模具设计中的冷却系统设计与优化分析
注塑模冷却系统设计原则及结构形式
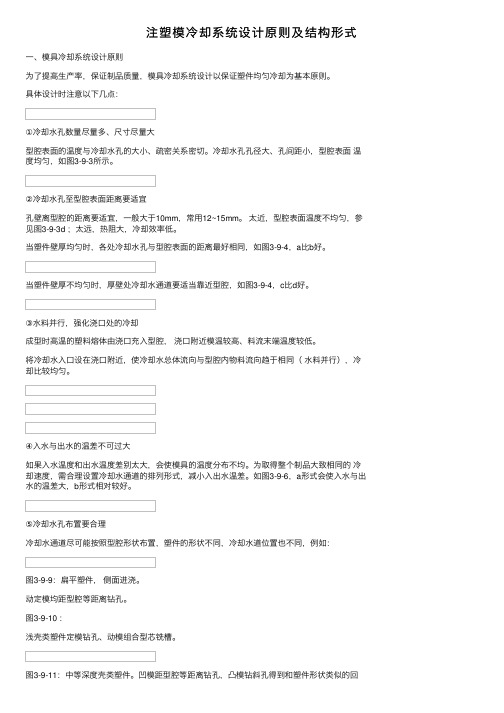
注塑模冷却系统设计原则及结构形式⼀、模具冷却系统设计原则为了提⾼⽣产率,保证制品质量,模具冷却系统设计以保证塑件均匀冷却为基本原则。
具体设计时注意以下⼏点:①冷却⽔孔数量尽量多、尺⼨尽量⼤型腔表⾯的温度与冷却⽔孔的⼤⼩、疏密关系密切。
冷却⽔孔孔径⼤、孔间距⼩,型腔表⾯温度均匀,如图3-9-3所⽰。
②冷却⽔孔⾄型腔表⾯距离要适宜孔壁离型腔的距离要适宜,⼀般⼤于10mm,常⽤12~15mm。
太近,型腔表⾯温度不均匀,参见图3-9-3d ;太远,热阻⼤,冷却效率低。
当塑件壁厚均匀时,各处冷却⽔孔与型腔表⾯的距离最好相同,如图3-9-4,a⽐b好。
当塑件壁厚不均匀时,厚壁处冷却⽔通道要适当靠近型腔,如图3-9-4,c⽐d好。
③⽔料并⾏,强化浇⼝处的冷却成型时⾼温的塑料熔体由浇⼝充⼊型腔,浇⼝附近模温较⾼、料流末端温度较低。
将冷却⽔⼊⼝设在浇⼝附近,使冷却⽔总体流向与型腔内物料流向趋于相同(⽔料并⾏),冷却⽐较均匀。
④⼊⽔与出⽔的温差不可过⼤如果⼊⽔温度和出⽔温度差别太⼤,会使模具的温度分布不均。
为取得整个制品⼤致相同的冷却速度,需合理设置冷却⽔通道的排列形式,减⼩⼊出⽔温差。
如图3-9-6,a形式会使⼊⽔与出⽔的温差⼤,b形式相对较好。
⑤冷却⽔孔布置要合理冷却⽔通道尽可能按照型腔形状布置,塑件的形状不同,冷却⽔道位置也不同,例如:图3-9-9:扁平塑件,侧⾯进浇。
动定模均距型腔等距离钻孔。
图3-9-10 :浅壳类塑件定模钻孔、动模组合型芯铣槽。
图3-9-11:中等深度壳类塑件。
凹模距型腔等距离钻孔,凸模钻斜孔得到和塑件形状类似的回路。
图3.9 1:深腔制品。
凸凹模均采⽤组合式,车螺旋槽冷却,从中⼼进⽔,在端⾯(浇⼝处)冷却后沿环绕成型零件的螺旋形⽔道顺序流出模具。
⑥冷却⽔道要便于加⼯装配冷却⽔道结构设计必须注意其加⼯⼯艺性,要易于加⼯制造,尽量采⽤钻孔等简单加⼯⼯艺。
对于镶装组合式冷却⽔道还要注意⽔路密封,防⽌冷却⽔漏⼊型腔造成型腔锈蚀。
模具冷却系统设计

家用电器模具冷却系统设计案例
散热器设计
家用电器模具的散热器 设计需考虑散热面积、 散热翅片间距和散热翅 片形状等因素,以提高 散热效率。
循环水道
家用电器模具的冷却系 统通常采用循环水道, 以确保冷却液能够持续 不断地流过模具表面, 带走热量。
控制系统
家用电器模具的控制系 统需具备温度控制、时 间控制和压力控制等功 能,以确保模具温度的 稳定和冷却液的循环。
05
模具冷却系统应用案例
汽车模具冷却系统设计案例
冷却水道设计
汽车模具冷却系统中的水道设计需根据模具的形状和大小进行定制, 以确保冷却液能够均匀地流过模具表面,提高冷却效果。
高效换热器
为了快速将热量从模具中带走,汽车模具冷却系统通常采用高效换 热器,如板式换热器或翅片式换热器。
控制系统
汽车模具冷却系统的控制系统需具备温度控制、流量控制和压力控制 等功能,以确保模具温度的稳定和冷却液的循环。
高生产效率。
降低能耗
选择高效的泵和风扇,以及合 适的冷却液,以降低系统能耗
