可聚合乳化剂复配体系对聚合前后苯丙乳液性能的影响规律研究
乳化剂体系对苯丙乳液平均粒径的影响

乳化剂体系对苯丙乳液平均粒径的影响柳泉润;仇鹏;范桂利;李明威;厉生权【摘要】设计苯丙乳液配方中的乳化剂体系,讨论了乳化剂的类型和用量、加入方式及其配比等对乳液平均粒径的影响.借助马尔文激光粒度分布仪对乳液平均粒径进行测试,结果表明:乳化剂总用量越多,乳液平均粒径越小;反应型阴离子乳化剂比普通阴离子乳化剂所得乳液平均粒径小;非离子乳化剂中聚氧乙烯基数目越多,乳液平均粒径越小;乳化剂在预乳化液与打底液中的分配比例越小,乳液平均粒径越小;对于阴非离子乳化剂复配体系,阴离子乳化剂用量比例越大,乳液平均粒径越小.【期刊名称】《涂料工业》【年(卷),期】2015(045)003【总页数】4页(P37-40)【关键词】苯丙乳液;反应型乳化剂;乳化剂复配体系;平均粒径【作者】柳泉润;仇鹏;范桂利;李明威;厉生权【作者单位】中海油能源发展股份有限公司惠州石化分公司,广东惠州516086;中海油能源发展股份有限公司惠州石化分公司,广东惠州516086;中海油能源发展股份有限公司惠州石化分公司,广东惠州516086;中海油能源发展股份有限公司惠州石化分公司,广东惠州516086;中海油能源发展股份有限公司惠州石化分公司,广东惠州516086【正文语种】中文【中图分类】TQ630.4苯丙乳液除具有丙烯酸酯系聚合物乳液的优点外,还有性价比高、无毒、无味、不燃等特点,其涂膜具有良好的硬度、耐水性、耐碱性及耐擦洗性等,因此在建筑涂料、金属表面乳胶涂料、木器涂料、防火涂料、纸张粘合剂、胶粘剂和油墨等领域有广泛应用[1]。
乳胶粒的大小及分布对苯丙乳液的性能及应用有很大的影响,因此研究苯丙乳液平均粒径具有重要意义。
乳化剂体系是苯丙乳液合成原料中的主要部分,其类型和用量是影响苯丙乳液平均粒径的关键因素,同时对乳液的稳定性及涂料应用性能等也具有重要影响。
为满足本研究对苯丙乳液稳定性的要求,拟制备粒径为120~130 nm的苯丙乳液;通过配方设计,考察了不同乳化剂复配体系对苯丙乳液平均粒径的影响,从而确定最终乳化剂复配配方。
苯丙乳液合成反应条件优化

苯丙乳液合成反应条件优化冯雪峰;李西营;陈蔚萍;张普玉;毛立群【摘要】以苯乙烯、丙烯酸、丙烯酸丁酯、甲基丙烯酸甲酯等为单体,采用乳液聚合制备了苯丙乳液,研究了合成温度、引发剂用量、乳化剂用量、功能性单体丙烯酸用量等反应条件对苯丙乳液性能的影响,并探讨了丙烯酸单体对乳液耐酸碱稳定性的影响,确定了合成反应条件.结果表明,随着合成温度的提高,混合单体的转化率迅速增加,78℃时转化率最大(达到97.1%),而后随温度继续提高基本保持不变.混合单体转化率随过硫酸钾引发剂用量的增加呈现先增加后逐渐降低的趋势,当过硫酸钾与混合单体质量比为0.010时转化率最大,此时单体转化完全.此外,随着乳化剂用量增加,乳液的外观、钙离子稳定性、凝胶等性能都有所提高,但吸水率也相应增加.最佳合成反应条件为:合成温度为78℃,混合单体组成为15 g苯乙烯、2 g丙烯酸、18 g丙烯酸丁酯、8 g甲基丙烯酸甲酯,引发剂和乳化剂与单体质量比分别为0.010和0.035.得到的苯丙乳液在酸性条件下具有良好的稳定性.【期刊名称】《化学研究》【年(卷),期】2014(025)002【总页数】6页(P181-186)【关键词】苯丙乳液;乳液聚合;合成;反应条件【作者】冯雪峰;李西营;陈蔚萍;张普玉;毛立群【作者单位】河南大学化学化工学院,河南开封475004;河南大学化学化工学院,河南开封475004;河南大学化学化工学院,河南开封475004;河南大学化学化工学院,河南开封475004;河南大学化学化工学院,河南开封475004【正文语种】中文【中图分类】TQ633水性涂料中常见的成膜物质有纯丙乳液、苯丙乳液、硅丙乳液、丁苯乳液、乙丙乳液等[1-4],其中苯丙乳液因具有无毒、无味、耐水、抗老化、耐碱、抗污、耐擦洗和低廉的生产成本等优异特性而被广泛用于水性涂料.水性涂料成膜物质的结构与性能对涂料和涂膜的影响很大,它能连续地铺展和附着于基底表面,屏蔽介质对基材的腐蚀.目前国内开发的苯丙乳液大多存在涂料强度低、耐水性不好、成膜温度较高等缺点,不能很好的满足水性涂料对成膜物质的要求[5].本文旨在研究合成条件,如温度、引发剂用量、乳化剂加入量、功能单体丙烯酸加入量等因素对苯丙乳液合成反应及其性能的影响,为其性能改进提供依据.苯乙烯(ST)、丙烯酸丁酯(BA)、甲基丙烯酸甲酯(MMA)、丙烯酸(AA)、过硫酸钾(KPS)、十二烷基硫酸钠(SDS)、碳酸氢钠(缓冲剂)、无水氯化钙、辛烷基苯酚聚氧乙烯醚(OP-10)、氨水,所有试剂均为分析纯,使用之前没有进一步提纯;实验用水为一次蒸馏水.超声波发生器;电鼓风干燥箱;激光粒径及Zeta电位分析仪(ZS90型,英国马尔文Zetasizer Nano);傅立叶变换红外光谱仪(AVATAR360型,美国尼高力公司);集热式恒温加热磁力搅拌器;玻璃仪器气流烘干器;分析电子天平.苯丙乳液的制备过程主要分为三个阶段:预乳化阶段、种子制备阶段和主反应阶段.1.2.1 预乳化阶段乳化剂为OP-10与SDS的混合物,两者的质量比为2∶1.将一定量的乳化剂(乳化剂与混合单体质量比(w)依次为0.009,0.017 9,0.026 9,0.035,0.044)与30g(1.67mol)蒸馏水加入250mL三口烧瓶中,在1 080r/min转速下搅拌使之混合均匀;量取43g混合单体,其组成为16g苯乙烯、1g丙烯酸、18g丙烯酸丁酯和8g甲基丙烯酸甲酯,其中丙烯酸作为功能性单体仅在考察其用量时改变用量(丙烯酸与单体质量比u=0.01,0.03,0.05,0.07,0.09);将单体混合均匀后转入恒压滴液漏斗中,缓慢滴加入乳化剂的水溶液中,滴加完成后继续搅拌15min得到乳白色的预乳液,静置待用.1.2.2 种子制备阶段分别量取17g预乳液,20g(1.11mol)蒸馏水,0.275g引发剂(KPS)和0.200g缓冲剂(碳酸氢钠)加入250mL三口烧瓶中;将三口烧瓶放入水浴中,使水浴温度升温至78℃(升温速率为1~2℃/min),达到设定温度后恒温15min得到种子溶液.1.2.3 主反应阶段将一定量的引发剂(引发剂与单体质量比(v)依次为0.004,0.006,0.008,0.010)和56g预乳液加入恒压滴液漏斗中,混合均匀;逐滴加入上述种子溶液中(滴加速度为1d/s,溶液温度为78℃),滴加完全后升温至85℃继续反应1h;使反应溶液冷却至室温,加入氨水调节pH至7~8,得到苯丙乳液.苯丙乳液的固含量(%)根据国标GB/T 11175-2002进行测试,单体转化率由下式进行计算:1.3.1 结构分析采用AVATAR360型傅立叶变换红外光谱仪测定苯丙乳液的红外吸收光谱,KBr压片;采用ZS90型激光粒径及Zeta电位分析仪测定苯丙乳液的粒径及粒径分布,测试在25℃下进行.1.3.2 性能测试苯丙乳液的外观、pH值、储存稳定性、冻融稳定性、稀释稳定性、机械稳定性、乳液成膜性等性能均参照国标GB/T 11175-2002进行测试;苯丙乳液涂膜耐水性参照国标GB/T 1733-93进行测试.保持原料配比不变(43g混合单体、1.5g乳化剂、0.2g缓冲剂、0.45g引发剂、50g蒸馏水),在种子制备阶段分别选取70、75、78、和81℃温度条件制备种子溶液.图1是不同温度下单体转化率曲线,可以看出,温度为70、75℃时,单体的转化率较低,合成出来的苯丙乳液仍然存在单体的气味;当温度达到78℃时,转化率达到97.1%,熟化保温后几乎没有单体的味道,代之以乳香;温度继续升高到81℃时,转化率为96.03%,但是反应结束后,三口烧瓶底部有沉渣出现.在较低的温度下(70~75℃),乳液成核困难,生成的晶核数量不足,直接影响到后续的晶核生长.此外,温度较低,热分解释氧反应速率太慢,也不利于晶核的形成;反之,温度过高(>81℃),聚合过程加剧,晶核生长速度加快,生成的晶粒过大.