关于对铸坯的冷却及裂纹缺陷分析基础知识
连铸坯表面裂纹形成及防止分析

浸入式水口对中,防止偏流 合理的浸入式水口设计(合适的出口直径,倾角) 合适的水口插入深度 合适的频率和振幅
(3) 结晶器振动
2 铸坯表面纵裂纹
(4) 出结晶器铸坯运行 二次冷却均匀性 (5) 调整钢水成分 钢中碳含量避开包晶区,C向下线或上线控制 钢中S<0.015% 残余元素Cu、As、Zn控制<0.1%
图2-4 拉速对纵裂纹的影响
2 铸坯表面纵裂纹
(3) 保护渣 液渣层厚度<10mm,纵裂纹增加(图2-5)。
图2-5 液渣层厚度对纵裂纹的影响
2 铸坯表面纵裂纹
(4) 结晶器液面波动 液面波动<±5mm,纵裂纹最少(图2-6);
图2-6 结晶器液面波动对纵裂纹的影响
2W (T1 T2 ) W
连铸坯表面裂纹 形成及防止
宋晔
内容
1 2 3 4 5 前言 铸坯表面纵裂纹 铸坯表面横裂纹 铸坯表面星形裂纹 结论
1.前言
连铸坯质量概念: ◆ 铸坯洁净度(夹杂物数量、类型、尺寸、 分布) ◆ 铸坯表面质量(表面裂纹、夹渣、气孔) ◆ 铸坯内部质量(内部裂纹、夹杂物,中 心疏松、缩孔、偏析) ◆ 铸坯形状缺陷(鼓肚、脱方)
2 铸坯表面纵裂纹
2.3 影响表面纵裂纹产生的因素
(1) 钢水成分
◆ [S]>0.015%,纵裂纹增加(图2-2);
◆ [C]=0.12~0.15%,纵裂纹产生严重(图2-3)
图2-2 钢中[S]与裂纹指数的关系
2 铸坯表面纵裂纹
பைடு நூலகம்
图2-3 含碳量对板坯宽面纵裂纹的影响
2 铸坯表面纵裂纹
(2) 拉速 拉速增加,纵裂纹指数增加(图2-4);
分析铸造热裂缺陷形成的原因及改进对策

分析铸造热裂缺陷形成的原因及改进对策铸造热裂缺陷是铸造过程中常见的一种缺陷形态,会对铸件的性能和质量造成重大影响。
为了解决这一问题,需要深入分析其成因,并制定改进对策。
本文将从铸造热裂缺陷的原因以及改进措施两个方面展开讨论,旨在为铸造工艺提升提供思路和指导。
一、铸造热裂缺陷的形成原因铸造热裂缺陷通常在铸件冷却过程中产生,以下是其形成的主要原因:1. 温度梯度引起的应力集中铸件冷却过程中,由于各部分温度变化不一致,会导致内部产生温度梯度,从而引起局部局部应力集中。
当材料的强度无法承受这种应力时,就会发生热裂缺陷。
2. 晶粒的收缩行为铸件在凝固过程中,晶粒会出现收缩。
若凝固过程中晶粒收缩不一致,就会引起内部应力的不平衡,从而产生热裂。
3. 液态膨胀引起的应力铸造过程中,液态金属体积较大,当其冷却凝固时,体积会缩小,引起内部应力。
若应力超过材料的承载能力,就会发生热裂缺陷。
二、改进对策为了解决铸造热裂缺陷问题,可以采取以下改进对策:1. 优化铸造工艺参数通过调整铸造温度、冷却速度以及铸件尺寸等参数,使得整个铸造过程中的温度分布更加均匀,减小温度梯度和晶粒收缩不一致性,从而减轻应力集中的程度,降低热裂的风险。
2. 控制液态膨胀行为合理控制铸造合金的成分,通过合金设计等方法来调整材料的液态膨胀行为。
降低材料在冷却凝固过程中产生的应力,减少热裂的概率。
3. 采用合适的铸型材料选择合适的铸型材料也是防止铸造热裂缺陷的关键。
