金属凝固成形工艺
金属成型工艺有哪些【详解】

一图看懂17种常见金属成型工艺,一起来看看吧。
1、刨削加工—是用刨刀对工件作水平相对直线往复运动的切削加工方法,主要用于零件的外形加工。
刨削加工的精度为IT9~IT7,表面粗糙度Ra为6.3~1.6um。
2、磨削加工—磨削是指用磨料,磨具切除工件上多余材料的加工方法。
磨削加工是应用较为广泛的切削加工方法之一。
3、选择性激光熔融—在一个铺满金属粉末的槽内,计算机控制着一束大功率的二氧化碳激光选择性地扫过金属粉末表面。
在激光所到之处,表层的金属粉末完全熔融结合在一起,而没有照到的地方依然保持着粉末状态。
整个过程都需要在一个充满惰性气体的密封舱内进行。
4、选择性激光烧结—是SLS法采用红外激光器作能源,使用的造型材料多为粉末材料。
加工时,首先将粉末预热到稍低于其熔点的温度,然后在刮平棍子的作用下将粉末铺平;激光束在计算机控制下根据分层截面信息进行有选择地烧结,一层完成后再进行下一层烧结,全部烧结完后去掉多余的粉末,则就可以得到一烧结好的零件。
目前成熟的工艺材料为蜡粉及塑料粉,用金属粉或陶瓷粉进行烧结的工艺还在研究之中。
5、金属沉积—与“挤奶油”式的熔融沉积有些相似,但喷出的是金属粉末。
喷嘴在喷出金属粉末材料的同时,还会一并提供高功率激光以及惰性气体保护。
这样不会受到金属粉末箱尺寸的局限,能直接制造出更大体积的零部件,而且也很适合对局部破损的精密零件进行修复。
6、辊轧成型—辊轧成型方法是使用一组连续机架来把不锈钢轧成复杂形状。
辊子的顺序是这样设计的,即:每个机架的辊型可连续使金属变形,直到获得所需的最终形状。
如果部件的形状复杂,最多可用三十六个机架,但形状简单的部件,三、四个机架就可以了。
7、模锻—是指在专用模锻设备上利用模具使毛坯成型而获得锻件的锻造方法。
此方法生产的锻件尺寸精确,加工余量较小,结构也比较复杂生产率高。
8、模切—即下料工艺,将前制程成型后的薄膜定位在冲切模公模上,合模去除多余的材料,保留产品3D外形,与模具型腔相匹配。
金属材料的成型工艺

金属材料的成型工艺金属材料的成型工艺是指通过物理或化学方法将金属材料加工成所需形状的工艺过程。
成型工艺广泛应用于各个领域,如汽车、航空、船舶、建筑、制造业等。
它可以改变金属材料的形状、尺寸、性能和组织结构,使其适应不同的使用需求。
锻造是将金属材料加热至一定温度后,施加力并改变形状的工艺。
锻造可分为自由锻造、模锻和精锻。
自由锻造是直接对金属进行锻造,适用于简单形状的零部件。
模锻是使用模具对金属进行锤击或压制,适用于复杂形状和高精度要求的零部件。
精锻是在高温下对金属进行精密锻造,适用于高精度要求的零部件。
冲压是通过金属板材的拉伸、弯曲、切割和成形等工艺来制作零部件。
冲压工艺具有高效、节约材料、适用于大批量生产等优点,广泛应用于汽车制造、家电制造等领域。
铸造是通过将金属材料熔化后倒入模具中,使其凝固成型的工艺。
铸造可分为压力铸造和重力铸造。
压力铸造包括压铸、低压铸造和真空压力铸造。
压铸是将熔融金属注入压铸机模腔中,通过高压填充,并快速凝固成型。
低压铸造是将熔融金属通过压力填充式注射系统注入模具中,然后通过压力使其充满整个模腔,并凝固成型。
真空压力铸造是在真空环境中进行压铸,以提高铸件的质量和密度。
重力铸造是靠铸造机中的重力将熔融金属倒入模具中,凝固成型。
焊接是通过加热材料至熔化状态,通过外界压力和/或其他形式的能量传递,使金属材料连接起来的工艺。
常用的焊接方法包括电弧焊、气体保护焊、激光焊接等。
焊接工艺广泛应用于电子、汽车、船舶、航空航天等领域。
拉伸成型是将金属材料通过拉伸、挤压或者弯曲等方法成型的工艺。