。
03
模具冷却系统设计流程
确定设计目标
01
02
03
降低模具温度
通过冷却系统降低模具温 度,保证模具在连续工作 过程中温度稳定。
提高产品质量
通过控制模具温度,减少 产品成型过程中的收缩和 翘曲,提高产品尺铝等,以提高冷却效果。
加工性能
选择易于加工和制造的材料,如钢材、铝材等,以降低生产成本 和加工难度。
冷却水道加工工艺
铸造法
适用于大型模具的冷却水道加工,可以制作复杂形状的水道。
机械加工法
适用于小型模具的冷却水道加工,可以通过钻孔、铣削等机械加工 方式制作水道。
注塑模大赛模具冷却系统优化设计及分析

注塑模大赛模具冷却系统优化设计及分析引言在注塑模具制造行业中,模具冷却系统的设计和优化对于模具的使用寿命和产品质量有着非常重要的影响。
冷却系统的设计不仅影响着产品的成型质量,还直接影响着生产效率和能耗。
对模具冷却系统进行优化设计和分析显得尤为重要。
本文将针对注塑模大赛中的模具冷却系统进行优化设计及分析,从而提高模具的使用寿命和产品的质量。
一、冷却系统的现状分析目前在注塑模具制造中,常见的冷却系统包括水冷却和油冷却两种方式。
其中水冷却是较为常见的一种方式,它通过循环水冷却来降低模具的温度,从而提高产品的成型质量和生产效率。
目前存在着一些问题需要解决:1. 冷却水温度不稳定:冷却水温度的稳定性对于模具的使用寿命和产品质量具有非常重要的影响。
目前一些冷却系统存在水温波动较大的问题,需要进一步优化。
2. 冷却水流速不均匀:在模具结构复杂的情况下,冷却水的流速分布不均匀,导致部分部位的温度较高,影响了产品的成型质量。
3. 冷却系统能耗较高:传统的冷却系统中,水泵的能耗较高,提高了生产成本,需要降低能耗,并提高能源利用效率。
以上问题的存在,导致了模具的使用寿命短、生产效率低和能耗高的情况,需要进行优化设计和分析。
二、冷却系统的优化设计1. 优化冷却水供应系统:为了解决冷却水温度不稳定的问题,需要对冷却水供应系统进行优化设计。
可以考虑设置温控阀门及温度传感器,实现对冷却水温度的精确控制。
可以考虑增加水箱的容量,提高冷却水的储备量,从而提高冷却水的稳定性。
2. 优化冷却水流通路径:针对冷却水流速不均匀的问题,可以对模具内部的冷却水通道进行优化设计。
通过调整通道的结构和布局,实现冷却水的均匀流通,提高冷却效果。
可以考虑利用CAD/CAE技术进行模拟分析,优化冷却水通道的设计,从而提高冷却效果。
3. 优化冷却系统的能耗:为了降低冷却系统的能耗,可以考虑使用高效节能的水泵,并通过优化管道布局和阀门设置,降低系统的压力损失。
注塑成型工艺中的模具设计与优化

注塑成型工艺中的模具设计与优化一、引言随着全球化的发展和消费需求的不断增长,注塑成型工艺在生产制造中扮演着越来越重要的角色。
在注塑成型工艺中,模具设计与优化是关键环节,决定了产品质量、生产效率和生产成本。
本文将深入探讨注塑成型工艺中的模具设计与优化。
二、模具设计的基本原理1. 注塑成型工艺的基本流程注塑成型工艺是将熔化的塑料料施加于一定压力下充填到模具腔道中,经冷却硬化得到所需产品的过程。
基本流程包括注塑机料斗→注射装置→模具→冷却→开模→脱模→修整,所以模具的设计与优化必须充分考虑每个环节。
