期脱氧熔焊过程中先期脱氧的特点是脱氧过程和脱氧产物与高温的液态金属不发生直接关系,脱氧产物直接参与造渣。
而在一般的熔炼钢铁炉中,也存在硅和锰等元素与炉气中的氧化性气体发生反应,生成的氧化物进入熔渣,但此时并不是有目的地为了脱氧。
(2)沉淀脱氧这种方法的优点是脱氧速度快,脱氧彻底。
但脱氧产物不能清除时将增加金属液中杂质的含量。
(3)扩散脱氧这种方法的优点是脱氧产物留在熔渣中,液态金属不会因脱氧而造成夹杂。
缺点是扩散过程进行的缓慢,脱氧时间长。
(4)真空脱氧在一般真空处理条件下,碳只能起到部分脱氧的作用,尽管如此,用碳脱氧,脱氧产物不留在钢液中,所以对提高钢液质量有明显的效用。
3、从冶金反应动力学角度分析熔渣粘度过大或过小所带来的问题。
答:(1)扩散脱氧是在熔渣中加入脱氧剂,使脱氧元素与熔渣中的氧化亚铁起作用而达到间接脱去钢液中氧化亚铁的目的。
如果熔渣粘度过大,不利于钢液中氧化亚铁向熔渣中扩散,从而影响脱氧效果。
(2)熔渣脱硫的原理与扩散脱氧相似,其反应也包括有扩散过程。
如果熔渣粘度过大,不容易传输,不利于脱硫反应进行。
(3)脱磷反应是在熔渣与钢液界面上进行的。
随着反应的进行,界面处的CaO和FeO 因反应而消耗,浓度减低,必然会引起渣层上方的CaO和FeO向界面传输。
与此同时,反应生成的磷酸钙在界面处浓度增高,必然会向渣层上方传输。
熔渣粘度过大,不利于这些传输过程的进行,因而脱磷效果降低。
塑性成形原理课后习题答案
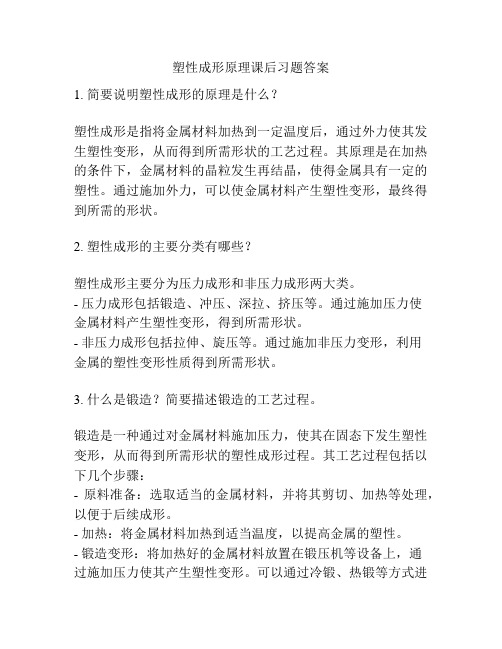
塑性成形原理课后习题答案1. 简要说明塑性成形的原理是什么?塑性成形是指将金属材料加热到一定温度后,通过外力使其发生塑性变形,从而得到所需形状的工艺过程。
其原理是在加热的条件下,金属材料的晶粒发生再结晶,使得金属具有一定的塑性。
通过施加外力,可以使金属材料产生塑性变形,最终得到所需的形状。
2. 塑性成形的主要分类有哪些?塑性成形主要分为压力成形和非压力成形两大类。
- 压力成形包括锻造、冲压、深拉、挤压等。
通过施加压力使金属材料产生塑性变形,得到所需形状。
- 非压力成形包括拉伸、旋压等。
通过施加非压力变形,利用金属的塑性变形性质得到所需形状。
3. 什么是锻造?简要描述锻造的工艺过程。
锻造是一种通过对金属材料施加压力,使其在固态下发生塑性变形,从而得到所需形状的塑性成形过程。
其工艺过程包括以下几个步骤:- 原料准备:选取适当的金属材料,并将其剪切、加热等处理,以便于后续成形。
- 加热:将金属材料加热到适当温度,以提高金属的塑性。
- 锻造变形:将加热好的金属材料放置在锻压机等设备上,通过施加压力使其产生塑性变形。
