1.8MM厚中(高)密度纤维板的生产工艺
中密度纤维板生产工艺及操作规程
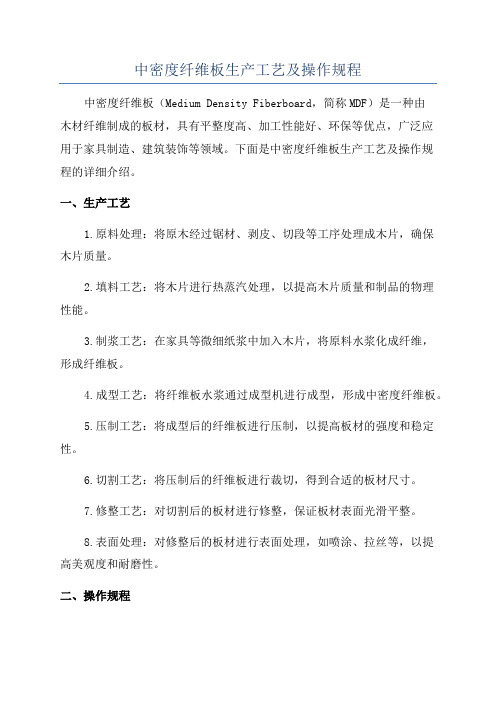
中密度纤维板生产工艺及操作规程中密度纤维板(Medium Density Fiberboard,简称MDF)是一种由木材纤维制成的板材,具有平整度高、加工性能好、环保等优点,广泛应用于家具制造、建筑装饰等领域。
下面是中密度纤维板生产工艺及操作规程的详细介绍。
一、生产工艺1.原料处理:将原木经过锯材、剥皮、切段等工序处理成木片,确保木片质量。
2.填料工艺:将木片进行热蒸汽处理,以提高木片质量和制品的物理性能。
3.制浆工艺:在家具等微细纸浆中加入木片,将原料水浆化成纤维,形成纤维板。
4.成型工艺:将纤维板水浆通过成型机进行成型,形成中密度纤维板。
5.压制工艺:将成型后的纤维板进行压制,以提高板材的强度和稳定性。
6.切割工艺:将压制后的纤维板进行裁切,得到合适的板材尺寸。
7.修整工艺:对切割后的板材进行修整,保证板材表面光滑平整。
8.表面处理:对修整后的板材进行表面处理,如喷涂、拉丝等,以提高美观度和耐磨性。
二、操作规程1.安全操作:操作人员必须穿戴好防护装备,如安全帽、防护镜、防护手套等。
操作人员需了解紧急情况下的应急逃生通道。
2.设备检查:在生产前,检查设备是否运行正常,各部位是否牢固,机械部件是否润滑良好。
3.原料质量检查:对原料进行质量检查,确保木片质量好、含湿率适宜等。
4.操作流程:按照生产工艺的要求,依次进行原料处理、填料工艺、制浆工艺、成型工艺、压制工艺、切割工艺、修整工艺和表面处理等。
5.检验标准:对生产过程中的每个环节,都必须进行检验和测试,确保产品质量达到标准要求。
6.设备维护:对设备定期进行维护和保养,检查各个部位是否有损坏、松动等情况。
7.清洁和卫生:保持生产车间的清洁和卫生,减少灰尘和杂质对产品质量的影响。
8.废弃物处理:废弃物应及时清理、收集和处理,保持生产环境整洁。
通过上述工艺和操作规程,可以确保中密度纤维板的生产质量和产品性能。
同时,操作人员需要经过专业培训,掌握相关的操作技能和安全知识,以确保生产过程的安全性和高效性。
中密度纤维板生产线工艺流程
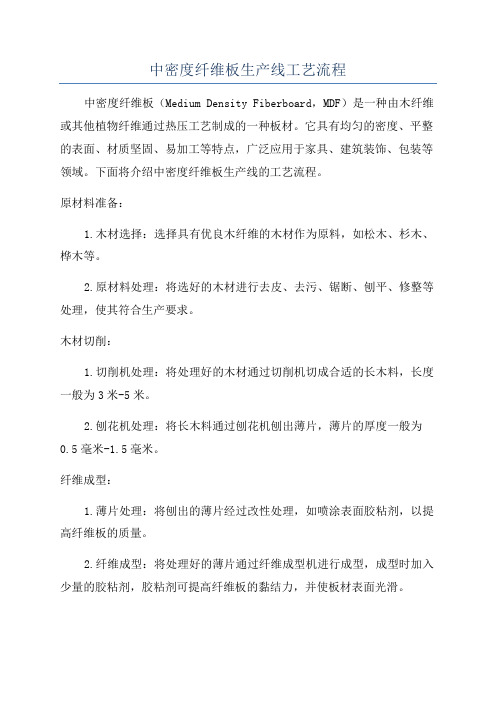
中密度纤维板生产线工艺流程中密度纤维板(Medium Density Fiberboard,MDF)是一种由木纤维或其他植物纤维通过热压工艺制成的一种板材。
它具有均匀的密度、平整的表面、材质坚固、易加工等特点,广泛应用于家具、建筑装饰、包装等领域。
下面将介绍中密度纤维板生产线的工艺流程。
原材料准备:1.木材选择:选择具有优良木纤维的木材作为原料,如松木、杉木、桦木等。
2.原材料处理:将选好的木材进行去皮、去污、锯断、刨平、修整等处理,使其符合生产要求。
木材切削:1.切削机处理:将处理好的木材通过切削机切成合适的长木料,长度一般为3米-5米。
2.刨花机处理:将长木料通过刨花机刨出薄片,薄片的厚度一般为0.5毫米-1.5毫米。
纤维成型:1.薄片处理:将刨出的薄片经过改性处理,如喷涂表面胶粘剂,以提高纤维板的质量。