2. 模具设计的原则(1)合理的结构设计:模具结构应合理布局,便于加工和组装,以提高生产效率。
同时,需要考虑模具在使用过程中的稳定性和耐用性。
(2)充分考虑产品特性:模具设计时要充分考虑产品的特性,例如产品形状、尺寸、材料等,以确保产品的质量和性能。
(3)考虑冷却系统:冷却系统是模具设计的关键,直接影响产品的成型质量和生产效率。
冷却系统应具备良好的冷却效果,确保产品均匀冷却,并减少生产周期。
三、模具设计的优化方法1. 充分了解材料特性模具的设计与优化首先要充分了解材料的特性,包括熔点、流动性、尺寸稳定性等,以便在设计过程中选择合适的材料,并做出相应的调整和优化。
2. 仿真技术的应用利用计算机辅助设计(CAD)和计算机辅助工程(CAE)技术,进行模具设计的仿真分析。
通过仿真,可以模拟产品的充填、冷却和开模等过程,优化模具的结构和尺寸,提高产品的质量和生产效率。
3. 模具设计的标准化模具设计的标准化是改善模具设计质量和效率的重要手段。
建立规范化的设计流程和标准,提高设计效率和一致性,并减少设计的错误和修正。
四、模具设计的实践案例以汽车零部件为例,介绍一个模具设计的实践案例,以展示模具设计与优化的重要性。
汽车零部件的模具设计需要考虑到产品的形状复杂、尺寸精度高等特点。
在该案例中,设计团队利用CAD和CAE技术对模具进行了三维建模和仿真分析。
模具冷却系统设计意义

模具冷却系统设计意义在现代化工业生产中,模具冷却系统发挥着至关重要的作用。
本文将详细探讨模具冷却系统的设计意义,以及它在提高生产效率、保证产品质量方面所起到的重要职能。
一、什么是模具冷却系统?模具冷却系统是注塑模具、压铸模具等热加工模具中不可或缺的组成部分。
其主要功能是在模具内部循环冷却介质,通过吸收模具热量,达到控制模具温度、保证产品质量和提高生产效率的目的。
二、模具冷却系统设计意义1.提高生产效率在热加工过程中,模具温度过高会导致生产周期延长,降低生产效率。
通过设计合理的模具冷却系统,可以有效控制模具温度,使得生产周期缩短,提高生产效率。
2.保证产品质量模具温度对产品质量具有重要影响。
合理的模具冷却系统可以确保模具温度均匀分布,减少产品变形、应力集中等缺陷,从而提高产品质量。
3.延长模具寿命过高的模具温度会导致模具材料性能下降,加速模具磨损,降低模具寿命。
通过设计合理的模具冷却系统,可以有效降低模具温度,延长模具的使用寿命。
4.减少能源消耗在热加工过程中,合理的模具冷却系统可以降低能源消耗。
因为冷却系统可以快速将模具热量带走,减少了对加热设备的依赖,从而降低了能源消耗。
5.提高产品竞争力设计合理的模具冷却系统,可以使得产品质量更高、生产周期更短,从而提高产品竞争力。
三、模具冷却系统设计要点1.合理选择冷却介质:根据生产需求和模具材料,选择合适的冷却介质,如水、油、空气等。
2.确定冷却通道布局:根据模具结构和产品要求,合理布局冷却通道,确保模具温度均匀分布。
3.优化冷却系统参数:根据实际生产情况,调整冷却系统参数,如流量、压力等,以实现最佳冷却效果。
4.考虑模具材料热导率:不同模具材料的热导率不同,设计时要充分考虑这一点,以提高冷却效果。
