延迟焦化工艺与工程
120Ⅹ104ta延迟焦化项目工艺管道施工设计

目前,石家庄炼化分公司炼油部分拥有500万吨/年常减压蒸馏、200万吨/年重油催化裂化、80万吨/年延迟焦化等22套生产装置。
原油一次加工能力达到500万吨/年,全流程综合配套能力达到420万吨/年,各项技术经济指标稳步提升,通过产品质量升级改造,产品质量达到国家新标准要求,部分产品可供北京市场,企业竞争实力进一步增强。
通过引进、消化、吸收、再创新,化纤部分己内酰胺生产能力已突破6.5万吨/年。
2006年7月中国石化正式批复化纤6.5改16万吨/年扩容改造项目,目前该工程已经建成。
该项目成功实施后,中国石化组织开发的己内酰胺成套新技术将全流程实现工业化,并可形成具有自主知识产权和国际竞争优势的工业化核心技术。
二、编制依据:1.中国石油天然气华东勘察设计研究院120Ⅹ104t/a延迟焦化项目工艺管道施工设计图;2.《石油化工有毒、可燃介质管道工程施工及验收规范》SH/T 3501-20023. 《工业金属管道工程施工及验收规范》GB50235-97;4. 《工业金属管道工程质量检验评定标准》GB50184-93;5. 《石油化工钢制管道工程施工工艺标准》SH/T3517-2001;6. 《现场设备、工业管道焊接工程施工及验收规范》GB50236-98;7. API598、API600(美国石油协会)标准;8. 劳动部《压力管道安全管理与监察规定》(1996版);9.本公司企业标准《压力管道安装质量体系程序文件》。
10. 《石油化工设备和管道涂料防腐蚀技术规范》SH3022-1999;11. 《石油化工设备管道钢结构表面色和标志规定》SH3043-2003。
12.《压力管道安装安全质量监督检验规则》[国质检锅]2002 83。
三、质量目标:(1)括附着件上的焊缝),应用液体渗透法或磁粉法进行检验。
(2)对所有焊缝还应该进行100%照相检测。
四、施工部署:管道系统试验前,必须经监理单位,建设单位,施工单位,设计单位对下列各种资料及安装情况进行联合检查确认后,具备系统试验条件方可进行试压。
延迟焦化工艺详解及其安全注意事项
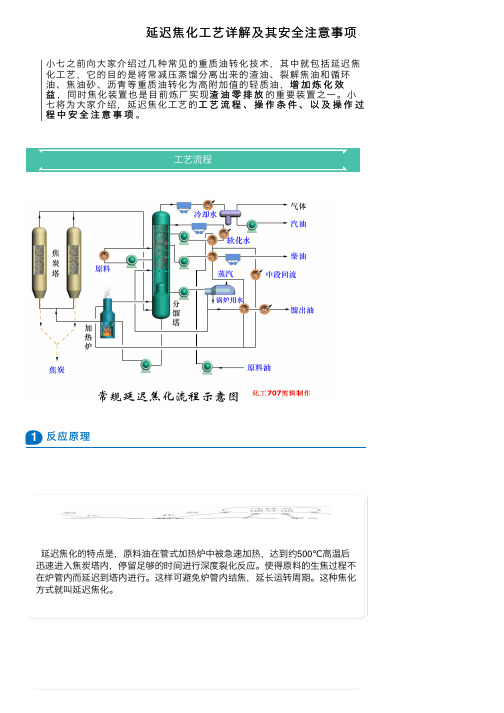
1延迟焦化⼯艺详解及其安全注意事项⼩七之前向⼤家介绍过⼏种常见的重质油转化技术,其中就包括延迟焦化⼯艺,它的⽬的是将常减压蒸馏分离出来的渣油、裂解焦油和循环油、焦油砂、沥青等重质油转化为⾼附加值的轻质油,增增加炼化效益,同时焦化装置也是⽬前炼⼚实现渣渣油零排放的重要装置之⼀。
⼩七将为⼤家介绍,延迟焦化⼯艺的⼯⼯艺流程、操作条件、以及操作过程中安全注意事项。
⼯艺流程反应原理延迟焦化的特点是,原料油在管式加热炉中被急速加热,达到约500℃⾼温后迅速进⼊焦炭塔内,停留⾜够的时间进⾏深度裂化反应。
使得原料的⽣焦过程不在炉管内⽽延迟到塔内进⾏。
这样可避免炉管内结焦,延长运转周期。
这种焦化⽅式就叫延迟焦化。
延迟焦化装置的⽣产⼯艺分焦化和除焦两部分,焦化为连续操作,除焦为间歇操作。
2由于⼯业装置⼀般设有两个或四个焦炭塔,所以整个⽣产过程仍为连续操作。
⼯艺描述原料经加热炉对流室预热管预热⾄350℃进⼊焦化分馏塔下部与来⾃焦炭塔顶的⾼温油⽓换热,可同时将轻质油蒸出。
