实验一半导体材料的缺陷显示及观察
半导体材料的缺陷特性研究

半导体材料的缺陷特性研究半导体材料,这玩意儿听起来是不是感觉挺高大上的?其实啊,它就在咱们身边,像手机、电脑,里面都有它的身影。
咱们今天就来好好聊聊半导体材料的缺陷特性。
先来说说什么是半导体材料的缺陷吧。
就好比一个班级,每个同学都应该好好坐在自己的座位上学习,可总有那么几个调皮捣蛋的,不好好待着,这就相当于半导体材料中的缺陷。
比如说,有点半导体材料里会有杂质原子混进去,这就像是班级里突然来了个转学生,还不太适应新环境,影响了整个班级的秩序。
还有一种情况叫空位缺陷,这就好比本来应该坐人的座位空着了,没人在那发挥作用。
我之前在实验室里就碰到过这么一档子事儿。
当时我们在研究一种新型的半导体材料,一切准备工作都做得妥妥的。
可等测试的时候,数据就是不对劲。
大家都急得像热锅上的蚂蚁,不知道问题出在哪儿。
后来经过反复排查,发现是材料里有一小部分出现了杂质缺陷,就因为这一点点小问题,整个实验都得重新来过。
再说说线缺陷,这就像是在操场上跑步,本来应该是直直的跑道,结果有一段凹下去了,那跑起来能顺溜吗?半导体材料里要是有了线缺陷,那电流传输也会受到影响。
半导体材料的缺陷还会影响它的电学性能。
比如说,有缺陷的地方电阻可能就会变大,电流就不容易通过,这就像路上有个大石头挡着,车开过去就得费更多的劲。
而且啊,半导体材料的缺陷对光学性能也有影响。
就好像一块原本透明的玻璃,因为有了瑕疵,光线透过的时候就会发生折射或者散射,不再那么清晰明亮。
在实际应用中,我们得想办法控制这些缺陷。
一方面,要尽量减少缺陷的产生,从原材料的选择到加工工艺,都得严格把关。
另一方面,有时候我们还会故意引入一些特定的缺陷,来实现我们想要的性能。
这就好比在一个团队里,合理安排每个人的角色,让大家都能发挥出最大的作用。
总之,半导体材料的缺陷特性可不是个小问题,我们得认真对待,才能让半导体材料更好地为我们服务。
就像我们在生活中,要及时发现自己的“缺陷”,努力改正或者利用它们,让自己变得更优秀!。
实验一半导体材料的缺陷显示及观察

实验一半导体材料的缺陷显示及观察实验目的1.掌握半导体的缺陷显示技术、金相观察技术;2.了解缺陷显示原理,位错的各晶面上的腐蚀图象的几何特性;3.了解层错和位错的测试方法。
一、实验原理半导体晶体在其生长过程或器件制作过程中都会产生许多晶体结构缺陷,缺陷的存在直接影响着晶体的物理性质及电学性能,晶体缺陷的研究在半导体技术上有着重要的意义。
半导体晶体的缺陷可以分为宏观缺陷和微观缺陷,微观缺陷又分点缺陷、线缺陷和面缺陷。
位错是半导体中的主要缺陷,属于线缺陷;层错是面缺陷。
在晶体中,由于部分原子滑移的结果造成晶格排列的“错乱”,因而产生位错。
所谓“位错线”,就是晶体中的滑移区与未滑移区的交界线,但并不是几何学上定义的线,而近乎是有一定宽度的“管道”。
位错线只能终止在晶体表面或晶粒间界上,不能终止在晶粒内部。
位错的存在意味着晶体的晶格受到破坏,晶体中原子的排列在位错处已失去原有的周期性,其平均能量比其它区域的原子能量大,原子不再是稳定的,所以在位错线附近不仅是高应力区,同时也是杂质的富集区。
因而,位错区就较晶格完整区对化学腐蚀剂的作用灵敏些,也就是说位错区的腐蚀速度大于非位错区的腐蚀速度,这样我们就可以通过腐蚀坑的图象来显示位错。
