0324注塑-产品变形翘曲原因分析及管控
注塑常见缺陷的解决方法

注塑常见缺陷的解决方法注塑是一种常见的制造工艺,可以用于生产各种塑料制品。
然而,在注塑过程中常常会出现一些缺陷,如翘曲、气泡、短射等。
这些缺陷会降低产品的质量,影响使用效果。
因此,解决这些缺陷是注塑加工中重要的一环。
下面是一些常见缺陷的解决方法:1.翘曲:翘曲是指注塑制品的形状变形,不符合设计要求。
翘曲的原因可能是注塑温度过高、材料流动不均匀等。
解决方法包括:优化注塑工艺参数,例如调整注塑温度、压力、速度等;增加型腔冷却方式,以提高产品的冷却效果;使用合适的塑料料种,如改变注塑材料的配方,选择更具平衡性能的材料。
2.气泡:气泡是指注塑制品中出现的气体孔洞,影响了产品的外观和性能。
气泡的形成可能是由于注塑材料中的挥发性成分未完全排除、注塑机排气不良等原因。
解决方法包括:增加注塑所需的压力和温度,以促使挥发性成分完全排出;改善注塑机的排气系统,有效排除气泡。
3.短射:短射是指注塑过程中,塑料流动未能充满整个模具的情况。
短射的原因可能是注塑料温度过低、注塑机压力不足、型腔阻力过大等。
解决方法包括:提高注塑温度和压力,以增加塑料的流动性;改善模具的设计,减少型腔的阻力;检查注塑机的喷嘴和螺杆是否损坏,及时更换。
4.热流线:热流线是指注塑制品表面出现的不均匀纹路,影响产品的外观。
热流线的形成可能是由于塑料流动速度过快、模具温度不均匀等原因。
解决方法包括:调整注塑机的喷嘴和螺杆速度,控制塑料的流动速度;优化模具的冷却系统,使模具温度均匀分布。
5.尺寸偏差:尺寸偏差是指注塑制品的尺寸与设计要求不符,可能是由于模具磨损、注塑工艺参数不恰当等原因。
解决方法包括:定期检查和修复模具,以保证模具的精度;优化注塑工艺参数,例如调整注射时间、压力和温度,以控制产品的尺寸。
总的来说,解决注塑常见缺陷需要综合考虑材料、工艺和设备等方面的因素。
通过不断优化参数和改进工艺,可以改善产品的质量,提高注塑加工的效率。
此外,定期维护和保养注塑设备和模具也是预防和解决缺陷的重要措施。
注塑模具制品的翘曲、变形原因及解决方法

注塑模具制品的翘曲、变形原因及解决方法
注塑成型是批量生产某些形状复杂部件时用到的一种加工方法。
具体指将受热融化的材料由高压射入模腔,经冷却固化后,得到成形品。
出现的翘曲、变形问题主要应从注塑模具设计方面解决,而成型条件的调整效果则是很有限的。
东莞恒圣塑胶实业有限公司专业为您介绍以下是翘曲、变形的原因及解决方法:
一、由成型条件引起残余应力造成变形时,可通过降低注射压力、提高注塑模具温度,并使注塑模具温度均匀,及提高树脂温度或采用退火方法予以消除应力。
二、脱模不良引起应力变形时,可通过增加推杆数量或面积、设置脱模斜度等方法加以解决。
三、由于冷却方法不合适,使冷却不均匀或冷却时间不足时,可调整冷却方法及延长冷却时间等。
四、对于成型收缩所引起的变形,就必须修正注塑模具的设计。
最重要的是应注意使制品壁厚一致。
关键词:模具加工,大型模具加工,大型注塑产品,注塑机产品。
注塑缺陷原因分析与解决方案

注塑缺陷原因分析与解决方案一、缺陷原因分析在注塑过程中,可能会出现各种缺陷,如短射、气泡、翘曲、脱模等。