2.纤维成型:将处理好的薄片通过纤维成型机进行成型,成型时加入少量的胶粘剂,胶粘剂可提高纤维板的黏结力,并使板材表面光滑。
3.热压:将成型好的纤维板放入热压机中进行热压处理,使纤维板的内部纤维更加紧密,提高板材的密度和强度。
修整与涂层:1.修整:将热压后的纤维板进行修整,去除边角毛刺,使板材的尺寸更加精确。
2.涂层:根据生产需求,对板材进行表面涂层处理,如喷涂染色剂、漆膜等,以改善纤维板的外观质感和保护作用。
质检与包装:1.质检:对生产好的纤维板进行质量检查,检查项包括板材尺寸、密度、强度、表面平整度等。
2.包装:将合格的纤维板进行包装,一般采用塑料薄膜包装或纸箱包装,以便运输和储存。
以上是中密度纤维板生产线的主要工艺流程。
在实际生产中,还需要根据具体需求,对工艺进行调整和改进,以提高生产效率和产品质量。
中密度纤维板生产工艺设计
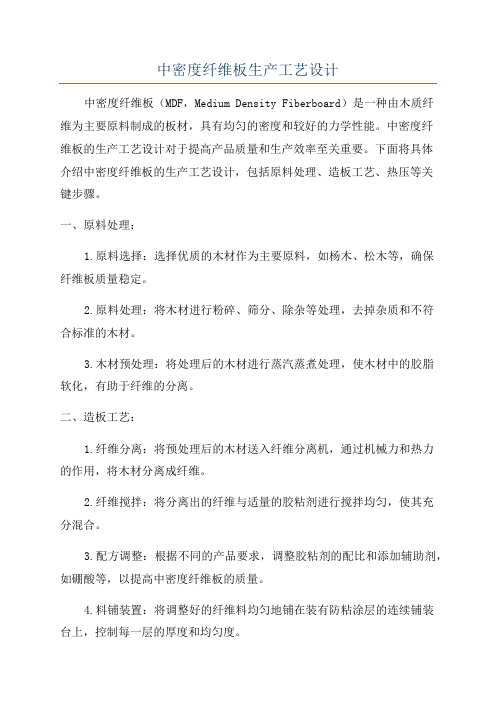
中密度纤维板生产工艺设计中密度纤维板(MDF,Medium Density Fiberboard)是一种由木质纤维为主要原料制成的板材,具有均匀的密度和较好的力学性能。
中密度纤维板的生产工艺设计对于提高产品质量和生产效率至关重要。
下面将具体介绍中密度纤维板的生产工艺设计,包括原料处理、造板工艺、热压等关键步骤。
一、原料处理:1.原料选择:选择优质的木材作为主要原料,如杨木、松木等,确保纤维板质量稳定。
2.原料处理:将木材进行粉碎、筛分、除杂等处理,去掉杂质和不符合标准的木材。
3.木材预处理:将处理后的木材进行蒸汽蒸煮处理,使木材中的胶脂软化,有助于纤维的分离。
二、造板工艺:1.纤维分离:将预处理后的木材送入纤维分离机,通过机械力和热力的作用,将木材分离成纤维。
2.纤维搅拌:将分离出的纤维与适量的胶粘剂进行搅拌均匀,使其充分混合。
3.配方调整:根据不同的产品要求,调整胶粘剂的配比和添加辅助剂,如硼酸等,以提高中密度纤维板的质量。
4.料铺装置:将调整好的纤维料均匀地铺在装有防粘涂层的连续铺装台上,控制每一层的厚度和均匀度。
5.预压:采用热压机对铺好纤维料的连续铺装台进行预压,去除纤维板中的空气和水分,增加纤维板的密度和强度。
三、热压:1.热压板材:将经过预压的纤维板经过涂胶剂处理后进行整齐叠放,放在热压机的压板上。
2.温度控制:通过热压机的加热系统,对纤维板进行高温热压处理,使胶粘剂在高温下固化和交联。
3.压力控制:通过热压机的液压系统,对热压板材进行适当的压力控制,以确保纤维板的密度和强度达到要求。
4.时间控制:控制热压的时间,使胶粘剂充分固化和交联,确保纤维板的质量和稳定性。
5.冷却处理:将热压后的纤维板送入冷却室进行冷却处理,以降低板材温度,保持纤维板的平整度和表面质量。
四、成品处理:1.面板处理:对冷却后的纤维板进行刨花、砂光等处理,使其表面平整、光滑。
2.尺寸修整:对成品纤维板进行尺寸削减和修整,使其符合产品规格和要求。
中(高)密度纤维板生产工艺论文
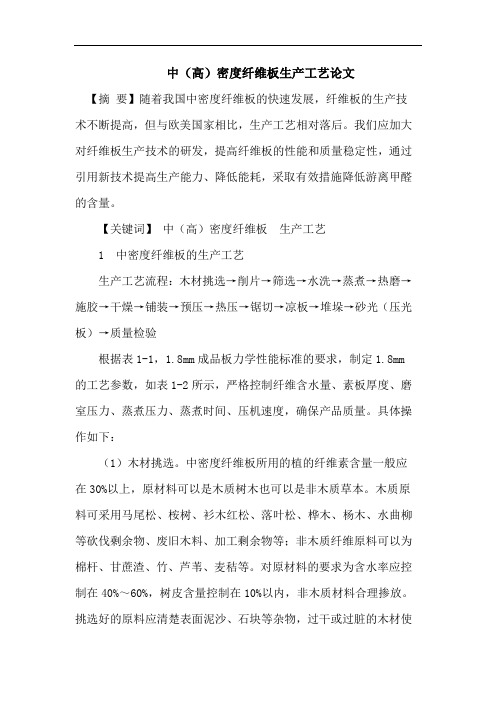
中(高)密度纤维板生产工艺论文【摘要】随着我国中密度纤维板的快速发展,纤维板的生产技术不断提高,但与欧美国家相比,生产工艺相对落后。