材料的导热性能和热传导能力会影响铸件冷却的速度,因此在选择铸型材料时要充分考虑其导热性和热传导性能。
4. 进行合理的余热处理通过对已铸造完成的铸件进行合理的余热处理,使其内部温度均衡分布,减少应力集中和热裂的风险。
此外,适当的余热处理还能改善铸件的织构和力学性能。
5. 严格控制冷却速度合理控制冷却速度是防止铸造热裂缺陷的重要措施之一。
通过对冷却介质的选择以及冷却方式的优化,可以实现对冷却速度的有效控制,降低热裂的风险。
铸造裂纹产生的原因和避免的措施
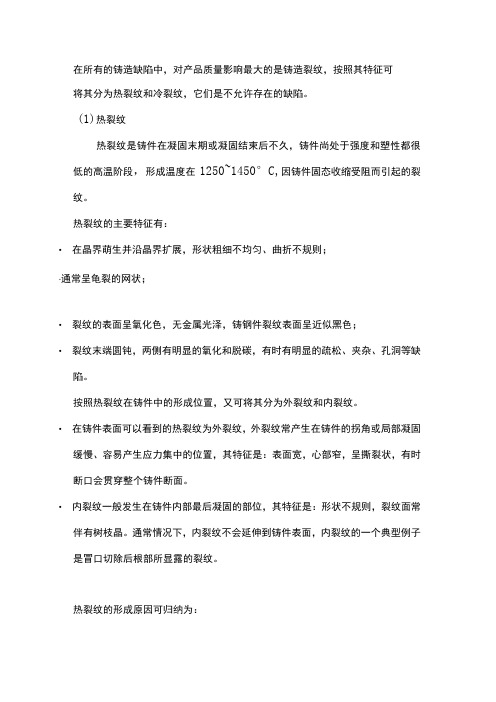
在所有的铸造缺陷中,对产品质量影响最大的是铸造裂纹,按照其特征可将其分为热裂纹和冷裂纹,它们是不允许存在的缺陷。
(1)热裂纹热裂纹是铸件在凝固末期或凝固结束后不久,铸件尚处于强度和塑性都很低的高温阶段,形成温度在1250~1450°C,因铸件固态收缩受阻而引起的裂纹。
热裂纹的主要特征有:•在晶界萌生并沿晶界扩展,形状粗细不均匀、曲折不规则;∙通常呈龟裂的网状;•裂纹的表面呈氧化色,无金属光泽,铸钢件裂纹表面呈近似黑色;•裂纹末端圆钝,两侧有明显的氧化和脱碳,有时有明显的疏松、夹杂、孔洞等缺陷。
按照热裂纹在铸件中的形成位置,又可将其分为外裂纹和内裂纹。
•在铸件表面可以看到的热裂纹为外裂纹,外裂纹常产生在铸件的拐角或局部凝固缓慢、容易产生应力集中的位置,其特征是:表面宽,心部窄,呈撕裂状,有时断口会贯穿整个铸件断面。
•内裂纹一般发生在铸件内部最后凝固的部位,其特征是:形状不规则,裂纹面常伴有树枝晶。
通常情况下,内裂纹不会延伸到铸件表面,内裂纹的一个典型例子是冒口切除后根部所显露的裂纹。
热裂纹的形成原因可归纳为:1.浇铸冷却过程中收缩应力过大;2.铸件在铸型中收缩受阻;3.铸件冷却不均匀;4.铸件结构设计不合理,存在几何尺寸突变;5.有害杂质在晶界富集;6.铸件表面与涂料之间产生了相互作用。
(2)冷裂纹冷裂纹是铸件凝固结束后继续冷却到室温的过程中,因铸件局部受到的拉应力大于铸件本体的破断强度而引起的开裂。
冷裂纹的主要特征有:L总是发生在承受拉应力的部位,特别是铸件形状、尺寸发生变化的应力集中部位;2.裂纹宽度均匀、细长,呈直线或折线状,穿晶扩展;3.裂纹面比较洁净、平整、细腻,有金属光泽或呈轻度氧化色;4.裂纹末端尖锐,裂纹两侧基本无氧化和脱碳,显微组织与基体的基本相同。
冷裂纹产生的原因,可归纳为:1.铸件结构系统设计不合理,铸件壁厚不均匀会导致铸造应力,有时会产生冷裂纹,刚性结构的铸件,由于其结构的阻碍,温度降低导致的收缩应力容易使铸件产生冷裂纹,薄壁大芯、壁薄均匀的铸件非常容易产生冷裂纹;2.浇冒口系统设计不合理,对于壁厚不均匀的铸件,如果内浇口设置在铸件的厚壁部分时,将使铸件厚壁部分的冷却速度更加缓慢,导致或加剧铸件各部分冷却速度的差别,增大了铸造热应力,容易使铸件产生冷裂纹,浇冒口位置设计不当时,也会直接阻碍铸件收缩,使铸件容易产生冷裂纹;3.型砂或型芯的强度太高,高温退让性差,或舂砂过紧,使铸件收缩受到阻碍,产生很大的拉应力,导致铸件产生冷裂纹;4.钢的化学成分不合格,有害元素磷含量过高,使钢的冷脆性增加,容易产生冷裂纹5.铸件开箱过早,落砂温度过高,或者在清砂时受到碰撞、挤压等都会引起铸件的开裂。