可以通过冷锻、热锻等方式进行。
- 后处理:对锻造好的金属材料进行去毛刺、修整、热处理等后续工序,以得到最终所需形状的产品。
4. 什么是冲压?简要描述冲压的工艺过程。
冲压是一种利用模具在冲床上对金属材料进行形状变化的塑性成形方法。
其工艺过程包括以下几个步骤:- 材料准备:选取适当的金属材料,并将其剪切成符合模具尺寸的工件。
- 模具装配:将冲床上的模具装配好,包括上模、下模、导向装置等。
- 冲压过程:将金属工件放置在上模上,通过冲床上的推力,使上模下压,使金属材料产生塑性变形,根据模具的设计形成所需形状。
- 后处理:对冲压好的金属材料进行去毛刺、抛光等后续处理,以得到最终所需形状的产品。
5. 什么是挤压?简要描述挤压的工艺过程。
挤压是利用挤压机将金属材料推进模具中进行变形的一种塑性成形方法。
其工艺过程包括以下几个步骤:- 材料准备:选取适当的金属材料,并将其按照挤压所需的截面形状加工成柱状工件,称为坯料。
材料成形基本原理(刘全坤)课后答案
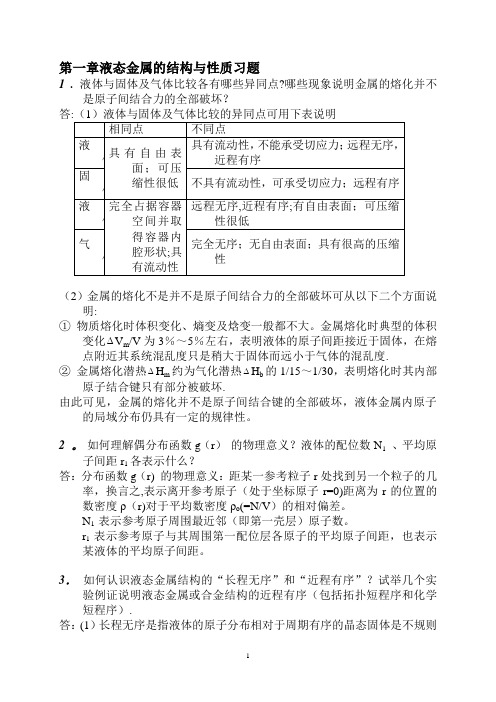
第一章液态金属的结构与性质习题1 .液体与固体及气体比较各有哪些异同点?哪些现象说明金属的熔化并不是原子间结合力的全部破坏?答(2)金属的熔化不是并不是原子间结合力的全部破坏可从以下二个方面说明:①物质熔化时体积变化、熵变及焓变一般都不大。
金属熔化时典型的体积变化∆V m/V为3%~5%左右,表明液体的原子间距接近于固体,在熔点附近其系统混乱度只是稍大于固体而远小于气体的混乱度.②金属熔化潜热∆H m约为气化潜热∆H b的1/15~1/30,表明熔化时其内部原子结合键只有部分被破坏.由此可见,金属的熔化并不是原子间结合键的全部破坏,液体金属内原子的局域分布仍具有一定的规律性。
2 。
如何理解偶分布函数g(r)的物理意义?液体的配位数N1、平均原子间距r1各表示什么?答:分布函数g(r) 的物理意义:距某一参考粒子r处找到另一个粒子的几率,换言之,表示离开参考原子(处于坐标原子r=0)距离为r的位置的数密度ρ(r)对于平均数密度ρo(=N/V)的相对偏差。
N1 表示参考原子周围最近邻(即第一壳层)原子数。
r1 表示参考原子与其周围第一配位层各原子的平均原子间距,也表示某液体的平均原子间距。
3.如何认识液态金属结构的“长程无序”和“近程有序”?试举几个实验例证说明液态金属或合金结构的近程有序(包括拓扑短程序和化学短程序).答:(1)长程无序是指液体的原子分布相对于周期有序的晶态固体是不规则的,液体结构宏观上不具备平移、对称性。