拉伸成型可以提高材料的强度、硬度和耐磨性。
常见的拉伸成型工艺包括拉伸成型、锻造成型和爆炸成型等。
热成型是通过加热金属材料至塑性状态,然后在模具中进行变形的工艺。
热成型可以提高材料的塑性,使其更容易成形,并改变金属材料的结构和性能。
常用的热成型方法包括热压成型、热挤压、热拉伸等。
挤压成型是通过将金属材料放置在模具中,然后施加压力,使其通过模孔挤压成型的工艺。
凝固成形

五、熔模铸造
熔模铸造师用易熔材料制成模型,然后在模型上 涂挂耐火材料,经硬化后,将模型熔化、排出型外, 从而获得无分型面的铸型。
六、离心铸造 离心铸造是将液态金属浇入高速旋转 (250~1500r/min)的铸型中,使金属注在离 心力作用下充填铸型并凝固的铸造方法。
几种常见凝固成形方法的比较
凝固成形
凝固成形(铸造)的定义 液态 金属 充 型 凝 固 铸 件
凝固成形俗称铸造,是将金属材料熔化成液态后浇注入与拟 成形的零件形状及尺寸相适应的模型空腔中,待液态金属冷却凝 固后将铸型打开(或破坏)取出所形成的铸件毛坯,然后清理掉 由于工艺需要而添加的部分(如浇口,冒口等)后,即可得到所 需的铸件。
二、金属型铸造
金属型铸造就是将液态金属浇入金属铸型,以获 得铸件的一种凝固成形方法。 由于金属型可以反复使用,故有永久型铸造之称。
三、压力铸造
压力铸造是在高压下(30~70MPa)快速地将液 态或半液态金属压入金属铸型中,并使液态金属在压 力下凝固,以获得铸件的凝固成形方法。
四、低压铸造
低压铸造是介于金属型铸造和压力铸造之间的一 种铸造方法,在30~70kPa压力的作用下,将金属液 注入型腔,并在压力下凝固,以获得铸件的凝固成形 方法。
液态金属
获得合格的高质量的液态金属是凝固成形技术的 非常重要的方面。 所谓合格的,高质量的液态金属,通常包括三个 方面的要求:
1、具有所需要的温度 2、杂质含量低 3、具有所要求的化学成分
凝固成形方法
一、砂型铸造
砂型铸造——在砂型中生产铸件的铸造方法。钢、 铁和大多数有色合金铸件都可用砂型铸造方法获得。 由于砂型铸造所用的造型材料价廉易得,铸型制造简 便,对铸件的单件生产、成批生产和大量生产均能适 应,长期以来,一直是铸造生产中的基本工艺。
铝合金压铸工艺

铝合金压铸工艺简介铝合金压铸是一种常见的金属成形工艺,通常用于制造各种铝合金零件。
其原理是将熔融的铝合金注入到模具中,并在一定的压力下冷却和凝固,最终得到所需的铝合金零件。
本文将介绍铝合金压铸的工艺流程以及相关的工艺参数。
工艺流程铝合金压铸的工艺流程主要包括模具准备、铝合金液态处理、注液和凝固、零件脱模和表面处理等几个主要步骤。
下面将详细介绍每个步骤的内容。
1. 模具准备在铝合金压铸工艺中,模具是非常重要的一部分。
首先需要根据所需零件的形状和尺寸设计制作模具。
模具通常由两部分构成,一部分是固定模,另一部分是活动模。
固定模固定在压铸机上,而活动模则与固定模相连,在注液和凝固过程中参与零件的成形。
模具内部还需要加工一些通道和排气口,以便铝合金的顺利注入和冷却。
在使用模具之前,还需要对其进行表面处理,以确保零件的顺利脱模。
2. 铝合金液态处理铝合金压铸需要使用熔融的铝合金作为原料。
在铝合金的制备过程中,需要控制好温度和成分的配比。
通常采用电炉或燃气炉加热铝合金,直到其达到液态状态。
同时,在熔炼过程中还需要添加一些合适的轻质合金元素,以提高铝合金的流动性和强度。
3. 注液和凝固当铝合金达到液态后,可以开始注入模具中进行成型。
首先将模具合拢,并在一定的压力下将铝合金注入到模具的腔室中。
在注液的过程中,铝合金要通过模具内部的通道和排气口,以确保零件填充完全且没有气泡。