我们应加大对纤维板生产技术的研发,提高纤维板的性能和质量稳定性,通过引用新技术提高生产能力、降低能耗,采取有效措施降低游离甲醛的含量。
【关键词】中(高)密度纤维板生产工艺1 中密度纤维板的生产工艺生产工艺流程:木材挑选→削片→筛选→水洗→蒸煮→热磨→施胶→干燥→铺装→预压→热压→锯切→凉板→堆垛→砂光(压光板)→质量检验根据表1-1,1.8mm成品板力学性能标准的要求,制定1.8mm 的工艺参数,如表1-2所示,严格控制纤维含水量、素板厚度、磨室压力、蒸煮压力、蒸煮时间、压机速度,确保产品质量。
具体操作如下:(1)木材挑选。
中密度纤维板所用的植的纤维素含量一般应在30%以上,原材料可以是木质树木也可以是非木质草本。
木质原料可采用马尾松、桉树、衫木红松、落叶松、桦木、杨木、水曲柳等砍伐剩余物、废旧木料、加工剩余物等;非木质纤维原料可以为棉杆、甘蔗渣、竹、芦苇、麦秸等。
对原材料的要求为含水率应控制在40%~60%,树皮含量控制在10%以内,非木质材料合理掺放。
挑选好的原料应清楚表面泥沙、石块等杂物,过干或过脏的木材使用喷水器润湿或清洗,清洗完毕后分类储藏,使用时根据不同树种纤维组织不同和pH值的不同,科学搭配使用。
(2)削片。
削片为木材加工的第一道工序,常用削片设备有削片机鼓式削片机和盘式削片机。
盘式削片机是将木料从减料口送入后,受到高速旋转切削盘上的切削刀片切削,把木片削成长16~30mm,宽15~25mm,厚3~5mm的木片,切削完毕的木片被高速旋转的切屑盘产生的气流送出,切除的木片要求木片大小均匀、平整。
盘式切削机生产效率较高,适用于对较直的原木,弯度较大的木块必须使用故事切片机。
(3)筛选。
如果木片过大或过碎将会影响蒸煮的效果,需要对切片进行筛选,筛选出尺寸较大的木片进行第二次切片。
中密度纤维板工艺流程

中密度纤维板工艺流程中密度纤维板(Medium Density Fiberboard,简称MDF)是一种由纤维素纤维和合成树脂黏合剂制成的均质平板,密度较高,具有良好的机械性能和加工性能。
下面是一篇关于中密度纤维板工艺流程的简要介绍。
首先,中密度纤维板的原料主要是纤维素纤维和合成树脂黏合剂。
纤维素纤维可以是硬木、软木或其他纤维素来源的纤维。
而合成树脂黏合剂主要有尿素醛、酚醛和酚醛脲甲醛树脂。
原料的选取要根据产品的具体要求和用途来确定。
接下来,原料需要进行预处理。
首先需要将纤维素纤维进行切割、磨碎,使其成为合适的长度和直径。
然后将纤维素纤维进行干燥,以减少含水率。
这样可以提高纤维素纤维的接触面积,并改善纤维的黏着能力。
在原料预处理的同时,需要对合成树脂黏合剂进行配比。
根据产品的要求和配方,将合成树脂黏合剂与其他辅料进行混合。
其中辅料包括填料、增强剂和添加剂等。
填料可以改善纤维板的硬度和密度,增强剂可以提高纤维板的强度和耐磨性,添加剂可以改善纤维板的加工性能和外观。
然后,进行成型操作。
首先将经过预处理的纤维素纤维放入成型机中。
成型机会将纤维素纤维进行定向布置,并通过加热和压力使其形成板状。
然后将混合好的合成树脂黏合剂均匀喷洒在纤维素纤维上。
通过加热和压力,使黏合剂固化,并将纤维素纤维牢固地粘结在一起。
