注塑成型技术简介
塑料成型技术现状与发展

塑料成型技术现状与发展塑料成型技术是一种将塑料原料通过一系列加工工艺,加热、压力等作用下,使其变形成为所需形状的方法。
随着塑料在工业生产和日常生活中的广泛应用,塑料成型技术也得到了快速发展。
本文将从塑料成型技术的现状与发展两个方面进行探讨。
一、塑料成型技术的现状1.注塑成型技术注塑成型技术是目前最常用的塑料成型技术之一。
它通过将加热熔化的塑料原料注入模具中,经过冷却后得到所需的产品形状。
注塑成型技术具有生产效率高、成本低、产品精度高等优点,广泛应用于电子、汽车、家电等领域。
2.吹塑成型技术吹塑成型技术主要用于生产中空塑料制品,如瓶子、容器等。
它是将热塑性塑料颗粒加热熔化后注入到吹塑机的模具中,通过气压将塑料吹成所需的形状。
吹塑成型技术具有生产效率高、成本低、产品质量好等特点,被广泛应用于食品、化妆品等行业。
3.挤出成型技术挤出成型技术是将加热熔化的塑料原料通过螺杆挤出机挤出成型。
挤出成型技术可以生产出形状复杂的塑料制品,如管道、板材等。
挤出成型技术具有生产效率高、产品质量稳定、适用范围广等优点,在建筑、包装等领域得到了广泛应用。
二、塑料成型技术的发展1.高速成型技术高速成型技术是近年来发展起来的一种新型塑料成型技术。
它通过增加注塑机的射出速度和压力,缩短冷却时间,实现塑料制品的高速生产。
高速成型技术能够提高生产效率,降低生产成本,适用于大批量生产的需求。
2.微纳米成型技术随着微纳米科技的发展,微纳米成型技术逐渐应用于塑料制品的生产。
微纳米成型技术可以制造出微小尺寸的塑料制品,如微型零件、微流控芯片等。
微纳米成型技术具有高精度、高灵活性等特点,有望在医疗、电子等领域得到更广泛的应用。
3.可持续发展成型技术随着环保意识的增强,可持续发展成型技术成为塑料成型技术的一个重要发展方向。
可持续发展成型技术主要包括生物降解塑料的应用、回收利用塑料原料等。
这些技术可以减少对环境的污染,提高资源利用率,符合可持续发展的要求。
塑料加工技术手册

塑料加工技术手册在现代工业中,塑料材料已经成为最为常用的材料之一。
在各类机械设备、家电产品和日常用品中,塑料制品随处可见。
因此,提高塑料加工技术已经成为了现代工业发展的一个重要方向。
本文将详细介绍塑料加工的各种方法和技术。
一、注塑成型技术注塑成型技术是目前最为常用的塑料加工方式之一。
这种方式是通过将熔化的塑料材料注入成型模具中,经过冷却硬化后取出成品。
注塑成型技术能够制造出各种形状和大小不同的产品,而且生产效率高,生产周期短。
注塑成型技术在生产中的应用非常广泛。
在汽车零部件、家电产品、玩具制品等领域,注塑成型技术都有着广泛的应用。
二、吹塑成型技术吹塑成型技术是一种利用空气压力将加热的塑料材料吹成型的加工方式。
这种方法主要用于生产中空体和薄壁体的产品,如瓶子、容器、桶等。
吹塑成型技术生产产品的周期较短,而且能够大量生产符合要求的产品。
同时,吹塑成型技术能够制造出形状规则、壁薄、重量轻、透明度高的产品。
三、挤出成型技术挤出成型技术是将塑料材料推入挤出机中,经过熔化和加工后,通过模头挤出制成成品的加工方式。