铸坯表面缺陷成因及对策

总热阻RT可表示为:
RT=R1+R2+R3+R4+R5+R6
R1:钢水-坯壳间的热阻, cm2℃/W 。
R2:通过坯壳的热阻, cm2℃/W ;
R3:通过保护渣膜的热阻, cm2℃/W ;
R4:通过气隙的热阻, cm2℃/W ;
R5:通过结晶器铜板的热阻, cm2℃/W ;
R6:结晶器壁-冷却水间的热阻,cm2℃/W;
t=0,0 x x1, Tp=Tp0
(3)
t=0, x1 x x2, Ts=Ts0
(4)
t 0, x=0, Tp=f(t)
(5)
0 t t1,x=x1,Ts=Tp
ks(s/x)=kp(p/x)
(6)
t1 t,x=x1,
ks(s/x)=kp(p/x)
= ((Ts/100)4- Tp/100)4)+h(Ts-Tp) (7)
22
纵裂纹在铸坯表面凹陷处形成
漏钢遗留坯壳厚度沿宽度方向的变化
23
铸坯纵裂纹长度与深度的对应关系
24
铸坯表层缺陷示意图
25
纵裂纹是在结晶器内产生的
纵裂纹开口表面光滑, 呈沿柱状晶低熔点晶界 开裂迹象。
粗大纵裂纹表面附近断口照片
裂纹开口表面覆盖有 液态保护渣膜。
26
粗大纵裂纹距表面一定距离处断口
凝固坯壳厚度的不均匀性与碳含量的关系 43
不均匀凝固随冷却速率的增加而提高
住友金属杉谷泰夫等的实验:
铁と钢,67(1981),1508
44
杉谷实验得到的不同冷却速率下坯壳形貌
45
不同厚度钢板侧凝固坯壳的照片
46
坯壳不均匀与凝固速率的关系
凝固定律: d=kt1/2
连铸坯的缺陷及控制

二冷段和末端区的电磁搅拌可有效抑制枝晶搭桥形成封闭 的液窝。
连铸主要工艺参数
① 拉坯速度及其控制 ② 铸坯的冷却(结晶器冷却、二次冷却)
连铸坯的内部凝固是在出结晶器后进行的,后继的二次水冷、 弯曲矫直等直接影响内部质量。
连铸坯的缺陷及控制
提高连铸坯内部质量的工艺措施:
① 控制二冷段的传热,使铸坯均匀凝固,提高等轴晶率; 偏析、缩孔、缩松
② 降低浇钢的过热度; ③ 使用性能好的保护渣,防止钢水二次氧化和污染; ④ 控制拉速,保证连铸机正常运行; ⑤ 电磁搅拌(二冷段和末端区)。 偏析、缩孔、缩松
连铸坯的缺陷及控制
提高连铸坯表面质量的工艺措施:
① 控制结晶器的传热,使初凝固壳均匀; 裂纹、凹陷
② 控制结晶器的振动;
振痕、横裂纹
③ 使用性能好的保护渣;
气孔、夹杂
④ 优化结晶器结构;
倒锥角度,弧形壁
⑤ 电磁搅拌;
气孔、夹杂
⑥ 软接触电磁连铸。
振痕、裂纹
电磁搅拌的部位:
结晶器电磁搅拌:
(1)借助旋转电磁场使连铸 机结晶器内的金属液产生平 面旋转,去除杂质、气体。
结晶器电磁搅拌:
(2)扩大等轴晶区改善宏观 偏析,减少粗大柱状晶区 。
软接触电磁连铸:
软接触电磁连铸:
(1)减轻结晶器振动对弯月 面的影响,液态渣膜连续均 匀。
软接触电磁连铸:
(2)减小初凝壳对结晶器的 连铸坯的内部缺陷
裂纹 气孔 夹杂 缩孔、缩松 成分偏析