注液的时间和压力应根据零件的大小和形状进行调整。
当铝合金填充完毕后,需要保持一定的压力,直到零件完全凝固。
4. 零件脱模在铝合金凝固后,需要将零件从模具中取出,这个过程称为脱模。
脱模的方法有很多种,可以通过机械力或气动力来推动零件从模具中顺利脱离。
在脱模之前,需要注意保护零件的表面,以免在脱模过程中造成刮擦或其他损坏。
5. 表面处理铝合金压铸零件脱模后,通常还需要进行一些表面处理工艺,以提高零件的外观和性能。
常见的表面处理方法包括机械抛光、电镀、喷涂、阳极氧化等。
金属材料成形工艺及控制
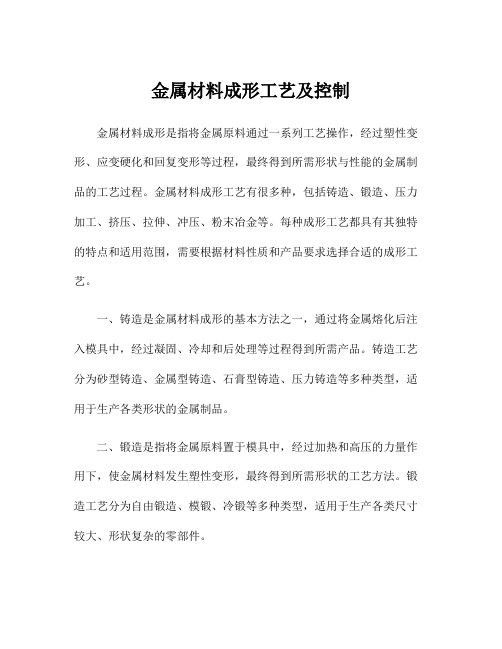
金属材料成形工艺及控制金属材料成形是指将金属原料通过一系列工艺操作,经过塑性变形、应变硬化和回复变形等过程,最终得到所需形状与性能的金属制品的工艺过程。
金属材料成形工艺有很多种,包括铸造、锻造、压力加工、挤压、拉伸、冲压、粉末冶金等。
每种成形工艺都具有其独特的特点和适用范围,需要根据材料性质和产品要求选择合适的成形工艺。
一、铸造是金属材料成形的基本方法之一,通过将金属熔化后注入模具中,经过凝固、冷却和后处理等过程得到所需产品。
铸造工艺分为砂型铸造、金属型铸造、石膏型铸造、压力铸造等多种类型,适用于生产各类形状的金属制品。
二、锻造是指将金属原料置于模具中,经过加热和高压的力量作用下,使金属材料发生塑性变形,最终得到所需形状的工艺方法。
锻造工艺分为自由锻造、模锻、冷锻等多种类型,适用于生产各类尺寸较大、形状复杂的零部件。
三、压力加工是指通过金属材料受到外力压缩、拉伸、弯曲等作用,使其发生塑性变形,并最终得到所需形状的金属成形方法。
压力加工包括挤压、拉伸、剪切、折弯等多种工艺,适用于生产各类薄板、管材、棒材等产品。
四、挤压是指将金属加热至熔点后,在压机的作用下通过模具挤出,得到所需形状的工艺方法。
挤压工艺适用于生产各类型材、异型材、电线电缆、铝箔等产品。
五、拉伸是指通过将金属材料置于拉伸机中,受到拉力的作用下,使其发生塑性变形,最终得到所需形状的金属成形方法。
拉伸工艺适用于生产各类细丝、线材、管子等产品。
六、冲压是指通过冲压机将金属板材置于模具中,经过冲击力的作用下,使其发生塑性变形,最终得到所需形状的金属成形方法。
冲压工艺适用于生产各类薄板金属产品,如汽车车身板、电器外壳等。
七、粉末冶金是指将金属粉末与非金属粉末按一定配比混合,压制成坯料后通过烧结等过程,最终得到具有一定形状和性能的金属制品的工艺方法。
粉末冶金工艺适用于生产各类复杂形状、高精度的金属制品。
以上是金属材料成形工艺的简要介绍,为了保证金属制品质量和实现成形工艺的控制,需要进行相应的工艺控制。
压铸的工作原理

压铸的工作原理压铸是一种常用的金属零件生产工艺,主要用于生产大批量、高精度、复杂形状的零件。
它是通过将熔融金属注入到模具中,快速凝固成形而得名。
本文将介绍压铸的工作原理及其关键步骤。
一、压铸的工作原理压铸的工作原理是将熔融金属注入到模腔中,然后利用高压力将金属填满模具中的所有空隙。
之后,将模具冷却并打开,将固化的金属零件从中取出。
整个过程分为注射、压力、冷却和脱模四个阶段。
二、压铸的关键步骤1. 设计模具模具的质量和设计直接影响到铸件的质量。
准确的模具设计能够减少或甚至消除一些质量问题。
模具应该能够满足所需的尺寸和表面质量。
2. 加热熔融金属在压铸之前,需要将金属加热到熔点以上。
熔化的金属通常是锌、铝、镁和铜等合金。
金属加热的温度和时间由所使用的材料和压铸时的要求而定。
3. 注射金属至模具中金属熔化后,将其从炉中注入到模具中。