5.重视冷却系统的维护:定期检查、清洗和更换冷却系统部件,确保冷却效果稳定。
总结:模具冷却系统设计在热加工行业中具有重要意义。
通过合理设计,可以降低模具温度、提高生产效率、保证产品质量、延长模具寿命,从而提高产品竞争力。
压铸模冷却系统设计

压铸模冷却系统设计模具温度是影响压铸件质量的一个重要因素,但在生产过程中往往未得到严格的控制。
大多数形状简单、成型工艺性好的压铸件对模具温度控制要求不高,模具温度在较大区间内变动仍能生产出合格的压铸件。
而生产形状复杂、质量要求高的压铸件时,则对模具温度有严格的要求,只有把模具温度控制在一个狭窄的温度区间内,才能生产出合格的压铸件。
因此,必须严格控制模具温度。
在一两个压铸循环中,模具型腔的温度要发生很大的变化。
铝合金压铸时,模具型腔温度上下波动可达300度左右。
使模具升温的热源,一是由金属液带入的热量:二是金属液充填型腔时消耗的一部分机械能转换变成热能。
模具在得到热量的同时也向周围空间散发热量,在模具表面喷涂的脱模剂挥发时也带走部分热量。
如果在单位时间内模具吸收的热量与散发的热量相等而达到一个平衡状态,则称为模具的热平衡。
模具的温度控制就是要把压铸模具在热平衡时的温度控制在模具的最佳温度区间内。
压铸生产中模具的温度由加热系统与冷却系统进行控制盒调节。
加热系统与冷却系统的主要作用:使压铸模达到较好的热平衡状态和改善压铸件顺序凝固条件:提高压铸件的内部质量和表面质量:稳定压铸件的尺寸精度:提高压铸生产的效率:降低模具热交应变力,提高压铸模使用寿命。
冷却系统的设计计压铸过程中,金属液在压铸模中凝固并冷却到顶出温度,释放的热量被模具吸收,同时模具通过辐射、导热和对流,将热量传出,在模具分型面上喷涂的分型剂挥发时也带走部分热量。
正常生产过程中传人模具的热量和从模具其中传出的热量应达到平衡。
在高效生产及大型厚壁铸件压铸时,往往要用强制冷却来保持模具的热平衡。
合理地设汁冷却系统对提高压铸生产效率,改善铸件质量及廷长模具使用寿命是十分重要的。
棋具冷却方法有:1)水冷水冷是在模具内设置冷却水通道,使冷却水通人模具带走热量。
水冷的效率高,易控制,是最常用的压铸摸冷却方法。
2)风冷对于压铸摸中难以用水冷却的部位,可采用风冷的方式。
注塑模冷却系统设计

注塑模冷却系统设计一、冷却系统原理冷却系统的设计原则包括以下几点:1.均匀冷却:冷却通道应布置得均匀,确保注塑模腔内的温度分布均匀,避免产生缺陷。
2.高效冷却:冷却通道应尽可能靠近模具表面,并减小冷却通道的截面积,以增加冷却介质对模具的冷却效果,提高生产效率。
3.多角度冷却:在模具中设置多个冷却通道,使冷却介质能够从不同的角度覆盖模具表面,提高冷却效果。
4.控制温度:通过合理设置冷却通道的长度、截面积和数量等参数,控制注塑模的冷却速度,确保产品达到理想的尺寸和性能。
二、冷却系统设计流程1.模具结构分析:根据产品的形状和尺寸,对模具进行结构分析,确定冷却通道的位置和数量。
2.冷却通道设计:根据模具结构,设计冷却通道的形状、截面积和长度等参数。
一般来说,冷却通道应尽量靠近模具表面,避免过于接近模腔导致冷却效果不佳。
3.冷却通道布置:根据模具结构和产品的需求,合理布置冷却通道的位置和数量。
