液态成型第二章第一节,第二节分析
第一章 金属液态成形理论基础

第一节 液态金属充型能力与流动性
0、什么是液态金属的充型能力
1)定义:
液体金属充满铸型型腔,获得尺寸精确、轮廓清晰的 成型件的能力,称为充型能力。
2)充型能力对成型的影响
充型能力不足时,会产生浇不足、冷隔、夹渣、气孔 等缺陷。
3)影响充型能力的因素
充型能力首先取决于金属本身的流动性(流动能力),同 时又受铸型性质、浇注条件和铸件结构等因素影响。
一、铸件的凝固方式
在铸件凝固过程中,其断面上一般存在三个区 域:固相区、凝固区和液相区。
1、分类
依据对铸件质量影响较大的凝固区的宽窄划分 铸件的凝固方式为如下三类:
(1)逐层凝固
纯金属和共晶成分的合金在凝固过程中不存在液、固并 存的凝固区,随着温度下降,固体层不断加厚,液体不 断减少,直达铸件中心,这种凝固方式称为逐层凝固。
机械应力
二、铸件的变形及其防止
1、变形的原因:
铸件内部残余内应力。 只有原来受拉伸部分产生压缩 变形、受压缩部分产生拉伸变 形,才能使铸件中的残余内应 力减小或消除。
平板铸件的变形
杆件的变形
床身铸件的变形
粱形铸件的弯曲变形
2、防止措施:
减小应力; 将铸件设计成对称结构,使其内应力互相平衡; 采用反变形法; 设置拉肋; 时效处理。
2、冷裂纹的特征
裂纹细小,呈连续直线状,裂缝内有金属光泽或轻 微氧化色。
3、防止措施
凡是能减少铸件内应力和降低合金脆性的因素 均能防止冷裂。 设置防裂肋亦可有效地防止铸件裂纹。
防裂肋
三、合金的吸气性
液态合金中吸入的气体,若在冷凝过程中不能溢 出,滞留在金属中,将在铸件内形成气孔。
一)气孔的危害
气孔破坏了金属的连续性,减少了其承载的有效 截面积,并在气孔附近引起应力集中,从而降低 了铸件的力学性能。 弥散性气孔还可促使显微缩松的形成,降低铸件 的气密性。
第2章金属液态成形
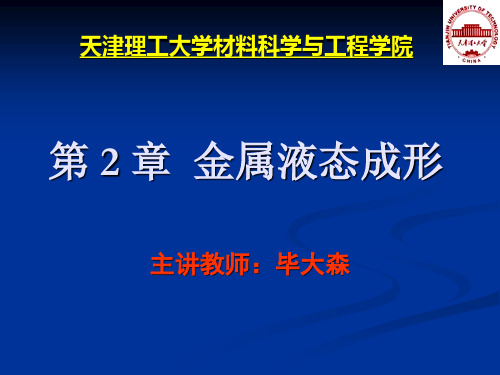
第2章 金属液态成形
固态金属按原子聚集形态分为晶体与非晶 体。
晶体——凡是原子在空间呈规则的周期性 重复排列的物质称为晶体。
单晶体——在晶体中所有原子排列位向相 同者称为单晶体
第2章 金属液态成形
(1)金属从固态熔化为液态时的变化 金属熔化时的体积增大量在3%~7%的
范围内。而金属从绝对零度到熔点温度的 固态体积膨胀量几乎都是约7%。
固态金属的结构可以看作由理想的晶体结 构加上缺陷(空穴、间隙原子、位错、晶 界等)组成。随着温度的升高,固态金属 中缺陷的数量增加,活动性增大。
第2章 金属液态成形
在力F的作用下,在X轴方向每一层原子 都相对于下一层原子产生相对运动,其平 均速度 v qF。
第2章 金属液态成形
v 值也可以写成微分形式:
v vx q F
y
作用在流体单位面积上的力用Pxy表示, 则:
F
Pxy 2
或者 F Pxy 2
第2章 金属液态成形
由上两式可得:
第2章 金属液态成形
如图是由X射线衍射结果整理而得的原子 密度分布曲线。
横坐标r为观测点至某一任意选定的原子 (参考中心)的距离,对于三维空间,它 相当于以所选原子为球心的一系列球体的 半径。
纵坐标表示当半径增减一个单位长度时, 球体(球壳)内原子个数的变化值,其中 (r)称为密度函数。
第2章 金属液态成形
第2章 金属液态成形
液态金属的粘度在温度不太高时,随温度 的升高粘度下降。
难熔化合物的粘度较高,而低熔点的共晶 成分合金的粘度低。
材料成型内容要点(完整版)
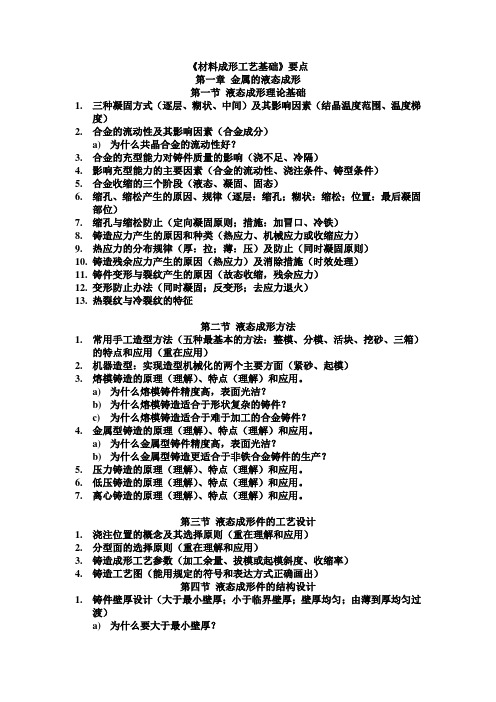
《材料成形工艺基础》要点第一章金属的液态成形第一节液态成形理论基础1.三种凝固方式(逐层、糊状、中间)及其影响因素(结晶温度范围、温度梯度)2.合金的流动性及其影响因素(合金成分)a)为什么共晶合金的流动性好?3.合金的充型能力对铸件质量的影响(浇不足、冷隔)4.影响充型能力的主要因素(合金的流动性、浇注条件、铸型条件)5.合金收缩的三个阶段(液态、凝固、固态)6.缩孔、缩松产生的原因、规律(逐层:缩孔;糊状:缩松;位置:最后凝固部位)7.缩孔与缩松防止(定向凝固原则;措施:加冒口、冷铁)8.铸造应力产生的原因和种类(热应力、机械应力或收缩应力)9.热应力的分布规律(厚:拉;薄:压)及防止(同时凝固原则)10.铸造残余应力产生的原因(热应力)及消除措施(时效处理)11.铸件变形与裂纹产生的原因(故态收缩,残余应力)12.变形防止办法(同时凝固;反变形;去应力退火)13.热裂纹与冷裂纹的特征第二节液态成形方法1.常用手工造型方法(五种最基本的方法:整模、分模、活块、挖砂、三箱)的特点和应用(重在应用)2.机器造型:实现造型机械化的两个主要方面(紧砂、起模)3.熔模铸造的原理(理解)、特点(理解)和应用。