换热后原料油温度约390~395℃,再与循环油⼀起泵⼊加热炉炉管,迅速加热到500℃再进⼊焦炭塔底。
为了防⽌炉管结焦,需向炉管内注⽔以加⼤流速。
渣油在焦炭塔内停留⾜够长时间以完成裂化、缩合反应,⽣成的焦炭留在焦炭塔内。
⾼温油⽓从塔顶通⼊分馏塔下部;经换热后分馏得到产品⽓、汽油、柴油等。
焦炭塔轮流使⽤。
操作条件影响焦化的主要因素有:原料性质、加热炉出⼝温度、反应压⼒。
加热炉出⼝温度:500℃左右;加热炉出⼝温度的变化直接影响到炉管内和焦炭塔内的反应深度,加热炉出⼝温度太⾼,反应速度和反应深度增⼤,⽓体、汽油和柴油的产率增⼤,蜡油的产率减⼩,焦炭产率也会由于所含挥发性组分的减⼩⽽降低 ,同时由于温度太⾼,会造成汽油、柴油继续裂解,结焦增多。
加热炉出⼝温度太低,则会造成反应不完全。
分馏塔底温度:375 ~395℃,过⾼易结焦。
分馏塔顶温度:100 ~110℃柴油输出线温度:275 ~285℃系统压⼒直接影响到焦炭塔的操作压⼒,⼀般来说,压⼒降低会使蜡油产率增⼤⽽使柴油产率降低。
延迟焦化装置吸收稳定系统工艺与操作要点ppt
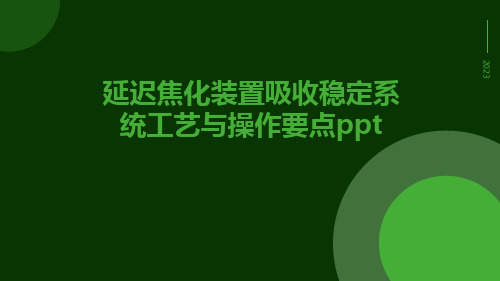
1 2
原料切割
将重油切割成小段,降低加热炉内的结焦倾向 。
加热和脱水
将原料加热到一定温度,并去除其中的水分和 轻质组分。
脱盐和脱硫
3
去除原料中的盐类和硫化物,防止腐蚀设备。
延迟焦化反应过程
加热炉加热
将原料加热到焦化反应所需温度。
焦化反应
原料在加热炉中发生裂解反应,生成气体、汽油 、柴油和重焦炭等产品。
对原料油的API、残碳、硫含量等性质进行严格把控,保 证进料质量。
原料加热
将原料加热到适当的温度,以便在焦化反应中达到最佳 效果。
进料方式选择
可选择连续进料或间歇进料方式,根据实际情况进行选 择。
反应条件优化
反应温度
01
通过控制加热炉出口温度,保证焦化反应在适宜的温度范围内
进行。
反应压力
02
通过控制分馏塔顶部压力,保证焦化反应在适宜的压力范围内
应用案例二:延迟焦化装置优化操作
优化背景
延迟焦化装置操作复杂,影响因素多,需要进行优化以提高装置的经济效益和环保性能。
优化内容
采用先进的在线监测和分析技术,对加热炉出口温度、压力,进料速度等关键参数进行实 时监测和调控。
优化效果
优化后装置运行更加稳定,产品质量和收率得到提高,同时降低了能耗和污染物排放。
2023
延迟焦化装置吸收稳定系 统工艺与操作要点ppt
目录
• 引言 • 延迟焦化装置工艺流程 • 操作要点 • 安全与环保 • 应用案例与效果展示
01
引言
目的和背景
介绍延迟焦化装置 吸收稳定系统的工 艺与操作要点
帮助企业优化生产 过程和提高经济效 益
为相关领域技术人 员提供操作指南
延迟焦化装置吸收稳定系统工艺与操作资料ppt

THANKS
谢谢您的观看
吸收稳定系统的工艺流程
03
脱乙烷塔
主要作用是将吸收剂中的C2组分脱除,避免C2组分进入吸收塔影响吸收效果。
吸收稳定系统的主要设备
01
吸收塔
是吸收稳定系统的核心设备,主要作用是进行吸收操作,使混合碳四烃中的C4、C5轻组分被吸收剂吸收。
02
分馏塔
主要作用是将吸收剂中的C5以上组分分离成液化气和富气。
作用