这个过程需要控制注入速度和数量,以确保金属填满整个模腔,但不会造成过量冲压和漏出。
4. 施加高压将金属填满模具金属注入到模具中后,施加高压以将金属压缩并填满模具内部,保证零件的密度和精度。
通常,压力的大小是根据所需的密度和强度来确定的。
5. 冷却金属零件在金属灌注完全填满模具后,直接将模具放在冷却装置中。
通过使金属快速凝固,可以保证零件的准确性和表面质量。
冷却时间通常由金属和设计要求决定。
6. 打开模具并取出零件当金属快速凝固后,就可以打开模具,并将铸件从中取出。
在取出零件之前,需要检查模具中是否还有金属残留物。
通常需要进行修理或抛光以去除表面缺陷。
三、结论压铸是一种高效、高精度、高质量的金属生产工艺。
准确的模具设计和良好的压力控制是获得优质铸件的关键。
压铸具有广泛的应用,可以用于生产各种工业部件、汽车零件和电子设备等。
不锈钢精铸的工作原理
不锈钢精铸的工作原理
不锈钢精铸是一种通过高温熔融不锈钢材料并在特定模具中凝固形成预定形状的工艺。
它工作的原理主要包括以下几个步骤:
1. 材料准备:选取合适的不锈钢原料,准确计量并按照配比要求进行混合。
2. 熔炼:将混合好的不锈钢原料放入电炉或其他熔炼设备中,加热至高温使其熔化。
3. 模具制备:事先准备好具有所需形状的模具,可以是砂型、金属模具等。
模具需要经过表面处理,以确保铸件的光洁度和尺寸精度。
4. 铸造:熔融状态的不锈钢材料被倒入事先准备好的模具中,填充整个模腔。
5. 冷却:铸件在模具中冷却和凝固,使不锈钢逐渐固化成所需形状。
6. 精整:冷却后,取出铸件并进行精整加工,包括切割、研磨、抛光等,以达到最终的精确尺寸和表面质量要求。
通过以上步骤,不锈钢精铸工艺可以制造出具有较高精度、良好表面质量和机械性能的铸件,被广泛应用于航空航天、汽车、工程机械等领域。
铸造成形成形原理、工艺特点
铸造成形成形原理、工艺特点
铸造成形是指将熔融金属或合金注入铸型中,通过冷却凝固形成所需的产品形状的制造过程。
铸造成形是一种非常重要的金属加工工艺,具有成本低、生产周期短、生产效率高等优点。
本文将介绍铸造成形的成形原理、工艺特点等相关内容。
1. 成形原理
铸造成形的成形原理是将熔融金属或合金注入铸型中,通过冷却凝固形成所需的产品形状。
铸造成形的成形过程主要分为注型、凝固、冷却、脱模等四个步骤。
在注型过程中,将熔融金属或合金注入铸型中,填满整个铸型腔,形成所需的产品形状。
凝固过程中,熔融金属或合金开始凝固,形成固态金属或合金。
冷却过程中,将固态金属或合金从铸型中取出后,通过自然冷却或强制冷却,让产品内部温度均匀降至室温。
最后,脱模过程中,将产品从铸型中取出,完成铸造成形的全过程。
2. 工艺特点
1) 生产周期短:铸造成形的生产周期短,可快速生产出大批量的产品。
2) 成本低:铸造成形的设备和原材料成本相对较低,可大幅降低产品生产成本。
3) 适用性广:铸造成形可用于生产各种形状的金属或合金制品,适用性非常广泛。
4) 生产效率高:铸造成形可进行自动化生产,提高生产效率和
生产能力,同时可大幅降低人力成本。
5) 重型、大型产品生产优势:铸造成形可生产大型、重型产品,如机床床身、发动机缸盖等。
总之,铸造成形是一种非常重要的金属加工工艺,具有成本低、生产周期短、生产效率高等优点,适用性广泛,可生产出各种形状的金属或合金制品。
压铸成形工艺及模具设计
压铸成形工艺及模具设计一、压铸成形工艺1.压铸成形工艺是指将熔融的金属注入到压铸模腔中,经过一定的冷却时间和压力,使金属凝固成型的一种工艺。
压铸成形工艺主要用于制造复杂形状、精度高、表面质量要求较高的金属零件。