a)为什么熔模铸件精度高,表面光洁?b)为什么熔模铸造适合于形状复杂的铸件?c)为什么熔模铸造适合于难于加工的合金铸件?4.金属型铸造的原理(理解)、特点(理解)和应用。
a)为什么金属型铸件精度高,表面光洁?b)为什么金属型铸造更适合于非铁合金铸件的生产?5.压力铸造的原理(理解)、特点(理解)和应用。
6.低压铸造的原理(理解)、特点(理解)和应用。
7.离心铸造的原理(理解)、特点(理解)和应用。
第三节液态成形件的工艺设计1.浇注位置的概念及其选择原则(重在理解和应用)2.分型面的选择原则(重在理解和应用)3.铸造成形工艺参数(加工余量、拔模或起模斜度、收缩率)4.铸造工艺图(能用规定的符号和表达方式正确画出)第四节液态成形件的结构设计1.铸件壁厚设计(大于最小壁厚;小于临界壁厚;壁厚均匀;由薄到厚均匀过渡)a)为什么要大于最小壁厚?b)为什么要小于临界壁厚?c)壁厚不均匀会产生什么问题?2.铸件壁间连接(圆角;避免锐角)3.铸件筋条设计(避免十字交叉)4.铸件外形设计和铸件内腔设计(理解;重在应用)5.结构斜度的设计(结构斜度与起模斜度的区别;重在应用)第二章金属的塑性成形第一节塑性成形工艺基础1.常用的六类塑性成形方法(轧制、拉拔、挤压、自由锻、模锻、板料冲压)2.与铸造比较,塑性成形法的最显著的特点(性能好,但形状不能太复杂)3.塑性变形对金属组织和性能的影响(冷变形条件下和热变形条件下;纤维组织及其性能特点)4.金属可锻性的衡量指标(塑性、变形抗力)及影响因素(成分;组织;温度)5.金属加热缺陷(过热、过烧、脱碳、过渡氧化)与碳钢始锻温度(低于固相线200℃)第二节热锻成形工艺1.自由锻基本工序(镦粗、拔长、冲孔、弯曲、切割、扭转)2.自由锻件结构工艺性3.模锻的基本原理(理解)及特点4.胎模锻的概念及特点(理解)第三节板料冲压1.两大类基本工序(分离工序和变形工序)2.冲裁的概念;冲裁变形过程(弹性变形阶段、塑性变形阶段、断裂分离阶段)及冲裁件断面特征(塌角或圆角带;光亮带;断裂带)3.切断的概念4.弯曲变形的特点(内:压;外:拉);弯曲的质量问题(弯裂;回弹);弯裂的防止办法(限制最小弯曲半径;弯曲线与纤维方向垂直);回弹的防止办法(模具角度比弯曲件角度小一个回弹角值)5.拉深的概念;拉深和冲裁工序所使用的凸、凹模之间的区别(间隙大小;圆角)拉深件质量问题(拉裂与起皱)6.拉深系数的概念及计算7.三类冲模的概念四种挤压方式第三章材料的连接成形第一节焊接成形工艺基础1.三大类焊接方法(熔化焊;压焊;钎焊);2.熔焊的冶金特点(理解)及保证焊接质量的基本措施(保护焊接区;渗加合金元素;脱氧脱硫);3.焊接接头的概念(焊缝加热影响区);4.焊接热影响区的概念(焊接过程中,焊缝两侧受焊接热作用而发生组织与性能变化的区域);5.低碳钢焊接热影响区的组成及其特点(熔合区;粗晶,性能差;过热区:粗晶,性能差;正火区:细晶,性能好;部分相变区:性能稍差);6.焊接应力与变形产生的原因(局部加热);7.防止和减少焊接应力的措施(焊前预热;焊接次序;焊后缓冷;焊后去应力退火);8.焊接变形的形式(收缩变形;角变形;弯曲变形;扭曲变形;波浪变形);9.防止和减小焊接变形的措施(刚性固定;反变形;焊接次序;焊前预热;焊后缓冷;矫正);10.焊接缺陷的种类及其检验方法(理解);第二节焊接方法1.焊条的组成及作用(焊芯和药皮;焊芯:作电极和焊缝的填充金属;药皮:稳定电弧燃烧;保护焊接区;渗加合金元素;脱氧脱硫);a)为什么焊条药皮中要加脱氧剂?2.两种重要的焊条(J422、J507);焊条选用原则(重在应用)3.埋弧焊的原理(理解)、特点和应用范围(水平位置焊接长直焊缝;大直径环形焊缝)b)埋弧焊的生产率为什么高于焊条电弧焊?c)埋弧焊与焊条电弧焊相比,为什么可以节省材料?d)埋弧焊为什么不能实现全位置焊接?4.氩弧焊的原理、特点及其应用;5.二氧化碳气体保护焊的原理、特点及其应用(注意与氩弧焊比较理解)e)二氧化碳保护焊时焊丝的成分有何要求,为什么?6.电渣焊的原理(电阻热)及其应用。