近程有序是指相对于完全无序的气体,液体中存在着许多不停“游荡”着的局域有序的原子集团(2)说明液态金属或合金结构的近程有序的实验例证①偶分布函数的特征对于气体,由于其粒子(分子或原子)的统计分布的均匀性,其偶分布函数g(r)在任何位置均相等,呈一条直线g(r)=1。
晶态固体因原子以特定方式周期排列,其g(r)以相应的规律呈分立的若干尖锐峰。
而液体的g(r)出现若干渐衰的钝化峰直至几个原子间距后趋于直线g(r)=1,表明液体存在短程有序的局域范围,其半径只有几个原子间距大小。
《材料成型基本原理》刘全坤版 第七章答案

1.焊接和铸造过程中的气体来源于何处?它们是如何产生的?答:焊接区内的气体:焊条药皮、焊剂、焊芯的造气剂,高价氧化物及有机物的分解气体,母材坡口的油污、油漆、铁锈、水分,空气中的气体、水分,保护气体及其杂质气体铸造过程中的气体:熔炼过程,气体主要来自各种炉料、炉气、炉衬、工具、熔剂及周围气氛中的水分、氮、氧、氢、CO2、CO、SO2和有机物燃烧产生的碳氢化合物等。
来自铸型中的气体主要是型砂中的水分。
浇注过程,浇包未烘干,铸型浇注系统设计不当,铸型透气性差,浇注速度控制不当,型腔内的气体不能及时排除等,都会使气体进入液态金属。
2. 气体是如何溶解到金属中的?电弧焊条件下,氮和氢的溶解过程一样吗?答:气体溶解到金属中分四个阶段:(1)气体分子向金属-气体界面上运动;(2)气体被金属表面吸附;(3)气体分子在金属表面上分解为原子;(4)原子穿过金属表面层向金属内部扩散。
电弧焊条件下,氮和氢的溶解过程不一样,氢在高温时分解度较大,电弧温度下可完全分解为原子氢,其溶解过程为分解 — 吸附 — 溶入。
在电弧气氛中,氮以分子形式存在,其溶解过程为吸附 — 分解 — 溶入。
3.哪些因素影响气体在金属中的溶解度,其影响因素如何?答:气体在金属中的溶解度与压力,温度,合金成分等因素有关:(1)当温度一定时,双原子的溶解度与其分压的平方根成正比(2)当压力一定时,溶解度与温度的关系决定于溶解反应类型,气体溶解过程为吸热反应时,△H为正值,溶解度随温度的升高而增加;金属吸收气体为放热反应时,△H为负值,溶解度随温度的上升而降低。
(3)合金成分对溶解度的影响:液态金属中加入能提高气体含量的合金元素,可提高气体的溶解度;若加入的合金元素能与气体形成稳定的化合物(即氮、氢、氧化合物),则可降低气体的溶解度。
此外,合金元素还能改变金属表面膜的性质及金属蒸气压,从而影响气体的溶解度。
(4)电流极性的影响:直流正接时,熔滴处于阴极,阳离子将向熔滴表面运动,由于熔滴温度高,比表面积大,故熔滴中将溶解大量的氢或氮;直流反接时,阳离子仍向阴极运动,但此时阴极已是温度较低的溶池,故氢或氮的溶解量要少。