2.压铸成形工艺流程:(1)模具闭合:将模具的上下模闭合,并确保两模之间的间隙均匀。
(2)进料:将预先加热熔融的金属材料注入到压铸机的料斗中。
(3)注料:借助压铸机的压力将熔融金属注入到模腔中。
(4)冷却:通过冷却系统使金属冷却固化。
(5)脱模:打开模具,将成型的零件取出。
3.压铸成形工艺的优势:(1)成型周期短:压铸成形工艺生产周期短,能够高效地生产大量复杂形状的金属零件。
(2)生产精度高:由于模具的尺寸稳定,压铸成形工艺能够保证零件的尺寸精度高,表面质量好。
(3)材料利用率高:压铸成形工艺可以通过智能化控制,精确控制金属的注入量,减少材料浪费。
(4)工序简单:压铸成形工艺只需进行模具的闭合、注料、冷却和脱模等简单工序即可完成零件的生产。
二、模具设计1.模具是压铸成形工艺中非常重要的工具,模具设计的好坏直接影响到成型零件的质量和生产效率。
2.模具设计需要考虑的因素:(1)零件的形状复杂度:根据零件的形状复杂度选择合适的模腔结构,以保证零件的成型质量。
(2)材料的流动性:通过模具的设计,合理控制金属材料的流动性,以避免金属在注入过程中产生气孔和缺陷等问题。
(3)模具的耐用性:考虑到模具在生产过程中需要承受高温和高压等环境,应选择耐磨、耐腐蚀的材料制作模具。
(4)模具的冷却系统:设计合理的冷却系统,以确保模具在生产过程中能够及时散热,提高生产效率。
(5)模具的可维修性:合理设计模具的结构,以便于进行模具的维修和调整,延长模具的使用寿命。
3.模具设计的步骤:(1)确定零件的几何形状和尺寸。
(2)选择模具的结构类型。
(3)设计模腔和配套零部件。
(4)设计冷却系统和排气系统。
(5)选择模具材料和热处理工艺。
压铸铝和挤压铝材质
压铸铝和挤压铝材质
压铸铝和挤压铝材质都是铝合金材料,但它们的制备工艺和性能有所不同。
1. 压铸铝:压铸是一种将液态金属注入到模具中,通过高压力和高速冷却过程,将金属凝固成形的工艺。
压铸铝通常具有较高的成型精度和表面光洁度,可以生产复杂形状的零件。
压铸铝的力学性能较好,具有较高的抗拉强度和硬度,同时具备一定的耐腐蚀性能。
压铸铝的缺点是晶粒粗大,易产生气孔和夹杂。
2. 挤压铝:挤压是一种通过将铝合金坯料加热到可塑状态,然后在模具中施加压力,通过模孔挤出来形成所需截面形状的工艺。
挤压铝的优点是制作成本低、制作过程中不会产生气孔和夹杂等缺陷。
挤压铝具有较好的力学性能,具有较高的强度和硬度,同时具备一定的耐蚀性能。
挤压铝的缺点是成型精度较低,表面光洁度一般较差。
总的来说,压铸铝适用于制造复杂形状的零件,要求高的表面光洁度和尺寸精度,而挤压铝适用于制造长条形截面的构件或者对成本要求较高的产品。
具体选择哪种材质要根据具体的应用和要求来决定。
- 1、下载文档前请自行甄别文档内容的完整性,平台不提供额外的编辑、内容补充、找答案等附加服务。
- 2、"仅部分预览"的文档,不可在线预览部分如存在完整性等问题,可反馈申请退款(可完整预览的文档不适用该条件!)。
- 3、如文档侵犯您的权益,请联系客服反馈,我们会尽快为您处理(人工客服工作时间:9:00-18:30)。
1.1.22The production of steelcastings
(一)铸钢的铸造工艺特点 铸造性能差:熔点高,钢液易氧化;流动性差;收缩较大 ,体收缩约为灰铸铁的三倍,线收缩约为灰铸铁的两倍。 因此铸钢较铸铁铸造困难,为保证铸件质量,避免出现缩 孔、缩松、裂纹、气孔和夹渣等缺陷,必须采取更为复杂 的工艺措施: (1)型砂的强度、耐火度和透气性要高 ,原砂要采用 耐火度很高的人造石英砂。中、大件的铸型一般都采用强 度较高的CO2硬化水玻璃砂型和粘土干砂型。为防止粘砂 ,铸型表面应涂刷一层耐火涂料。