通过吸收稳定系统,可以降低混合碳四烃中C4、C5轻组分和C6以上的重组分的含量,同时增加液化气中丙烷和丁烷的含量,从而满足液化气产品的质量要求。
吸收稳定系统的定义和作用
原料
进入吸收稳定系统的原料主要是来自延迟焦化装置的混合碳四烃。
工艺流程
混合碳四烃进入吸收塔,与脱乙烷塔来的贫油逆流接触,C4以下组分被吸收到油相中,从塔顶排出;C5以上组分从塔釜排出进入分馏塔,在分馏塔中切割成液化气和富气。
延迟焦化装置的操作
在操作过程中,需要控制加热炉出口温度、焦炭塔压力、分馏塔液面等参数,保证装置的稳定运行。
吸收稳定系统的操作
吸收稳定系统的操作主要包括吸收塔和稳定塔的操作。吸收塔主要通过控制吸收剂的流量和温度来吸收气体中的轻组分,而稳定塔则通过降低吸收塔顶部流出的富吸收油中的轻组分含量来达到操作要求。
xx年xx月xx日
延迟焦化装置吸收稳定系统工艺与操作资料
延迟焦化装置介绍吸收稳定系统介绍延迟焦化装置操作资料吸收稳定系统操作资料延迟焦化装置与吸收稳定系统的关系实际操作中的注意事项
contents
目录
01
延迟焦化装置介绍
延迟焦化是将重质烃类在高温高压下进行裂解和缩合反应,生成气体、汽油、柴油、蜡油等产品的过程。
延迟焦化工艺与工程
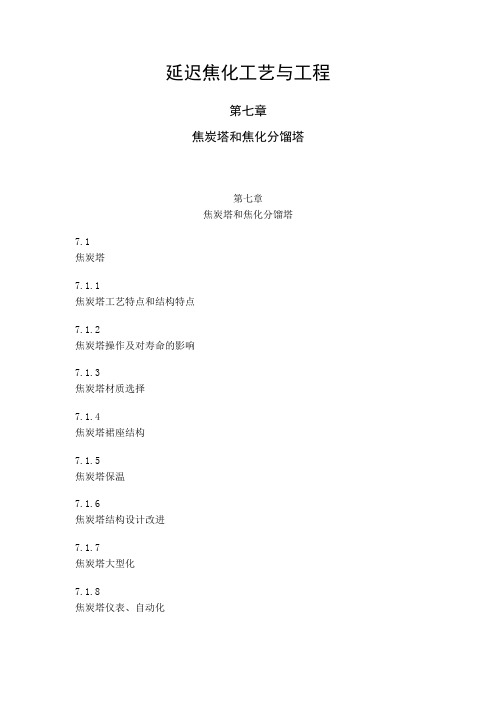
延迟焦化工艺与工程第七章焦炭塔和焦化分馏塔第七章焦炭塔和焦化分馏塔7.1焦炭塔7.1.1焦炭塔工艺特点和结构特点7.1.2焦炭塔操作及对寿命的影响7.1.3焦炭塔材质选择7.1.4焦炭塔裙座结构7.1.5焦炭塔保温7.1.6焦炭塔结构设计改进7.1.7焦炭塔大型化7.1.8焦炭塔仪表、自动化7.1.9焦炭塔的检测和寿命评估7.2 焦化分馏塔7.2.1焦化分馏塔设计特点7.2.2焦化分馏塔的塔板结构第七章焦炭塔和焦化分馏塔7.1焦炭塔7.1.1焦炭塔的工艺特点和设备特点延迟焦化是以渣油或类似渣油的各种重质油、污油及原油为原料,通过加热炉快速加热到一定的温度后进入焦炭塔,在塔内适宜的温度、压力条件下发生裂解、缩合反应,生成气体、汽油、柴油、蜡油、循环油组分和焦炭的工艺过程,见图7-1。
延迟焦化装置的主要设备有焦化加热炉、焦炭塔、焦化分馏塔、吹汽放空塔、加热炉进料泵、水力除焦机械等,其中焦化加热炉被认为是焦化装置的关键设备,而焦炭塔则是焦化装置的核心设备。
因为焦炭塔是焦化装置的反应器,加热炉、分馏塔、放空系统、冷切焦水处理系统、水力除焦系统等均与之有关。
虽然焦炭塔是一个空筒设备,但它的设计涉及到几乎全装置的工艺过程。
焦炭塔的工艺特点是操作温度高,最高可达到495℃,操作温度变化频繁,每一个操作周期都要由常温变化到最高操作温度,并生焦周期越短,变温速度越快;它不但是一个反应器而且还是一个装焦炭的容器,操作不当会使生焦的泡沫溢出,造成后部系统结焦。
焦炭塔在生焦过程中基本处于恒温操作。
在除焦过程中要经过先降温再升温的变化过程,往往由这一个变温操作过程使焦炭塔及其相关系统的设计有些复杂。
焦炭塔一般是两台一组,每套延迟焦化装置中有的是一组(两台),有的是两组(四台)焦炭塔。
在每组塔中,一台塔在反应生焦时,另一台塔则处于除焦阶段。
即当一台塔内焦炭积聚到一定高度时进行切换,切换后先通入少量蒸汽把轻质烃类汽提去分馏塔,再大量通入蒸汽,汽提重质烃类去放空冷却塔,回收重油和水。
分析延迟焦化装置工艺技术特点及其应用