第2章 液态成形中的流动与传热

2013-9-12
上一内容 Principle 下一内容of Materials Forming 返回 回主目录
2013-9-12
14
材料成型原理——液态成形
15 5表面张力 造型材料一般不被液态金属润湿,即润湿角>90°。 故液态金属在铸型细簿部分的液面是凸起的,而由表面张力 产生一个指向液体内部的附加压力,阻碍对该部分的充填。 所以,表面张力对薄壁铸件、铸件的细簿部分和棱角的成形 有影响。型腔越细薄,棱角的曲率半径越小,表面张力的影 响则越大。为克服附加压力的阻碍,必须在正常的充型压头
材料成型原理——液态成形
第 2 章 液态成形中的流动与传热
2013-9-12
1
Principle of Materials Forming
材料成型原理——液态成形
2.1 液态金属的流动性与充型能力
充型能力是指液态金属充满铸型型腔,获得形状完整、轮廓清晰的铸件的 能力,即液态金属充填铸型的能力。是设计浇注系统的重要依据之一;此外 还涉及此过程中可能产生的浇不足、冷隔、砂眼、铁豆、抬箱,以及卷入性 气孔、夹砂等缺陷的防止措施。因此获得质量健全的铸件必须对此进行掌握
上增加一个附加压头h。
液态金属充填铸型尖角处的能力还与铸型的激冷能力有 关。在激冷作用较大的铸型中,可在合金中加入表面活性元 素或采用特殊涂料,降低或润湿角 。
上一内容 Principle 下一内容of Materials Forming 返回 回主目录
2013-9-12
材料成型原理——液态成形
铸型的蓄热系数b2表示铸型从其中的金属中吸取并储存于本 身中热量的能力。蓄热系数b2越大,铸型的激冷能力就越强, 金属液于其中保持液态的时间就越短,充型能力下降。 c2ρ2---单位体积的铸型在温度升高1℃时所吸取的热量。 此值大,铸型吸取较多的热量而本身的温升较小,使金属 与铸型之间在较长时间内保持较大的温差。 λ2-铸型的导热系数大,表示从金属吸取的热量能很快地由 温度较高的型内表面传导到温度较低的“后方”,使铸型参 加蓄热的部分增多,从而能够储存更多的热量,并且铸型内 表面的热量能迅速传走,温升速度也就比较缓慢,而保持继 续吸取热量的能力。
第二章 液态成形工艺——铸造
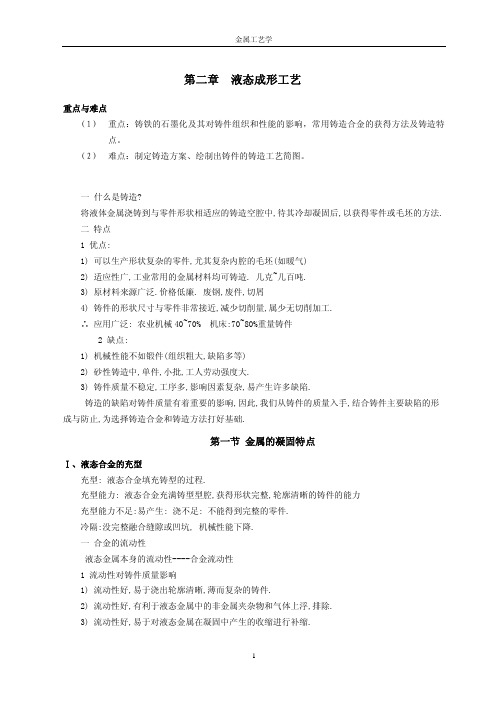
金属工艺学第二章 液态成形工艺重点与难点(1)重点:铸铁的石墨化及其对铸件组织和性能的影响,常用铸造合金的获得方法及铸造特点。
(2)难点:制定铸造方案、绘制出铸件的铸造工艺简图。
一 什么是铸造?将液体金属浇铸到与零件形状相适应的铸造空腔中,待其冷却凝固后,以获得零件或毛坯的方法.二 特点1 优点:1) 可以生产形状复杂的零件,尤其复杂内腔的毛坯(如暖气)2) 适应性广,工业常用的金属材料均可铸造. 几克~几百吨.3) 原材料来源广泛.价格低廉. 废钢,废件,切屑4) 铸件的形状尺寸与零件非常接近,减少切削量,属少无切削加工.∴ 应用广泛: 农业机械40~70% 机床:70~80%重量铸件2 缺点:1) 机械性能不如锻件(组织粗大,缺陷多等)2) 砂性铸造中,单件,小批,工人劳动强度大.3) 铸件质量不稳定,工序多,影响因素复杂,易产生许多缺陷.铸造的缺陷对铸件质量有着重要的影响,因此,我们从铸件的质量入手,结合铸件主要缺陷的形成与防止,为选择铸造合金和铸造方法打好基础.第一节 金属的凝固特点Ⅰ、液态合金的充型充型: 液态合金填充铸型的过程.充型能力: 液态合金充满铸型型腔,获得形状完整,轮廓清晰的铸件的能力充型能力不足:易产生: 浇不足: 不能得到完整的零件.冷隔:没完整融合缝隙或凹坑, 机械性能下降.