采用热分解型过硫酸钾作为引发剂制备苯丙乳液.在78℃,43g混合单体,乳化剂与混合单体质量比w=0.035的条件下,改变引发剂用量进行乳液制备,考察了引发剂用量对单体转化率的影响(见图2).从图2中可以看出,当v=0.004~0.010时,单体的转化率随引发剂用量的增加而增加,合成出来的苯丙乳液还存在单体的味道;当v>0.010时,单体的转化率缓慢减少,单体味道消失,乳液有股淡淡的乳香味.引发剂的加入量过少,单体的转化率偏低;而加入量过多,在反应初期会形成较多的自由基,粒子间碰撞次数增加,最终导致粒径增大,转化率增大[6-8].图3是在不同引发剂用量下合成的苯丙乳液的红外谱图.当引发剂的加入量较低(v <0.010)时,在1 636cm-1处尚有C=C双键的吸收峰存在,说明单体未全部参与聚合反应;而当v=0.010时,在1 636 cm-1处C=C双键的吸收峰几乎完全消失,说明单体基本上参与了聚合反应.在78℃,43g混合单体和v=0.010的条件下,改变乳化剂用量w进行乳液制备,考察乳化剂用量对乳液性能的影响,如乳液的外观、成膜性、Ca2+稳定性、凝聚情况、吸水率、耐水时间(见表1)、以及乳液的粒径大小(见图4).从表1中可以看出,当乳化剂用量较低(w<0.018)时,苯丙乳液的吸水率相对较低,但乳液外观、涂膜外观比较差,这是因为乳化剂较少,胶粒易聚合,产生凝胶,影响了乳液外观;随着乳化剂加入量的增加(w>0.026),苯丙乳液的各项性能均得到改善.这是因为乳化剂增加,胶粒数增多,避免了合成过程中凝胶、破乳的发生,从而使乳液稳定性增加;但是随着乳化剂用量的增大,吸水率明显增大,这可归因于复合乳化剂的亲水性.从图4中可知,w=0.017时,苯丙乳液的粒径较大,超过1 000nm;当w=0.026时,苯丙乳液的平均粒径为136nm;当w=0.035时,苯丙乳液的平均粒径为130nm;当w=0.044时,苯丙乳液的粒径主要分布在13~110nm,平均粒径为82nm.在乳化剂用量比较少时,乳液的粒径较大;但随着乳化剂用量的增加苯丙乳液粒径逐渐减小,这是因为乳化剂用量增加,体系中胶束粒子变多,反应速率加快,乳液粒径变小.w=0.035时,乳液的平均粒径较小.结合表1乳液的各项性能测试结果,乳化剂的最佳用量为w=0.035.苯丙乳液在酸性环境以及金属离子的存在下不稳定,易出现凝胶[9],因此往往在合成苯丙乳液时加入一些功能性单体引起乳液交联,形成网状结构,提高苯丙乳液的稳定性.丙烯酸带有亲水基—COOH,既可溶于水相又可溶于油相,可以抑制凝胶的产生,增加乳胶粒的溶剂化作用,从而使苯丙乳液具有较好的电解质稳定性能[12].同时,功能性单体丙烯酸的加入还能改善乳液性能,如涂膜耐水性、涂膜耐擦洗性等[13-14].因此,选用丙烯酸作为功能单体来增强苯丙乳液的稳定性能,并且考察丙烯酸用量对合成的乳液耐水性能的影响(见表2).从表2可以看出,加入功能性单体丙烯酸后,苯丙乳液的耐酸碱pH范围增大,尤其是当丙烯酸用量与单体质量比值u=0.03时,苯丙乳液显示出较好的耐酸碱性,可以在pH=5~14的范围内保持稳定,不产生凝胶,这是因为AA中有极性基团羧基,引入乳液后在胶粒表面形成包裹,减少了粒子间的团聚,抑制了凝胶的发生,从而提高了苯丙乳液的耐酸碱性能.从表2还可以看出,随着丙烯酸加入量的增加,苯丙乳液涂膜后的吸水率增加,这是因为AA中的羧基是亲水性基团,用量过大会影响涂膜的耐水性.因为合成的苯丙乳液要用到酸性介质中,对苯丙乳液的耐酸稳定性要求较高,因此确定其最佳用量u为0.03~0.05.根据实验数据得到本实验制备苯丙乳液的最佳配比,具体配比如表3:以苯乙烯、丙烯酸丁酯、甲基丙烯酸甲酯、丙烯酸为单体合成了能在酸性条件下使用的苯丙乳液,主要研究结论如下:(1)影响单体转化率的主要因素有反应温度、引发剂和乳化剂用量,转化率随三种因素的增加均呈现先增后降的变化趋势,由此确定乳液聚合的最佳反应条件为:温度为78℃,43g混合单体,v=0.010,w=0.035;(2)丙烯酸作为功能单体对苯丙乳液的耐酸碱稳定性有着显著的影响,适当提高其用量(u=0.03~0.05)可以增进乳液的交联度,并对生成的乳液粒子进行表面修饰,抑制其团聚,提高乳液在酸性条件下的稳定性;(3)根据测试结果,最佳的乳液合成的原料质量配比为:15.8%苯乙烯、18.9%丙烯酸丁酯、8.4%甲基丙烯酸甲酯、2.1%丙烯酸、0.5%过硫酸钾、0.2%碳酸氢钠、52.5%蒸馏水、1.6%乳化剂.【相关文献】[1]ZOU Mingxuan,WANG Shijie,ZHANG Zhicheng,et al.Preparation and charaeterization of polysiloxane-poly(butyl acrylate-styrene)composite lattices and their film properties[J].Eur Polym J,2005,41(11):2602-2613.[2]WU Yumin,DUAN Hongdong,YU Yaoqin,et al.Preparation and performance in paper coating of silicone-modified styrene-butyl acrylate copolymer latex[J].J Appl Polym Sci,2001,79(2):333-336.[3]ZUBITUR M,ASUA J M.Factors affecting kinetics and coagulum formation duringthe emulsion copolymerization of styrene/butyl acrylate[J].Polymer,2001,42(14):5979-5985.[4]马祥梅,王斌,王武生.我国苯丙乳液的研究进展[J].化学与粘合,2003(1):30-39. [5]黄力涛.影响苯丙乳液性能的因素探讨[J].现代涂料与涂装,2010,13(5):39-40. [6]胡金生,曹同玉,刘庆普.乳液聚合[M].化学工业出版社,1987:202-204.[7]MAXWELL I A,NAPPER D H,GILBERT R G.Emulsion polymerization of butyl acrylate [J].J Chem Soc,Faraday Trans I,1987,3:1449-1467.[8]傅和青,黄洪,陈焕钦.引发剂及其对乳液聚合的影响[J].合成材料老化与应用,2004,33(3):39-42.[9]尚定书.水乳性铁锈转化涂料的配制与应用[J].材料保护,1996,29(8):38-39. [10]管睿,艾照全,李建宗,等.聚合工艺对丙烯酸酯乳液性能的影响[J].高分子材料科学与工程,1997,13(3):123-126.[11]MENGER F M,TSUNO T.Crosslinked polystyrene in corporating water-pobls [J].J Am Chem Soc,1990,112:1263-1264.[12]汪慧.SiO2气凝胶/苯丙原位复合乳液的制备及其在隔热涂料中的应用[D].广东:广东工业大学,2011.[13]罗正汤,侯友军,宁平,等.涂料用丙烯酸酯—苯乙烯超微乳液的研究[J].华南理工大学学报:自然科学版,2001,29(3):71-74.[14]黄力涛.影响苯丙乳液性能的因素探讨[J].现代涂料与涂装,2010,13(5):39-40.。
乳化剂体系对乳液压敏胶粘剂性能的影响[1]
![乳化剂体系对乳液压敏胶粘剂性能的影响[1]](https://img.taocdn.com/s3/m/7f52f6d126fff705cc170a75.png)