位错的显示一般都是利用校验过的化学显示腐蚀剂来完成。
腐蚀剂按其用途来分,可分为化学抛光剂与缺陷显示剂,缺陷显示剂就其腐蚀出图样的特点又可分为择优的和非择优的。
位错腐蚀坑的形状与腐蚀表面的晶向有关,与腐蚀剂的成分,腐蚀条件有关,与样品的性质也有关,影响腐蚀的因素相当繁杂,需要实践和熟悉的过程,以硅为例,表1列出硅中位错在各种界面上的腐蚀图象。
二、位错蚀坑的形状当腐蚀条件为铬酸腐蚀剂时,<100>晶面上呈正方形蚀坑,<110>晶面上呈菱形或矩形蚀坑,<111>晶面上呈正三角形蚀坑。
(见图1)。
表1-1 硅中位错在各种晶面上的腐蚀图象为获得较完整晶体和满足半导体器件的某些要求,通常硅单晶都选择<111>方向为生长方向,硅的四个<111>晶面围成一正四面体,当在金相显微镜下观察<111>晶面的位错蚀坑形态时,皆呈黑褐色有立体感而规则。
半导体碳化硅外延层中的缺陷及检测技术详解
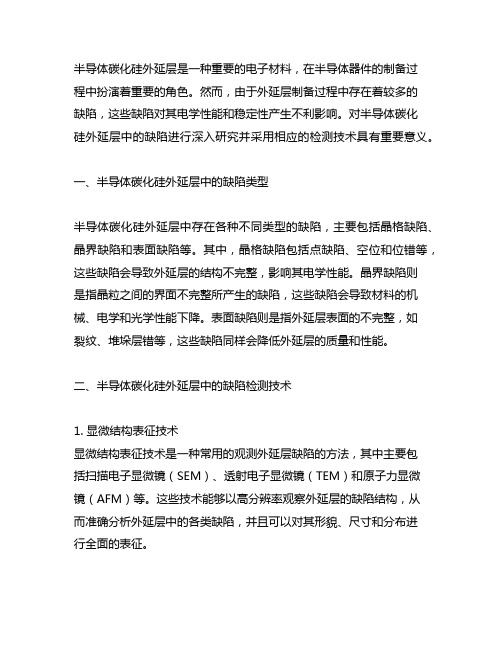
半导体碳化硅外延层是一种重要的电子材料,在半导体器件的制备过程中扮演着重要的角色。
然而,由于外延层制备过程中存在着较多的缺陷,这些缺陷对其电学性能和稳定性产生不利影响。
对半导体碳化硅外延层中的缺陷进行深入研究并采用相应的检测技术具有重要意义。
一、半导体碳化硅外延层中的缺陷类型半导体碳化硅外延层中存在各种不同类型的缺陷,主要包括晶格缺陷、晶界缺陷和表面缺陷等。
其中,晶格缺陷包括点缺陷、空位和位错等,这些缺陷会导致外延层的结构不完整,影响其电学性能。
晶界缺陷则是指晶粒之间的界面不完整所产生的缺陷,这些缺陷会导致材料的机械、电学和光学性能下降。
表面缺陷则是指外延层表面的不完整,如裂纹、堆垛层错等,这些缺陷同样会降低外延层的质量和性能。
二、半导体碳化硅外延层中的缺陷检测技术1. 显微结构表征技术显微结构表征技术是一种常用的观测外延层缺陷的方法,其中主要包括扫描电子显微镜(SEM)、透射电子显微镜(TEM)和原子力显微镜(AFM)等。
这些技术能够以高分辨率观察外延层的缺陷结构,从而准确分析外延层中的各类缺陷,并且可以对其形貌、尺寸和分布进行全面的表征。
2. 光学特性表征技术半导体碳化硅外延层的缺陷对其光学性能有着重要的影响,因此利用光学特性表征技术对外延层中的缺陷进行检测具有重要意义。
这些技术主要包括拉曼光谱、荧光光谱和激光散射等。
利用这些技术可以非常精确地分析外延层材料的光学响应,进而发现其中的缺陷和不完整结构。
3. 电学性能表征技术半导体碳化硅外延层的缺陷会影响其电学性能,因此通过电学性能表征技术可以检测外延层中的缺陷。
这些技术主要包括电子束诱导电流(EBIC)、深能量电子捕捉谱(DLTS)和微观电磁声谱等。
这些技术能够量化外延层中的缺陷浓度和类型,并且可以准确地分析缺陷对外延层电学性能的影响。
4. X射线和能谱技术X射线和能谱技术是一种常用的物质表征技术,通过测量外延层材料的X射线衍射图谱和能谱图谱,可以准确地鉴定外延层中的各类缺陷。
半导体材料中的缺陷工程与性能改善
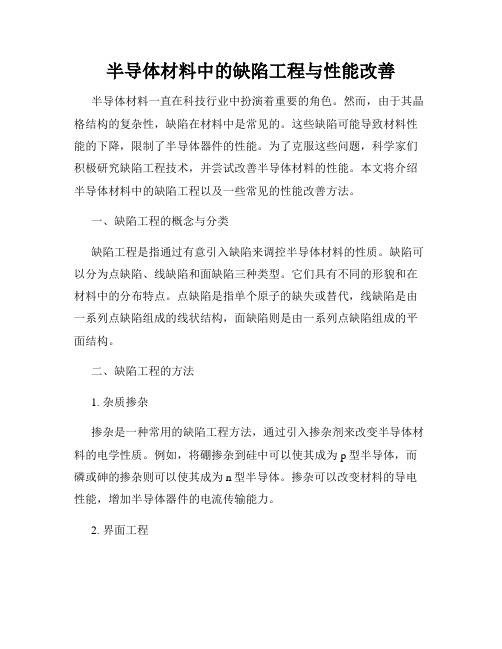
半导体材料中的缺陷工程与性能改善半导体材料一直在科技行业中扮演着重要的角色。
然而,由于其晶格结构的复杂性,缺陷在材料中是常见的。