连铸坯的缺陷及控制
连铸坯的缺陷及控制
1. 连铸坯的表面缺陷
裂纹 气孔 夹杂 振痕、凹陷 成分偏析
连铸坯的缺陷及控制
1. 连铸坯的表面缺陷
灰铸铁件损伤、冷裂、温裂、变形、金相不合格、过硬六大缺陷的防止方法

灰铸铁件损伤、冷裂、温裂、变形、金相不合格、过硬六大缺陷的防止方法灰铸铁件由于落砂清理、热处理时造成的主要缺陷及其原因分析与防止方法(1)损伤特征及发现方法:损坏了铸件的完整性用外观检查可以发现原因分析:1.在开箱、搬运或清理时不注意2.打浇、冒口的方向不对或冒口颈过大,造成带肉缺陷防止方法:1.认真按照工艺规程和要求操作2.正确掌握打浇、冒口的方向(2)冷裂特征及发现方法:1.薄壳零件落砂时被振裂,并违反操作规程2.采用水爆清砂时,热应力较大,当应力超过铸件某部分的抗拉强度时,应生冷裂防止方法:1.对易裂的薄壳零件,清理时应挑出,另行清理,并认真执行合理的操作规程2.根据铸件结构和性能特点,选用合理的清理方式和清理工其3.严格执行水爆工艺4.在运输和清理过程中,尽量减轻碰撞(3)温裂特征及发现方法:开裂处金属表皮氧化用外观检查,透光法,磁力探伤,打压试验,煤油渗透等方法发现原因分析:由于气割、焊接或热处理不当,温度应力大所引起防止方法:正确制订并认真执行合理的焊接、热处理规范和操作规程(4)变形特征及发现方法:长的或扁平类铸件在靠近壁厚的一方凹入成弯曲形用外观检查,划线等方法发现原因分析:在铸件冷却过程中,产生的铸造应力超过该材质的屈服极限时,则产生塑性变形和挠曲为减少和消除铸件的残留应力,可采用人工时效(即退火热处理),若热处理规范不正确,仍会产生变形和挠曲防止方法:1.改变热处理规范,使其合理,并认真执行2.延长开箱时间或把刚落砂的铸件送入保温炉中保温,并随炉缓慢冷却(5)金相不合格特征及发现方法:铸件断面的粗视组织和显微组织不符合标准或技术条件用断面观察,金相检验可以发现原因分析:1.开箱时间不当2.热处理规范不正确防止方法:1.按技术要求,合理控制铸件的开箱时间2.改变热处理规范,使其合理,并认真执行(6)过硬特征及发现方法:在铸件边缘和薄璧处出现白口铁组织断面观察,硬度试验,机械加工可以发现原因分析:开箱时间过早防止方法:适当延长开箱时间或在退火炉中缓慢降温。
分析铸造热裂缺陷形成的机理及改进措施

分析铸造热裂缺陷形成的机理及改进措施铸造热裂缺陷是铸造过程中常见的一种缺陷,它对铸件的质量和性能产生严重的影响。
了解和分析铸造热裂缺陷形成的机理,并采取适当的改进措施,对于提高铸件的质量和性能具有重要意义。
一、铸造热裂缺陷的机理分析铸造热裂缺陷的形成主要与铸造过程中的温度变化和应力积累有关。
具体的机理可以从以下几个方面进行分析:1. 温度梯度引起的热应力在铸造过程中,液态金属流注入型腔中后,由于型腔的温度梯度不均匀,会导致金属在冷却过程中产生温度梯度,从而引起不均匀的热收缩和热应力的积累。
当应力达到材料的承载极限时,就会发生裂纹的形成。
2. 金属的热固性和热收缩不匹配不同金属具有不同的热膨胀系数和热收缩系数,当金属与型腔或其他部件接触时,由于温度变化而引起的热收缩不匹配,也会导致热应力的产生。