第19卷第2期2001年6月胶体与聚合物Ch inese Jou rnal of Co llo id&po lym erV o l.19 N o.2Jun.2001乳化剂体系对乳液压敏胶粘剂性能的影响Ξ曾宪家(河北华夏实业(集团)股份有限公司,涿州市,072750)摘 要 利用三种不同的乳化剂体系合成丙烯酸酯乳液压敏胶粘剂,研究了乳化剂体系对产物分子量、分子量分布以及对压敏胶各项性能的影响。
结果表明,用阴离子乳化剂 制得的乳液具有较高的平均分子量,持粘性好,但乳液的稳定性较差。
而用复合乳化剂 制备的乳液的平均分子量较低,持粘性差,但乳液的稳定性好。
用复合乳化剂 制备的乳液具有较好的综合性能。
关键词 乳化剂;压敏胶粘剂;乳液乳液压敏胶粘剂在我国压敏胶粘剂工业中占有相当重要的地位,约占全国压敏胶粘剂总产量的80%,占全部丙烯酸酯乳液的60%。
1997年全国丙烯酸酯乳液压敏胶粘剂的产量达10万吨左右,广泛用于制作包装胶粘带、文具胶粘带以及商标纸等。
在乳液压敏胶粘剂中,乳化剂起着十分重要的作用。
它能降低体系的表面张力,使单体得到分散和乳化,但它对压敏胶粘剂的性能也会产生一定不利的影响。
乳化剂会影响聚合物的稳定性以及乳胶粒的粒径和数目[1],还会影响乳液压敏胶粘剂的胶粘性能[2]。
对聚丙烯酸酯乳液压敏胶粘剂的研究较多[3,4,5],但大多数仅局限于聚合工艺和聚合动力学的研究,关于乳化剂的影响也只局限于乳液稳定性等简单性能的对比。
为了进一步了解乳化剂对乳液压敏胶粘剂的影响。
我们选择了三种不同的乳化剂体系,从聚合物分子量的角度考察了它们对乳液压敏胶粘剂各项性能的影响1 实验部分111 原料 丙烯酸丁酯、丙烯酸、丙烯酸羟丙酯、丙烯酸2-乙基己酯、丙烯酸乙酯(工业品),过硫酸钾(工业品),去离子水(自制),乳化剂 (磺酸盐),乳化剂 和乳化剂 为自配复合型乳化剂,氨水(工业品)。
112 仪器 BLD-200D型电子剥离实验机,CZY-G型初粘性测试仪,CZY-3S型持粘性测试仪, NDJ-1旋转粘度计。
苯丙乳液

反应型乳化剂对苯丙微皂乳液聚合及性能的影响卢保森,王小妹*(中山大学化学与化学工程学院,广东广州 510275)摘要采用不同结构类型的反应型乳化剂应用于苯丙微皂乳液的聚合,主要讨论了聚合方式、乳化剂的结构类型和用量等对乳液聚合及性能的影响。
借助DSC、粒径分散仪、FT-IR、力学实验技术、TEM等仪器技术对制得的苯丙乳液的性能进行表征分析,发现通过半连续核壳聚合方式,采用合适的反应型乳化剂复配体系,可以制备出综合性能优异,粒径小于100nm的苯丙微皂乳液。
关键词反应型乳化剂,两阶段聚合,苯丙微皂乳液前言苯乙烯-丙烯酸酯乳液(苯丙乳液)是乳液聚合中研究较多的体系,也是当今世界有重要工业应用价值的十大非交联型乳液之一[1]。
由于其较高的性价比,在建筑涂料、金属表面乳胶涂料、地面涂料、防火涂料、纸张粘合剂、胶粘剂、油墨等领域应用广泛[2]。
近年来,进一步提高和完善苯丙乳液性能的研究日趋活跃,采用反应型乳化剂制备微皂乳液就是其中热点之一[3~6]。
微皂乳液是指采用带有反应性基团的单体或高分子作反应型乳化剂部分或全部替代传统乳化剂体系合成的乳液。
采用反应型乳化剂比传统乳化剂有明显的优点,由于其具有聚合活性,其反应性官能团能参与乳液聚合反应,除了起常规乳化剂的作用外,还可以以共价键的方式键合到聚合物粒子表面,成为聚合物的一部分,避免了乳化剂从聚合物粒子上解吸或在乳胶膜中迁移,大大减少了乳胶膜表面的亲水基团,从而能提高乳液的稳定性和改进乳胶膜的耐水性和力学性能[7]。
同时通过粒子设计,可以有效的调节乳液的最低成膜温度(MFT),提高乳液的成膜性能[8]。
本研究事先通过粒子设计,然后采用不同的反应型乳化剂体系,考察了反应型乳化剂的结构类型对苯丙微皂乳液聚合及性能的影响。
1.实验部分1.1主要实验原料苯乙烯(St),丙烯酸-2-乙基己酯(2-EHA),丙烯酸丁酯(BA),甲基丙烯酸甲酯(MMA),甲基丙烯酸(MAA),丙烯酸(AA),工业级,以上均为东方化工厂产品;过硫酸铵(APS),正戊醇(n-PTL),醋酸钠(NaAc),AR级,以上均为广州市化学试剂厂产品;聚甲基丙烯酸钠(保护胶),自制;氨水,工业级,广州市东江化工厂。
反应性乳化剂对苯丙乳液合成及性能的影响

采用适当的聚合技术和聚合条件,能使单体(或 基团)在乳胶粒表面的分布率提高。反应性乳化剂
2008 年 12 月第17 卷第 12期 Vol.17 No.12,Dec.2008
中国胶粘剂
CHINA ADHESIVES
-5-
反应性乳化剂对苯丙乳液合成及性能的影响
徐小波,邓宝祥,郑海涛,林 艳,熊齐春
(天津工业大学材料科学与化学工程学院,天津 300160)
摘要:在反应性阴离子乳化剂[甲基丙烯酸羟丙磺酸钠(HPMAS)]的作用下,采用甲基丙烯酸甲酯(MMA)、苯 乙烯(St)、丙烯酸丁酯(BA)和丙烯腈(AN)为主单体,丙烯酸(AA)为功能性单体,合成了性能优异的无皂苯丙乳 液。研究了软硬单体配比、乳化剂、链转移剂和引发剂用量对乳液性能的影响。研究结果表明,合成无皂苯丙 乳液的适宜条件(相对于单体总质量而言)是:w(HPMAS)=4%,w(引发剂)=0.8%,w(链转移剂)=2%且前期 加入。
加大甚至相互聚集,故乳液体系极不稳定;当过硫酸
铵用量过多时,聚合速率较快,过多的引发链同时反
应,导致体系粘度上升、聚合度降低、相对分子质量
减小、成核粒子数增多且乳液粒径减小,此时反应热
难以排除,易产生“爆聚”现象。此外,过硫酸铵属于
电解质,用量过多时,一部分过硫酸铵起着电解质的
作用,导致体系中电解质浓度增加,影响聚合过程的
1 实验部分
国药集团化学试剂有限公司;碳酸氢钠(NaHCO3),分 析纯,天津市永大化学试剂开发中心;氨水(NH·3 H2O), 分析纯,天津石英钟厂霸州市化工分厂。
含功能性单体的苯_丙乳液的聚合稳定性_张心亚

华南理工大学学报(自然科学版)第32卷第3期Journal of South China University of TechnologyVol .32 No .32004年3月(Natural Science Edition )Mar ch 2004文章编号:1000565X (2004)03001505含功能性单体的苯/丙乳液的聚合稳定性*张心亚 蓝仁华 陈焕钦(华南理工大学化学工程研究所,广东广州510640)摘 要:采用乳液聚合工艺,以过硫酸钾为引发剂,合成了含功能性单体甲基丙烯酸羟乙酯和丙烯酸的苯乙烯/丙烯酸丁酯共聚乳液.系统研究了乳化体系、引发体系、含功能基单体含量、聚合工艺和聚合温度等对乳液聚合过程稳定性的影响,发现聚合温度降低,采用半连续聚合工艺以及适当提高乳化剂的浓度均有利于乳液聚合反应的稳定性提高.关键词:乳液聚合;功能性单体;苯/丙乳液;聚合稳定性中图分类号:TQ 433 文献标识码:A 收稿日期:20030928*基金项目:广东省科技厅科技计划项目(2003B 10506);广东省计划发展委员会高技术产业化项目(粤财企[2002]347号急件);广州市科技局科技攻关重点项目(2002Z 2_D 0071) 作者简介:张心亚(1974-),男,博士,讲师,主要从事乳液及其相关新产品研究.E _mail :cexyzh @scut .edu .cn 在乳液聚合过程中,凝聚物的形成在乳液生产中具有极大的危害,它不仅降低了单体的收率,增加了聚合装置的停机时间(清理凝聚物)和处理凝聚物的费用,而且加大了各釜间产品的不一致性.因此,聚合过程的稳定性对乳液制备过程有重要作用.乳液聚合内部反应极其复杂,如果反应过程控制不当或选用的工艺、配方不合适等,均可能导致凝聚现象发生.余樟清等曾对乳液聚合过程中凝聚物的形成机理进行了探讨[1],并研究了含氨基、羟基丙烯酸乳液聚合的稳定性[2].史沈明[3]、赵永金[4]等对影响丙烯酸酯类乳液聚合稳定性的因素进行了探讨,并提出了控制乳液聚合稳定性的方法.