这些缺陷可能导致材料性能的下降,限制了半导体器件的性能。
为了克服这些问题,科学家们积极研究缺陷工程技术,并尝试改善半导体材料的性能。
本文将介绍半导体材料中的缺陷工程以及一些常见的性能改善方法。
一、缺陷工程的概念与分类缺陷工程是指通过有意引入缺陷来调控半导体材料的性质。
缺陷可以分为点缺陷、线缺陷和面缺陷三种类型。
它们具有不同的形貌和在材料中的分布特点。
点缺陷是指单个原子的缺失或替代,线缺陷是由一系列点缺陷组成的线状结构,面缺陷则是由一系列点缺陷组成的平面结构。
二、缺陷工程的方法1. 杂质掺杂掺杂是一种常用的缺陷工程方法,通过引入掺杂剂来改变半导体材料的电学性质。
例如,将硼掺杂到硅中可以使其成为p型半导体,而磷或砷的掺杂则可以使其成为n型半导体。
掺杂可以改变材料的导电性能,增加半导体器件的电流传输能力。
2. 界面工程界面工程是指通过调控半导体材料的界面结构和特性来改善性能。
例如,在异质结构中,通过调整两种材料的界面匹配度,可以减少内部缺陷的产生,提高能带的连续性,从而提高材料的导电性能。
3. 外延生长外延生长是一种通过在已有晶体表面上延长新的晶体层来制备材料的方法。
这种方法可以控制材料的晶格缺陷,并使其在大面积上具有均匀的结构。
通过调控外延生长的条件和参数,可以减少缺陷的产生,提高材料的纯度。
三、性能改善方法1. 光电性能改善半导体材料的光电性能是其在光学和电子学领域中的重要性能。
为了改善材料的光电性能,可以通过改变材料的能带结构来实现。
例如,通过掺杂或量子点结构调控,可以提高材料对特定波段光的吸收能力,增强光电转换效率。
2. 热学性能改善半导体材料的热学性能对器件的工作稳定性和散热能力至关重要。
为了改善热学性能,可以通过调控材料的热导率和热膨胀系数来实现。
例如,通过合金化可以增加材料的热导率,提高其散热能力。
半导体缺陷测量

目镜的放大倍数M目为M目=A2B2/A1B1=250/F2
显微镜观察时总的放大倍数M为M =M物·M目=△/F1·250/F2
3.XJG-05型金相显微镜极其光学系统原理
位错腐坑在腐蚀过程中沿着位错线长度方向发展,腐蚀坑始终是尖底形的。显微镜明场观察时,真实的位错腐蚀坑是黑的,因为尖底蚀坑的微细台阶侧面不能将反射光反射回物镜中。
在高温下,位错在滑移中遇到障碍受阻时,后面接连而来的滑移位错也依次停下来,排成一排,出现位错排,高密度的位错排构成系属结构,它沿(110)晶向,大量的系属结构组成三角形或六角结构。
普通放大镜的放大倍数有限,不能用来观察微小的物体,因此需要用显微镜。最简单的显微镜可看作是由两片凸透镜组成的光学系统。如图五所示。靠近物体有透镜L1叫物镜,靠近眼睛的透镜叫目镜。被观察的物体AB放在物镜的焦点之外,通过物镜后可获得一个倒立的实像A1B1,它恰好位于目镜的焦点之内,目镜将此像再次放大,在明视距离S处成虚像A2B2,A2B2为眼睛这一光学系统的目标,在视网膜上成的像便是物体通过显微镜获得的最终图像,相对于物体是倒立的。
滑移时除了沿某一滑移面外,滑移方向也是一定的。滑移方向一般都是取原子距离最小的晶列方向,因为每移动一次必须移动一个院子距离或原子间距的整数倍。在原子距离小的晶列方向滑移,所需要的能量最小。所以这样的景象晶向是最容易滑移的方向。
(2)硅中位错线的特点及观察:
位错线一般开口在晶体表面上,在位错管道附近存在着应力场。原子排列受到破坏,内能较高,化学活性较强,往往比其他地方低,较易失去电子而导致优先腐蚀,且往往因有活性杂质聚集于管道周围,更加强了位错区的优先腐蚀。适当选择腐蚀剂就会在晶体表面位错露头处显出化学腐蚀凹坑。硅(111)面是双层原子,相邻双层的面间距最小,共价键面密度最大,腐蚀速度最慢。故在位错露头处出现的蚀坑一般以(111)面系为其侧面,{111}面系在硅中组成四面体,所以蚀坑应该是正四面体与所观察的晶面交线的图形。显然,(111)面蚀坑为三角形,(100)面为正方形,(110)面为菱形。如晶面偏离,则该面与正四面体的交线形状也会改变,蚀坑形状发生偏移。
半导体中杂质与缺陷表现
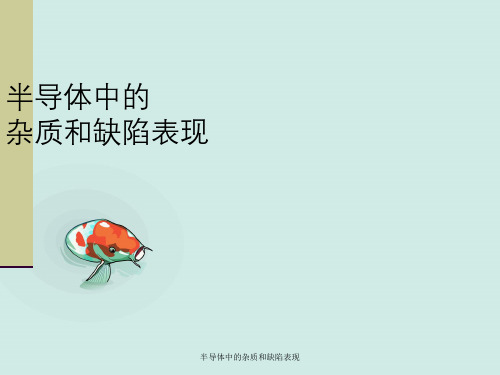
玻尔原子模型
玻尔原子电子的运动轨道半径为:
rH
oh2 mo q2
n2
n=1为基态电子的运动轨迹
玻尔能级:
En
moq4 8 o2h2n2
半导体中的杂质和缺陷表现
(2)受主电离能和受主能级
受主电离能△EA=空穴摆脱受主杂质束缚成为导电 空穴所需要的能量
受主能级EA:被受主杂质所束缚的空穴能量
Ec
EAEAEV
△EA
EA
Ev
半导体中的杂质和缺陷表现
受主杂质的电离能小,在 常温下基本上为价带电离 的电子所占据——空穴由 受主能级向价带激发。
Ec
+ ED
Ev
施主电离能
施主电离能△ED=弱束缚的电子摆脱杂质原子 束缚成为晶格中自由运动的 电子(导带中的电子)所需 要的能量
EC △ED =EC- ED ED
EV
半导体中的杂质和缺陷表现
施主杂质的电离能小, 在常温下基本上电离。
晶 体P
杂质 As Sb
Si 0.044 0.049 0.039
金刚石结构Si中,一 个晶胞内的原子占晶 体原胞的34%,空隙 占66%。
半导体中的杂质和缺陷表现
(1) 间隙式→杂质位于组成
半导体的元素或离子的格
点之间的间隙位置。
Li:0.068nm
(2) 替位式→杂质占据格点的 位置。大小接近、电子壳层
Si
Si
Si
Li
Si
P
Si
结构相近
Si:r=0.117nm
重点 掌握锗、硅晶体中的杂质能级, Ⅲ-Ⅴ 族化合物半导体的杂质能级。
施主/受主 施主杂质/受主杂质
浅能级杂质电离能的计算
半导体中的杂质和缺陷

不含任何杂质
实际应用中的
极其微量的杂质和缺陷, 能够对半导体材料的物理性质 和化学性质产生决定性的影响
在硅晶体中,若以105个硅原子中掺入一个杂质原子的比例掺入硼(B)原子,则硅晶体的导电率在室温下将增加103倍。 用于生产一般硅平面器件的硅单晶,位错密度要求控制在103cm-2以下,若位错密度过高,则不可能生产出性能良好的器件。(缺陷的一种)
添加标题
实验测得,Ⅴ族元素原子在硅、锗中的电离能很小,在硅中电离能约为0.04~0.05eV,在锗中电离能约为0.01eV,比硅、锗的禁带宽度小得多。
2.1.2 施主杂质、施主能级3
2.1.2 施主杂质、施主能级4
2.1.3 受主杂质、受主能级1
硅中掺入硼(B)为例,研究Ⅲ族元素杂质的作用。当一个硼原子占据了硅原子的位置,如图所示,硼原子有三个价电子,当它和周围的四个硅原子形成共价键时,还缺少一个电子,必须从别处的硅原子中夺取一个价电子,于是在硅晶体的共价键中产生了一个空穴。硼原子成为一个带有一个负电荷的硼离子(B-),称为负电中心硼离子。其效果相当于形成了一个负电中心和一个多余的空穴。