挤出成型技术广泛应用于生产各种管材、棒材、板材以及各类异型材料等。
挤出成型技术的特点是可以生产出连续性的成型产品,而且产品尺寸可以根据需要进行调整。
挤出成型技术的应用范围非常广泛,在建筑、自行车、包装等行业都有着广泛的应用。
四、热熔焊接技术热熔焊接技术是指将两个或多个物体通过加热使它们的接触表面部分熔化,然后冷却成型后制成焊接部分的过程。
对于塑料材料的加工和制造过程中,热熔焊接技术应用非常广泛,尤其是在各种管道和容器的制造和修复中更受重视。
通过热熔焊接技术可以对塑料材料进行加工和制造,从而制成符合工业要求和使用要求的塑料制品。
五、压延成型技术压延成型技术是指将加热的材料通过辊子的挤压和冷却制成各种板材状的制品的加工方式。
压延成型技术应用非常广泛,在建筑、家电以及日常用品制造的过程中都有着重要的作用。
注塑成型的工作原理

注塑成型的工作原理注塑成型是一种常见的塑料加工技术,通过将熔化的塑料注入模具中,并在固化后得到所需形状的制品。
本文将详细介绍注塑成型的工作原理,并探讨其具体步骤及相关特点。
一、工作原理注塑成型的工作原理基于热塑性塑料的特点,其主要包括以下几个步骤:1. 塑料熔化:首先,将塑料颗粒加入注射机的料斗中。
然后,通过外加热源,调节注射机的温度,使塑料颗粒迅速熔化成为黏稠的熔融塑料。
2. 注射:在塑料熔化的同时,注射机会将熔融塑料注入模具中。
注射机通过螺杆运动,将熔融塑料推动到注射筒前端,并通过喷嘴进入模具的腔体。
3. 塑料充填:一旦熔融塑料进入模具腔体,它会填充整个腔体,包括模具中所定义的产品形状。
在此过程中,注射机保持一定的压力,以确保塑料充分填充模具。
4. 塑料固化:一旦塑料充填完成,它会开始在模具中逐渐冷却,并渐渐固化。
注射机会保持模具一定的冷却时间,以确保塑料完全固化。
5. 产品脱模:当塑料完全固化后,模具会打开并释放成形的产品。
产品的脱模可以通过模具的自动弹出装置或人工操作实现。
释放后,可以开始进行下一次注射循环。
二、特点与优势注塑成型作为一种成熟的塑料加工技术,具有以下特点与优势:1. 精度高:注塑成型产品的尺寸精度高,可以满足不同行业的严格要求,如医疗器械、汽车零部件等。
2. 产品种类多样:注塑成型可以加工各种形状的产品,从小到大,从简单到复杂,包括零件、容器、玩具等。
3. 生产效率高:注塑成型具有高效连续生产的能力,可以快速完成成形循环,满足大批量生产的需求。
4. 自动化程度高:注塑成型设备智能化程度高,可以实现自动化操作,提高生产效率和产品质量。
5. 材料选择广泛:注塑成型可适用于热塑性塑料、热固性塑料和橡胶等材料,具有较广泛的应用范围。
三、应用领域注塑成型技术广泛应用于众多行业,例如:1. 汽车工业:注塑成型可制造汽车内部和外部的零部件,如仪表盘、门把手、保险杠等。
2. 电子电器:注塑成型可制造电子产品的外壳,如手机壳、电视遥控器等。
注塑技术文档
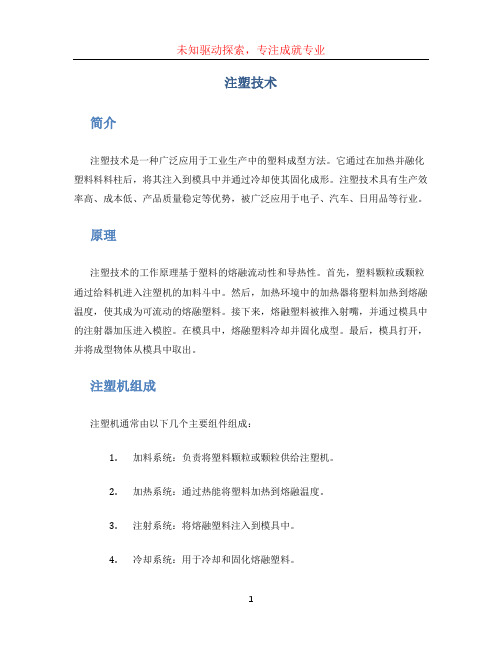
注塑技术简介注塑技术是一种广泛应用于工业生产中的塑料成型方法。
它通过在加热并融化塑料料料柱后,将其注入到模具中并通过冷却使其固化成形。