一 合金的流动性液态金属本身的流动性----合金流动性1 流动性对铸件质量影响1) 流动性好,易于浇出轮廓清晰,薄而复杂的铸件.2) 流动性好,有利于液态金属中的非金属夹杂物和气体上浮,排除.3) 流动性好,易于对液态金属在凝固中产生的收缩进行补缩.12 测定流动性的方法:以螺旋形试件的长度来测定: 如 灰口铁:浇铸温度1300℃ 试件长1800mm.铸钢: 1600℃ 100mm3 影响流动性的因素主要是化学成分:1) 纯金属流动性好:一定温度下结晶,凝固层表面平滑,对液流阻力小2) 共晶成分流动性好:恒温凝固,固体层表面光滑,且熔点低,过热度大.3) 非共晶成分流动性差: 结晶在一定温度范围内进行,初生数枝状晶阻碍液流二 浇注条件1 浇注温度: t↑ 合金粘度下降,过热度高. 合金在铸件中保持流动的时间长,∴ t↑ 提高充型能力. 但过高,易产生缩孔,粘砂,气孔等,故不宜过高2 充型压力: 液态合金在流动方向上所受的压力↑ 充型能力↑如 砂形铸造---直浇道,静压力. 压力铸造,离心铸造等充型压力高.三 铸型条件1 铸型结构: 若不合理,如壁厚小, 直浇口低, 浇口小等 充↓2 铸型导热能力: 导热↑ 金属降温快,充↓ 如金属型3 铸型温度: t↑ 充↑ 如金属型预热4 铸型中气体: 排气能力↑ 充↑ 减少气体来源,提高透气性, 少量气体在铸型与金属液之间形成一层气膜,减少流动阻力,有利于充型.Ⅱ、铸件的凝固和收缩一 铸件的凝固1 凝固方式:铸件凝固过程中,其断面上一般分为三个区: 1—固相区 2—凝固区 3—液相区 对凝固区影响较大的是凝固区的宽窄,依此划分凝固方式.1) 逐层凝固:纯金属,共晶成分合金在凝固过程中没有凝固区,断面液,固两相由一条界限清楚分开,随温度下降,固相层不断增加,液相层不断减少,直达中心.2) 糊状凝固合金结晶温度范围很宽,在凝固某段时间内,铸件表面不存在固体层,凝固区贯穿整个断面,先糊状,后固化.故---3) 中间凝固大多数合金的凝固介于逐层凝固和糊状凝固之间.2 影响铸件凝固方式的因素1) 合金的结晶温度范围范围小: 凝固区窄,愈倾向于逐层凝固如: 砂型铸造, 低碳钢 逐层凝固, 高碳钢 糊状凝固金属工艺学2) 铸件的温度梯度合金结晶温度范围一定时,凝固区宽度取决于铸件内外层的温度梯度.温度梯度愈小,凝固区愈宽.(内外温差大,冷却快,凝固区窄)二 合金的收缩液态合金从浇注温度至凝固冷却到室温的过程中,体积和尺寸减少的现象---.是铸件许多缺陷(缩孔,缩松,裂纹,变形,残余应力)产生的基本原因.1 收缩的几个阶段1) 液态收缩: 从金属液浇入铸型到开始凝固之前. 液态收缩减少的体积与浇注温度质开始凝固的温度的温差成正比.2) 凝固收缩: 从凝固开始到凝固完毕. 同一类合金,凝固温度范围大者,凝固体积收缩率大.如: 35钢,体积收缩率3.0%, 45钢 4.3%3) 固态收缩: 凝固以后到常温. 固态收缩影响铸件尺寸,故用线收缩表示.2 影响收缩的因素1) 化学成分: 铸铁中促进石墨形成的元素增加,收缩减少. 如: 灰口铁 C, Si↑,收↓,S↑ 收↑.因石墨比容大,体积膨胀,抵销部分凝固收缩.2) 浇注温度: 温度↑ 液态收缩↑3) 铸件结构与铸型条件铸件在铸型中收缩会受铸型和型芯的阻碍.实际收缩小于自由收缩.∴ 铸型要有好的退让性.3 缩孔形成在铸件最后凝固的地方出现一些空洞,集中—缩孔. 纯金属,共晶成分易产生缩孔*产生缩孔的基本原因: 铸件在凝固冷却期间,金属的液态及凝固受缩之和远远大于固态收缩.4 影响缩孔容积的因素(补充)1) 液态收缩,凝固收缩 ↑ 缩孔容积↑2) 凝固期间,固态收缩↑,缩孔容积↓3) 浇注速度↓ 缩孔容积↓4) 浇注速度↑ 液态收缩↑ 易产生缩孔5 缩松的形成由于铸件最后凝固区域的收缩未能得到补足,或者,因合金呈糊状凝固,被树枝状晶体分隔开的小液体区难以得到补缩所至.1) 宏观缩松肉眼可见,往往出现在缩孔附近,或铸件截面的中心.非共晶成分,结晶范围愈宽,愈易形成缩松.2) 微观缩松凝固过程中,晶粒之间形成微小孔洞---凝固区,先形成的枝晶把金属液分割成许多微小孤立部分,冷凝时收缩,形成晶间微小孔洞. 凝固区愈宽,愈易形成微观缩松,对铸件危害不大,故不列为缺陷,但对气密性,机械性能等要求较高的铸3件,则必须设法减少.