这些缺陷的产生原因可能涉及材料、模具、注塑机、工艺参数等多个方面。
下面将分析常见的注塑缺陷原因。
1.材料原因材料的质量和性能对注塑产品的质量起着决定性的影响。
常见的材料问题包括:(1)原料质量不合格:原料中可能含有杂质、水分过高等问题,导致注塑产品出现气泡、色差等缺陷。
(2)材料熔体流动性差:材料的熔体流动性差,容易导致短射、翘曲等缺陷。
2.模具原因模具的设计和制造质量对注塑产品的质量有着重要影响。
常见的模具问题包括:(1)模具设计不合理:模具的结构设计不合理,可能导致产品出现翘曲、脱模等缺陷。
(2)模具制造精度不高:模具的制造精度不高,可能导致产品尺寸不准确、表面粗糙等缺陷。
3.注塑机原因注塑机的性能和调试对注塑产品的质量也有着重要影响。
常见的注塑机问题包括:(1)注射压力不稳定:注射压力不稳定可能导致产品出现短射、气泡等缺陷。
(2)注射速度过快或过慢:注射速度过快或过慢都可能导致产品出现短射、翘曲等缺陷。
4.工艺参数原因工艺参数的设置对注塑产品的质量起着决定性的影响。
常见的工艺参数问题包括:(1)注射温度不合适:注射温度过高或过低都可能导致产品出现短射、变形等缺陷。
(2)冷却时间不足:冷却时间不足可能导致产品出现翘曲、脱模等缺陷。
二、缺陷解决方案针对不同的缺陷原因,可以采取相应的解决方案来改善注塑产品的质量。
1.材料问题解决方案(1)严格控制原料质量:选择合格的原料供应商,进行严格的原料检测,确保原料质量符合要求。
(2)合理调整材料熔体流动性:根据产品要求和注塑机性能,合理调整材料的熔体流动性,确保注塑过程顺利进行。
2.模具问题解决方案(1)优化模具设计:根据产品的结构和要求,进行模具设计优化,确保产品形状准确、结构合理。
(2)提高模具制造精度:采用高精度的数控机床和加工工艺,提高模具制造的精度,确保产品尺寸准确、表面光洁。
塑胶加工中翘曲变形的原因及解决办法

一. 翘曲变形是指注塑制品的形状偏离了模具型腔的形状,它是塑料制品常见的缺陷之一。
出现翘曲变形的原因很多,单靠工艺参数解决往往力不从心。
结合相关资料和实际工作经验,下面对影响注塑制品翘曲变形的因素作简要分析。
二、模具的结构对注塑制品翘曲变形的影响。
在模具方面,影响塑件变形的因素主要有浇注系统、冷却系统与顶出系统等。
1.浇注系统注塑模具浇口的位置、形式和浇口的数量将影响塑料在模具型腔内的填充状态,从而导致塑件产生变形。
流动距离越长,由冻结层与中心流动层之间流动和补缩引起的内应力越大;反之,流动距离越短,从浇口到制件流动末端的流动时间越短,充模时冻结层厚度减薄,内应力降低,翘曲变形也会因此大为减少。
一些平板形塑件,如果只使用一个中心浇口,因直径方向上的收缩率大于圆周方向上的收缩率,成型后的塑件会产生扭曲变形;若改用多个点浇口或薄膜型浇口,则可有效地防止翘曲变形。
当采用点浇口进行成型时,同样由于塑料收缩的异向性,浇口的位置、数量都对塑件的变形程度有很大的影响。
另外,多浇口的使用还能使塑料的流动比(L/t)缩短,从而使模腔内熔体密度更趋均匀,收缩更均匀。
同时,整个塑件能在较小的注塑压力下充满。