材料成型基本原理课后答案解析

第一章习题1 . 液体与固体及气体比较各有哪些异同点?哪些现象说明金属的熔化并不是原子间结合力的全部破坏?答:(1)液体与固体及气体比较的异同点可用下表说明相同点不同点液体具有自由表面;可压缩性很低具有流动性,不能承受切应力;远程无序,近程有序固体不具有流动性,可承受切应力;远程有序液体完全占据容器空间并取得容器内腔形状;具有流动性远程无序,近程有序;有自由表面;可压缩性很低气体完全无序;无自由表面;具有很高的压缩性(2)金属的熔化不是并不是原子间结合力的全部破坏可从以下二个方面说明:①物质熔化时体积变化、熵变及焓变一般都不大。
金属熔化时典型的体积变化∆V m/V为3%~5%左右,表明液体的原子间距接近于固体,在熔点附近其系统混乱度只是稍大于固体而远小于气体的混乱度。
②金属熔化潜热∆H m约为气化潜热∆H b的1/15~1/30,表明熔化时其内部原子结合键只有部分被破坏。
由此可见,金属的熔化并不是原子间结合键的全部破坏,液体金属内原子的局域分布仍具有一定的规律性。
2 . 如何理解偶分布函数g(r) 的物理意义?液体的配位数N1、平均原子间距r1各表示什么?答:分布函数g(r) 的物理意义:距某一参考粒子r处找到另一个粒子的几率,换言之,表示离开参考原子(处于坐标原子r=0)距离为r的位置的数密度ρ(r)对于平均数密度ρo(=N/V)的相对偏差。
N1 表示参考原子周围最近邻(即第一壳层)原子数。
r1 表示参考原子与其周围第一配位层各原子的平均原子间距,也表示某液体的平均原子间距。
3.如何认识液态金属结构的“长程无序”和“近程有序”?试举几个实验例证说明液态金属或合金结构的近程有序(包括拓扑短程序和化学短程序)。
答:(1)长程无序是指液体的原子分布相对于周期有序的晶态固体是不规则的,液体结构宏观上不具备平移、对称性。
近程有序是指相对于完全无序的气体,液体中存在着许多不停“游荡”着的局域有序的原子集团(2)说明液态金属或合金结构的近程有序的实验例证①偶分布函数的特征对于气体,由于其粒子(分子或原子)的统计分布的均匀性,其偶分布函数g(r)在任何位置均相等,呈一条直线g(r)=1。
《材料成形理论基础Ⅰ》课后题答案
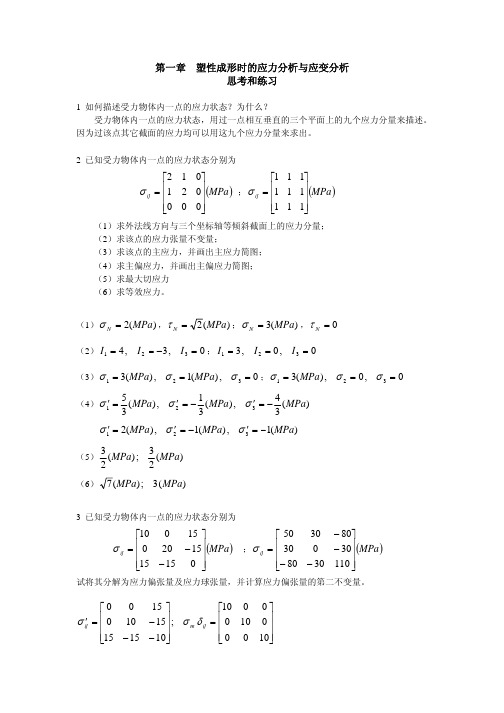
确定,则转角ϕ 也就被确定了,已知某一条滑移线上一点的平均应力σ m ,则沿该条滑移线
上任意一点的平均应力均可求出。由于两族滑移线是相互正交的,因此,整个塑性区内各点 的平均应力均可以求出,确定出整个塑性区内各点的应力状态。
8 滑移线场有哪些典型的应力边界条件?