通常情况下,冷却通道应均匀分布在模具的各个部位,并且覆盖整个模具表面。
4.冷却介质选型:选择合适的冷却介质,通常是冷水。
冷却介质的选择应考虑到模具材料的热导率、流动性以及生产环境等因素。
5.防止冷却死角:在冷却系统设计中,应尽量避免冷却死角的产生。
冷却死角是指冷却介质在注塑模内积聚,无法很好地冷却模具的局部区域。
为了避免冷却死角,可以设置细小的冷却通道或者采用多角度冷却。
三、冷却系统优化方面为了进一步提高冷却系统的效果,可以从以下几个方面进行优化:1.模腔温度分析:利用模具流动分析软件,对模腔的温度分布进行分析,找出温度较高或较低的区域,并针对性地调整冷却通道的布置。
2.冷却介质控制:通过对冷却介质的输送速度、温度和压力等参数进行控制,进一步提高冷却效果。
3.冷却材料选择:选择具有较好导热性能的冷却材料,如铜合金等,以提高冷却效果。
4.模具表面处理:在模具表面进行特殊处理,如磨削、喷砂等,增加表面的热传导性,提高冷却效果。
模具加热与冷却系统设计
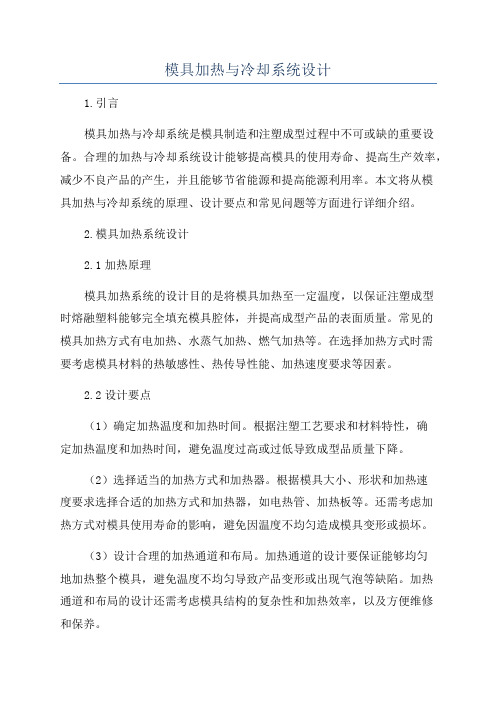
模具加热与冷却系统设计1.引言模具加热与冷却系统是模具制造和注塑成型过程中不可或缺的重要设备。
合理的加热与冷却系统设计能够提高模具的使用寿命、提高生产效率,减少不良产品的产生,并且能够节省能源和提高能源利用率。
本文将从模具加热与冷却系统的原理、设计要点和常见问题等方面进行详细介绍。
2.模具加热系统设计2.1加热原理模具加热系统的设计目的是将模具加热至一定温度,以保证注塑成型时熔融塑料能够完全填充模具腔体,并提高成型产品的表面质量。
常见的模具加热方式有电加热、水蒸气加热、燃气加热等。
在选择加热方式时需要考虑模具材料的热敏感性、热传导性能、加热速度要求等因素。
2.2设计要点(1)确定加热温度和加热时间。
根据注塑工艺要求和材料特性,确定加热温度和加热时间,避免温度过高或过低导致成型品质量下降。
(2)选择适当的加热方式和加热器。
根据模具大小、形状和加热速度要求选择合适的加热方式和加热器,如电热管、加热板等。
还需考虑加热方式对模具使用寿命的影响,避免因温度不均匀造成模具变形或损坏。
(3)设计合理的加热通道和布局。
加热通道的设计要保证能够均匀地加热整个模具,避免温度不均匀导致产品变形或出现气泡等缺陷。
加热通道和布局的设计还需考虑模具结构的复杂性和加热效率,以及方便维修和保养。
3.1冷却原理模具冷却系统的设计目的是将模具迅速冷却至一定温度,使注塑成型的产品迅速凝固,以便顺利脱模。
冷却系统一般采用水冷或油冷方式。
水冷却系统又可分为内冷和外冷两种形式。
选择合适的冷却方式和冷却介质需考虑模具的形状、材料及成型周期等因素。
3.2设计要点(1)冷却通道的设计。
冷却通道的设计要保证能够覆盖整个模具,使冷却介质能够充分接触模具表面,实现快速冷却。
通道的布局要合理,避免对产品的冷却时产生热死区。
(2)冷却介质选择。
根据模具的要求,选择合适的冷却介质,如自来水、循环水或特殊的冷却液等。
应考虑冷却介质的对模具材料的腐蚀性、冷却效果和成本等因素。