(先凝固的收缩比后凝固的小,因后凝固的有液,凝,固三个收缩,先凝固的有凝,固二个收缩区----这也是形成微观缩松的基本原因.与缩孔形成基本原因类似)6 缩孔,缩松的防止办法基本原则: 制定合理工艺—补缩, 缩松转化成缩孔.顺序凝固: 冒口—补缩同时凝固: 冷铁—厚处. 减小热应力,但心部缩松,故用于收缩小的合金. 安置冒口,实行顺序凝固,可有效的防止缩孔,但冒口浪费金属,浪费工时,是铸件成本增加.而且,铸件内应力加大,易于产生变形和裂纹.∴主要用于凝固收缩大,结晶间隔小的合金. 非共晶成分合金,先结晶树枝晶,阻碍金属流动,冒口作用甚小. 对于结晶温度范围甚宽的合金,由于倾向于糊状凝固,结晶开始之后,发达的树枝状骨状布满整个截面,使冒口补缩道路受阻,因而难避免显微缩松的产生.显然,选用近共晶成分和结晶范围较窄的合金生产铸件是适宜的.铸造内应力,变形和裂纹凝固之后的继续冷却过程中,其固态收缩若受到阻碍,铸件内部就发生内应力,内应力是铸件产生变形和裂纹的基本原因.(有时相变膨胀受阻,负收缩)一 内应力形成1 热应力: 铸件厚度不均,冷速不同,收缩不一致产生.塑性状态: 金属在高于再结晶温度以上的固态冷却阶段,受力变形,产生加工硬化,同时发生的再结晶降硬化抵消,内应力自行消失.(简单说,处于屈服状态,受力—变形无应力)弹性状态: 低于再结晶温度,外力作用下,金属发生弹性变形,变形后应力继续存在.举例: a) 凝固开始,粗 细处都为塑性状态,无内应力∵两杆冷速不同,细杆快,收缩大,∵受粗杆限制,不能自由收缩,相对被拉长,粗杆相对被压缩,结果两杆等量收缩.b) 细杆冷速大,先进如弹性阶段,而粗杆仍为塑性阶段,随细杆收缩发生塑性收缩,无应力.c) 细杆收缩先停止,粗杆继续收缩,压迫细杆,而细杆又阻止粗杆的收缩,至室温, 粗杆受拉应力(+),(-)由此可见,各部分的温差越大,热应力也越大,冷却较慢的部分形成拉应力,冷却较快的部分形成压应力.预防方法: 1 壁厚均匀 2 同时凝固—薄处设浇口,厚处放冷铁优点: 省冒口,省工,省料缺点: 心部易出现缩孔或缩松,应用于灰铁锡青铜,因灰铁缩孔、缩松倾向小,锡青铜糊状凝固,用顺序凝固也难以有效地消除其显微缩松。
金属材料成型基础之金属液态成型(ppt 101页)_5572

§1-2 液态金属的凝固与收缩
一、铸件的凝固方式
温度 温度
1. 逐层凝固 2. 糊状凝固 3. 中间凝固
a bc
液相线
S
液相线 固相线
影响铸件凝固方 成分 式的主要因素 :
固
表层
液
中心
(1)合金的结晶温度范围
固
表层
液
中心 表层 中心
凝固区
合金的结晶温度范围愈小,凝固区域愈窄, 愈倾向于逐层凝固 。
浇口杯
出气口
流动性(cm)
温度(℃)
30 0 20 0 10 00
80
60
40
20
0
Pb
20
40
60
80 Sb
合金流动性主要取决于合金化学成分所决定的结晶特点
温度(℃)
流动性(cm)
300 200 100
0 80 60 40 20 0
Pb 20 40 60 80 Sb
a)在恒温下凝固 b)在一定温度范围内凝固
上型
合金的线收缩受到铸型、 型芯、浇冒系统的机械阻 碍而形成的内应力。
机械应力是暂时应力。
下型
2.热应力
热应力是由于铸件壁厚不均匀,各部分冷却速度不同, 以致在同一时期内铸件各部分收缩不一致而引起的应力。
T
1
TH
1
Hale Waihona Puke 2塑性状态++-
t0~t1: t1~t2: t2~t3:
11
T临
22
2
T室
弹性状态
t
二、浇注条件
(1)浇注温度 一般T浇越高,液态金属的充型能力越强。 (2)充型压力 液态金属在流动方向上所受的压力越大,
液态成形概述
注意2个过程: (1)充填型腔; (2)凝固冷却
金属液态成型
定义:所谓金属液态成型,即铸造,casting, 是将金属加热到液态,使其具有流动性,然后 浇入到具有一定形状的型腔的铸型中,液态金 属在重力场或外力场的作用下充满型腔,冷却 并凝固成具有型腔形状的铸件。
实质:液态金属(或合金)充填铸型型腔并在其中
复合材料制备)
现代铸造
我国已成功地生产出了世界上最大的轧
钢机机架铸钢件(重410t)和长江三峡 电站巨型水轮机的特大型铸件
感受铸造