利用杂质补偿的作用,就可以根据需要用扩散或离子注入等方法来改变半导体中某一区域的导电类型,以制备各种器件。
若控制不当,会出现ND≈NA的现象,这时,施主电子刚好填充受主能级,虽然晶体中杂质可以很多,但不能向导带和价带提供电子和空穴,(杂质的高度补偿)。这种材料容易被误认为是高纯度的半导体,实际上却含有很多杂质,性能很差。
2.1.3 受主杂质、受主能级2
02
单击此处添加小标题
03
单击此处添加小标题
单击此处添加小标题
01
2.1.3 受主杂质、受主能级3
半导体材料中的缺陷与杂质控制技术

半导体材料中的缺陷与杂质控制技术半导体材料是现代电子器件制造中的关键材料之一。
为了保证半导体器件的性能和可靠性,需对半导体材料中的缺陷和杂质进行控制。
本文将重点讨论半导体材料中的缺陷与杂质控制技术。
一、半导体材料的缺陷类型半导体材料中常见的缺陷类型包括点缺陷、线缺陷和面缺陷。
点缺陷指的是材料中的单个原子或多个原子的缺失或占据,如空位和间隙原子;线缺陷是由材料中原子排列的缺陷引起的,如位错和脆性晶粒界;面缺陷则是材料表面或晶界处的缺陷,如二维氧化物缺陷和界面能带不平整。
二、缺陷对半导体性能的影响缺陷对半导体器件的性能和可靠性具有重要影响。
例如,点缺陷会降低半导体的载流子浓度,并影响电子迁移率和电阻;线缺陷会导致晶格畸变、局部应变和电子复合增加,降低载流子迁移率和器件寿命;面缺陷则会导致界面态和能带弯曲,进一步影响器件的电学性能。
三、缺陷与杂质控制技术为了控制半导体材料中的缺陷与杂质,需要实施一系列控制技术。
以下是几种常用的控制技术:1. 生长技术半导体晶体的生长是控制材料缺陷和杂质的重要方法。
例如,通过外延生长技术可以在晶体中控制点缺陷和线缺陷的形成;通过气相沉积技术可以控制杂质的浓度和分布。
2. 退火技术退火技术可以通过热处理来消除或减少材料中的缺陷和杂质。
例如,热退火可以使点缺陷移动和缩减;退火还可以使线缺陷部分消失或接近消失。
3. 加工工艺加工工艺可以通过控制材料的加工条件和方法来减少缺陷的形成。
例如,减小晶圆加工过程中的机械应力和温度梯度,可以减少缺陷的产生。
4. 杂质掺杂技术杂质掺杂技术可以通过控制材料中的杂质浓度和种类来改变材料的性能和控制缺陷。
例如,控制掺杂过程中的杂质浓度和扩散温度,可以有效控制杂质的分布和缺陷的形成。
5. 表面修饰技术表面修饰技术可以通过改变材料表面的能带结构来控制缺陷和杂质。
例如,通过表面处理或修饰来改变半导体材料的表面状态和化学反应性,可以减少表面缺陷和界面态的形成。
- 1、下载文档前请自行甄别文档内容的完整性,平台不提供额外的编辑、内容补充、找答案等附加服务。
- 2、"仅部分预览"的文档,不可在线预览部分如存在完整性等问题,可反馈申请退款(可完整预览的文档不适用该条件!)。
- 3、如文档侵犯您的权益,请联系客服反馈,我们会尽快为您处理(人工客服工作时间:9:00-18:30)。
实验一半导体材料的缺陷显示及观察实验目的1.掌握半导体的缺陷显示技术、金相观察技术;2.了解缺陷显示原理,位错的各晶面上的腐蚀图象的几何特性;3.了解层错和位错的测试方法。
一、实验原理半导体晶体在其生长过程或器件制作过程中都会产生许多晶体结构缺陷,缺陷的存在直接影响着晶体的物理性质及电学性能,晶体缺陷的研究在半导体技术上有着重要的意义。