随后,进行后处理操作。
成型好的中密度纤维板需要进行修边和切割,以使其尺寸更加准确。
然后进行砂光和抛光等表面处理,以提高中密度纤维板的光滑度和平整度。
最后,通过质检,包括检查尺寸偏差、弯曲、开裂等问题,确保产品的质量。
最后,进行包装和存储。
对成品中密度纤维板进行包装,可以采用纸箱或包装袋等材料。
然后将包装好的中密度纤维板存放在干燥通风的库房中,以防止受潮和发霉。
综上所述,中密度纤维板的工艺流程包括原料预处理、合成树脂黏合剂配比、成型、后处理、质检以及包装和存储。
这些工艺环节的科学运用及操作规范,对于生产出高质量的中密度纤维板具有重要意义。
中纤板工艺流程

中纤板工艺流程中纤板,又称中密度纤维板,是一种以植物纤维为原料,经过高温高压加工而成的一种人造板材。
它具有密度均匀、强度高、不易变形等优点,因此在家具制造、建筑装饰等领域得到了广泛的应用。
下面将介绍中纤板的生产工艺流程。
1. 原料准备中纤板的主要原料是植物纤维,常用的有木材纤维、竹子纤维等。
首先需要对原料进行筛分、破碎和干燥处理,以确保原料的质量和干燥度符合生产要求。
2. 纤维预处理经过原料准备后,需要对纤维进行预处理。
首先将纤维放入蒸煮锅中进行蒸煮处理,以软化纤维并去除其中的杂质。
接着进行磨浆处理,将纤维磨成细小的纤维素颗粒,以便后续的成型加工。
3. 料浆调制将经过预处理的纤维素颗粒与粘合剂、防腐剂等添加剂混合,制成一定浓度的纤维素料浆。
在这一过程中需要严格控制料浆的配比和搅拌时间,以确保料浆的均匀性和稳定性。
4. 成型将调制好的料浆倒入成型机中,经过模具压制成型。
成型过程中需要控制压力和温度,以确保中纤板的密度和强度符合要求。
成型后的中纤板需要经过一定的时间进行固化和冷却。
5. 热压固化冷却后的中纤板需要进行热压处理,以提高其密度和强度。
在热压过程中,需要控制压力、温度和时间,以确保中纤板的质量和性能。
6. 整理修边经过热压处理后的中纤板需要进行整理修边,以确保其尺寸和平整度符合要求。
修边过程中需要使用专业的修边设备,以确保修边的精度和效率。
7. 质检包装最后对成品中纤板进行质量检测,检查其密度、强度、平整度等指标是否符合要求。
合格的中纤板进行包装,以便运输和销售。
以上就是中纤板的生产工艺流程,通过严格控制每个环节的工艺参数和质量要求,可以生产出质量稳定、性能优良的中纤板产品,满足不同领域的应用需求。
中密度纤维板生产线实用工艺流程

生产中厚板时原木不要求剥皮,但树皮允许体积分数小于8%%。原木装
载机将小径木、枝桠材等木材原料放在储木台上,通过皮带运输机送 入削片
机,削片机前装有金属探测器,避免带有金属的木材进入削片机。进
入削片机
的木材被削成规格木片,经由螺旋运输机和斗式提升机送人木片储仓 储存。
由于软材硬材要按比例混合,所以采用两个储仓,分别储存软材和硬 材木片。
理化学性质稳定、来源广泛、价格低廉、无毒无味无污染等特点,但 蒸汽用于热压工序时也有几个不易克服的缺点:一是热压工序通常需 要较高的温度,一般在160――220C之间,与此相对应的蒸汽压力 为1.6――2.5MPa,因此,需要整个供热系统(包括锅炉、管道及其