砂型sand mould铸造工艺流程图
型砂molding sand配制造型砂型干燥 工装准备炉料准备合金冶炼 芯砂core sand配制造芯core making型芯干燥
青铜文化
司母辛觥
豕尊
春秋晚期越国青铜兵器 出土于湖北江陵楚墓
长55.7厘米
剑锷锋芒犀利
锋能割断头发
湖北江陵楚墓出土越王勾践宝剑
三星堆
立人像铸于商代晚期,人像
高172厘米,底座高90厘米, 通高262厘米,是世界上最 大的青铜立人像,被尊称为 “世界铜像之王”。
突目面具铸于商代晚期,原
件高64.5厘米,宽138厘米, 眼球柱状外突长达13.5厘米, 其造型在世界上亦属首见。
第一篇 液态成形原理
第一章 概述
第二章 液态金属的结构与性质 第三章 液态成形过程的传热
第章 液态金属的结晶
第五章 铸件凝固组织的形成及控制
第六章 铸件中缺陷及其控制
第一章
液态材料 浇注 铸型模腔
概述
凝固 固态毛坯
金属的铸造工艺
陶瓷的注浆成形
塑料的注射成形
材料成形工艺原理第二章液态金属的结构和性质
在碰撞时,有的原子将一部分能量传给别 的原子,而本身的能量降低了。
结果是每时每刻都有一些原子的能量超过 原子的平均能量,有些原子的能量则远小于 平均能量。这种能量的不均匀性称为“能量 起伏”。
由于能量起伏,一些原子则可能越过势垒跑到原 子之间的间隙中或金属表面,而失去大量能量,在 新的位置上作微小振动(图1-3)。一旦有机会获得 能量,又可以跑到新的位置上。
接近熔点时,晶界上的原子则可能脱离原晶粒表 面,向邻近晶粒跳跃,晶粒逐渐失去固定形状。
特征:
将金属加热至熔点时,金属体积突然膨胀3~5%, 等于固态金属从热力学温度零度加热到熔点前的总 膨胀量。
金属的其它性质如电阻、粘性等发生突变,吸收 大量热能——熔化潜热,而金属的温度不升高。
这些突变现象是不能仅仅用离位原子和空穴数目 的增加加以解释的。因为空穴数目的增加不可能是 突变的。
(5) 如前所述,由于势能曲线是极不对称的,向左振动 时,动能很快就全部转化为势能,原子所能达到的最大 偏离位置较小。
向右振动,则需较大的偏离,动能才全部转化为势 能,振幅的中心位置则由Ro→R1 …。但是,这种膨胀 只改变原子的间距,并不改变原子排列的相对位置。
(6) 晶体中每个原子的振动能量不是均等的, 振动方向杂乱无章。
或
当R=R0 时,F (R0)=0,即
对应于能量的极小值,状态 稳定。原子之间倾向于保持一定 的间距,这就是在一定条件下, 金属中的原子具有一定排列的原 因。
当R=R1时,吸引力最大,即
对应能量曲线的拐点。 当R>R1时,吸引力开始减小, 势能向最大值转折。
二、金属的加热膨胀
晶体中原子并不是固定不动的,只要温度高于热力学 温度0K,每个原子皆在平衡位置附近振动,即所谓热振 动。温度升高时振动能量增加,振动频率和振幅加大。
液态成型工艺(
震击噪音小,劳动条件好。
生产率高(120箱/h),铸件质量好。 机器使用可靠,维修方便,价格低。
微震压实原理图
第四节
一、高压造型概述
水平分型高压造型
高压造型优缺点 优点:铸件质量高。 由于铸件质量高,可减少机加工余量,成本低。 降低劳动强度,改善劳动条件,提高生产率。 适应性强,能制造复杂、较大的铸件。 二、水平分型高压造型工艺过程 1、水平分型有箱高压造型 2、水平分型脱箱高压造型
四、冷冻造型
又称低温硬化造型法。其过程是采用普通石英砂作为骨架材料,加入少 量水,必要时加少量粘土,按普通造型方法制好铸型后送入冷冻室中, 用液态氮或二氧化碳作为制冷剂,使铸型冷冻,借助于包覆在砂粒表面 的冷冻水分而实现砂粒的结合,使铸型具有很高的强度及硬度。浇注时, 铸型温度升高,水分蒸发,铸型逐步解冻,稍加振动立即溃散,可方便 地取出铸件。 与其他造型方法相比,冷冻造型法具有以下特点: (1) 型砂中除少量的水及粘土外,无其他辅助材料,铸件的清理落砂方 便,设备简单; (2) 粉尘及有害气体少,环境污染小; (3) 铸型强度高、硬度大、透气性好,铸件表面粗糙度低、缺陷少。采 用这种造型方法生产球墨铸铁件可实现无冒口铸造,不会产生白口组织。
2、机器造型的特点
要使用模板 使用标准或专用砂箱
尽量采用单一砂