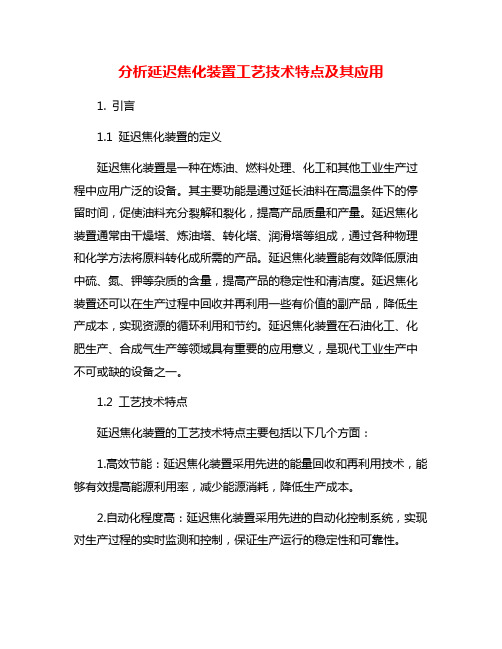
分析延迟焦化装置工艺技术特点及其应用1. 引言1.1 延迟焦化装置的定义延迟焦化装置是一种在炼油、燃料处理、化工和其他工业生产过程中应用广泛的设备。
其主要功能是通过延长油料在高温条件下的停留时间,促使油料充分裂解和裂化,提高产品质量和产量。
延迟焦化装置通常由干燥塔、炼油塔、转化塔、润滑塔等组成,通过各种物理和化学方法将原料转化成所需的产品。
延迟焦化装置能有效降低原油中硫、氮、钾等杂质的含量,提高产品的稳定性和清洁度。
延迟焦化装置还可以在生产过程中回收并再利用一些有价值的副产品,降低生产成本,实现资源的循环利用和节约。
延迟焦化装置在石油化工、化肥生产、合成气生产等领域具有重要的应用意义,是现代工业生产中不可或缺的设备之一。
1.2 工艺技术特点延迟焦化装置的工艺技术特点主要包括以下几个方面:1.高效节能:延迟焦化装置采用先进的能量回收和再利用技术,能够有效提高能源利用率,减少能源消耗,降低生产成本。
2.自动化程度高:延迟焦化装置采用先进的自动化控制系统,实现对生产过程的实时监测和控制,保证生产运行的稳定性和可靠性。
3.适应性强:延迟焦化装置具有较强的适应性,可以根据不同原料的特性和生产需求进行灵活调整,保证生产过程的稳定性和高效性。
4.产品质量高:延迟焦化装置在生产过程中采用先进的分离和净化技术,能够有效提高产品的纯度和质量,满足不同行业的需求。
5.环保性好:延迟焦化装置在设计和运行过程中注重环保要求,采用先进的污染治理技术,减少排放物对环境的影响,符合现代工业发展的可持续发展理念。
延迟焦化装置的工艺技术特点体现了其在煤化工和石油化工等领域的重要性和广泛应用前景。
通过不断优化和改进,延迟焦化装置的工艺技术将有望进一步提升生产效率和产品质量,推动相关产业的发展和升级。
1.3 应用领域延迟焦化装置是一种在煤化工和石油化工行业中被广泛应用的重要设备。
其主要应用领域包括煤焦油、石油焦油、裂解油、石脑油等石油化工产品的生产过程中。
分析延迟焦化装置工艺技术特点及其应用

分析延迟焦化装置工艺技术特点及其应用
延迟焦化是一种石化工艺,它将重油迅速加热至高的温度和压力下进行裂解,生成烯
烃和芳香烃。
它的工艺技术特点主要体现在以下几个方面:
1. 裂解时延迟:延迟焦化采用了反应器之外的加热装置,将液态重油迅速加热至高
温度,并在反应器中加入催化剂,让重油进行裂解。
这种工艺使得反应时间延迟,可以增
加裂解产物的芳香烃和烯烃含量。
2. 高温高压:延迟焦化反应器内部的温度和压力非常高,通常需要在1000℃以上和1.5 MPa以上的条件下操作。
高温高压环境才能促进重油的裂解,同时也会增加反应物中
间体的生成和分解,从而增加了反应物转化率。
3. 重油先热解再裂解:在延迟焦化中,重油首先经过热解阶段,使得重油中的大分
子化合物转化为小分子烃,主要为液化气,成分为丁烷、丙烷和乙烷等。
热解反应所生成
的烃类会随后进入裂解阶段,利用催化剂进一步裂解为烯烃和芳香烃。
4. 高效催化剂:延迟焦化需要使用高效催化剂,以提高重油的裂解效率和选择性。
目前常用的催化剂有氢氧化镁、氢氧化钠和氢氧化钾等。
延迟焦化可以处理各种成分的重油,包括低成分的重油、深层储层的油田油和油砂等。