苯乙烯/丙烯酸酯乳液在制备过程中,丙烯酸(AA )、甲基丙烯酸羟乙酯(H EMA )等作为功能性单体参与共聚,可以提高乳液涂膜的耐水性、耐溶剂性、耐沾污性和机械强度.但这些极性单体常常具有很强的亲水性,在乳液聚合过程中易在水相中发生均聚,形成水溶性大分子并产生絮凝作用,使体系破乳.本研究在用乳液聚合方法合成含功能性单体的苯丙乳液过程的基础上,着重考察了乳化剂体系、引发剂体系、功能性单体的类型及用量、聚合温度和单体加入方式等对乳液聚合稳定性的影响.1 实验部分1.1 实验原料共聚单体为丙烯酸丁酯(BA )、苯乙烯(St )、丙烯酸(AA )、甲基丙烯酸甲酯(MMA )、甲基丙烯酸羟乙酯(H EMA ),均为工业级,新鲜蒸馏后低温贮存备用;乳化剂十二烷基苯磺酸钠(SDBS )、十二烷基硫酸钠(SLS )、壬基酚聚氧乙烯(40)醚(NP 40)、辛基酚聚氧乙烯(20)醚(OP10)和引发剂过硫酸铵(APS )等均为化学纯,配成一定浓度的水溶液待用.1.2 乳液合成间歇工艺:将单体全部预乳化,然后升温至反应温度,加入引发剂反应.半连续工艺:(a )纯单体滴加法 将部分单体、水和乳化剂在反应釜内预乳化30min ,然后加入引发剂升温至80℃下反应约30min 后,开始滴加混合单体,其间补加引发剂,在4h 内滴完.滴完后,升温至90℃,保温1h 后降温,用氨水调节乳液的pH 值为7~8.5,过滤出料.(b )预乳化单体滴加法 先将单体、部分乳化剂和水在室温下预乳化制得预乳液,将部分该预乳液、适量引发剂和水置于反应釜中,在75~85℃下反应约30min ,然后同时滴加预乳化单体和引发剂水溶液,在4h 内滴完.滴完后,升温至90℃,保温1h 后降温,用氨水调节乳液的pH 值为7~8.5,过滤出料.1.3 分析测试1)转化率 聚合反应的转化率由称重法测定.2)凝聚率 乳液聚合反应的稳定性用凝聚率w c 表示,凝聚率由称重法获得.在乳液聚合反应结束后收集聚合体系中的凝聚物,在烘箱中烘至恒重,凝聚率根据下式进行计算:w c =m cm m×100%(1)式中:m c 为凝聚物的质量,g ;m m 为单体的总质量,g .w c 值越小,表示乳液聚合反应过程的稳定性越好.3)粒径及其分布 本实验中,乳胶粒的粒径和粒径分布采用英国H onrywell 公司的Microtr ace UPA 150型粒度仪进行测定,操作温度为25℃.4)粘度 采用Brookfield RVDL II +粘度仪测定,选用2号转子,转速60r /min ,测定温度为25℃.2 结果与讨论2.1 乳化体系对聚合过程稳定性的影响乳化剂的选择是决定乳液聚合体系稳定性的关键因素之一.一般认为,采用非离子型乳化剂与阴离子型乳化剂联合使用,可使阴离子乳化剂的电荷稳定和非离子乳化剂的空间位阻作用产生协同效应,提高乳液聚合的稳定性和乳胶粒的稳定性.对于乳液聚合体系,乳化剂可通过单体与乳化剂的亲水亲油平衡值(H LB 值)相近的原则或通过单体的乳液稳定性试验来选择,但对含有强亲水性单体H EMA 和AA 的多元共聚合体系,使聚合过程稳定的乳化剂体系仍需通过聚合稳定性试验确定.本文中将阴离子乳化剂SLS 、SDBS 和非离子型乳化剂OP 10、NP 40进行复配试验(结果如表1所示),通过稳定性实验选择适宜的乳化体系.由表1实验结果可见,SLS /NP 40对含功能性单体的苯/丙乳液聚合反应稳定性最差,只有在SLS 含量较高时聚合反应才能进行,但单体最终的转化率相对较低;SLS /OP 10、SDBS /NP 40也近似有相同的结果;而SDBS /OP 10体系,其聚合过程的凝聚率最低,聚合稳定性最好,阴、非离子乳化剂的配比范围也最宽.因此,在后面的实验过程中,主要采用SDBS 复配乳化剂进行试验.表1 乳化剂配比对乳液聚合反应稳定性的影响Table 1 Ef fect of the em ulsif ier ra tio on stability of emul -sion polymer iza tion乳化剂复配质量比率聚合稳定性转化率/%凝聚率w c /%平均粒径/n m SLS /NP 40 2∶11∶11∶2稳定粘度过大不稳定93.06——2.93——175——SLS /OP 10 2∶11∶11∶2稳定稳定不稳定95.3889.64—2.413.33—102237—SDBS /NP 40 2∶11∶11∶2稳定不稳定不稳定98.51——1.89——110——SDBS /OP 102∶11∶11∶2稳定稳定稳定99.9999.9697.350.440.871.2180100178 实验采用半连续聚合工艺(a ),单体质量比m (St )∶m (BA )∶m (AA )∶m (H EMA )=60∶36∶1∶1,引发剂量为0.4%,乳化剂量为2.4%.实验中还发现,对机械稳定性不好的乳液,加大阴离子型乳化剂,可减少搅拌轴叶片及温度计套管上吸附的凝聚物;对化学稳定性不好的乳液,增加非离子型乳化剂,可减少反应容器内壁结皮等现象.图1所示为乳化剂总量对体系凝聚率的影响.由图1可见,随着乳化剂总量的增加,乳液聚合反应的凝聚率降低,这有利于乳液聚合反应的稳定性.但由于影响乳液凝聚率的因素还有很多,如反应温度及搅拌速度等,当乳化剂用量达到一定值后,凝聚率曲线趋向平缓,因此不可能单纯靠增大乳化剂用量来降低乳液的凝聚率而提高乳液聚合反应的稳定性.图1 乳化剂用量对乳液聚合稳定性的影响Fig .1 Eff ect of emulsifier dosage on stability of emul -sion polym erization实验采用工艺、单体质量比、引发剂量同表1乳化剂SDB S /OP 10质量比=2∶116华南理工大学学报(自然科学版) 第32卷2.2 引发体系对聚合过程稳定性的影响引发体系对于含强亲水性基团单体(如AA 、HEMA )苯/丙乳液聚合体系的乳液聚合稳定性有较大的影响.引发剂用量主要影响乳液聚合的最终转化率和凝聚率,如图2所示.当其它条件一定时,随引发剂用量的增加,最终转化率逐渐增大,当达到一定值时,曲线趋向平缓;而凝聚率则是先显著降低到一定的程度,而后又随着引发剂用量的增加而明显增大.其乳液聚合反应速率如下式所示[5]: R p =103NK p [M ]/(2N A )(2)式中:R p 为聚合反应速率;N 为单位体积中胶粒的数目;K p 为聚合反应速率常数;[M ]为乳胶粒中反应单体的浓度;N A 为阿弗加德罗常数.图2 引发剂用量对乳液聚合反应稳定性的影响F ig .2 Effe ct of initiator dosage on sta bility of emulsionpolymer ization实验采用工艺、单体质量比同表1乳化剂SDBS /OP 10质量比=2∶1,用量为2.4%在引发剂用量较小时,体系中乳胶粒获得自由基的几率较小,参加聚合反应的有效乳胶粒数较少,即在上式中N 的有效值小,R p 较小,最终转化率较低;而随着引发剂量的增加,乳胶粒获得自由基的几率增加,N 的有效值增加,反应加快,最终转化率提高;再继续增大引发剂的用量,并不能有效提高最终转化率,反而会因引发剂用量过大,容易导致凝聚率显著增大,从而使乳液聚合反应失控.实验发现,选用0.4%~0.5%的引发剂量,可使制备的苯/丙乳液呈现出蓝光,乳液粒子的粒度小,乳液的稳定性好.2.3 功能性单体对聚合过程稳定性的影响选择带有一定极性基团的功能性单体AA 和HEMA 参与反应,可以使共聚物产生轻微的交联,并形成一定程度的网络结构,同时,由于形成分子网络的化学键代替了单纯的分子间作用力,在一定程度上提高了共聚物的刚性,又由于极性基团的引入,提高了共聚物乳液的内聚力.对于水溶性的AA 和H EMA 的甲基丙烯酸链节倾向于分布在粒子表面和近表层,降低了乳胶粒与水的界面能,它的存在对聚合过程稳定性有利.随着AA 和HEMA 总含量的增加,乳液共聚合过程的稳定性增加,如图3所示,但当其含量超过4%后,乳液聚合的稳定性又有下降的趋势.