附件与接头等)具有较高的耐压强度,这就使供热系统结构复杂,投 资增大,运行管理不便;二是为了保证热压质量,要求热压板面温度 尽可能均匀一致,一般要求同一块压板板面上的温差小于3°C,各层 热压板之间的温差小于5°C,这就要求载热体在进出热压板时的温度 差要尽可能小。采用蒸汽加热时,往往会由于凝结水排故不及时,使 热压质量降低;三是蒸汽在热压机中放热后排出的凝结水具有较高的 温度(一般在160C以上),其回收难度较大,若处理不当,则可能造 成严重的能源浪费。由于蒸汽加热具有这些不易克服的缺点,所以, 近年来越来越多的汽车内饰生产热压机都采用了高温热油供热系统。 热油供热的特点热油又称为导热油,属于一种高温有机热载体,
被送入直径为4500MM的高效旋风分离器,在这里将纤维和湿空气 分离,湿热空气排到大气中。干燥纤维能力为5000KG/H,蒸汽耗 量最大为8200KG/H,设计
风量为95000M3/H,风压为4500PA。于纤维通过旋转出料器排出 至螺旋称重进
料机,纤维在这里被准确称出重量。该装置还ห้องสมุดไป่ตู้按预置定的胶和纤维 的比例
中密度纤维板生产线工艺流程

中密度纤维板生产线工艺流程中密度纤维板生产线工艺流程1,削片―筛选生产中厚板时原木不要求剥皮,但树皮允许体积分数小于8%。
原木装载机将小径木、枝桠材等木材原料放在储木台上,通过皮带运输机送入削片机,削片机前装有金属探测器,避免带有金属的木材进入削片机。
进入削片机的木材被削成规格木片,经由螺旋运输机和斗式提升机送人木片储仓储存。
由于软材硬材要按比例混合,所以采用两个储仓,分别储存软材和硬材木片。
储仓下部的出料装置能控制出料速度,根据工艺配比,由出料装置控制出料量,使软硬木片按要求的比例均匀混合。
软硬木片之比为3:7 或4:6。
混合木片的PH 值最好能相对稳定在5,0---5,5 之间。
然后,木片经皮带运输机送至振动筛进行筛分,筛选机一般有两层。
在除去过大的和过小的木片和杂物后,将合格木片送至清洗设备除去泥沙、小碎石、污物及金属块等。
木片清洗可分为水洗和干洗两种方式。
根据我国原料的现状,采用水洗较合适。
但木片水洗耗水量大,又有污水处理问题,且造价较高,虽然木片清洗的质量好,效率高,有利于纤维分离和板的质量,但生产中厚板的中小生产规模厂有不少还是采用了木片干洗方式。
净化后的木片经螺旋运输机和斗式提升机送往热磨间。
2,热磨―施胶―干燥木片经过磁鼓除去切片当中的铁块,进入热磨机前的预蒸料仓临时储存,预蒸料仓的有效容积为6M3,装有料位指示器,可观测木片的过满或空缺。
木片经振动给料器,木塞螺旋进入垂直蒸煮器进行蒸煮软化,增加含水率,蒸煮器配有!射线料位计,用来控制料位和预置蒸煮时间。
木片在蒸煮软化后由运输螺旋送人热磨机进行纤维分离。
在热磨系统中配有起动分离器,热磨机起动时,通常开始热磨的纤维质量不符合生产要求,这些不合格纤维通过排料阀和排料管进入起动分离器,然后落入废料堆场。
当纤维质量达到生产要求时,排料阀关闭,生产出料阀打开。
与此同时,根据工艺要求将胶料按一定比例调好,定量送往施胶系统,石蜡采用直接加热熔化,然后送往投放装置。
- 1、下载文档前请自行甄别文档内容的完整性,平台不提供额外的编辑、内容补充、找答案等附加服务。