• 液态收缩 • 凝固收缩 • 固态收缩
易造成缩松和缩孔
:是铸造应力、变形和裂 纹等缺陷产生的基本原因
请问影响合金收缩的因素有哪些?P7
• 化学成分 • 浇注温度 • 铸件结构和铸型条件
请问缩松和缩孔的形成条件分别是什么?P7
• 缩孔:铸件以逐层凝固的方式凝固 • 缩松:铸件以糊状凝固的方式凝固
Inoculation
• 定义:向铁液中冲入硅铁合金孕育剂,然后进行
浇注的处理方法。
• • • 。
硅铁合金孕育剂 硅铁 孕育剂
Advantages:
1 加入孕育剂后,由于铁水均匀分布着大量 外来人工晶核,因而有利于石墨化,降低白口 倾向,提高灰口铸铁的强度和硬度; 2 冷却速度对组织和性能的影响较小,铸件 厚大截面的力学性能较为均匀。 Application : 孕育铸铁适于制造要求较高强度、高耐磨性和 高气密性的铸件,特别是厚大铸件,如床身、 凸轮、汽缸体和汽缸套等。
2 出铁水炉温度较高~至少在1420℃以上。 3 球化处理和孕育处理。
外壳胀大造成最后凝固部位出现问题
冲入法球化示意图
1,顺序凝固原则,安放冒口和冷铁
4 铸型工艺
2,采用经烘干的铸型或水玻璃砂制作铸型
5 球墨铸铁的热处理~提高强度、硬度及耐磨性,并减少铸造残余应力。
(三) Malleable iron(可锻铸铁)
宏观缩松多分布在铸件最后凝固的部位, 显微缩松则是存在于在晶粒之间的微小孔洞
缩松的的形成
5、铸件的内应力、变形和裂纹
(1)铸件的内应力:铸件的凝固收缩受到阻碍时,就会 产生内应力。有两类: a)热应力:Solidification and cooling process,
different area due to uneven shrinkage caused by stress.
2)使用补缩冒口和冷铁,实现定向凝固 , 补缩冒口一般为铸 件质量的25%~50%,造型和切割冒口的工作量大。如图156所示为ZG230-450齿圈的铸造工艺方案。该齿圈尽管壁厚 均匀,但因壁厚较大(80mm),心部的热节处(整圈)极易 形成缩孔和缩松,铸造时必须保证对心部的充分补缩。由于冒 口的补缩距离有限,为此,除采用三个冒口外,在各冒口间还 须安放冷铁,使齿圈形成三个独立的补缩区。浇入的钢液首先 在冷铁处凝固,形成朝着冒口方向的定向凝固,使齿圈上各部 分的收缩都能得到金属液的补充 (3)严格掌握浇注温度,防止过高或过低 低碳钢(流动性较 差)、薄壁小件或结构复杂不容易浇满的铸件,应取较高的浇 注温度;高碳钢(流动性较好)、大铸件、厚壁铸件及容易产 生热裂的铸件,应取较低的浇注温度。一般为1500~1650℃ 。
请将下列合金的流动性排序:P4 硅黄酮,铸钢,灰铸铁,
灰铸铁>硅黄铜>铸钢
提示: 1.一般规律:合金的凝固范围宽,流动性差。 2.磷、硅能提高流动性;锰对流动性影响不 大;硫易形成硫化锰,降低流动性。
请简述合金的凝固方式有哪些?P6
• 逐层凝固 • 糊状凝固 • 中间凝固
请简述合金的收缩方式有哪些?P6
• 冷隔、浇不足 • 气孔 • 夹渣 • 缩孔
铸件的凝固方式
4、铸件中的缩孔和缩松
缩孔是容积较大而集中的孔洞。缩松是细 小而分散的孔洞。
圆柱体铸件中缩孔形成示意图
(2)缩松:Distribution in the casting axis region, thick parts
or near the gate. The basic reason is that liquid shrinkage and shrinkage in the solidification process.