它能够生产高品质的清洁燃料,如芳香烃和烯烃,被广泛应用于石化工业领域中。
同时,
使用延迟焦化可以降低重油的处理成本,提高原油利用率和产品质量,具有很高的经济效
益和社会效益。
延迟焦化操作规程
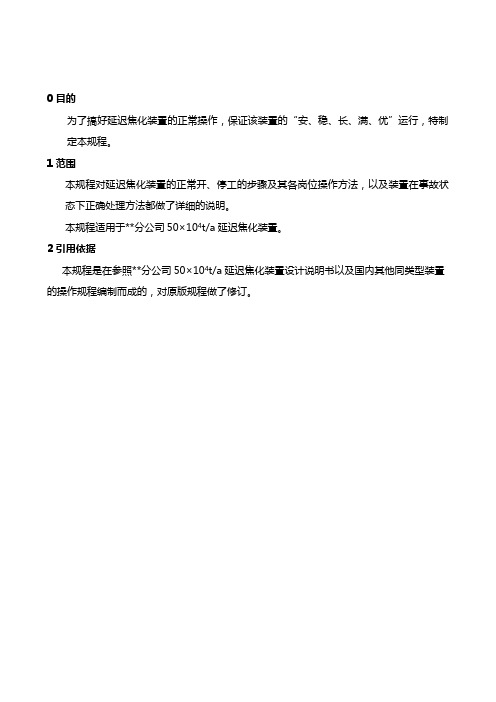
0目的为了搞好延迟焦化装置的正常操作,保证该装置的“安、稳、长、满、优”运行,特制定本规程。
1范围本规程对延迟焦化装置的正常开、停工的步骤及其各岗位操作方法,以及装置在事故状态下正确处理方法都做了详细的说明。
本规程适用于**分公司50×104t/a延迟焦化装置。
2引用依据本规程是在参照**分公司50×104t/a延迟焦化装置设计说明书以及国内其他同类型装置的操作规程编制而成的,对原版规程做了修订。
一装置简介1.概述延迟焦化装置由中国石化北京设计院设计,中国石化第四建设公司主要施工,于1999.3.29一次开车成功。
装置占地22500m2,包括加热炉1台、塔5座、容器39台、压缩机1台、冷换设备41台、通用机械81台、电梯1台、水力除焦设备2套、5000 m3原料罐3座、1000 m3甩油罐1座。
1.1设计依据(1)**炼油厂改建工程50×104t/a延迟焦化装置初步设计文件L8204-12。
(2)关于**炼油厂改建工程50×104t/a延迟焦化装置初步设计的批复,中石化(1996)建设字287号。
(3)**炼油厂与中国石化北京设计院签定的合同书:“**炼油厂改建工程50×104t/a 延迟焦化装置,合同号:44-96039”。
1.2设计规模装置设计加工能力50×104t/a,年开工时数8000小时。
1.3主要技术特点(1)采用无单独开工循环线的无堵焦阀焦炭塔开工暖塔工艺流程。
(2)采用油水分离的单塔两段接触冷却塔,缓和塔底油带水,塔顶冷凝水带油的现象。
(3)水力除焦操作过程采用PLC安全自保连锁控制,保证了水力除焦操作的安全性。
(4)采用有井架水力除焦技术。
(5)按照初步设计的批复意见,装置不设重蜡油系统,但对分馏塔预留重蜡油抽出口。
1.4物料平衡本装置设计加工能力50×104t/a,年开工时数8000小时,循环比0.4。
物料平衡表1.5本装置产生的压缩焦化气体出装置后去车用液化气装置。
- 1、下载文档前请自行甄别文档内容的完整性,平台不提供额外的编辑、内容补充、找答案等附加服务。
- 2、"仅部分预览"的文档,不可在线预览部分如存在完整性等问题,可反馈申请退款(可完整预览的文档不适用该条件!)。
- 3、如文档侵犯您的权益,请联系客服反馈,我们会尽快为您处理(人工客服工作时间:9:00-18:30)。
延迟焦化工艺与工程第七章焦炭塔和焦化分馏塔第七章焦炭塔和焦化分馏塔7.1焦炭塔7.1.1焦炭塔工艺特点和结构特点7.1.2焦炭塔操作及对寿命的影响7.1.3焦炭塔材质选择7.1.4焦炭塔裙座结构7.1.5焦炭塔保温7.1.6焦炭塔结构设计改进7.1.7焦炭塔大型化7.1.8焦炭塔仪表、自动化7.1.9焦炭塔的检测和寿命评估7.2 焦化分馏塔7.2.1焦化分馏塔设计特点7.2.2焦化分馏塔的塔板结构第七章焦炭塔和焦化分馏塔7.1焦炭塔7.1.1焦炭塔的工艺特点和设备特点延迟焦化是以渣油或类似渣油的各种重质油、污油及原油为原料,通过加热炉快速加热到一定的温度后进入焦炭塔,在塔内适宜的温度、压力条件下发生裂解、缩合反应,生成气体、汽油、柴油、蜡油、循环油组分和焦炭的工艺过程,见图7-1。