- 2、"仅部分预览"的文档,不可在线预览部分如存在完整性等问题,可反馈申请退款(可完整预览的文档不适用该条件!)。
- 3、如文档侵犯您的权益,请联系客服反馈,我们会尽快为您处理(人工客服工作时间:9:00-18:30)。
1.8MM厚中(高)密度纤维板的生产工艺作者:黄祖青叶新华来源:《中国科技纵横》2014年第13期【摘要】纤维板又称密度板,广泛应用于家具、室内装修(强化地板、吊顶、墙板)、音响或乐器的壳体、建筑、车(船)装饰等,根据密度的不同纤维板可分为高、中、低密度纤维板。
中密度纤维板是以小径级原木、采伐、加工剩余物及其它植物纤维经过一系列工艺加工而成的人造板材,它的密度一般在500到880kg每立方米左右,具有优良的物理力学性能(静曲强度、平面抗拉强度高,弹性模数较刨花板好,吸水性能较低、厚度膨胀率低)、装饰性能(纤维板表面光滑、平整度好,便于涂饰、节约涂料)和加工性能(可以锯、钻、开槽、雕刻、抛光、开榫)。
其特点为:变形量少、屋里力学性能适中特点,而且内部结构均匀、密度适中、加工性能好、表面平整光滑。
高密度纤维板是指密度大于880kg/m3的纤维板,其内部结构细密,强度高,尺寸稳定性好,寿命长,耐温耐湿性能好,常用于复合地板、强化地板、室内外装潢以及高档家私、音响、车船装饰材料等。
本文主要介绍中密度纤维板的生产工艺,并结合生产过程中出现的质量问题,并提出有效策略。
【关键词】中(高)密度纤维板生产工艺1 中密度纤维板的生产工艺生产工艺流程:木材挑选→削片→筛选→水洗→蒸煮→热磨→施胶→干燥→铺装→预压→热压→锯切→凉板→堆垛→砂光(压光板)→质量检验根据表1-1,1.8mm成品板力学性能标准的要求,制定1.8mm的工艺参数,如表1-2所示,严格控制纤维含水量、素板厚度、磨室压力、蒸煮压力、蒸煮时间、压机速度,确保产品质量。
具体操作如下:(1)木材挑选。
中密度纤维板所用的植的纤维素含量一般应在30%以上,原材料可以是木质树木也可以是非木质草本。
木质原料可采用马尾松、桉树、衫木红松、落叶松、桦木、杨木、水曲柳等砍伐剩余物、废旧木料、加工剩余物等;非木质纤维原料可以为棉杆、甘蔗渣、竹、芦苇、麦秸等。
对原材料的要求为含水率应控制在40%~60%,树皮含量控制在10%以内,非木质材料合理掺放。
挑选好的原料应清楚表面泥沙、石块等杂物,过干或过脏的木材使用喷水器润湿或清洗,清洗完毕后分类储藏,使用时根据不同树种纤维组织不同和pH值的不同,科学搭配使用。
(2)削片。
削片为木材加工的第一道工序,常用削片设备有削片机鼓式削片机和盘式削片机。
盘式削片机是将木料从减料口送入后,受到高速旋转切削盘上的切削刀片切削,把木片削成长16~30mm,宽15~25mm,厚3~5mm的木片,切削完毕的木片被高速旋转的切屑盘产生的气流送出,切除的木片要求木片大小均匀、平整。
盘式切削机生产效率较高,适用于对较直的原木,弯度较大的木块必须使用故事切片机。
(3)筛选。
如果木片过大或过碎将会影响蒸煮的效果,需要对切片进行筛选,筛选出尺寸较大的木片进行第二次切片。
(4)水洗。
切片之后的木片含有泥沙、金属(废木料中的铁钉)、细屑等杂物,且一些木片的含水率不足,需要进行水洗。