注塑技术具有生产效率高、成本低、产品质量稳定等优势,被广泛应用于电子、汽车、日用品等行业。
原理注塑技术的工作原理基于塑料的熔融流动性和导热性。
首先,塑料颗粒或颗粒通过给料机进入注塑机的加料斗中。
然后,加热环境中的加热器将塑料加热到熔融温度,使其成为可流动的熔融塑料。
接下来,熔融塑料被推入射嘴,并通过模具中的注射器加压进入模腔。
在模具中,熔融塑料冷却并固化成型。
最后,模具打开,并将成型物体从模具中取出。
注塑机组成注塑机通常由以下几个主要组件组成:1.加料系统:负责将塑料颗粒或颗粒供给注塑机。
2.加热系统:通过热能将塑料加热到熔融温度。
3.注射系统:将熔融塑料注入到模具中。
4.冷却系统:用于冷却和固化熔融塑料。
5.开模系统:用于模具的开合和成型产品的取出。
6.控制系统:控制整个注塑过程的参数和运行状态。
模具设计模具设计是注塑技术中至关重要的一环。
一个好的模具设计可以确保成型产品的质量和稳定性。
以下是几个常见的模具设计要点:1.模腔设计:模腔的形状和尺寸直接影响成型产品的外观和尺寸精度。
模腔应具备充分的冷却系统以保证塑料能够均匀快速地冷却和固化。
2.料斗设计:料斗应具备合适的形状和尺寸,以确保塑料料柱能够顺利进入注射系统,避免塑料质量的变化。
3.喷嘴设计:喷嘴是将熔融塑料从注射系统推入模腔的关键部件。
喷嘴应具备合适的结构和材料,以确保塑料能够流畅地进入模腔,避免气泡和热焊接等缺陷。
4.冷却系统设计:模具的冷却系统直接影响到塑料的冷却速度和固化时间。
冷却系统应具备足够的冷却介质流通性,以确保模具各处温度均匀。
注塑工艺控制注塑技术是一个复杂的加工过程,需要进行精确的工艺控制以获得高质量的成型产品。
以下是注塑工艺控制的几个关键参数:1.温度控制:注塑过程涉及到多个温度控制区域,如加热器、注射系统和冷却系统。
科学注塑成型技术讲解
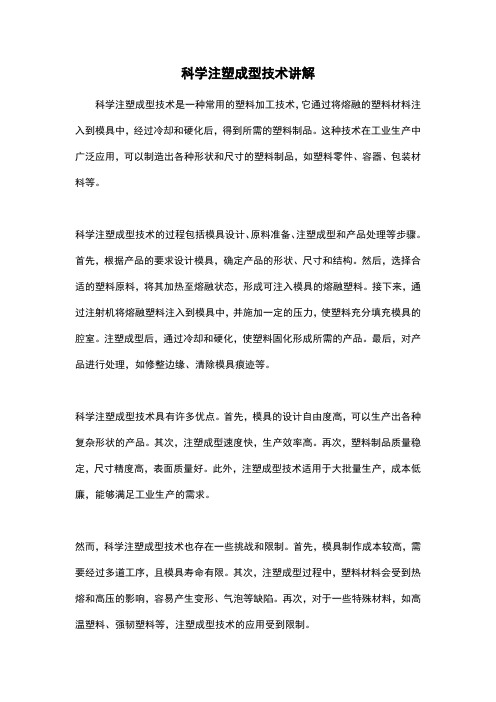
科学注塑成型技术讲解
科学注塑成型技术是一种常用的塑料加工技术,它通过将熔融的塑料材料注入到模具中,经过冷却和硬化后,得到所需的塑料制品。
这种技术在工业生产中广泛应用,可以制造出各种形状和尺寸的塑料制品,如塑料零件、容器、包装材料等。
科学注塑成型技术的过程包括模具设计、原料准备、注塑成型和产品处理等步骤。
首先,根据产品的要求设计模具,确定产品的形状、尺寸和结构。
然后,选择合适的塑料原料,将其加热至熔融状态,形成可注入模具的熔融塑料。
接下来,通过注射机将熔融塑料注入到模具中,并施加一定的压力,使塑料充分填充模具的腔室。
注塑成型后,通过冷却和硬化,使塑料固化形成所需的产品。
最后,对产品进行处理,如修整边缘、清除模具痕迹等。
科学注塑成型技术具有许多优点。
首先,模具的设计自由度高,可以生产出各种复杂形状的产品。
其次,注塑成型速度快,生产效率高。
再次,塑料制品质量稳定,尺寸精度高,表面质量好。
此外,注塑成型技术适用于大批量生产,成本低廉,能够满足工业生产的需求。
然而,科学注塑成型技术也存在一些挑战和限制。
首先,模具制作成本较高,需要经过多道工序,且模具寿命有限。