半导体晶体的缺陷可以分为宏观缺陷和微观缺陷,微观缺陷又分点缺陷、线缺陷和面缺陷。
位错是半导体中的主要缺陷,属于线缺陷;层错是面缺陷。
在晶体中,由于部分原子滑移的结果造成晶格排列的“错乱”,因而产生位错。
所谓“位错线”,就是晶体中的滑移区与未滑移区的交界线,但并不是几何学上定义的线,而近乎是有一定宽度的“管道”。
位错线只能终止在晶体表面或晶粒间界上,不能终止在晶粒内部。
位错的存在意味着晶体的晶格受到破坏,晶体中原子的排列在位错处已失去原有的周期性,其平均能量比其它区域的原子能量大,原子不再是稳定的,所以在位错线附近不仅是高应力区,同时也是杂质的富集区。
因而,位错区就较晶格完整区对化学腐蚀剂的作用灵敏些,也就是说位错区的腐蚀速度大于非位错区的腐蚀速度,这样我们就可以通过腐蚀坑的图象来显示位错。
位错的显示一般都是利用校验过的化学显示腐蚀剂来完成。
腐蚀剂按其用途来分,可分为化学抛光剂与缺陷显示剂,缺陷显示剂就其腐蚀出图样的特点又可分为择优的和非择优的。
位错腐蚀坑的形状与腐蚀表面的晶向有关,与腐蚀剂的成分,腐蚀条件有关,与样品的性质也有关,影响腐蚀的因素相当繁杂,需要实践和熟悉的过程,以硅为例,表1列出硅中位错在各种界面上的腐蚀图象。
二、位错蚀坑的形状当腐蚀条件为铬酸腐蚀剂时,<100>晶面上呈正方形蚀坑,<110>晶面上呈菱形或矩形蚀坑,<111>晶面上呈正三角形蚀坑。
(见图1)。
表1-1 硅中位错在各种晶面上的腐蚀图象为获得较完整晶体和满足半导体器件的某些要求,通常硅单晶都选择<111>方向为生长方向,硅的四个<111>晶面围成一正四面体,当在金相显微镜下观察<111>晶面的位错蚀坑形态时,皆呈黑褐色有立体感而规则。
图1(a)是在朝籽晶方向的<111>晶面上获得的刃型位错蚀坑形状,呈金字塔顶式,即正四面体的顶视图形态。
(a)x400 (b) x270 (c) x270<111>晶面的位错蚀坑<100>晶面的位错蚀坑<110>晶面的位错蚀坑图1 硅中位错蚀坑的形状三、位错密度的测定位错的面密度——穿过单位截面积的位错线数;用S ρ表示S N S /=ρS 为单晶截面积;N 为穿过截面积S 的位错线数。
位错的面密度在金相显微镜下测定,金相显微镜是专门用来研究金属组织结构的光学显微镜。
金相技术在半导体材料和器件的生产工艺中有着极其广泛的应用;它直观、简单,是进行其它研究的基础也是研究晶体缺陷的有力工具。
用金相显微镜来测定位错的面密度,显微镜视场面积应计算得准确,否则将引起不允许的误差。
在实验中金相显微镜配以测微目镜,用刻度精确的石英测微尺来定标,测量视场面积。
视场面积的大小需根据晶体中位错密度的大小来决定,一般位错密度大时,放大倍数也应大些,即视场面积选小些,位错密度小时放大倍数则应小些。
我国国家标准(GB1554-79)中规定:位错密度在101个/cm 2以下者,采用1mm 2视场面积,位错密度104个cm 2以上者采用2 mm 2视场面积,并规定取距边缘2mm 2的区域以内的最大密度作为出厂依据,为了粗略反映位错的分布情况还应加测中心点。
四、层错的观察和测量在晶体密堆积结构中正常层序发生破坏的区域被称为堆积层错或堆垛层错,简称层错,层错属于面缺陷。