3. 相变引起的应力集中在铸造过程中,液态金属在冷却过程中会发生相变,如固态化、固相转变等。
这些相变对金属的体积变化和应力产生有着重要影响。
当相变速率较快时,容易引起应力集中,从而形成裂纹。
二、改进措施为了减少铸造热裂缺陷的发生,可以采取以下改进措施:1. 控制铸造温度和温度梯度合理控制铸造过程中的温度和温度梯度对于减少热应力的产生具有重要作用。
可以通过调整浇注温度、冷却速度等参数来控制温度梯度的变化,减少热应力的积累。
2. 选择合适的金属材料选择具有匹配热膨胀系数和热收缩系数的金属材料,可以减少热收缩不匹配引起的应力积累。
同时,还应选择具有较好耐热性能的材料,以降低温度梯度引起的热应力。
3. 优化铸造工艺合理设计铸造工艺,采用预热、降温等措施,可以有效降低热应力的产生。
此外,还应注意避免温度梯度过大的情况,避免铸件过厚或形状复杂等导致热应力增加的问题。
4. 消除应力集中点铸造热裂缺陷的形成与应力集中有关,因此,要尽量消除或减少应力集中点。
对于已经存在的应力集中点,可以采取修补、改进设计等方式进行处理,以减少裂纹的产生。
连铸坯表面裂纹缺陷分析

《 中国重型装备》
C I A H A Y E UP N H N E V Q I ME T
从 图 4可 以看 出 , 轧 态 、 火 态 和 调 质 态 热 正 6 S2 n钢 8 0C亚温 淬 火 的 转 变 产物 为 马 氏体 0 iM 0 ̄
体延 伸形成 的三 角 区部 位 晶粒 明显要 比裂 纹的 另 侧 晶粒要 细 , 纹两侧 组织 不 同 , 明裂纹 两侧 裂 说
一
端存 在沿 奥 氏体 晶界 向基体 延 伸 的 现象 , 明横 说
裂是 沿 晶开裂 , 钢水 结 晶成 固体 以后 产生 的 , 是 是
一
形成 组织 的温度不 同。三角 区部位 晶粒 细说 明该
钢亚 温淬火 后韧性 好 、 度高 的原 因之一 。 强
双相合 金 中双 相 的形 态对 试样 的力学性 能有
影响 , 主要表 现 在 对 裂纹 扩 展 的 阻碍 作 用 上 。当
铁 素体 呈针状 时 , 氏体 被铁 素 体 最 大限 度 的分 马 开 , 裂纹 的扩展 不仅 通过 马氏体 , 故 还必然 通过 铁 素体 。铁素 体在 断裂前会 产生 大量 塑性变形 而 消
若铁 素体呈 块状 形 态 时 , 则裂 纹 容 易 只沿 着 马 氏 体基 体扩展 , 而不 与孤立 的铁 素体相 遇 , 从而 使试 样 的韧性变 差 。另外 , 素体 呈针状 、 氏体 为细 铁 马
小板条 状时 , 晶界 总面积 较块状 时要 大 的多 , 也有 利 于力学性 能 的提 高 。针状组 织 比颗 粒状组 织细 小 , 材料变 形 和断 裂 的过 程 中能 吸收 更 多 的能 在
耗较 多 能量 , 而 对 裂 纹 的 扩 展 起 到 阻碍 作 用 。 从
- 1、下载文档前请自行甄别文档内容的完整性,平台不提供额外的编辑、内容补充、找答案等附加服务。
- 2、"仅部分预览"的文档,不可在线预览部分如存在完整性等问题,可反馈申请退款(可完整预览的文档不适用该条件!)。