自由表面、无摩擦的接触表面、摩擦切应力达到最大值 k 的接触表面、当 0 < τ f < k 时
⎢⎣0 0 0⎥⎦
⎢⎣1 1 1⎥⎦
(1)求外法线方向与三个坐标轴等倾斜截面上的应力分量; (2)求该点的应力张量不变量; (3)求该点的主应力,并画出主应力简图; (4)求主偏应力,并画出主偏应力简图; (5)求最大切应力 (6)求等效应力。
(1)σ N = 2(MPa) ,τ N = 2(MPa) ;σ N = 3(MPa) ,τ N = 0
0
20
− 15⎥⎥(MPa )
;σ ij
=
⎢ ⎢
30
0 − 30⎥⎥(MPa)
⎢⎣15 −15 0 ⎥⎦
⎢⎣− 80 − 30 110 ⎥⎦
试将其分解为应力偏张量及应力球张量,并计算应力偏张量的第二不变量。
⎡ 0 0 15 ⎤
⎡10 0 0 ⎤
σ i′j
=
⎢ ⎢
0
10
−15⎥⎥ ;
σ m δ ij
《材料成型基本原理》刘全坤版塑性部分课后答案

字号:[ 放大、标准]塑性成形:是利用金属的塑性,在外力作用下使金属发生塑性变形,从而获得所需形状和性能的工件的一种加工方法,因此又称为塑性加工或压力加工。
塑性:是指金属材料在外力作用下发生变形而不破坏其完整性的能力。
与其他加工方法相比,金属塑性成形有如下优点:(1)生产效率高,适用于大批量生产(2)改善了金属的组织和结构(3)材料利用率高(4)尺寸精度高根据加工时金属受力和变形特点的不同,塑性成形可分为体积成形和板料成形两大类。
前者的典型加工方法有锻造、轧制、挤压和拉拔等;后者则有冲裁、弯曲、拉延和成型等。
虽然塑性成形方法多种多样,且具有各自的个性特点,但他们都涉及一些共同性的问题,主要有:(1)塑性变形的物理本质和机理;(2)塑性变形过程中金属的塑性行为、抗力行为和组织性能的变化规律;(3)变形体内部的应力、应变分布和质点流动规律;(4)所需变形力和变形功的合理评估等。
研究和掌握这些共性问题,对于保证塑性加工的顺利进行和推动工艺的进步均具有重要的理论指导意义,本章将环绕这些方面作简要介绍,以为读者学习各种塑性成形技术奠定理论基础。
三、塑性变形成形理论的发展概况塑性成形力学,是塑性理论(或塑性力学)的发展和应用中逐渐形成的:1864年法国工程师H.Tresca首次提出最大切应力屈服准则1925年德国卡尔曼用初等应力法建立了轧制时的应力分布规律;萨克斯和齐别尔提出了切块法即主应力法;再后来,滑移线法、上限法、有限元法等相继得到发展。
四、本课程的任务目的:科学系统地阐明金属塑性成形的基础和规律,为合理制订塑性成形工艺奠定理论基础。
任务:1)掌握塑性成形时的金属学基础,以便使工件在成形时获得最佳的塑性状态,最高的变形效率和优质的性能; 2)掌握应力、应变、应力应变关系和屈服准则等塑性理论基础知识,以便对变形过程进行应力应变分析,并寻找塑性变形物体的应力应变分布规律;3)掌握塑性成形时的金属流动规律和变形特点,分析影响金属塑性流动的各种因素,以合理地确定坯料尺寸和成形工序,使工件顺利成形;4)掌握塑性成形力学问题的各种解法及其在具体工艺中的应用,以便确定变形体中的应力应变分布规律和所需的变形力和功,为选择成形设备和设计模具提供依据。
- 1、下载文档前请自行甄别文档内容的完整性,平台不提供额外的编辑、内容补充、找答案等附加服务。
- 2、"仅部分预览"的文档,不可在线预览部分如存在完整性等问题,可反馈申请退款(可完整预览的文档不适用该条件!)。
- 3、如文档侵犯您的权益,请联系客服反馈,我们会尽快为您处理(人工客服工作时间:9:00-18:30)。