其次,注塑成型过程中,塑料材料会受到热熔和高压的影响,容易产生变形、气泡等缺陷。
再次,对于一些特殊材料,如高温塑料、强韧塑料等,注塑成型技术的应用受到限制。
总之,科学注塑成型技术是一种重要的塑料加工技术,能够满足各种工业生产需求。
随着科技的不断发展,注塑成型技术也在不断创新和改进,以提高产品质量和生产效率。
相信在未来的发展中,科学注塑成型技术将会得到更广泛的应用。
纳米注塑成型技术介绍
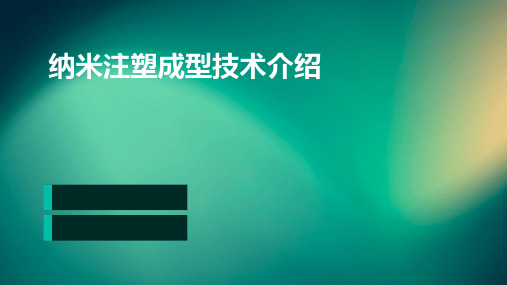
技术掌握难度高
该技术需要较高的技术 水平和经验,对操作人
员的技能要求较高。
材料选择受限
某些特殊材料在纳米注塑成 型过程中可能会出现流动不
均、填充困难等问题。
环境保护问题
在生产过程中可能产生 废料和有害物质,需要 采取相应的环保措施。
解决方案与应对策略
加强研发与培训
通过研发和技术培训,提高操作人员的技能 水平,降低技术掌握难度。
医疗领域
用于制造医疗器械和植入物等, 如人工关节、牙套等,提高产品
的生物相容性和机械性能。
Байду номын сангаас
02 纳米注塑成型技术发展历 程
起源与早期发展
起源
纳米注塑成型技术起源于20世纪90 年代,当时主要受到纳米材料和精密 注射成型技术的启发。
早期发展
在初期阶段,该技术主要关注于将纳 米粒子添加到传统塑料中以提高其性 能。
医疗器械制造
制造高精度、高性能的医 疗器械零部件,如人工关 节、牙科植入物等。
对环境和社会的影响
资源节约
纳米注塑成型技术能够实 现材料的高效利用,减少 浪费,有助于节约资源。
减少环境污染
通过优化注塑工艺,降低 废品率,减少废料对环境 的污染。
提高生产效率
纳米注塑成型技术能够提 高生产效率,降低生产成 本,有助于推动产业的发 展和进步。
THANKS FOR WATCHING
感谢您的观看
智能化控制技术
利用人工智能和机器学习技术,实 现注塑过程的智能控制和优化,提 高产品质量和生产效率。
产业应用前景
01
02
03
汽车制造业
利用纳米注塑成型技术制 造汽车零部件,提高零部 件性能、减轻重量、降低 成本。
05节-注塑压缩成型工艺简介

第五节注射压缩成型工艺简介一、注射压缩成型(ICM)的定义:注射压缩成型(injection compression moulding/简称ICM)是传统注塑和压缩模塑的组合成型技术,又叫二次合模注射成型。
这种成型工艺原是为了成型光学透镜而开发的。
众所周知,光学透镜对其几何精度要求非常高、既要尺寸准确,又要求变形小,而一般注射成型就难以达到此要求。
二、注射压缩成型的工作原理:在一般传统注射成型过程之外加入模具压缩的过程,即在填充之初模具不完全闭合(留有0.2㎜左右,视产品结构定),将部分熔融塑料(体积约占型腔60%-75%间,具体按产品与模具设计定)注入型腔后;再利用锁模机构闭合模具,向型腔内熔料施加压力,压缩熔体,直至完成型腔充填。
它要经过注塑和压缩两个阶段。
成型时,模具先未完成闭合,由于模具型芯部分设有台阶,当熔体被注入型腔后不会泄溢,当熔体注射完毕后,由专设的闭模活塞进行第二次合模,熔体被铺平压实。