延迟焦化装置的主要设备有焦化加热炉、焦炭塔、焦化分馏塔、吹汽放空塔、加热炉进料泵、水力除焦机械等,其中焦化加热炉被认为是焦化装置的关键设备,而焦炭塔则是焦化装置的核心设备。
因为焦炭塔是焦化装置的反应器,加热炉、分馏塔、放空系统、冷切焦水处理系统、水力除焦系统等均与之有关。
虽然焦炭塔是一个空筒设备,但它的设计涉及到几乎全装置的工艺过程。
焦炭塔的工艺特点是操作温度高,最高可达到495℃,操作温度变化频繁,每一个操作周期都要由常温变化到最高操作温度,并生焦周期越短,变温速度越快;它不但是一个反应器而且还是一个装焦炭的容器,操作不当会使生焦的泡沫溢出,造成后部系统结焦。
焦炭塔在生焦过程中基本处于恒温操作。
在除焦过程中要经过先降温再升温的变化过程,往往由这一个变温操作过程使焦炭塔及其相关系统的设计有些复杂。
焦炭塔一般是两台一组,每套延迟焦化装置中有的是一组(两台),有的是两组(四台)焦炭塔。
在每组塔中,一台塔在反应生焦时,另一台塔则处于除焦阶段。
即当一台塔内焦炭积聚到一定高度时进行切换,切换后先通入少量蒸汽把轻质烃类汽提去分馏塔,再大量通入蒸汽,汽提重质烃类去放空冷却塔,回收重油和水。
待含在焦炭内的大量油被吹出后再通入冷却水使焦炭冷却到80℃左右,然后除焦。
除焦完成后再用另一个塔的油气预热到400℃左右,然后切换进料。
每台塔的切换使用周期一般为48小时,其中生焦24小时,除焦及其它辅助操作24小时(见表7-1)。
除焦采用高压水,高压水压力达14.8~30MPa。
取决于塔径的大小。
随着技术的进步,目前每台塔的切换周期已缩短,一般30~36小时。
除下的焦炭落入焦池,同时用桥式起重抓斗经皮带输送到别处存放或装车外运。
装置所产的气体和汽油,分别用气体压缩机和泵送入稳定吸收系统进行分离,得到干气及液化气,并使汽油的蒸汽压合格。
柴油需要加氢精制,蜡油可作为催化裂化及加氢裂化原料或燃料油。
表7-1图7-1延迟焦化流程焦炭塔的工艺设计主要包括焦炭塔直径的确定、塔高的确定、和相关系统的设计。
焦炭塔的直径和高度焦炭塔的直径和高度主要取决于装置的处理量、原料性质、操作温度、操作压力和循环比。
装置的处理量是决定焦炭塔大小的主要参数,目前国内单塔处理量和焦炭塔规格的对应关系如下:焦炭塔的单塔处理量越大,要求的焦炭塔直径越大,这主要是由焦炭塔塔内的允许气速决定的。
焦化原料渣油在加热炉中被快速加热到500℃左右进入焦炭塔,为防止加热炉管结焦,炉出口的反应转化率一般不大于8%(气体和汽油的转化率),大部分的反应延迟到焦炭塔内进行。
原料进入焦炭塔,在塔内适宜的压力、温度和停留时间的条件下发生裂解和缩合反应,裂解为吸热反应,缩合为放热反应,裂解的热量除了来自原料渣油本身外还有一部分由缩合反应提供,缩合反应生成的焦炭停留在塔内,并由塔壁向中心扩展,中心形成进料通道,在焦炭层以上为主要反应区,即泡沫层。
泡沫层分油相泡沫和气相泡沫,气相泡沫在上部,其密度约为30~100kg/m3,油相泡沫在焦层以上,其密度约为100~700 kg/m3,焦化反应温度即为泡沫层温度,一般为460~480℃,并且生焦率越高,该反应温度越高。