字号:[ 放大、标准]塑性成形:是利用金属的塑性,在外力作用下使金属发生塑性变形,从而获得所需形状和性能的工件的一种加工方法,因此又称为塑性加工或压力加工。
塑性:是指金属材料在外力作用下发生变形而不破坏其完整性的能力。
与其他加工方法相比,金属塑性成形有如下优点:(1)生产效率高,适用于大批量生产(2)改善了金属的组织和结构(3)材料利用率高(4)尺寸精度高根据加工时金属受力和变形特点的不同,塑性成形可分为体积成形和板料成形两大类。
前者的典型加工方法有锻造、轧制、挤压和拉拔等;后者则有冲裁、弯曲、拉延和成型等。
虽然塑性成形方法多种多样,且具有各自的个性特点,但他们都涉及一些共同性的问题,主要有:(1)塑性变形的物理本质和机理;(2)塑性变形过程中金属的塑性行为、抗力行为和组织性能的变化规律;(3)变形体内部的应力、应变分布和质点流动规律;(4)所需变形力和变形功的合理评估等。
研究和掌握这些共性问题,对于保证塑性加工的顺利进行和推动工艺的进步均具有重要的理论指导意义,本章将环绕这些方面作简要介绍,以为读者学习各种塑性成形技术奠定理论基础。
三、塑性变形成形理论的发展概况塑性成形力学,是塑性理论(或塑性力学)的发展和应用中逐渐形成的:1864年法国工程师H.Tresca首次提出最大切应力屈服准则1925年德国卡尔曼用初等应力法建立了轧制时的应力分布规律;萨克斯和齐别尔提出了切块法即主应力法;再后来,滑移线法、上限法、有限元法等相继得到发展。
四、本课程的任务目的:科学系统地阐明金属塑性成形的基础和规律,为合理制订塑性成形工艺奠定理论基础。
任务:1)掌握塑性成形时的金属学基础,以便使工件在成形时获得最佳的塑性状态,最高的变形效率和优质的性能; 2)掌握应力、应变、应力应变关系和屈服准则等塑性理论基础知识,以便对变形过程进行应力应变分析,并寻找塑性变形物体的应力应变分布规律;3)掌握塑性成形时的金属流动规律和变形特点,分析影响金属塑性流动的各种因素,以合理地确定坯料尺寸和成形工序,使工件顺利成形;4)掌握塑性成形力学问题的各种解法及其在具体工艺中的应用,以便确定变形体中的应力应变分布规律和所需的变形力和功,为选择成形设备和设计模具提供依据。
字号:[ 放大、标准]塑性理论:研究金属在塑性状态的力学行为称为塑性理论或塑性力学,是连续介质力学的一个分支。
塑性理论假设:(1)变形体是连续的;(2)变形体是均质和各向同性的;(3)在变形的任一瞬间,力的作用是平衡的;(4)在一般情况下,忽略体积力的影响;在塑性理论中,分析问题的方法:·静力学:根据静力学平衡条件导出应力分量之间的关系式——平衡微分方程·几何学:根据变形体的连续性和均匀性,导出应变与位移分量之间的关系式——几何方程。
·物理学:根据实验与假设导出应变与应力分量之间的关系式——物理方程或本构方程。
·此外,建立变形体在塑性状态下应力分量与材料性能之间的关系——屈服准则或塑性条件。
角标符号:成组的符号和数组可以用一个带下角标的符号表示,这种符号叫角标符号。
如可用xi即(x1,x2,x3)表示一点的坐标;如应力分量δxx,δxy,δxz,可简记为δij(i,j=x,y,z)等。
一般地,如果一个坐标系有m个角标,每个角标取n个值,则该角标符号代表着nm▲★个元素,例如δij(i,j=x,y,z)(m=2,n=3)就包含有9个元素。
导数记号:导数记为f 'j,表示f(xi)对xj的导数,逗号后边的下标表示对相应坐标的求导克氏符号:δij称为克罗内克(Kronecker)符号,δij定义为求和约定:在一项中,没有重复出现的角标叫自由标,表示该项的个数。