防止措施:改善铸型和型芯的退让性;采用“同时
凝固原则”铸造工艺.....2)铸件的变形及铸件的裂纹 •
•
铸件变形产生的原因:铸件为松弛内应力而 发生的不同程度的形状变化。是一种自发过程. 铸件裂纹产生原因:内应力超过合金的强度
极限
合金的铸造性能主要有哪些?P3
温 度
900-980℃
Fe 3C→A+石墨 720℃
750℃
A→F+石墨 650℃ P→F+石墨 ① F+团絮状石墨 时间
② P+团絮状石墨
图1-4-7 可锻铸铁的石墨化退火工艺 可锻铸铁的石墨化退火工艺
(四) Production of Vermicular Iron(蠕墨铸铁的生产)
定义: 在一定成分的铁液中加入适量的蠕化剂进行蠕 化处理而成的。
请问缩孔、缩松的防止措施有哪些?P8
A.采用定向凝 固的凝固方式
安放冒口 放置冷铁
B.合理确定铸件的浇注位置、 内浇道位置及浇注工艺
铸件的裂纹有哪些分类及它们的防止措施?P12
分类:热裂和冷裂 防止措施:结构设计合理,改善退让性,
减少内应力,降低合金的脆性。。。。。
铸件的变形有哪些防止措施?P12 防止变形方法: • a) 壁厚均匀,形状对称,同时凝固; • b)反变形法: • c)进行去应力退火: • d) 设置工艺肋:
•
合金的充型能力:In the actual
production conditions, the molten metal to fill the mold cavity, to obtain complete shape, contour clear casting capacity
请指出下列图片存在哪些铸造缺陷?
请问铸件中的气孔有哪些特征及其分类:P13
• 特征:空洞内壁光滑,明亮或带有轻微氧
化 色,一般呈梨形,椭圆形等 侵入气孔
分 类
析出气孔
反应气孔
1.1.2
Common alloy castings production
Cast iron
Alloy castings
Cast steel
Copper and copper alloys
Non ferrous alloy castings
Aluminium and aluminium alloys
1
1 The production of iron castings
• (1)Gray cast iron production
Grey cast iron is the most widely used cast iron, its crop occupies the 80% above of total output of cast iron. Common gray cast iron has a generally good technological properties, casting process is relatively simple. But its low strength, wall thickness, which is suitable for the production of stress is smaller, more complex shape and castings, such as base(机座), pump shell(泵体), box(箱体), not manufacturing wall thickness of casting. Therefore, in order to further improve the mechanical properties of gray cast iron, is more effective measures to reduce carbon, silicon content, and inoculation(孕育处理) 。
Metal solidification process design The solidification of metal structure Design
注释:solidification 凝固成形
Logo
活动流程:
1. 先由本组成员概括本节知识要点,该成员概括结 束后将会按照小组顺序提问夯实基础概念题(每题 一分)(即:在1分钟之内该成员将连续向小组提出 问题)按照答对题数给分。 2.当本组5名成员概括结束后进行第二轮提问能力 提升题(涵盖本章所有知识)。本环节可抢答,小 组成员可高举手中的组号以抢得答题机会。能力提 升题按照难度有3分,5分题。 3.按照总分高低进行排名。
The production of ductile cast iron(球墨铸铁)
• • • • • • • •
球墨铸铁 In the production process : 1 严格控制铁液的化学成分 High carbon ~提高铁水流动性,消除白口和减少缩松, 使石墨球化好。 Low manganese (锰)~锰会使铸铁的加工变得困难 。 Low sulfur(低硫)~硫会消耗球化剂,还会产生球化衰 退和皮下气孔。 Low phosphorus(低磷)~增加冷脆性,降低球墨铸铁 的塑性和韧性。 还有一定量的Mg、稀土元素。
防止的根本途径:壁厚均匀;采用“同时凝固原则”
铸造工艺;薄处设冒口,厚处放冷铁 ....... b)机械应力(收缩应力): Casting shrinkage was