下图所示为注射压缩成型过程:1.模具初次闭合:这时并不是将动、定模完全闭合,而是留有0.2mm左右的间隙;2.注射熔体:随之计量精确的熔料注射入模腔,由于模具的型芯部分设有台阶,虽然模具尚未闭合,但型腔中的熔料也不会泄漏。
3.压缩成型:当螺杆前移达到注射所预定的位置时,即向合模装置发出第二次合模信号,由专用的闭模活塞实施第二次合模,合模装置随后立即增大锁模力并推动动模前进,将动、定模板完全合拢,这时模腔中的熔料即在动模的压缩作用下取得型腔的精确形状。
需要注意的是:塑件固化后,必须在闭模活塞对模具的压力消失后,才可进行开模和顶出塑件,所以,注射压缩成型的注塑机必须有专用闭模液压缸。
图1所示三、注射压缩成型的优点:比起传统的射出成型,射出压缩成型具有以下优点:1.减少熔体分子取向,降低塑件的残余应力,降低应力偏析;2.改善产品变形,使产品有很高精度;故特别适合要求高度透明、且变形小的光学塑料制品成型,如光学镜片及医疗生物芯片等。
注塑技术培训资料
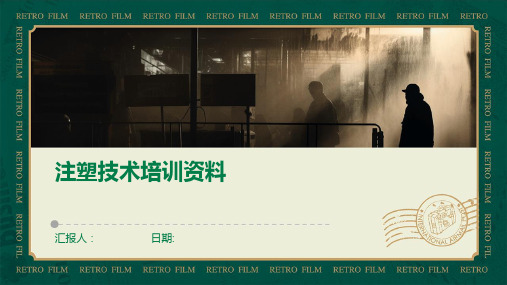
成型过程中的注意事项及维护保养方法
温度控制 压力调整 循环时间控制 维护保养
注塑过程中需严格控制模具和原材料的温度,以获得最佳的成 型效果。同时,定期检查加热元件、冷却系统等是否正常工作
。
根据产品需求和模具结构,合理调整注射压力、保压压力等参 数,以保证注塑件的质量和稳定性。
优化注射、保压、冷却等环节的时间,以提高生产效率。
操作步骤
根据生产计划,准备好原料、模具和 机器,调整注射成型参数,进行生产 。
注射压力、注射速度、保压时间等参数的设置与调整
01
02
03
注射压力
根据产品大小和模具情况 设定适当的注射压力,一 般不超过1500bar。
注射速度
根据产品厚度和模具结构 设定适当的注射速度,一 般不超过150mm/s。
保压时间
定期对注塑机、模具等设备进行保养,包括润滑、清洁、紧固 等措施,以延长设备的使用寿命。
成型后的产品检验及质量评估方法
外观检测
尺寸检测
观察注塑件是否有气孔、缩孔、流痕等缺 陷,以及尺寸是否符合要求。
使用测量工具对注塑件的尺寸进行精确测 量,包括长度、宽度、高度等参数。
性能测试
质量评估
根据产品需求,对注塑件进行相应的性能 测试,如耐温性、耐冲击性、耐磨损性等 。
具有较好的强度和耐冲击 性,适用于机械零件和家 电制品等领域。
塑料的收缩率及影响因素
塑料的收缩率
塑料制品的收缩率是指其尺寸在熔融状态下与冷却后的差异,不同的塑料品种和 加工条件下的收缩率会有所不同。
收缩率的影响因素
塑料的收缩率主要受到其结晶度、分子量、添加剂和加工条件等因素的影响。
选材原则及注意事项
由于冷却不均匀或其他因素,可 能导致成型件变形。解决方法是 优化冷却系统设计和成型条件,
- 1、下载文档前请自行甄别文档内容的完整性,平台不提供额外的编辑、内容补充、找答案等附加服务。
- 2、"仅部分预览"的文档,不可在线预览部分如存在完整性等问题,可反馈申请退款(可完整预览的文档不适用该条件!)。
- 3、如文档侵犯您的权益,请联系客服反馈,我们会尽快为您处理(人工客服工作时间:9:00-18:30)。