在一项中,同一角标出现二次,则对该角标自1到n的所有元素求和,这种角标在求和之后不再出现,称之为哑标,这一运算称之为求和约定。
张量:由若干个当坐标系改变时满足转换关系的分量组成的集合,称为张量,需要用空间坐标系中的三个矢量,即9个分量才能完整地表示。
它的重要特征是在不同的坐标系中分量之间可以用一定的线性关系来换算。
描述张量分量的个数用阶表示。
在三维空间中,其张量分量的个数为3n ,如应力、应变是二阶张量,有32 =9个分量。
不同坐标系中的应力分量之间的转换关系其中,lki,llj为新坐标系的坐标轴关于原坐标系的方向余弦。
表示点应力状态的九个应力分量构成二阶张量,称为应力张量。
1、张量不变量:二阶张量存在三个独立的不变量。
2、张量可以叠加和分解:几个同阶张量各对应的分量之和或差定义为另一个同阶张量。
3、张量可分为对称张量、非对称张量、反对称张量任意非对称张量可以分解为一个对称张量和一个反对称张量。
4、二阶对称张量存在三个主轴和三个主值以主轴为坐标轴,两个下角标不同的分量均为零,只留下两个下角标相同的三个分量,叫作主值。
字号:[ 放大、标准]小变形:物体在外力作用下产生变形,与本身几何尺寸相比是非常小的量(0.001~0.01),这种变形称作小变形。
在小变形分析中,变形量的二次微量可以忽略。
塑性加工中产生的塑性变形是大变形,分析大变形需要采用增量理论和有限变形,但小变形分析比较简单直观,而且大变形分析可以直接借用小变形分析的结果,因此本章只讨论小变形分析。
一、位移变形体内质点变形前与变形后的直线距离称为位移,位移是矢量。
在坐标系中,一点的位移矢量在三个坐标轴上的投影称为该点的位移分量,用u、v、w表示,或用角标符号ui表示,如图15-1b所示。
根据连续性假设,位移是坐标的连续函数,而且一般都有一阶偏导数,即物体中某点产生了位移,还不表明物体产生了变形,只有质点间产生相对位移,才会引起物体变形。
例如,与相邻质点(x+dx, y+dy, z+dz)在变形中产生位移矢量,即,和相比,产生了位移增量,或与之间相对位置变化量。
如果,两质点间没有相对位移,没有产生变形,仅仅产生了刚体移动二、应变1、线应变质点间产生的相对位移图15-2a中设单元体平面PABC 仅仅在xy 坐标平面内发生了很小的拉变形,则:对于平行于坐标轴的线元分别有:2、切应变设:该单元体在xy平面内发生了角度的变化(切变形),图15-2b,线元PC和PA所夹的直角缩小了,相当于C点在垂直于PC方向偏移了,表明变形后两棱边PC和PA的夹角减小了,称为工程切应变。
图15-2b所示的可以看成是由线元PA和PC同时向内偏移相同的角度和而成,如图15-2c 所示,且把和定义为切应变。
表示x方向的线元向y方向偏转的角度。
字号:[ 放大、标准]塑性力学是建立在实验基础之上的。
通过对实验结果的归纳总结,并提出合理的假设和简化模型,从而可以建立塑性力学基本方程。
屈服准则(Yield Criterion)是塑性力学基本方程之一,它是判断材料从弹性状态进入塑性状态的判据。
本章主要讨论金属材料最常用的两个屈服准则——屈雷斯加屈服准则和密塞斯屈服准则。
材料真实应力-应变曲线是建立塑性理论的重要依据,通常采用单向拉伸或单向压缩实验来确定这种曲线。
室温下在万能材料拉伸机上准静态拉伸(/S)标准试样,记录下来的拉伸力P与试样标距的绝对伸长Δl 之间的关系曲线称为拉伸图。