随着功能性单体总用量的进一步增大,共聚物乳液的聚合稳定性能又开始下降.产生这种情况的原因可能是:随着功能性单体总用量的增加,体系中的交联点的数目也逐渐增加,当达到3%~4%时,体系中交联点数及其分布,引入的极性基团的数量正好处于一个最佳状态;再增加功能性单体用量,会导致体系中的交联度过大,使共聚物乳液体系凝聚而失稳[6].图3 功能性单体总量对乳液聚合稳定性的影响Fig .3 Ef fect of f unctional monomers dosage on stabili -ty of emulsion polymer ization实验条件:半连续聚合工艺(a ),AA /HEMA 质量比=1∶1,引发剂量为0.4%,乳化剂SDBS /OP 10质量比=2∶1,用量为2.4%2.4 聚合工艺对聚合过程稳定性的影响聚合工艺对聚合过程稳定性的影响如表2所示,实验研究表明,在间歇式反应过程中,经过一段时间的诱导期后,反应开始进行,反应一旦开始,由于热量的转移不及时,会使反应器内部温度急剧升高,造成自动加速反应,使反应温度一度达到95℃而发生内部暴聚,处于沸腾状态.此时由于反应速率快,乳化剂不能迅速地吸附到乳胶粒表面以维持乳胶粒的稳定,乳胶粒子之间聚结的作用力增大,从而导致凝聚产生使反应失稳;而半连续反应,不管是预乳化单体滴加,还是纯单体滴加,都增加了聚合反应的稳定性,转化率高,而且所得乳液的粒径分布均匀,贮存稳定性更好.这可能是由于采用半连续法聚合时,加入的单体很快在乳胶粒表面聚合,水相中存17第3期张心亚等:含功能性单体的苯/丙乳液的聚合稳定性在的游离单体含量较少,亲水性功能单体H EMA、AA发生均聚的几率较小;而在间歇反应时,水相中存在的游离单体含量多,亲水性功能单体H EMA、AA发生均聚的几率较大,它们的均聚物具有一定的絮凝作用,可导致聚合反应过程稳定性及乳液贮存稳定性的下降.表2 聚合工艺对乳液聚合反应稳定性的影响Table2 Effe ct of polyme rization pr ocesses on stability of emulsion polymer iza tion聚合工艺聚合稳定性转化率/%凝聚率wc/%平均粒径/nm间歇式半连续(a)半连续(b)不稳定稳定稳定91.3599.9699.995.210.870.4417812080 实验采用工艺、单体质量比、引发剂量同表1,乳化剂SDBS/OP_10质量比=2∶1,用量为2.4%.2.5 反应温度对聚合过程稳定性的影响反应温度对聚合反应速度及聚合稳定性也有较大的影响,如表3所示.苯/丙乳液聚合一般采用分段控温.单体滴加阶段控制反应温度在78~85℃之间,聚合温度低于78℃时,反应速度明显减慢,滴加的单体不能很快聚合,造成体系中单体局部浓度过大,极易引起暴聚冲釜,操作难度增大;聚合反应温度高于85℃时,乳化剂不能迅速地吸附到乳胶粒表面以维持乳胶粒的稳定,同时由于聚合反应速率增大,聚合物粒子变软,粘性增加,使乳胶粒子间因碰撞而凝聚的可能性增加,不利于乳化体系的稳定,乳液内部易产生粗粒子.如果聚合体系中同时存在可发生交联反应的官能团单体,则聚合温度升高将加快乳胶粒间交联反应速度,降低乳液的聚合稳定性.表3 聚合反应温度对乳液聚合反应稳定性的影响Table3 Effe ct of polyme rization tem pe ra tur e on stability of emulsion polymer iza tion反应温度/℃聚合稳定性转化率/%凝聚率wc/%平均粒径/nm70~75 75~80 80~85 85~90 >90反应时间过长稳定粘度过大不稳定不稳定90.1493.0699.9995.38—2.930.483.53——15280217—— 实验条件同表2.实验中还发现,操作不当如加料速度过快或引发剂加入过快,都会引起反应温度过高,从而导致反应器内壁凝聚物结皮较厚、凝聚物明显增多,反应稳定性显著下降.而同样地,聚合反应温度过低,也会使反应控制变得困难.因温度过低,引发剂的半衰期很长,前期引发不足,使后期未反应单体浓度偏高,反应剧烈放热,温度急剧升高,导致反应失稳.此外,当搅拌速率过大或过小,乳液体系中电解质含量和乳液固体含量增加以及采用的水为非精制水、水相比较小时,都会引起反应过程的稳定性降低.3 结 论1)不同的乳化剂类型及用量对苯丙乳液聚合反应的稳定性有较大的影响,采用阴离子型乳化剂与非离子型乳化剂复配,且乳化剂量为2.4%时,聚合反应较稳定.2)对苯/丙乳液聚合体系,引发剂的用量在0.4%~0.5%时,聚合反应的稳定性较好.3)对苯/丙乳液聚合体系,功能性单体HEMA、AA的量为4%左右时,聚合反应的稳定性较好.由于各体系的聚合稳定性主要影响因素不同,而聚合过程稳定性又直接影响着聚合过程的效率及乳液产品的最终性能,为提高乳液生产过程和乳液产品性能的稳定性,增强乳液产品的市场竞争力,应对含官能团单体的乳液聚合过程的稳定性研究给予足够的重视.参考文献:[1] Yu Zh ang_qin,Che n H uan_qin,Li Bao_geng,et al.Stability of emulsion polym er ization of acrylicmonomers containing f unctional m onomers[J].NewBuilding M ater ials,1999(4):33-35.[2] Yu Zhang_qin,Li Bao_geng,Pan Zu_re n,et al.Stabili-ty of em ulsion polymer iz ation of acr ylic monomerscontaining amino and hydr oxyl gr oups[J].ChemicalJour nal of China Univer sity,1998,19(3):472-476.[3] Shi Shen_ming.I nvestigations into polymer ic stabilityof acr ylic resin emulsion[J].Le ather Che micals,1994(1):22-26.[4] Zhao Yong_jin.The fa ctors of a cryla tes af fec ting sta-biliz ation of e mulsion polymer iz ation and thecontr ol-ling methods[J].Jour nal of Shihez i Institute of Agr i-culture,1994,12(3-4):113-116.[5] Hu Jin_sheng,Cao Tong_yu,Liu Qin_pu.Em ulsionpolymer iz ation[M].Beijing:Che mical Industrial18华南理工大学学报(自然科学版) 第32卷Pr ess ,1987.