砂型只能有一个分型面 一般为流水线生产,浇注速度快,对浇注系统要求高
3、机器造型方法分类
砂型表面单位面积所受的压力称为压实比压。 根据比压大小可分为: 高压造型-----比压≥0.689MPa 中压造型-----比压在0.4~0.7MPa 低压造型-----比压在0.13~0.4MPa
5、出气孔与排气槽
四、垂直分型无箱高造型
第二章 液态成型
2.1.1 液态金属的充型能力
(1) 液态合金的充型能力与流动性
液态金属充型一般是纯液态下充满或边充 型边结晶 充型能力:液态合金充满铸型型腔,获得形状 完整,轮廓清晰铸件的能力。
衡量充型能力可用所能形成的铸件最小壁厚
不同金属和铸造方法铸造的铸件最小壁厚/mm
砂型 灰铸铁 铸钢 铝合金
3
金属型
>4
熔模
0.4~0.8
壳型
0.8~1.5
压铸
——
4
8~10
0.5~1
2.5
——
3
3~4
——
——
0.6~0.8
充型能力的好与差, 首先取决于铸 造合金的流动性;同时又受到外界条件, 如铸型性质、浇注条件、铸件结构等因 素的影响,是各种因素的综合反映。
流动性:液态铸造合金本身的流动
能力。 衡量流动性一般采用螺旋试样 长度
合金成分对流动行的影响
金属在结晶状态下流动
Fe-C合金流动性与状态图的关系
总的来说,流动性好的合金在多数 情况下其充型能力都较强;流动性差的 合金其充型能力较差。 但也可以通过改善其它条件来提高 充型能力(如提高熔炼质量、浇注温度 和浇注速度,改善铸型条件及铸件结构 等),以获得健全铸件。
(2) 影响合金充型能力的主要因素
铸造应力是热应力、相变应力和收缩应力 三者的矢量和。 在不同情况下,三种应力有时相互抵消, 时相互叠加;有时是临时的,有时是剩余的。 但在实际生产中,对于不同形状的铸件,其铸 造应力的大小分布是十分复杂的。
铸件中各种应力与产生部位的关 系
铸造应力对厚薄不均、截面不对称,细长杆、板及 轮类结构,当残余应力 >屈服强度,产生翘曲变 形。
- 1、下载文档前请自行甄别文档内容的完整性,平台不提供额外的编辑、内容补充、找答案等附加服务。
- 2、"仅部分预览"的文档,不可在线预览部分如存在完整性等问题,可反馈申请退款(可完整预览的文档不适用该条件!)。
- 3、如文档侵犯您的权益,请联系客服反馈,我们会尽快为您处理(人工客服工作时间:9:00-18:30)。
Pb 20 40 60 80 Sb
a)在恒温下凝固 b)在一定温度范围内凝固
合金的物理性能对流动性的影响
合金的热导率(λ),比热容(C)和密度(ρ): C、ρ较大, λ较小的合金,因其本身含有较多的热量,而热
量的散失又较慢,因此,流动性好;反之,流动性较差。
合金的表面张力: 在相同条件下,一般合金表面张力大的,流动性较差;反之,
但是,随着浇注温度的提高,合金的吸气、氧化现象严重,总 收缩量增加,反而易产生气孔、缩孔等缺陷,而且铸件结晶组 织粗大。
原则:
在保证足够流动性的前提下,应尽可能降低浇注温度。
2) 充型压头
压头(压力头): 指直接施加在液态金属表面的静压力,用液柱高度值表示
液态合金在流动方向上所受的压力越大,充型能力越好。
第2章 液态金属成型
2.1 概述 2.2 铸造成型基本理论 2.3 砂型铸造 2.4 特种铸造 2.5 现代铸造方法的发展
2.1 概述
2.1.1 液态成形的基本概念 2.1.2 铸造生产的特点 2.1.3 铸造方法
2.1.1 液态成形的基本概念
液态成形(铸造):
是熔炼金属,制造铸型,并 将熔融金属浇入到铸型的 型腔中,凝固后获得毛坯 或铸件的一种工艺方法。
合金获得优质铸件的能力,即在铸造生产中表现 出来的工艺性能。
• 合金铸造Biblioteka 能:包括液态合金的充型能力、收缩性、偏析倾 向性、氧化性和吸气性等。
2.2.1 合金的充型能力
1 基本概念 2 影响充型能力的因素及工艺措施
1 基本概念
合金的充型能力:
液态合金充满铸型型腔,获得形状完整、 轮廓清晰的健全铸件的能力。
2.1.2 铸造生产的特点
缺点: 1) 零件的力学性能较差 2) 质量稳定性较差 3) 劳动强度较大
2.1.3 铸造方法
根据造型材料可将铸造分为两大类: 1 砂型铸造 2 特种铸造
1 砂型铸造