通过水洗可以有效地清除各种杂物,能提高、均匀木片的含水率,使纤维分离时能顺利进料,水分能吸收研磨时的摩擦热,降低原料软化的温度。
(5)蒸煮。
热磨前使用热水或饱和蒸汽对木片进行水煮或汽蒸,使纤维胞间层软化或部分溶解,提高纤维原料的塑性,减少动力消耗,缩短解纤的时间,提高纤维分离的质量。
蒸煮时应控制蒸煮温度,随着蒸煮温度的提高,纤维之间的联接被削弱,解纤时纤维所受的机械损伤减少,纤维形态较好,有利于纤维之间的结合,板强度提高。
蒸煮温度过高,纤维本身将受到严重破坏,机械强度降低,所以板强度降低;蒸煮温度不变时,适当延长蒸煮时间,板强度得到提高。
但蒸煮时间过长,板强度反而下降。
一般采用饱和蒸汽压0.8~1.2MPa,蒸煮软化时间控制在1.2~1.7min,蒸煮温度160~180℃。
(6)热磨。
充分利用植物纤维胞间层纤维素含量高、软化点低的特点,使用饱和蒸汽将原料加热到160~180℃,热磨压力控制在 7.4~7.6bar,植物纤维受热软化,当热磨机的轴向往复运动时,木片受到压力、剪切力、扭转力和拉伸力,产生塑性变形,当外力消失后纤维又恢复原状,当经过上千次的变形恢复后产生疲劳,最后分离。
在实际生产中,增大磨盘的直径或提高磨盘的转速都会加快分离速度。
(7)施胶。
首先制备CARB,制备方法为按1.1~1.5的摩尔比称量甲醛与尿素,然后将尿素分批加入反应液中,反应温度控制在75~95℃,当反应液的粘度为20s时停止反应,配置完毕后,然后按照固体树脂对绝干纤维之比8~12%均匀施胶。
(8)干燥。
由于经过热磨工艺后纤维含水率为30%~40%,施加液体胶粘剂后的含水率可高至40%~50%,导致纤维易结团,难以输送和达到均匀铺装效果,需要进行干燥处理。
中密度纤维板生产线干燥剂均采用闪急式管道干燥系统,由燃烧炉、空气预热器、干燥管道、风送系统、旋风分离器、监控装置及防火安全设施组成[1]。
要求干燥介质温度为160℃~200℃,气流速度为20~30m/S,干燥时间为4到5秒,干燥后纤维含水率为8%~12%。
(9)铺装。
铺装包括机械铺装和气流铺装,机械铺装利用机械所产生的动力,将纤维打散,然后在离心力和重力的作用下沉降成型,均匀的铺撒在铺装运输带上;气流成型是在气流作用下,纤维成分散状态自由下落并沉积在成型网带上,形成一定厚度的板坯。
铺装成型工序直接影响制品的各项物理力学性能,而且影响板的翘曲变形、尺寸稳定性及其密度、厚度偏差。
因此铺装板坯时要求密度均匀稳定,厚薄一致,具有一定的密实度,并保证达到足够的厚度和尺寸规格,以满足产品质量的要求。
(10)预压。
预压的作用是排除板坯内留存的空气,防止热压时大量空气外逸冲破板坯;通过预压,使板坯具有一定的密实度,提高自身的支撑强度,以保证板坯在输送、切割、装板时,不致产生断裂和破损。
(11)热压。
热压指在热量和压力的联合作用下,板坯中的水分汽化、蒸发、密度增加、胶粘剂固化、防水剂重新分布,经过生一系列物理化学变化,从而使纤维间形成各种结合力,使制品达到并符合质量要求,是纤维板成型的重要工序之一。
热压分为四个阶段分别为板坯压缩排空气、温度渗透、加压至规定厚度、卸压排气定型。
热压过程中控制的主要工艺参数有:温度、压力、时间、位置、含水率等,影响压后毛板质量的因素还有:压机闭合速度的快慢(一般控制在1300mm/s)、同闭机构的同步性、卸荷速度的快慢。