1、层错的形成图2画出了面心立方结构中原子分布的不同类型,AA 方向就是<111>晶向,外延层通常是沿此方向生长的。
从<111>方向看去,原子都分布在一系列相互平行的<111>面上。
把这些不同层的原子,分别标成A、B、C。
在晶体的其它部分的原子,都是按照ABCABC……这样的层序重复排列的,直到晶体表面。
如果把这些原子画成立体排列的形式(取<111>晶面向上),则每个原子都和它上面一层最近邻的三个原子组成一正四面体。
完整的晶体,可认为是这些正四面体在空间有规则重复的排列所构成的,如图3所示。
在实际的外延生长过程中,发现硅原子并不完全按照ABCABC……这样的层序排列,而可能出现缺陷,层错就是最常见的一种。
所谓层错,就是在晶体的生长过程中,某些地方的硅原子,按层排列的次序发生了混乱。
例如,相对于正常排列的层序ABCABC……,少了一层,成为ABCACABC……;或者多出一层,成为ABCACBC…….在晶体中某处发生错乱的排列后,随外延生长,逐渐传播开来,直到晶体的表面,成为区域性的缺陷。
在外延生长过程中,层错的形成和传播如图4所示。
假定衬底表面层的原子是按A型排列的,即按正常生长层序,外延生长的第一层应为B型排列。
但由于某种原因,使得表面的某一区域出现反常情况而成C型排列。
即按ABCACABC……(抽出B层)排列。
它向上发展,并逐层扩大,最终沿三个〈111〉面发育成为一倒立的四面体(见图5)。
这个四面体相当于前述的许多小正四面体堆积起来的。
由于此四面体是由错配的晶核发育而成的,因此,在它与正常生长的晶体的界面两侧,原子是失配的。
也就是说,晶格的完整性在这些界面附近受到破坏,但在层错的内部,晶格仍是完整的。
由错配的晶核为起源的层错,并不一定都能沿三个<111>面发展到表面,即在表面并不都呈三角形。
在外延生长过程中,形成层错的机理较复杂。
在某些情况下,层错周围的正常生长可能很快,抢先占据了上面的自由空间,因而使得层错不能充分发育。
这表现在层错的腐蚀图形不是完整的三角形,而可能是一条直线,或者为一角,如图6所示。
以上讨论的是沿<111>晶向生长的情况,发育完全的层错在<111>面上的边界是正三角形。
当沿其它晶向生长时,层错的边界线,便是生长面与层错四面体的交线。
在不同的生长面上,层错的边界形状也不相同。
在外延生长时,引起表面某一区域排列反常的原因,主要是由于衬底表面的结构缺陷;衬底面上的外来杂质;或生长过程中出现的晶体内部的局部应力等。
因此,层错一般起始于外延层和衬底的交界面,有时也发生在外延生长过程中。
2、利用层错三角形计算外延层的厚度利用化学腐蚀的方法可以显示缺陷图形,虽然有的层错是从外延层中间开始发生的,但多数从衬底与外延层界面上开始出现,因此缺陷图形与外延层厚度之间有一简单关系。
利用这种关系通过测定缺陷图形的几何尺寸,便可计算出外延层厚度。
不同晶向的衬底,沿倾斜的<111>面发展起来的层错终止在晶片表面的图形也各不相同。
表2列出了各种方向上生长外延层时缺陷图形各边长与外延层厚度之间的比例关系,依据比例关系可正确推算出外延层的厚度。
表2 不同晶向层错图形边长(1 、2 、3 )与外层厚度(t )的关系。
层错法测外延层厚度虽然比较简便,但也存在一些问题,应予以注意。
外延层层错有时不是起源于衬底片与外延层的交界面,这时缺陷的图形轮廓就不如从交界面上发生的层错图形大,在选定某一图形作测量之前,应在显微镜下扫描整个外延片面积,然后选定最大者进行测量。