铸型是以型砂(或芯砂)作为造型材料 特点:
生产成本低、适应性强 占铸造总产量的80%以上
2 特种铸造
除砂型铸造以外的所有其它铸造方法。
方法:
熔模铸造、金属型铸造、压力铸造、离心 铸造
它们在模样材料、造型材料、造型方法、 浇注方法等与砂型铸造有较大区别。
2.2 铸造成型基本理论
• 在液态合金成型过程中,合金铸造性能的优劣对 能否获得优质铸件有着重要影响。
• 合金铸造性能是指在一定铸造工艺条件下某种
B 铸造合金流动性的测试
浇口杯
出气口
0.45%C 铸钢:200 4.3%C 铸铁:1800
C 影响铸造合金流动性的因素
• 合金的成分及结晶特点 • 合金的物理性能
合金的成分及结晶特点对流动性的影响
合金流动性主要取决于合金化学成分所决定的结晶特点
温度(℃)
流动性(cm)
300 200 100
溅,使金属氧化和产生“铁豆”缺陷,而且型腔中气体来不 及排出,使反压力增加,以致造成浇不足或冷隔缺陷。
3) 浇注系统的结构
浇注系统的结构越复杂,液 态金属的流动阻力越大,其 充型能力有所下降。
在设计浇注系统时,必须合 理地布置内浇道在铸件上的 位置,选择恰当的浇注系统 结构及各组元(直浇道、横 浇道和内浇道)的尺寸。
2.1.1 液态成形的基本概念
2.1.2 铸造生产的特点
优点: 1) 适用范围广
常用金属材料均可在液态下成形; 铸件的大小、形状几乎不受限制。 2) 尺寸精度高 比锻件、焊接件尺寸精确,加工余量小,节约加工 工时和材料 3) 成本低廉 可大量利用废、旧金属料;与锻件相比,动力消耗 少;尺寸精度高;易批量生产
在砂型铸造中,常采用增大直浇口的高度提高液态合金的静 压力。 在压力铸造和低压铸造等特种铸造中,常采用人工加压的方 法提高液态合金的充型能力。
3)充型压头
压头(压力头): 指直接施加在液态金属表面的静压力,用液柱高度值表示
液态合金在流动方向上所受的压力越大,充型能力越好。
但是: 金属液的静压头过大或充型速度过高时,会使金属液飞
充型能力不足时,铸件易形成冷隔、浇不 足等缺陷。
2 影响充型能力的因素及工艺措施
液态合金的充型能力: 首先取决于合金本身的流动性 同时受某些工艺因素的影响
2 影响充型能力的因素及工艺措施
(1) 铸造合金的流动性 (2) 铸型性质 (3) 浇注条件 (4) 铸件结构
(1) 铸造合金的流动性
• A 铸造合金流动性的概念 • B 铸造合金流动性的测试 • C 影响铸造合金流动性的因素
为提高型砂的透气性,在铸型上开设通气孔是十分必 要且经常应用的工艺措施。
(3) 浇注条件
1) 浇注温度 2) 充型压头 3) 浇注系统的结构
1) 浇注温度
浇注温度越高,使合金粘度下降,且保持流动的时间增长, 故充型能力增强;反之,充型能力下降。
对于薄壁铸件或流动性差的合金,利用提高浇注温度以改善 充型能力,在生产中采用也比较方便。
A 铸造合金流动性的概念
流动性:液态铸造合金本身的流动能力。
流动性好的铸造合金,充型能力强,浇注时能迅速充满铸型 型腔,易于获得形状完整、轮廓清晰的铸件;
流动性好的铸造合金,可使液态合金中的气体、夹杂物易于 浮出,减少铸件中气孔和夹杂物的存在;
流动性好的铸造合金,也可使铸件在凝固期间产生的缩孔和 因收缩受阻产生的裂纹得到充填和弥合。
金属型铸造比砂型铸造更容易产生浇不足、冷隔等缺 陷。
2)铸型的温度
预热铸型能减小金属与铸型的温差,从而提高 金属液的充型能力。
预热铸型是金属型铸造中必须采取的工艺措施 之一。
3)铸型中的气体
铸型具有一定的发气能力时,能在金属液与铸型之间 形成气膜,可减少流动的摩擦阻力,有利于充型。
但是铸型的发气性过大时,在金属液的热作用下可产 生大量气体,如果铸型的排气能力小或浇注速度过快,型 腔中的气体压力增大,则阻碍金属液流动。
则流动性较好。
液态合金的粘度: 一般粘度越大,流动性就越差,而粘度越小流动性就越好。
(2) 铸型性质
1) 铸型的蓄热系数 2) 铸型的温度 3) 铸型中的气体
1)铸型的蓄热系数
铸型的蓄热系数表示铸型从其中的金属吸取热量并将 所吸取的热量储存在本身中的能力。
蓄热系数越大,铸型的激冷能力就越强,金属液于其 中保持液态的时间就越短,充型能力下降。