[6] F ang Shao _ming ,Feng Xian _ping ,Chen Hai _jun .Acr ylate e mulsion press sensitivity glu [J ].Technolo -gy on Adhesion a nd Sealing ,1996(2):13-15.Polymerization Stability of St _BA _HEMA _AA Copolymeric Latex Containing Functional MonomersZhang Xin _ya Lan Ren _hua Chen Huan _qin(R ese arch I nstit ute of Che mical Engine ering ,South China Univ .of Te ch .,Guangzhou 510640,Guangdong ,C hina )Ab stract :The quaternary copolymer ic latex of styrene _butyl acrylate containing functional monomers ,such as hydroxyethyl methacrylate and acrylic acid ,was pr epared by the emulsion polymerization pro -cess with potassium sulfate as the initiator .The ef fects of emulsifier system ,initiator system ,functional monomer dosage ,polymerization pr ocess and polymer ization temper ature etc .on the stability of emul -sion polymer ization were systemically investigated .I t is found that the decr ease in polymer ization tem -per ature ,the incre ase in emulsifier dosage and the adoption of semi _continuous e mulsion polymer ization pr ocess are benef icial to impr oving the stability of e mulsion polyme rization .Ke y words :emulsion polymerization ;f unctional monomer ;St _BA _HEMA _AA copolyme ric latex ;poly -merization stability (上接第9页)Preparation and Property of a Novel Al 3+_doped Silica GelAdsorptive M aterialFang Yu _tang 1 Ding Jing 1 Fan Juan 1 Y ang Jian _ping 1 Y ang X iao _xi 2(1.Key Labor atory of Enhanced H eat Tr ansfe r a nd Energy C onser vation of the Ministr y of Education ,South China Univ .of Te ch .,Guangzhou 510640,Guangdong ,C hina ;2.Dept .of chemistr y ,Dongguan Univ .of Tech .,Donggua n 523106,Guangdong ,C hina )Ab stract :A novel Al 3+_doped silica gel adsorptive material with excellen t adsorption proper ty was pr e -par ed by treating cer amic f iber matrix with the aqueous solution of sodium silicate (N a 2SiO 3)and alu -minum salt e tc .,as well as with pH value adjustment .The effects of impregnation conditions on the ad -sorptive proper ty and surface structure of the novel material were investigated ,thus obtaining the opti -mal reaction condition ,that is ,26.7%(mass fr action )of N a 2SiO 3,10%(mass f raction )of aluminum salt ,impregnation time per iod of 120min ,reaction temper atur e of 60℃and the pH value of the solutionof 1.8.It is f ound that Al 3+_doped silica gel can perfectly deposit on the surf ace and in the aper tures of cer amic fiber ,and its mesopores play a key role in adsor ption .For the substitution insertion of alu -minum into the silica gel f ramework (Al 3+doped ),the adsorption proper ty ,hea t r esistance proper ty and mechanical strength of the novel mater ial are superior to those of silica gel .Ke y word s :impregnation ;adsorption ;Al 3+_doped silica gel ;heat resistance property ;mechanical strength19第3期张心亚等:含功能性单体的苯/丙乳液的聚合稳定性。
毕业设计与论文(40000吨年苯丙乳液聚合装置工艺设计)

40000吨/年苯丙乳液聚合装置工艺设计摘要:本文以生产苯丙乳液为目的,阐述了苯丙乳液的研究现状。
通过对各种合成工艺路线综合评价、分析比较,选择合理的生产工艺,确定经济合理的工艺流程。
计算出每批物料的进料量、反应热,从而选择合适的换热方式和设备。
根据测得的物料粘度选择合适的搅拌器和搅拌功率,从而最终按照40000吨/年苯丙乳液的规格设计出主要设备——聚合釜,并对其工艺工程进行设计,绘制合理的工艺流程图。
关键词:苯丙乳液;生产工艺;搅拌装置;聚合釜Abstract :This paper production styrene-acrylic latex for the purpose, expounds the presentsituation of the study styrene-acrylic latex, through various synthesis process route comprehensive evaluation, the analysis and comparison, the choice of reasonable production process, determine the economic and reasonable process flow. Calculated each batch of material feed rate, reaction heat, to choose a suitable heat transfer methods and equipment. According to the measurement of material viscosity choose appropriate mixer and mixing power, and in the end to 40000 tons/year styrene-acrylic latex design specifications of the main equipment-polymerization kettle, and its technological engineering design, draw reasonable process flow diagram.Key word:Styrene-acrylic emulsion; the production process; stirring device ; polymerizer.