五、实验设备和器材:(1)金相显微镜二台(其中一台配有电子目镜);(2)各种半导体晶体样品,盖玻片,镊子;(3)格值0.01mm石英标尺一片;(4)计算机一台。
六、实验步骤:1.把样品抛光的一面朝下放在显微镜上,用带电子目镜的显微镜观察硅[111]晶面刃型位错蚀坑图形(应为正三角形,有立体感),(操作方法见附2),保存图形文件,打印输出,附在实验报告中。
ρN/S,N为显2.取下电子目镜,换上普通目镜,测量位错密度=微镜视场内的位错蚀坑个数,S为视场面积,视场直径校正如下:目镜物镜视场直径10X 10X ф1.8mm10X 40X ф0.44mm3.在有电子目镜的显微镜上观察层错三角形:硅<111>晶面的层错蚀坑图形为正三角形,或不完整的正三角形(600夹角或一条直线),当层错重叠时会出现平行线。
层错三角形无立体感。
保存该图像文件,并打印输出,附在实验报告中。
4.利用层错三角形推算硅外延层厚度:硅[111]晶面层错三角形的边长L与硅外延层厚度t 有关系:t=0.816L。
为了用显微镜测量层错三角形的边长L,必须先用石英标尺对显微镜视场进行刻度校正,校正方法如下:将石英标尺有刻度的一面朝下放在显微镜上,调节显微镜使在视场中清晰的观察到石英标尺中心圆环内的刻度线,然后测量出两条刻度线之间的距离的读数值x(注意:显示屏上的读数并非实际尺寸),该读数对应的实际尺寸是0.01mm,记下这一校正比例关系。
在测量出层错三角形边长的读数值y后,利用校正比例关系求出层错三角形的边长L=0.01y/x。
附1:硅单晶[111]面的位错显示实验设备和器材:(1)4X型金相显微镜1台(2)MCV-15测微目镜一架(3)[111]面硅单晶片(4)300# 600# 302# 303#金刚砂(5)化学腐蚀间:设施:通风柜、冷热去离子水装置;(6)化学试剂:硝酸、氢氟酸、三氧化铬、酒精、丙酮、甲苯等;(7)器皿:量筒、烧杯、氟塑料杯、塑料腐槽、镊子等。
实验步骤:(1)样品准备:取[111]面硅片。
用300# 600# 302# 303#金刚砂依次细磨,去离子水冲洗煮沸清洗干净。
(2)抛光:打开通风柜,准备好所需化学试剂。
抛光液配比:HF(42%):HNO3(65%)=1:2.5。
配制好抛光液倒入氟塑料杯中,将清洗干净的硅片用镊子轻轻夹入抛光液中,密切注意表面变化,操作时注意样品应始终淹没在抛光液中,同时应当不停地搅拌以改进抛光均匀性,待硅片表面光亮如镜,则抛光毕,迅速将硅片夹入预先准备好的去离子水杯中,再用流动的去离子水冲洗,在抛光过程中,蚀速对温度异常敏感。
一般说来在温度18℃~25℃的范围,抛光时间约为1.5~4分钟。
(3)铬酸法显示位错a、配制铬酸标准,配比为:标准液=5克CrO3+100去离子水。
B、按需要配制下述比例腐蚀剂:1.标准液:HF(40%)=2:1 (慢蚀速)2.标准液:HF(40%)=3:2 (中蚀速)3.标准液:HF(40%)=1:1 (快蚀速)4.标准液:HF(40%)=1:2 (快蚀速)一般采用第三种配方,将抛光后的样品放入蚀槽,倒入腐蚀剂,蚀剂量的多少以样品不露出液面即可:一般情况在15℃~20℃的温度下腐蚀15~30分钟便可取出,用去离子水充分清洗并煮沸,用无水乙醇脱水,红外灯下烘干。