而较小的注射压力可减少塑料的分子取向倾向,降低其2.冷却系统在注射过程中,塑件冷却速度的不均匀也将形成塑件收缩的不均匀,这种收缩差别导致弯曲力矩的产生而使塑件发生翘曲。
如果在注射成型平板形塑件(如手机电池壳)时所用的模具型腔、型芯的温度相差过大,由于贴近冷模腔面的熔体很快冷却下来,而贴近热模腔面的料层则会继续收缩,收缩的不均匀将使塑件翘曲。
因此,注塑模的冷却应当注意型腔、型芯的温度趋于平衡,两者的温差不能太大(此时可考虑使用两个模温机). 除了考虑塑件内外表的温度趋于平衡外,还应考虑塑件各侧的温度一致,即模具冷却时要尽量保持型腔、型芯各处温度均匀一致,使塑件各处的冷却速度均衡,从而使各处的收缩更趋均匀,有效地防止变形的产生。
注塑成型零件翘曲变形的解决方法

注塑成型零件翘曲变形的解决方法下载提示:该文档是本店铺精心编制而成的,希望大家下载后,能够帮助大家解决实际问题。
文档下载后可定制修改,请根据实际需要进行调整和使用,谢谢!本店铺为大家提供各种类型的实用资料,如教育随笔、日记赏析、句子摘抄、古诗大全、经典美文、话题作文、工作总结、词语解析、文案摘录、其他资料等等,想了解不同资料格式和写法,敬请关注!Download tips: This document is carefully compiled by this editor. I hope that after you download it, it can help you solve practical problems. The document can be customized and modified after downloading, please adjust and use it according to actual needs, thank you! In addition, this shop provides you with various types of practical materials, such as educational essays, diary appreciation, sentence excerpts, ancient poems, classic articles, topic composition, work summary, word parsing, copy excerpts, other materials and so on, want to know different data formats and writing methods, please pay attention!引言注塑成型是一种广泛应用于工业生产的重要制造工艺,可生产出形状复杂、精度高的零件。
塑料制品的翘曲变形的原因分析和解决方法图文稿
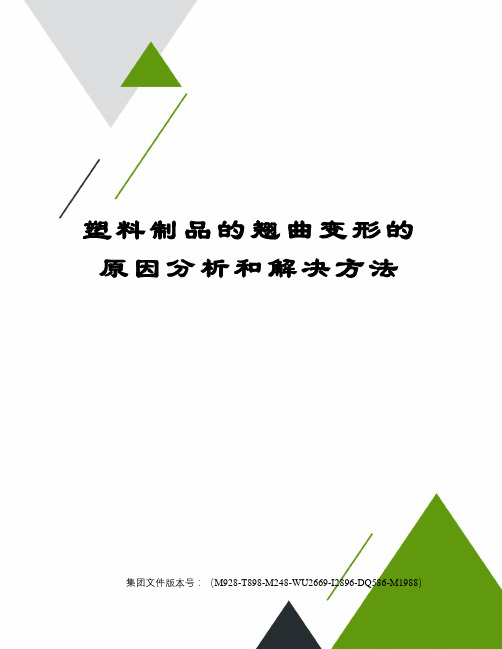
塑料制品的翘曲变形的原因分析和解决方法集团文件版本号:(M928-T898-M248-WU2669-I2896-DQ586-M1988)塑料制品的翘曲变形的原因分析和解决方法一、前言翘曲变形是指注塑制品的形状偏离了模具型腔的形状,它是塑料制品常见的缺陷之一。
出现翘曲变形的原因很多,单靠工艺参数解决往往力不从心。