若试样的初始横截面面积为,标距长为,则条件应力(名义应力)和相对伸长ε(条件应变)为如果用和ε替代F和Δl,曲线形状不发生变化,只是改变刻度大小,可以很方便地将拉伸图变化为条件应力-应变曲线。
(1)弹性变形阶段Oe(2)均匀塑性变形阶段eb(3)局部塑性变形阶段bk真实应力试样瞬时横截面A 上所作用的应力Y 称为真实应力,亦称为流动应力。
由于试样的瞬时截面面积与原始截面面积有如下关系:所以2. 真实应变设初始长度为的试样在变形过程中某时刻的长度为l,定义真实应变为:3. 真实应力-应变曲线在均匀变形阶段,根据式(16-3)和(16-4)将条件应力-应变曲线直接变换成真实应力-应变曲线,即Y-∈曲线,如图16-2所示。
在b点以后,由于出现缩颈,不再是均匀变形,上述公式不再成立。
因此,b 点以后的曲线只能近似作出。
一般记录下断裂点k的试样横截面面积,按下式计算k点的真实应力-应变曲线。
这样便可作出曲线的段b'k'。
但由于出现缩颈后,试样的形状发生了明显的变化,缩颈部位应力状态已变为三向拉应力状态,实验表明,缩颈断面上的径向应力和轴向应力的分布如图16-3。
上式的意义如图16-4,表示在曲线Y-∈上,失稳点所作的切线的斜率为Yb,该斜线与横坐标轴的交点到失稳点横坐标的距离为∈= 1。
实验所得的真实应力-应变曲线一般都不是简单的函数关系。
在解决实际塑性成形问题时,为便于计算,常采用一些简化的材料模型,如图(一)指数硬化型大多数工程金属在室温下都有加工硬化,其真实应力-应变曲线近似于抛物线形状,如图16-5a,可用指数方程表达。
式中,B是强度系数;n是硬化指数。
B和n的值可用失稳点的特性确定如下,对上式求导数,得根据失稳点的特性又有比较上述两式,可得硬化指数n 是表明材料加工硬化特性的一个重要参数,n 值越大,说明材料的应变强化能力越强。
对金属材料,n 的范围是0<n<1。
B与n不仅与材料的化学成分有关,而且与其热处理状态有关,常用材料的和可查相关手册。
(二)有初始屈服应力的刚塑性硬化曲线型当有初始屈服应力时,其真实应力-应变曲线可表达为式中,m、——是与材料性能有关的参数由于与塑性变形相比,弹性变形很小,可忽略,如图16-5b。
所以,该形式为刚塑性硬化曲线型。
(三)有初始屈服应力的刚塑性硬化直线型为了简化计算,可用直线代替硬化曲线,如图16-5c,则为线性硬化形式,其真实应力-应变曲线表达式为式中,——是强度系数。
(四)无加工硬化的水平直线型对于几乎不产生加工硬化的材料,此时n=0,其真实应力-应变曲线是一水平直线,如图16-5d,表达式为这是理想刚塑性材料模型。
大多数金属在高温低速下的大变形及一些低熔点金属在室温下的大变形可采用无加工硬化模型假设。
如果要考虑弹性变形,则为理想弹塑性材料模型。
高温低速下的小塑性变形,可近似认为是这种情况。
字号:[ 放大、标准]应力应变之间的关系叫本构关系(Constitutive Relations),这种关系的数学表达式称为本构方程,也叫物理方程。
塑性应力应变关系和屈服准则都是求解塑性变形问题的基本方程。
单向应力状态下线弹性阶段的应力应变关系服从虎克定律。
将其推广到一般应力状态下的各向同性材料,就是广义虎克定律,即式中,E——是弹性模量(MPa);ν——是泊松比;G——是剪切模量(MPa)。
三个弹性常数E、ν 、G之间有如下关系将式(17-1)的、、相加整理后得即上式表明,弹性变形时其单位体积变化率()与平均应力成正比,说明应力球张量使物体产生了弹性体积改变。