成型收缩率 0.2~0.6% 0.4~0.8% 0.2~0.6% 0.2~0.8% 1.5~5% 1.5~5% 0.8~2.5% 1~5% 0.1~0.4% 0.7~2% 0.6~0.8% 0.6~2% 0.7~0.8% 0.6~2% 0.2~0.7% 0.70% 1~2% 0.5~2%
5
射出压力
500~1000kg/cm2 500~1500kg/cm2 700~1500kg/cm2 700~1500kg/cm2 300~1000kg/cm2 300~1500kg/cm2 400~1500kg/cm2 600~1500kg/cm2 900~1500kg/cm2 600~1500kg/cm2 1000~1500kg/cm2 500~1500kg/cm2 1200~1300kg/cm2 500~1400kg/cm2 700~900kg/cm2 700~2000kg/cm2 700~1400kg/cm2 300~1200kg/cm2
塑料名称 干燥温度 干燥时间
ABS PS PE PP
PVC PMMA
PA PC POM MPPO PBT R-PET PPS
80℃~ 70~80℃ 60~80℃ 60~80℃ 60~70℃ 80~90℃
80℃~ 120~℃ 80~℃ 80~100℃ 130℃~ 130~℃ 130~180℃
2hr~ 1~2hr 1~2hr 1~2hr 1~2hr 3hr~ 4~6hr 2~4hr 2hr~ 2~4hr 3~42hr 4~5hr 1~3hr
初期水分
0.2~0.4% 0.1~0.2% 0.1~0.2% 0.1~0.2% 0.1~0.2% 0.2~0.4% 0.5~2.0% 0.1~0.2% 0.2~0.4%
0.1%~ 0.2~0.4% 0.2~0.4% 0.1~0.2%
适合水 分
0.07% 0.07% 0.07% 0.07% 0.07% 0.07% 0.10% 0.02% 0.02% 0.02% 0.02% 0.02% 0.05%
热风
○ ※ ※ ※ ※ ○ × ○ ○ ○ ○ □ ※
除湿 ※
※ ※ ※ ※ ※ ※ ※
注: ※最佳;○可接受By;Eric □Guo 尽量避免;×不好
4
原料的使用参数
料别 PA ABS AS PMMA LDPE HDPE PP 软PVC 硬PVC EVA PC POM 改生PPO PA CA PSF PET PBT
适当模温 40~60℃ 50~70℃ 50~70℃ 59~80℃ 35~65℃ 40~70℃ 20~80℃ 50~70℃ 50~70℃ 20~55℃ 80~120℃ 80~120℃ 60~100℃ 20~90℃ 20~80℃ 90~165℃ 50~150℃ 60~70℃
料筒温度 160~260℃ 190~260℃ 170~290℃ 180~260℃ 140~300℃ 150~300℃ 180~300℃ 150~190℃ 150~190℃ 120~200℃ 260~320℃ 190~240℃ 260~280℃ 220~285℃ 170~265℃ 330~420℃ 290~315℃ 230~270℃
2004/6/20
何谓塑料的「收缩率」?