- 1、下载文档前请自行甄别文档内容的完整性,平台不提供额外的编辑、内容补充、找答案等附加服务。
- 2、"仅部分预览"的文档,不可在线预览部分如存在完整性等问题,可反馈申请退款(可完整预览的文档不适用该条件!)。
- 3、如文档侵犯您的权益,请联系客服反馈,我们会尽快为您处理(人工客服工作时间:9:00-18:30)。
模具设计中的冷却系统设计与优化分析
在模具设计中,冷却系统的设计和优化是非常重要的一部分。
冷却系统的设计
直接影响着模具的使用寿命、生产效率和产品质量。
本文将从冷却系统的设计原则、优化方法和实际案例分析三个方面来探讨模具设计中的冷却系统设计与优化分析。
一、冷却系统的设计原则
冷却系统的设计原则主要包括以下几个方面:
1. 冷却系统的位置和布局:冷却系统应该尽可能地靠近模具的加热部位,以提
高冷却效果。
同时,冷却系统的布局应该合理,避免冷却死角,确保冷却水能够充分覆盖模具表面。
2. 冷却水的流速和温度:冷却水的流速应该适中,过大会浪费资源,过小则无
法有效降温。
冷却水的温度也需要控制在合适的范围内,过高会导致冷却效果不佳,过低则可能引起冷凝水等问题。
3. 冷却系统的材料选择:冷却系统的材料应该具有良好的导热性和耐腐蚀性。
常见的冷却系统材料有铜、铝、不锈钢等。
在选择材料时,需要考虑模具的工作环境和使用寿命。
4. 冷却系统的管道设计:冷却系统的管道设计应该尽量简洁明了,避免过多的
弯曲和分支,以减少流阻和压力损失。
同时,管道的直径和厚度也需要合理选择,以保证冷却水的流量和压力。
二、冷却系统的优化方法
在模具设计中,冷却系统的优化方法主要包括以下几个方面:
1. 流场模拟分析:通过流场模拟分析,可以预测冷却水的流动情况和温度分布,帮助设计师找出冷却死角和热点位置,并进行合理的优化设计。
2. 冷却系统的分区设计:根据模具的不同部位和工艺要求,将冷却系统划分为不同的区域,以便针对性地进行优化设计。
例如,在需要加热的部位增加冷却水的流量和温度,以提高冷却效果。
3. 冷却系统的循环方式:冷却系统的循环方式有单循环和双循环两种。
单循环适用于冷却要求相对较低的模具,而双循环适用于冷却要求较高的模具。
在选择循环方式时,需要考虑冷却效果和成本之间的平衡。
三、实际案例分析
为了更好地理解模具设计中的冷却系统设计与优化分析,下面将以一个注塑模具为例进行实际案例分析。
某注塑模具的冷却系统设计存在以下问题:冷却水的流速过大,导致冷却效果不佳;冷却系统的布局不合理,存在冷却死角;冷却水的温度过高,影响了模具的使用寿命。
针对以上问题,可以采取以下优化措施:调整冷却水的流速,使其适中;重新布局冷却系统,确保冷却水能够充分覆盖模具表面;控制冷却水的温度,使其保持在合适的范围内。
通过对冷却系统的优化设计,可以明显提高模具的使用寿命、生产效率和产品质量。
同时,还可以降低能耗和生产成本,提高企业的竞争力。
总结起来,模具设计中的冷却系统设计与优化分析是一个复杂而重要的工作。
只有合理设计和优化冷却系统,才能提高模具的使用寿命、生产效率和产品质量。
通过流场模拟分析、冷却系统的分区设计和冷却系统的循环方式选择等方法,可以实现冷却系统的优化设计。
希望本文对于模具设计中的冷却系统设计与优化分析有所帮助。