目录第一部分绪论 (1)1 苯丙乳液的用途和特点 (1)2 苯丙乳液的研究进展 (2)2.1 乳化剂体系研究进展 (2)2.2 引发剂体系研究进展 (3)2.3 苯丙乳液的改性研究 (3)2.4 苯丙乳液聚合工艺研究进展 (6)3 苯丙乳液聚合的方法 (8)4 研究目的和步骤 (8)第二部分工艺计算与选型依据 (9)1 小试原料配比和工艺条件选择的依据 (9)1.1 单体用量 (9)1.2 乳化剂的选择和用量 (9)1.3 引发剂的用量 (9)1.4 反应温度的选择 (10)1.5 反应时间的选择 (10)1.6 产品主要技术性能指标 (10)2 搅拌罐的设计 (11)2.1 罐体的长径比 (12)2.2 装料系数 (12)2.4 确定筒体直径和高度 (13)3 搅拌设备的传热 (13)3.1 传热方式 (13)3.2 确定传热方式 (15)4 搅拌器 (16)4.1 搅拌器分类及参数 (16)4.2 搅拌器选型 (17)4.3 搅拌槽体及附件 (17)4.4 叶轮位置与标准搅拌槽 (18)4.5 搅拌器功率的估算 (18)第3部分工艺设计 (20)1 物料衡算 (20)1.1 预乳化液组成 (20)1.2 引发剂组成 (20)1.3 各物料含量 (20)2 热量衡算 (21)3 反应釜设计 (22)3.1 估算内径 (23)3.2 封头设计 (23)3.3确定筒体高度 (23)3.4传热面积 (24)3.5确定筒体厚度 (25)4夹套的设计 (25)4.1 确定夹套直径 (25)4.2 确定夹套高度 (26)4.3 确定夹套筒体壁厚 (26)4.4确定夹套封头壁厚 (26)5 水压测试 (26)5.1 釜体试水压 (26)5.2 夹套试水压时釜体稳定性 (26)5.3 夹套水压试验 (26)6 搅拌器设计 (27)6.1搅拌器类型选择 (27)6.2 搅拌功率计算 (27)7设计结果 (28)致谢 (29)参考文献 (30)附录一外压受压圆筒几何参数计算图 (32)附录二外压圆筒、管子和球壳厚度计算图 (33)附录三聚合釜总装备图 (34)附录四苯丙乳液聚合工艺流程图 (35)第一部分绪论1 苯丙乳液的用途和特点随着建筑业的发展,外墙涂料的在涂料工业中的地位也越来越重要了。
探讨苯丙乳液聚合研究进展
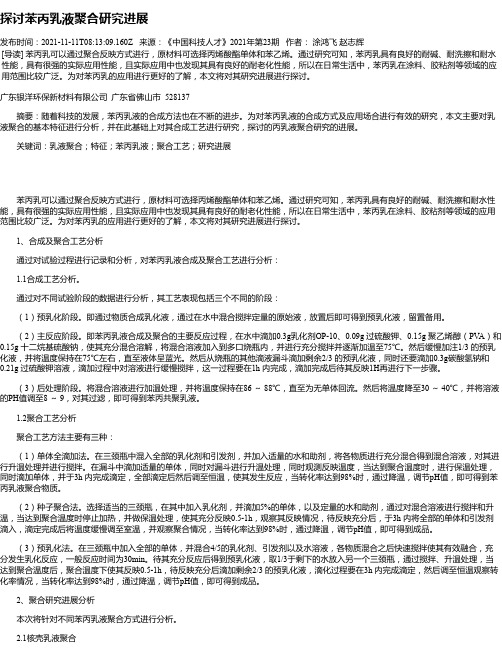
探讨苯丙乳液聚合研究进展发布时间:2021-11-11T08:13:09.160Z 来源:《中国科技人才》2021年第23期作者:涂鸿飞赵志辉[导读] 苯丙乳可以通过聚合反映方式进行,原材料可选择丙烯酸酯单体和苯乙烯。
通过研究可知,苯丙乳具有良好的耐碱、耐洗擦和耐水性能,具有很强的实际应用性能,且实际应用中也发现其具有良好的耐老化性能,所以在日常生活中,苯丙乳在涂料、胶粘剂等领域的应用范围比较广泛。
为对苯丙乳的应用进行更好的了解,本文将对其研究进展进行探讨。
广东银洋环保新材料有限公司广东省佛山市 528137摘要:随着科技的发展,苯丙乳液的合成方法也在不断的进步。
为对苯丙乳液的合成方式及应用场合进行有效的研究,本文主要对乳液聚合的基本特征进行分析,并在此基础上对其合成工艺进行研究,探讨的丙乳液聚合研究的进展。
关键词:乳液聚合;特征;苯丙乳液;聚合工艺;研究进展苯丙乳可以通过聚合反映方式进行,原材料可选择丙烯酸酯单体和苯乙烯。
通过研究可知,苯丙乳具有良好的耐碱、耐洗擦和耐水性能,具有很强的实际应用性能,且实际应用中也发现其具有良好的耐老化性能,所以在日常生活中,苯丙乳在涂料、胶粘剂等领域的应用范围比较广泛。
为对苯丙乳的应用进行更好的了解,本文将对其研究进展进行探讨。
1、合成及聚合工艺分析通过对试验过程进行记录和分析,对苯丙乳液合成及聚合工艺进行分析:1.1合成工艺分析。
通过对不同试验阶段的数据进行分析,其工艺表现包括三个不同的阶段:(1)预乳化阶段。
即通过物质合成乳化液,通过在水中混合搅拌定量的原始液,放置后即可得到预乳化液,留置备用。
(2)主反应阶段。
即苯丙乳液合成及聚合的主要反应过程,在水中滴加0.3g乳化剂OP-10、0.09g 过硫酸钾、0.15g 聚乙烯醇(PV A)和0.15g 十二烷基硫酸钠,使其充分混合溶解,将混合溶液加入到多口烧瓶内,并进行充分搅拌并逐渐加温至75℃。
然后缓慢加注1/3 的预乳化液,并将温度保持在75℃左右,直至液体呈蓝光。
- 1、下载文档前请自行甄别文档内容的完整性,平台不提供额外的编辑、内容补充、找答案等附加服务。
- 2、"仅部分预览"的文档,不可在线预览部分如存在完整性等问题,可反馈申请退款(可完整预览的文档不适用该条件!)。
- 3、如文档侵犯您的权益,请联系客服反馈,我们会尽快为您处理(人工客服工作时间:9:00-18:30)。
可聚合乳化剂复配体系对聚合前后苯丙乳液性能的影响规律研究王娣;何浪;余越;关红艳;洪昕林【摘要】选择常规阴离子型十二烷基硫酸钠(SDS)、非离子型壬基酚聚氧乙烯醚(OP-10)以及可聚合型烯丙氧基壬基苯氧基丙醇聚氧乙烯醚硫酸铵(SE-10)乳化剂为研究对象,在复配乳化剂(OP-10/SDS、SE-10/SDS、SE-10/OP-10/SDS)体系中制备得到聚苯乙烯-丙烯酸酯(苯丙)乳液.对比研究了预乳液的稳定性,以及不同配比的乳化剂对苯丙乳液转化率、粒径、乳液稳定性(聚合稳定性、化学稳定性、冻融稳定性、贮存稳定性)以及乳胶膜耐水性等的影响规律.结果表明:3种复配乳化剂体系乳液的化学稳定性和贮存稳定性均较优异.OP-10/SDS体系乳液聚合转化率较低,但凝胶率低,冻融稳定性好,聚合物膜吸水率最高.SE-10/SDS体系转化率提高,涂膜吸水率小,随体系中SDS量的增加凝胶率降低,冻融稳定性提高.而SE-10/OP-10/SDS体系的转化率最高,但凝胶率也偏高,冻融稳定性差,吸水率随着SE-10量的减小呈增大的趋势.【期刊名称】《涂料工业》【年(卷),期】2016(046)005【总页数】6页(P7-11,16)【关键词】苯丙乳液;可聚合乳化剂;稳定性;复配体系【作者】王娣;何浪;余越;关红艳;洪昕林【作者单位】武汉大学化学与分子科学学院,武汉430072;武汉大学化学与分子科学学院,武汉430072;武汉大学化学与分子科学学院,武汉430072;武汉大学化学与分子科学学院,武汉430072;武汉大学化学与分子科学学院,武汉430072【正文语种】中文【中图分类】TQ630.4+94随国家环保法规的日益严格和人们环保意识的逐渐增强,水性涂料在整个涂料工业体系中扮演着越来越重要的角色,而水性树脂则是决定其漆膜性能的关键材料。
苯丙乳液系苯乙烯与丙烯酸酯类单体的共聚物乳液,具有优良的耐热性、耐候性、耐腐蚀性、抗污性、光泽等,广泛应用于工业涂料、建筑涂料等领域[1]。
乳液聚合是制备苯丙乳液最常用的方法,多采用阴离子乳化剂、非离子乳化剂或两者复合,如十二烷基硫酸钠(SDS)、十二烷基苯磺酸钠(SDBS)、壬基酚聚氧乙烯醚(OP-10)等[2]。
但所用小分子乳化剂在所制备聚合物乳液中以物理吸附的方式附着在乳胶粒表面,易受环境的影响发生解吸,使乳液稳定性降低,而且在成膜过程中容易富集在漆膜表面或者其与底材的界面,从而对漆膜的耐水性及附着力等均有严重影响。
目前解决该问题的有效措施是采用可聚合乳化剂,通过在乳化剂结构中引入可聚合双键,参与单体的乳液聚合,从而可以通过化学键合的方式连接在乳胶粒表面,而不会向表面或者界面迁移。