结合相关资料和实际工作经验,下面对影响注塑制品翘曲变形的因素作简要分析。
二、模具的结构对注塑制品翘曲变形的影响。
在模具方面,影响塑件变形的因素主要有浇注系统、冷却系统与顶出系统等。
1.浇注系统注塑模具浇口的位置、形式和浇口的数量将影响塑料在模具型腔内的填充状态,从而导致塑件产生变形。
流动距离越长,由冻结层与中心流动层之间流动和补缩引起的内应力越大;反之,流动距离越短,从浇口到制件流动末端的流动时间越短,充模时冻结层厚度减薄,内应力降低,翘曲变形也会因此大为减少。
一些平板形塑件,如果只使用一个中心浇口,因直径方向上的收缩率大于圆周方向上的收缩率,成型后的塑件会产生扭曲变形;若改用多个点浇口或薄膜型浇口,则可有效地防止翘曲变形。
当采用点浇口进行成型时,同样由于塑料收缩的异向性,浇口的位置、数量都对塑件的变形程度有很大的影响。
另外,多浇口的使用还能使塑料的流动比(L/t)缩短,从而使模腔内熔体密度更趋均匀,收缩更均匀。
同时,整个塑件能在较小的注塑压力下充满。
而较小的注射压力可减少塑料的分子取向倾向,降低其内应力,因而可减少塑件的变形。
2. 冷却系统在注射过程中,塑件冷却速度的不均匀也将形成塑件收缩的不均匀,这种收缩差别导致弯曲力矩的产生而使塑件发生翘曲。
如果在注射成型平板形塑件(如手机电池壳)时所用的模具型腔、型芯的温度相差过大,由于贴近冷模腔面的熔体很快冷却下来,而贴近热模腔面的料层则会继续收缩,收缩的不均匀将使塑件翘曲。
因此,注塑模的冷却应当注意型腔、型芯的温度趋于平衡,两者的温差不能太大(此时可考虑使用两个模温机)。
翘曲变形原因
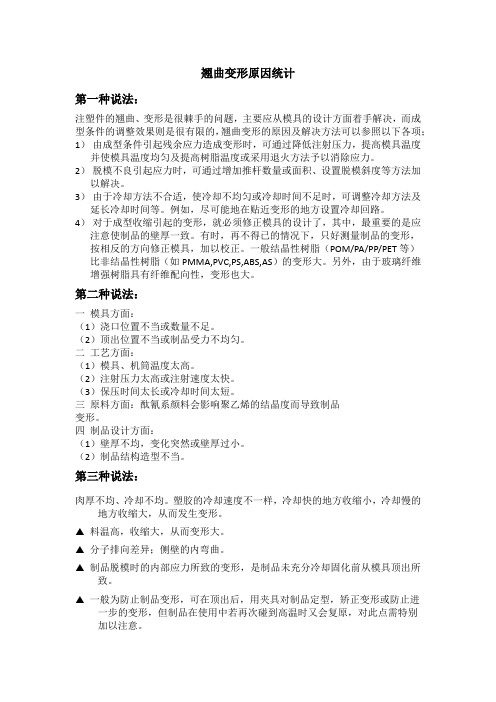
翘曲变形原因统计第一种说法:注塑件的翘曲、变形是很棘手的问题,主要应从模具的设计方面着手解决,而成型条件的调整效果则是很有限的,翘曲变形的原因及解决方法可以参照以下各项;1)由成型条件引起残余应力造成变形时,可通过降低注射压力,提高模具温度并使模具温度均匀及提高树脂温度或采用退火方法予以消除应力。
2)脱模不良引起应力时,可通过增加推杆数量或面积、设置脱模斜度等方法加以解决。
3)由于冷却方法不合适,使冷却不均匀或冷却时间不足时,可调整冷却方法及延长冷却时间等。
例如,尽可能地在贴近变形的地方设置冷却回路。
4)对于成型收缩引起的变形,就必须修正模具的设计了,其中,最重要的是应注意使制品的壁厚一致。
有时,再不得已的情况下,只好测量制品的变形,按相反的方向修正模具,加以校正。
一般结晶性树脂(POM/PA/PP/PET等)比非结晶性树脂(如PMMA,PVC,PS,ABS,AS)的变形大。
另外,由于玻璃纤维增强树脂具有纤维配向性,变形也大。
第二种说法:一模具方面:(1)浇口位置不当或数量不足。
(2)顶出位置不当或制品受力不均匀。
二工艺方面:(1)模具、机筒温度太高。
(2)注射压力太高或注射速度太快。
(3)保压时间太长或冷却时间太短。
三原料方面:酞氰系颜料会影响聚乙烯的结晶度而导致制品变形。
四制品设计方面:(1)壁厚不均,变化突然或壁厚过小。
(2)制品结构造型不当。
第三种说法:肉厚不均、冷却不均。