随着原料的不断进入,产生的焦炭量不断增加,焦炭层高度增加,泡沫层也随之连续升高。
塔内反应示意见图7-2。
图7-2焦炭塔内生焦示意图由于泡沫层为反应区,一般不希望正在反应的泡沫被油气夹带到焦炭塔顶口的大油气管线和分馏塔,导致管线结焦和分馏塔内结焦影响产品质量。
焦炭塔内油气的允许气速可用下式计算:其中Uc为塔内气相线速,m/s;为轻相泡沫层密度,kg/m3;为气相层密度,kg/m3;据资料报导,国外在焦炭塔内不注入消泡剂时,允许气速一般为0.11~0.17m/s。
在使用消泡剂时,正常的设计油气速度应低于0.12~0.21m/s。
根据允许的油气速度和焦炭塔内的油气流量,结合进料性质和塔顶操作压力即可确定焦炭塔的直径。
焦炭塔内的油气体积流量除和渣油进料量有关外,与原料性质、操作条件也有密切的关系。
在确定焦炭塔的直径以前应首先确定焦炭塔的操作条件和产品分布。
渣油是以碳、氢为主要元素的大分子烃类,通常分为饱和烃、芳烃、胶质和沥青质,沥青质含量高的渣油生焦率较高,轻油收率较低。
一般生焦率的估算可按式:Wc=1.6K进行,其中K为渣油的康氏残炭,产品分布一般最终由试验确定。
当原料性质确定后,对生焦率和产品分布影响较大的主要是循环比、反应温度和压力。
循环比减少10%,生焦率一般减少1%,同时焦化蜡油收率增加,气体、汽油、柴油收率下降。
当需要提高装置的液体收率时一般采用降低循环比(0.15~0.25)或零循环比操作;当需要多产焦化石脑油和柴油时一般采用较大循环比(0.25~0.45)操作;当焦化蜡油无出路或需要最大可能地生产柴油和乙烯原料时一般采用大循环比(0.4~1.0)操作。
循环比越大,焦炭塔内的油气体积流量越大。
提高焦化温度可增产液体产品收率,但基于焦化反应的特点,反应温度(炉出口温度控制)调整的幅度是很窄的,温度过高会导致提前结焦,堵塞炉管、转油线,影响开工周期,同时易生成硬质石油焦,使除焦困难;温度过低导致热量不足反应深度不够,轻油收率降低,焦炭挥发分增大或产生焦油。
一般情况下是根据原料性质确定最佳的操作温度,通常焦化炉出口温度为495~505℃,芳烃含量和沥青质含量的比值较大时宜采用较高的炉出口温度。
采用低压操作可改善焦化产品分布,在国内外已普遍认可,国内焦炭塔塔顶操作压力一般为0.15~0.20Mpa,国外最低的达到0.1~0.15Mpa。
压力降低一般能提高蜡油的收率,但是增大了焦炭塔的气体体积流量,势必使焦炭塔的塔径和油气管线加大,并影响压缩机的加大,所以装置的投资增加,因此应综合设备投资、操作费用和产品分布等因素确定适宜的操作压力。
在基本确定焦炭塔的直径后,根据焦炭产率、生焦时间、泡沫层高度来确定焦炭塔的高度。
焦炭产率和原料性质、操作条件有关,泡沫层高度和原料性质、反应温度及压力有关,一般情况下生焦率高的渣油反应的泡沫层高度小,生焦率低的渣油的泡沫层高度大。
当在焦炭塔内注入消泡剂后,泡沫层的高度一般减少40~65%。
当单塔处理能力、原料性质和操作条件确定后,塔内的焦层高度主要决定于生焦时间。
目前国内焦化装置设计的生焦时间均为24小时,国外焦化生焦时间为12~24小时,采用16~18小时的占大多数,采用短的生焦时间,可以提高焦炭塔的利用率,或者同等规模的焦炭塔的高度减少。
在确定焦炭塔高度时应留有一定的安全空高,安全空高一般为塔顶切线离泡沫层顶部的距离。