温度提高了纤维的塑性,为各种键的结合创造了有利条件;热量使板坯中的水分汽化;热量使脲胶受热,流动性增加,有利于加速固化。
常用的脲醛树脂胶热压温度为160~180℃,酚醛树脂胶热压温度为185~195℃。
热压力克服板坯的反弹力,进一步排除板坯中的空气,增大纤维之间的接触面与交织性达到控制板厚度和密度的要求,一般热压压力为2.5~3.5MPa,制造高强度板或用硬质木材纤维时,压力可达5.0~5.5MPa。
热压时间由胶的种类与性能、纤维的质量、板坯含水率、热压的温度、压力、加热方式、板的厚度与密度等工艺因素来确定。
一般板坯含水率控制在8%~12%,为了提高传热效率和板面硬度,可允许表层纤维含水率比芯层高1%~2%。
在相同的热压压力下,不同的加压速度,影响板的性能和断面密度分布;加压速度快,板的静曲强度高,内结合强度降低。
加压速度慢,板的静曲强度下降,预固化层加厚,内结合力提高,但过慢会使整张板松软达不到质量要求,一般平均加压速度为5mm/s。
(12)锯切。
为了保证产品具有一定的规格,需要对热压成型的板材锯边,锯切时经常检查锯片外观,确保锯切质量。
(13)凉板、堆垛。
热压结束之后,纤维板的温度较高需要降至60摄氏度以下具有一定的强度后进行堆垛,凉板过程中可以通冷风冷却,利于排除热压后存在的甲醛,凉板结束后便可进行堆垛。
(14)砂光。
热压后板制品的表面不平整,有预固化层,密度不够,影响外观和性能。
砂光操作时,注意控制进料速度,砂带应与砂光机保持平行,防治振动产生波纹,同时注意砂光结束后厚度偏差符合要求。
(15)质量检验。
砂光结束后检查纤维板的外观质量、密度、厚度、尺寸、平整度、强度是否满足要求,其外观质量检测如表1-3所示,检测纤维板外观、板面等是否存在缺陷,纤维含水率是否达到要求,按照质量标准划分优等品、合格品和次品,然后根据不同材质、质量分别存放。
2 中密度纤维板生产过程中常见的质量问题及对策2.1 耗能问题及对策问题:纤维板生产过程中用到高耗能设备,如送料电机、除尘电机、热能电机和干燥电机,如果采用传统的启动方式耗能较高,增加了生产成本。
对策:为降低电能的损耗,采用变频技术。
从表1-4电机节能项目测试表和表1-5沪千节电工频与变频状态下用电对比表中可以看出,在满足生产需要的情况下,采用变频工作可以降低4.5%左右的电耗。
2.2 生产质量不稳定,游离甲醛含量高问题:中密度纤维板局部松软、边角缺失等产品表面达不到要求;厚度、几何偏差过大,边缘垂直度过大等尺寸偏差达不到要求;静曲模量、弹性模量等强度达不到要求。
对策:严格控制生产过程,加强重要环节的管控,提高产品质量;增加自动化设备的投入,提高自动化控制水平;加强游离甲醛的检测,确保甲醛释放在规定范围内。
3 结语随着我国中密度纤维板的快速发展,纤维板的生产技术不断提高,但与欧美国家相比,生产工艺相对落后。
我们应加大对纤维板生产技术的研发,提高纤维板的性能和质量稳定性,通过引用新技术提高生产能力、降低能耗,采取有效措施降低游离甲醛的含量。
参考文献:[1]欧阳琳.中密度纤维板生产工艺学[J].北京木材工业,1994:20-21.。