塑胶的冷却速度不一样,冷却快的地方收缩小,冷却慢的地方收缩大,从而发生变形。
☐料温高,收缩大,从而变形大。
☐分子排向差异;侧壁的内弯曲。
☐制品脱模时的内部应力所致的变形,是制品未充分冷却固化前从模具顶出所致。
☐一般为防止制品变形,可在顶出后,用夹具对制品定型,矫正变形或防止进一步的变形,但制品在使用中若再次碰到高温时又会复原,对此点需特别加以注意。
第四种说法:如果制件的收缩均匀,那么成型件不会发生变形或翘曲,只是单纯地变小了。
注塑件翘曲的原因
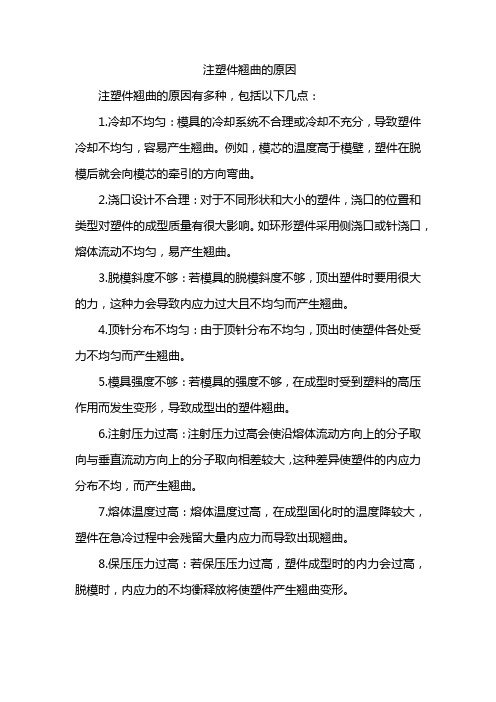
注塑件翘曲的原因
注塑件翘曲的原因有多种,包括以下几点:
1.冷却不均匀:模具的冷却系统不合理或冷却不充分,导致塑件冷却不均匀,容易产生翘曲。
例如,模芯的温度高于模壁,塑件在脱模后就会向模芯的牵引的方向弯曲。
2.浇口设计不合理:对于不同形状和大小的塑件,浇口的位置和类型对塑件的成型质量有很大影响。
如环形塑件采用侧浇口或针浇口,熔体流动不均匀,易产生翘曲。
3.脱模斜度不够:若模具的脱模斜度不够,顶出塑件时要用很大的力,这种力会导致内应力过大且不均匀而产生翘曲。
4.顶针分布不均匀:由于顶针分布不均匀,顶出时使塑件各处受力不均匀而产生翘曲。
5.模具强度不够:若模具的强度不够,在成型时受到塑料的高压作用而发生变形,导致成型出的塑件翘曲。
6.注射压力过高:注射压力过高会使沿熔体流动方向上的分子取向与垂直流动方向上的分子取向相差较大,这种差异使塑件的内应力分布不均,而产生翘曲。
7.熔体温度过高:熔体温度过高,在成型固化时的温度降较大,塑件在急冷过程中会残留大量内应力而导致出现翘曲。
8.保压压力过高:若保压压力过高,塑件成型时的内力会过高,脱模时,内应力的不均衡释放将使塑件产生翘曲变形。
以上原因仅供参考,具体的情况可能需要根据实际的注塑过程进行分析和调整。
- 1、下载文档前请自行甄别文档内容的完整性,平台不提供额外的编辑、内容补充、找答案等附加服务。
- 2、"仅部分预览"的文档,不可在线预览部分如存在完整性等问题,可反馈申请退款(可完整预览的文档不适用该条件!)。
- 3、如文档侵犯您的权益,请联系客服反馈,我们会尽快为您处理(人工客服工作时间:9:00-18:30)。
改善措施
• 優化工藝,適當降低充模壓力、充模時間。 • 調節模具溫度,使用前後模溫差。
• 適當提升料溫,增加流動性。 • 修改澆口位置及產品結構,消除內應力 集中點。 • 薄壁產品,盡量采用性能優良的高速機 生產。
三、外力作用變形
• 粘模 • 脫模不平衡 • 產品遭受擠壓
外力作用變形原因
• 模面粗糙度不一致或有倒扣,開模時拉變形。 • 頂出機構不合理,產品脫模時不平衡而變形。 • 包裝方式不合理,產品擠壓而變形。
导致成型收缩不均的主要原因
1)成型品厚度不均,冷卻收縮速度不一致。 2)模具温度,冷卻收縮速度不一致。 3)因流动方向而产生的收缩率异向性
4)材料的收縮率太大。
5)成型工藝不合理,冷卻時間過短。
收縮變形的改善方案
•修改產品結構,盡量使產品各部位膠位厚度均 勻。 •加強模具泠卻系統,保證產品泠卻均勻 •修正澆口大小形狀及位置。 •更換低收縮率、低翹曲的材料。 •優化工藝,適當延長冷卻時間,使冷卻收縮 (結晶)盡可能在模腔內完成。