可聚合乳化剂单独应用于乳液聚合时,体系稳定性较差,聚合凝胶率较大,因此需要与传统乳化剂复合使用[3-4],但目前关于两者复配体系对混合单体及所制备聚合物乳液物理化学性质与应用性能的影响规律研究罕见报道。
基于此,本文选取可聚合乳化剂烯丙氧基壬基苯氧基丙醇聚氧乙烯醚硫酸铵(SE-10)作为研究对象,将其与OP-10、SDS单独或复合使用,比较了OP-10/SDS、SE-10/SDS 、SE-10/OP-10/SDS 这 3 个乳化剂体系与混合单体制成的预乳液的稳定性,考察了不同配比的乳化剂对苯丙乳液转化率、粒径、稳定性(聚合稳定性、化学稳定性、冻融稳定性、贮存稳定性)以及乳胶膜耐水性等性能的影响。
1.1 实验原料苯乙烯(St)、丙烯酸丁酯(BA)、甲基丙烯酸丁酯(BMA)、甲基丙烯酸羟乙酯(HEMA):工业级,中山大桥化工集团有限公司;甲基丙烯酸(MAA)、十二烷基硫酸钠(SDS):化学纯,国药集团化学试剂有限公司;壬基酚聚氧乙烯醚(OP-10)、N,N-二甲基乙醇胺:分析纯,天津市科密欧化学试剂有限公司;过硫酸铵:分析纯,国药集团化学试剂有限公司;烯丙氧基壬基苯氧基丙醇聚氧乙烯醚硫酸铵(SE-10):工业级,佛山市科的气体化工有限公司。
SE-10的结构如式(1)所示。
1.2 预乳化、半连续的乳液聚合工艺称取 100 g 一定比例的 St/BA/BMA/HEMA/MAA混合单体;称取4 g乳化剂溶于100 g水中作为乳化剂溶液;称取0.45 g过硫酸铵溶于22 g去离子水中作为引发剂水溶液。
在500 mL烧杯中,加入70 g乳化剂溶液,开动搅拌器(550 r/min),缓慢加入90 g的混合单体进行乳化,搅拌30 min后,即得预乳液。
在装有搅拌器、回流冷凝管、恒压滴液漏斗和温度计的四口烧瓶中加入剩余乳化剂溶液和单体,搅拌通氮气并升温至80℃后,将全部引发剂用量的25%加入到四口烧瓶中,保温30 min得到种子乳液。
在种子乳液的基础上缓慢滴加预乳液和剩余的引发剂水溶液,控制在5 h滴完。
继续反应 2 h后降温,加入N,N-二甲基乙醇胺调节 pH至7,在室温下过滤出料得到苯丙乳液。
1.3 分析测试1.3.1 混合单体预乳液稳定性在500 mL烧杯中,加入总质量42 g的乳化剂和水,开动搅拌器(550 r/min),缓慢加入54 g以一定比例混合的 St/BA/BMA/HEMA/MAA,乳化 30 min 后,停止搅拌,将乳化液转入100 mL量筒中,静置一定时间后读取清液的体积。
1.3.2 转化率取一定量(m1)乳液于表面皿(m2)中,在鼓风干燥箱内,120℃干燥至恒质量后称量(m3),按式(2)、式(3)计算固含量(s)及单体转化率。
式(2)中,m4—投料总质量;m5—投料中不挥发物质量;m6—单体总质量。
1.3.3 粒径及其分布取微量乳液用去离子水稀释后,用英国马尔文公司Nano ZS型动态光散射仪测定乳液的Z均粒径。
1.3.4 凝胶率聚合反应结束后,用200目标准筛过滤乳液,收集滤渣及反应器、搅拌器上的凝聚物,反复清洗后在烘箱中烘至恒质量,凝聚物质量占加入单体质量的百分率即为凝胶率。
1.3.5 乳液稳定性冻融稳定性参照GB/T 11175—2002测定;化学稳定性根据GB/T 20623—2006测定;贮存稳定性根据GB/T 11175—2002测定。
1.3.6 吸水率参照GB/T 12626.8—1990测定涂膜吸水率。
2.1 混合单体预乳液稳定性单体液滴的稳定性对乳液聚合过程有着重要影响,而单体液滴的稳定与乳化剂的选择密切相关。
一般文献中考察乳化剂乳化能力时均选择与水不混溶的有机溶剂作为油相,这与实际聚合中的复杂混合单体并不一致。
鉴于此,本研究采用苯丙乳液聚合中常见混合单体作为油相,系统考察了3种乳化剂SDS、OP-10和SE-10复配时的混合单体乳液的稳定性,结果如表1所示。
由表1可以看出,在OP-10/SDS系列中,单独使用非离子型乳化剂OP-10时,单体乳化稳定性很差,当OP-10/SDS质量比为3∶1时,乳化稳定性最好,此时阴离子乳化剂SDS的电荷稳定和非离子乳化剂OP-10的空间位阻作用较好地发挥了协同效应,提高了乳化能力,其后随着SDS比例的增多,乳化稳定性开始变差,直至单独使用阴离子乳化剂SDS,乳化稳定性最差。
在SE-10/SDS系列中,单独使用可聚合乳化剂SE-10时,单体乳化稳定性较好,这是因为SE-10同时是离子型和非离子型乳化剂,而当SDS比例逐渐增大,乳化稳定性也逐渐变差。
而将质量比3∶1的OP-10/SDS体系作为一个整体与SE-10再复配得到的SE-10/OP-10/SDS系列乳化稳定性均较好,5 h内都不会分层,其中比例为3∶0.75∶0.25时,乳化稳定性最好,在观察的38 h内不分层。
从表1结果可以看出,单独使用非离子乳化剂(OP-10)、阴离子乳化剂(SDS)或阴离子乳化剂比例较高时,混合单体的乳液稳定性均不好。
乳化效果不好的单体预乳液很快出现分层现象,所得的共聚物性能也较差[5]。
本研究乳液聚合时预乳液的滴加时间为5 h,要想获得均匀、稳定性较好的共聚物乳液,预乳液就要在相当长的一段时间内保持稳定。
因此选择预乳液在5 h内不会分层的体系,即OP-10/SDS比例为3∶1、2∶2,SE-10/SDS 比例为4 ∶0、3∶1、2 ∶2, SE-10/OP-10/SDS 比例为4∶0∶0、3 ∶0.75 ∶0.25、2 ∶1.5 ∶0.5、1 ∶2.25∶0.75、0∶3 ∶1继续研究,以保证预乳液在滴加过程中不分层,混合单体的乳液稳定性良好。
2.2 乳化剂对乳液转化率和粒径的影响乳化剂可通过单体与乳化剂的HLB值(亲疏水平衡值)相近的原则或通过单体的乳液稳定性试验来选择[6]。
本研究根据混合单体的乳液稳定性试验,选取能保证混合单体的乳液稳定性良好的乳化剂体系制备乳液,进一步测试不同乳化剂对乳液转化率和粒径的影响,结果见图1及图2。
其中,SE-10/OP-10/SDS系列是将OP-10/SDS作为一个整体与SE-10 复配,4∶0即为单独使用 SE-10,0∶4即OP-10/SDS质量比为3∶1。
由图1可以看出,随着SDS比例增加,3个系列聚合反应的转化率都降低。
在SE-10/OP-10/SDS系列中,比例为4 ∶0 ∶0、3 ∶0.75 ∶0.25、2 ∶1.5 ∶0.5、1 ∶2.25∶0.75时转化率差别均很小,当SE-10量为0时转化率达到最低值。
对比这3个系列,OP-10/SDS转化率最小,而 SE-10/SDS、SE-10/OP-10/SDS 系列转化率较高,说明使用可聚合乳化剂进行乳液聚合可以提高乳液的转化率。
由图2(A)、(B)可以看出, OP-10/SDS、SE-10/SDS系列中,随着SDS比例增加,乳液的粒径减小,分别由141 nm降到107 nm,由131 nm降到98 nm最后降到90 nm,这是因为阴离子型乳化剂SDS的相对分子质量小且临界胶束浓度低,当用量相同时,阴离子乳化剂会产生更多的胶束,生成的乳胶粒的数目增大,导致乳液平均粒径减小[7]。
由图3(C)可以看出,SE-10/OP-10/SDS 系列的粒径差别较小,基本都在130 nm左右。
图2(D)为SE-10/SDS比例为3∶1时所制备的乳液的扫描电镜图,由图可见,当SE-10/SDS比例为3∶1时,乳液中球形的、近单分散的粒子密集堆积着,粒子粒径在90 nm左右。
同时,在实验过程中发现,乳化效果不好的体系,在聚合反应的滴加过程中,预乳液出现分层现象,所制备的乳液转化率低、粒径大。
2.3 乳化剂对乳液稳定性的影响影响乳液稳定性的因素有很多,如聚合物乳液的配方和聚合工艺。
在聚合物乳液的贮存和使用过程中,其稳定性还受到诸如冻结和融化作用、电解质以及放置时间等因素的影响。
乳化剂在聚合前分散增溶单体,形成稳定的单体乳化液,由其形成的单体溶胀胶束又为单体聚合提供场所,而反应性乳化剂甚至直接参与聚合反应[8]。