国内设计的焦炭塔一般安全空高大于等于5米,国外焦炭塔的安全空高一般为2~3米。
空高越大,焦炭塔的利用率越低,但油气在塔内的停留时间延长,对减少油气线和分馏塔内结焦有利。
空高的计算公式如下:其中:H切-焦炭塔切线高度,m;G焦-焦炭生焦率,kg/h;焦-生焦时间,hr;焦-塔内焦炭堆密度,kg/m3(800~900kg/m3);V锥-焦炭塔锥体体积:m3;D塔-焦炭塔直径,m;H泡沫-泡沫层高度,m。
通常所说的缩短生焦时间可以提高处理量,只是焦炭塔的安全空高增大,相应的油气线速可以在较高的范围内操作。
另外采用在生焦初期加大焦炭塔的进料,生焦末期减少焦炭塔的进料的措施,也可以提高装置的年加工能力。
焦炭塔直径和切线高度的关系焦炭塔直径和高度相互补充,当装置处理量、操作条件确定后,直径增大可以降低高度,高度增加也可以适当减少塔径。
国内在过去建设的焦炭塔的直径一般为5.4~6.4米,其高径比一般为3~4。
最近建设的大直径焦炭塔的高径比一般为2~3。
美国焦炭塔的高径比一般为2~3。
焦炭塔的直径和高度受到水力除焦机械,制造、运输、吊装等的限制,不宜太大和太高,美国目前运行的最大焦炭塔的直径为9.114米。
建议在装置处理量较大,采用一炉二塔使焦炭塔的直径和高度特别庞大时,采用二炉四塔或三炉六塔更为适宜。
焦炭塔的结构特点焦炭塔是一个直立园柱壳压力容器,顶部是球形或椭圆形封头,下部是锥体,见图7-3。
直径范围通常为4.6~9.4米,高约25~35米。
在顶部有直径为φ600~φ1500的盲板法兰(即钻焦口),底部有φ1600~φ2000的盲板法兰(即卸焦口),该盲板法兰上有φ150~φ300的渣油入口接管。
裙座位于连接壳体与锥体焊缝的区域,用来支撑塔体。
通常焦炭塔是用碳钢、C-1/2Mo、1Cr-1/2Mo、1 1/4Cr-1/2Mo和2 1/4Cr-1.0Mo钢制造,其壁厚通常在14~42毫米之间。
通常,焦炭塔壳体采用不锈钢复合板制造,复层为厚2.0~3.2mm的405或410S型不锈钢,以抵抗腐蚀。
焦炭塔设计压力范围为0.2~0.8MPa,一般为0.25~0.35MPa。
操作温度为427~495℃。
焦炭塔外保温通常采用120~180mm的玻璃纤维或复合硅酸盐等保温材料,并用铝合金薄板或不锈钢薄板作为保护层。
压力安全阀位于焦炭塔顶部,料位测量通常采用三个中子料位计,安装于塔体外表面。
焦炭塔上封头过去大多采用球形封头,其优点是受力条件好,耗材少;但近来大都采用椭圆封头(2:1),其优点在于在保证塔顶标高不变的情况下(即钻杆长度不变)的情况下,能增加焦炭塔筒体段的有效体积。
以φ8800焦炭塔为例,将球形封头改为椭圆封头,能增加体积44.6米3。
焦炭塔下部进料口的接管的结构型式大致有三种,即从侧面进入、水平并呈向上倾斜方向进入和轴向进入。
操作经验表明,500℃左右的原料油从侧面进入焦炭塔会造成塔底加热不均匀,所引起的变形会促使塔体倾斜并产生裂纹、鼓胀和其它缺陷,将使塔的可靠性下降。
当原料油入口接管呈水平方向和呈向上倾斜方向配置时,对面的器壁受较强烈加热而产生附加的应力;若原料油在中心轴向进入,则可以保证设备均匀加热,焦炭塔操作的可靠性增大,这种结构设计使变形减少。
目前焦炭塔大都采用这种轴向进料方式。