- 3、如文档侵犯您的权益,请联系客服反馈,我们会尽快为您处理(人工客服工作时间:9:00-18:30)。
关于对铸坯的冷却及裂纹缺陷分析
在铜液温度和铸造速度一定时,冷却强度对铸坯组织起决定性作用。
一般情况下,冷却速度小,有利于粗等轴晶和柱状晶的生长,当冷却速度较大时,则有利于细等轴晶和细柱状晶的生长。
冷却强度以锭坯拉出时表面呈暗红色不开裂为好。
一次水压过高会导致结晶区往炉口方向移动,易于拉裂;水压过低则容易拉漏。
二次冷却的作用是促进轴向凝固,使液穴浅而平,以获得致密的铸锭组织,二次冷却强度越大,液穴越浅平,越有利于轴向凝固,铸锭组织越致密。
1.浇铸温度紫铜熔点l 085℃。
紫铜生产多采用40—80℃的过热度或取液相点
1.05—1.1倍作为浇铸温度。
紫铜水平连铸的铸造温度应选择1 135—1 170℃
之间,铸造开始时将温度升高到上限有利于铜液粘结在引锭头上不会拉漏。
当
引锭头离开结晶器后打开二次冷却水。
立即加料降温,将浇铸温度控制在
1140℃为宜,并保持连续铸造过程温度稳定。
2.浇铸速度金属铜凝固时间其断面存在3个区域:固相区、凝固区、液相区,
许多缺陷都是在凝固区内形成,所以凝固区的宽度对管坯的质量影响很大,由
于不同的拉铸速度会改变铸锭断面的温度梯度大小,这是浇铸速度作为水平连
铸的一个重要工艺制度的主要原因。
由于不同拉速,其产生的液穴也不相同,
管坯的液穴深度与铸造速度成正比,随着铸造速度的增加,液穴深度加大,当
液穴深度过大时,管坯内部处于液态。
外表面管坯已进入一次冷却区域,大的
冷却强度使管坯处于强烈的线收缩状态。
根据铸造强度理论,紫铜在线收缩开
始温度到平衡固相点之间的有效结晶温度范围内,强度与塑性最低,在铸造应
力作用下产裂纹。
这就解释了在高铸造速度下容易产生管坯裂纹。
3.冷却强度冷却强度指管坯周围的介质(冷却水)在单位时间内导出的热量(传
热速度)。
冷却强度越大,管坯断面的温度梯度越大,管坯的凝固速度越快,
水平连铸管坯的冷却强度主要取决于冷却水的用量与水压。
由于管坯在结晶器
内的一次冷却导出总热量的15—20%,其余热量由二次冷却导出,一次冷却
作用使管坯成型并有足够厚度的凝壳能抵抗铜液的静压力、铸锭与结晶器间的
摩擦力和凝固的收缩力,使铸造管坯不会变形与开裂。
一次冷却水压高,液穴
深度随之增大,凝固过渡段向炉口方向移动有拉裂管坯的倾向,不利于提高铸
造管坯质量;一次冷却水压过小,过渡区向远离炉口方向移动容易拉漏。
二冷
可改善偏析但二冷强度的提高要以不产生回热型内裂和不恶化表面质量为
限。
关于裂纹:
1.表面横向裂纹发生在管体内外表面的裂纹,铜管表面产生凹陷,严重的凹陷
处管壁内表面发生裂纹,裂纹比较细小,多发生在脱型区段。
紫铜管坯的表面横
向裂纹主要是热裂纹,它是在凝固末期或终凝后不久管坯尚处于强度和塑性很低
状态下因管坯固态收缩受阻两弓起的。
它的断口严重氧化,无金属光泽,呈粗细
不均、曲折而不规则的曲线,长度在3—10 m/ft.,深度在2—5 mm之间。
避免
铸坯表面产生横向拉裂的主要工艺措施是:①结晶器、引锭托座都应放置水平,
而且二者中心应该对正。