一、收縮變形
收 縮
•塑膠料為高分子材料。在成型時受熱膨脹,分 子間距離遠遠大於其分子鍵長度,成型冷卻後, 由於分子間引力,產生收縮。 •後收縮 成型完成後,產品內分子間距仍大於分子鍵, 存在引力 (或結晶仍未完成),收縮仍在繼續。
收縮變形
• 收縮變形
成型品各部分收缩不均时,就會产生变形 /翹曲。换言之,如果成型品收缩均匀, 就不会发生变形。
外力作用變形改善措施
• 拋光模具 • 修正脫模方式 • 改用合理的包裝方式
具體案例分析
•L形變形 •平板型變形 •箱形變形
L形變形
L形成型品一般产生向内侧的倾倒变形。
其原因有: L部分的成型品在向模具放热过程中,内侧比外侧差,相应地, 内侧比外侧冷却慢。因此,内侧比外侧的成型收缩率大,产生 向内侧的倾倒变形。
二、內應力變形
內應力
成型時充填過度,分子間距小於分子鍵長,分 子間存在排斥力。 產品離開模腔後,內應力釋放引起變形/翹曲。
產生內應力的原因
• 充填過度 充模壓力過大,時間過長,導致內應力過大。 • 模溫過低 膠料流動時阻力大,充模壓力需求增大,強行充填, 導致內應力過大。 • 料溫過低 膠料流動時阻力大,充模壓力需求增大,強行充填, 導致內應力過大。 • 澆口位置不合差異過大,產生應力集中 點 • 成型機射速不夠 薄壁產品,冷卻快,需要較高射速。
(1)非增强品种
(2)玻璃纤维增强等品种
•
L形的变形对策 L形的内侧倾倒变形对策如下:
改善對策
减少拐角内侧材料 通过拐角内侧的减料,非增强品种及玻璃纤维增强品种的内侧倾倒变形均得到大幅度改善。
改变浇口位置 通过浇口位置的改变,使内侧倾倒发生改变。特别是在玻璃纤维增强品种中,从拐角处设置浇口后,内侧倾 倒变形得到改善。
產品變形/翹曲原因分析及管控
注塑課:伍先武
080328
產品變形/翹曲
隨著SMT貼裝技術的使用越來越廣泛,對 塑膠產品的平整度要求也越來越高。
變形/翹曲的分類
• 收縮變形 • 內應力變形 • 外力作用變形
變形易產生位置
• • • • 塑膠產品熔結痕部位 產品膠位不均勻的地方,特別薄片結構產品 遠膠口部位 應力集中的部位
改变无浇口侧的厚度 在非增强品种中,通过反浇口侧的厚度变薄,使内侧倾倒变形得到改善。薄部位与厚部位之比小于1/2时, 变为向外侧倾倒。 但是,在玻璃纤维增强品种中没有此效果。 在拐角的内侧与外侧之间设置模具温度差 如图2-3-4所示,通过拐角内侧模具的充分冷却,可使非增强品种的内侧倾倒变形得到改善。但是我们看到, 要使倾倒角度接近0度,温度差需要达到20℃以上。如果模具结构比较简单,可只对拐角内侧进行局部冷却 时,则没有问题。但如果模具的结构比较复杂,由于温度差增大会对模具的啮合产生影响,需要注意。 另外,在玻璃纤维增强品种中几乎没有此效果。 在拐角的内侧设置三角肋条 此手法最为有效,非增强品种及玻璃纤维增强品种的内侧倾倒变形均可得到大幅度改善。三角肋条必须从 尽可能高的位置设置才有好的效果。其厚度设定为L形厚度的1/3~1/2,由此还可防止产生凹痕。但是,由 于受到部件性能上的制约,有时不能设置肋条,因此需要充分的注意和确认。
箱形變形
平板型變形