收缩率系指塑料制品冷却固化经脱模成形后,其尺 寸与原模具尺寸间之误差百分比。在塑料模具设计 时,须先考虑收缩率,以免造成成品尺寸的误差, 导致成品不良。
6
2004/6/20
何谓塑料的「结晶性」
塑料之构造是由许多线状、细长之高分子化合物组成的集合体, 依分子成正规排列的程度,称为结晶化程度(结晶度),而结晶 化程度可用x线的反射来量测。有机化合物的构造复杂,塑料构造 更复杂,且分子链的构造(线状、毛球状、折迭状、螺旋状等) 多变化,致其构造亦因成形条件不同而有很大的变化。结晶度大 的塑料为结晶性塑料,分子间的引力易相互作用,而成为强韧的 塑料。为了要结晶化及规则的正确排列,故体积变小,成形收缩 率及热膨胀率变大。因此,若结晶性越高,则透明性越差,但强 度越大。
7
2004/6/20
何谓塑料的「MI」值?
MI的全名为「熔液流动指数」(Melt Flow Index),简称「熔融指数」 (Melt Index),是一种表示塑料材料加工时流动性的数值。它是美 国量测标准协会(ASTM)根据美国杜邦公司(Du Pont)惯用的鉴定塑 料特性之方法制定而成,其测试方法是使塑料粒在一定时间(10 分钟)内,一定温度及压力(各种材料标准不同)下,融化之塑 料流体,通过一直径2.1mm圆管所流出之克数。其值越大,表示 此塑料材料之加工流动性越佳,反之则越差。最常使用之测试标 准为ASTM D 1238,该测试标准的量测仪器-熔液指数计(Melt Indexer)的结构如下:将待测高分子(塑料)原料置入小槽中,槽 末接有细管,细管直径为2.095mm,管长度为8mm。加温至某温 度后,原料上端藉由活塞施加某一定重量向下压挤,量测该原料 在10分钟内所被挤出的重量,即为该塑料的流动指数。所以有时 您会看到如下的表示法25g / 10min,清楚的表示其MI为25,且是 在10分钟内挤出25g之意。一般常用的塑料其MI值大约介于1~25 之间,MI愈大,代表该塑料原料黏度愈小及分子重量愈小。而MI 愈小,代表该塑料黏度愈大及分子重量愈大。
结晶性塑料有明显熔点(Tm),固体时分子呈规则排列,强度较强, 拉力也较强。熔解时比容积变化大,固化后较易收缩,内应力不 易释放出来,成品不透明,成形中散热慢,冷模生产之日后收缩 较大,热模生产之日后收缩较小。相对于结晶性塑料,另有一种 为非结晶性塑料,其无明显熔点,固体时分子呈不规则排列,熔 解时比容积变化不大,固化后不易收缩,成品透明性佳,料温越 高色泽越黄,成形中散热快,以下针对两者物性进行比较。
注塑成型技术简介
包括主要的项目
原料 机器 模具。 辅助设备 热水冷水机,温控器,油压机,天
车,机械手,传送带,干燥机,混料机。 空压机,水塔。
2
2004/6/20
常见的塑料原料
ABS TPU TPE PMMA
PC
PBT PET PSF
PP
AS(SAN) PE
PSPVC
POM PA PC+ABS
PPO PPS PTFE LCP
分类:结晶性,非结晶性,热塑性弹性体
2004/6/20
原料的干燥
成型加工前,塑胶必须被充分的干燥。含有水分的材料进入模腔后,会 使制件的表 面出现银绦状的瑕斑,甚至会在高温时发生加水分解的现象, 致使材质劣化。因此在成型加 工前一定要对材料进行预处理,使得材料 能保持合适的水分。