防止偏心造成摩擦力加大,在凝壳的初期拉断管坯;②
适当降低拉坯速度。
使管坯凝壳厚度增加到可抵御横裂;③保护结晶器内熔体,
避免铜液氧化和造渣减少铜液面的温降;④当裂纹发生后,增加反推过程中停止
时间对限制裂纹的继续发展起到效果较好;⑤出现裂纹后改变铸造工艺,调整铸
造温度,调节冷却强度都能使裂纹发生变化,其中以改变浇铸工艺为最快;⑥生
产过程中发现有些裂纹具有一定的记忆性,即不论如何调整工艺参数只能改变裂
纹的位置无法根本消除。
此时可采用停止铸机升温至启铸温度重新铸造,这样可消除管坯裂纹的记忆性。
2.表面横向裂纹TP2铜管坯的表面横向裂纹主要是热裂纹,它是在凝固末期或终
凝后不久,管坯尚处于强度和塑性很低状态下,因管坯固态收缩受阻而引起的。
它的断口严重氧化,无金属光泽,呈粗细不均、曲折而不规则的曲线,长度在5~
15 mm,深度在1.0-2.5 mm,主要分布在管坯上半部,水平连铸过程中,由于
管坯外表面与结晶器石墨型内壁、管坯内表面与石墨芯之间有相对运动,因此在它们之间有摩擦阻力,而且管坯受到牵引力,如果管坯所受的摩擦阻力和牵引力的合力大于管坯凝固层的强度时,便会将管坯表面拉裂,这是造成横向裂纹的基本原因。
由于结晶器内部表面不光,或者变形,或者没有放置水平,或者未与引锭托座中心对正,均可使管坯表面产生横向拉裂现象。
另一方面,如果管坯表面不光,管坯表面有夹杂或偏析等存在时,或者管坯表面与石墨结晶器之间润滑不良时,也都可使管坯表面产生横向拉裂。
水平连续铸造中由于重力的作用,管坯表面受到的冷却不均匀,下半部冷却强度比上半部要好,所以下半部凝固层比上半部要厚,因此下半部凝固层强度比上半部要好,不容易拉裂,这就导致了表面横向裂纹主要分布在管坯上半部。
避免铸坯表面产生横向拉裂的主要工艺措施是:
①加强管坯与结晶器之间的润滑j在石墨型内壁覆盖涂层;②结晶器、引锭托座
都应放置水平,而且二者中心应该对正;③适当降低拉坯力;④保护结晶器内的熔体,避免铜液氧化和造渣,减少铜液面的温降;⑤调节一次冷却水流量使管坯表面冷却均匀。
3.内部裂纹内部裂纹铸坯发生内部裂纹的根本原因,除了与TP2铜自身的热
脆性质有关外,主要是由于管坯表面和内部温差大,且所产生的热应力大于内部TP2铜的强度所造成的。
TP2铜管坯内部裂纹的发生主要取决于两个条件:一是存在于管坯内部的应力大小,一个是有应力存在的管坯内部TP2铜的强度高低。
应力的大小主要是由管坯凝固时的收缩量和其表面与内部的温差大小所决定的。
TP2铜管坯的化学成分和断面尺寸都是一定的,因此应力的大小主要由管坯表面和内部的温差大小决定。
因此提高铸造温度,或加快铸造速度、增大冷却强度等,都会使管坯的表面和内部温差增大,使管坯中的应力增大;管坯内部TP2铜的强度高低,除与管坯的化学成分和温度有关外,还与实际的结晶组织、缺陷分布情况等因素有关。
因此当管坯内部某处的应力强度大于该处TP2铜的强度时,就会出现内部裂纹。
为了避免管坯内部发生裂纹,可采取以下措施:①严格控制TP2铜的化学成分,避免化学成分达到偏析临界值;②降低铸造温度;③减小冷却强度;④减慢铸造速度。
沙漠野狼
2012年06月25日。